连接器检测不良及原因
连接器十大不良PPT培训课件

绝缘不良
总结词
绝缘不良是指连接器在正常工作状态 下,其绝缘材料或绝缘层存在缺陷, 导致电气性能下降。
详细描述
绝缘不良可能是由于连接器绝缘材料 老化、破损或制造工艺不良等原因引 起的。它可能导致电路短路、漏电或 电击等安全问题。
短路
总结词
短路是指连接器的电路被意外短路,导致电流不经过负载直 接流过。
详细描述
极性反接可能是由于操作失误或连接器标识不清等原因引起的。它会导致电路功能异常、设备损坏或 安全问题等后果。
0错位
总结词
0错位是指连接器的插针或插孔在装配过程 中出现错位,导致无法正常插入或拔出。
详细描述
0错位可能是由于制造工艺控制不当、插针 或插孔的设计不合理或使用不当等原因引起 的。它会影响连接器的正常使用和可靠性, 严重时会导致设备损坏或安全问题。
人为操作注意事项
总结词
提高操作人员素质和意识
详细描述
加强操作人员的培训和教育,提高其专业素质和安全意 识。规范操作流程,强调安全操作注意事项,避免因人 为操作失误导致连接器损坏或事故发生。
05 连接器不良现象案例分析
案例一:某品牌手机充电口接触不良问题
总结词
充电口接触不良是手机连接器常见问题之一,可能导 致充电速度慢、无法充电或充电过程中断等问题。
VS
详细描述
压接不良可能是由于线缆插入的深度不够 、插头的端子松动或压接工具使用不当等 原因引起的。它会影响信号传输的质量和 稳定性,严重时会导致线缆脱落或电路断 路。
焊接不良
总结词
焊接不良是指连接器的焊接点存在虚焊、脱焊、焊点粗糙等问题,导致电气性能下降。
详细描述
焊接不良可能是由于焊接工艺控制不当、焊接材料质量差或焊接操作不规范等原因引起的。它会导致电路电阻增 大、接触不良或短路等安全问题。
连接器检测不良及原因

连接器检测不良及原因1 引言不论是高频电连接器,还是低频电连接器,绝缘电阻、介质耐压(又称抗电强度)和接触电阻都是保证电连接器能正常可靠地工作的最基本的电气参数。
通常在电连接器产品技术条件的质量一致性检验A、B组常规交收检验项目中都列有明确的技术指标要求和试验方法。
这三个检验项目也是用户判别电连接器质量和可靠性优劣的重要依据。
但根据笔者多年来从事电连接器检验的实践发现,目前各生产厂之间以及生产厂和使用厂之间,在具体执行有关技术条件时尚存在许多不一致和差异,往往由于采用的仪器、测试工装、操作方法、样品处理和环境条件等因素不同,直接影响到检验准确和一致。
为此,笔者认为,针对目前这三个常规电性能检验项目和实际操作中存在的问题进行一些专题研讨,对提高电连接器检验可靠性是十分有益的。
另外,随着电子信息技术的迅猛发展,新一代的多功能自动检测仪正在逐步替代原有的单参数测试仪。
这些新型测试仪器的应用必将大大提高电性能的检测速度、效率和准确可靠性。
2 绝缘电阻检验2.1作用原理绝缘电阻是指在连接器的绝缘部分施加电压,从而使绝缘部分的表面或内部产生漏电流而呈现出的电阻值。
即绝缘电阴(MΩ)=加在绝缘体上的电压(V)/泄漏电流(μA)。
