模压及层压成型
碳纤维复合材料加工工艺介绍
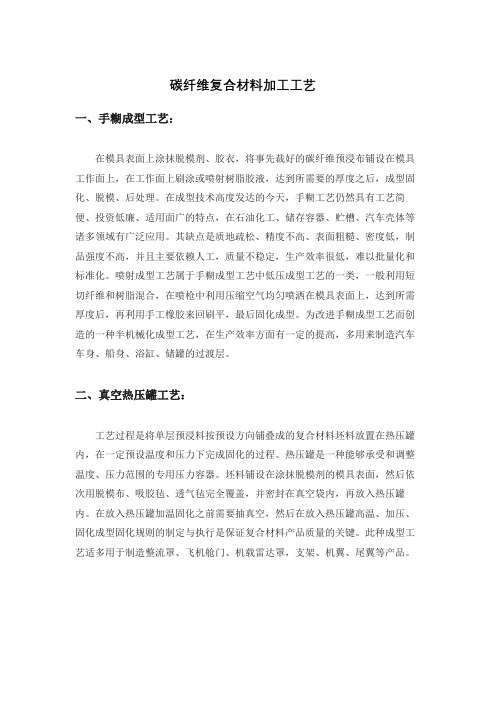
碳纤维复合材料加工工艺一、手糊成型工艺:在模具表面上涂抹脱模剂、胶衣,将事先裁好的碳纤维预浸布铺设在模具工作面上,在工作面上刷涂或喷射树脂胶液,达到所需要的厚度之后,成型固化、脱模、后处理。
在成型技术高度发达的今天,手糊工艺仍然具有工艺简便、投资低廉、适用面广的特点,在石油化工、储存容器、贮槽、汽车壳体等诸多领域有广泛应用。
其缺点是质地疏松、精度不高、表面粗糙、密度低,制品强度不高,并且主要依赖人工,质量不稳定,生产效率很低,难以批量化和标准化。
喷射成型工艺属于手糊成型工艺中低压成型工艺的一类,一般利用短切纤维和树脂混合,在喷枪中利用压缩空气均匀喷洒在模具表面上,达到所需厚度后,再利用手工橡胶来回刷平,最后固化成型。
为改进手糊成型工艺而创造的一种半机械化成型工艺,在生产效率方面有一定的提高,多用来制造汽车车身、船身、浴缸、储罐的过渡层。
二、真空热压罐工艺:工艺过程是将单层预浸料按预设方向铺叠成的复合材料坯料放置在热压罐内,在一定预设温度和压力下完成固化的过程。
热压罐是一种能够承受和调整温度、压力范围的专用压力容器。
坯料铺设在涂抹脱模剂的模具表面,然后依次用脱模布、吸胶毡、透气毡完全覆盖,并密封在真空袋内,再放入热压罐内。
在放入热压罐加温固化之前需要抽真空,然后在放入热压罐高温、加压、固化成型固化规则的制定与执行是保证复合材料产品质量的关键。
此种成型工艺适多用于制造整流罩、飞机舱门、机载雷达罩,支架、机翼、尾翼等产品。
三、层压成型工艺:把一层层铺设的预浸料放置在上下平板模之间通过加压高温固化成型,这种工艺可以直接利用木胶合板的生产方法和设备,并根据树脂的流动性能,进而进行改进与完善。
此种成型工艺主要用来生产不同规格、不同用途的复合材料板材。
具有机械化和自动化程度高、产品质量稳定、利用批量化等特点,但是设备投资较大,成本较高。
四、缠绕成型:缠绕成型工艺的发展已经有半个世纪,随着缠绕技术的不断更新,缠绕工艺基本已经成型,并成为金属铝复合材料重要施工工艺之一。
模压成型工艺

PART 3
优点
优点
1.生产效率高,便于实 现专业化和自动化生产
2.产品尺寸精度高,重 复性好
3.表面光洁,无需二次 修饰
PART 4
缺点
12
缺点
1.模具制造复杂
2.投资较大
PART 5
层压成型
1.定义
是以片状或纤维状材 料作为填料,在加热 、加压条件下把相同 或不同的材料的两层 或多层结合成为一个 整体的方法
层压成型
2.4热压
1)预热、预压阶段
使树脂熔化,除去挥 发分,使熔融树 脂 进一步浸渍纤维布, 并使树脂进入凝胶状 态
层压成型
2)热压阶段——从 加全压到热压结束
为了更好地排除挥发 分,使制品内外受热 均匀,升温不能过快 。 预浸料流动性差 ,挥发分低,流胶 不严重,升温加压速 度可稍快
层压成型
层压成型
2.5冷却脱模
两种方式 ①热压结束,关闭热源,通冷却水,在 保压状态下冷却 ②取出放在冷却砧板上冷却
2.6后处理
在烘房内进行的处理 程序,目的是使树脂 进一步固化。对不同 的树 脂后固化处理 的温度、时间不同
2.7工艺参数
