配方因素对三元乙丙橡胶密封圈硫化胶性能的影响
配方设计与硫化胶物理性能的关系(doc8)

配方设计与硫化胶物理性能的关系配方设计与硫化胶物理性能的关系一.拉伸强度拉伸强度表征制品能够抵抗拉伸破坏的极限能力· 橡胶的拉伸强度:未填充硫化胶:聚氨酯橡胶PUR>天然橡胶NR/异戊IR>氯丁橡胶CR>丁基橡胶IIR>氯磺化聚乙烯CSM>丁晴橡胶NBR/氟橡胶FKM>顺丁橡胶BR>三元乙丙橡胶EPDM>丁苯橡胶SBR>丙烯酸酯橡胶ACM>氯醇橡胶CO>硅橡胶Q填充硫化胶:聚氨酯橡胶PUR>聚酯型热塑性弹性体>天然橡胶NR/异戊IR>SBS热塑性弹性体>丁晴橡胶NBR/氯丁橡胶CR>丁苯橡胶SBR/三元乙丙橡胶EPDM/氟橡胶FKM>氯磺化聚乙烯CSM>丁基橡胶IIR>顺丁橡胶BR/氯醇橡胶CO>丙烯酸酯橡胶ACM>硅橡胶Q在快速形变下,橡胶的拉伸强度比慢速形变时高;高温下测试的拉伸强度,远远低与室温下的拉伸强度.· 硫化体系的影响对常用的软质硫化胶而言,欲通过硫化体系提高拉伸强度时,应采用硫磺-促进剂的传统硫化体系,并适当提高硫磺用量.同时促进剂选用噻唑类如M,DM与胍类并用,并适当增加用量.· 填充体系的影响*填料的粒径越小,比表面积越大,表面活性越大,则补强效果越好.*结晶型(如天然橡胶)为基础的硫化胶,拉伸强度随填充剂用量增大,可出现单调下降. *非结晶型(如丁苯橡胶)为基础的硫化胶,拉伸强度随填充剂用量增大而增大,达到最大值,然后下降.*低不饱和度橡胶(如三元乙丙橡胶,丁基橡胶)为基础的硫化胶,拉伸强度随填充剂用量增大而增大,达到最大值后可以保持不变.*对热塑型弹性体而言,填充剂使其拉伸强度降低.*一般情况下,软质橡胶的碳黑用量在40-60份时,硫化胶的拉伸性能比较好.· 软化体系的影响总的来说,加入软化剂会降低硫化橡胶的拉伸强度.但软化剂数量不超过5份时,硫化橡胶的拉伸强度有可能增大.因为含有少量软化剂,可以使碳黑的分散效果好.*芳氢油对非极性的不饱和橡胶(异戊橡胶,顺丁橡胶,丁苯橡胶)硫化胶的拉伸强度影响小.用量5-15份*石蜡油对非极性的不饱和橡胶(异戊橡胶,顺丁橡胶,丁苯橡胶)硫化胶的拉伸强度影响大.*对极性的不饱和橡胶(如丁晴橡胶,氯丁橡胶),最好采用芳氢油和酯类软化剂(如DBP,DOP等)· 提高硫化胶拉伸强度的其他方法:*橡胶和某些树脂共混;如天然胶,丁苯橡胶和高苯乙烯树脂共混.天然胶和聚乙烯共混.丁晴橡胶和聚氯乙烯共混,乙丙橡胶与聚丙烯共混.*橡胶的化学改性.*填料的改性==>使用表面活性剂或偶联剂.二.撕裂强度是由于材料中的裂纹或裂口受力时迅速扩大开裂而导致破坏的现象.· 各种橡胶(硫化胶)的撕裂强度:天然橡胶NR>聚酯型热塑性弹性体>异戊橡胶IR>聚氨酯橡胶PUR>氯醇橡胶CO>丁晴橡胶NBR>丁基橡胶IIR>氯丁橡胶CR>氯磺化聚乙烯CSM>SBS热塑性弹性体>顺丁橡胶BR>丁苯橡胶SBR>三元乙丙橡胶EPDM>氟橡胶FKM>硅橡胶Q>丙烯酸酯橡胶ACM· 撕裂强度和硫化体系的关系:*撕裂强度和交联密度的关系有一个极大值,一般随交联密度的增加,撕裂强度增大,并出现一个极大值;然后随交联密度的增加,撕裂强度急剧下降.和拉伸强度类似,但最佳撕裂强度的交联密度不拉伸强度达到最佳值的交联密度要低。
橡胶制品的配方设计原理、配方设计与硫化物性的关系

橡胶制品的配方设计原理、配方设计与硫化物性的关系橡胶制品的配方设计原理 -一、橡胶的并用。
