起重机主梁上拱度计算方法
起重机主梁上拱度和悬臂上翘度的测量方法

△f 测起重机主梁上拱度和悬臂上翘度的测量方法1. 测量条件:室内起重机应水平放置,并无强辐射和热源影响;室外起重机应水平放置,并无风、无日照。
当测量时,有日照影响,其实测上拱值应为测得的上拱值减去附表 2.1 的修正值。
2. 上拱度应在跨中 S/10 区域内测量;悬臂上翘度应在悬臂全长处及最大有效悬臂处分别测量(后者为与测下挠度值。
3. 计算上拱度值或上翘度值的基准点。
当采用电动单梁起重机时,应为两侧大车车轮中 心向跨内约 500~600mm 处确定的基准点;当采用通用桥式起重机及通用门式起重机时, 应为主梁上翼缘板的测量线与大车轮中心铅垂线的交点。
4. 当有条件时,可以用经纬仪、水准仪等测标高的方法进行基准线测量,亦可以张紧的钢丝进行基准测量。
5. 测量时,宜清除小车自重的影响。
6. 电动单梁起重机主梁跨中上拱度的测量(附图 2,应采用 15kg 的重锤将直径为ф0.49~ф0.52m m 的钢丝拉好(附图 2,测出上拱度测量值△F 测。
上拱值应按下式计算:F=△F 测-△g (附 2.1)式中: F ---△F 测 ----上拱度测量值(mm );△ g ---正值(,可按附表 2.2 取值。
起重机械作业指导书附表2.1 测量上梁上拱度的日照温度差扣除值注:①上翼板的温度应在主梁中段位置的横筋板之间、受阳面轨道侧附近测量;②下翼缘板的温度应在主梁中段位置两横筋板之间、翼缘板中心位置测量;③对起重量为30~50t的起重机,表中数值应乘以0.85;④非标准跨度的起重机,可以用比例插入法计算。
附表2.2 测量跨中上拱度时钢丝下垂修正值△g7.通用桥式起重机主梁跨中上拱度的测量(附图2.2),应用15kg 的重锤将直径为φ0.49~φ0.52mm 的钢丝绳按附图 2.2 拉好,钢丝位置在主梁上翼缘板宽度中心,当已铺好轨道时,钢丝可稍偏离宽度中心,并宜避开轨道压板,再将两根长度为h 的等高棒于端梁中心处并垂直于端梁,测量出主梁在跨中横筋板处的上翼缘板表面与钢丝间的距离,找出拱度最高点即为上拱度检测值 h1,上拱度测量结果应按下式计算:(附2.2)F=h-h1- △g式中:F结果(;h1---(;h--至钢丝间距离△g影响值(。
桥式起重机门式起重机
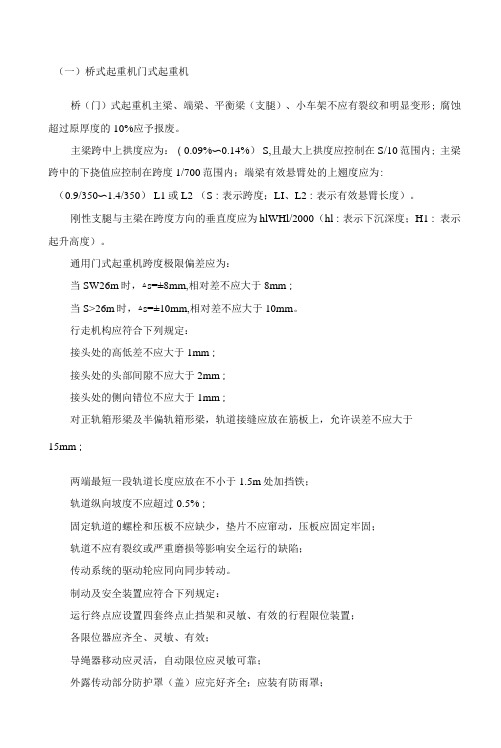
(一)桥式起重机门式起重机桥(门)式起重机主梁、端梁、平衡梁(支腿)、小车架不应有裂纹和明显变形; 腐蚀超过原厚度的10%应予报废。
主梁跨中上拱度应为:(0.09%〜0.14%) S,且最大上拱度应控制在S/10范围内; 主梁跨中的下挠值应控制在跨度1/700范围内;端梁有效悬臂处的上翘度应为:(0.9/350〜1.4/350) L1或L2 (S:表示跨度;LI、L2:表示有效悬臂长度)。
刚性支腿与主梁在跨度方向的垂直度应为hlWHl/2000(hl:表示下沉深度;H1:表示起升高度)。