与模压成型一样,温 度、时间、和压力是 三个重要的工艺条件
层压成型
层压成型
1)层压温度
层压温度取决于 ①树脂类型和固化速度 ②浸胶材料的含胶量
③树脂中的挥发 份及不溶胶树脂 的含量
④层压制品的厚度
压制的温度控制一般 分为五个阶段
层压成型
层压成型
预热阶段:板坯的温 度升至树脂开始交联 反应的温度,使树脂 开始熔化,并进一步 渗入增强材料中,同 时排出部分挥发物。 此时的压力=最高压 力的三分之一到二分 之一
模压成型工艺条件及控制三要素

模压成型工艺(条件)及控制三要素SMC/BMC模压成型进程中要重点注意控制好“3个点”,即3个主要工艺参数:模压温度、模压压力和模压时刻。
一、模压温度模压温度是模压成型时所规定的模具温度,这一工艺参数肯定了模具向模腔内物料的传热条件,对物料的熔融、流动和固化进程有决定性的影响。
SMC/BMC模塑料在模压进程中的温度转变情形较复杂,由于塑料是热的不良导体,物料中心和边缘在成型的开始阶段温差较大,这将致使固化交联反映在物料的内外层不是同时开始。
表层料由于受热早先固化而形成硬的壳层,而内层料在稍后的固化收缩因受到外部硬壳层的限制,致使模压制品的表层内常存有残余压应力,而内层则带有残余拉应力,残余应力的存在会引发制品翘曲、开裂和强度下降。
因此采取办法尽力减小模腔内物料的内外温差,消除不均匀固化是取得高质量制品的重要条件之一。
SMC/BMC模塑料的模压温度取决于固化体系的放热峰温度和固化速度,通常取固化峰温度稍低一点的温度范围为其固化温度范围,一般约为135~170℃并通过实验来肯定;固化速度快的体系取偏低点的温度,固化速度慢的体系取偏高些的温度。
成型薄壁制品时取温度范围的上限,成型厚壁制品可取温度范围的下限,但成型深度专门大的薄壁制品时,由于流程长为避免流动进程中物料固化,也应取温度范围的下限。
在不损害制品强度和其他性能指标的前提下,适当提高模压温度,对缩短成型周期和提高制品质量都有利。
模压温度太低不仅熔融后的物料黏度高、流动性差,而且由于交联反映难于充分进行,从而使制品强度不高,外观无光泽,脱模时出现粘模和顶出变形。
二、模压压力模压压力通常常利用模压压强(MPa)来表示,即玻璃钢液压机施加在模具上的总力与模具型腔在施压方向上的投影面积之比。
模压压力在模压成型进程中的作用,是使模具紧密闭归并使物料增密,和增进熔料流动和平衡模腔内低分子物挥发所产生的压力。
紧缩率大的模压料,由于使其增密时要消耗较多的能量,因此成型时需用较高的模压压强,故模压散状料比模压料坯的压力高,而SMC/BMC模压料又比模压粉状料的压力高。
模压成型工艺
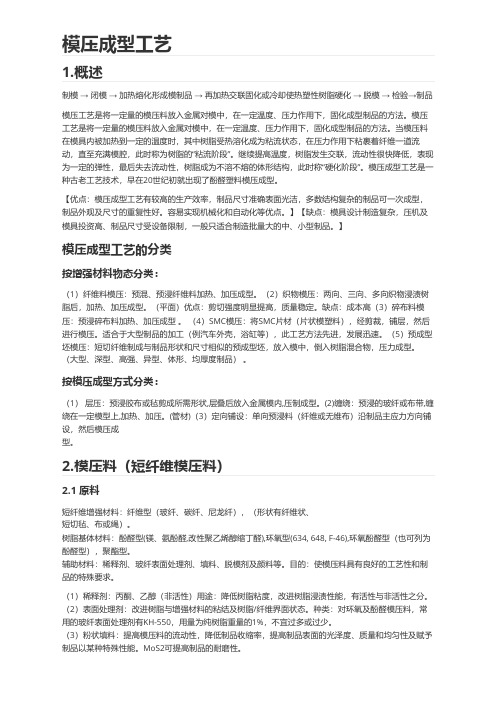
模压成型工艺1.概述制模→闭模→加热熔化形成模制品→再加热交联固化或冷却使热塑性树脂硬化→脱模→检验→制品模压工艺是将一定量的模压料放入金属对模中,在一定温度、压力作用下,固化成型制品的方法。
模压工艺是将一定量的模压料放入金属对模中,在一定温度、压力作用下,固化成型制品的方法。
当模压料在模具内被加热到一定的温度时,其中树脂受热溶化成为粘流状态,在压力作用下粘裹着纤维一道流动,直至充满模腔,此时称为树脂的“粘流阶段”。
