真空感应熔炼新技术
真空感应炉冶炼原理及工艺

2.3 罗茨泵
罗茨真空泵(简称罗茨泵)是一种旋转式变容真空泵。根据罗茨真空泵工作范围的 不同,又分为直排大气的低真空罗茨泵、中真空罗茨泵(又称机械增压泵)和高真空多 级罗茨泵。
图 5 罗茨真空泵结构示意图
4
罗茨泵的结构如图 5 所示。在泵腔内,有二个“8”字形的转子相互垂直地安装在一 对平行轴上,由传动比为 1 的一对齿轮带动作彼此反向的同步旋转运动。在转子之间, 转子与泵壳内壁之间,保持有一定的间隙,可以实现高转速运行。由于罗茨泵是一种无 内压缩的真空泵,通常压缩比很低,故高、中真空泵需要前级泵。罗茨泵的极限真空除 取决于泵本身结构和制造精度外,还取决于前级泵的极限真空。为了提高泵的极限真空 度,可将罗茨泵串联使用。 实际设备中往往用多个泵的串联来组成真空泵组,获得真空室中符合要求的真空 度。
3.1 感应加热原理
感应熔炼是除电弧炉以外较重要的一种电炉熔炼方法。与电弧炉相比,其特点有: (1)电磁感应加热。由于加热方式不同,感应炉没有电弧加热所必须的石墨电极, 从而杜绝了电极增碳的可能,因而可以熔炼电弧炉很难熔炼的含碳量极低的钢和合金。 (2)熔池中存在一定强度的电磁搅拌,可促进钢水成分和温度均匀,钢中夹杂合 并、长大和上浮。 (3)熔池比表面积小。优点是熔炼过程中容易控制气氛,无电弧及电弧下高温区, 合金元素烧损少、吸气少,所以有利于成分控制、气体含量低和缩短熔炼时间;缺点是 渣钢界面面积小,再加上熔渣不能被感应加热,渣温低,流动性差,反应力低,不利于 渣钢界面冶金反应的进行,特别是脱硫、脱磷等,因而对原材料要求较为严格。 (4)烟尘少对环境污染小。熔炼过程中基本无火焰,也无燃烧产物。 感应加热原理主要依据两则电学基本定律。一是法拉第电磁感应定律: E B L v sin (v B)
真空感应熔炼原理及工艺
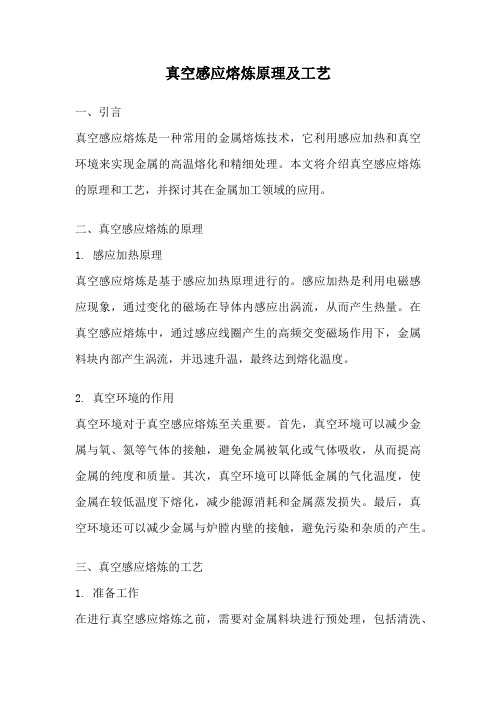
真空感应熔炼原理及工艺一、引言真空感应熔炼是一种常用的金属熔炼技术,它利用感应加热和真空环境来实现金属的高温熔化和精细处理。
本文将介绍真空感应熔炼的原理和工艺,并探讨其在金属加工领域的应用。
二、真空感应熔炼的原理1. 感应加热原理真空感应熔炼是基于感应加热原理进行的。
感应加热是利用电磁感应现象,通过变化的磁场在导体内感应出涡流,从而产生热量。
在真空感应熔炼中,通过感应线圈产生的高频交变磁场作用下,金属料块内部产生涡流,并迅速升温,最终达到熔化温度。
2. 真空环境的作用真空环境对于真空感应熔炼至关重要。
首先,真空环境可以减少金属与氧、氮等气体的接触,避免金属被氧化或气体吸收,从而提高金属的纯度和质量。
其次,真空环境可以降低金属的气化温度,使金属在较低温度下熔化,减少能源消耗和金属蒸发损失。
最后,真空环境还可以减少金属与炉膛内壁的接触,避免污染和杂质的产生。
三、真空感应熔炼的工艺1. 准备工作在进行真空感应熔炼之前,需要对金属料块进行预处理,包括清洗、切割和称重等。
同时,还需要准备好感应线圈、感应炉膛和真空系统等设备,并进行检查和调试,确保正常运行。
2. 熔炼过程将预处理好的金属料块放入感应炉膛内,然后启动感应线圈,产生高频交变磁场。
金属料块受到磁场的作用,内部涡流产生,温度迅速升高,最终达到熔化温度。
同时,开启真空系统,将炉膛内的气体抽出,形成真空环境。
在熔炼过程中,可以根据需要进行金属的合金化和成分调整。
3. 精细处理在金属熔化后,可以进行一系列的精细处理,包括脱气、去杂、调温等。
通过控制真空度和温度,可以实现金属的脱气和杂质的去除,提高金属纯度和质量。
同时,还可以根据需要调整金属的温度,以满足后续工艺的要求。
四、真空感应熔炼的应用真空感应熔炼广泛应用于金属材料的制备和加工领域。