通用门式起重机跨度极限偏差应为:当SW26m时,△s=±8mm,相对差不应大于8mm;当S>26m时,△s=±10mm,相对差不应大于10mm。
行走机构应符合下列规定:接头处的高低差不应大于1mm;接头处的头部间隙不应大于2mm;接头处的侧向错位不应大于1mm;对正轨箱形梁及半偏轨箱形梁,轨道接缝应放在筋板上,允许误差不应大于15mm;两端最短一段轨道长度应放在不小于1.5m处加挡铁;轨道纵向坡度不应超过0.5%;固定轨道的螺栓和压板不应缺少,垫片不应窜动,压板应固定牢固;轨道不应有裂纹或严重磨损等影响安全运行的缺陷;传动系统的驱动轮应同向同步转动。
制动及安全装置应符合下列规定:运行终点应设置四套终点止挡架和灵敏、有效的行程限位装置;各限位器应齐全、灵敏、有效;导绳器移动应灵活,自动限位应灵敏可靠;外露传动部分防护罩(盖)应完好齐全;应装有防雨罩;进入起重机的门和司机室到桥架上的门,应设有电器连锁保护装置,当任何一个门打开时,起重机所有机构均应停止工作;大车轨道铺设在工作面或地面时,起重机应设置扫轨板;扫轨板距轨面不应大于10mm;应设置非自动复位型的紧急断电开关,并保证司机操作方便;在主梁一侧落钩的单主梁起重机应设置防倾翻安全钩;小车正常运行时,应保证安全钩与主梁的间隙适宜,运行不应有卡阻;吊运炽热金属的起升机构应装两套高度限位器,两套开关动作应有先后,并应控制不同的断路装置或采用不同的结构形式,功能应可靠、有效;桥式起重机司机室位于大车滑线端时,通向起重机的梯子和走台与滑线间应设置防护板;滑线端的端梁下,应设置防护板。
起重机主梁上拱度计算方法

起重机主梁上拱度计算方法拱度计算的基本原理:主梁的拱度计算是基于静力平衡原理和材料力学原理。
主梁在负荷作用下会发生弯曲,导致拱度产生。
主梁的拱度可以通过弯矩和横向力的平衡计算得出。
弯曲计算方法:1.分析负荷:首先需要分析主梁所承受的负荷,包括自重、荷载和冲击荷载等。
负荷的大小和分布方式对主梁的弯曲变形有直接影响。
2.计算支反力:在计算主梁的拱度之前,需要先确定主梁的支反力。
支反力的计算可以根据静力平衡法和等效条件法来进行。
3.计算弯矩:弯曲计算的关键是计算主梁上的弯矩。
弯矩可以通过结构力学方程和静力平衡方程进行计算。
4.计算曲率半径:曲率半径是衡量主梁弯曲程度的指标。
曲率半径可以通过弯矩和剪力的关系以及截面矩量和剪力量的计算得出。
5.计算拱度:拱度计算的最终目标是计算主梁上各个截面的拱度。
拱度的计算可以通过弯矩和曲率半径的公式计算得出。
工程实例:以一座起重机主梁为例,该主梁的长度为15米,宽度为2米,厚度为0.2米。
主梁所承受的负荷为10吨,负荷集中在主梁的中间点。
弯曲计算的目标是计算主梁中间点的拱度。
1.分析负荷:主梁的负荷为10吨,集中在主梁的中间点。
2.计算支反力:根据静力平衡法,主梁的支反力为负荷的一半,即5吨。
3.计算弯矩:主梁的弯矩可以通过结构力学方程和静力平衡方程得出。
根据梁的弯曲理论,主梁的弯矩为M=(P*h)/4,其中P为负荷,h为主梁高度。