继续提高温度,树脂发生交联,流动性很快降低,表现为一定的弹性,最后失去流动性,树脂成为不溶不熔的体形结构,此时称“硬化阶段”。
模压成型工艺是一种古老工艺技术,早在20世纪初就出现了酚醛塑料模压成型。
【优点:模压成型工艺有较高的生产效率,制品尺寸准确表面光洁,多数结构复杂的制品可一次成型,制品外观及尺寸的重复性好。
容易实现机械化和自动化等优点。
】【缺点:模具设计制造复杂,压机及模具投资高、制品尺寸受设备限制,一般只适合制造批量大的中、小型制品。
】模压成型工艺的分类按增强材料物态分类:(1)纤维料模压:预混、预浸纤维料加热、加压成型。
(2)织物模压:两向、三向、多向织物浸渍树脂后,加热、加压成型。
(平面)优点:剪切强度明显提高,质量稳定。
缺点:成本高(3)碎布料模压:预浸碎布料加热、加压成型。
(4)SMC模压:将SMC片材(片状模塑料),经剪裁,铺层,然后进行模压。
适合于大型制品的加工(例汽车外壳,浴缸等),此工艺方法先进,发展迅速。
(5)预成型坯模压:短切纤维制成与制品形状和尺寸相似的预成型坯,放入模中,倒入树脂混合物,压力成型。
(大型、深型、高强、异型、体形、均厚度制品)。
按模压成型方式分类:(1)层压:预浸胶布或毡剪成所需形状,层叠后放入金属模内,压制成型。
(2)缠绕:预浸的玻纤或布带,缠绕在一定模型上,加热、加压。
(管材)(3)定向铺设:单向预浸料(纤维或无维布)沿制品主应力方向铺设,然后模压成型。
模压成型工艺

加入热塑性树脂粉可显著降低制品收缩,后面课 程讨论。
(2)、模具结构和制品形状的影响 模具的结构不同对制品的收缩尺寸也有影响,模具刚
度不够时,压制时变形会使尺寸增大,特别对较薄的制 品因为压制时的变形,使制品尺寸有时会大于模具尺寸。 因此,要根据生产经验考虑模具结构的影响。
4.2.3.3 模压料的压缩性
压缩比: 是指模压料和模压制品比容的比值。 即制品密度与模压料密度的比值。
压缩比= 模压料比容 = 制品密度 制品比容 模压料密度
压缩比过大,即模压料过于蓬松,给装模带来困难, 对于压缩比太大的模压料,一般需要采取预成型工艺。 纤维状的模压料的压缩比一般为6~10。
作业:1、什么是模压料的收缩性?由哪几种收缩组成? 2、简述成型工艺条件对模压制品收缩率的影响。
(4)高聚物分子结构的影响 a、分子量愈大,粘度愈大。分子量愈大一般链段愈多, 分子链重心的相对移动愈难,即粘度愈大,流动性愈差。
粘度与分子量间的关系:
3.4
0 AM w
η0——剪切速度较低时的表观粘度 A ——经验常数 Mw——重均分子量
b、刚性高分子流动性差,由于刚性高分子的链段长, 因此流动困难。 c、分子量相同,支链愈多、愈短,粘度愈低,流动愈 好。
工艺流程: 树脂调配 ↓
玻璃纤维→热处理→切割→混合→撕松→烘干→模压料
模压料配方: P75,表4-1
生产步骤: 以镁酚醛为例 P75 ,8条
设 备: 主要有纤维切割机、捏合机、撕松机
4.2.2.2 短纤维模压料的质量控制 指标: 树脂含量;挥发物含量;不溶性树脂含量。
见P76 表4-2
常用的十大塑料成型工艺(优缺点介绍)
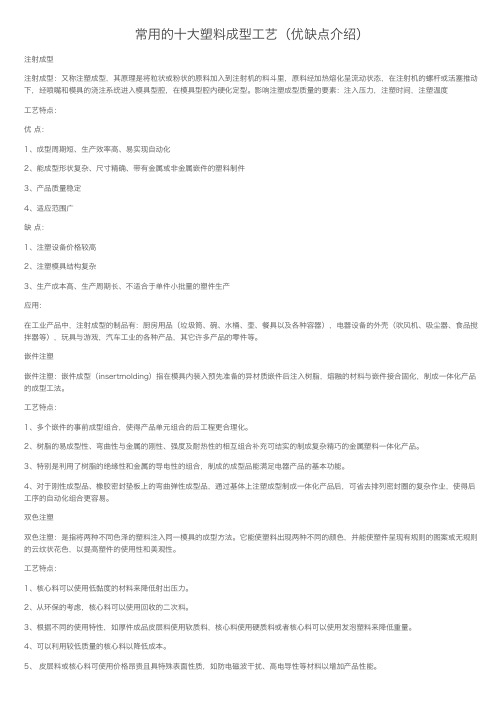