首先,它可以用于高纯度金属的制备,如高纯铜、高纯铝等。
其次,它可以用于合金的制备,如钢、铜合金等。
此外,真空感应熔炼还可以用于金属粉末的制备、金属材料的再生利用等方面。
金属冶炼中的新技术与新材料

连铸连轧技术
总结词
高效、节能的金属加工技术
详细描述
连铸连轧技术是一种高效、节能的金属加工技术,将铸造和轧制工艺连续进行 ,实现金属材料的连续加工。该技术具有生产效率高、节能降耗、降低生产成 本等优点,广泛应用于钢铁、有色金属等领域。
CHAPTER
新设备在金属冶炼中的应用
真空冶炼设备
真空感应熔炼炉
利用真空条件下,通过感 应加热原理熔炼金属,具 有熔炼温度高、杂质去除 效果好等优点。
真空电弧熔炼炉
通过电弧在真空条件下加 热和熔炼金属,可实现高 熔速、高纯净度熔炼。
真空电子束熔炼炉
利用电子束在真空条件下 对金属进行加热和熔炼, 具有熔炼温度高、纯净度 高、节能环保等优点。
废水处理技术
01
沉淀法
通过添加沉淀剂使废水中的重金 属离子或悬浮物沉降下来,达到 净水的目的。
生物处理法
02
03
高级氧化技术
利用微生物的代谢作用,将废水 中的有机物转化为无害的物质, 达到净水的目的。
通过强氧化剂将废水中的有机物 氧化成无害的物质,达到净水的 目的。
废渣处理技术
压实法
通过压实机将废渣压缩成块,减少体积,便于运输和 处置。
固化法
通过添加固化剂将废渣中的有害物质固定在固化体中 ,减少对环境的危害。
焚烧法
通过高温焚烧将废渣中的有害物质燃烧成无害的物质 ,达到处置的目的。
04
CHAPTER
新工艺在金属冶炼中的应用
真空感应熔炼技术的发展及趋势
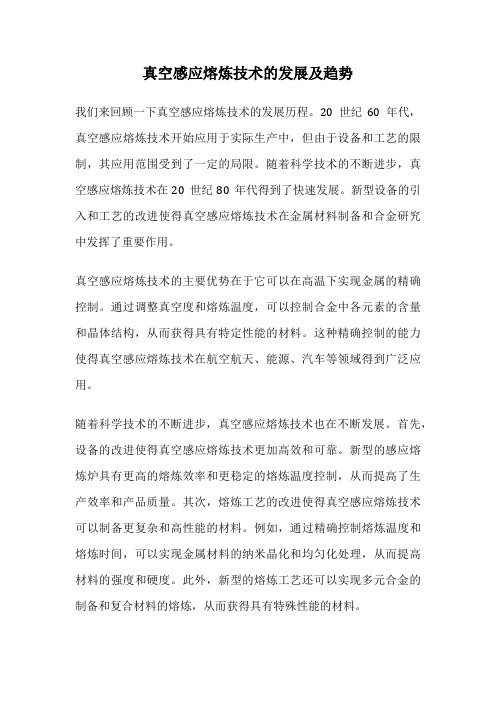
真空感应熔炼技术的发展及趋势我们来回顾一下真空感应熔炼技术的发展历程。
20世纪60年代,真空感应熔炼技术开始应用于实际生产中,但由于设备和工艺的限制,其应用范围受到了一定的局限。
随着科学技术的不断进步,真空感应熔炼技术在20世纪80年代得到了快速发展。
新型设备的引入和工艺的改进使得真空感应熔炼技术在金属材料制备和合金研究中发挥了重要作用。
真空感应熔炼技术的主要优势在于它可以在高温下实现金属的精确控制。
通过调整真空度和熔炼温度,可以控制合金中各元素的含量和晶体结构,从而获得具有特定性能的材料。
这种精确控制的能力使得真空感应熔炼技术在航空航天、能源、汽车等领域得到广泛应用。
随着科学技术的不断进步,真空感应熔炼技术也在不断发展。
首先,设备的改进使得真空感应熔炼技术更加高效和可靠。
新型的感应熔炼炉具有更高的熔炼效率和更稳定的熔炼温度控制,从而提高了生产效率和产品质量。
其次,熔炼工艺的改进使得真空感应熔炼技术可以制备更复杂和高性能的材料。
例如,通过精确控制熔炼温度和熔炼时间,可以实现金属材料的纳米晶化和均匀化处理,从而提高材料的强度和硬度。
此外,新型的熔炼工艺还可以实现多元合金的制备和复合材料的熔炼,从而获得具有特殊性能的材料。
未来,随着科学技术的不断进步,真空感应熔炼技术将会继续发展并发挥更大的作用。
首先,随着新材料的涌现,真空感应熔炼技术将在新材料的制备和研究中发挥重要作用。
例如,通过引入新的合金元素和控制熔炼工艺,可以实现新型材料的制备,如高温合金、超导材料和高强度钢等。
其次,随着环保意识的提高,真空感应熔炼技术将在资源循环利用和废弃物处理中发挥重要作用。
例如,通过回收废旧金属和利用废弃物进行熔炼,可以实现资源的有效利用和环境的可持续发展。
真空感应熔炼技术是一项重要的金属材料制备和加工技术,其发展历程和未来趋势与科学技术的进步密切相关。
通过不断改进设备和工艺,真空感应熔炼技术将在新材料制备、环境保护和资源循环利用等方面发挥更大的作用。
真空感应熔炼技术的发展及趋势

