起重机主梁上拱度计算方法
起重机主梁上拱度和悬臂上翘度的测量方法

△f 测起重机主梁上拱度和悬臂上翘度的测量方法1. 测量条件:室内起重机应水平放置,并无强辐射和热源影响;室外起重机应水平放置,并无风、无日照。
当测量时,有日照影响,其实测上拱值应为测得的上拱值减去附表 2.1 的修正值。
2. 上拱度应在跨中 S/10 区域内测量;悬臂上翘度应在悬臂全长处及最大有效悬臂处分别测量(后者为与测下挠度值。
3. 计算上拱度值或上翘度值的基准点。
当采用电动单梁起重机时,应为两侧大车车轮中 心向跨内约 500~600mm 处确定的基准点;当采用通用桥式起重机及通用门式起重机时, 应为主梁上翼缘板的测量线与大车轮中心铅垂线的交点。
4. 当有条件时,可以用经纬仪、水准仪等测标高的方法进行基准线测量,亦可以张紧的钢丝进行基准测量。
5. 测量时,宜清除小车自重的影响。
6. 电动单梁起重机主梁跨中上拱度的测量(附图 2,应采用 15kg 的重锤将直径为ф0.49~ф0.52m m 的钢丝拉好(附图 2,测出上拱度测量值△F 测。
上拱值应按下式计算:F=△F 测-△g (附 2.1)式中: F ---△F 测 ----上拱度测量值(mm );△ g ---正值(,可按附表 2.2 取值。
起重机械作业指导书附表2.1 测量上梁上拱度的日照温度差扣除值注:①上翼板的温度应在主梁中段位置的横筋板之间、受阳面轨道侧附近测量;②下翼缘板的温度应在主梁中段位置两横筋板之间、翼缘板中心位置测量;③对起重量为30~50t的起重机,表中数值应乘以0.85;④非标准跨度的起重机,可以用比例插入法计算。
附表2.2 测量跨中上拱度时钢丝下垂修正值△g7.通用桥式起重机主梁跨中上拱度的测量(附图2.2),应用15kg 的重锤将直径为φ0.49~φ0.52mm 的钢丝绳按附图 2.2 拉好,钢丝位置在主梁上翼缘板宽度中心,当已铺好轨道时,钢丝可稍偏离宽度中心,并宜避开轨道压板,再将两根长度为h 的等高棒于端梁中心处并垂直于端梁,测量出主梁在跨中横筋板处的上翼缘板表面与钢丝间的距离,找出拱度最高点即为上拱度检测值 h1,上拱度测量结果应按下式计算:(附2.2)F=h-h1- △g式中:F结果(;h1---(;h--至钢丝间距离△g影响值(。
起重机主梁上拱度计算方法

起重机主梁上拱度计算方法拱度计算的基本原理:主梁的拱度计算是基于静力平衡原理和材料力学原理。
主梁在负荷作用下会发生弯曲,导致拱度产生。
主梁的拱度可以通过弯矩和横向力的平衡计算得出。
弯曲计算方法:1.分析负荷:首先需要分析主梁所承受的负荷,包括自重、荷载和冲击荷载等。
负荷的大小和分布方式对主梁的弯曲变形有直接影响。
2.计算支反力:在计算主梁的拱度之前,需要先确定主梁的支反力。
支反力的计算可以根据静力平衡法和等效条件法来进行。
3.计算弯矩:弯曲计算的关键是计算主梁上的弯矩。
弯矩可以通过结构力学方程和静力平衡方程进行计算。
4.计算曲率半径:曲率半径是衡量主梁弯曲程度的指标。
曲率半径可以通过弯矩和剪力的关系以及截面矩量和剪力量的计算得出。
5.计算拱度:拱度计算的最终目标是计算主梁上各个截面的拱度。
拱度的计算可以通过弯矩和曲率半径的公式计算得出。
工程实例:以一座起重机主梁为例,该主梁的长度为15米,宽度为2米,厚度为0.2米。
主梁所承受的负荷为10吨,负荷集中在主梁的中间点。
弯曲计算的目标是计算主梁中间点的拱度。