常⽤的⼗⼤塑料成型⼯艺(优缺点介绍)注射成型注射成型:⼜称注塑成型,其原理是将粒状或粉状的原料加⼊到注射机的料⽃⾥,原料经加热熔化呈流动状态,在注射机的螺杆或活塞推动下,经喷嘴和模具的浇注系统进⼊模具型腔,在模具型腔内硬化定型。
影响注塑成型质量的要素:注⼊压⼒,注塑时间,注塑温度⼯艺特点:优 点:1、成型周期短、⽣产效率⾼、易实现⾃动化2、能成型形状复杂、尺⼨精确、带有⾦属或⾮⾦属嵌件的塑料制件3、产品质量稳定4、适应范围⼴缺 点:1、注塑设备价格较⾼2、注塑模具结构复杂3、⽣产成本⾼、⽣产周期长、不适合于单件⼩批量的塑件⽣产应⽤:在⼯业产品中,注射成型的制品有:厨房⽤品(垃圾筒、碗、⽔桶、壶、餐具以及各种容器),电器设备的外壳(吹风机、吸尘器、⾷品搅拌器等),玩具与游戏,汽车⼯业的各种产品,其它许多产品的零件等。
嵌件注塑嵌件注塑:嵌件成型(insertmolding)指在模具内装⼊预先准备的异材质嵌件后注⼊树脂,熔融的材料与嵌件接合固化,制成⼀体化产品的成型⼯法。
⼯艺特点:1、多个嵌件的事前成型组合,使得产品单元组合的后⼯程更合理化。
2、树脂的易成型性、弯曲性与⾦属的刚性、强度及耐热性的相互组合补充可结实的制成复杂精巧的⾦属塑料⼀体化产品。
3、特别是利⽤了树脂的绝缘性和⾦属的导电性的组合,制成的成型品能满⾜电器产品的基本功能。
4、对于刚性成型品、橡胶密封垫板上的弯曲弹性成型品,通过基体上注塑成型制成⼀体化产品后,可省去排列密封圈的复杂作业,使得后⼯序的⾃动化组合更容易。
双⾊注塑双⾊注塑:是指将两种不同⾊泽的塑料注⼊同⼀模具的成型⽅法。
它能使塑料出现两种不同的颜⾊,并能使塑件呈现有规则的图案或⽆规则的云纹状花⾊,以提⾼塑件的使⽤性和美观性。
⼯艺特点:1、核⼼料可以使⽤低黏度的材料来降低射出压⼒。
2、从环保的考虑,核⼼料可以使⽤回收的⼆次料。
3、根据不同的使⽤特性,如厚件成品⽪层料使⽤软质料,核⼼料使⽤硬质料或者核⼼料可以使⽤发泡塑料来降低重量。
模压工艺生产操作-成型工艺
模压⼯艺⽣产操作-成型⼯艺模压⼯艺⽣产操作-成型⼯艺(⼀)预浸布层压成型⼯艺1. 概述层压成型⼯艺是指将浸渍或涂有树脂的⽚材层叠,组成叠合体,送⼊层压机,在加热和加压条件下,固化成型复合材料制品的⼀种成型⼯艺。
层压成型⼯艺主要是⽣产各种规格、不同⽤途的复合材料板材。
它具有机械化、⾃动化程度⾼、产品质量稳定等特点,但是设备⼀次性投资⼤。
层压成型技术特点是加压⽅向与制品的板⾯⽅向垂直。
层压成型技术包含两⽅⾯内容:胶布⽣产技术和压制成型技术。
2.层压板成型⼯艺在上述⽣产⼯艺中,热压过程的温度、压⼒和时间是三个最重要的⼯艺参数。
复合材料的层压⼯艺的热压过程,⼀般分为预热预压和热压两个阶段。
(1)第⼀阶段⼀预热预压阶段。
此阶段的主要⽬的是使树脂熔化,去除挥发物、浸渍纤维,并且使树脂逐步固化⾄凝胶状态。
此阶段的成型压⼒为全压的1/3-1/2。
(2)第⼆阶段-中间保温阶段这⼀阶段的作⽤是使胶布在较低的反应速度下进⾏固化。
保温过程中应密切注意树脂的流胶情况。
当流出的树脂已经凝胶,不能拉成细丝时,应⽴即加全压。
(3)第三阶段-升温阶段⽬的在于提⾼反应温度,加快固化速度。