真空感应熔炼技术的发展及趋势引言真空感应熔炼技术是一种将金属材料在真空条件下进行熔化和铸造的先进技术方法。
它具有高纯度、无气孔、低含氧量等优点,广泛应用于金属材料制备和铸造领域。
本文将对真空感应熔炼技术的发展历程和未来趋势进行全面、详细的探讨。
二级标题:真空感应熔炼技术的发展历程真空感应熔炼技术起源于20世纪50年代,经过多年的发展和改进,取得了显著的成果。
下面将具体介绍几个重要的发展阶段。
三级标题:第一阶段:真空感应熔炼技术的初步研究(20世纪50年代-70年代)在这一阶段,研究人员主要关注真空对金属材料熔炼和铸造过程的影响。
通过实验和理论研究,他们发现真空条件下可以有效地减少杂质氧化、氢的生成和熔体的不均匀性。
真空感应熔炼技术逐渐在实际生产中得到应用,并取得了一定的经济效益。
三级标题:第二阶段:真空感应熔炼技术的关键突破(80年代-90年代)在这一阶段,随着材料科学和金属工艺技术的进一步发展,真空感应熔炼技术取得了一系列关键突破。
研究人员设计了更加高效的感应加热系统,提高了熔炼速度和材料的均匀性。
同时,他们还引入了先进的气体保护措施,进一步降低了杂质含量和气孔率。
这些改进使得真空感应熔炼技术在高精度合金和特殊金属材料制备中得到广泛应用。
三级标题:第三阶段:真空感应熔炼技术的自动化与智能化发展(21世纪以来)随着信息技术的不断发展,真空感应熔炼技术开始向自动化和智能化方向发展。
研究人员通过引入先进的传感器和计算机控制系统,实现了对真空熔炼过程的实时监测和控制。
同时,他们还开发了一系列智能化铸造设备,能够根据不同材料的性质和要求自动调整工艺参数。
这些技术的引入使得真空感应熔炼技术更加高效、可靠,进一步拓宽了其应用领域。
二级标题:真空感应熔炼技术的未来趋势三级标题:高能效与低污染随着人们对可持续发展和环境保护的关注不断增加,真空感应熔炼技术的未来趋势将更加注重高能效和低污染。
研究人员将进一步提高熔炼设备的能源利用效率,降低能耗和碳排放。
真空感应熔炼炉工艺特点及其技术进展
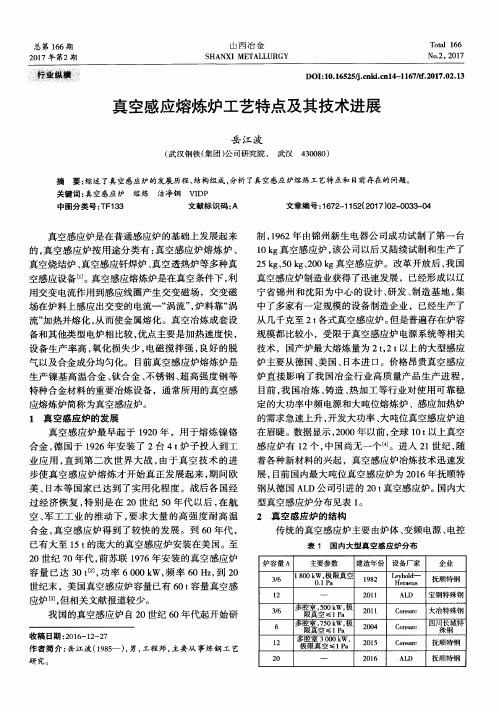
L e v bபைடு நூலகம்n l d — 抚顺特钢
A L D 宝 钢 特殊 钢
我国的真空感应炉 自2 0 世纪 6 0年代起开始研
收 稿 日期 : 2 0 1 6 —1 2 — 2 7
3 / 6
6
1 2
多腔室 , 5 0 0k W, 极 2 0 1 1 限真 空 ≤ 1 P a 多腔室 , 7 5 0 k W, 极 2 o o 4 限真 空 ≤ 1 P a
传统 的真 空感 应炉 主要 由炉 体 、 变频 电源 、 电控
表1 国 内大 型 真 空 感 应 炉分 布
炉容量 / t 3 , 6
1 2
主要参数
0 . 1 P a
建造年份 设备厂家
He r a e u s
企业
1 8 0 0 k W, 极 限真空 1 9 8 2
熔炼
洁净钢
V I DP
文献标识l i  ̄ : A 文章编号 : 1 6 7 2 — 1 1 5 2 ( 2 0 1 7 ) 0 2 — 0 0 3 3 — 0 4
真 空感应 炉是 在普 通感 应炉 的基 础 上发 展起 来 的, 真 空 感应 炉 按 用 途分 类 有 : 真 空感 应 炉 熔炼 炉 、 真 空烧 结炉 、 真 空感应 钎焊 炉 、 真 空 透热 炉等 多种 真 空感 应 设备 n ] 。真 空感应 熔 炼炉是 在 真空条 件下 , 利 用交 变 电流作 用 到感应 线 圈产 生交 变磁 场 ,交 变磁 场 在炉 料上感 应 出交 变 的电流一 “ 涡流 ” , 炉 料靠 “ 涡
流” 加热并熔化 , 从而使金属熔化。真空冶炼成套设 备 和其 他类 型 电炉相 比较 , 优点 主要 是 加热 速度 快 ,
3.真空感应炉熔炼-西安建筑科技大学
