[塑料]-塑胶喷涂丝印工艺、不良缺陷及QC控制要点
塑胶件常见缺陷不良分析及对策讲解
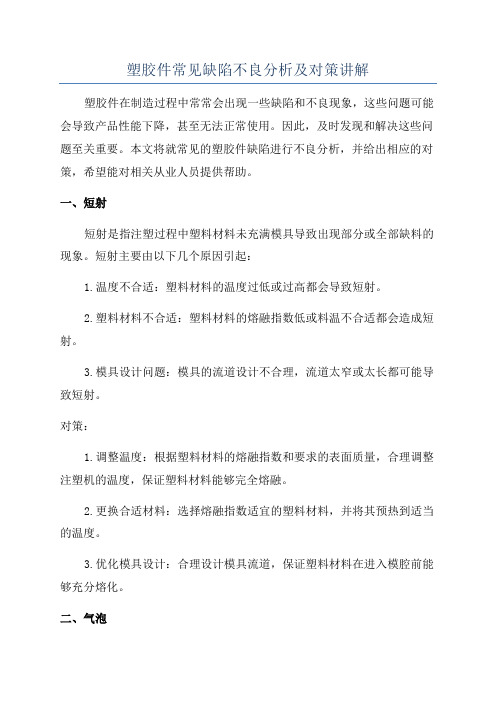
塑胶件常见缺陷不良分析及对策讲解塑胶件在制造过程中常常会出现一些缺陷和不良现象,这些问题可能会导致产品性能下降,甚至无法正常使用。
因此,及时发现和解决这些问题至关重要。
本文将就常见的塑胶件缺陷进行不良分析,并给出相应的对策,希望能对相关从业人员提供帮助。
一、短射短射是指注塑过程中塑料材料未充满模具导致出现部分或全部缺料的现象。
短射主要由以下几个原因引起:1.温度不合适:塑料材料的温度过低或过高都会导致短射。
2.塑料材料不合适:塑料材料的熔融指数低或料温不合适都会造成短射。
3.模具设计问题:模具的流道设计不合理,流道太窄或太长都可能导致短射。
对策:1.调整温度:根据塑料材料的熔融指数和要求的表面质量,合理调整注塑机的温度,保证塑料材料能够完全熔融。
2.更换合适材料:选择熔融指数适宜的塑料材料,并将其预热到适当的温度。
3.优化模具设计:合理设计模具流道,保证塑料材料在进入模腔前能够充分熔化。
二、气泡气泡是指塑胶件表面或内部出现的小气孔或气泡。
气泡可能导致产品外观不良或性能下降。
气泡的产生主要有以下几个原因:1.塑料材料中含有挥发性成分:一些塑料材料中含有挥发性成分,如果注塑温度过高,这些挥发性成分就会挥发出来形成气泡。
2.模具表面不洁净:如果模具表面不干净或有油污等杂质,气泡就会在塑料注入过程中被吸附在塑料中形成。
3.注塑机压力过高:注塑机压力过高会导致空气被压进模具中,形成气泡。
对策:1.调整注塑温度:根据塑料材料的特性,合理调整注塑温度。
温度过高易导致气泡产生,温度过低则容易短射。
2.模具清洁:保持模具表面干净,定期对模具进行清洗,去除杂质和油污。
3.控制注塑机压力:根据塑料材料的特性和模具的要求,合理控制注塑机的压力,避免空气进入模具。
三、热处理不当塑胶件经过热处理后,如果处理不当,可能导致产品性能下降或出现变形等问题。
常见的热处理问题有:1.温度不合适:热处理时,温度不合适会导致产品硬度不均匀或过硬。
整理塑胶产品常见缺陷讲义剖析
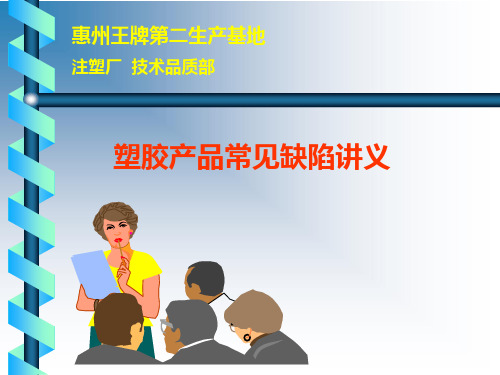
高”。(按括手或影响装配来判定)
4/16
(二)、制品表面缺陷
1.粘胶:在上一制品后残留的胶渣在模腔内,导致粘在后一制品表面, 称为“粘胶、胶屎”。
2.熔接线:来自不同方向的流体热熔接时不够紧密形成线状的痕迹,常 称“夹水纹”。(依照样板判定)
区域。常称“光身、光印、骨影”。(不明显或后续喷油能遮盖的 可
接收) 15.表面粗糙:模具喷砂过粗或7/模16具表面刨光不良,使制品表面皮纹粗
(二)、制品表面缺陷
16.皮纹不均:模具喷砂不良,使制品表面皮纹粗、细不均。 17.锈渍:模腔生锈,使制品表面出现相应类似皮纹,但极不均匀的片
状或斑块。(视所出现的表面不同程度来判定) 18.颜色变异:制品相对样板或装配颜色偏差,即颜色不配套。(以打
4. 缺陷收货标准 4.1 严格按照GB2828抽样方式计数表来判定,祥情参阅GB2828抽样方式。 5. 缺陷的名称 6. 缺陷形成原因、对策。 6.1 不良现象的分析和解决方法通常采用特性要因图(即因果图、鱼剌
图),并从 以下五个方面来着手改善: A、人员、B.材料、C.方法、D.设备、E.环境。
23.烘影:制品局部受热在表面形成“哑克色”的圆印亦称“鬼影”。 24.打磨烧边:一般指透明镜面因刮伤、划伤进行打磨时温度太高,促
使颜色变异。 25.打磨不均:镜面以打磨后存在蹭迹或其它污渍物。
(用绒布能擦除的按次要缺点来判定)
9/16
(三)、喷油不良
2.烫金字体断线:烫金字体不完整、欠缺。 3.烫金漏黑:烫金纸留有少量油漆没有完全烫到制品的表面上,使表面
烫金漏底,一般底座与产品吻合不良造成。 4.烫金皱纹:产品表面所烫的油层起皱,烫金纸没拉平或底座与产品吻
塑胶产品喷涂异常的处理

浅谈喷涂异常处理喷涂产品技术员,QC和生产人员,如果对喷涂的异常处理有些了解的话,就会对工作有新帮助,就可以通过新遇到的质量缺陷进行分析找出其原因以及要采取的改善对策,从而提高产品质量的鉴别能力,下面就喷涂日常出现的异常处理,行业内要作的物性测试作些简单的介绍。
一.浅谈喷涂异常处理:1.变色:由于油漆质量不好会产生一系列的不良现象,异色就是其中之一。
之所以会出现异色、变色由以下几种原因造成:(1)涂料中颜料的密度不同,密度大的颜料下沉,轻的浮在上面(2)含铅式铜系颜料与硫化氰起化学反应变黑。