代入数值可得M=(10*5)/4=12.5吨米。
4.计算曲率半径:曲率半径可以通过弯矩和剪力的关系以及截面矩量和剪力量的计算得出。
对于矩形截面的主梁,曲率半径R可以通过公式R=M/(W*D^2)来计算,其中W为主梁宽度,D为主梁厚度。
代入数值可得R=12.5/(2*0.2^2)=312.5米。
5.计算拱度:拱度的计算可以通过弯矩和曲率半径的公式计算得出。
拱度d可以通过公式d=(M/R)*(L/2)^2来计算,其中L为主梁长度。
代入数值可得d=(12.5/312.5)*(15/2)^2=7.5毫米。
起重机主梁上拱度和悬臂上翘度的测量方法

△f 测起重机主梁上拱度和悬臂上翘度的测量方法1. 测量条件:室内起重机应水平放置,并无强辐射和热源影响;室外起重机应水平放置,并无风、无日照。
当测量时,有日照影响,其实测上拱值应为测得的上拱值减去附表 2.1 的修正值。
2. 上拱度应在跨中 S/10 区域内测量;悬臂上翘度应在悬臂全长处及最大有效悬臂处分别测量(后者为与测下挠度值。
3. 计算上拱度值或上翘度值的基准点。
当采用电动单梁起重机时,应为两侧大车车轮中 心向跨内约 500~600mm 处确定的基准点;当采用通用桥式起重机及通用门式起重机时, 应为主梁上翼缘板的测量线与大车轮中心铅垂线的交点。
4. 当有条件时,可以用经纬仪、水准仪等测标高的方法进行基准线测量,亦可以张紧的钢丝进行基准测量。
5. 测量时,宜清除小车自重的影响。
6. 电动单梁起重机主梁跨中上拱度的测量(附图 2,应采用 15kg 的重锤将直径为ф0.49~ф0.52m m 的钢丝拉好(附图 2,测出上拱度测量值△F 测。
上拱值应按下式计算:F=△F 测-△g (附 2.1)式中: F ---△F 测 ----上拱度测量值(mm );△ g ---正值(,可按附表 2.2 取值。
起重机械作业指导书附表2.1 测量上梁上拱度的日照温度差扣除值注:①上翼板的温度应在主梁中段位置的横筋板之间、受阳面轨道侧附近测量;②下翼缘板的温度应在主梁中段位置两横筋板之间、翼缘板中心位置测量;③对起重量为30~50t的起重机,表中数值应乘以0.85;④非标准跨度的起重机,可以用比例插入法计算。
附表2.2 测量跨中上拱度时钢丝下垂修正值△g7.通用桥式起重机主梁跨中上拱度的测量(附图2.2),应用15kg 的重锤将直径为φ0.49~φ0.52mm 的钢丝绳按附图 2.2 拉好,钢丝位置在主梁上翼缘板宽度中心,当已铺好轨道时,钢丝可稍偏离宽度中心,并宜避开轨道压板,再将两根长度为h 的等高棒于端梁中心处并垂直于端梁,测量出主梁在跨中横筋板处的上翼缘板表面与钢丝间的距离,找出拱度最高点即为上拱度检测值 h1,上拱度测量结果应按下式计算:(附2.2)F=h-h1- △g式中:F结果(;h1---(;h--至钢丝间距离△g影响值(。
桥式起重机载荷试验方案