3[Ca]+2[P]=Ca 3P2
参与反应的钙可以 是金属钙也可以是 钙的合金(硅钙合 金)或钙的化合物 (CaC2)
31
3.6 新技术在感应炉冶炼中的应用
反应产物Ca3P2不溶于钢液,在炼钢温度下会以液态上浮而进入 渣中,在炼钢条件下不稳定,是一种强的还原剂,当炉内气氛氧 势偏高和渣中存在易还原的氧化物时,会发生如下反应:
镁特定的物化性质决定着,在镁的加入操作中,镁的加入 方式回收率的控制都是难以完善解决的工艺问题,使用镁合金 如:Ni-Mg、Ni-Mg-Me以降低镁的蒸汽压,提高熔点和沸点。 镁处理的操作过程为: 精炼期结束后,若要求添加B、Ce,在B、Ce加入后,调节 熔池温度,使温度低于出钢温度20℃; 真空室内充高纯氩气至13-27kPa; 镁以块状的含镁中间合金加入金属熔池; 镁加入后立即大功率搅拌,时间不宜过长,为减少镁的 损失,加镁后,通常1-5min内出钢;
22
3.3真空感应炉冶炼工艺过程
3.3.4 出钢和浇注
合金化结束后,坩埚中的金属液达到预定的成分 和温度,真空度也符合要求,则可出钢; 采用真空浇注,小型炉用上注,大型炉也可以下 注。
23
3.4元素的挥发与控制
所有金属都存在一个平衡的蒸汽压pi*,它取决于该金属的物 性、气态的存在形式(单原子、双原子还是多原子组成气态分 子)以及温度。i物质的蒸汽压pi*,与温度的关系式为:
40CrNiMo(SAE4340),(C:0.42%;Mn:0.76%;Cr:0.77%;
Ni:1.67%;Mo:0.20%)
14
3.1.3 真空感应炉熔炼的特点
不同熔炼方法生产的钢与合金中夹杂物含量
钢与合金
Cr20 Cr16Ni25W5AlTi2 氧化物夹杂/%
真空感应炉熔炼工艺
真空感应炉熔炼工艺真空感应熔炼VIM是在真空条件下,利用电磁感应在金属导体内产生涡流加热炉料进行熔炼的方法,具有熔炼室体积小,抽真空时间和熔炼周期短,便于温度压力控制、可回收易挥发元素、准确控制合金成分等特点;由于以上特点,现在已发展为特殊钢、精密合金、电热合金、高温合金及耐蚀合金等特殊合金生产的重要工序之一;1、基本原理:真空感应熔炼的两个基本原理应用是:感应加热和真空环境;感应熔炼是除电弧炉以外较重要的一种电炉熔炼方法;与电弧炉相比,其特点有:1电磁感应加热;由于加热方式不同,感应炉没有电弧加热所必须的石墨电极,从而杜绝了电极增碳的可能,因而可以熔炼电弧炉很难熔炼的含碳量极低的钢和合金;2熔池中存在一定强度的电磁搅拌,可促进钢水成分和温度均匀,钢中夹杂合并、长大和上浮;3熔池比表面积小;优点是熔炼过程中容易控制气氛,无电弧及电弧下高温区,合金元素烧损少、吸气少,所以有利于成分控制、气体含量低和缩短熔炼时间;缺点是渣钢界面面积小,再加上熔渣不能被感应加热,渣温低,流动性差,反应力低,不利于渣钢界面冶金反应的进行,特别是脱硫、脱磷等,因而对原材料要求较为严格;4烟尘少对环境污染小;熔炼过程中基本无火焰,也无燃烧产物;感应加热的原理:感应加热原理主要依据两则电学基本定律:一是法拉第电磁感应定律:E=B·L·v·sin∠v·BE:导体两端所感应的电势;B:磁感应强度;v:相对速度;∠v·B:磁感应强度的方向与速度方向之间的夹角;当一座无芯感应炉的感应线圈中通有频率为f的交变电流时,则在感应圈所包围的空间和四周产生一个交变磁场,该交变磁场的极性、磁感应强度与交变频率随着产生该交变磁场的交变电流而变化;若感应线圈内砌有坩埚并装满金属炉料,则交变磁场的一部分磁力线将穿过金属炉料,磁力线的交变就相当于金属炉料与磁力线之间产生了切割磁力线的相对运动;因此,在金属炉料中将产生感应电动势E,其大小通常以下式确定:E=Ф·f·nФ:感应线圈中交变磁场的磁通量,Wb;f:交变电流的频率,Hz;n:炉料所形成回路的匝数,通常n=1;二是焦耳-楞茨定律:又称为电流热效应原理;当电流在导体内流动时,定向流动的电子要克服各种阻力,这种阻力用导体的电阻来描述,电流克服电阻所消耗的能量将以热能的形式放出;这就是电流的热效应:Q=I2RtQ: 