改善对策:(1)彻底均匀搅拌后再使用,(2)有硫化氰的环境不使用含铅式含铜系颜料2.发哑、发白:如果天气温度过重,硝基漆易泛白,或移植释剂配比不当会出现喷漆产品光泽度不够颜色发哑(发暗)改善对策:(1)可先低温预热被涂物,或加入10—20%的防白剂,喷漆场所应尽量保持恒温,恒湿状态,可防止喷涂产品发白(2)当空气中的温度过高,大多是在一些比较简陋的喷漆场所,可将喷涂完毕之产品放在烘炉内烘烤几分钟可防止喷漆品颜色发哑3:附着力不够:由于一些油漆质量不好或塑胶素材脏污,油漆喷上会出现脱漆或涂膜本身无法附着于素材表面或底部.改善对策:1)如果油漆质量不良应该调换,也可使用较稀释剂调漆,或适当加入一定比例固化剂;<我公司目前不用>(2)为防止产品表面由于脏污不清洁而造成的脱漆,必须于喷漆前先将素材清洁干净后方可喷涂.《我社采用前处理/静电除尘》4.针孔,油点:产品喷涂后在溶剂挥发到初期结膜阶段,由于溶剂的急剧挥发,特别是受高温烘烤时漆膜收缩来不及补足空档,而形成一系列小穴即针孔,如果溶剂使用不当,或温度加热高,过快就易产生针孔,当喷漆环境相对过高,或喷涂设备的油水分离器失灵,喷涂时水分随空压机经喷嘴与涂料同时喷出,也会造成喷涂后出现表面针孔.改善对策:(1)烘烤型涂料粘度要适中,喷涂后要在恒温下静置约5—10分钟,烘烤时,先低温预热后按规定温度和时间使溶剂能正常挥发;(2)使用适当稀释剂,避免加热过于剧烈;(3)喷涂面漆时,喷漆环境相对温度应于65%以下为宜,检查油水分离器的可靠性,空气压缩机经过滤,杜绝油和水及其它杂质带进涂料中。
塑胶外壳喷涂丝印检验规范

惠州市兄辉电子塑胶有限公司文件编号2020/06/27版本/版次A/0塑胶外壳喷涂丝印检验规范发布部门品质部目的:为规范外壳喷涂、丝印检查方法、标准,特制订本检验规范。
范围:适用于外壳喷涂、丝印的品质检验、控制检验说明:抽样标准:单次AQL:CRI=0MAJ=0.4MIN=1.5严重缺陷:对使用者人体或环境产生危害之缺陷主要缺陷:影响产品使用功能或外观之缺陷。
次要缺陷:不影响产品功能或外观之轻微缺陷。
检验条件检查距离:被检物品距离肉眼25±5cm 光源强度:800luxs检查时间:10±5秒钟内确认缺陷检查角度:被测面与光源成45°±15°角度检验项目一.外观:软划伤标准【缩写表示:N=Number(数量),L=Lenght(长度),W=Width(宽度),A=Area(区域),D=Diameter(直径),DS=distance(距离)。
】缺陷类型:软划伤表面等级缺陷水平判定缺陷数量L(mm)W(mm)D(mm)S(mm )DS(mm)Acc.Min.Maj.Cri.A≤0.5≤0.08>20X 30.5--1≤0.08>20X 21--20.08-0.10X1>2>0.10X1B≤2≤0.05>20X 32--3≤0.08>20X 22--3≤0.10X1>3>0.10X1C ≤5≤0.10>20X 2≤50.10-0.15X1>5>0.15X1.喷涂、丝印尘点、异色点标准2.喷涂、丝印其它外观标准二.可靠性测试标准:1.附着力测试测试方法:用锋利刀片(刀锋角度为15°~30°)在测试样本表面划10×10个1mm×1mm 小网格,每一条划线应深及油漆的底层;用毛刷将测试区域的碎片刷干净;用粘附力350~400g/cm2的胶带(3M610号胶纸或等同)牢牢粘住被测试小网格,并用橡皮擦用力擦拭胶带,以加大胶带与被测区域的接触面积及力度;用手抓住胶带一端,在垂直方向(90°)迅速扯下胶纸,同一位置进行3次相同试验;结果判定:要求附着力≥4B 时为合格。
塑胶件喷油及丝印检验标准
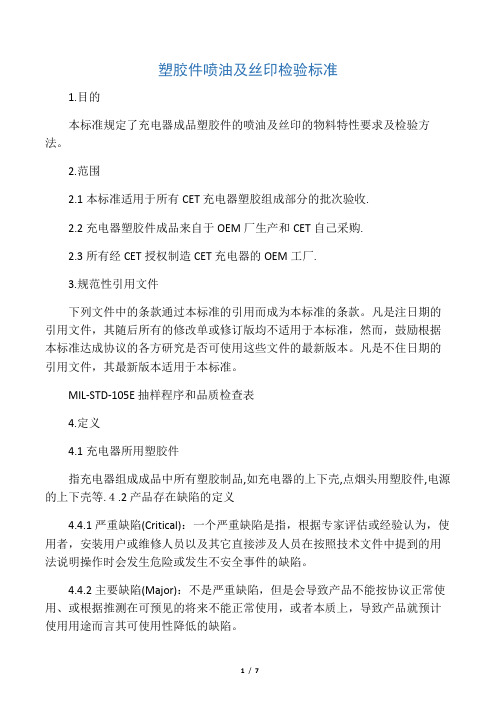
塑胶件喷油及丝印检验标准1.目的本标准规定了充电器成品塑胶件的喷油及丝印的物料特性要求及检验方法。
2.范围2.1本标准适用于所有CET充电器塑胶组成部分的批次验收.2.2充电器塑胶件成品来自于OEM厂生产和CET自己采购.2.3所有经CET授权制造CET充电器的OEM工厂.3.规范性引用文件下列文件中的条款通过本标准的引用而成为本标准的条款。
凡是注日期的引用文件,其随后所有的修改单或修订版均不适用于本标准,然而,鼓励根据本标准达成协议的各方研究是否可使用这些文件的最新版本。
凡是不住日期的引用文件,其最新版本适用于本标准。
MIL-STD-105E抽样程序和品质检查表4.定义4.1充电器所用塑胶件指充电器组成成品中所有塑胶制品,如充电器的上下壳,点烟头用塑胶件,电源的上下壳等.4.2产品存在缺陷的定义4.4.1严重缺陷(Critical):一个严重缺陷是指,根据专家评估或经验认为,使用者,安装用户或维修人员以及其它直接涉及人员在按照技术文件中提到的用法说明操作时会发生危险或发生不安全事件的缺陷。
