3金属旋压工艺详解
浅探金属旋压加工工艺
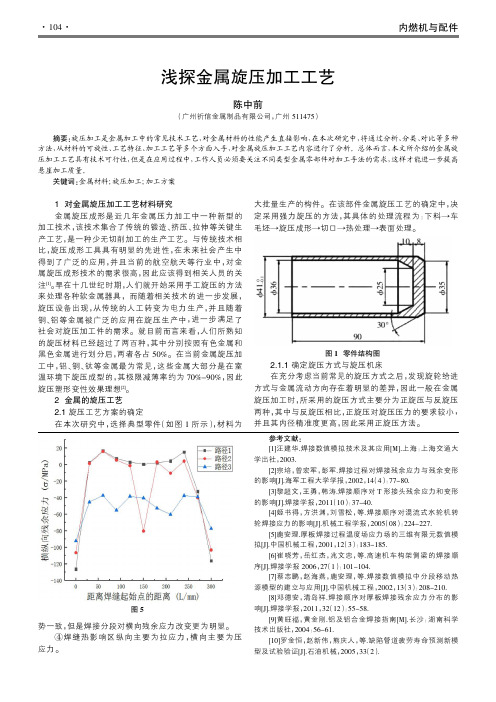
毛坯→旋压成形→切口→热处理→表面处理。
图1零件结构图
2.1.1确定旋压方式与旋压机床
在充分考虑当前常见的旋压方式之后,发现旋轮给进方式与金属流动方向存在着明显的差异,因此一般在金属旋压加工时,所采用的旋压方式主要分为正旋压与反旋压两种,其中与反旋压相比,正旋压对旋压压力的要求较小,并且其内径精准度更高,因此采用正旋压方法。
势一致,但是焊接分段对横向残余应力改变更为明显。
④焊缝热影响区纵向主要为拉应力,横向主要为压应力。
参考文献:
[1]汪建华.焊接数值模拟技术及其应用[M].上海:上海交通大学出社,2003.
[2]宗培,曾宏军,彭军.焊接过程对焊接残余应力与残余变形的影响[J].海军工程大学学报,2002,14(4):77-80.
[3]黎超文,王勇,韩涛.焊接顺序对T形接头残余应力和变形的影响[J].焊接学报,2011(10):37-40.
[4]姬书得,方洪渊,刘雪松,等.焊接顺序对混流式水轮机转轮焊接应力的影响[J].机械工程学报,2005(08):224-227. [5]鹿安理.厚板焊接过程温度场应力场的三维有限元数值模
图5
在上述公式中,
长度;t0代表筒底厚度,
在毛坯设计中,
现严重的厚度变化问题,。
简述旋压成型的工艺流程
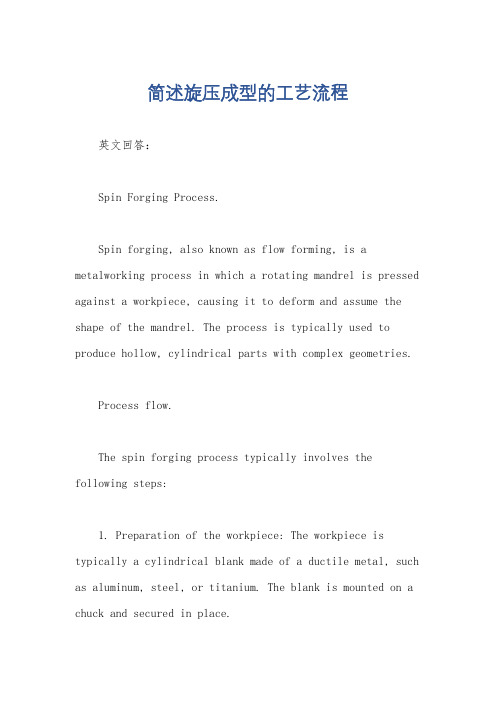
简述旋压成型的工艺流程英文回答:Spin Forging Process.Spin forging, also known as flow forming, is a metalworking process in which a rotating mandrel is pressed against a workpiece, causing it to deform and assume the shape of the mandrel. The process is typically used to produce hollow, cylindrical parts with complex geometries.Process flow.The spin forging process typically involves the following steps:1. Preparation of the workpiece: The workpiece is typically a cylindrical blank made of a ductile metal, such as aluminum, steel, or titanium. The blank is mounted on a chuck and secured in place.2. Mandrel selection: The mandrel is a cylindrical tool with the desired shape of the finished part. The mandrel is typically made of a hard material, such as tool steel or carbide.3. Lubrication: A lubricant is applied to the workpiece and mandrel to reduce friction and prevent galling.4. Spinning: The workpiece is rotated at a high speed while