无论是什么橡胶不可能具有十全十美的性能,使用部门往往对产品提出多方面的性能要求,为了满足此目的,而采用橡胶并用的方法。
如,为提高二烯烃类橡胶耐热、耐光老化性能,可加入氯磺化聚乙烯。
丁睛橡胶的耐粙性很好,但耐寒性不好,若并用10%的天然胶,便可改善它的耐寒性。
在橡胶中并用高苯乙烯、改性酚醛树脂、三聚氰胺树脂等都可改善橡胶的补强性能。
合成橡胶的工艺性能一般都不够好,特别是饱和较高的合成橡胶,无论是炼胶、压延、贴合、硫化等性能都比较差,所以常加入天然橡胶或树脂。
以改善其未硫化胶的加工性能。
如,丁苯橡胶加入5-20份低压聚乙烯,可减少丁苯橡胶的收缩率。
乙丙橡胶中加入酚醛树脂可提高粘性。
加入天然胶对一般合成橡胶的工艺性能都会有所改善。
为了改进工艺加工性能,并用天然胶或树脂的比例一般都在20%以下。
有些合成橡胶性能优良,但价格昂贵,在不损害原物性的前提下,并用其它橡胶或树脂是完全可行的,如,丁睛胶中并用聚氯乙烯或丁苯胶中掺入天然橡胶,都能起到这一作用。
1. 橡胶并用必须具有一定的相溶性,对橡胶来说天然、顺丁、异戊橡胶等能以任何比例均一地混合,最终达到相溶状态。
而天然胶与丁基橡胶就不能均一地混合。
若硬性机械地混合,所得硫化胶的实际使用性能会显着地下降,这是因为它们的相溶性很差。
并用体系最重要的因素是相溶性,从应用的观点来看,如果混合不均,非但达不到并用的目的,反而影响工艺加工,特别是硫化。
因此,并用问题的焦点是两种橡胶能否相互混合,以及混合后达到什么样的相容程度。
固体橡胶并用时,因橡胶本身粘度很大,高分子的布朗运动不像液体那么容易,扩散速度较慢,对大分子的位移造成很大的阻力,严重影响橡胶间的互容作用。
为此在工业生产中都采用机械力强化分子运动,用提高温度和加入软化剂的方法来降低粘度,以促进两种橡胶的混合,所以产物从宏观上来看虽没有相分离,但真正达到溶解状态也不是很多的,其原因包括下来有以下几点,橡胶的极性、内聚能密度、橡胶的结晶、橡胶的分子量等。
三元乙丙橡胶的分子结构参数对其性能的影响

± 0. 5° 的角度摆动, 采用美国 Alpha 技术公司生 产的 MDR 2000 型无转子 硫 化 仪 测 定 焦 烧 时 间 ( t1 ) 、 t90 、 最低转矩( M L ) 、 最高转矩 ( M H ) 、 转矩差 ( MH - ML ) 、 硫化速率等相关硫化特性参数。 交联结构参数 采用德国 IIC Innovative Imaging 公司生产的 MR - CDS 3500 型核磁共振交联 密度仪进行测定。共振频率 15 MHz, 信号拟合采 用高斯指数和单指数方程进行拟合 。从硫化胶中 裁取长约 8 mm、 宽约 5 mm 的试样放入玻璃管顶 端, 插入磁场中稳定 2 ~ 3 min, 设定相关测试参 数, 然后测定试样的总交联密度 ( D T ) 和横向弛豫 时间( T2 ) 。 拉伸 性 能 按 GB / T 528 —2009 用 德 国 Zwick 公司生产的 BT 1 - FR 005 TN A 50 型 Z 030 橡胶电子拉力试验机进行测定, 拉伸速率为 500 mm / min。 热氧老化性能 采用无锡苏南实验设备有限 公司生产的型号为 RLH - 225 的热空气老化箱对 胶料进行耐热氧老化性能的研究, 老化条件分别 150 ℃ × 24 h。 