4.4.2主要缺陷(Major):不是严重缺陷,但是会导致产品不能按协议正常使用、或根据推测在可预见的将来不能正常使用,或者本质上,导致产品就预计使用用途而言其可使用性降低的缺陷。
4.4.3小缺陷(Minor):是指没有被定义为严重和主要缺陷的缺陷。
与约定规格稍有出入,但不大可能降低产品事实上的使用性能,不影响产品的预计使用用途的缺陷。
5.技术要求5.1塑胶件喷油,丝印的外观要求5.1.1塑胶件喷油丝印整体可见表面污点(含簧片表面污渍)面积小于0.5mm2,,数量不多于2个;5.1.2塑胶件喷油丝印整体可见表面划伤,直径小于0.2mm,长度小于2mm,数量不多于2个;5.1.3塑胶件喷油的上下壳无色差;5.1.4塑胶件整体无变形,缩水,批锋,油渍等不良;;5.1.5塑胶件的丝印表面位置无偏移,漏印,错印,杂色等不良现象;5.1.6在塑胶件中有生产日期的标识。
塑胶件QC检查标准
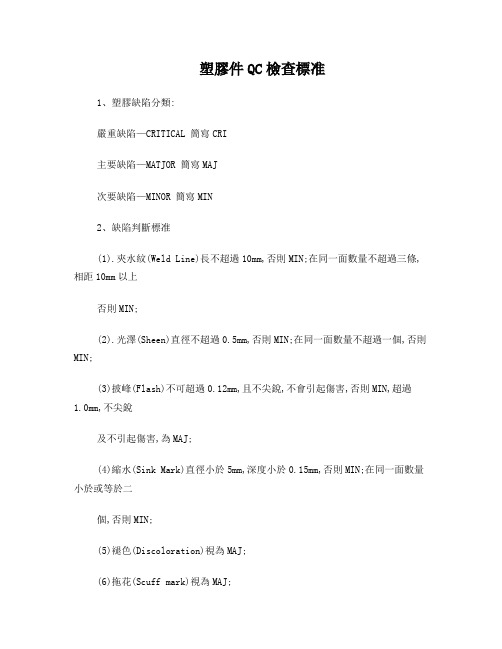
塑膠件QC檢查標准1、塑膠缺陷分類:嚴重缺陷—CRITICAL 簡寫CRI主要缺陷—MATJOR 簡寫MAJ次要缺陷—MINOR 簡寫MIN2、缺陷判斷標准(1).夾水紋(Weld Line)長不超過10mm,否則MIN;在同一面數量不超過三條,相距10mm以上否則MIN;(2).光澤(Sheen)直徑不超過0.5mm,否則MIN;在同一面數量不超過一個,否則MIN;(3)披峰(Flash)不可超過0.12mm,且不尖銳,不會引起傷害,否則MIN,超過1.0mm,不尖銳及不引起傷害,為MAJ;(4)縮水(Sink Mark)直徑小於5mm,深度小於0.15mm,否則MIN;在同一面數量小於或等於二個,否則MIN;(5)褪色(Discoloration)視為MAJ;(6)拖花(Scuff mark)視為MAJ;(7)烘印(Shadow mark)視為MAJ;(8)混色(Contamination)數量大於三點,為MAJ,在直徑1mm內有二點,且直徑≧0.15mm,為MIN;一點直徑大於0.3mm為MAJ;(9)發白(White mark)在塑件柱位或扣位根部出現發白;若發白長度小於柱位直徑或扣拉寬度的1/3為MIN;(10)間隙(GNP)對塑膠件最大尺寸150mm,間隙允收0.2mm,否則MIN;對塑件最大尺寸150mm,間隙允許0.3mm否則MIN;(11)掛手(over Hang)對左右殼配合而言,兩殼外表高度差大於0.2mm為MIN;兩殼外表高度差大於0.3mm為MAJ。
對於上下殼配合而言,面殼大於底殼,大於0.2mm為MIN。
面殼大於底殼大於0.5mm為MAJ。
底殼大於面殼為MAJ。
前後模錯位,台階高度不能大於0.2mm否則為MIN,大於0.3mm為MAJ。
(12)缺料(Short Shots)若組裝後不影響外觀,則為MIN,若內腔筋骨缺料,則可接受(Acceptable);(13)變形(war page)若影響配合,則為MAJ,一般變形,則為MIN;(14)表面蝕紋(surface streaking)同一塑件表面蝕紋要一致,否則為MAJ;不同塑件但相互要組合的外表面蝕紋要一致,否則為MAJ;(15)顏色(Color)若顏色不對samples或分布不均,則為MAJ,若配件顏色不配則為MIN(特殊要求除外);(16)入水太陽紋,視為MAJ;(17)蛇紋(wave marks)視為MAJ;(18)裂紋(crack line)若裂紋出現在開鍵部位,則為CRI;若裂紋出現在次要部位或隱蔽部位,則為MAJ;(19)流痕(Flow Mark)出現在正面,影響外觀,視為MAJ,否則MIN;(20)刀紋(scrape)若出現在外殼外表面且不明顯,則為MIN;若出現在透明表面,則為MAJ;(21)表面不夠靚(pcor surface finish)視為MIN;(22)击點(DOT)直徑不超過0.3mm,否則MIN,在同一面數量不超過一個,否則MIN;(23)凹坑(pit)直徑不超過0.3mm,否則MIN,在同一面數量不超過一個,否則MIN;(24)氣泡(Air-orifice)出現在透明或半透明件上為MAJ,出現在非透明件上為MIN;(25)銀紋出現在透明或半透明件上為MAJ;出現在非透明件上為MIN;(26)震紋(波紋)出現在透明或半透明件上為MAJ,出現在非透明件上為MIN;(27)發白,霧暈出現在非透明件上,為MIN,否則為MAJ;(28)白煙,黑斑出現在非透明件上為MIN,否則為MAJ;(29)白霜(拋光後可除去)視為MIN;(30)白邊視為MIN;(31)焦化,變色若出現在非外表面,為MIN,否則MAJ;(32)腫脹,鼓泡視為MIN;(33)光芒線