the mandrel is pressed against it. The force of the press causes the workpiece to deform and flow around the mandrel.5. Forming: The workpiece is gradually formed into the desired shape as the mandrel is moved along its length.6. Cooling: After the workpiece is formed, it is cooled to room temperature.7. Trimming: Any excess material is trimmed from the workpiece.Advantages of spin forging.Spin forging offers several advantages over other metalworking processes, including:High precision: Spin forging can produce parts with very precise dimensions and tolerances.Complex geometries: Spin forging can be used to produce parts with complex geometries that would be difficult or impossible to produce using other methods.High strength: Spin forging can produce parts with high strength and durability.Low cost: Spin forging is a relatively low-cost process, especially for high-volume production.Applications of spin forging.Spin forging is used in a variety of industries,including:Automotive: Spin forging is used to produce a varietyof automotive components, such as wheels, gears, and shafts.Aerospace: Spin forging is used to produce aerospace components, such as engine casings and fuel tanks.Medical: Spin forging is used to produce medical implants, such as bone screws and artificial joints.Electronics: Spin forging is used to produceelectronic components, such as heat sinks and connectors.中文回答:旋压成型工艺流程。
金属旋压成形工艺课件

8)金属旋压与板材冲压相比较,金属旋压能大大简化 工艺所使用的装备,一些需要多次冲压的制件,旋压一 次即可制造出来。
中国兵器工业集团第五五研究所
中国兵器工业集团第五五研究所
3/11/2021
16
中国兵器工业集团第五五研究所
二、普通旋压成形技术
1)从上图可看出 未成形区①的凸缘坯料与旋轮型面Ι接触,,产生