此时,升温速度不能过快,否则会引起暴聚,使固化反应放热过于集中,导致材料层间分层。
(4)第四阶段-热压保温阶段⽬的在于使树脂能够充分固化。
从加全压到整个热压结束,称为热压阶段。
⽽从达到指定的热压温度到热压结束的时间,称为恒温时间。
热压阶段的温度、压⼒和恒温时间,也是由配⽅决定。
(5)第五阶段-冷却阶段在保压的情况下,采取⾃然冷却或者强制冷却到室温,然后卸压,取出产品。
冷却时间过短,容易使产品产⽣翘曲、开裂等现象。
冷却时间过长,对制品质量⽆明显帮助,但是使⽣产效率明显降低。
(⼆)预浸料模压成型⼯艺预浸料模压成型⼯艺基本过程是:将⼀定量经⼀定预处理的模压料放⼊预热的模具内,施加较⾼的压⼒使模压料填充模腔。
在⼀定的压⼒和温度下使模压料逐渐固化,然后将制品从模具内取出,再进⾏必要的辅助加⼯即得产品。
高分子材料加工技术--压制成型
1.2工艺过程
高分子材料成型加工
高分子材料成型加工
2.片状模塑料模压成型
(Sheet Molding Compound. SMC)
2.1 配比:
不饱和聚酯 约20~30%
增稠剂
约 5%
无机填料 40~50%
引发剂
2~3%
脱模剂
0.5~1%
短切玻璃纤维或毡片 适量
2.2 工艺过程
高分子材料成型加工
高分子材料成型加工
三. 模型硫化工艺及硫化条件
工艺过程
混炼胶和橡胶半成品→ 计量→ 加料→ 闭 模→排气 →保压(硫化)→ 脱模→ 制品
这一过程基本上与热固性塑料的模压成型 相同,硫化工艺条件是硫化压力、硫化温 度和硫化时间。
高分子材料成型加工
1.硫化压力 大多数的橡胶制品的硫化是在一定压力下 进行的 一般模压制品的硫化压力为2~4 MPa 胶料流动性差,制品形状复杂,制品表面 花纹细致,结构复杂,厚制品,硫化温度 高,则硫化压力高一些。 太高的硫化压力会加速橡胶分子链的热降 解
高分子材料成型加工
一. 热固性模塑料的成型工艺性能:
1.流动性:热固性模塑料的流动性是指其在受热和受 压情况下充满整个模具型腔的能力。 影响流动性的因素:
压模塑料的性能和组成(分子量、颗粒形状、小分 子物质)
模具与成型条件(光洁度、流道形状、预热)
流动性要适中:
太大:溢出模外,塑料在型腔内填塞不紧,或树脂 与填料分头聚集。
高分子材料成型加工
根据实践经验,在选择模压成型的工艺条 件时,可以从模压压力、温度和时间三者 中先固定一个条件,如按经验选定成型压 力,然后再变化成型的温度和时间,从实 验中找出合理的条件来。
(完整版)高分子材料成型加工四种成型加工方法优缺点
1.压制成型:应用于热固塑料和橡胶制品的成型加工压制成型方法对于热固性塑料、橡胶制品和增强复合材料而言,都是将原料加入模具加压得到制品,成型过程都是一个物理—化学变化过程。
不同的是橡胶制品的成型中要对原料进行硫化。
橡胶通过硫化获得了必需的物理机械性能和化学性能。
而在复合材料压制成型过程中,还用到了层压成型(在压力和温度的作用下将多层相同或不同材料的片状物通过树脂的粘结和熔合,压制成层压塑料的成型方法)和手糊成型(以玻璃纤维布作为增强材料,均匀涂布作为黏合剂的不饱和聚酯树脂或环氧树脂的复合材料)。
2.挤出成型:适用于所有高分子材料,广泛用于制造轮胎胎面、内胎、胎管及各种断面形状复杂或空心、实心的半成品,也用于包胶操作。