(出現在點澆口注塑制件表面上)視為MIN;(34)鵰字不清或缺劃視為MAJ;(35)絲印:絲印傾斜為MAJ;絲印模糊可分辨清楚,為MIN,絲印模糊難以分辨為MAJ;(36)特殊表面(如貼LABEL)不平或光視為MIN;(37)扣位若兩殼組合後,在不借助外力作用下,人手難以分兩殼,則為MAJ;若組裝前後扣位斷,則為MAJ,若組裝前後扣位發白但不超過扣位寬度的1/3,則為MIN,否則MAJ;若組裝後扣位配合不良則為MIN;(38)模號,零件號若條件充許,制作內表面無模號,零件號標志則為MIN;(39)尺寸:若配合尺寸不到位,則為MAJ,若貼標簽位尺寸不到位,則為MIN,若扣位尺寸不到位,則為MAJ;3、PASS判斷標准(1)對透明件或半透明件而言:CRI=0 MAJ=0 MIN=2%(2)對重要制件(如外殼)而言:CRI=0 MAJ=1%MIN=5%(3)對一般制件而言:CRI=0 MAJ=3%MIN=8%(4)判斷標准列表如下:CRI MAJ MINPASS OK OK OKWAIVE OK OK 不OKREJECT 不OK 不OK OK或不OK注PASS-合格WAIVE-暫時通過但要改相關缺陷REJECT-拒絕接收以上判斷標准可作為QC一般檢查依據,但客戶特殊要求除外。
[塑料]-塑胶喷涂丝印工艺、不良缺陷及QC控制要点
![[塑料]-塑胶喷涂丝印工艺、不良缺陷及QC控制要点](https://img.taocdn.com/s3/m/34435005f705cc1754270989.png)
[塑料]塑胶喷涂/丝印工艺、不良缺陷及QC控制要点一、喷漆常见缺陷1。
飞油因套模不正或胶件变形导致油从套缝中飞出:~)l;n% f&W2。
流油因喷漆末干而流动的油层3。
积油喷漆不均匀积成油块# e’ U;o6 R8 Y4. 油渍胶件上粘有油质而导致喷时不上漆5。
油污胶件被油漆污染*|j' r" |5 e&O1 \+ u6 F6 s6。
上色不足喷漆时颜色没有签板深( k! h N2 |$r& o#H7 G' w7。
砂孔反映在制品表面象砂子大小的孔,打磨后可再加工8 N0 O; B4 y; q4 Z) j8。
走位涂层处理位置不正确,同样板有偏差,调整相应机械或工具可改善9. 起牙边涂层处理后其边参差不齐,调整丝印网版,移印胶头或喷漆模可改善# r) T1 ~!F! l&R4 H#M10. 甩油涂层处理后,表面一块块脱掉,可改变盛放方法及等涂层全干后投入生产11. 反底因胶件或油漆的原因令油层遮盖不到胶件的颜色$V6 {8 P5 G* x, |$ \:g; N)Q9 |12. 漏喷漆应喷漆而没有喷漆的位置13. 刮花胶件或喷漆层由于外界碰擦而刮花的痕迹4 t” H*b3 m2 S7 M! H14。
色差涂层颜色不一致,异于样板,常见于配套配色胶件; I5 ^。
O0 h- n15. 哑色或称无光泽,由油漆质量或喷涂层厚薄所致。
16。
拉丝由于涂层太浓,而致使移开网版,胶头或模具时而留下的丝状物(F7 j2 Z!E0 b1 f:|%p17。
油面末干油面接触到硬物件时,其硬度不够凹下二、移印常见缺陷1。
漏印规定移印的位置末有移印2。
重印移印过多次,图案上易有叠影* P9 D x;`2 n- L% M3 T( T3。
印错位没有将图案印在规定的位置#m/ U,j+ R& ]2 Q3 P!w" q5 Y4. 移位移印的图案位置与规定的位置有误差’ v- Y+ |4 k/ I% h” V5。
塑胶件常见品质缺陷(注塑、喷油、丝印) 精品
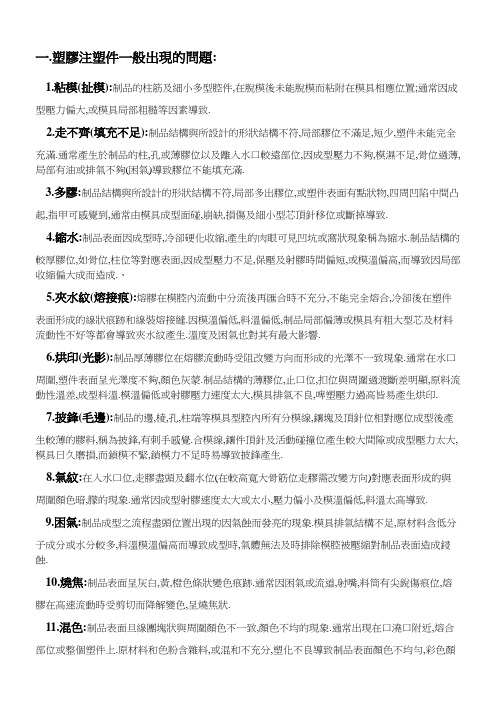
一.塑膠注塑件一般出現的問題:1.粘模(扯模):制品的柱筋及細小多型腔件,在脫模後未能脫模而粘附在模具相應位置;通常因成型壓力偏大,或模具局部粗糙等因素導致.2.走不齊(填充不足):制品結構與所設計的形狀結構不符,局部膠位不滿足,短少,塑件未能完全充滿.通常產生於制品的柱,孔或薄膠位以及離入水口較遠部位,因成型壓力不夠,模濕不足,骨位過薄,局部有油或排氣不夠(困氣)導致膠位不能填充滿.3.多膠:制品結構與所設計的形狀結構不符,局部多出膠位,或塑件表面有點狀物,四周凹陷中間凸起,指甲可感覺到,通常由模具成型面碰,崩缺,損傷及細小型芯頂針移位或斷掉導致.4.縮水:制品表面因成型時,冷卻硬化收縮,產生的肉眼可見凹坑或窩狀現象稱為縮水.制品結構的較厚膠位,如骨位,柱位等對應表面,因成型壓力不足,保壓及射膠時間偏短,或模溫偏高,而導致因局部收縮偏大成而造成.、5.夾水紋(熔接痕):熔膠在模腔內流動中分流後再匯合時不充分,不能完全熔合,冷卻後在塑件表面形成的線狀痕跡和線裝熔接縫.因模溫偏低,料溫偏低,制品局部偏薄或模具有粗大型芯及材料流動性不好等都會導致夾水紋產生.