为 100 ℃ × 24 h、 动态机械 热 分析 采用德国 GABO 公司生 产的 EPLEXOR 500 N 型 动 态 热 机 械 分 析 仪 ( DMTS) 测试, 测试条件为频率 1 Hz, 温度 - 80 ~ 80 ℃ , 升温速率 3 ℃ / min, 采用拉伸形变模式测 定弹性模量( E ' ) 和损耗因子 ( tan δ ) 与温度的关 系曲线。 动态应变扫描 采用美国 Alpha 公司生产的 RPA 2000 型橡胶加工分析仪( RPA) 进行分析, 频 率 1 Hz, 温 度 60 ℃ , 应 变 测 试 范 围: 0. 28% ~ 100% , 其中储能模量用 G ' 表示。
硫化体系对三元乙丙胶的性能影响

罗晓锋等:硫化体系对三元乙丙胶的性能影响
绝缘 材料
2 0 1 3 , 4 6 ( 4 )
硫 化体 系对 三元 乙丙胶 的性能影响
罗晓锋 ,康春梅 ,刘春防 ,翟旭亚 ,刘永红 ,刘 惠华 ,邓春燕
( 特变电工 ( 德阳) 电缆股份有 限公 司 ,四川 德 阳 6 1 8 0 0 0 ) 摘要 : 为研究硫 化体 系对三元 乙丙胶性 能 的影 响 , 分别对 比分析 了不 同过 氧化二异 丙苯 ( D C P ) 含 量和 N, N, 一 间苯撑双马来酰亚胺 ( H v A . 2 ) 含量对三元 乙丙胶硫化性能 、 力学性能 以及电性能 的影响。结果表明 : 随着
Ef f e c t 0 f V_ ul c a ni z a t i o n S y s t e m o n t he Pr o pe r t i e s
o f Et h y l e ne Pr o py l e n e Di e ne Mo no me r
L u o Xi a o f e n g,Ka n g Ch u nme i ,Li u Ch u n f a n g ,Zh a i Xu y a ,Li u Yo n g h o n g ,Li u Hui h u a ,De n g Ch u n y a n
DC P 和H V A . 2 含量的增加 , 三元 乙丙胶 的硫 化速度和拉伸强度逐渐增大 , 而断裂伸长率 和击穿强度逐渐 降
低; 在硫化过程 中D C P 起主导作用 , H V A一 2 起促进作用。 关键 词: 三元乙丙胶 ; D C P ; H V A . 2 ; 电线电缆 中图分类号 : T M2 1 5 . 2 文献标志码 : A 文章编号 : 1 0 0 9 . 9 2 3 9 ( 2 0 1 3 ) 0 4 . 0 0 7 0 . 0 5
三元乙丙橡胶材料密封圈硬度对密封性能的影响
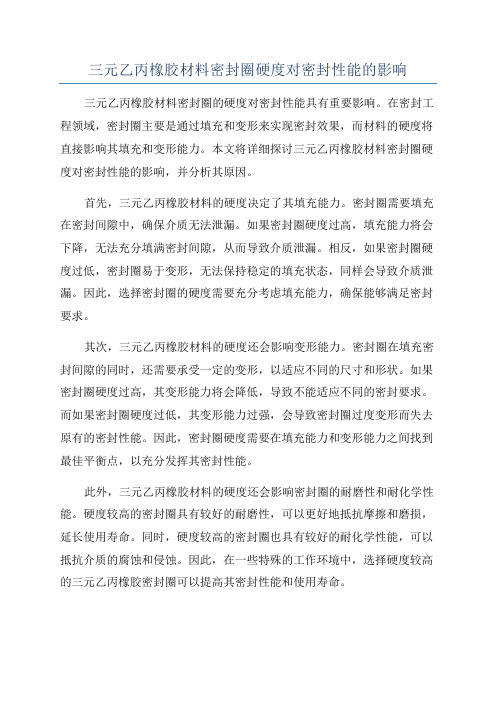
三元乙丙橡胶材料密封圈硬度对密封性能的影响三元乙丙橡胶材料密封圈的硬度对密封性能具有重要影响。
在密封工程领域,密封圈主要是通过填充和变形来实现密封效果,而材料的硬度将直接影响其填充和变形能力。
本文将详细探讨三元乙丙橡胶材料密封圈硬度对密封性能的影响,并分析其原因。
首先,三元乙丙橡胶材料的硬度决定了其填充能力。
密封圈需要填充在密封间隙中,确保介质无法泄漏。
如果密封圈硬度过高,填充能力将会下降,无法充分填满密封间隙,从而导致介质泄漏。