挤出成型挤出成型对于高分子三大合成材料所用的设备和加工原理基本上是相同的。
有区别的是橡胶挤出是在压出机中对混炼胶加热与塑化,通过螺杆的旋转,使胶料在螺杆和料筒筒壁之间受到强大的挤压作用,不断向前推进,并借助于口型(口模)压出具有一定断面形状的橡胶半成品。
而合成纤维的挤出纺丝过程,采用三种基本方法:熔融纺丝、干法纺丝、湿法纺丝。
一般采用熔融纺丝(在熔融纺丝机中将高聚物加热熔融制成溶体,通过纺丝泵打入喷丝头,并由喷丝头喷成细流,再经冷凝而成纤维)。
3.注射成型:应用十分广泛,几乎所有的热塑性塑料及多种热固性塑料都可用此法成型,也可以成型橡胶制品。
注射成型高分子三大合成材料的注射成型过程中所用设备和工艺原理比较相似,但是从基本过程和要求看热固性塑料注射和热塑性塑料注射有很多不同之处。
热固性塑料的注射成型要求成型物料首先在温度相对较低的料筒内预塑化到半熔融状态,然后在随后的注射充模过程中进一步塑化,避免其因发生化学反应而使黏度升高,甚至交联硬化为固体。
塑料注射成型原料是粒状或粉状的塑料,而橡胶注射成型原料则是条状或块粒状的混炼胶,且混炼胶在注压入模后须停留在加热的模具中一段时间,使橡胶进行硫化反应。
高分子材料成型加工四种成型加工方法优缺点
1.压制成型:应用于热固塑料和橡胶制品的成型加工压制成型方法对于热固性塑料、橡胶制品和增强复合材料而言,都是将原料加入模具加压得到制品,成型过程都是一个物理—化学变化过程。
不同的是橡胶制品的成型中要对原料进行硫化。
橡胶通过硫化获得了必需的物理机械性能和化学性能。
而在复合材料压制成型过程中,还用到了层压成型(在压力和温度的作用下将多层相同或不同材料的片状物通过树脂的粘结和熔合,压制成层压塑料的成型方法)和手糊成型(以玻璃纤维布作为增强材料,均匀涂布作为黏合剂的不饱和聚酯树脂或环氧树脂的复合材料)。
2.挤出成型:适用于所有高分子材料,广泛用于制造轮胎胎面、内胎、胎管及各种断面形状复杂或空心、实心的半成品,也用于包胶操作。
挤出成型对于高分子三大合成材料所用的设备和加工原理基本上是相同的。
有区别的是橡胶挤出是在压出机中对混炼胶加热与塑化,通过螺杆的旋转,使胶料在螺杆和料筒筒壁之间受到强大的挤压作用,不断向前推进,并借助于口型(口模)压出具有一定断面形状的橡胶半成品。
而合成纤维的挤出纺丝过程,采用三种基本方法:熔融纺丝、干法纺丝、湿法纺丝。
一般采用熔融纺丝(在熔融纺丝机中将高聚物加热熔融制成溶体,通过纺丝泵打入喷丝头,并由喷丝头喷成细流,再经冷凝而成纤维)。
3.注射成型:应用十分广泛,几乎所有的热塑性塑料及多种热固性塑料都可用此法成型,也可以成型橡胶制品。
注射成型高分子三大合成材料的注射成型过程中所用设备和工艺原理比较相似,但是从基本过程和要求看热固性塑料注射和热塑性塑料注射有很多不同之处。
热固性塑料的注射成型要求成型物料首先在温度相对较低的料筒内预塑化到半熔融状态,然后在随后的注射充模过程中进一步塑化,避免其因发生化学反应而使黏度升高,甚至交联硬化为固体。
塑料注射成型原料是粒状或粉状的塑料,而橡胶注射成型原料则是条状或块粒状的混炼胶,且混炼胶在注压入模后须停留在加热的模具中一段时间,使橡胶进行硫化反应。