通过绝缘电阻检验,确定连接器的绝缘性能能否符合电路设计的要求,或在经受高温、潮湿等环境应力时,其绝缘电阻是否符合有关技术条件的规定。
绝缘电阻是设计高阻抗电路的限制因素。
绝缘电阻低,意味着漏电流大,这将破坏电路和正常工作。
如形成反馈回路,过大的漏电流所产生的热和直流电解,将使绝缘破坏或使连接器的电性能变劣。
2.2影响因素主要受绝缘材料、温度、湿度、污损、试验电压及连续施加测试电压的持续时间等因素影响。
2.2.1绝缘材料设计电连接器时选用何种绝缘材料非常重要,它往往影响产品的绝缘电阻能否稳定合格。
如某厂原使用酚醛玻纤塑料和增强尼龙等材料制作绝缘体,这些材料内含极性基因,吸湿性大,在常温下绝缘性能可满足产品要求,而在高温潮湿下则绝缘性能不合格。
连接器十大不良
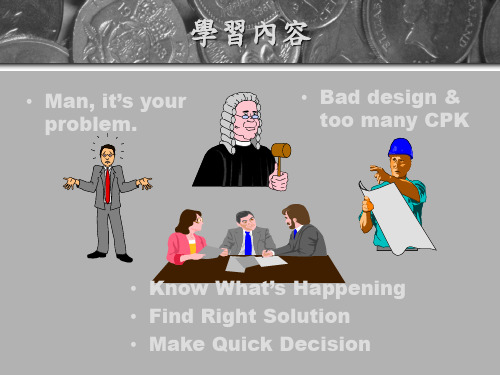
• 主因(二)
– 方向性玻纖排 列造成MD與 TD方向收縮不 均。
• 解決方案
– 採樑結購方式 設計
– 局部逃料玻亂 方向
翹曲變形(Warpage)
• 主因(三)
– 產品肉厚太薄 或流動長度過 長導致流動困 難及殘留應力 過大。
• 解決方案
– 設計考慮成型 性(如L/T比)
• 主因(四)
– 模溫冷卻系統設計 不當,公母模溫差 大。兩面收縮不同 造成翹曲。
• 解決方案
– 加肉厚降射壓 – Gate加頂針
• 主因(二)
– 頂出系統不平 衡,導致頂穿 而黏模。
• 解決方案
– 考量整體配置 – 料深區需於兩
側加裝頂針
脫模不順
• 主因(三)
– 分模線設計不 當黏母模,無 法脫模。。
• 主因(四)
– 模仁損傷或組 配不量,造成 毛頭產生影響 脫模。
• 解決方案
– 頂出平衡 – Gate與夾持面積大
之區域加裝頂針
翹曲變形(Warpage)
• 主因(七)
– 模具冷卻不足, 產品強度尚不足。 頂出時產品發生 變形。
• 解決方案
– 冷卻時間加長 – 冷卻局部熱集中
區(加冷卻機構)
短射(Short Shot)
• 現象
– 融膠射入模穴 中,產品某區 域無法完全充 填,因而產生 填料不足之現 象。
銀線(Silver Streak)
塑料除濕 乾燥完全
塑料的水份或揮 發物於射出時汽 化所致,螺桿捲 入空氣亦是原因
結論
•成型品質不是用機台調的 •產品/模具設計主宰品質 •品質是大家的問題
短射(Short Shot)
• 主因(一)
连接器三大致命故障

连接器三大致命故障
美昊电子:/news/
我们在使用连接器接线端子的过程中,或多或少都会遇到一些问题:如腐蚀、划伤、飞边、破裂,又或者是接触部位的做工粗糙、变形等各种各样的原因造成的外观不良,亦或者是配合尺寸不合等故障;JST一级代理商的美昊电子电气工程师分析接线端子常见的致命故障,归纳总结为以下3点:
1.接触不良:
导致原因:接触件设计不合理,材料选用错误,尺寸不合标准,或电镀层处理不当。
造成后果:影响电源、信号等传递,严重的可能导致无法传递。
2.固定不良:
导致原因:由于设计不可靠,选材错误,成型工艺选择不当,热处理,模具,装配,熔接等工艺质量差,装配不到位等;
也或是有时粗心大意安装不完善,或者产品耐久度有限如插拔次数太多。