拉伸变形,坯料承受轴向拉应力,切向和径向压 应力,呈两向压缩、一向拉伸的体积应变状态。
变形区②的坯料与旋轮圆角Ⅱ及芯模接触,产生 扎压与弯曲变形。承受轴向拉应力,切向压应力 ,厚度方向有压应力σr,呈一向拉伸、两向压缩 的体积应变状态。
按照旋压件的形状特点,旋压工艺可分为筒形件旋压和异形件旋压两 类。由于旋压件都是在其自身的旋转运动中成形的,因此所有的旋压 件都是旋转体零件,例外的只是旋出母线的形状及其与旋转轴线的相 互位置关系不同而已。
由于旋压设备的自动化程度的不断提高,旋压工艺技术的不断改进, 使得旋压技术在原有基础上又派生出了多种旋压成型方法,例如:超 声波旋压法、通用芯模旋压法、斜扎式旋压法、多旋轮的错距旋压法 、劈开旋压法、射流旋压法等。
提高进给比可以提高效率,但对初期道次需相应 减小起旋点仰角,以防止起皱。减小进给比有助 于改善表面粗糙度,过小进给比易造成局部减薄 ,不贴膜。采用反推辊时适当加大进给比可防止 坯料减薄过多,常用进给比f=0.5~3.0mm/r。
中国兵器工业集团第五五研究所Biblioteka 3/11/202123
二、普通旋压成形技术
5)制品范围广。普通旋压可以成形出球形、椭球形、 曲母线形、杯形、锥形及变截面带台阶的异形薄壁回转 体零件。
铁锅旋压工艺
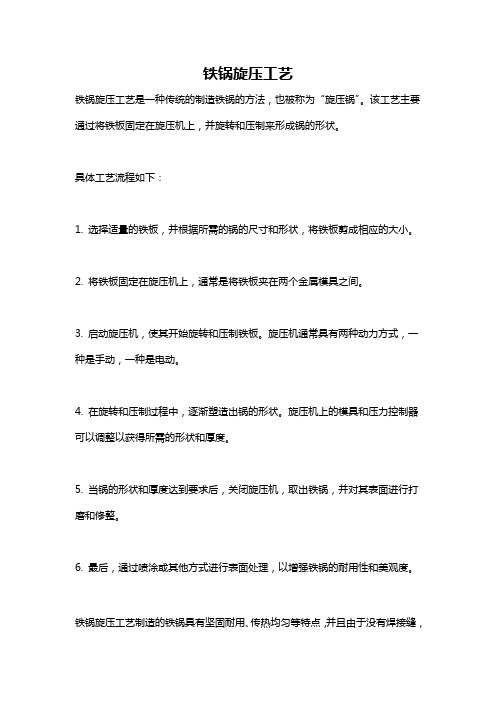
铁锅旋压工艺
铁锅旋压工艺是一种传统的制造铁锅的方法,也被称为“旋压锅”。
该工艺主要通过将铁板固定在旋压机上,并旋转和压制来形成锅的形状。
具体工艺流程如下:
1. 选择适量的铁板,并根据所需的锅的尺寸和形状,将铁板剪成相应的大小。
2. 将铁板固定在旋压机上,通常是将铁板夹在两个金属模具之间。
3. 启动旋压机,使其开始旋转和压制铁板。
旋压机通常具有两种动力方式,一种是手动,一种是电动。
4. 在旋转和压制过程中,逐渐塑造出锅的形状。
旋压机上的模具和压力控制器可以调整以获得所需的形状和厚度。
5. 当锅的形状和厚度达到要求后,关闭旋压机,取出铁锅,并对其表面进行打磨和修整。
6. 最后,通过喷涂或其他方式进行表面处理,以增强铁锅的耐用性和美观度。
铁锅旋压工艺制造的铁锅具有坚固耐用、传热均匀等特点,并且由于没有焊接缝,
减少了可能出现漏气的可能性。
该工艺在许多地方都有应用,尤其受到传统厨具制造业的青睐。
铝旋压生产工艺流程

铝旋压生产工艺流程
一、材料准备阶段
1.确定铝板规格
(1)根据产品要求选择合适规格的铝板(2)确认铝板厚度和尺寸
2.表面处理
(1)清洁铝板表面
(2)去除氧化层
二、模具设计与制作
1.确定产品图纸
(1)设计产品结构和尺寸
(2)确认旋压成型要求
2.制作旋压模具
(1)加工模具结构
(2)确保模具精度
三、旋压成型
1.装夹铝板
(1)将铝板固定在旋压机上
(2)调整夹紧力和位置
2.旋压成型
(1)控制旋压速度和压力
(2)确保成型质量
四、表面处理
1.喷涂涂层
(1)选择合适的涂层类型
(2)控制喷涂厚度和均匀度
2.表面抛光
(1)进行表面打磨处理
(2)确保表面光洁度
五、检测与质量控制
1.外观检测
(1)检查成型产品外观
(2)发现缺陷及时修复
2.尺寸测量
(1)使用测量工具进行尺寸检测(2)确保产品尺寸符合要求六、包装与出库
1.包装
(1)选择合适包装材料(2)包装产品并标识2.出库
(1)检查产品质量(2)完成出库手续。
旋压技术

旋压技术基本概念金属旋压技术的基本原理相似于古代的制陶生产技术。
旋压成型的零件一般为回转体筒形件或碟形件,旋压件毛坯通常为厚壁筒形件或圆形板料。
旋压机的原理与结构类似于金属切削车床。
