精密和超精密加工技术复习题
精密及超精密加工技术复习思考题
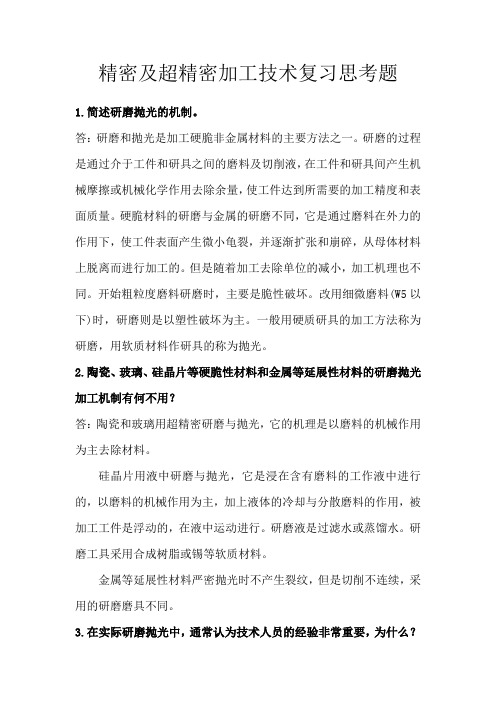
精密及超精密加工技术复习思考题1.简述研磨抛光的机制。
答:研磨和抛光是加工硬脆非金属材料的主要方法之一。
研磨的过程是通过介于工件和研具之间的磨料及切削液,在工件和研具间产生机械摩擦或机械化学作用去除余量,使工件达到所需要的加工精度和表面质量。
硬脆材料的研磨与金属的研磨不同,它是通过磨料在外力的作用下,使工件表面产生微小龟裂,并逐渐扩张和崩碎,从母体材料上脱离而进行加工的。
但是随着加工去除单位的减小,加工机理也不同。
开始粗粒度磨料研磨时,主要是脆性破坏。
改用细微磨料(W5以下)时,研磨则是以塑性破坏为主。
一般用硬质研具的加工方法称为研磨,用软质材料作研具的称为抛光。
2.陶瓷、玻璃、硅晶片等硬脆性材料和金属等延展性材料的研磨抛光加工机制有何不用?答:陶瓷和玻璃用超精密研磨与抛光,它的机理是以磨料的机械作用为主去除材料。
硅晶片用液中研磨与抛光,它是浸在含有磨料的工作液中进行的,以磨料的机械作用为主,加上液体的冷却与分散磨料的作用,被加工工件是浮动的,在液中运动进行。
研磨液是过滤水或蒸馏水。
研磨工具采用合成树脂或锡等软质材料。
金属等延展性材料严密抛光时不产生裂纹,但是切削不连续,采用的研磨磨具不同。
3.在实际研磨抛光中,通常认为技术人员的经验非常重要,为什么?答:一般来说手动抛光机之技术,多半都有是依照操作人员个人的操作经验与习惯而养成的抛光动作,往往都是因人而异,所以在手动抛光机的操作技术上,无法清楚的归纳具体的操场作技术,所以说通常认为技术人员的经验非常重要。
4.解释研磨、抛光、EEM和CMP的加工原理。
答:研磨加工原理:利用工件与研具相对运动,通过研磨剂作用而获得高质量、高精度的加工。
抛光加工原理:抛光是在较软质或有弹性变形特性只研磨布上,而只以塑性变形去除微小量的材料表面,使镜面加工变形少。
EEM加工原理:它的加工原理是高速旋转的树脂球对工件产生一定的压力和气流,并在它们之间加上含有磨料的工作液,使树脂球冲击或擦过工件表面进行加工。
精密与特种加工技术试题库及参考答案

精密与特种加工技术试题库及参考答案一、名词解释:1. 极性效应在电火花加工中, 把由于正负极性接法不同而蚀除速度不同的现象叫极性效应。
2. 线性电解液如NaCl电解液, 其电流效率为接近100%的常数, 加工速度v L和与电流密度i的曲线为通过原点的直线(v L=ηωi), 生产率高, 但存在杂散腐蚀, 加工精度差。
3. 平衡间隙(电解加工中)当电解加工一定时间后, 工件的溶解速度vL和阴极的进给速度v相等, 加工过程达到动态平衡, 此时的加工间隙为平衡间隙Δb 。
4. 快速成形技术是一种基于离散堆积成形原理的新型成形技术, 材料在计算机控制下逐渐累加成形, 零件是逐渐生长出来的, 属于“增材法”。
5. 激光束模式激光束经聚焦后光斑内光强的分布形式。
二、判断题:01.实验研究发现, 金刚石刀具的磨损和破损主要是由于111晶面的微观解理所造成的。
(√)02. 电解加工时由于电流的通过, 电极的平衡状态被打破, 使得阳极电位向正方向增大(代数值增大)。
(√)03. 电解磨削时主要靠砂轮的磨削作用来去除金属,电化学作用是为了加速磨削过程。
(×)04. 与电火花加工、电解加工相比, 超声波加工的加工精度高, 加工表面质量好, 但加工金属材料时效率低。