1.分析负荷:主梁的负荷为10吨,集中在主梁的中间点。
2.计算支反力:根据静力平衡法,主梁的支反力为负荷的一半,即5吨。
3.计算弯矩:主梁的弯矩可以通过结构力学方程和静力平衡方程得出。
根据梁的弯曲理论,主梁的弯矩为M=(P*h)/4,其中P为负荷,h为主梁高度。
代入数值可得M=(10*5)/4=12.5吨米。
4.计算曲率半径:曲率半径可以通过弯矩和剪力的关系以及截面矩量和剪力量的计算得出。
对于矩形截面的主梁,曲率半径R可以通过公式R=M/(W*D^2)来计算,其中W为主梁宽度,D为主梁厚度。
代入数值可得R=12.5/(2*0.2^2)=312.5米。
5.计算拱度:拱度的计算可以通过弯矩和曲率半径的公式计算得出。
拱度d可以通过公式d=(M/R)*(L/2)^2来计算,其中L为主梁长度。
代入数值可得d=(12.5/312.5)*(15/2)^2=7.5毫米。
起重机主梁上拱度检验技术初探

起重机主梁上拱度检验技术初探起重机主梁是起重机的重要组成部分,负责承载和传递起重物品的重量。
主梁的安全可靠性对起重机的正常运行起到至关重要的作用。
拱度是主梁的重要指标之一,它反映了主梁在负荷作用下的强度和刚度。
本文将初步探讨起重机主梁拱度的检验技术。
起重机主梁的拱度检验主要有两种方法:传统的测量与新型的无损检测技术。
传统的测量方法是通过直观观察和测量工具来判断主梁的拱度。
可以通过肉眼观察梁的弯曲情况,如果主梁呈现明显的弯曲,则需要进一步进行测量分析。
可以使用水平仪来检测主梁的水平度,如果水平仪呈现明显的倾斜,则说明主梁存在拱度。
可以使用测量工具,如测量尺、拉线等来精确地测量主梁的上下距离和下凹程度。
通过这些测量,可以进一步评估主梁的拱度情况。
传统的测量方法存在一些缺点。
需要人工进行测量,测量结果受个人主观因素的影响,可能存在误差。
传统测量方法相对复杂,需要耗费较多的时间和人力成本。
最重要的是,传统方法只能获得局部的拱度情况,对整个主梁的拱度评估有一定的局限性。
为了克服传统方法的不足,新型的无损检测技术应运而生。
其中一种主要技术是应变测量。
应变测量利用变形传感器将主梁受力时的变形转化为电信号进行测量和分析。
通过在主梁上布置应变测量点,可以实时监测主梁的应变情况。
当主梁受到外力作用时,应变测量点会产生相应的应变信号,通过对信号的处理和分析,可以得到主梁的实时应变情况,进而评估主梁的拱度。
相比传统方法,无损检测技术具有测量结果准确、检测速度快、操作简单等优点。
而且,该技术可以实时监测主梁的应变情况,有助于及时发现和解决主梁拱度问题,提高起重机的安全可靠性。
起重机主梁的拱度是影响起重机安全可靠性的重要因素。
传统的测量方法和新型的无损检测技术是常用的主梁拱度检验方法。
传统方法通过测量工具和肉眼观察来评估主梁的拱度,但存在测量结果不准确、人力成本高等问题。
而无损检测技术利用应变测量进行实时监测,具有准确、快速、简单等优点。
新旧国标-桥式起重机主梁上拱度验收标准对比

新旧国标-桥式起重机主梁上拱度验收标准对比 GB/T14405-2011是2011年修订的《通用桥式起重机》国家标准,与GB/T14405-1993版相比有较大的改变。
现仅就对桥式起重机主梁的上拱度的检验验收标准及其如何满足标准要求进行分析对比,来加强对就GB/T14405-2011版的技术标准的理解。