相反,如果密封圈硬度过低,密封圈易于变形,无法保持稳定的填充状态,同样会导致介质泄漏。
因此,选择密封圈的硬度需要充分考虑填充能力,确保能够满足密封要求。
其次,三元乙丙橡胶材料的硬度还会影响变形能力。
密封圈在填充密封间隙的同时,还需要承受一定的变形,以适应不同的尺寸和形状。
如果密封圈硬度过高,其变形能力将会降低,导致不能适应不同的密封要求。
而如果密封圈硬度过低,其变形能力过强,会导致密封圈过度变形而失去原有的密封性能。
因此,密封圈硬度需要在填充能力和变形能力之间找到最佳平衡点,以充分发挥其密封性能。
此外,三元乙丙橡胶材料的硬度还会影响密封圈的耐磨性和耐化学性能。
硬度较高的密封圈具有较好的耐磨性,可以更好地抵抗摩擦和磨损,延长使用寿命。
同时,硬度较高的密封圈也具有较好的耐化学性能,可以抵抗介质的腐蚀和侵蚀。
因此,在一些特殊的工作环境中,选择硬度较高的三元乙丙橡胶密封圈可以提高其密封性能和使用寿命。
然而,密封圈硬度的选择也需要根据具体的应用进行考虑。
不同的工作环境和应用要求可能需要不同硬度的密封圈。
因此,在实际应用中,需要根据具体情况进行硬度的选择和调整。
同时,在制造过程中,可以通过材料配方和工艺参数的调整来改变三元乙丙橡胶材料的硬度,以满足不同的密封要求。
综上所述,三元乙丙橡胶材料密封圈的硬度对密封性能有着重要的影响。
硬度的选择需要在填充能力和变形能力之间找到最佳平衡点,并兼顾耐磨性和耐化学性能。
橡胶制品配方设计与胶料工艺性能的关系
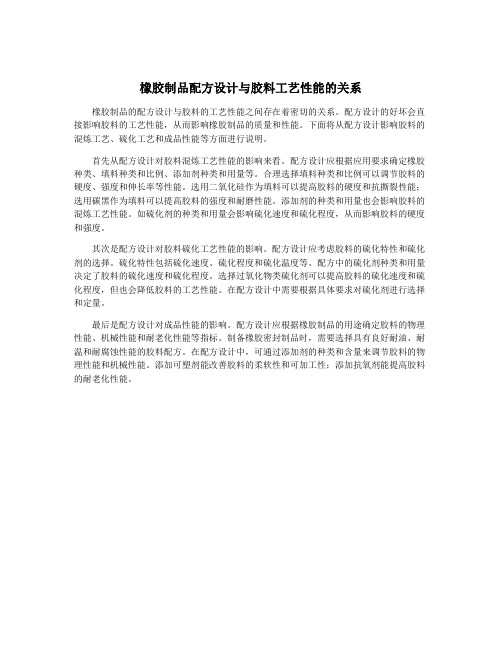
橡胶制品配方设计与胶料工艺性能的关系
橡胶制品的配方设计与胶料的工艺性能之间存在着密切的关系。
配方设计的好坏会直接影响胶料的工艺性能,从而影响橡胶制品的质量和性能。
下面将从配方设计影响胶料的混炼工艺、硫化工艺和成品性能等方面进行说明。
首先从配方设计对胶料混炼工艺性能的影响来看。
配方设计应根据应用要求确定橡胶种类、填料种类和比例、添加剂种类和用量等。
合理选择填料种类和比例可以调节胶料的硬度、强度和伸长率等性能。
选用二氧化硅作为填料可以提高胶料的硬度和抗撕裂性能;选用碳黑作为填料可以提高胶料的强度和耐磨性能。
添加剂的种类和用量也会影响胶料的混炼工艺性能。
如硫化剂的种类和用量会影响硫化速度和硫化程度,从而影响胶料的硬度和强度。
其次是配方设计对胶料硫化工艺性能的影响。
配方设计应考虑胶料的硫化特性和硫化剂的选择。
硫化特性包括硫化速度、硫化程度和硫化温度等。
配方中的硫化剂种类和用量决定了胶料的硫化速度和硫化程度。
选择过氧化物类硫化剂可以提高胶料的硫化速度和硫化程度,但也会降低胶料的工艺性能。
在配方设计中需要根据具体要求对硫化剂进行选择和定量。
最后是配方设计对成品性能的影响。
配方设计应根据橡胶制品的用途确定胶料的物理性能、机械性能和耐老化性能等指标。
制备橡胶密封制品时,需要选择具有良好耐油、耐温和耐腐蚀性能的胶料配方。
在配方设计中,可通过添加剂的种类和含量来调节胶料的物理性能和机械性能。
添加可塑剂能改善胶料的柔软性和可加工性;添加抗氧剂能提高胶料的耐老化性能。
橡胶配方设计与性能的关系-参考模板
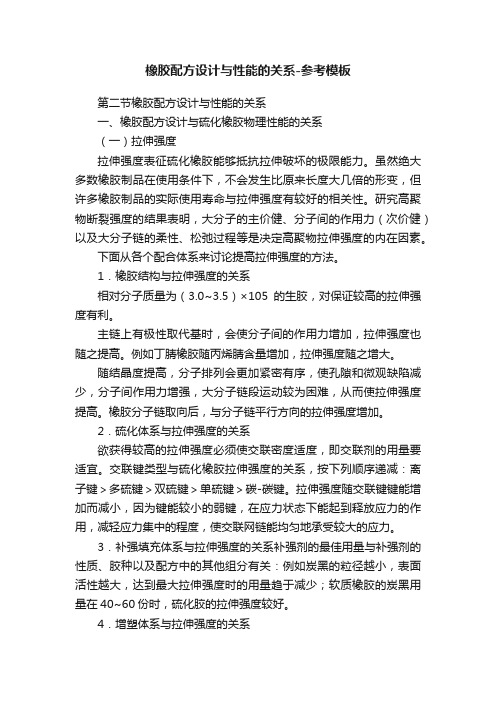
橡胶配方设计与性能的关系-参考模板第二节橡胶配方设计与性能的关系一、橡胶配方设计与硫化橡胶物理性能的关系(一)拉伸强度拉伸强度表征硫化橡胶能够抵抗拉伸破坏的极限能力。