(√)05. 从提高生产率和减小工具损耗角度来看, 极性效应越显著越好, 所以, 电火花加工一般都采用单向脉冲电源。
(√)06. 电火花线切割加工中, 电源可以选用直流脉冲电源或交流电源。
(×)07. 阳极钝化现象的存在, 会使电解加工中阳极溶解速度下降甚至停顿, 所以它是有害的现象,在生产中应尽量避免它。
(×)08. 电子束加工是利用电能使电子加速转换成动能撞击工件, 又转换成热能来蚀除金属的。
(√)09.电火花线切割加工中, 电源可以选用直流脉冲电源或交流电源。
(×)10. 电火花加工是非接触性加工(工具和工件不接触), 所以加工后的工件表面无残余应力。
精密和超精密加工技术期末考试题及答案

1、八面体的单晶金刚石的晶体结构包括晶轴、晶面、面网密度和面网距。
晶面:通过原子中心的平面,即晶体中各种方位上的原子面。
晶轴:与晶面垂直的轴面网密度(致密度) :面网单位面积上的原子数面网距:晶体面网之间的距离用解理现象解释晶体的好磨难磨方向:解理现象是某些晶体特有的现象,晶体受到定向的机械力作用时,沿平行于某个平面平整的劈开的现象。
解理发生的原因主要是因为111)面的宽的面间距是金刚石晶体中所有晶面间距中的最大的一个,并且其中的连接共价键数最少,只需击破一个价键就可使其劈开。
金刚石的解理现象即沿解理面(111)平整的劈开两半,且金刚石的破碎和磨损都和解理现象直接有关。
金刚石的耐磨性可用相对磨削率来表示,对于金刚石研磨时,各晶面均有“好磨”和“难磨”方向。
高磨削率方向称为“好磨方向”,低磨削率方向称为“难磨方向”。
2、高速切削应用场合,由哪些特点决定的?应用场合:1)航空航天:由于有大量薄壁、细筋的大型轻合金整体构件加工,高速切削,随切削速度提高,切削力可减少30%以上,可以减少工件变形。
铝合金整体结构件的高速切削,不再铆接,省去了装配工作;薄壁件加工等。
2)模具业:高速切削可加工硬度HRC45~65的淬硬钢铁件,如高速切削加工淬硬后的模具可减少甚至取代放电加工和磨削加工,满足加工质量的要求,加快产品开发周期,大大降低制造成本。
3)汽车工业:采用高速数控机床和高速加工中心组成高速柔性生产线,实现多品种、中小批量的高效生产,高速切削使加工时间减少,切削效率提高3~5倍。
加工成本可降低20%-40%。
4)仪器仪表:精密光学零件加工。
转速的提高,使切削系统的工作频率远离机床的低阶固有频率,加工中鳞刺、积屑瘤、加工硬化、残余应力等也受到抑制。
因此,高速切削加工可大大降低加工表面粗糙度,加工表面质量可提高1~2等级。
有利于减少加工零件的内应力和热变形,也提高了加工精度。
这题有个简单的答案由于高速切削加工具有高生产效率,减少切削力,提高加工精度和表面质量,降低生产成本并且可加工高硬材料等许多优点,已在汽车和摩托车制造业、模具业、轴承业、航空航天业、机床业、工程机械、石墨电极等行业中广泛应用。
精密加工技术期末复习资料
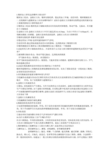
1.精密加工研究包括哪些主要内容?精密加工机床,金刚石刀具,精密切削机理,稳定的加工环境,误差补偿,精密测量技术二.实现精密与超精密加工应具备哪些条件?试结合金刚石刀具精密切削简述切削用量对加工质量的影响及主要控制技术?①精密加工机床-精密机床主轴轴承要求具有很高的回转精度,转动平稳,无振动,其关键在于主轴轴承②金刚石刀具-金刚石刀具的刀口半径只能达到0.1-0.3/um。