造成后果:轻者影响接触可靠造成瞬间断电,严重的就是产品解体。
3.绝缘不良:
导致原因:主要的原因是由于连接器在制造的时候选材不当;也有可能是由于绝缘体表面或内部存在金属多余物,表面尘埃,焊剂等污染受潮,有机材料析出物及有害气体吸附膜与表面水膜融合形成离子性导电通道,吸潮,长霉,绝缘材料老化等原因,都会造成短路,漏电,击穿,绝缘电阻低等原因造成。
造成后果:绝缘体的作用是使接触件保持正确的位置排列,并使接触件与接触件之间,接触件与壳体之间相互绝缘。
手机连接器概述及失效分析方法
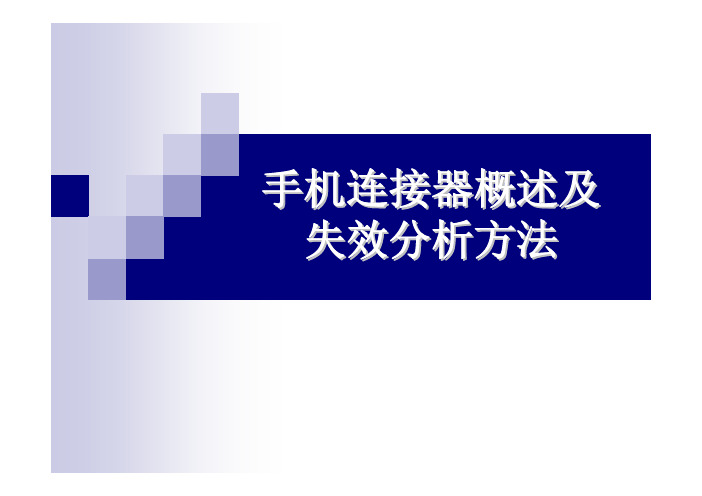
3)接触类型 接触类型有单触点和双触点两种。双接触可靠性更高,推荐使用
双接触点类型的BTB。
单接触
双接触
4)平面度 平面度直接影响焊接效果,要求控制在0.08mm以内。
5)防爬锡设计 一般端子采用露Ni电镀方式来满足要求。锡爬到端子接触区和弹片
位置会影响使用寿命及接触可靠性。
插座
插头
4.2、FPC插座:
Mini usb
micro usb
五 手机连接器生产流程简介
连接器的生产主要包括以下几方面: 1. 五金件冲压,电镀。 2. 塑胶件注塑成型 3. 成品组装(以USB为例说明)
电镀 五金件冲压成型 塑胶件注塑成型
入庫 成品组装
出货
5.1 五金件冲压
冲压是一种先进的金属加工方法,是建立在金属塑性变形的基础上,利用
2)侦测开关结构
用于侦测耳机是否插入,常见有两种结构,一种用两跟端子直接 作用,插入插头后实现闭合或者断开,从而侦测出耳机已经插入。另 一种用两跟端子通过插头实现闭合,从而实现功能,这种方式可以减 少耳机模式问题。
一
二
4.7、USB插座
用于数据传输和充电,由信号端子,塑胶,铁壳组成。有 mini,micro两种形式。按焊板方式可分为贴板式,插板式,沉 板式等几种。
2. 端子加工制造
切料,將端子切成預定 PIN數小片
通过折弯治具把端子折成要求 的形状
折弯前(左图) 折弯后(右)
3. 端子和塑胶组装 通过手工和相应治具把端子装进塑胶槽内
插针
压针
压针后 半成品
4. solder pin的成型
通过相应的治具把端子脚加工成SMT,DIP类型,并切成规格长度。
切针前
关于连接器之接线端子常见故障的分析

关于连接器之接线端子常见故障的分析接线端子的塑料绝缘材料和导电部件直接关系到端子的质量,它们分别决定了端子的绝缘性能和导电性能。
任何一个接线端子失效都将导致整个系统工程的失败。
都说预防是目的,分析是基础。
所以仪器仪表世界网指出从某个使用角度讲,接线端子应该达到的功能是:接触部位该导通的地方必须导通,接触可靠。
绝缘部位不该导通的地方必须绝缘可靠。
接线端子常见的故障形式有以下三种:1.接触不良接线端子内部的金属导体是端子的核心零件,它将来自外部电线或电缆的电压,电流或信号传递到与其相配的连接器对应的接触件上。
故接触件必须具备优良的结构,稳定可靠的接触保持力和良好的导电性能。
由于接触件结构设计不合理,材料选用错误,模具不稳定,加工尺寸超差,表面粗糙,热处理电镀等表面处理工艺不合理,组装不当,贮存使用环境恶劣和操作使用不当,都会在接触件的接触部位和配合部位造成接触不良。