在车床大拖板的位置,设计成带有有轴向运动动力的旋轮架,固定在旋轮架上的旋轮可作径向移动;与主轴同轴联接的是一芯模(轴),旋压毛坯套在芯模(轴)上;旋轮通过与套在芯模(轴)上的毛坯接触产生的摩擦力反向被动旋转;与此同时,旋轮架在轴向大推力油缸的作用下,作轴向运动。
旋轮架在轴向、旋轮在径向力的共同作用下,对坯料表面实施逐点连续塑性变形。
在车床尾顶支架的位置上,设计成与主轴同一轴线的尾顶液压缸,液压缸对套在芯模(轴)上的坯料端面施加轴向推力。
旋压成型有普通旋压和强力旋压成型两种。
不改变坯料厚度,只改变坯料形状的旋压叫普通旋压成型;即改变坯料厚度,又改变坯料形状的旋压叫强力旋压成型。
强力旋压成型所需要的旋压力较大,旋压机的结构一般也较复杂。
强力旋压成型又依旋轮移动的方向与金属流动的方向,分为正旋和反旋。
旋轮移动的方向与金属流动的方向相同,叫正旋;反之,称为反旋。
同一种材料,反旋成型所需的旋压力较大。
采用哪种旋压方式成型,要依据零件的形状和工艺要求确定。
旋压机的选型由旋压工艺及多种成型工艺条件要求确定。
旋压机分强力旋压机和普通旋压机二大类型。
强力旋压机又分双旋轮和三旋轮。
还有用于特殊零件旋压的旋压机,如热旋压机、钢球旋压机等。
我国金属旋压成型技术的发展历史近四十年,而在国防工业的应用研究尤为广泛,研究应用水平很高,特别是在旋压成型工艺及装备方面,已经处于国内领先地位。
旋压机的设计和制造能力也很强。
旋压技术简介什么叫旋压技术,也叫金属旋压成形技术,通过旋转使之受力点由点到线由线到面,同时在某个方向给予一定的压力使金属材料沿着这一方向变形和流动而成型某一形状的技术。
这里,金属材料必须具有塑性变形或流动性能,旋压成形不等同塑性变形,它是集塑性变形和流动变形的复杂过程,特别需要指出的是,我们所说的旋压成形技术不是单一的强力旋压和普通旋压,它是两者的结合;强力旋压用于各种筒、锥体异形体的旋压成型壳体的加工技术,是一种比较老的成熟的方法和工艺,也叫滚压法。
金属旋压成型工艺及操作步骤
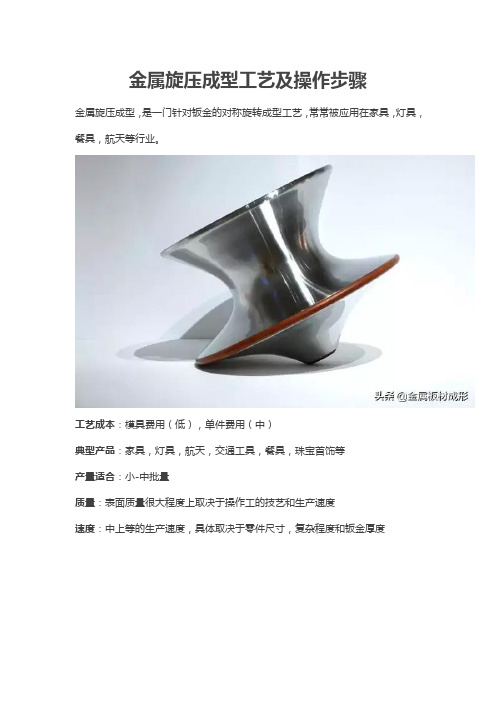
金属旋压成型工艺及操作步骤
金属旋压成型,是一门针对钣金的对称旋转成型工艺,常常被应用在家具,灯具,餐具,航天等行业。
工艺成本:模具费用(低),单件费用(中)
典型产品:家具,灯具,航天,交通工具,餐具,珠宝首饰等
产量适合:小-中批量
质量:表面质量很大程度上取决于操作工的技艺和生产速度
速度:中上等的生产速度,具体取决于零件尺寸,复杂程度和钣金厚度
适用材料
适用于温性金属板材,例如不锈钢,黄铜,铜,铝,钛等
设计考虑因素
1.金属旋压成型只适用于制造旋转对称的零件,最理想的形体为半球形薄壳金属零件
2.通过金属旋压成型的零件,内部直径应控制在2.5m之内
工艺图示
步骤1:将切割好的圆形金属板材固定在机器芯棒上
步骤2:芯棒带动圆形金属板材高速旋转,带有转轮的工具开始按压金属表面,直至金属板材完全贴合模具内壁成型
步骤3:成型完成后,芯棒被取出,零件的顶部和底部被切除以便脱模
实例1:灯罩的金属旋压成型(图)
步骤:
实例2:其他金属产品的旋压工艺。
1 旋压成形工艺及设备

(8)金属旋压法能制作超宽板材,其方法是将旋压的筒形 件沿母线方向切开展平。在国外能旋压Φ2m筒形件的旋 压机不算很大的设备,利用这样的设备很容易制造6m宽 的板材,但是采用传统的轧制方法要生产3m宽的板材就 需要相当大型的轧机。美国用旋压工艺制造出宽7.5m, 长9m的超宽板材。 (9)在旋压过程中,由于被旋压坯料近似逐点变形,因 此,其中任何夹渣、夹层、裂纹、砂眼等缺陷很容易暴 露出来。这样,旋压过程也附带起到了对制品检验作用。 (10)坯料来源广,可采用空心的冲压件,挤压件,铸件, 焊接件,机加工的锻件和轧制件以及圆板作坯料;并且, 能旋压钛、钼、钨、钽、铌一类难变形的金属及其合金。