崇信发电铁路集煤站接卸系统工程桥式起重载荷试验方案中国水电四局崇信发电铁路集煤站接卸系统工程项目部二O一四年三月十日批准:审核:编制:1、工程概况项目名称:崇信发电铁路集煤站接卸系统建筑安装工程建设地点:甘肃省平凉市崇信县铜城乡本工程翻车机室安装有一台电动双梁桥式起重机,其型号为QD20/5-13.5A5,起重机跨距为13.5米,设备自身重量为22.76吨。
设备性能参数见下表:2、编制依据2.1《通用桥式起重机》GB/T14405-1993;2.2《起重机械安装工程施工及验收规范》GB50278-1998;2.3《电气装置安装工程起重机电气装置施工及验收规范》GB50256-1996;2.4《起重机试验规范和程序》GB/T5095-1986;2.5《桥式起重机安全检查规程》;2.6《起重机安全规程》GB6067-1985;2.7《吊车轨道联结》G325;2.8 合同文件及设备随机资料。
3、试车前的准备和检验3.1 关闭电源,按图纸尺寸和技术要求检查各固定件连接是否牢固,各传动机械装配是否精确灵活,金属结构是否变形,钢丝绳在滑轮和卷筒上的缠绕情况。
3.2 检查起重机的安装架设是否符合安装架设的有关规定,有兆欧表检查电路和所有电气设备的绝缘电阻。
3.3 各润滑点加注润滑油脂。
3.4 保证电气设备工作正常可靠,其中必须特别注意电磁铁、限位开关,安全开关和紧急开关的工作可靠性。
在电动机与运行机构断开的情况下分别驱动大车电机,检查两电动机运转方向是否一致,否则应改变接线相序,使两台电机同相运转。
3.5 采取措施防止在起重机上参加试验的人员触及带电设备。
4、负荷试验4.1 无负荷试运转用手转动各机构的制动轮,使车轮轴或卷筒轴不得有卡住现象,然后分别对大车运行机构、小车运行机构、起升机构空载通电试车,各机构应正常运转,小车运行时,主动轮应在轨道全长上接触,检查各限位开关电否安全可靠。
电缆导电的松紧要适当,能顺利地放缆和收缆。
起重机主梁跨中上拱度的快速估算

起重机主梁跨中上拱度的快速估算主要内容:本文主要针对起重机主梁跨中上拱度值(0.9/1000~1.4/1000)S在实际工作中运算很不方便,推导出其快速估算公式,以供大家交流参考。
关键词:起重机上拱度估算一、概述桥、门式起重机主梁跨中上拱度是起重机产品制造安全监督检验的考核项目之一。
GB/T14405《通用桥式起重机》和GB/T14406《通用门式起重机》标准中规定:起重机主梁跨中上拱度应为(0.9/1000~1.4/1000)S;JB/T1306《电动单梁起重机》和JB/T2603《电动单梁悬挂起重机》标准中规定:起重机主梁跨中上拱度为(1/1000~1.4/1000)S。
由于0.9与1.4都不是整数, S(起重机跨度)也不一定为整数,且其大多为车间跨度实测值,因此在实际工作中运算操作很不方便。
二、上拱度的估算鉴于对起重机不合理的吊运、存放和安装等原因会导致上拱度减小,起重机制造单位在实际生产过程中对起重机的实际跨中上拱度都按标准的上限值(即1.4 S /1000)来考核控制。