2.绝缘不良绝缘体的作用是使接触件保持正确的位置排列,并使接触件与接触件之间,接触件与壳体之间相互绝缘。
故绝缘件必须具备优良的电气性能,机械性能和工艺成型性能。
特别是随着高密度,小型化接线端子的广泛使用,绝缘体的有效壁厚越来越薄。
这对绝缘材料,注塑模具精度和成型工艺等提出了更苛严的要求。
由于绝缘体表面或内部存在金属多余物,表面尘埃,焊剂等污染受潮,有机材料析出物及有害气体吸附膜与表面水膜融合形成离子性导电通道,吸潮,长霉,绝缘材料老化等原因,都会造成短路,漏电,击穿,绝缘电阻低等绝缘不良现象。
3.固定不良绝缘体不仅起绝缘作用,通常也为伸出的接触件提供精确的对中和保护,同时还具有安装定位,锁紧固定在设备上的功能。
固定不良,轻者影响接触可靠造成瞬间断电,严重的就是产品解体。
解体是指接线端子在插合状态下,由于材料,设计,工艺等原因导致结构不可靠造成的插头与插座之间,插针与插孔之间的不正常分离,将造成控制系统电能传输和信号控制中断的严重后果。
由于设计不可靠,选材错误,成型工艺选择不当,热处理,模具,装配,熔接等工艺质量差,装配不到位等都会造成固定不良。
连接器通用检验标准
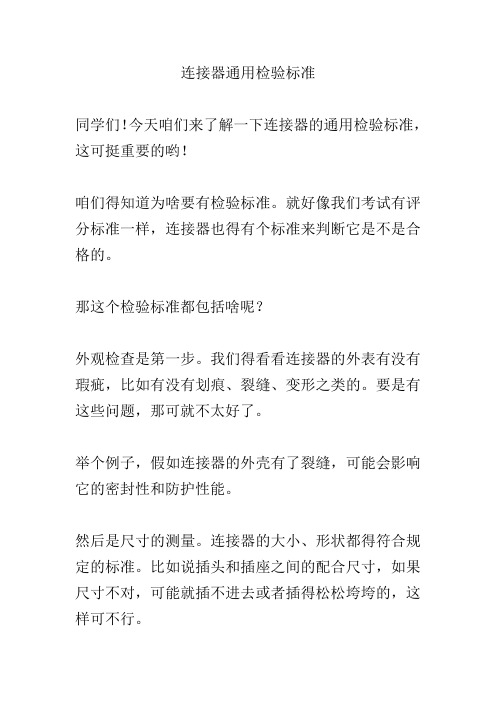
连接器通用检验标准同学们!今天咱们来了解一下连接器的通用检验标准,这可挺重要的哟!咱们得知道为啥要有检验标准。
就好像我们考试有评分标准一样,连接器也得有个标准来判断它是不是合格的。
那这个检验标准都包括啥呢?外观检查是第一步。
我们得看看连接器的外表有没有瑕疵,比如有没有划痕、裂缝、变形之类的。
要是有这些问题,那可就不太好了。
举个例子,假如连接器的外壳有了裂缝,可能会影响它的密封性和防护性能。
然后是尺寸的测量。
连接器的大小、形状都得符合规定的标准。
比如说插头和插座之间的配合尺寸,如果尺寸不对,可能就插不进去或者插得松松垮垮的,这样可不行。
再说说电气性能的检验。
这就像是检查连接器能不能好好“导电”。
我们要测测它的电阻、电容、绝缘电阻这些参数。
如果电阻太大,电流通过就会有损耗;如果绝缘电阻不够,可能会漏电,这都是很危险的。
比如说,在一些精密的电子设备中,连接器的电气性能不好,可能会导致设备故障甚至损坏。
还有插拔力的测试。
就是看看插头插进插座和拔出来的时候,需要用多大的力气。
插拔力太大或者太小都不行。
太大了插拔困难,太小了又容易松动。
手机充电线的连接器,如果插拔力不合适,用着用着可能就接触不良了。
接着是耐腐蚀性的检验。
因为连接器可能会在各种环境中使用,如果不耐腐蚀,很快就会坏掉。
在潮湿或者有化学物质的环境中,不耐腐蚀的连接器会生锈或者被腐蚀掉。
还有可靠性和稳定性的测试。
要模拟连接器在长期使用中的情况,看看它能不能一直保持良好的性能。
不断地插拔连接器,看它经过多次使用后会不会出现问题。
连接器的通用检验标准就像是给连接器做了一个全面的“体检”,从外观到性能,各个方面都要检查到位,只有都合格了,才能算是一个好的连接器。