当刃口半径小于0.01um时,必须解决测量上的难题。
金刚石晶体的晶面选择。
金刚石刀具刃口的锋利性③精密切削机理-掌握其变化规律④稳定的加工环境-包括恒温防振和空气净化⑤误差补偿-通过消除或抵消误差本身的影响,达到提高加工精度的目的⑥精密测量技术-精密加工要求测量精度比加工精度高一个数量级3.试述常用几种主轴轴承的特点,并说明为什么目前大部分精密和超精密机床采用空气轴承?①液体静压轴承-特点:转动平稳无振动,达到较高的刚度空气轴承-特点:刚度低,承受载荷小②空气轴承造成的热变形小,刚度低,只能承受较小的载荷,超精密切削时切削力小,空气轴承能满足要求4.试述在线检测和误差补偿技术在精密加工中的作用精密和超精密加工的精度是依靠检测精度来保证的,而为了消除误差进一步提高加工精度,必须使用误差补偿技术5.常用微量进给装置有哪些种类与作用?①机械传动或液压传动式②弹性变形式③热变形式④流体膜变形式⑤磁致伸缩式⑥电致伸缩式作用:为了实现精密与超精密加工6.金刚石刀具破损形式①裂纹:结构缺陷可产生裂纹,另外当切屑经过刀具表面时,金刚石收到循环应力的作用也可产生裂纹②碎裂:由于金刚石材料较脆,在切削过程中收到冲击和振动都会使金刚石刀刃产生细微的解理形成碎裂③解理:金刚石晶面方面选择不当,切削力容易引起金刚石的解理,刀具寿命下降7.金刚石刀具磨损形式①机械磨损②破损③碳化磨损8.微量进给机构的作用及类型①电致伸缩微量进给装置,作用:用于误差在线补偿②机械结构弹性变形微量进给装置,作用:用于手动操作③压电或电致伸缩微量进给装置,作用:用于实现自动微量进给9.导轨类型①滚动导轨②液体静压导轨③气浮导轨和空气静压导轨10.为什么精密切削加工会产生碾压作用?在刃口圆弧处,不同的切削深度,刀具的实际前角是变化的,实际前角为较大的负前角,在刀具刃口圆弧处将产生很大的挤压摩擦作用,被加工表面将产生残余压应力1.精密磨削加工按磨料加工大致分为哪几类?试述其特点及适用场合①磨料加工,固结磨料加工:磨削,砂轮磨削,砂带磨削研磨等游离磨料加工:抛光,研磨:干式研磨,湿式研磨,磁式研磨。
精密加工与特种加工技术试题(一)
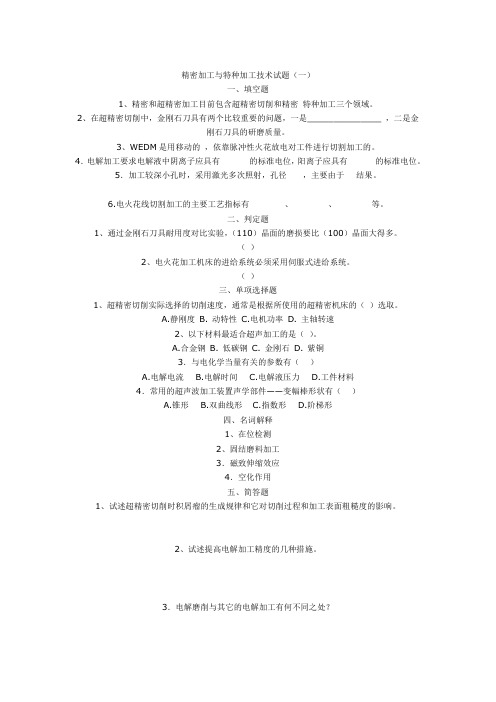
精密加工与特种加工技术试题(一)一、填空题1、精密和超精密加工目前包含超精密切削和精密特种加工三个领域。
2、在超精密切削中,金刚石刀具有两个比较重要的问题,一是______________ ,二是金刚石刀具的研磨质量。
3、WEDM是用移动的,依靠脉冲性火花放电对工件进行切割加工的。
4.电解加工要求电解液中阴离子应具有的标准电位,阳离子应具有的标准电位。
5.加工较深小孔时,采用激光多次照射,孔径,主要由于结果。
6.电火花线切割加工的主要工艺指标有、、等。
二、判定题1、通过金刚石刀具耐用度对比实验,(110)晶面的磨损要比(100)晶面大得多。
()2、电火花加工机床的进给系统必须采用伺服式进给系统。
()三、单项选择题1、超精密切削实际选择的切削速度,通常是根据所使用的超精密机床的()选取。
A.静刚度B. 动特性C.电机功率D. 主轴转速2、以下材料最适合超声加工的是()。
A.合金钢B. 低碳钢C. 金刚石D. 紫铜3.与电化学当量有关的参数有()A.电解电流B.电解时间C.电解液压力D.工件材料4.常用的超声波加工装置声学部件——变幅棒形状有()A.锥形B.双曲线形C.指数形D.阶梯形四、名词解释1、在位检测2、固结磨料加工3.磁致伸缩效应4.空化作用五、简答题1、试述超精密切削时积屑瘤的生成规律和它对切削过程和加工表面粗糙度的影响。
