Layout设计与改善的六大原则
LAYOUT

2)对应技术的进步和变化时 作业的机械化、自动化以及材料、加工 方法的技术进步和革新。 3)设计变更时 随着设计变更而工艺和作业方法必须变 更。 4)现状的工厂布置效率不佳时 根据稼动分析和工艺分析,现场有很多 浪费。
5)生产量常有增减时 生产量有巨大的增减,必须换装设备和工 序变更。 6)现场有必要移动时 全工厂部门间变更。 7)新产品投入时 新产品导入生产,必须增设机械、工程和 加工方法的变更。
3)按流程布局(层流) 流水化布局(层流) 精益生产称之为层流布局
1) 2) 3) 4) 5)
加工工序按功能划分布局的优点 各加工功能的利用率相对较高,可以减 少投资 产品及作业的改变较多,工艺复杂的情 况下容易对应 同种加工集中管理及培训容易 工种内抗干扰强,如:材料、人员、相 邻工序的干扰问题 容易计件
其他方面还应注意,运营管理的便利。形 式上直列流程未必最好。“U字布局”及 环形布局都可考虑。
LAYOUT的基本方式范围与参考标准
1)固定式布局方法(产品中心)
以产品为中心,人、机械、道具、移动。
2)按功能及加工方法布局(设备中心) • 传统布局(乱流)
• 按功能、区域放置的布局,精益生产称之为乱流布局。
装配作业流水化部局
1)
流水化、高效率 2) 易培训 3) 中间品减少 4) 一次布局,容易管理 5) 专业化,设备移动少 LAYOUT 改善大体分三个层面 A. 作业区域内的布局改善(零件工具的放置方法) B. 工厂、楼层、作业区域设定的布局(作业区的配置) C. 工厂设备布局(建筑物的设施等配置) 过道宽度参见表
相关性分析(Activity analysis)
LAYOUT 改善评价项目与公式
中外企业在布局差异上的比较
Layout 的原则
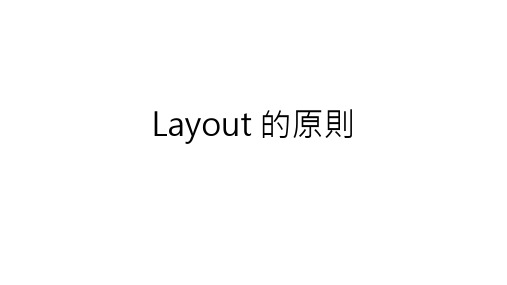
生產流程安排
− 單件流(one-piece-flow)原則 − 按工程順序,“一筆化”原則 − 三線一體原則(組裝、測試、維修在一起) − “成長帶”,不要離線作業 − 不要有“孤島式”佈局(例如烤爐,水洗…)
單件流 VS 批次流 (batch flow)
• 每次流動一個 • 在製品少,流動時間快
• 同批次中最後一件加工完 成後再移動
• 在製品多,流動時間慢
Little Law : L/T = Throughput rate x WIP
按工程順序佈局,“一筆化”原則
三線一體原則(組裝、測試、維修在一起)
“成長帶”,不要離線作業
பைடு நூலகம்
整体布局要有“阵势”…主观的感觉
− 座向要对。配合整体厂房、动线、规划产线动线流向 − 宽敞:产线间距、工位间距、过道间距、5S整理 − 明亮:车间灯光照度≥300-500Lux/色系标准 − 和谐/协调:不高低参差 − 一目了然:不要有管理死角(磨砂窗、房中房…)
LAYOUT应注意事项
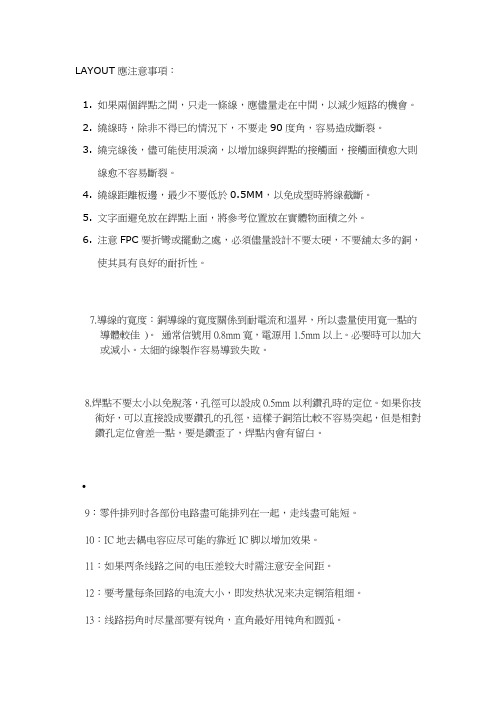
LAYOUT應注意事項:1.如果兩個銲點之間,只走一條線,應儘量走在中間,以減少短路的機會。
2.繞線時,除非不得已的情況下,不要走90度角,容易造成斷裂。
3.繞完線後,儘可能使用淚滴,以增加線與銲點的接觸面,接觸面積愈大則線愈不容易斷裂。
4.繞線距離板邊,最少不要低於0.5MM,以免成型時將線截斷。
5.文字面避免放在銲點上面,將參考位置放在實體物面積之外。
6.注意FPC要折彎或擺動之處,必須儘量設計不要太硬,不要舖太多的銅,使其具有良好的耐折性。
7.導線的寬度:銅導線的寬度關係到耐電流和溫昇,所以盡量使用寬一點的導體較佳)。
通常信號用0.8mm寬,電源用1.5mm以上。
必要時可以加大或減小。
太細的線製作容易導致失敗。