为此,结合实际工作经验,现将其估算公式简单推导如下:上拱度值上限值:F=1.4 S /1000=(1+0.5-0.1)S/1000=(S+S/2-S/10)/1000= S/1000+(S/2)/1000-(S/10)/1000 ---①S<20m时, 0 <(S/10)/1000<2 mm,即-1<(S/10)/1000-1<1 mm20≤S<30m 时, 2≤(S/10)/1000<3 mm,即0≤(S/10)/1000-2<1 mm30≤S<40m时, 3≤(S/10)/1000<4 mm,即0≤(S/10)/1000-3<1 mm……假设 N1=(S/10)/1000-1 ,则(S/10)/1000= N1+1 ---②N2=(S/10)/1000-2 ,则(S/10)/1000= N2+2 ---③N3=(S/10)/1000-3,则(S/10)/1000= N3+3 ---④……因│N1│、│N2│、│N3│…均<1mm,对于快速估算来说可忽略不计。
起重设备安装工程施工及验收规范

目次第—章⋯⋯⋯⋯⋯⋯⋯⋯⋯⋯⋯⋯⋯⋯⋯⋯⋯(1) 第二章般定⋯⋯⋯⋯⋯⋯⋯⋯⋯⋯⋯⋯⋯⋯⋯⋯⋯⋯(2) 第三章起重机道和档⋯⋯⋯⋯⋯⋯⋯⋯⋯⋯⋯⋯⋯(4) 第四章葫芦⋯⋯⋯⋯⋯⋯⋯⋯⋯⋯⋯⋯⋯⋯⋯⋯⋯(9) 第五章手梁式起重机和手梁式挂起重机⋯⋯⋯⋯(9) 第六章梁式起重机和梁式挂起重机⋯⋯⋯(12)第七章通用式起重机⋯⋯⋯⋯⋯⋯⋯⋯⋯⋯⋯⋯⋯⋯(16) 第八章冶金起重机⋯⋯⋯⋯⋯⋯⋯⋯⋯⋯⋯⋯⋯⋯⋯⋯(20) 第九章通用式起重机和装卸⋯⋯⋯⋯⋯⋯⋯⋯⋯⋯(26) 第十章壁上起重机和柱式臂起重机⋯⋯⋯⋯⋯⋯⋯(31)第十一章起重机的运⋯⋯⋯⋯⋯⋯⋯⋯⋯⋯⋯⋯⋯(34) 第十二章工程收⋯⋯⋯⋯⋯⋯⋯⋯⋯⋯⋯⋯⋯⋯⋯⋯(38) 附一起重机及其道跨度的量方法⋯⋯⋯⋯⋯⋯⋯(39) 附二起重机主梁上拱度和臂上度的量方法⋯⋯(44) 附三起重机水平偏斜的量方法⋯⋯⋯⋯⋯⋯⋯(50) 附凹本范用明⋯⋯⋯⋯⋯⋯⋯⋯⋯⋯⋯⋯⋯⋯(51) 附带明⋯⋯⋯⋯⋯⋯⋯⋯⋯⋯⋯⋯⋯⋯⋯⋯⋯⋯⋯(52) 附:条则明⋯⋯⋯⋯⋯⋯⋯⋯⋯⋯⋯⋯⋯⋯⋯⋯⋯⋯⋯(53)第一章总则第 1.0.1 条为保证起重设施安装工程的质量和促使安装技术的进步,制定本规范。
第 1.0.2 条本规范合用于电动葫芦、手 ( 电 ) 动梁式起重机、手 ( 电 ) 动梁式悬挂起重机、通用桥式起重机、冶金起重机、通用门式起重机与装卸桥、壁上起重机和柱式悬壁起重机的安装。
第 1.0.3 条起重设施安装工程应从设施开箱起,至设施试运行合格办理工程查收为止。
第 1.0.4 条对大型、特别、复杂的起重设施的吊装,应拟订完美的吊装方案;当利用建筑构造柱、梁等作为吊装的重要承力点时,应经构造汁算,并经有关部门赞同后方可利用。
第 1.0.5 条起重设施安装完成,一定经负荷试运行合格办理工程查罢手续后,方可投入生产使用。
第条起重设施安装工程施工及查收除应按本规范的规定履行外,尚应切合现行有关国家标准规范的规定。
桥(门)式起重机主梁挠度的检测
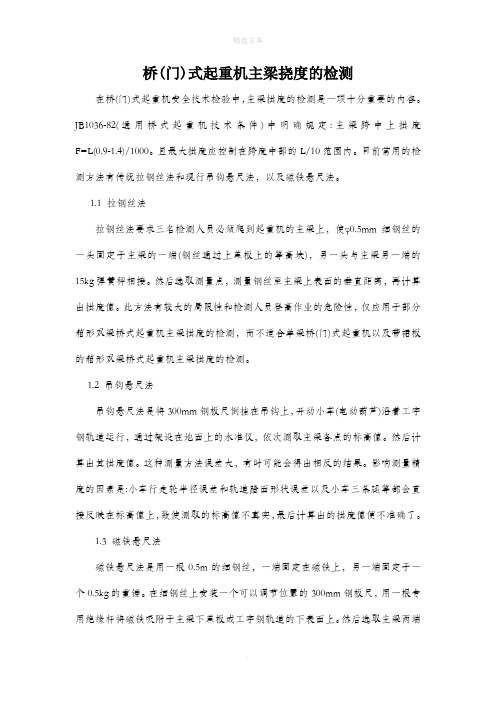
