降低正压直吹式制粉系统电耗的探索
降低正压直吹式制粉系统电耗的探索

降低正压直吹式制粉系统电耗的探索摘要在煤种稳定的燃烧过程中,通过采取优化密封风机运行方式、合理调整一次风压、有效控制磨煤机出力和钢球装载量等手段,在保证锅炉稳定运行的前提下,降低了发电厂的制粉电耗。
关键词双进双出磨煤机;正压直吹式制粉系统;制粉电耗;探索随着煤炭市场供应关系日趋紧张,火力发电厂的节能降耗成为开源节流的重中之重。
制粉电耗占厂用电相当大的份额,降低制粉电耗对控制发电成本有着重要意义。
本文通过对双进双出磨煤机正压直吹式制粉系统的试验和运行分析,总结出了有效降低制粉电耗的手段。
1 机组和系统简介巩义豫联电厂锅炉为东方锅炉厂制造的DG1025/17.4-Ⅱ14型亚临界压力中间一次再热的自然循环锅炉,双拱形单炉膛,“W”型火焰燃烧方式,尾部双烟道结构,固态排渣,全钢悬吊结构。
采用3台沈重BBD4062型双进双出球磨机,两台一次风机,两台密封风机,6台电子称重式皮带给煤机。
锅炉配有18个双旋风筒分离式煤粉燃烧器,以45°角向下喷入炉膛。
2 降低磨密封风电耗试验原设计两台密封风机运行,入口挡板开度都在35%时,单台密封风机电流65A,出口风压12.5 kPa~13kPa,满足磨煤机运行要求。
通过试验,在额定负荷(300mW)下,单台密封风机运行时,入口挡板开至90%,电流70A,出口压力12.2kPa,三台磨煤机密封风差压都在3.0kPa以上,已能满足密封风差压要求,但电耗几乎减少一半。
同时单台密封风机运行可以实现设备的可靠备用。
小结:额定负荷试验中,在保证差压的前提下,通过调整单台密封风机运行,可以优化运行方式。
两台密封风机运行时电流为:130A单台密封风机运行时电流:70A。
年节约电量为:(130A-70A)×380V×1.732×0.85×7200小时=241676.352 kW·h通过对密封风的调整,密封风电耗每年可节约电能241676.352kW·h。
降低制粉系统电耗

降低煤粉炉制粉系统电耗的措施李建摘要:本文针对热电公司480T/H煤粉炉的制粉系统电耗较高的问题,基于对制粉系统的深刻研究以及对制粉系统设备运行的客观分析,从运行参数控制和现场设备管理等方面入手,最大限度的找出造成制粉系统电耗高的原因,从而制定降低煤粉炉制粉系统电耗的有效措施并加以实施,以提高电厂效益。
关键词:分析降低制粉系统电耗措施正文:1 论文选题背景唐山三友集团热电公司为集团的汽电能源基地,备有2台480t/h的煤粉炉,共有四套中间储仓式制粉系统,长期以来,制粉系统电耗高的问题一直制约着电厂效益的提高。
因此,本文以降低制粉系统电耗为主题,与读者共同探讨降低制粉系统电耗的方法。
2 制粉系统及相关设备简介2.1 制粉系统的主要任务为锅炉制备合格的煤粉以供锅炉进行燃烧。
2.2 制粉系统简图2.2 制粉系统主要设备介绍2.2.1 原煤仓:储存原煤;2.2.2 给煤机:为磨煤机提供原煤,保证原煤均匀的送入磨煤机中,热电公司煤粉炉配有四台皮带给煤机;2.2.3 磨煤机:将原煤磨制成煤粉,热电公司配有四台筒形球磨机。