GB/T14405-1993版标准关于桥式起重机主梁上拱度的描述为: 桥架在运行机构组装完成以后,主梁应有上拱,跨中上拱度应为(0.9-1.4)S/1000(S为主梁跨度),且放大上拱应:应控制在跨中的S/10范围内。
这项要求是制作后出厂前的验收条件。
在静载试验时,起升机构按1.25Gn(Gn为起重机的额定起重重)加权,超升离地面100mm-200mm高度处,悬空时间不少于10分钟,重复三次。
卸才先后,小车开至跨端,检查主梁实有上拱度应不小子0.7S/1000。
GB/T14405-2011版标准关于桥式起重机主梁上拱度的描述为: 起重机在做完静载试验时,应能承受1.25 Gn的试验载荷,主梁不应有永久变形。
静载试验后的主梁,当空载小东在极|破位置时,上拱最高点应在跨度中部S/10范围内,其值不应小于O.7S/1000。
显然GB/TI4405-2011版标准与GB/T14405-1993版标准关于桥架桥式起重机主梁上拱度拱度的要求的区别在于,GB/TI4405-2011版标准没有对组装后的桥式起重机主梁的上拱皮直接提出验收条件,而是对静载试验后提山了上拱度的要求。
在GB/T14405-1993标准应用过程中,生产现场为达到标准要求,通常采取的措施是,第一,质检方面综合各种因素按桥式起重机主梁跨度分成两个区段对上拱度制定验收标准,即S≤9.5m时,主梁上拱度按(1.2-1.4)S/1000验收,当S>19.5m时,主梁上拱度核(1.4-1.6)S/1000验收。
第二,腹板下料前生产班组对腹板的上拱度再增加一个附加值,经过焊接等过程后确保上拱度达到检验要求。
桥(门)式起重机主梁挠度的检测
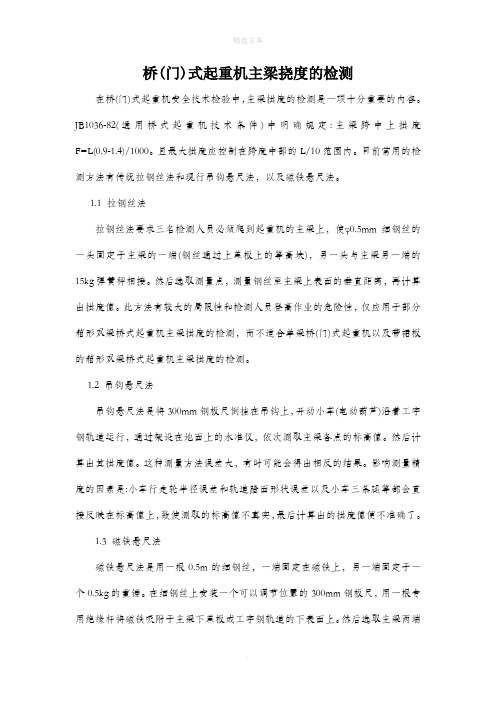
桥(门)式起重机主梁挠度的检测在桥(门)式起重机安全技术检验中,主梁拱度的检测是一项十分重要的内容。
JB1036-82(通用桥式起重机技术条件)中明确规定:主梁跨中上拱度F=L(0.9-1.4)/1000。
且最大拱度应控制在跨度中部的L/10范围内。
目前常用的检测方法有传统拉钢丝法和现行吊钩悬尺法,以及磁铁悬尺法。
1.1 拉钢丝法拉钢丝法要求三名检测人员必须爬到起重机的主梁上,使φ0.5mm细钢丝的一头固定于主梁的一端(钢丝通过上盖板上的等高块),另一头与主梁另一端的15kg弹簧秤相接。
然后选取测量点,测量钢丝至主梁上表面的垂直距离,再计算出拱度值。
此方法有较大的局限性和检测人员登高作业的危险性,仅应用于部分箱形双梁桥式起重机主梁拱度的检测,而不适合单梁桥(门)式起重机以及带裙板的箱形双梁桥式起重机主梁拱度的检测。
1.2 吊钩悬尺法吊钩悬尺法是将300mm钢板尺倒挂在吊钩上,开动小车(电动葫芦)沿着工字钢轨道运行,通过架设在地面上的水准仪,依次测取主梁各点的标高值。
然后计算出其拱度值。
这种测量方法误差大,有时可能会得出相反的结果。
影响测量精度的因素是:小车行走轮半径误差和轨道踏面形状误差以及小车三条腿等都会直接反映在标高值上,致使测取的标高值不真实,最后计算出的拱度值便不准确了。
1.3 磁铁悬尺法磁铁悬尺法是用一根0.5m的细钢丝,一端固定在磁铁上,另一端固定于一个0.5kg的重锤。
在细钢丝上安装一个可以调节位置的300mm钢板尺,用一根专用绝缘杆将磁铁吸附于主梁下盖板或工字钢轨道的下表面上。
然后选取主梁两端和梁中三个测量点,通过架设在地面上的水准仪读取被磁铁悬挂标尺上的数值,从而计算出主梁跨中的拱度值。
即主梁跨中拱度值=跨中标高值-1/2(较高端跨端标高值+较底端跨端标高值)。