溫度及困氣也對其有最大影響.6.烘印(光影):制品厚薄膠位在熔膠流動時受阻改變方向而形成的光澤不一致現象.通常在水口周圍,塑件表面呈光澤度不夠,顏色灰蒙.制品結構的薄膠位,止口位,扣位與周圍過渡斷差明顯,原料流動性溫差,成型料溫.模溫偏低或射膠壓力速度太大,模具排氣不良,啤塑壓力過高皆易產生烘印.7.披鋒(毛邊):制品的邊,棱,孔,柱端等模具型腔內所有分模線,鑲塊及頂針位相對應位成型後產生較薄的膠料,稱為披鋒,有刺手感覺.合模線,鑲件頂針及活動碰撞位產生較大間隙或成型壓力太大,模具日久磨損,而鎖模不緊,鎖模力不足時易導致披鋒產生.8.氣紋:在入水口位,走膠盡頭及翻水位(在較高寬大骨筋位走膠需改變方向)對應表面形成的與周圍顏色暗,朦的現象.通常因成型射膠速度太大或太小,壓力偏小及模溫偏低,料溫太高導致.9.困氣:制品成型之流程盡頭位置出現的因氣蝕而發亮的現象.模具排氣結構不足,原材料含低分子成分或水分較多,料溫模溫偏高而導致成型時,氣體無法及時排除模腔被壓縮對制品表面造成鋟蝕.10.燒焦:制品表面呈灰白,黃,橙色條狀變色痕跡.通常因困氣或流道,射嘴,料筒有尖銳傷痕位,熔膠在高速流動時受剪切而降解變色,呈燒焦狀.11.混色:制品表面旦線團塊狀與周圍顏色不一致,顏色不均的現象.通常出現在口澆口附近,熔合部位或整個塑件上.原材料和色粉含雜料,或混和不充分,塑化不良導致制品表面顏色不均勻,彩色顏件最容易形成,也與料筒清潔或背壓有關.12.發白:制品水口有脫模時爆裂,發白或不規則斷裂.因成型壓力大,射膠(保壓)(冷卻)時間太長或頂出太快(頂針分佈不合理),水口不光滑等原因導致脫模時水口受力偏大而發生不良,主要發生在透明制品,使用較脆膠料(如PS,PMMA等料).13.水口加工不良:制品水口被剪除偏高,偏低,白化變形,熱剪後卷起及漏加工等.因加工方法不合理,或加工工具不合適,加工不認真,導致水口位加工不合要求,影響外觀或裝配.14.鋸齒邊:加工部位被加工太多或加工面不平滑,因加工方法,工具或人為因素而導致.15.麻點:制品光滑表面出現的細小密集點狀凸起,模糊不清晰,指圍感覺不到,稱為麻點.因材料內含有的輔助劑(如防火PC料的陰燃劑),或成型工藝不合理而導致,或原料本身或熔料不好引起. 16.拖傷:制品的側邊,孔等位置在脫模時被拖成的痕跡,因制品側邊,孔等位置脫模斜度不夠,蝕紋偏粗或脫出受力偏大導致.17.拖花:出模後造成損傷.通常出現在邊角位上,可能因出模角度與紋路有問題引起.18.拖白:制品的側邊,柱孔等位脫模時產生的發白現象.因制品的側邊,柱孔等位脫模斜度不夠,蝕紋偏粗局部不夠光滑,而導致脫出受力偏大導致.19.頂白:頂針位在脫模頂出時,使對應表面出現發白痕跡或清晰白印,向上凸起.因頂針分佈不合理,頂針位結構偏薄.模具頂針過少,或頂出太快,冷卻時間不足,而導致頂傷制品.20.拖絲:水口脫出時,從射嘴拖出的絲狀物未被清除而被成型粘復到焉一制品的表面,呈絲線狀或線狀痕,稱拖絲.因射嘴溫度偏高,或模溫不當,或防流涎裝置不良,或成型工藝不合理導致.21.冷膠:與制品整體膠料未完全融合,有清晰分界線的團塊狀的現象.因模具流道及射嘴等位在上啤時溢出或斷裂遺留的未清除冷膠被成型到下一啤制品外表面所致.22.料花:制品表面細小不規則的冷膠料,稱料花.因模具流道和型腔內遺留有上一啤脫模時的細小碎膠料被成型到下一啤制品上所致.23.氣泡:塑料在充模過程中受到氣體的干擾而在制品表面上呈現中空狀凸起,或透明制品膠位內中空泡狀.由塑膠原料水分含量偏大,低分子產物含量偏大,料溫偏高,或背壓不夠,成型工藝不合理,冷卻時間不足等原因造成.24.油漬:制品上附著有模具上的油跡(防銹油,頂針油,或黃油等).在塑件表面呈不規則痕跡,影響塑件光澤度.模具結構位用油太多,清除不夠干凈導致表面產生的斑點狀發亮現狀,稱為油點.頂針及行位,導柱部位用油較多,運動時滴落到模腔內.25.手指印:制品表面有手指印跡.因手指有油污,汗漬而手指接觸到制品表面而產生的印跡.26.膠漬:制品蝕紋部位不規則光亮痕,光滑面呈霧狀,麻點狀不光亮現象.模具表面被細微膠粉遮蓋或被低分子產物遮蔽,而導致制品表面不能清晰表現設計的狀態.27.黑點(雜質點):制品表面的呈不同於制品顏色的點,線狀異物,因原材料,色粉內有異物,或環境中的雜質及模具活動部分損傷的金屬等吸附到模具型腔,而成型到制品表面所致.28.衝紋(流紋):制品表面沿流動(填充)方向呈現的蛇形或放射狀的紋路,呈花紋狀流痕,清晰可見,指圍感覺不到,稱衝紋.因模溫太低或太高,射速過低,或射速過快,半凝固料受到熱熔料推擠而導致.白色件最容易產生.二.塑膠組件一般容易出現的問題:1.尺寸不符:制品尺寸超出圖紙或規定的控制尺寸範圍.