同学们,现在是不是对连接器的检验标准有了更清楚的了解啦?。
JACK连接器8D报告(变形缺损)案例

版次:B/3有 限 公 司异 常 通 知 单□内部检查、审核 ■QC □其它□环境检查、审核 □预防措施 NO.130426-3■急件 □一般件 □厂内 ■厂外(供方) 问题发生部门提出部门品保提出时间2020年04月26日1 异 常 说 明进贵司TP6152T 开关,经敝司生产1000PCS ,检测发现有3PCS 开关按键压伤变形、缺损(见不良图片)请贵司分析上述不良原因,提出有效改善措施,以确保后续交货品质,并回复,谢谢!审核: 提出者:2 原因分析成员负责人 完成日期2020.04.27 3 不良紧急遏制计划1. 装配部立即停止生产(暂无生产) 2.暂停出货,库存品重检。
2020.04.274 根本原因分析1.此为按键套入底座时挤压变形。
2.缺损此为注塑机在长时间运作中,注塑参数发生波动,压力偏小所致。
2020.04.275 长 期 对 策1.组装时按键应单边套入底座中不可强行挤入;2.后续生产时,注塑部每小时对注塑参数进行确认一次,发现异常及时调整,并将不良品区分处理。
3.全检QC 作100%外观检查;2020.04.276 对策有效性验证暂无库存2020.04.277 再现性预防1.装配部生产时按键与底座组立须放正,组立时,先将单边扣位按入上盖到位以后再进行另一边扣位按入。
2. IPQC 巡检/QA 抽检时对产品外观有无异常作重点确认。
2020.04.278 批准: 审核: 报告人: 以上2~8项由问题发生单位填写,急件24小时内回复。
□实际完成日期及验证情况验证者:按键压伤变形 按键缺损。
- 1、下载文档前请自行甄别文档内容的完整性,平台不提供额外的编辑、内容补充、找答案等附加服务。
- 2、"仅部分预览"的文档,不可在线预览部分如存在完整性等问题,可反馈申请退款(可完整预览的文档不适用该条件!)。
- 3、如文档侵犯您的权益,请联系客服反馈,我们会尽快为您处理(人工客服工作时间:9:00-18:30)。
连接器检测不良及原因1引言不论是高频电连接器,还是低频电连接器,绝缘电阻、介质耐压(又称抗电强度)和接触电阻都是保证电连接器能正常可靠地工作的最基本的电气参数。
通常在电连接器产品技术条件的质量一致性检验A、B组常规交收检验项目中都列有明确的技术指标要求和试验方法。
这三个检验项目也是用户判别电连接器质量和可靠性优劣的重要依据。
但根据笔者多年来从事电连接器检验的实践发现,目前各生产厂之间以及生产厂和使用厂之间,在具体执行有关技术条件时尚存在许多不一致和差异,往往由于采用的仪器、测试工装、操作方法、样品处理和环境条件等因素不同,直接影响到检验准确和一致。
为此,笔者认为,针对目前这三个常规电性能检验项目和实际操作中存在的问题进行一些专题研讨,对提高电连接器检验可靠性是十分有益的。
另外,随着电子信息技术的迅猛发展,新一代的多功能自动检测仪正在逐步替代原有的单参数测试仪。
这些新型测试仪器的应用必将大大提高电性能的检测速度、效率和准确可靠性。