2、试述提高电解加工精度的几种措施。
3.电解磨削与其它的电解加工有何不同之处?4.什么是极性效应?在电火花加工中如何充分利用极性效应?六、综合题1.光华机械厂用NaCl电解液加工一种铝零件,加工余量为30cm3,要求2min电解加工完一个零件,求需要用多大的电流?如有2800A容量的直流电源,电解时间需要多少?(ω=124mm3/(A•h),η=96%)2.需要线切割加工如下图所示的轨迹,编写线切割加工轨迹控制的3B程序。
3.用3B代码编制加工图所示的线切割加工程序。
已知线切割加工用的电极直径为0.18mm,单边放电间隙为0.01mm,图中A点为穿丝孔,加工沿A-B精密加工与特种加工试卷(二)一、填空题1、精密和超精密加工目前包含超精密切削、和精密特种加工三个领域。
精密和超精密加工技术

1、通常将加工精度在0.1-1um、加工表面粗糙度R在0.02-0.1um之间的加工方法称为精密加工。
而将加工精度高于0.1um、加工表面粗糙度R小于0.01um的加工方法称为超精密加工。
2、提高加工精度的原因:提高制造精度后可提高产品的性能和质量,提高其稳定性和可靠性;促进产品的小型化;增强零件的互换性,提高装配生产率,并促进自动化装配。
3、精密和超精密加工目前包含三个领域:超精密切削;精密和超精密磨削研磨‘精密特种加工。
4、金刚石刀具的超精密切削加工技术,主要应用于两个方面:单件的大型超精密零件的切削加工和大量生产的中小型零件的超精密切削加工技术。
5、金刚石刀具有两个比较重要的问题:晶面的选择;切削刃钝圆半径。
6、超稳定环境条件主要是指恒温、防振、超净和恒湿五个方面的条件。
7、我国应开展超精密加工技术基础的研究,其主要内容包括以下四个方面:1)超精密切削、磨削的基本理论和工艺。
2)超精密设备的关键技术、精度、动特性和热稳定性。
3)超精密加工的精度检测、在线检测和误差补偿。
4)超精密加工的环境条件。
5)超精密加工的材料。
8、超精密切削实际选择的切削速度,经常是根据所使用的超精密机床的动特性和切削系统的动特性选取,即选择振动最小的转速。
9、超精密切削实际能达到的最小切削厚度和金刚石刀具的锋锐度、使用的超精密机床的性能状态、切削时的环境等都直接有关。
10、为实现超精密切削,刀具应具有如下性能:1)极高的硬度、极高的耐磨性和极高的弹性模量,以保证刀具有很长的寿命和很高的尺寸耐用度。
2)切削刃钝圆能磨得极其锋锐,切削刃钝圆半径r值极小,能实现超薄切削厚度。
3)切削刃无缺陷,切削时刃形将复印在加工表面上,能得到超光滑的镜面。
4)和工件材料的抗粘结性好、化学亲和性小、摩擦因素低,能得到极好的加工表面完整性。
11、SPDT——金刚石刀具切削和超精密切削。
12、晶体受到定向的机械力作用时,可以沿平行于某个平面平整地劈开的现象称为解理现象。
精密特种加工考试题库(考试必备)选择填空判断等
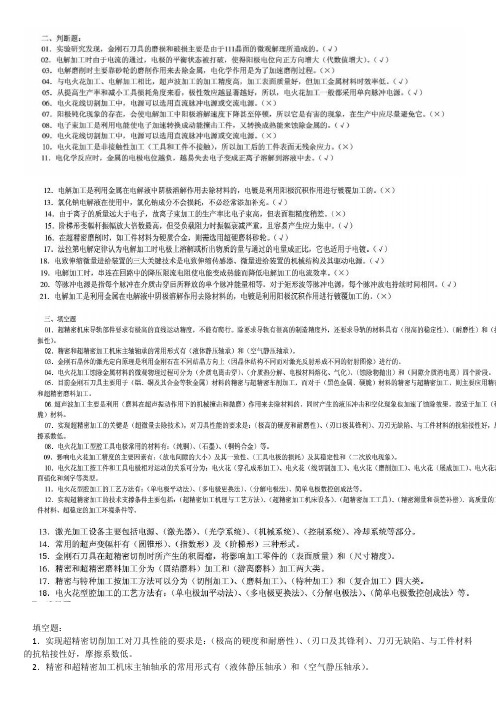
填空题:1.实现超精密切削加工对刀具性能的要求是:(极高的硬度和耐磨性)、(刃口及其锋利)、刀刃无缺陷、与工件材料的抗粘接性好,摩擦系数低。
2.精密和超精密加工机床主轴轴承的常用形式有(液体静压轴承)和(空气静压轴承)。