焦耳-楞茨热,J;I:电流强度,A;R:导体电阻,Ω;t:导体通电时间,s;当感应炉通以交流电后,在感应线圈内坩埚里的金属炉料由一法拉第电磁感应定律产生感应电动势,由于金属炉料本身形成一闭合回路,所以在金属炉料中产生感应电流:I=Ф·f/R,R:金属炉料的有效电阻,Ω;该感应电流又依照二焦耳-楞茨定律在炉料中放出热量,使炉料被加热;真空冶金的原理:影响一个化学反应的外部因素主要是:温度、浓度和压力;真空冶金就是通过改变外界压力对冶金过程中诸多化学反应中有气相参加的反应产生影响,当反应生成物中的气体摩尔数大于反应物中的气体摩尔数,减小系统的压力即增加真空度则可以使平衡反应向着增加气态物质的方向移动,促使反应进行的更完全;以下几类反应器中发生的反应属于此类:真空下的碳脱氧反应:〔C〕+〔O〕→CO↑真空下的脱气反应: 2〔H〕→H2↑2〔N〕→N2↑金属中元素的挥发:〔Me〕→Me↑1 在真空环境下,碳的行为很有意思;在常压下,碳的脱氧能力较弱,因此常用金属脱氧剂如硅、铝等来进行沉淀脱氧,但硅、铝脱氧后形成的氧化物夹杂会部分残留在钢中,降低钢的纯洁度;在一般条件下,当钢中〔C〕=%,与之平衡的〔O〕=%,当钢中〔C〕降低时,与之平衡的〔O〕还要升高,而现今有些特殊用途的钢和合金中的氧含量要求又远低于%,因而在一般条件下仅用碳来脱氧是达不到脱氧要求的;碳氧反应的平衡常数为:K=P CO/a c ·a O= P CO/〔%C〕·f C·〔%O〕·f O即:〔%C〕·〔%O〕= P CO/K由于K值在某一温度下是一常数,当将炉内CO不断抽走,即降低炉内的P CO,〔%C〕·〔%O〕的数值也会同时降低,即在真空条件下,碳氧反应会进行的更完全;当气相压力降至时,碳的脱氧能力可超过硅;若气相压力降至时,碳的脱氧能力可超过铝;但碳的脱氧能力并不会随着真空度的提高而无限制的提高,因为只有液气分界面的碳氧反应仅只遵循上述热力学原理,金属液体内部的碳氧反应不仅遵循上述热力学原理,还要受到动力学条件的约束;金属液体内部如果要形成CO气泡,那么CO的生成压必须大于炉气压力、气泡产生处金属液柱的静压力和表面张力造成的压力之和;因而仅减小炉气压力即增加真空度是不够的,此时限制碳脱氧的主要因素是表面张力和静压力;此原理不仅能降低溶解于金属中的氧,还能还原金属夹杂中的氧,如: MnO+〔C〕→〔Mn〕+CO↑SiO2+2〔C〕→〔Si〕+2CO↑Al2O3+3〔C〕→2〔Al〕+3CO↑同时,真空下碳这一特性也会作用于坩埚耐火材料;在真空熔炼的精炼期,此时熔池处于高温、高真空下,炉衬中的氧化物及杂质会分解并与碳发生还原反应;因而坩埚材料的选择很重要;由于以上过程的存在,反过来也会消耗〔C〕,降低钢中〔C〕;2真空下的脱气:金属中的气体是指溶解在其中的氢和氮而言;氢和氮在空气中以分子状态存在,在金属中则以单原子或离子状态存在,这种双原子气体在金属中的溶解度与气体分压力的平方根成正比;〔%H〕=K H√P H2〔%N〕=K N√P