2绝缘电阻检验2.1作用原理绝缘电阻是指在连接器的绝缘部分施加电压,从而使绝缘部分的表面或内部产生漏电流而呈现出的电阻值。
即绝缘电阴(MΩ)=加在绝缘体上的电压(V)/泄漏电流(μA)。
通过绝缘电阻检验,确定连接器的绝缘性能能否符合电路设计的要求,或在经受高温、潮湿等环境应力时,其绝缘电阻是否符合有关技术条件的规定。
绝缘电阻是设计高阻抗电路的限制因素。
绝缘电阻低,意味着漏电流大,这将破坏电路和正常工作。
如形成反馈回路,过大的漏电流所产生的热和直流电解,将使绝缘破坏或使连接器的电性能变劣。
2.2影响因素主要受绝缘材料、温度、湿度、污损、试验电压及连续施加测试电压的持续时间等因素影响。
2.2.1绝缘材料设计电连接器时选用何种绝缘材料非常重要,它往往影响产品的绝缘电阻能否稳定合格。
如某厂原使用酚醛玻纤塑料和增强尼龙等材料制作绝缘体,这些材料内含极性基因,吸湿性大,在常温下绝缘性能可满足产品要求,而在高温潮湿下则绝缘性能不合格。
后采用特种工程塑料PES(聚苯醚砜)材料,产品经200℃、1000h和240h潮湿试验,绝缘电阻变化较小,仍在105MΩ以上,无异常变化。
2.2.2温度高温会破坏绝缘材料,引起绝缘电阻和耐压性能降低。
对金属壳体,高温可使接触件失去弹性、加速氧化和发生镀层变质。
如按GJB598生产的耐环境快速分离电连接器系列II产品,绝缘电阻规定25℃时应不小于5000MΩ,而200℃时,则降低至不小于500MΩ。
2.2.3温度潮湿环境引起水蒸气在绝缘体表面的吸引和扩散,容易使绝缘电阻降低到MΩ级以下。
长期处于高温环境下会引起绝缘体物理变形、分解、逸出生成物,产生呼吸效应及电解腐蚀及裂纹。
如按GJB2281生产的带状电缆电连接器,标准大气条件下的绝缘电阻值应不小于5000MΩ,而经相对湿度90%~95%、温度40±2℃、96h湿热试验后的绝缘电阻降至不小于1000MΩ。
2.2.4污损绝缘体内部和表面的洁净度对绝缘电阻影响很大,由于注塑绝缘体用的粉料或胶接上、下绝缘安装板的胶料中混有杂质,或由于多次插拔磨损残留的金属屑及锡焊端接时残留的焊剂渗入绝缘体表面,都会明显降低绝缘电阻。
如某厂生产的圆形电连接器在成品交收试验时发现有一个产品接触件之间的绝缘电阻很低,仅20MΩ,不合格。
后经解剖分析发现,这是因注塑绝缘体用的粉料中混有杂质而造成的。
后只得将该批产品全部报废。
2.2.5试验电压绝缘电阻检验时施加的试验电压对测试结果有很大关系。
因为试验电压升高时,漏电流的增加不成线性关系,电流增加的速率大于电压增加的速率,故试验电压升高时测得的绝缘电阻值将会下降。
电连接器产品技术条件引用的试验方法中,对试验电压都有明确的规定,通常规定为500V。
因此不能用一般欧姆表、直流电桥等电阻测量仪器来测量绝缘电阻。
2.2.6持续时间(读数时间)由于被测电连接器在测量极之间存在着一定的电容,测量初期电源先要对电容充电,因此在测试时往往会出现绝缘电阻测试仪上指示的电阻值有逐渐上升的趋势,这是正常现象。
不少电连接器试验方法中明确规定,读取绝缘电阻测试仪上的读数必须在电压施加1min后进行。