因成型時壓力偏大偏小,射膠時間偏長偏短或模具局部鑲件及活動結構位鬆動等原因造成.2.偏位(shift):一般指螺絲柱,孔位等偏離中心,嚴重者會破裂.3.裝配鬆緊:相關制品在組裝時,偏鬆偏緊,影響到產品的使用功能效果或造成生產線裝配困難.因相關制品尺寸超差或結構位不良導致.4.裝配間隙大:相關制品在組裝後,在邊或角位產生間隙(通常以不大0.2mm為合格).因相應制品變形或尺寸超差及局部缺陷導致.5.裝配刮手(段差或錯位):相關制品在組裝後,邊或角位單獨移出,形成斷面差,觸摸刮手.(通常以不大0.2mm為合格)6.裝配卡鍵(JAM KEY):字鈕鍵組裝到相應鈕孔位,字鈕鍵不能順暢按設計功能作回復運動.字鈕孔位有披鋒或尺寸大,按鈕鍵偏大偏小或高度低等原因導致.7.機身不平(變形):相應制品組裝後在自然放置時,機身底部不平(通常以不大於0.2mm腳不平為合格).相關制品因為尺寸超差,扣位不合,收螺絲不平衡,成型及包裝導致扭曲變形而造成.8.虛扣(扣位高低):相關組合件,組裝後扣位未扣實,用手掰開或跌落震機試驗,扣位會張開形成明顯間隙.扣位尺寸超差或整件尺寸超差(模具成型扣位部分鑲件或行位鬆動變形)導致.9.柱爆(滑牙):柱孔在打螺絲時被打爆裂或發白,或按規定次數重復打螺絲時收不緊(不能受力),柱孔直徑或深度不符,或所用原料機械性能不夠,成型時料溫偏高使機械性能降低而導致.三.塑膠成品一般容易出現的問題:1.噴涂類:(1)塑膠顏色不符:制品外表顏色或蝕紋效果與樣板不一樣(超出一PantoneNo為顏色不符).通常因色粉(色種)配比,原料的底色,料溫的高低造成.(2)顏色不符:噴涂後制品表面顏色不同於樣板或規定的顏色.(通常以一個PantoneNo為標準,超出為不合格).歷為所用油墨色與塑膠件顏色不同,或噴涂層偏厚偏薄導致色差.(3)位置不符:規定噴油的部分未噴或不需噴油的部位被噴上油墨.不明確要求或噴涂工具和程序不合適而導致.(4)粗糙:制品表面噴油層手感不光滑,因噴槍調節不合適,噴涂距離偏近或油墨不符造成.(5)蜂窩點:制品表面噴油層有密集凹陷坑點狀痕.因噴涂方式及噴槍調節不當導致.(6)啞色:指制品表面噴油層不夠光亮,色澤偏暗偏朦.油墨配比不當或噴涂時間距離偏遠或偏近導致.(7)光亮:制品表面噴油層光滑,返光耀眼(通常以樣板程度為標準控制).因油墨配比不當或噴涂層太厚造成.(8)砂紙痕:制品表面噴油層呈現的塊狀條形痕跡.對噴油部位不良缺陷用砂紙加工時,砂紙偏粗,或加工力度偏大導致.(9)有塵:制品表面噴油層呈現,點線狀明顯凸起.因制品暴露在環境中時間偏長,環境不夠干凈,油墨不夠純凈而導致.(10)污糟:指制品表面噴油層有不可擦拭清除的髒物,噴槍用壓縮空氣水分含量大,制品表面髒未清除干淨等因素導致噴油後的污糟。
- 1、下载文档前请自行甄别文档内容的完整性,平台不提供额外的编辑、内容补充、找答案等附加服务。
- 2、"仅部分预览"的文档,不可在线预览部分如存在完整性等问题,可反馈申请退款(可完整预览的文档不适用该条件!)。
- 3、如文档侵犯您的权益,请联系客服反馈,我们会尽快为您处理(人工客服工作时间:9:00-18:30)。
[塑料]塑胶喷涂/丝印工艺、不良缺陷及QC控制要点一、喷漆常见缺陷1. 飞油因套模不正或胶件变形导致油从套缝中飞出: ~) l; n% f& W2. 流油因喷漆末干而流动的油层3. 积油喷漆不均匀积成油块# e' U; o6 R8 Y4. 油渍胶件上粘有油质而导致喷时不上漆5. 油污胶件被油漆污染* | j' r" |5 e& O1 \+ u6 F6 s6. 上色不足喷漆时颜色没有签板深( k! h N2 |$ r& o# H7 G' w7. 砂孔反映在制品表面象砂子大小的孔,打磨后可再加工8 N0 O; B4 y; q4 Z) j8. 走位涂层处理位置不正确,同样板有偏差,调整相应机械或工具可改善9. 起牙边涂层处理后其边参差不齐,调整丝印网版,移印胶头或喷漆模可改善# r) T1 ~! F! l& R4 H# M10. 甩油涂层处理后,表面一块块脱掉,可改变盛放方法及等涂层全干后投入生产11. 反底因胶件或油漆的原因令油层遮盖不到胶件的颜色$ V6 {8 P5 G* x, |$ \: g; N) Q9 |12. 漏喷漆应喷漆而没有喷漆的位置13. 刮花胶件或喷漆层由于外界碰擦而刮花的痕迹4 t" H* b3 m2 S7 M! H14. 色差涂层颜色不一致,异于样板,常见于配套配色胶件; I5 ^. O0 h- n15. 哑色或称无光泽,由油漆质量或喷涂层厚薄所致。