钢板尺正向固定于细钢丝上,测得结果是正值时为上拱,反之为下挠。
利用此法可检测各种型式起重机主梁拱度,方法简捷,结果准确,省时省力。
门式起闭机主梁上拱度确定与修复焊接变形的生产工艺改进

门式起闭机主梁上拱度确定与修复焊接变形的生产工艺改进【摘要】主要讲述了轨道梁起拱目的,设计上拱度与制造上拱度的确定,制造起拱方法。
轨道梁焊接弯曲变形后的修复方法介绍。
【关键词】上拱度;上拱曲线;焊接弯曲变形;修复方法0 概述由我公司设计与生产制造QM2X1250/650KN大跨度门式起闭机的结构形式:轨道梁为偏轨T型钢与腹板、翼板组合箱形梁,主梁结构重37.23吨,长度为17500mm、双轨距为9500mm、主梁腹板高1860mm、厚度为14mm,翼板宽2300mm、厚度为20mm,在腹板压力区布置2道纵向加劲杆,在全跨布置有横向大隔板9块,腹板压力区有8块小隔板,材质为:Q345B。
1 技术要求1.1 按GB/T14406《通用门式起重机》和JB6128《水电站门式起重机》的要求制造和检验1.2 主梁腹板、翼板拼接板的对接焊缝接头应错开300mm以上,对接焊缝质量射线检测按GB3323规定的II级,超声波检测按GB11354的BI级1.3 主梁水平弯曲≤5.6mm,主梁腹板垂直偏斜≤9.3mm1.4 主梁主腹板的波浪度在离盖板960mm以内的区域≤9.8mm,其余区域≤16mm1.5 门架主梁安装后跨中上拱度13.1-20.3mm,且最大拱度应控制在跨中1.5m范围内1.6 主梁轨道下腹板、翼板采用T型钢和腹板、翼板对接组成箱形梁2 生产工艺中的难题2.1 上拱度确定中的难题2.1.1 起拱目的当启闭机吊起闸门行走并加上启闭机自重和轨道梁自重的作用下,轨道梁产生垂直的弹性下挠弯曲变形,使轨道梁产生坡度。
大跨度时,由于坡度会增加启闭机的运行阻力和消耗动力。
甚至有时在制动时,会产生打滑现象或停机后会发生自滑现象。
主梁及轨道梁起拱的目的就是为了避免或减少启闭机运行的阻力和打滑与自滑现象的发生,从而保证启闭机的安全运行。
2.1.2 上拱度要求:根据图中设计要求上拱度Fs要求为13.1-20.3mm。
2.1.3 传统的起拱方法在以往的生产施工中,大跨度的箱型梁的起拱方法的确定,往往是比较困难的。
桥式起重机主梁上拱度测量值的修正

维普资讯
围内的测 量盲 区 ,从 而无 法准 确测 量起 重机 主 梁 的
主梁 2 端标高的平均值与主梁中间标高的差计算得
到上 拱度 值 ,如 图 1 所示 ,则为 F=厂 ( ) 一 [ f
上拱 度值 。 ()小 车重 量影 响的 修正 :在 测量 过程 中 ,将 2 小 车开 至起 重机 端梁 一侧 ,减 小小 车 重量 的影 响 。 小 车 车身结 构 影响 的修 正 :以起 重机 的跨 度 为 横 坐标 , 以上 拱 度 标 高 测 量 值 为 纵 坐标 建 立 坐标 系 ,如 图 1 所示 。测 量点 分 别 为 a ,C ,e等 ,b ,d ( 可根 据 计 算 方 法 的需 要 确 定 测 量 点 的 多 少 ) ,设
小到一定程度 ,起重机就需要维修或者报废 ,所 以
在 其他 条件 一定 的情 况下 ,上拱 度值 是否合 理 、是
否得到保证 ,直接关 系到起重机的使用寿命。所以 在使用过程中要随时关注此参数的变化 ,出现问题