工作原理为:磨煤机通体转动时,桶内钢球和煤在离心力和摩擦力的作用下被提升到一定高度,由于重力作用而跌落,桶内原煤受到下落钢球的撞击作用以及钢球与钢球之间、钢球与护甲之间的挤压和碾磨作用而被破碎磨制成具有一定细度的煤粉;2.2.4 粗分离:利用重力、惯性力、离心力的作用将合格的煤粉与不合格的煤粉分离,将不合格的煤粉通过回粉管送回磨煤机中继续磨制,还可以调节煤粉细度;2.2.5 细分离:将煤粉与热风分离,将煤粉送到粉仓中储存,部分风粉混合物由排粉机送入炉膛中燃烧;2.2.6 排粉机:为整个制粉系统提供动力,保证系统负压运行。
3 制粉系统电耗的定义及计算方法3.1 制粉系统电耗即通常所说的吨汽磨电耗,是指锅炉每产生一吨蒸汽,磨煤机所耗费的电量,计算公式为:吨汽磨电耗=一段时间内磨煤机的耗电量/该时间内的产汽量单位:度/吨汽因为外界用汽量的多少决定锅炉的产汽量,为不可控因素,因此,降低制粉系统电耗的方法为降低磨煤机的耗电量。
660MW机组中速磨直吹式制粉系统节能优化探究
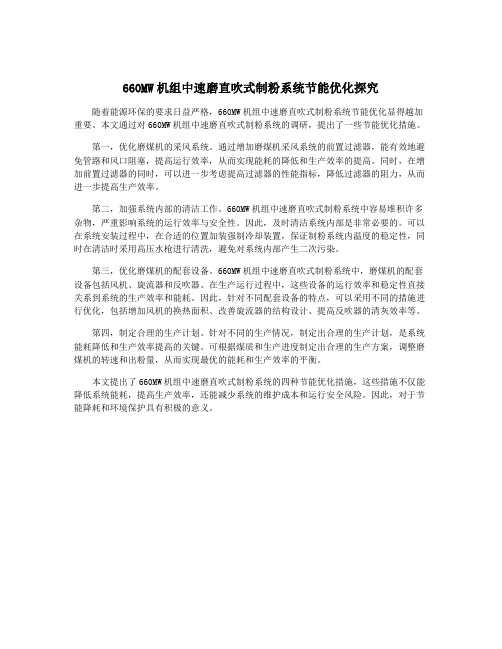
660MW机组中速磨直吹式制粉系统节能优化探究随着能源环保的要求日益严格,660MW机组中速磨直吹式制粉系统节能优化显得越加重要。
本文通过对660MW机组中速磨直吹式制粉系统的调研,提出了一些节能优化措施。
第一,优化磨煤机的采风系统。
通过增加磨煤机采风系统的前置过滤器,能有效地避免管路和风口阻塞,提高运行效率,从而实现能耗的降低和生产效率的提高。
同时,在增加前置过滤器的同时,可以进一步考虑提高过滤器的性能指标,降低过滤器的阻力,从而进一步提高生产效率。
第二,加强系统内部的清洁工作。
660MW机组中速磨直吹式制粉系统中容易堆积许多杂物,严重影响系统的运行效率与安全性。
因此,及时清洁系统内部是非常必要的。
可以在系统安装过程中,在合适的位置加装强制冷却装置,保证制粉系统内温度的稳定性,同时在清洁时采用高压水枪进行清洗,避免对系统内部产生二次污染。
第三,优化磨煤机的配套设备。
660MW机组中速磨直吹式制粉系统中,磨煤机的配套设备包括风机、旋流器和反吹器。
在生产运行过程中,这些设备的运行效率和稳定性直接关系到系统的生产效率和能耗。
因此,针对不同配套设备的特点,可以采用不同的措施进行优化,包括增加风机的换热面积、改善旋流器的结构设计、提高反吹器的清灰效率等。
第四,制定合理的生产计划。
针对不同的生产情况,制定出合理的生产计划,是系统能耗降低和生产效率提高的关键。
可根据煤质和生产进度制定出合理的生产方案,调整磨煤机的转速和出粉量,从而实现最优的能耗和生产效率的平衡。
本文提出了660MW机组中速磨直吹式制粉系统的四种节能优化措施,这些措施不仅能降低系统能耗,提高生产效率,还能减少系统的维护成本和运行安全风险。
因此,对于节能降耗和环境保护具有积极的意义。
《锅炉设备及运行》测试题+参考答案
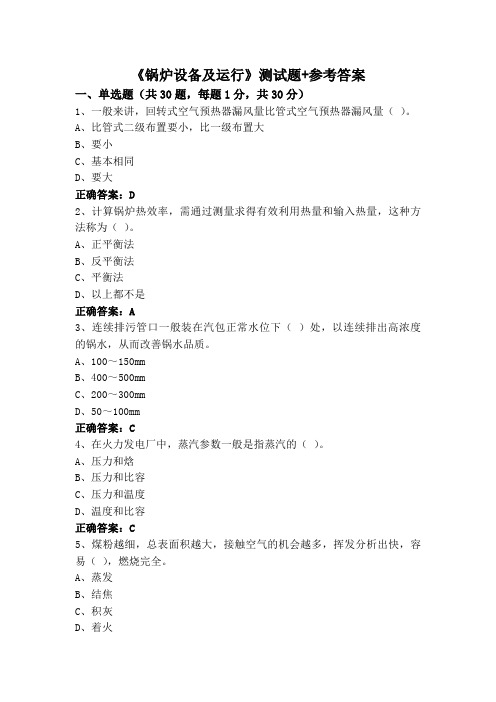
《锅炉设备及运行》测试题+参考答案一、单选题(共30题,每题1分,共30分)1、一般来讲,回转式空气预热器漏风量比管式空气预热器漏风量()。
A、比管式二级布置要小,比一级布置大B、要小C、基本相同D、要大正确答案:D2、计算锅炉热效率,需通过测量求得有效利用热量和输入热量,这种方法称为()。