N23真空下杂质及合金元素的挥发:在真空条件下,金属中某些蒸气压较高的元素,当熔室内压力降低至低于其蒸气压力时,这些元素就会从液态金属中挥发出来;因而应合理制定工艺制度,促进杂质的挥发、减少有用元素的挥发;500kg真空感应炉1、真空系统2、加料系统3、感应线圈4、坩埚5、电源6、锭模车2、真空感应炉熔炼的工艺过程:就是结合真空冶金与感应熔炼的特点制定合理有效的工艺;其整个周期可分为以下几个主要阶段,即装料、熔化、精炼、浇注;(1)装料:真空感应炉所用炉料一般都是经过表面除锈和油污后的高纯原料,有的合金元素还以纯金属形式加入;严禁采用潮湿的炉料,以免带入气体和在熔炼时产生喷溅;装料时,应做到上松下紧,以防熔化过程中上部炉料因卡住或焊接而出现“架桥”;在装大料前,应先在炉底铺垫一层细小的轻料;高熔点不易氧化的炉料应装在坩埚的中、下部高温区;易氧化的炉料应在金属液脱氧良好的条件下加入;易挥发的元素加入时,熔炼室应先充以惰性气体Ar为好;(2)熔化期:装料完毕后,应开始抽真空;当真空室压强达到时,便可送电加热炉料;熔化初期,由于感应电流的集肤效应,炉料逐层熔化;这种逐层熔化非常有利于去气和去除非金属夹杂,所以熔化期要保持较高真空度和缓慢的熔化速度;所以开始熔化时不要求输入最大的功率,而是根据金属炉料的不同特点,逐级增加输入功率,使炉料以适当的速度熔化;若熔化过快,则气体有可能从金属液中急剧析出,这将会引起熔池的剧烈沸腾,甚至产生喷溅;如果发生喷溅,可采取降低熔化速度减小输入功率或适当提高熔炼室压力关闭真空阀门或充入一定量的惰性气体的方法加以控制;若采用两次加料熔化时,第二次炉料应在坩埚炉料熔化70%~80%时加入,并等到补加料开始发红后再提高输入功率,以免冷料突然加入而放出大量气体产生喷溅;当金属全部熔化,熔池表面无气泡逸出时,熔炼进入精炼期;(3)精炼期:精炼期的主要任务是:脱氧、去气、去除挥发性夹杂、调整温度、调整成分;为完成上述任务必须控制好精炼温度、真空度和真空下保持时间等工艺参数;a、精炼温度:温度升高有利于碳氧反应的进行、夹杂的分解挥发;但温度过高会加剧坩埚与金属间的反应、增加合金元素的挥发损失,所以通常合金钢的精炼温度控制在所炼金属的熔点以上100℃;b、真空度:真空度提高将促进碳氧反应,随着CO气泡的上浮排出,有利于〔H〕和〔N〕的析出、非金属夹杂的上浮、氮化物的分解、微量有害元素的挥发;但过高的真空度会加剧坩埚与金属间的反应、增加合金元素的挥发损失,所以对于大型真空感应炉,精炼期的真空度通常控制在15~150Pa;小型炉则控制在~1Pa;c、真空下保持时间:金属液内氧含量是先降后升的,所以当氧含量达到最低值的时间就是精炼时间,500kg的炉子精炼时间为50~70min;炉料熔清后,应立即加入适量的块状石墨或其他高碳材料进行碳氧反应;精炼后期,充分脱氧、去气、挥发夹杂物时,加入活泼金属和微量添加元素,调整成分,加入顺序一般为Al、Ti、Zr、B、Re、Mg、Ca,应做到均匀、缓慢,以免产生喷溅,加入后用大功率搅拌1~2min,以加速合金的熔化和分布均匀,由于Mn的挥发性较强,一般在出钢前3~5min加入;4浇注:合金化后,温度成分合格后即可出钢浇注;浇注时采用保温帽或绝热板;对于成分复杂的高温合金,浇注后可在真空下冷却;3、结语:真空感应熔炼作为制造高温合金、精密合金、特殊功能材料等的重要工序之一,其作用将越来越重要、应用将越来越广泛;。
真空感应熔炼炉原理
真空感应熔炼炉原理
真空感应熔炼炉是一种利用感应加热和真空环境进行金属熔炼和精炼的设备。
其原理可以归纳如下:
1. 感应加热原理:感应加热是利用变化磁场在金属导体中产生涡流并产生热量的过程。
当通电线圈中通过交流电时,会产生变化的磁场,这个磁场会穿透到工作线圈中的金属导体。
金属导体由于交变磁场的作用,导致其内部产生涡流。
涡流通过电阻热效应产生热量,使金属导体迅速升温。
2. 真空环境:真空状况下,可以有效地减少氧气、水蒸气等气体对金属的污染和氧化。
同时,真空环境可以避免金属表面的气体泡沫和熔渣的形成,提高金属的纯度和质量。
真空感应熔炼炉的工作过程如下:
1. 在感应熔炼炉中,先将金属材料放入感应线圈中,在外部供电的作用下,感应线圈中产生变化的磁场。
2. 由于金属导体的存在,感应线圈中的变化磁场会产生涡流,并在金属导体内部产生热量。
3. 金属材料在涡流的作用下,迅速升温,最终达到熔点,开始熔化。