- 1、下载文档前请自行甄别文档内容的完整性,平台不提供额外的编辑、内容补充、找答案等附加服务。
- 2、"仅部分预览"的文档,不可在线预览部分如存在完整性等问题,可反馈申请退款(可完整预览的文档不适用该条件!)。
- 3、如文档侵犯您的权益,请联系客服反馈,我们会尽快为您处理(人工客服工作时间:9:00-18:30)。
• 增加人力、设备; • 松散度大、长纤维:难压; • 结构复杂或混色的制品不宜用预压。 (2)预压工艺条件 • 温度:一般不加热,若室温不易压,可50~60℃ 预压。 • 压力:要求预压物的ρ为制品ρ的80%;预压力 40~200MPa。
3. 预热和干燥 (1)预热和干燥的作用:提高制品质量,除水份和 挥发物 • 预热:可缩短模压周期;提高制品质量;提高流动 性;降低模塑压力(不预热PF,30±0.5 MPa;预 热PF,15~20 MPa)。 • 预热规程的确定:获得最大流动性的规程,先定温 度、找出最佳流动性的预热时间。 (2)预热和干燥的设备及操作 • 电热板加热 • 烘箱加热 • 红外线加热:波长为1~1.2X10-4m的红外线灯照射 • 高频加热:用于极性分子的塑料
第二节 层压成型 一. 概述 1. 层压成型: • 指用或不用粘结剂,在加热、加压条件下把相同 或不同材料的两层或多层结合为整体的方法 • 粘结剂:树脂,如酚醛(PF)、环氧树脂(EP)、 不饱和树脂(UP)、氨基树脂。 • 材料:填料,如纸、木、棉布、玻纤及织物 • 附胶材料:成型前浸有或涂有树脂的材料
• 树脂本身具有良好的物理力学性能 • 树脂硬化时收缩率要小 • 树脂要有良好的工艺性: 成型时不须很高的温度及压力、黏度小(但黏 度过小,易流失)、硬化前使用寿命长 2. 常用树脂特性 (1)PF树脂 • 模压用酸催化的PF;层压用碱催化PF
1. 模压成型特点: (1)设备简单,造价低,模结构简单 (2)填料的方向性小,成型压力低; (3)原料损耗少,适用于多种材料; (4)生产效率低,制品精度低; (5)劳动强度大,难于实现自动化。 2. 树脂: • 常用:PF、UP、环氧树脂(EP)、脲醛(UF) 3. 模压成型工艺: • 预处理:预热、预压 • 成型过程:嵌件安放、加料、闭模、排气、固化、脱模 • 后处理:热处理、机加工、修饰、装配、检验 4. 物料在模压成型中的变化:熔融流动、胶凝、固化
• • •
• • •
影响因素: 压缩率h:h大,模压压力应高 预热温度:与模压压力应有一最佳配合 模温:模温高利于流动和硬化,压力可减小,但 模温过高,模塑过早硬化,流动性↓,需较大模压 压力。 制品厚度:0.98~1.47MPa/每增加1cm厚 制品深:深度大的制品增加20~30%的模压压力 制品密度:压力大,密度↑
(2)模压温度:模压时所规定的模具温度 • 模压温度对制品性能影响:
• 模温过高:流动性↓;降解分层、表里硬化不一、 内应力大、开裂、变形;色料变质、色暗淡。 • 模温过低:生产周期长、硬化不足光泽差;水份挥 发物作用易肿胀变形,性能↓。
模温与模压周期的关系: • 高温短时,低温长时(不损 害制件强度及其他性能); • 厚制件:低温长时; • 预热料:模压温度可提高, 制品内外温均匀,流动性提 高。