8.焊點不要太小以免脫落,孔徑可以設成0.5mm以利鑽孔時的定位。
如果你技術好,可以直接設成要鑽孔的孔徑,這樣子銅箔比較不容易突起,但是相對鑽孔定位會差一點,要是鑽歪了,焊點內會有留白。
9:零件排列时各部份电路盡可能排列在一起,走线盡可能短。
10:IC地去耦电容应尽可能的靠近IC脚以增加效果。
11:如果两条线路之间的电压差较大时需注意安全间距。
12:要考量每条回路的电流大小,即发热状况来决定铜箔粗细。
13:线路拐角时尽量部要有锐角,直角最好用钝角和圆弧。
14:对高频电路而言,两条线路最好不要平行走太长,以减少分布电容的影响,一般采取顶层底层众项的方式。
15:高频电路须考量地线的高频阻抗,一般采用大面積接地的方式,各点就近接地,减小地线的电感份量,讓各接地点的电位相近。
16:高频电路的走线要粗而短,减小因走线太长而产生的电感及高频阻抗对电路的影响。
17:零件排列时,一般要把同类零件排在一起,盡量整齐,对有极性的元件盡可能的方向一致,降低淺在的生产成本。
18:对RF机种而言,电源部份的零件盡量遠离接收板,以减少干擾。
19:对TF机种而言,发射器应盡可能离PIR远一些,以减少发射时对PIR造成的干扰。
精益生产之LAYOUT

业更加有序
简化
经过取消,合并,重排后的必要工序,应考虑能否采用
(Simplify)
最简单的方法及设备代替,以节省人力和时间
A.产品流程分析检查表
项目
内容
省略的工序
可以和其他工序 重新组合的工序 简化工序
1.是否有不必要的工序内容2.有效利用工装设备省略工序3. 改变作业场地省略工序4.调整改变工艺顺序省略工序5.通过 设计变更省略工序6.通过零件,材料变更省略工序
已经完成
正在进行
未完成
3.工程分析表
分析对 象 分析日 期
分析者
工程分析表
备注
加工时间合计
停滞时间合计
搬运时间合计
数量检查时间合计 符号
中间在制品时间合计 质量检查时间合计
作业内容 1 2 3 4 5 6 7 8 合计
数量 距离 时间(分) 问题点
某电子厂,由于成品包装车间的工作效率低,中间再制品 多,占用空间多,人员的积极性不高,包装作业生产周期 长,导致交货期延长的频率越来越高。为了快速解决问题, 分析如下:
品 质 部 出 库
数外 量观 检检 查查
搬输 运入 至机 电身 脑号
包 装 加 工
传 达
处
改善后包装作业流程图
封 搬储 箱 运存
至 成 品 仓
4.改变车间布局
品质部开关盒储存区
辅料存放 区
包装车间开关盒 临时存放区
电脑输入
保
出
证
书
包装LINE A
打 印
包装LINE B
区
包装LINE C
包装LINE D
73.2
104.3
单位:分
搬动距离 (米) 30
如何实现Layout最优化

如何实现Layout最优化课程描述:Layout即布局。
为了达到整个制造系统中人流与物流的运输顺畅化、搬运最优化、流程最优化和效率最大化,人们会通过工序之间、车间之间的研究,对整个工厂的整体设备、工作台、物流通道、仓库等配置、电、气设施等进行重新考虑和综合整理。
但怎样研究工厂布局现状?怎样选择最优、最与企业相匹配的布局形式?本课程将结合实战案例,为您一一阐述!解决方案:他山之石,可以攻玉!虽然各类生产行业在实现Layout最优化时,都有不同的策略,但万变不离其宗!下面我们从实战经验中给大家总结一些方法流程,以便大家参考!要实现Layout最优化,1.我们先要进行现状调查;2.同时进行现状分析;3.接着,我们要根据现状情况和需求选择与公司相匹配的layout 方式;4.最后,我们要对该方案进行评估。
进行现状调查时,主要是了解公司主产品的产品特征、产能需求、人力资源需求、工艺流程和生产辅助资料。
通过一系列相关信息的收集后,我们还得对现状分析,确认生产方式,对产品流程进行分析,通过接近关联分析或流入流出分析的方法对现状有个清晰把握。