桥(门)式起重机主梁挠度的检测在桥(门)式起重机安全技术检验中,主梁拱度的检测是一项十分重要的内容。
JB1036-82(通用桥式起重机技术条件)中明确规定:主梁跨中上拱度F=L(0.9-1.4)/1000。
且最大拱度应控制在跨度中部的L/10范围内。
目前常用的检测方法有传统拉钢丝法和现行吊钩悬尺法,以及磁铁悬尺法。
1.1 拉钢丝法拉钢丝法要求三名检测人员必须爬到起重机的主梁上,使φ0.5mm细钢丝的一头固定于主梁的一端(钢丝通过上盖板上的等高块),另一头与主梁另一端的15kg弹簧秤相接。
然后选取测量点,测量钢丝至主梁上表面的垂直距离,再计算出拱度值。
此方法有较大的局限性和检测人员登高作业的危险性,仅应用于部分箱形双梁桥式起重机主梁拱度的检测,而不适合单梁桥(门)式起重机以及带裙板的箱形双梁桥式起重机主梁拱度的检测。
1.2 吊钩悬尺法吊钩悬尺法是将300mm钢板尺倒挂在吊钩上,开动小车(电动葫芦)沿着工字钢轨道运行,通过架设在地面上的水准仪,依次测取主梁各点的标高值。
然后计算出其拱度值。
这种测量方法误差大,有时可能会得出相反的结果。
影响测量精度的因素是:小车行走轮半径误差和轨道踏面形状误差以及小车三条腿等都会直接反映在标高值上,致使测取的标高值不真实,最后计算出的拱度值便不准确了。
1.3 磁铁悬尺法磁铁悬尺法是用一根0.5m的细钢丝,一端固定在磁铁上,另一端固定于一个0.5kg的重锤。
在细钢丝上安装一个可以调节位置的300mm钢板尺,用一根专用绝缘杆将磁铁吸附于主梁下盖板或工字钢轨道的下表面上。
然后选取主梁两端和梁中三个测量点,通过架设在地面上的水准仪读取被磁铁悬挂标尺上的数值,从而计算出主梁跨中的拱度值。
即主梁跨中拱度值=跨中标高值-1/2(较高端跨端标高值+较底端跨端标高值)。
钢板尺正向固定于细钢丝上,测得结果是正值时为上拱,反之为下挠。
利用此法可检测各种型式起重机主梁拱度,方法简捷,结果准确,省时省力。
- 1、下载文档前请自行甄别文档内容的完整性,平台不提供额外的编辑、内容补充、找答案等附加服务。
- 2、"仅部分预览"的文档,不可在线预览部分如存在完整性等问题,可反馈申请退款(可完整预览的文档不适用该条件!)。
- 3、如文档侵犯您的权益,请联系客服反馈,我们会尽快为您处理(人工客服工作时间:9:00-18:30)。
起重机主梁上拱度计算方法
传统检测法有:“水准仪”检测法,包括吊钩检测法、塔尺检测法两种;测距仪法。
由于受电动单梁起重机主梁结构、小车行程止挡限位及电动葫芦等多种因素的限制,对在用电动单梁起重机主梁上拱度的检验不管采用哪种检测方法,测量时所选取的跨度与起重机实际跨度或多或少都存在有一定的偏差。
有时(如采用吊钩法)这种偏差甚至会达
1〜2mm。
此时如果没有对所检测的主梁上拱度进行正确的修正,那么对检验结果的判定(特别是跨度较小时)很有可能会出现误判。
如:1台新安装的电动单梁起重机的实际跨度为
7.0m,而测量时所选取的跨度最大只能为 6.0m。