虽然绝大多数橡胶制品在使用条件下,不会发生比原来长度大几倍的形变,但许多橡胶制品的实际使用寿命与拉伸强度有较好的相关性。
研究高聚物断裂强度的结果表明,大分子的主价健、分子间的作用力(次价健)以及大分子链的柔性、松弛过程等是决定高聚物拉伸强度的内在因素。
下面从各个配合体系来讨论提高拉伸强度的方法。
1.橡胶结构与拉伸强度的关系相对分子质量为(3.0~3.5)×105的生胶,对保证较高的拉伸强度有利。
主链上有极性取代基时,会使分子间的作用力增加,拉伸强度也随之提高。
例如丁腈橡胶随丙烯腈含量增加,拉伸强度随之增大。
随结晶度提高,分子排列会更加紧密有序,使孔隙和微观缺陷减少,分子间作用力增强,大分子链段运动较为困难,从而使拉伸强度提高。
橡胶分子链取向后,与分子链平行方向的拉伸强度增加。
2.硫化体系与拉伸强度的关系欲获得较高的拉伸强度必须使交联密度适度,即交联剂的用量要适宜。
交联键类型与硫化橡胶拉伸强度的关系,按下列顺序递减:离子键>多硫键>双硫键>单硫键>碳-碳键。
拉伸强度随交联键键能增加而减小,因为键能较小的弱键,在应力状态下能起到释放应力的作用,减轻应力集中的程度,使交联网链能均匀地承受较大的应力。
3.补强填充体系与拉伸强度的关系补强剂的最佳用量与补强剂的性质、胶种以及配方中的其他组分有关:例如炭黑的粒径越小,表面活性越大,达到最大拉伸强度时的用量趋于减少;软质橡胶的炭黑用量在40~60份时,硫化胶的拉伸强度较好。
4.增塑体系与拉伸强度的关系总地来说,软化剂用量超过5份时,就会使硫化胶的拉伸强度降低。
对非极性的不饱和橡胶(如NR、IR、SBR、BR),芳烃油对其硫化胶的拉伸强度影响较小;石蜡油对它则有不良的影响;环烷油的影响介于两者之间。
三元乙丙混炼胶硫磺硫化体系的优化

三元乙丙混炼胶硫磺硫化体系的优化三元乙丙混炼胶(EPDM)是一种具有良好的物理性能和化学稳定性的合成橡胶,广泛应用于橡胶制品、橡胶密封件、橡胶衬里、汽车零部件等领域。
硫磺硫化是目前EPDM胶最常用的硫化体系之一,通过优化硫磺硫化体系,可以进一步提高EPDM胶的性能和加工效率。
EPDM胶的硫磺硫化体系通常由硫磺、促进剂、活性填料和硫化剂等组成。
硫磺是硫磺硫化体系中最主要的硫化剂,其主要功能是与EPDM胶分子中的双键反应形成交联结构。
促进剂的作用是提高硫磺硫化速率和交联效果,常用的促进剂有过氧化物类、亚硝胺类和二硫化物类等。
活性填料可以提高硫磺硫化的均匀性,并增强硫磺与EPDM胶分子的相容性。
硫化剂是硫磺硫化反应的辅助剂,可以提高硫磺硫化的效果。
优化EPDM胶的硫磺硫化体系需要考虑以下几个方面:1.选择合适的硫磺含量:硫磺的含量对EPDM胶的硫化速率、硫化程度和物理性能有着重要的影响。
过高的硫磺含量会导致硫磺过剩,影响EPDM胶的流动性和加工性能,同时会使硫化后的胶件呈现硬化和脆化的现象。
过低的硫磺含量会导致硫化不完全,影响胶件的交联密度和物理性能。
因此,需要通过实验和试验,确定最佳的硫磺含量。
2.选择合适的促进剂:不同的促进剂对硫磺硫化体系的效果会有所差异,因此需要根据EPDM胶的具体要求选择合适的促进剂。
过氧化物类促进剂具有较高的活性,可以提高硫磺硫化的速率。
亚硝胺类促进剂在硫磺硫化体系中具有较好的活性和交联效果。