2.3问题研讨2.3.1检验环境温、湿度的影响电连接器技术条件通常都规定了产品的使用环境温度和湿度,如温度为-55~125℃,湿度为40±2℃、95%±3%。
笔者认为,检验环境条件和使用环境条件是有区别的。
技术条件规定产品可以在上述温湿度使用环境下工作,并不意味着生产厂在上述使用环境条件下测试绝缘电阻都应满足正常大气压下的考核指标。
如有使用温度上限125℃和40±2℃、93%±3%湿热环境条件下测绝缘电阻,则应按技术条件规定的高温和湿热环境试验的考核指标进行考核,而不应按正常大气压下的考核指标进行考核。
笔者在实际检验时多次发现,同一批产品在北方气候较干燥的条件下(湿度<50%)出厂检验绝缘电阻大于1000MΩ,是合格的;但产品发运至南方使用厂,在较潮湿的环境下(湿度>80%)复验,绝缘电阻仅为100MΩ~200MΩ,属不合格。
遇此情况,有时用酒精清洗烘干后,刚取出检验是合格的,但放置到次日再复测又不合格。
为此,建议生产厂在产品交收试验时,应将绝缘电阻控制在规定值以上一个恰当水平,保持有一定的裕度;不要将在干燥环境下勉强达到规定值的产品判为合格出厂,以免供需双方因检验气候环境条件不同造成检验结果不一致而引起争议。
为明确检验环境温湿度要求,现在有部分试验方法既规定了测试的环境温湿度(相对较宽的范围),又规定了出现分歧仲裁时的温湿度要求(相对取中限较窄的范围)。
如GJB1217-91《电连接器试验方法》规定:试验的标准大气条件,温度15~35℃,湿度20%~80%,气压73~103kPa。
仲裁试验的标准大气条件,温度25±1℃,湿度50%±2%,气压86~106kPa。
2.3.2检验工装的影响电连接器技术条件规定,电连接器所有接触件之间和所有接触件与壳体之间的绝缘电阻都应符合规定值;又规定其施加电压的持续时间要大于1min。
故许多电连接器生产厂对其所生产的每一型号规格产品都备有相应的2~3个不同编排连接方式的检验工装(头孔配座针工装或头针配座孔工装),通过对其接触件点与点之间、排与排之间和所有接点与壳体之间并联施加试验电压,检验其绝缘电阻是否合格。
这种用检验工装并联施加电压比单个接点间施加电压条件苛刻。
故若用检验工装测试发现绝缘电阻不合格时,允许不用工装直接用表棒在单点间施加电压进行复测。
但现有部分生产厂和绝大多数使用单位都不用检验工装,而是直接采用与绝缘电阻测试仪相连的两根测试表棒,在每个接触件之间或接触件与壳体之间搭接,检验其绝缘电阻是否合格。
这种不同检验工装的方法有以下缺点:一是随机性很大,极有可能产生漏检;二是每个接点不可能像有检验工装那样,可以停留1min后再读数,故有可能造成误判,检验的可靠性较差。
当然,即使使用检验工装,在检验前必须首先保证工装合格,要保证工装洁净和干燥,其本身绝缘电阻必须合格,且留有充分余量。
3介质耐压检验3.1作用原理介质耐压检验又称抗电强度检验。
它是在连接器接触件与接触件之间、接触件与壳体之间,在规定时间内施加规定的电压,以此来确定连接器额定电压下能否安全工作,能否耐受由于开关浪涌及其它类似现象所导致的过电位的能力,从而评定电连接器绝缘材料或绝缘间隙是否合格。