及时解 决 ,以保 障起重 作业 安全 。 实 际 工作 中测 量 值 与真 实 值 不 可能 完 全 一致 , 而 是存在 一 定 的偏 差 ,并 且误 差是 不 可避免 的。 当
维普资讯
桥 式 起 重 机 主 梁 上 拱 度 测 量 值 的修 正
淄博齐泰安全技术评价有限公 司 周洪沛
按照 国家 相关 标准 的要求 ,桥 式起重 机 主梁 需 设置 一 定 的上 拱 度值 ,其 主要 目的是 为 了提 高起 重 用 2等高 块 ( 度 为 日 放 置在 主 梁 与 端 梁 联 高 接 处上 盖板 中心 的位 置 ,用 直 径 为 04 05 a .9 .2nn i 的钢 丝 ,一端 固定 在起 重机 端梁 上绕 过 2 高块 端 等 另一 端用 弹簧 称 拉 紧 ,拉 力为 10N,侧 量跨 中 . 5 s / 1 最 高点 与钢丝 之 间 的距 离 日 。 0处
起重机主梁上拱度计算公式

起重机主梁的拱度计算可以基于梁的几何形状和应力分析进行估算。
下面是一个常用的起重机主梁拱度计算的近似公式,基于简化的梁理论:δ = (5 * w * L^4) / (384 * E * I)其中:δ 是主梁的最大拱度(单位:米)w 是主梁上的均布载荷(单位:牛顿/米)L 是主梁的跨度(单位:米)E 是主梁材料的弹性模量(单位:帕斯卡)I 是主梁的截面惯性矩(单位:米^4)这个公式基于简化的梁理论假设,适用于较细长、小拱度的主梁。
如果主梁具有复杂的截面形状或非均布载荷,需要考虑更复杂的分析方法和有限元分析等工具来获得更精确的拱度计算结果。
此外,根据不同国家和地区的规范和标准,可能会有特定的拱度限制和计算方法。
因此,在实际工程中,建议参考适用的规范和标准,并咨询专业工程师进行具体的拱度计算和设计。
在继续计算起重机主梁拱度之前,需要了解主梁的截面形状和材料属性。
截面形状可以是矩形、I型、H型或其他复杂形状,每种形状的截面惯性矩(I)的计算方法不同。
材料属性包括弹性模量(E),这是一个材料的力学特性,描述了材料在受力时的应变与应力之间的关系。
以下是几种常见主梁截面形状的截面惯性矩计算公式:矩形截面:对于矩形截面,截面惯性矩的计算公式为:I = (b * h^3) / 12 其中,b 是矩形截面的宽度,h 是矩形截面的高度。
I型截面:对于I型截面,截面惯性矩的计算公式为:I = (b1 * h1^3) / 12 + b1 * h1 * (h/2 + h1/2)^2 + (b2 * h2^3) / 12 + b2 * h2 * (h/2 + h2/2)^2 其中,b1、h1 是上部矩形的宽度和高度,b2、h2 是下部矩形的宽度和高度,h 是I型截面的总高度。
H型截面:对于H型截面,截面惯性矩的计算公式可以根据H型截面的具体几何参数进行推导或查阅相关资料得出。
计算得到截面惯性矩后,即可将其代入前面给出的拱度计算公式中,进而计算出起重机主梁的最大拱度。
- 1、下载文档前请自行甄别文档内容的完整性,平台不提供额外的编辑、内容补充、找答案等附加服务。
- 2、"仅部分预览"的文档,不可在线预览部分如存在完整性等问题,可反馈申请退款(可完整预览的文档不适用该条件!)。
- 3、如文档侵犯您的权益,请联系客服反馈,我们会尽快为您处理(人工客服工作时间:9:00-18:30)。
起重机主梁上拱度计算方法
传统检测法有:“水准仪”检测法,包括吊钩检测法、塔尺检测法两种;测距仪法。