A、正平衡法B、反平衡法C、平衡法D、以上都不是正确答案:A3、连续排污管口一般装在汽包正常水位下()处,以连续排出高浓度的锅水,从而改善锅水品质。
A、100~150mmB、400~500mmC、200~300mmD、50~100mm正确答案:C4、在火力发电厂中,蒸汽参数一般是指蒸汽的()。
A、压力和焓B、压力和比容C、压力和温度D、温度和比容正确答案:C5、煤粉越细,总表面积越大,接触空气的机会越多,挥发分析出快,容易(),燃烧完全。
A、蒸发B、结焦C、积灰D、着火正确答案:D6、()的水冷壁进口装置了节流圈,使流量能按管子所受热负荷大小来合理分配。
A、汽包锅炉B、直流锅炉C、复合循环锅炉D、强制循环锅炉正确答案:D7、大容量锅炉一般采用()水冷壁。
A、膜式B、光管式C、丁爪式正确答案:A8、任一台给煤机跳闸时,应联动()。
A、开启对应的冷风门B、关闭对应的总风门,开启对应的冷风门C、关闭对应的热风门和冷风门D、关闭对应的总风门正确答案:B9、E型磨煤机碾磨件包括上、下磨环和钢球,配合型线均为圆弧,钢球在上下磨环间自由滚动,不断地改变自身的旋转轴线,其配合线型始终保持不变,磨损较均匀,对磨煤机出力影响()。
A、较小B、较大C、随运行小时变化D、一般正确答案:A10、当锅水含盐量达到临界含盐量时,蒸汽的湿度将()。
A、不变B、急剧增大C、减少D、逐渐增大正确答案:B11、事故放水管在汽包上的开口位置宜在()。
A、最高水位处B、汽包下部C、正常水位与最低水位之间正确答案:C12、强制循环锅炉的循环倍率比自然循环锅炉的循环倍率()。
降低1000 M W机组综合厂用电率的探索与应用

降低1000 M W机组综合厂用电率的探索与应用摘要:随着电力行业改革的不断深化,厂网分家、竞价上网等政策的逐步实施,降低厂综合用电率、发电成本和提高电价竞争力,已成为各发电厂努力追求的经济目标。
本文对影响厂用电率的因素进行分析,并提出了降低厂用电率的方案和措施,为火电厂今后的节能减排、创造效益提供了基础和保障。
关键词:降低1000MW机组综合厂用电率能源工业作为国民经济的基础,对于社会、经济的发展和人民生活水平的提高都极为重要。
在高速增长的经济环境下,中国能源工业面临经济增长与环境保护的双重压力。
而且还受资金、技术、能源价格等因素的影响,中国能源利用效率比发达国家低得多,只及发达国家的50%左右,90%以上的能源在开采、加工转换、储运和终端利用过程中损失和浪费。
由此可见,对能源的有效利用在我国已经非常迫切。
火电厂是最主要的能源消耗大户,在我国的二次能源结构中,约占74%。
而在火力发电厂中,泵与风机是最主要的耗电设备,加上这些设备存在着“大马拉小车”的现场,同时由于这些设备长期连续运行和经常处于低负荷运行状态,运行工况点偏离高效点,运行效率降低,大量的能源在终端利用中被白白地浪费掉。
1000MW机组是新型的机组,在技术上还有提高空间,通过对其全面研究,可以进一步提高运行人员的技术水平,因此,本文重点探索降低1000MW机组综合厂用电率的措施。
1、1000MW机组现场运行情况分析我厂1000MW机组锅炉为高效超超临界参数变压直流炉,设计煤种,校核煤种:兖矿煤和济北煤矿的混煤。
制粉系统采用正压直吹式,设有两台50%容量的动叶可调轴流式一次风机提供一次热、冷风输送煤粉。