模压及层压成型
• 学习目的与要求: 1. 掌握模压与层压成型的工艺特点与工艺过程; 2. 掌握模压与层压工艺参数对制品性能的影响; 3. 了解模压与层压成型所用的模具。
第一节 模压成型
一. 概述 • 模压成型(压制成型、压缩模塑):粉状、 粒状或纤维状的模塑料放入加热的模具型 腔后闭模,加压、加热使其成型并固化的 方法。 • 压制成型动画,某些性能比原有树 脂有较大提高的一类塑料;多指用玻纤或其织 物为填料的塑料 • 复合材料:由两种或两种以上不同材料组成的 一种制品或材料 2. 分类:
二、常用树脂 1. 树脂的选择 (1)树脂在复合材料中的作用: • 粘结填料,承担部分载荷、传递载荷 • 使填料不致发生屈曲变形 • 保护填料 (2)对树脂的要求 • 对填料有良好粘结力、润湿能力 可加偶联剂改善(增加吸引力)
2. 控制因素 (1)模压压力: • 模压时使料充满型腔和进行硬化而由压机对料所 施加的压力。 • 压力作用: 使物料流动充模;压实物料;防止制品变形 • 模具型式及模压压力:
• 不溢式模具:模具型腔体积 随模压压力及所加物料量变 化;物料所受压力等于模压 压力。 • 有支承面的半溢式模:模腔 体积不变,物料可溢流。
二. 成型前准备 1. 原料的贮存 (1)吸湿性与环境湿度:湿度≯70% • 吸湿大: 流动性大、飞边大; 树脂含量↓,制品收缩大; 变形、膨胀、分层、尺寸↓。 • 含水量少: 流动性差、充不满模,制品疏松,欠熟。 (2)贮存温度:≯25℃ (3)贮存时间:不宜过长,UF≯3个月,热固性 PF≯6个月,热塑性PF三年
2. 预压 • ——将疏松的粉状、碎屑状或纤维状的热固性料 预先用冷压法压成重量一定、形状规整的密实体 的作业 预压成型工艺1.exe 预压成型工艺2.exe (1)作用 • 便于加料,改善劳动条件; • 降低压缩比,从而简化模具结构; • 缩短周期,提高制品质量; • 改善预热规程(PF粉100~120℃,PF预压物 170~190℃); • 便于模压较大或带有精细嵌件的制品。
(3)模压时间 • 模压时间与制品类型、形状、厚度,模具结构, 模压规程等有关 • 时间过短:硬化不足“欠熟”,制品性能差、无 光泽、易变形、翘曲; • 适当提高时间:制品收缩小,耐热性略高、物理 机械性能↑,但介电性↓; • 过分延长时间:“过熟”,降低制品性能和生产 效率,多消耗热量。 • 故,在不影响制品性能的前提下,尽量缩短模压 时间
三. 模压成型工艺过程及控制因素 1. 模压成型工艺过程 压制成型工艺.exe 物料预压→ 预热 ↓ 计量 ↓ 模具预热→涂脱模剂→ 安放嵌件→加料→ 闭模→ 排气 ↑ ↓ ← —————制品顶出 ←开模 ←硬化 清模
(1)嵌件安放 (2)加料 • 加料方式:人工加、加料器;重量法、容积法、计 算法。 • 注意:准确,堆放合理,利于排气(中高周低。) (3)闭模:先快后慢 (4)排气:1~3次,每次几秒至二十秒 (5)硬化: • 热塑性料:在模内冷却硬化 • 热固性料:模内交联硬化 • 硬化速率低的料:用后烘方法(90~150℃,8~ 12h) (6)脱模 (7)清理模具:工具使用适当