由于受电动单梁起重机主梁结构、小车行程止挡限位及电动葫芦等多种因素的限制,对在用电动单梁起重机主梁上拱度的检验不管采用哪种检测方法,测量时所选取的跨度与起重机实际跨度或多或少都存在有一定的偏差。
有时(如采用吊钩法)这种偏差甚至会达1~2mm。
此时如果没有对所检测的主梁上拱度进行正确的修正,那么对检验结果的判定(特别是跨度较小时)很有可能会出现误判。
如:1台新安装的电动单梁起重机的实际跨度为7.0m,而测量时所选取的跨度最大只能为6.0m。
试载前所检测出的上拱度为5.5mm。
根据检验标准规定新安装的电动单梁起重机主梁上拱度应为(1~1.4)S/1000,此时如果按跨度7.0m简单地按测量所选取的6.0m跨度所对应的标准来直接判定所检测的数值时,可能会误判为该项目不合格,而实际上将检测数据经过跨度偏差修正后,其上拱度应为合格。
因为跨度的偏差与上拱值并非成线性关系,所以,对所测的上拱值如果不加以正确修正,那么其所检测的上拱值对检验结果的判定影响很大,甚至可能会出现误判。
如图1所示为起重机主梁检测示意图,检测时所需拱度尺寸为HE。
图1 现场检验电动单梁起重机主梁示意图
1.主梁
2.电动葫芦
3.大车轨道
4.小车行程止挡装置
基于高精度全站仪与AC MES 的现场检查方法如下:
现场测量得:AF 、EF 、CH
根据几何关系可计算得: ()
EF EF AF OE 22
2+= 22CH OE OH -=
则:
OH OE HE -=
起重机轨道检测
1、轨道测量参数
超高基准:左右两根钢轨中心之间的距离
基本轨距:左右两根钢轨表面以下16mm处内侧之间的距离;
棱镜常数/高度:轨道小车棱镜常数-34.4mm;
图4.1.2-1 中心线、超高说明图
中心线:轨距的一半,在直线段是平行于两根铁轨的,而在曲线段应该是平行于曲线切线的。
超高:两根铁轨表面中心线之间在竖直面内高差。
2、起重机行车轨道自动检测系统一代效果图及实物图
图4.1.4-1 轨道小车一代效果图
图4.1.4-2 轨道小车一代实物图
图4.1.4-3 轨道小车一代细节图
图4.1.4-4 起重机行车轨道自动检测系统总图
3、测量流程
(一)勘测现场,明确测量的轨道;
(二)选择合适位置安装轨道小车;
对于精调测量的工作距离,建议10-360m ,有效工作距离350m;最远不要超过400m,否则难保证测量精度,尤其是高程精度。
(三)安装全站仪基座,架设全站仪,并进行基准定位;
1、通常来说,全站仪安置于轨道小车有固定棱镜一侧,架设于线路的外轨(高轨)正上方,且保证全站仪架设高度尽量低;直线段高低轨参考下一段大里程方向曲线段。
2、全站仪即可架设在大里程端,也可架设在小里程端;
3、全站仪与小车棱镜同侧是保证线路平面精度;
4、全站仪架设高度尽量低是保证线路高程精度;
(四)启动采集软件,遥控轨道小车动作;
(五)记录相关数据,生成分析报表并输出;
4、起重机行车轨道自动检测系统性能参数
测量精度:±1.0mm;
工作温度:-10℃- 50℃
测量范围:0.5米- 600米
精准范围:10米- 360米
小车重量:6.8公斤
工作时长:16 小时
待机时长:25天
遥控器时长:180天
遥控半径:750米
左、右轨向(10米弦)示值误差:±1.0mm;左、右高低(10米弦)示值误差:±1.0mm;
轨距测量范围:1410mm~1470mm;
轨距变化率示值误差:0.5‰;
轨距示值误差:±0.5mm;
水平及超高测量范围:200mm;
水平及超高示值误差:±0.5mm;
里程示值误差:±5‰;。