采用两台静叶可调吸风机和两台动叶可调送风机。
每台锅炉配有6台双进双出、单电机驱动钢球磨。
锅炉给水系统配置有2台50%BMCR容量的汽动变速给水泵,一台25%BMCR容量的变速电动给水泵作为备用。
凝汽器设计为双壳体、双背压、单流程,可在机组最大出力、循环冷却水温33℃,背压不大于4.5/5.7kPa工况下长期运行。
直吹式制粉系统单耗偏高分析及有效措施

直吹式制粉系统单耗偏高分析及有效措施近年来,随着我国现代化经济体制改革的不断深入,在极大地推动了各生产行业发展进步的同时,也对各生产领域尤其是传统的高能耗行业的节能减排提出了新要求与新标准。
作为火电厂锅炉的关键组成部分,直吹式制粉系统运行效率直接关系着企业的整体经济效益。
但就目前而言,我国火电厂直吹式制粉系统普遍存在单耗偏高问题,这不利于相关企业经济效益的实现,也不符合当前可持续发展与节能减排的要求。
本文针对直吹式制粉系统单耗偏高原因,探讨了应如何通过有效控制措施,降低直吹式制粉系统单耗。
标签:直吹式;制粉系统;单耗偏高;原因;措施引言直吹式制粉系统具有占地面积少、成本投入低、操作简单、维护方便、适应强、相应迅速等诸多优势,因而在我国火电厂得到广泛的应用普及。
但大部分火电厂直吹式制粉系统在实际运行过程,往往存在着单耗过高的情况,这极大地限制了直吹式制粉系统的生产效率与经济效益,所以深入分析探讨造成直吹式制粉系统单耗原因的并针对问题,采取相应的改进措施,对于我国火电厂节能减排与提高经济效益的目标实现具有重要的现实意义。
1直吹式制粉系统单耗偏高原因分析1.1管理水平低,节能意识差目前,我国大部分火电厂对直吹式制粉系统的管理水平偏低,尤其是操作人员整体业务水平低,缺少专业培训,在工作中往往容易出现误操作;系统出现问题也无法及时进行调整改进。
同时,部分火电厂管理者与人员节能意识差,没有正确认识节能减排对于企业发展的重要作用,即使设备已经出现严重老化,甚至发生泄漏也不及时进行更换维护。
这些都是造成直吹式制粉系统单耗偏高的重要因素。
1.2设计选型不合理一些火电厂在发展初期,在设备选型与系统设计方面欠缺考虑,存在不合理情况。
如磨煤机的选型不合理,就会导致无法保障制粉细度与出力;分离器选择不恰当,造成煤粉细度无法保障,分离效果难以达到标准要求;通风系统设计不当,导致局部堵塞,煤仓经常性出现堵煤问题,设计选型不合理使得直吹式制粉系统往往无法处于正常、稳定的运行状态,进而导致单耗偏高。
660MW机组中速磨直吹式制粉系统节能优化探究
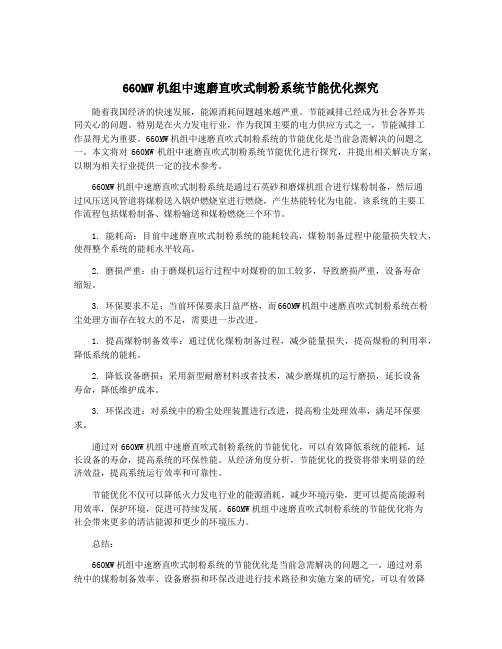
660MW机组中速磨直吹式制粉系统节能优化探究随着我国经济的快速发展,能源消耗问题越来越严重。
节能减排已经成为社会各界共同关心的问题。
特别是在火力发电行业,作为我国主要的电力供应方式之一,节能减排工作显得尤为重要。
660MW机组中速磨直吹式制粉系统的节能优化是当前急需解决的问题之一。
本文将对660MW机组中速磨直吹式制粉系统节能优化进行探究,并提出相关解决方案,以期为相关行业提供一定的技术参考。
660MW机组中速磨直吹式制粉系统是通过石英砂和磨煤机组合进行煤粉制备,然后通过风压送风管道将煤粉送入锅炉燃烧室进行燃烧,产生热能转化为电能。