根据实际应用需要,可以选择单一的促进剂或者多种促进剂组合使用。
3.选择合适的活性填料:活性填料的选择和用量对硫磺硫化体系和EPDM胶的性能有重要影响。
常用的活性填料有炭黑、硅石、沉淀二氧化硅等。
活性填料可以提高硫磺和EPDM胶的相容性,防止硫磺的局部团聚和分散不均匀现象。
同时,活性填料还可以增加胶料的维持性能,提高胶件的耐热性和耐老化性能。
4.选择合适的硫化剂:硫化剂可以提高硫磺硫化的效果。
- 1、下载文档前请自行甄别文档内容的完整性,平台不提供额外的编辑、内容补充、找答案等附加服务。
- 2、"仅部分预览"的文档,不可在线预览部分如存在完整性等问题,可反馈申请退款(可完整预览的文档不适用该条件!)。
- 3、如文档侵犯您的权益,请联系客服反馈,我们会尽快为您处理(人工客服工作时间:9:00-18:30)。
NS 0. 8,增塑剂A 2。要提高硫化胶的拉伸强
度,可适当增大硫黄用量。
2. 2. 2 拉断伸长率
配方因素对硫化胶拉断伸长率的影响如图1
所 示。 从 图 1 可 以 看 出,随 着 硫 黄 用 量 增 大,硫 化
胶拉断伸长率逐渐减小,这是因为硫黄用量增大,
交 联 键 以 多 硫 键 结 构 为 主,而 多 硫 键 键 能 低 且 不 稳定[5],在受力作用时极易发生断裂,导致硫化胶
14. 6
17. 86
315. 32
75. 1
14. 0
18. 65
228. 50
74. 0
16. 1
15. 75
531. 50
79. 1
12. 3
15. 98
359. 75
75. 4
12. 4
16. 88
369. 95
72. 2
16. 1
17. 80
286. 75
75. 1
14. 3
18. 54
211. 40
配方因素对硫化胶拉伸强度的影响如图1所 示。 从 图1可 以 看 出,硫 化 胶 拉 伸 强 度 随 着 硫 黄 用 量 的 增 大 而 增 大,这 是 因 为 硫 化 体 系 中 硫 黄 用 量增大,硫化胶的交联程度增大。防老剂4010NA 用量对硫化胶拉伸强度的影响不大。随着促进剂 TMTD和NS用量增大,硫化胶的拉伸强度先增大后 略有减小,这是因为促进剂用量增大提高了硫化胶 的交联密度,因而拉伸强度增大;促进剂用量过大 时,硫化胶的交联密度过高,造成橡胶网络应力集 中,拉伸强度减小。增塑剂A用量为2份时,硫化胶 的拉伸强度最大。增塑剂A用量较小时,有利于配 合 剂 的 分 散,提 高 硫 化 胶 的 整 体 性 能;增 塑 剂 A 用 量过大时,削弱了橡胶分子链间作用力,破坏了橡 胶大分子链交联结构,硫化胶的拉伸强度减小。
1 实验 1. 1 配方
根 据 污 水 泵 密 封 圈 的 实 际 工 作 环 境,设 计 的 胶料试验配方如下:EPDM 100,炭黑N115 45, 氧化锌 5,硬脂酸 1,防老剂4010NA、硫黄、促 进剂TMTD、促进剂NS、增塑剂A 变量。 1. 2 主要设备和仪器
XK-160E型 开 炼 机 智 能 炼 胶 实 验 平 台,自 制;X(S)M-1. 7 L型密炼机,青岛科技大学产品; QLB-400×400×2 型 平 板 硫 化 机,上 海 第 一 橡 胶
368. 964 355. 170 339. 292
343. 272 348. 780 346. 544
346. 764 341. 450 353. 720