如果绝缘体内有缺陷,在施加试验电压后,则必然产生击穿放电或损坏。
击穿放电表现为飞弧(表面放电)、火花放电(空气放电)或击穿(击穿放电)现象。
过大漏电流可能引起电参数或物理性能的改变。
由于过电位,即使是在低于击穿电压时也可能有损于绝缘或降低其安全系数,所以应当慎重地进行介质耐压检验。
在例行试验中,如果需要连续施加试验电压时,最好在进行随后的试验时降低电位。
3.2影响因素主要受绝缘材料、洁净度、湿度、大气压力、接触件间距、爬电距离和耐压持续时间等因素影响。
3.2.1绝缘材料设计必须选用恰当的工程塑料制作绝缘体,才能满足预定的耐压性能指标要求。
如选用击穿电压为16kV/mm的PES(聚苯醚砜)特种工程塑料,能满足GJB598《耐环境快速分离圆形电连接器》YB系列II产品标准大气压下耐压为1500V的要求。
氟塑料(F4)具有比其它材料更高的介质耐压和绝缘电阻,广泛用于制作射频同轴电连接器绝缘体。
3.2.2洁净度绝缘体内部和表面洁净度对介质耐压影响很大。
笔者在某圆形连接器补充筛选时发现有一产品要求耐压1500V,实际测试施加电压至400V,即在两个接触件之间产生击穿现象。
经与生产厂共同进行解剖分析后认为:击穿发生于绝缘体上、下两个绝缘安装板的胶接界面,是由于胶粘剂中混有杂质所致。
3.2.3湿度增加湿度会降低介质耐压。
如J36A矩形电连接器技术条件规定:正常条件下耐压为1000V;而经40±2℃、93%±2℃、48h湿热试验后耐压降为500V。
3.2.4低气压在空气稀薄的高空,绝缘体材料会放出气体污染接触件,并使电晕产生的趋势增加,耐压性能下降,使电路产生短路故障。
故高空使用的非密封电连接器都必须降额使用,如Y27A圆形电连接器技术条件规定:正常条件下耐压为1300V,而在1.33Pa低气压条件下耐压降为200V。
3.2.5接触件间距连接器的小型化和高密度的发展,具体体现在矩形电连接器和印制电路电连接器上,要求间距能达到0.635mm,甚至0.3mm,外形尺寸中最关键的高度尺寸已减小到1~1.5mm。
表面贴装技术(SMT)与小型化的发展有着密切的关系。
这就要求我们选用耐压性能更高的绝缘材料,以满足设计尺寸小型化的要求。
3.2.6爬电距离它是指接触件与接触件之间,或接触件与壳体之间沿绝缘体表面量得的最短距离。
爬电路离短容易引起表面放电(飞弧)。
故有部分连接器的绝缘安装板表面插针(孔)安装孔设计成凹凸台阶形状,以增加爬电距离,提高抵抗表面放电的能力。
3.2.7耐压持续时间一般电连接器技术条件均规定为电压施加到规定值后持续1min应无击穿、飞弧、放电现象。
但许多电连接器生产厂在做成品交收试验时,为提高检测速度,往往采用提高试验电压20%、缩短耐压持续时间为5s或10s的方法。
笔者认为,它们之间不存在某种函数关系。
从交流耐压击穿机理来分析,击穿主要是由泄漏引起的,即泄漏电流大于规定值就认为击穿。
另一种是热击穿,提高试验电压强加泄漏,热击穿与时间长短没有关系。
如国军标GJ1217-91《电连接器试验方法》规定,试验电压加至规定值后应持续1min。
当有规定时,厂内质量一致性试验时的保持时间可降至最少5s。