该系统的主要工作流程包括煤粉制备、煤粉输送和煤粉燃烧三个环节。
1. 能耗高:目前中速磨直吹式制粉系统的能耗较高,煤粉制备过程中能量损失较大,使得整个系统的能耗水平较高。
2. 磨损严重:由于磨煤机运行过程中对煤粉的加工较多,导致磨损严重,设备寿命缩短。
3. 环保要求不足:当前环保要求日益严格,而660MW机组中速磨直吹式制粉系统在粉尘处理方面存在较大的不足,需要进一步改进。
1. 提高煤粉制备效率:通过优化煤粉制备过程,减少能量损失,提高煤粉的利用率,降低系统的能耗。
2. 降低设备磨损:采用新型耐磨材料或者技术,减少磨煤机的运行磨损,延长设备寿命,降低维护成本。
3. 环保改进:对系统中的粉尘处理装置进行改进,提高粉尘处理效率,满足环保要求。
通过对660MW机组中速磨直吹式制粉系统的节能优化,可以有效降低系统的能耗,延长设备的寿命,提高系统的环保性能。
从经济角度分析,节能优化的投资将带来明显的经济效益,提高系统运行效率和可靠性。
节能优化不仅可以降低火力发电行业的能源消耗,减少环境污染,更可以提高能源利用效率,保护环境,促进可持续发展。
660MW机组中速磨直吹式制粉系统的节能优化将为社会带来更多的清洁能源和更少的环境压力。
总结:660MW机组中速磨直吹式制粉系统的节能优化是当前急需解决的问题之一。
如何降低600MW机组制粉系统单耗

如何降低600MW机组制粉系统单耗关键词制粉单耗:在设计条件下,制出1kg煤粉所消耗的电量厂用电率:厂用电耗电量占发电厂全部发电量的百分数,称为厂用电率。
厂用电率是发电厂运行的主要经济指标之一。
燃料:用来燃烧以取得热量的物质直吹式制粉系统:是指经过磨煤机磨制的煤粉,全部直接吹入炉膛进行燃烧的制粉系统600MW机组是现在的主力机组,山东邹县发电厂600MW机组是山东第一台600MW机组,其中有很多的经验对其它的电厂也是一个很好的借鉴。
我在邹县电厂600MW工作了7年,对如何降低600MW机组制粉系统单耗,有一些深刻的认识,对于围绕如何降低制粉系统单耗所做的措施也有很深的认识。
山东邹县发电厂600MW机组,其锅炉(2020t/h系亚临界中间再热自然循环燃煤汽包炉)制粉系统为正压直吹式,配有6台美国FW公司生产的D-10-D型双进双出钢球磨煤机和12台EG24型电子称重式皮带给煤机以及2台美国TLT—Babcok公司生产的双吸离心静叶可调式一次风机。
在MCR 工况下,五台磨煤机运行,一台备用。
每台磨煤机每端有2根煤粉管,4根煤粉管接入同一层喷燃器,6台磨煤机共带有24只喷燃器。
该喷燃器是由FW公司独创的CF/SF低NOx燃烧器,前后墙布置对冲燃烧。
两台双吸离心式一次风机,将环境空气,直接送入两台三分仓空气预热器的一次风仓格中加热至300℃,分别送入6台双进双出滚筒式钢球磨煤机的一次风入口端,作为磨煤机的干燥剂,并将磨制的煤粉送入炉膛;一次风机出口压力冷风,旁路预热器,分别进入磨煤机的各部位,作为磨煤机、给煤机的密封风,以及一次风煤粉管道的辅助风。
原煤由原煤仓下来,经两台皮带式给煤机,从磨煤机两端分别送入磨煤机,原煤在磨煤机内与一次风混合,风粉混合物经磨煤机两端的分离器分离后,粗粉重新回到磨煤机内,细粉和一次风则通过磨煤机两端的4根一次风管,分别进入该磨煤机所对应的4台CF/SF 低NOX型燃烧器,送入炉膛进行燃烧。