16. 拉丝由于涂层太浓,而致使移开网版,胶头或模具时而留下的丝状物( F7 j2 Z! E0 b1 f: |% p17. 油面末干油面接触到硬物件时,其硬度不够凹下二、移印常见缺陷1. 漏印规定移印的位置末有移印2. 重印移印过多次,图案上易有叠影* P9 D x; `2 n- L% M3 T( T3. 印错位没有将图案印在规定的位置# m/ U, j+ R& ]2 Q3 P! w" q5 Y4. 移位移印的图案位置与规定的位置有误差' v- Y+ |4 k/ I% h" V5. 变形移印的图案的形状与签板规定的形状不完全相同& q! z, q# x1 ?7 U. U8 S/ g6. 油起毛因油干,机头回转时有油层7. 油不清晰因油调得太稀而导致移印在啤件上的图案颜色不明显Z# o4 _2 O9 K9 z* l& ]# m8. 油不均匀油还没调和,致使移印图案清晰程度不完全相同9. 不对色移印图案的颜色与签板的颜色不完全相同10. 套色偏移套色移印时位置发生误差4 k# v/ g. U g* y; O5 m9 ^11. 断线字体或图案自某一部分断开来,看上去不是一个完整的整体( E; _' V& y7 {& n F三、丝印) i) { P% j I: @' a1. 飞油字体、图案边缘出现不规则的图形,比原来印出的图案浅色2. 尘埃字体或图案边缘有多出的小点,小孔或图形缺损& T* R3 T+ G+ @; C- i/ v9 M3. 漏油在不需要印刷的部位多了一些油点,严重的出现大面积油污: R! F! V+ M, X# m: j% r4 z4. 干网字体或图案边角位变得圆滑、无棱角或图案变小5. 起泡印刷面上出现一粒粒的凹凸不光滑图形,如橙皮一样皱纹6. 粘网在图案上出现厚薄不均匀现象,有时印出的油很薄,干后出现砂孔,有时印出的油很厚,干后出现爆裂7. 起丝图案边缘出现一条条的细丝或相连小点9 P0三、喷涂QC工作要项1. 喷涂QC必须使用经批准的参考样板,清楚界定接收/拒收标准。
2. 所有的来料必须核对样板,针对颜色、外观及结构进行检查,及时发现和反映问题,避免不合格物料流入生产。
: n3 S0 m( D0 f8 f2 i; b3. 认识一般胶件喷漆或移印、丝印的生产流程,了解油漆、溶剂的一般性生产问题及使用注意事项。
9 Y- b6 Y/ @' o6 R4. 通过相关工程资料,了解待喷印的胶件材质、油漆颜色、编号,如PP料,搪胶件等。
4 V, ~( M& s9 w2 a+ T1 r' S5. 新开拉的产品,不论是新旧产品都须针对喷漆颜色、位置、形状每一工序检查,及时发现问题,反映问题。
6. 同一工序有若干个喷漆模时,形状和颜色极易偏差,同一产品多个部件或位置喷同一种油漆时,颜色易偏差,QC巡检及收货时须作针对性检查和配套检查。
7. QC巡拉或收货发现问题向上级汇报时,必须附带典型次品样板,了解次品数量及比例,以及次品是否流入后工序及其数量,且须及时追踪上司跟进结果及次品处理情况。
) k# `3 } ~1 p8 d8. 首件产品检查数量为20 PCS,缺陷收0退1,油漆附着力测试数量及频率为每个产品每4小时做10 PCS。
为避免大批量不合格现象,可将喷涂伯放入烘炉中烘烤2小时,使其充分干透、冷却后进行检查。
9. 拒收物料须清楚地标识及隔离,且经过返工后须再次检验方可交付后工序生产。
10. 确保任何让步接收都必须经过管理层的同意和批准。
不合格半成品或末经检验半成品若流入后工序,QC应及时向上级反映并通知相关工序QC跟进。
11. 所有易刮花、擦花喷漆件应保证包装搬运及贮存不良导致大量次品,一般采用胶袋装和垫拷贝纸等方式加以保护。
! w& X0 D7 a; C12. 不论是收货还是退货的标签,必须填写清楚日期、数量及产品名称、检查员姓名,以便于追溯和跟踪。
' j+ C3 {: N% X! x13. 外观缺陷形成的原因主要有:A.工人操作B.模具、胶头、网版C.油墨D胶件质量E.调机技术F.摆放方法等。
5 u% N* H4 U! D0 Z" B- l9 T, T14. 油漆附着力不合格的原因主要有:A用错开油水B.胶件有脱模剂或其它机油C.油漆质量。
15. 油漆、开油水、清漆、硝基漆、油墨、聚合物或其它物质等外来物料须有其制造商提供的质量保证书、合格证书、分析报告或实验室报告(社会认可实验室),并要存档。
& 17. 模具、胶头、网版必须有一个固定的清洗周期,所有用于清洁的溶剂、溶液须符合要求。
18. 所有油漆、溶剂及喷具的清洁介质必须有明确的标记,以免混用误用。
4 u. x) h) b* k19. 所有模具、胶头、网版须设定编号及明显标记,以便识别,且需建立相应的摆放清单,并保存在一个合理的条件下。
20.所有油漆、溶剂等化学品应参照下图加贴警戒标志,以确保职业安全健康。