直径(mm) 最大厚度(mm)
低碳钢 <1219 12.7 不锈钢或高 铝合金 金属钢 6.35 9.52 15.84 38.1 15.84 31.75 50.8 76.2
1219~1829 19.05 1829~3048 31.75 3048~4674 38.1
1.3 旋压技术的应用
(1)导弹、火箭、宇宙航行方面 美国在发展导弹、 火箭的初期,在制造超高强度轻质火箭发动机壳 体时,许多次失败都是由与焊缝有关的缺陷所引 起的。如形状的不连续性,强度降低,容易产生 脆裂以及应力集中等。这些缺陷随着材料厚度的 减薄,重量的轻型化及材料强度水平的提高变得 更加严重。随着导弹、火箭技术的发展对材料的 比强度提出更高的要求,减少火箭发动机壳体和 压力容器的焊缝是非常有益的。
(1)金属变形条件好,旋压时由于旋轮与金 属接触近乎点接触,因此接触面积小,单 位压力高,可达250~350kg/mm2以上, 因此旋压适于加工高强度难变形的材料。 而且,所需总变形力较小,从而使功率消 耗也大大降低。加工同样大小的制件,旋 压机床的吨位只是压力机吨位的 1/20左 右。
- 1、下载文档前请自行甄别文档内容的完整性,平台不提供额外的编辑、内容补充、找答案等附加服务。
- 2、"仅部分预览"的文档,不可在线预览部分如存在完整性等问题,可反馈申请退款(可完整预览的文档不适用该条件!)。
- 3、如文档侵犯您的权益,请联系客服反馈,我们会尽快为您处理(人工客服工作时间:9:00-18:30)。
4.焊接的毛坯 为了旋出大型锥形件、封头或筒形件等,由于轧制的板材 和管材不能满足尺寸要求,故采用平板拼焊成大型板坯, 或用长板料冷弯后焊成圆管坯。 5.经车削的铸造毛坯 强力旋压也有采用经车削的铸造毛坯。有些铸造毛坯经过 适当热处理可以冷旋压。这种铸件多为管状毛坯。 6.轧制或挤压的管坯 这类管坏经车削后,可旋压出等壁厚、变壁厚、带坯缘或 带筋的零件。 7.用粉末冶金法生产的毛坯 某些难熔金属及其合金(如钨、铜、锡及其合金)必须用粉末 冶金法和等静压法生产成毛坯,然后用热旋压法旋压成所 需的零件。 8.用圆锭作为毛坯 用圆锭料旋压一挤压成筒形件、锥形件和盆形件。
3.7 工艺装备的设计
3.7.1 主要工艺装备 3.7.1.1 旋轮 旋轮是旋压加工的主要工具之一,也是使旋压工艺取得 良好效果的一个重要影响因素。旋轮在工作时,承受巨 大的接触压力,剧烈的磨擦和一定的工作温度(尤其是加 热旋压时)。 旋轮设计得正确与否,将直接影响工件的成形质量和旋 压力的大小。旋轮工作部分的表面状况(形状尺寸,精度, 硬度和光洁度等)也直接地反映到工件的外表面上。因此, 对于旋轮的要求是具有足够的强度,刚度,硬度和耐热 性,合理的结构形状和尺寸精度以及良好的工作表面。 旋轮的具体结构,工作型面,表面状况及尺寸等均与旋 压机的类型,用途,被加工工件的材料,形状,尺寸及 其变形程度等有密切关系。
a) 普通旋压(拉伸旋压)用的 b)变通旋压与减薄旋压用的 c)、d) 普通旋压和滚压筋用的 e) 擀光表面用的
剪切旋压用旋轮的形状 D:300~500mm左右,h:50~175mm左右, W:50~75mm左右(给出的尺寸用于重型旋压)
筒形变薄旋压所用旋轮的形状
旋轮结构形式
轻型旋轮架结构