- 1、下载文档前请自行甄别文档内容的完整性,平台不提供额外的编辑、内容补充、找答案等附加服务。
- 2、"仅部分预览"的文档,不可在线预览部分如存在完整性等问题,可反馈申请退款(可完整预览的文档不适用该条件!)。
- 3、如文档侵犯您的权益,请联系客服反馈,我们会尽快为您处理(人工客服工作时间:9:00-18:30)。
降低正压直吹式制粉系统电耗的探索摘要在煤种稳定的燃烧过程中,通过采取优化密封风机运行方式、合理调整一次风压、有效控制磨煤机出力和钢球装载量等手段,在保证锅炉稳定运行的前提下,降低了发电厂的制粉电耗。
关键词双进双出磨煤机;正压直吹式制粉系统;制粉电耗;探索
中图分类号tm621 文献标识码a 文章编号 1674-6708(2011)37-0025-02
随着煤炭市场供应关系日趋紧张,火力发电厂的节能降耗成为开源节流的重中之重。
制粉电耗占厂用电相当大的份额,降低制粉电耗对控制发电成本有着重要意义。
本文通过对双进双出磨煤机正压直吹式制粉系统的试验和运行分析,总结出了有效降低制粉电耗的手段。
1 机组和系统简介
巩义豫联电厂锅炉为东方锅炉厂制造的dg1025/17.4-ⅱ14型亚临界压力中间一次再热的自然循环锅炉,双拱形单炉膛,“w”型火焰燃烧方式,尾部双烟道结构,固态排渣,全钢悬吊结构。
采用3台沈重bbd4062型双进双出球磨机,两台一次风机,两台密封风机,6台电子称重式皮带给煤机。
锅炉配有18个双旋风筒分离式煤粉燃烧器,以45°角向下喷入炉膛。
2 降低磨密封风电耗试验
原设计两台密封风机运行,入口挡板开度都在35%时,单台密封风机电流65a,出口风压12.5 kpa~13kpa,满足磨煤机运行要求。
通过试验,在额定负荷(300mw)下,单台密封风机运行时,入口挡板开至90%,电流70a,出口压力12.2kpa,三台磨煤机密封风差压都在3.0kpa以上,已能满足密封风差压要求,但电耗几乎减少一半。
同时单台密封风机运行可以实现设备的可靠备用。
小结:额定负荷试验中,在保证差压的前提下,通过调整单台密封风机运行,可以优化运行方式。
两台密封风机运行时电流为:130a
单台密封风机运行时电流:70a。
年节约电量为:(130a-70a)×380v×1.732×0.85×7200小时=241676.352 kw·h
通过对密封风的调整,密封风电耗每年可节约电能
241676.352kw·h。
3 降低一次风机电耗试验
机组试运初期,额定负荷下一次风母管压力经常保持
11kpa~11.5kpa。
经过调整发现一次风母管压力保持在10.5kpa,磨入口风压控制在8kpa~8.5kpa时,一次风速可控制在22m/s~25m/s 的最佳范围内,同时也满足机组接带负荷的需要。
因此,在煤质发生变化或升降负荷后,通过合理搭配磨热风挡板和容量风挡板开度,在保证运行稳定的条件下可降低一次风母管压力,从而降低一
次风机的电耗。
小结:在满足额定负荷(300mw)前提下,通过调整磨煤机热风挡板和容量风挡板开度降低一次风母管压力,以降低一次风机电耗。
一次风压11kpa时,风机电流93+87=180a