3.金刚石晶体的激光定向原理是利用金刚石在不同结晶方向上(因晶体结构不同而对激光放射形成不同的衍射图像)进行的。
4.电火花加工蚀除金属材料的微观物理过程可分为(介质电离击穿)、(介质热分解、电极材料熔化、气化)、(蚀除物抛出)和(间隙介质电离)四个阶段。
5.超精密加工机床的关键部件主要有:(精密主轴部件)、(导轨部件)和(进给驱动系统)等。
5 超精密加工机床的关键部件主要有:(精密主轴部件)、(导轨部件)和(进给驱动系统)等。
6.电火花加工粗加工时工件常接(负)极,精加工时工件常接(正)极;线切割加工时工件接(正)极;电解加工时工件接(正)极;电解磨削时工件接(正)极;电镀时工件接(负)极。
7.电子束加工是在(真空)条件下,利用(聚焦后能量密度极高、速度极高的电子)对工件进行加工的方法。
8.精密和超精密磨料加工分为(固结磨料)加工和(游离磨料)加工两大类。
9.电火花型腔加工时使用最广泛的工具电极材料是:(纯铜)和(石墨)。
10.影响电火花加工精度的主要因素有:(放电间隙的大小)及其一致性、(工具电极的损耗)及其稳定性和(二次放电现象)。
11.超精密机床主轴的驱动方式主要有电动机通过带传动驱动、(电动机通过柔性联轴器驱动)和(采用内装式同轴电动机驱动)三种。
12.超精密加工中超稳定的加工环境条件主要指(恒温)、(恒湿)、(防振)和(超净)四个方面的条件。
13.目前金刚石刀具主要用于(铝、铜及其合金等软金属)材料的精密与超精密加工,而对于(黑色金属)材料的精密与超精密加工,则主要应用精密和超精密磨料加工。
14.电火花加工按工件和工具电极相对运动的关系可分为:电火花(穿孔成形加工)、电火花(线切割加工)、电火花(磨削加工)、电火花(展成加工)、电火花表面强化和刻字等类型。
精密与超精密加工技术精密与超精密加工技术部分习题
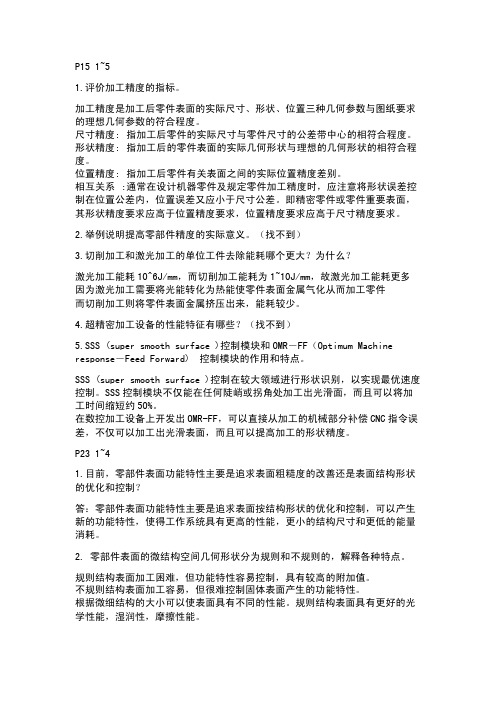
P15 1~51.评价加工精度的指标。
加工精度是加工后零件表面的实际尺寸、形状、位置三种几何参数与图纸要求的理想几何参数的符合程度。
尺寸精度:指加工后零件的实际尺寸与零件尺寸的公差带中心的相符合程度。
形状精度:指加工后的零件表面的实际几何形状与理想的几何形状的相符合程度。
位置精度:指加工后零件有关表面之间的实际位置精度差别。
相互关系:通常在设计机器零件及规定零件加工精度时,应注意将形状误差控制在位置公差内,位置误差又应小于尺寸公差。
即精密零件或零件重要表面,其形状精度要求应高于位置精度要求,位置精度要求应高于尺寸精度要求。
2.举例说明提高零部件精度的实际意义。
(找不到)3.切削加工和激光加工的单位工件去除能耗哪个更大?为什么?激光加工能耗10^6J/mm,而切削加工能耗为1~10J/mm,故激光加工能耗更多因为激光加工需要将光能转化为热能使零件表面金属气化从而加工零件而切削加工则将零件表面金属挤压出来,能耗较少。
4.超精密加工设备的性能特征有哪些?(找不到)5.SSS (super smooth surface )控制模块和OMR-FF(Optimum Machine response-Feed Forward)控制模块的作用和特点。
SSS (super smooth surface )控制在较大领域进行形状识别,以实现最优速度控制。
SSS控制模块不仅能在任何陡峭或拐角处加工出光滑面,而且可以将加工时间缩短约50%。