2 d- B* `! m9 H `' Y;四、喷漆装饰工艺2 e; d b* C3 f' O* R2 D7 S K一、涂料/油漆' s3 ^& W8 ]% u) _8 R含有颜料或不含颜料的以树脂或油制成的混合液体涂于需装饰物表面(主要指塑胶表面)经干燥,硬化成坚韧的涂膜,起到保护作用,此种混合液体即称之为油漆。
二、喷漆生产概念用压缩空气作为动力使油漆从喷枪嘴中喷出呈雾状而只得覆于工件表面的一种涂漆方式。
地般需配有喷漆模具以确定喷涂位置,不需喷剂的位置被模具遮盖,不用喷漆模具的喷漆y 方式叫散枪喷漆。
. ^) r+ y1 [7 b2 I: L三、喷漆装饰的评价优点:油漆快干,密着性好,施工高效,对于涂面几何结构复杂的表面大都能获得薄而均的涂层效果。
+ }9 m& z" n/ t5 F缺点:损耗量大,扩散于空气中的油漆有害人体,施工环境要求有良好抽气通风系统。
四、喷漆生产工艺流程工件清洁表面喷漆模边夹模或散枪QC首检QC巡检9 c* X+ U4 o% i$ ]- D# C油漆喷漆生产自然风干$ g# F8 }% z) K+ N. g调稀油漆及过滤C% o/ O: u6 J! Z7 U3 e2 N' }开油水加漆试喷QC抽检喷枪调节出油量喷漆半成品包装出货(一)工件:7 n' Z) N& k' P2 o1.油漆及溶剂须同工件材质相配合。
硬胶、软胶、PP料、金属表面、橡胶料和电镀件0 k5 Z. m% J! Z1 @" J/ ]$ q# n2.检查喷漆表面是否有注塑及处理过程中产生的脱模剂类物质会造成喷漆不上油及易甩油。
a& N% J: S1 m$ z M! T3.检查喷漆表面不可存在包装不良或环境造成的灰尘、脏物、污染。
4.检查喷漆胶件不可有缩水、变形现象,此类缺陷易造成胶件不合模而导致飞油。
( 二)油漆特性1.油漆的作用对被施工物体(如胶件、家具等)起装饰和保护作用。
2.油漆的组成:/ }1 w) g8 O+ F$ ]" p由树脂(RESIN),颜料(PIGMENT),溶剂(SOLVENT)三种成份组成。
油漆由挥发部分和不挥发部分组成,挥发部分主要是溶剂(由辅助成膜的物质组成);不挥发部分由树脂油脂(主要成膜物质)和颜料(次要成膜物质)组成。
(1树脂/油增加光泽/胶接能力/耐磨能力+ z2 ]9 \; k, a9 e6 }(2)颜料赋予色彩/增加机械强度/增加耐光性、耐水性及耐硬性% P3 P$ N6 ]0 a: G' l$ X (3)稀释剂稀释颜料以使其易于喷涂,降低漆料粘度,增加渗透力,但加入太多会损害光泽(4)添加剂产生光泽、半光泽或无光泽涂层(5)打底剂喷涂前在底层使用打底剂以提高质量3.油漆的制成a、可溶性颜料加开油水搅拌成色浆;b、不可溶性颜料研磨成粉状加一定树脂和开油水搅拌成色浆。
) F; d& k0 k3 [, G9 S4.漆的适用性软胶和硬胶相应使用软胶油和硬胶油。
a. 软胶是指PVC等和搪胶类;软胶油主要是聚氯乙稀树脂漆,软胶开油水含环已酮成份。
+ k: b, ~2 j% Y$ L3 gb. 硬胶是指ABS,GPPS(聚苯已烯),HIPS(改性聚苯已烯),PC(防弹胶),POM(CELON)即赛钢等;. 硬胶油主要是由丙烯酸,醇酸树脂,织维素漆组成,硬胶开油水含MEK(丁酮)成份。
5.开油水一般配方(具体比例一般随气候变化而变化)! H3 K. O3 X& ^! z软胶开油水成份:二甲苯(树脂溶剂)丁酮(助挥发溶剂)! w& |+ b: P; b v& d环已酮(湿润胶件表面,改善平流性,# K% G1 H. c5 Y) K* { D5 E# z7 A移印时均用此溶剂作开油水)1 A' @4 M _ E! S" @. X5 [( w丙酮(去油作用)硬胶开油水成份:甲苯(树脂溶剂)MEK+防潮剂(湿润剂)醋酸丁脂(挥发慢树脂溶剂)6.油漆分类(按施工方法分)% \7 b u$ i5 }刷漆、烘漆、喷漆、电泳漆等,玩具行业主要是喷漆.' W5 W4 x' n$ r4 @2 v8 k(四)喷枪枪顶针可调节出油量的大小,喷漆操作要求:喷着压力-----以3.0-3.5kg/cm2为宜喷出量-----因油漆粘度、压力不同,可自由调节喷枪喷出形状-----可自由调节喷枪中部之控制螺旋喷漆距离-----一般以20-40cm为宜,需视喷漆模和胶件情况而定- {$ K+ x' p6 T' \; s1 [' }0 z0 l 速度-----以喷出1m/2s为宜' h8 U- E, c' J4 z O# D5 Q( }涂膜的重叠-----应注意喷着面1/3区域重叠喷漆(五)溶剂! T/ ? e, y" ]8 x6 Z常用溶液的认识溶液名称用途% e f4 n h' E t7 N. W) |' L白火酒用于清洁胶件表面污渍、消毒,使用时避免接触金属。