一次风压10.5kpa,风机电流88+83=171a
年节约电量:(180a-171a)×6000v×1.732×0.85×7200小时=572391.36 kw·h
一次风机电耗每年可节约电能572 391.36kw·h。
4 降低磨煤机电耗试验
机组试运初期,额定负荷下,三台磨煤机均保持140a电流运行。
通过进行最佳钢球装载量试验,磨煤机出力特性试验,最终确定了磨煤机的最佳运行方式。
4.1 确定最佳钢球装载量试验
在一定的范围内,随着筒体内钢球装载量的增多,磨煤机出力增加,制粉单位电耗(磨煤单位电耗与通风单位电耗之和)有所下降,但当钢球装载量增加到一定程度后,由于充球容积的增大,钢球落下的有效工作高度减小,撞击作用减弱,磨煤机出力的增加程度减缓,甚至下降。
这时磨煤功率的增加并不减缓,因而磨煤单位电耗将有显著的增加。
钢球装载量试验方法:利用机组停运检修机会,将磨煤机内钢
球取出筛选后,分别在a磨内装载60t钢球,b磨内装载75t钢球,c磨内装载70t钢球,保持磨煤机的分离器折向挡板开度(30%-35%)。
机组启动加入运行后,保持机组负荷稳定,煤质稳定,调整各磨煤机的容量风风量一致、各磨煤机出力一致,调整后稳定2小时,测定各煤粉管道煤粉细度r90,记录数据如下:
通过试验,发现磨煤机内装球量为75t时,各煤粉管道煤粉细度r90值最接近设计值。
4.2 磨煤机出力特性试验
运行中发现,磨煤机磨煤时的功率损耗与不磨煤时的能量消耗相差无几,其主要原因是由于磨煤机筒体和钢球的质量要比其中煤的质量大许多倍,绝大部分的能量都消耗在筒体转动和提升钢球上。
由此可知,磨煤单位电耗随磨煤机出力的降低磨煤单位电耗增加,所以磨煤机在低负荷或低于额定负荷下运行是不经济的;但磨煤机出力过大时,会导致煤粉细度得不到保证。
磨煤机出力特性试验:分别将磨煤机出力调整到40t/h、50t/h、55t/h,各工况稳定2h,测定煤份细度。
通过试验,发现磨煤机最大出力为55t,当单台磨出力超过55t时,各煤粉管道煤粉细度r90值就会偏离燃烧要求值。
由此可知,若再增加进煤量,由于筒体内载煤量大,钢球落下高度减小,由于球间煤层加厚,一部分能量将消耗于煤层变形,钢球能量不能得到充分利用,磨煤机有效出力将随载煤量增加反而减低。
小结:通过试验发现磨煤机内装球量在75t,同时出力不超过55t时运行状况最佳。
对制粉系统优化调整后,三台磨煤机平均电流由试运时的140a 降至135a。
年节约电量:(140-135)×3×6000v×1.732×0.85×7200小时=953985.6 kw·h
5 结论
1)加强对密封风机滤网的清理维护工作,以保证单台密封风机运行时风压足够,实现密封风机一运一备,达到降低密封风机电耗的目的;
2)在一次风压允许值的范围内合理调整磨组热风挡板和容量风挡板开度,达到最佳的运行工况,同时实现降低一次风机电耗;
3)通过试验,确定了磨煤机的最佳装球量及磨煤机的最大出力,在煤粉细度得到保证的情况下,既保证锅炉安全经济运行,也降低了磨煤机制粉电耗。
参考文献
[1]编委会.火电厂设备安装调试运行与维护检修技术及危险点预控实务全书[m].北京:中国电力出版社,2010,6.
[2]姚志松,吴军.工业企业实用节电技术[m].北京:中国电力出版社,2010,7.。