340. 050 343. 150 366. 730
28. 914 13. 720 33. 346
2
2
5
注:影响由大到小的顺序为硫黄用量、防老剂4010NA用量、增
70. 6
15. 8
15. 71
590. 45
78. 2
12. 9
16. 92
370. 25
76. 6
12. 6
17. 05
330. 22
73. 8
14. 5
17. 40
302. 15
71. 8
14. 8
18. 03
210. 50
70. 1
16. 7
15. 91
509. 11
82. 4
11. 2
16. 13
关键词:密封圈;三元乙丙橡胶;硫化胶;拉伸性能;老化性能;配方设计;正交试验 中图分类号:TQ333. 4;TQ336. 4+2 文献标志码:A 文章编号:1000-890X(2016) - -06
橡胶密封圈是污水泵的重要零件,然而在实际 使用中往往达不到污水泵的检修期就需要提前单 独更换,这无疑增加了污水泵维护及保养工作量。 因此,研发一种适合污水泵较长期使用的橡胶密封 材 料 是 非 常 有 必 要 的。 三 元 乙 丙 橡 胶(EPDM)主 链由化学稳定的饱和烃组成,侧链中含有不饱和双 键,故其具有耐臭氧、耐酸碱腐蚀、耐老化、使用寿 命长等优点,被广泛应用于密封件[1]。本工作针对 污 水 泵(生 活 用)工 作 环 境,采 用 正 交 试 验 法 设 计 试 验 配 方,考 察 配 方 中 硫 黄、防 老 剂、促 进 剂 以 及 增塑剂用量对EPDM密封圈硫化胶物理性能和耐 老 化 性 能 的 影 响,旨 在 为 今 后 设 计 污 水 泵 橡 胶 密 封圈胶料配方提供参考。
用量
用量
用量
用量
用量
1 0. 5
0
0. 5
0. 2
0
21
1
1
0. 4
2
3 1. 5
2
1. 5
0. 6
4
42
3
2
0. 8
6
5 2. 5
4
2. 5
1
8
在 密 炼 机 中 依 次 加 入EPDM(0. 5 min)、增
塑 剂 A、氧 化 锌、硬 脂 酸、防 老 剂 4010NA、1/2 炭 黑
N115(2. 5 min)、1/2炭 黑N115(1 min)进 行 一 段 混炼,转子转速为70 r·min-1,填充因数为0. 7。
75. 6
15. 4
表性能指标随因子水平变动而产生的变动幅度;
表中K x(x为1,2,3,4,5)为各因子x水平的性能结 果平均值[4]。
பைடு நூலகம்
从 表 3 可 以 看 出,本 试 验 硫 化 胶 拉 伸 强
度 最 优 的 因 子 组 合 配 方 为:硫 黄 2. 5,防 老
剂 4010NA 1,促 进 剂 TMTD 1. 5,促 进 剂
因子
项目 硫黄用量
K1 K2 K3 K4 K5 R 最优水平
14. 946 16. 180 17. 148 17. 694 18. 218 3. 272
5
防老剂 4010NA
用量 16. 306 17. 022 16. 958 16. 928 16. 972 0. 716
2
促进剂 TMTD 用量 16. 484 16. 918 17. 374 16. 726 16. 684 0. 890
采 用 正 交 试 验 法[2],选 取 硫 黄 用 量、防 老 剂 4010NA用量、促进剂TMTD用量、促进剂NS用量、 增塑剂A用量(单位均为质量份)作为试验因子,每 个因子选择5个水平,设计五水平六因子的L25(56) 正交试验。正交试验的因子和水平如表1所示。