试载前所检测出的上拱度为 5.5mm。
根据
检验标准规定新安装的电动单梁起重机主梁上拱度应为(1〜1.4)S/1000,此时如果按跨度7.0m简单地按测量所选取的 6.0m跨度所对应的标准来直接判定所检测的数值时,可能会误判为该项目不合格,而实际上将检测数据经过跨度偏差修正后,其上拱度应为合格。
因为跨度的偏差与上拱值并非成线性关系,所以,对所测的上拱值如果不加以正确修正,那么其所检测的上拱值对检验结果的判定影响很大,甚至可能会出现误判。
如图1所示为起重机主梁检测示意图,检测时所需拱度尺寸为HE。
图1现场检验电动单梁起重机主梁示意图
1.主梁
2.电动葫芦
3.大车轨道
4.小车行程止挡装置
基于高精度全站仪与AC MES的现场检查方法如下: 现场测量得:AF、EF、CH
根据几何关系可计算得:
OE
AF2 EF2 \ 2EF
OH = 、0E2-CH 则:
HE =0E -OH
1、轨道测量参数
超高基准:左右两根钢轨中心之间的距离
基本轨距:左右两根钢轨表面以下16mn处内侧之间的距离;
棱镜常数/高度:轨道小车棱镜常数-34.4mm;
图4.1.2-1中心线、超高说明图
在直线段是平行于两根铁轨的,而在曲线段应该是平超高:两根铁轨表面中心线之间在竖直面内高差
SOik:fn<UtL
起重机轨道检测
中心线:轨距的一半,
行于曲线切线的。
2、起重机行车轨道自动检测系统一代效果图及实物图
图4.1.4-1轨道小车一代效果图
图4.1.4-2 轨道小车一代实物图
图4.1.4-3 轨道小车一代细节图
图4.1.4-4 起重机行车轨道自动检测系统总图
3、测量流程
(一)勘测现场,明确测量的轨道;
(二)选择合适位置安装轨道小车;
对于精调测量的工作距离,建议10-360m,有效工作距离350m最远不要超过400m否则难保证测量精度,尤其是高程精度。
(三)安装全站仪基座,架设全站仪,并进行基准定位;
1、通常来说,全站仪安置于轨道小车有固定棱镜一侧,架设于线路的外轨(高轨)正上方,且保证全站仪架设高度尽量低;直线段高低轨参考下一段大里程方向曲线段。
2、全站仪即可架设在大里程端,也可架设在小里程端;
3、全站仪与小车棱镜同侧是保证线路平面精度;
4、全站仪架设高度尽量低是保证线路高程精度;
(四)启动采集软件,遥控轨道小车动作;
(五)记录相关数据,生成分析报表并输出;
4、起重机行车轨道自动检测系统性能参数
测量精度:±1.0mm;
工作温度:-10C - 50E
测量范围:0.5米-600米
精准范围:10米-360米
小车重量:6.8公斤
工作时长:16小时
待机时长:25天
遥控器时长:180天
遥控半径:750米
左、右轨向(10米弦)示值误差:±1.0mm;左、右高低(10米弦)示值误差:±1.0mm;轨距测量范围:1410mm〜1470mm;
轨距变化率示值误差:0.5%。
;
轨距示值误差:±0.5mm;
水平及超高测量范围:200mm;
水平及超高示值误差:±0.5mm;
里程示值误差:±5% ;。