在数控加工设备上开发出OMR-FF,可以直接从加工的机械部分补偿CNC指令误差,不仅可以加工出光滑表面,而且可以提高加工的形状精度。
P23 1~41.目前,零部件表面功能特性主要是追求表面粗糙度的改善还是表面结构形状的优化和控制?答:零部件表面功能特性主要是追求表面按结构形状的优化和控制,可以产生新的功能特性,使得工作系统具有更高的性能,更小的结构尺寸和更低的能量消耗。
2. 零部件表面的微结构空间几何形状分为规则和不规则的,解释各种特点。
- 1、下载文档前请自行甄别文档内容的完整性,平台不提供额外的编辑、内容补充、找答案等附加服务。
- 2、"仅部分预览"的文档,不可在线预览部分如存在完整性等问题,可反馈申请退款(可完整预览的文档不适用该条件!)。
- 3、如文档侵犯您的权益,请联系客服反馈,我们会尽快为您处理(人工客服工作时间:9:00-18:30)。
2)刃口能磨得极其锋锐,刃口半径值极小,能实现超薄切削厚度。
3)刀刃无缺陷,切削时刃形将复印在加工表面上,能得到超光滑的镜面。
4)和工件材料的抗粘结性好、化学亲和性小、摩擦系数低,能得到极好的加工表面完整性。
天然单晶金刚石有着一系列优异的特件。如硬度极高、耐磨性和强度高、导热性能好、和有色金属摩擦系数低,能磨出极锋锐的刀刃等。因此虽然它的价格昂贵,仍被一致公认为理想的、不能代替的超精密切削刀具材料。
46、集成电路的主要工艺有外延生长、氧化、光刻、选择扩散和真空镀膜等。
47、所谓恒温条件主要两个指标来进行衡量:恒温基数、恒温精度。
48、外部支撑环境主要包括空气环境、热环境、振动环境、声环境和电场、电磁环境等。
49、空气过滤器是空气净化的关键设备,过滤器的性能指标主要有效率、阻力、容尘量、风速和虑速等。
第七章
38、研磨加工通常是指利用硬度比加工材料更高的微米级磨粒,在硬质研磨盘作用下产生的微切削和滚轧作用实现被加工表面的微量材料去除,使工件的形状、尺寸精度达到要求值,并降低表面粗糙度、减小加工变质层的加工方法。
被加工材料的去除是依靠磨粒的滚轧作用或微切削作用。
39、研磨加工的主要特点:微量切削、按进化原理成形、多刃多向切削。
提高制造精度后可提高产品的性能和质量,提高其稳定性和可靠性;促进产品的小型化;增强零件的互换性,提高装配生产率,并促进自动化装配。
3.精密和超精密加工现在包括哪些领域。
答:精密和超精密加工目前包含三个领域:
1)超精密切削,如超精密金刚石刀具切削,可加工各种镜面。它成功地解决了高精度陀螺仪,激光反射镜和某些大型反射镜的加工。
5)工艺件好,容易制造。
6)微量近给机构应又有好的动特性,即具有高的频响。
7)微量进给机构应能实现微进给的自功控制。
第五章
28、试述精密加工中测量技术的新发展。
答:精密加工中测量技术的新发展主要包括:
1.极高精度测量方法和测量仪器的发展
近年研制成功测量长度时能达到 级的双频激光测量系统和x射线事涉仪等;测量表面微观形貌达 级的扫描隧道显微镜和原了力显微镜等,测量角度达到 的精密测角仪等。
36、试述微位移系统的作用及其成。
答:微位移系统一般由微位移机构、检测装置和控制系统所组成,其目的是要实现小行程(一般小于毫米级)、高灵敏度和高精度(—般为亚微米、纳米级)的位移。微位移机构是实现微位移的执行机构、其核心部分是微位移器件。
37、压电效应:电介质受到机械应力作用时,会产生电极化(表面产生电荷),电极化的大小(电荷密度)与施加的机械应力成正比,电极化的方向随应力的方向而改变,这种现象称为正压电效应,简称压电效应。压电效应和电致伸缩效应统称为机电耦合效应。