2.对毛坯尺寸精度要求 (1)毛坯壁厚偏差的影响 对于筒形件旋压成形,由于毛 坯壁厚偏差过大,会影响旋压件的直度,甚至会产生弯 曲现象。对于锥形件和曲母线形件,预制毛坯壁厚偏差 会使旋压过程不能严格按正弦规律进行,导致旋压件内 外精度降低,壁厚偏差增大,因此毛坯的壁厚偏差通常 应小于0.1mm。 (2)毛坯内径偏差 毛坯内径偏差过大,容易造成旋压件 的椭圆度和扩径。 (3)预制毛坯的椭圆度和毛坯不同部位的不同轴度 (4)毛坯底部与其轴线不垂直度 (5)毛坯与其芯模间的间隙 3.对毛坯材料性能均匀性的要求 毛坯的金相组织和应力分布不均匀,会使旋压中的毛坯 变形不均,从而使旋压件鼓包或断裂,使不同部位的材 料强度不相同。此外,旋压件尺寸精度会降低,椭圆度 会增长。
3.2 毛坯的种类及要求
1.平板坯 多用来旋压锥形件、双锥角形件、双向圆形锥形件、阶 梯圆锥件、曲母线形件、筒形件以及组合件等。 2.由平板坯预成形的毛坯 这种毛坯可通过普通旋压、冲压或其他成形加工方法得 到,多用来旋压成尖顶锥形件、曲母线锥形件、球形封 头和筒形件等。 3.经车削的锻造毛坯 为了旋出等壁厚零件,减轻零件的重量,使毛坯变形符 合应遵循的变形规律,变形程度不超过极限值,有时需 采用经车削加工的锻造毛坯。这种毛坯多用于旋压成母 线为抛物线或其他曲母线的等壁厚的零件。等壁厚球形 封头或筒形(管形)件等。
3.3 毛坯的设计计算
普通旋压的毛坯设计计算,可参考冲压拉 深中相应的计算公式,但因普通旋压过程 中有一定的延伸率(一般为3~5%),故普 通旋压的毛坯可比拉伸的毛坯稍小一些。 3.3.1 一般锥形件的毛坯计算
对于需多道次旋压的锥形件,毛坯余量应留大些, 对于旋压道次少的锥形件,毛坯余量留少一些。
3 金属旋压工艺
3.1 旋压工艺方案的选择 旋压工艺方案的选择是旋压加工中首先遇到的问 题。在旋压件生产任务确定之后,根据旋压件的 材料性质、结构形式、尺寸精度、表面质量、所 需设备性能和用途以及生产经济性等因素进行综 合考虑,选出最佳的旋压工艺方案。 3.1.1 旋压方式的选择 3.1.2 毛坯的处理 3.1.3 旋压设备的选用 3.2 毛坯的种类及要求 一、毛坯种类
二、对毛坯的要求 在旋压过程中,毛坯内部和表层的缺陷会被扩大, 因此对旋压用的毛坯有如下要求: 1.对毛坯内外层的要求 (1)毛坯内部不得有隔层、夹杂、裂纹和疏松等 缺陷,否则,旋压件易出现断裂、内裂及微裂等 缺陷。因此,有些大毛坯,有焊缝的毛坯要进行 探伤检查。 (2)毛坯表面不得有斑痕,加工印记、裂纹和毛 刺等缺陷,否则,旋压件表面会起鳞皮。在变形 量大的情况下,还会发生断裂。 (3)毛坯表面的污垢和鳞皮应除掉,以免压伤制 件和弄脏润滑剂。
3.5 旋压道次规范和旋轮运动轨迹
对于普通旋压而言,旋压道次规范取决于:旋轮沿毛坯 表面的进给量,道次间距△α,旋轮圆角半径和坯料机 械性能,相对厚比,以及旋轮所走的轨迹设计(对于仿形 旋压要进行仿形板型面设计,对于数控旋压设计出合理 的运行轨迹)。
3.6 金属旋压的润滑和冷却
旋压的润滑和其他塑性加工的润滑一样,目的在 于减小加工时的阻力,改善加工表面,增加工具 寿命,控制加工强度以及防止坯料表面与工具粘 着。在强力旋压中,若旋压后毛坯伸长,则可使 用润滑脂,石蜡、牛脂、皂基润滑脂等作为润滑 剂。对薄金属板以较小压力旋压时,可使用水溶 性油。若旋压中放出的热量很大,而需要很大的 加工力,则须分别考虑容易吸热和散热的冷却剂, 以及能减小摩擦力的润滑剂。
ห้องสมุดไป่ตู้
由板坯旋制的双锥角形件
由板坯旋制的双向锥形件
用板坯旋压不同壁厚与锥角的锥形件
用板坯旋制的曲母线形件
用不等厚度毛坯旋压的曲母线形件
3.4 旋压过程工艺参数的选择
合理的选择工艺参数是保证旋压成功的重要条件。旋压 过程中主要的工艺参数有:减薄率、主轴转速、进给量、 芯模和旋轮的间隙、旋轮安装角、旋压角度、旋压道次 规范、旋轮运动轨迹和旋轮的几何形状等。