4. 在金属熔化的同时,真空泵将炉腔中的气体抽除,使腔内形成高真空环境。
5. 在高真空环境下进行熔炼和精炼过程,可以避免污染、氧化以及气泡和熔渣的形成,提高金属的纯度和质量。
6. 当金属熔化、纯化达到要求后,通过倾炉或其他方式,将熔融金属倒出。
通过上述原理和工作过程,真空感应熔炼炉可以实现对金属材料的高温融化和精炼,具有较高的熔炼效率和精度。
同时,利用真空环境可以提高金属材料的纯度和质量,适用于各种金属的熔炼和冶炼工艺。
金属冶炼中的真空冶炼技术
对于一些难以通过常规方法制备的特殊合金,如高强度铝合金、钛 合金等,真空感应熔炼技术也具有显著优势。
有色金属熔炼
除了钢铁等黑色金属外,真空感应熔炼技术也可应用于铜、铝等有 色金属的熔炼和提纯。
CHAPTER 03
真空电弧熔炼
真空电弧熔炼原理
真空电弧熔炼是在高真空条件下,利 用电流通过金属电极(通常为两根石 墨电极)产生电弧来熔炼金属的工艺 。
金属冶炼中的真空冶 炼技术
汇报人:可编辑 2024-01-06
目录
• 真空冶炼技术概述 • 真空感应熔炼 • 真空电弧熔炼 • 真空电子束熔炼 • 真空冶炼技术的发展趋势与展望
CHAPTER 01
真空冶炼技术概述
定义与原理
定义
真空冶炼技术是指在真空环境中进行 的金属冶炼过程,通过降低压力和气 体含量,实现金属的高效提取和纯化 。
电子枪是设备的核心部分 ,能够产生高能电子束。
真空室用于提供熔炼所需 的真空环境,同时收集和 排出熔炼过程中产生的气 体和烟尘。
控制系统用于控制设备的 各项参数,保证熔炼过程 的稳定性和准确性。
冷却系统用于控制设备的 温度,保证设备的稳定运 行。
真空电子束熔炼工艺参数
真空度
电子束功率
真空度是影响熔炼过程的重要参数,它决 定了熔炼过程中气体的分压,从而影响金 属的纯度和凝固组织。
真空电子束熔炼
真空电子束熔炼原理
电子束熔炼是一种利用高能电 子束作为热源的真空熔炼技术 。
电子束熔炼过程中,高能电子 束与金属材料相互作用,使金 属材料熔化并形成液态金属。
液态金属在真空环境下进行净 化、精炼和凝固,最终得到高 纯度、高性能的金属材料。
真空电子束熔炼设备
- 1、下载文档前请自行甄别文档内容的完整性,平台不提供额外的编辑、内容补充、找答案等附加服务。
- 2、"仅部分预览"的文档,不可在线预览部分如存在完整性等问题,可反馈申请退款(可完整预览的文档不适用该条件!)。
- 3、如文档侵犯您的权益,请联系客服反馈,我们会尽快为您处理(人工客服工作时间:9:00-18:30)。
一、真空感应炉国内外的发展现状
真空感应炉大约始于1920年,用于熔炼镍铬合金。
直到第2次世界大战,由于真空技术的进步使真空感应炉熔炼才开始真正发展起来。
1926年德国用真空感应炉(容量4t,功率350kw)熔化Co、Ni合金。
二战期间欧美等国家已达到了实用化程度并取得了飞速发展,日本也相继采用。
这种方法多用于熔炼耐热钢、轴承钢、纯铁、铁镍合金、不锈钢等多种金属材料。
这一方法使材料的断裂强度、高温韧性、耐氧化性等都得到了改善。
由于大型真空抽气设备(如增压泵)的出现,真空感应炉也逐步向大型化发展。
以美国为例,1969年真空感应炉的容量已达到27.60t的规模。
满足了各种金属材料工业化生产的要求。
西欧各国也在20世纪60年代,将炉子向大型化发展并不断改进,可在冶炼过程中不破坏真空,在装料、铸模准备及浇铸操作等过程实现连续的或半连续的真空感应熔炼。
美国consarc公司和德国ALD是目前国际上最主要的大型真空感应熔炼炉制造企业,生产的大型真空感应熔炼炉可以达到30t,甚至更大。
中国自行生产的真空感应熔炼炉的容量一般比较小,主要为5-1500kg。
2t 以上的大型感应炉主要从德国、美国、日本进口。