第四章
27、液体静压轴承有较高的刚度和回转精度,但有下列缺点不易解决:
1.液体静压轴承的油温升高。2.静压油回油时将空气带人油源。
解决的措施:1.提高静压油的压力到6-8MPa,使油中微小气泡的影响减小,提高了静压轴承的刚度和动特性。
2.静压轴承用油经温度控制,基本达到恒温,减少轴承的温升。
3.轴承用恒温水冷却,减小轴承的温升。
43、电子束、离子束、激光束
44、激光除了具有普通光的反射、折射、绕射和干涉等共性外,尚有一些特有的特性:
1.强度高、亮度大。2.单色性好,波长谱线宽度狭窄;3.相干性好,相干长度长;4.方向性好,发散角可达0.1mrad,光束直径可聚到0.01mm。
45、激光的表面改性利用激光对材料表面进行处理可改变其物理结构、化学成分和金相组织,从而改善材料表面的物理、力学、化学性质,如硬度、耐磨性、耐疲劳性、耐腐蚀性等,称之为激光表面改性技术。
9、超精密切削能达到的最小切削厚度与那些因素有关
答:实际切削达到的的最小切削厚度和金刚石刀具的锋锐度、使用的超精密机床的性能状态、切削时的环境条件等都有直接有关。还有被切材料的物理力学性能有关。
10、超精密切削对刀具有哪些要求?为什么单晶金刚石是被公认为理想的、不能代替的超精密切削的刀具材料?
答:为实现超精密切削。刀具应具有如下性能。
17、金刚石粗研效率与下列因素有关:研磨方向、研磨速度和压力、使用的金刚石微粉的粒度等。
18、精研与那些因素有关:磨料粒度、研磨盘质量、研磨方向、精抛。
第三章
19、精密和超精密磨料加工是利用细粒度的磨粒和微粉对黑色金属、硬脆材料等进行加工等得到高加工精度和小表面粗糙度值。
20、精密和超精密磨料加工可分为固结磨料和游离磨料两大类加工方式,
在线检测:即工件在加工过程中同时进行检测。特点:1)能够连续检测加工过程中的变化,了解在加工过程中误差分布和发展;2)检测结果能反映实际加工情况;3)在线检测由于是在加工过程中进行,会受到加工过程中的一些条件限制,在线检测的难度一般较大;4)在线检测大都用非接触传感器,对传感器的性能要求较高。非接触测量不会破坏已加工表面;5)在线检测一般是自动运行,形成在线检测系统,包括误差信号的采集、处理和输出。
6、超稳定环境条件主要是指恒温、防振、超净和恒湿。相应发展起恒温技术、防振技术、净化技术。
7、我目要发展精密和超精密加工技术,应重点发展哪些方面的内容。
答:根据我国的当前实际情况,参考国外的发展趋势,我国应开展超精密加工技术基础的研究,其主要内容包括以下几个方面:
1)超精密切削磨削的基本理论和工艺;
40、精密研磨与抛光加工的主要工艺因素包括加工设备、研具、磨粒、加工液、工艺参数和加工环境等。
第八章
41、现代制造技术的发展有两大趋势,一是向着自动化、柔性化、集成化、智能化等方向发展。二是寻求制造技术极小尺度、极大尺度和极端功能的极限发展。
42、微细加工技术是指制造微小尺寸零件的生产加工技术。
精度是用其加工误差与加工尺寸的比值来表示,在微细加工时,由于加工尺寸很小,精度就必须用尺寸的绝对值来表示。
11、SPDT:金刚石刀具切削和超精密切削等同起来叫做。
12、试述超精密切削用金刚石刀具的磨损和破损特点。
答:金刚石刀具的磨损,主要是机械磨损,其磨损本质是微观解理的积累。金刚石晶体的破损,主要产生于(111)晶面的解理。
13、金刚石晶体有哪些定向方法?