表1 因子和水平
因子
水平 硫黄 防老剂4010NA 促进剂TMTD 促进剂NS 增塑剂A
3
促进剂NS 增塑剂A
用量
用量
16. 408 16. 510 17. 130 17. 262 16. 876 0. 854
4
16. 464 17. 072 17. 032 16. 908 16. 710 0. 608
2
注 :影 响 由 大 到 小 的 顺 序 为 硫 黄 用 量 、促 进 剂 T M T D 用 量 、促
表2 硫化胶性能
拉伸强度/ 拉断伸长率/ 拉断伸长率 压缩永久
MPa
%
保持率/% 变形/%
12. 98
501. 35
73. 9
13. 3
15. 76
341. 55
75. 1
13. 3
17. 59
321. 75
73. 5
14. 7
17. 62
245. 70
72. 1
15. 6
17. 58
201. 35
第期
曾宪奎等.配方因素对三元乙丙橡胶密封圈硫化胶性能的影响
1
配方因素对三元乙丙橡胶密封圈硫化胶性能的影响
曾宪奎,韩广文,孙延奎
(青岛科技大学 机电工程学院,山东 青岛 266061)
摘 要:采 用正交 试 验法研究 硫 黄、防老 剂4010NA、促 进 剂TMTD、促 进 剂NS以 及 增 塑 剂A的 用 量 对 三 元 乙 丙 橡 胶 (EPDM)密封圈硫化胶拉伸强度、拉断伸长率、拉断伸长率保持率和压缩永久变形的影响。结果表明,硫黄用量对EPDM 密封圈硫化胶各项性能的影响最为显著;当硫黄、防老剂4010NA、促进剂TMTD、促进剂NS和增塑剂A用量分别为0. 5, 2,1. 5,1和2份时,硫化胶的耐压缩永久变形性能最好。
塑剂A用量、促进剂TMTD用量、促进剂NS用量。
18
600
ડறͨ᫁ည
500 17
400
16
300
200 15
100
14
0
0
1
2
3
4
Ꮴҍ4010NAၸ᧙͊
18
600
500 17
400
ડறͨ᫁ည
ડறͨ᫁ည ડͨुऎMPa
ડͨुऎMPa
16
15
14 0.5
1.5
2.0
2.5
ΧᤈҍTMTDၸ᧙͊
2 结果与讨论 2. 1 试验结果
拉伸强度和拉断伸长率是评定密封圈硫化胶 物 理 性 能 的 指 标,拉 断 伸 长 率 保 持 率 和 压 缩 永 久 变形是评定密封圈硫化胶耐老化性能的指标。本 工 作 采 用 正 交 试 验 法 设 计 了 25 组 试 验 配 方,测 定 了各组试验配方硫化胶的拉伸强度、拉断伸长率, 以及经过100 ℃×7 d污水介质环境加速老化试验 后的拉断伸长率保持率和压缩永久变形[3],结果如 表2所示。 2. 2 配方因素对硫化胶物理性能的影响 2. 2. 1 拉伸强度
160 ℃/10 MPa×t 90。 1. 4 测试方法
拉伸强度、拉断伸长率按照GB/T 528—2009 《硫化橡胶或热塑性橡胶 拉伸应力应变性能的 测 定》进 行 测 试,哑 铃 形 Ⅱ 型 试 样,拉 伸 速 率 为 500 mm·min-1,测试温度为23 ℃。压缩永久变形 按 照GB/T 7759. 1—2015《硫 化 橡 胶 或 热 塑 性 橡 胶 压缩永久变形的测定 第1部分:在常温及高温 条件下》进行测试,采用A型试样,压缩率25%。