20世纪80年代初,抚钢在国内率先从德国引进3t/6t大型真空感应炉。
从90年代以后国内宝钢特钢、东北特钢和攀长钢等企业先后从国外引进了大型真空感应炉,最大容量为12t。
目前正在引进的最大容量为24t。
二、新技术在真空感应炉的应用
1. 电磁搅拌和惰性气体搅拌
感应炉冶炼本身已存在较强烈的搅拌作用,加上电磁搅拌后,气体上升到熔液界面大量析出,对于材料的去气有很好的效果。
必须注意的是,要选择合适的搅拌功率,避免对炉衬的过度冲击。
在气体搅拌时,惰性气体通过注入坩埚底部的锥型多孔塞进入熔池。
当惰性气体穿过熔融金属时,气泡体积和表面积增大,靠近金属液面时,体积明显膨胀,使气体和金属间有更高的比表面进行交换反应,缩短了熔液表面的更换周期,并改善整个熔池的均匀性。
同时,还使细小的氧化物聚集,夹杂物漂浮到熔融金属表面,达到净化材料的效果。
从脱气角度看,感应炉设计也要考虑感应圈的直径与高度之比,使熔液上表面增大,有利于脱气,并使耐火材料与熔融金属的接触面显著减少,降低对炉衬的侵蚀。
2. 冶炼电源
早期的感应炉电源都是电动机-发电机变频机组。
到了1967年,西德leybold 公司为美国howmet公司生产的5.477t的炉子中,使用了可控硅变频电源,功率1000kw,频率180Hz。
此后的3a间,变频发电机组和静止变频器共存,交
替过渡。
到1970年后,所有真空感应炉都配置可控硅静止变频电源。
经过30多年的发展,可控硅静止变频电源技术已经非常成熟。
在整个冶炼周期中,功率从1%-10%的平滑调节,使操作极其灵活、准确、无波动;变频电源的频率在一定的范围内是变化的,能自动跟踪适应炉料的变化,无需大电流接触器来开关电容器,调节炉子的功率因数;效率高,三相对称电网负荷,工作状态非常优越。
变频电源的功率已达10MW。
3. PLC控制
可编程序控制技术,使得真空熔炼设备的自动化和半自动化运行成为可能。
设备严格按用户设置的程序运行,工艺技术条件得以严格控制,可重复性强。
对设备运行和工艺过程实施高度控制。
例如,真空机组的开关、监测,真空阀门的开闭、联锁、切换,故障的识别、报警,预防误操作等都由PLC控制。
4. 计算机辅助系统的应用
根据实践所积累的丰富经验数据,编制成计算机软件,计算机通过对实测的温度与软件给定的工艺曲线进行比较,调整电源功率输出,从而控制钢液的温度,防止精炼期熔液的温度过热和过低,实现经济运行。
熔池的实际温度是通过扫描式光学高温计连续测定的。
在测量过程中,熔池表面的渣子、添加合金元素、光学玻璃的污染等原因都会影响被测数据的准确性,计算机将自动进行修正。
精炼后期,取样分析后一般要调整合金成分。
在中间分析的基础上,按合金成分的要求,补加合金元素的数量由计算机计算决定,并由打印机记录存档。
较大的真空感应炉都带有流槽装置,使得锭子的补缩颇为困难。
小型锭子(棒型电极)更容易产生缩孔和短锭。
为获得更高的收得率,就必须将缩孔减至最低限度。
国外研制出一种视频监控系统,由一套摄像观察装置和视频软件组成,可以从显示器上观察浇注情况和从显示器上用光标控制补缩。
由于对材料质量要求越来越高,所以感应炉生产工艺过程要求有高度的稳定性和可重复性。
国外发明了用于VIM的气体分压力分析的质谱控制仪,使VIM 工艺实现最佳化选择,从而实现经济运行。
通过对炉内残余气体含量的连续测定分析,以测定添加活性元素的最有利时间和加入的顺序;测定工艺过程的进展阶段,如精炼期的终结、出钢时间等;及时发现炉子的漏气,冷却水和液压管线的泄漏。
5. 中间包冶金技术的应用
为了更好地去除钢中夹杂物,提高钢水洁净度,添加可实现加热、保温功能滤渣去杂中间包系统。
中间包设有挡墙和挡坝,有利于各类杂质的上浮,钢水经挡渣、过滤后注入锭模,减少了渣子和夹杂物进入钢锭对提高钢材质量有极大的作用。