答:现在采用的金刚石晶体定向方法有:人工目测定向;X射线晶体定向;激光晶体定向。
21、涂覆磨具:基底、粘接膜、粘接剂(底胶)、粘接剂(覆胶)、磨粒。
22、所用磨床应满足以下要求:高几何精度、低速进给运动的稳定性、减少振动。
23、超硬磨料砂轮目前主要指金刚石砂轮和立方氮化硼(CBN)砂轮。
24、超硬磨料砂轮磨削的共同特点是:
答:1.可用来加工各种高硬度、高脆性金属材料和非金属材料。
在位检测:工件加工完毕后,在机床上不卸下工件的情况下进行检测,称之为在位检测。特点:在位检测也只能检测加工后的结果,也不一定能反映加工时的实际情况.同时也不能连续检测加工过程的变化,但可免除离线检测时由于定位基准所带来的误差,如加工时所用的定位基准与检测时所用的定位基准不重合,工件上定位基准的制造误差所造成的定位基准位移等。因此,与离线检测相比,其检测结果更接近实际加工情况。
精密和超精密加工技术
第一章
1.从机械制造技术发展看,过去和现在达到怎样的精度可被称为精密和超精密加工。
答:通常将加工精度在0.1-lμm,加工表面粗糙度在Ra0.02-0.1μm之间的加工方法称为精密加工。而将加工精度高于0.1μm,加工表面粗糙度小于Ra0.01μm的加工方法称为超精密加工。
2、现代机械工业之所以要至于提高加工精度,其主要原因在于:
2)超精密设备的精度,动特性和热稳定性;
3)超精密加工精度检测及在线检测和误差补偿;
4)超精密加工的环境条件;
5)超精密加工的材料。
第二章
8、金刚石刀具超精密切削的切削速度应如何选择?
答:超精密切削实际选择的切削速度,经常是根据所使用的超精密机床的动特性和切削系统的动特性选取,即选择振动最小的转速,因为在该转速时表面粗糙度最小,加工质量最高,获得高质量的加工表面是超精密切削的首要问题。使用质量好,特别是动特性好,振动小的超精密机床可以使用高的切削速度,可以提高加工的效率。
26、.超精密磨削的含义是什么?镜面磨削的含义是什么?
答:超精密磨削是最高加工精度、最低表面粗糙度的砂轮磨削方法。一般是指加工精度达到或者高于0.1μm,加工表面粗糙度小于Ra0.025μm,是一种亚微米级的加工方法。镜面磨削一般是指加工表面粗糙度达到Ra0.02-0.01μm,表面光泽如镜的磨削方法。
28、精密加工对微量进给装置的性能要求是什么?
答:1)精微进给和粗进给应分开、以提高微位移的精度、分辨力和稳定性。
2)运动部分必须是低摩擦和高稳定度的,以便实现很高的重复精度。
3)末级传动元件必须有很高的刚度,即夹金刚石刀具处必须是高刚度的。
4)微量进给机构内部联接必须是可靠联接,尽量采用整体结构或刚性联接,否则这微量进给机构很难实现很高的重复精度。
14、设计超精密切削用金刚石刀具最主要的问题有三个:优选切削部分的几何形状,前后面选择最佳晶面,确定刀具结构和金刚石在刀具上的固定方法。
15、试述金刚石刀具的金刚石固定方法。
答:机械夹固;粉末冶金法固定;粘结或钎焊固定。
16、.试述单晶金刚石刀具的研磨加工方法。
答:一颗单晶金刚石毛坯,要做成精密金刚石刀具。首先要经过晶体定向,确定制成刀具的前面、后面的空间位置,确定需要磨去的部分。金刚石要再经过仔细检查,观察切削部分的金刚石内部有没有裂纹、杂质或其他缺陷。金刚石开始粗磨,一般采用高速旋转的铸铁盘加金刚石微粉进行粗研磨,基本成形后,最后进行精研。
35、试阐述离线检测、在位检测和在线检测的含义,并分析其特点。
答:离线检测:工件加工完毕后,从机床上取下,在机床旁或在检测室中进行检测,就是离线检测.特点:离线检测只能检测加工后的结果,不—定能反映加工时的实际情况,也不能连续检测加工过程的变化,但检测条件较好,不受加工条件的限制,可充分利用各种测量仪器。因此,测量的精度比较高。