得出现状结论后,我们需要适时选择正确的layout方式。
常见的layout种类有流程式、功能型、固定式和混合式这四种,但不是所有的都能拿来就用,我们要结合企业现状和选择依据,选出最合适的,比如,layout要做到统一原则、距离最短原则、价值流畅原则、立体空间充分利用原则、安全性原则和灵活机动性原则。
此外,我们还需要对Layout设计方案进行评估,通过观察其空间利用性、适应性、搬运效率和操作人员的方便性来评估方案是否合理,是否为最优。
最后,我们把这几个方面串起来,就形成了“实现Layout最优化”的完整流程。
感谢大家的学习,我们下堂课再见!或许文字的话大家并不是很清楚,我们可以看下面的思维导图,能让你更加形象的理解和明白该如何实现Layout最优化。
相关课程:如何运用MOD法设定标准时间如何推进初期清扫如何推行设备目视化管理如何建立设备自主管理机制如何实施专业保全活动想学习以上课程可以扫描下面的二维码,里面有详细内容及海量课程。
Layout设计原理和方法
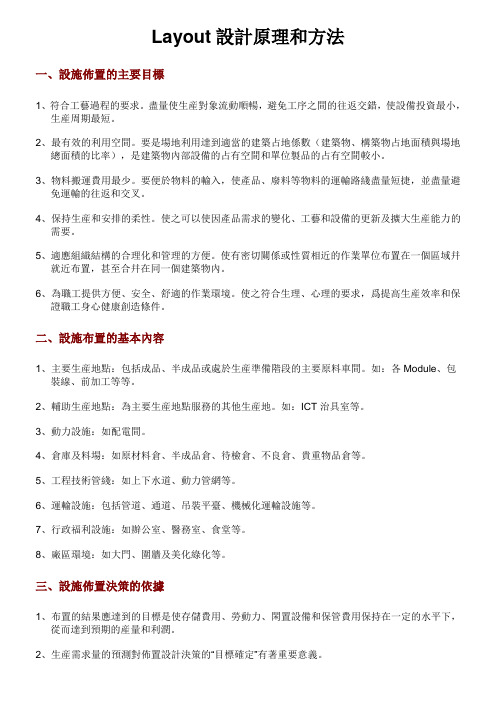
Layout設計原理和方法一、設施佈置的主要目標1、符合工藝過程的要求。
盡量使生産對象流動順暢,避免工序之間的往返交錯,使設備投資最小,生産周期最短。
2、最有效的利用空間。
要是場地利用達到適當的建築占地係數(建築物、構築物占地面積與場地總面積的比率),是建築物內部設備的占有空間和單位製品的占有空間較小。
3、物料搬運費用最少。
要便於物料的輸入,使產品、廢料等物料的運輸路綫盡量短捷,並盡量避免運輸的往返和交叉。
4、保持生産和安排的柔性。
使之可以使因產品需求的變化、工藝和設備的更新及擴大生産能力的需要。
5、適應組織結構的合理化和管理的方便。
使有密切關係或性質相近的作業單位布置在一個區域幷就近布置,甚至合幷在同一個建築物內。
6、為職工提供方便、安全、舒適的作業環境。
使之符合生理、心理的要求,爲提高生産效率和保證職工身心健康創造條件。
二、設施布置的基本內容1、主要生産地點:包括成品、半成品或處於生産準備階段的主要原料車間。
如:各Module、包裝線、前加工等等。
2、輔助生産地點:為主要生産地點服務的其他生産地。
如:ICT治具室等。
3、動力設施:如配電間。
4、倉庫及料場:如原材料倉、半成品倉、待檢倉、不良倉、貴重物品倉等。
5、工程技術管綫:如上下水道、動力管網等。
6、運輸設施:包括管道、通道、吊裝平臺、機械化運輸設施等。
7、行政福利設施:如辦公室、醫務室、食堂等。
8、廠區環境:如大門、圍牆及美化綠化等。
三、設施佈置決策的依據1、布置的結果應達到的目標是使存儲費用、勞動力、閑置設備和保管費用保持在一定的水平下,從而達到預期的産量和利潤。
2、生産需求量的預測對佈置設計決策的“目標確定”有著重要意義。
3、加工過程的要求是設施佈置決策重要依據。
4、第四個主要依據是要進行布置的建築物或場所的有效空間總數。
四、機器設備布置原則1、按照人機關係布置原則1.1根據機器與人之間的信息交換頻率布置機器。
將使用頻率高的機器布置在離操作者近的地方。
layout设计原则

layout设计原则在设计一个网页或者应用程序的布局时,布局设计原则是非常重要的。
良好的布局设计可以提高用户的使用体验,使用户更容易理解和操作页面的内容。
下面将介绍一些常用的布局设计原则。
1. 一致性:在设计布局时,应保持一致性。
这意味着相似功能的元素应具有相似的外观和位置。
例如,导航栏应该在每个页面的相同位置,并且具有相似的样式。
这样可以帮助用户快速熟悉页面结构,并提高用户的效率和满意度。
2. 对齐:对齐是布局设计中非常重要的一项原则。
元素之间的对齐可以使页面看起来更整洁和有序。
常用的对齐方式有左对齐、右对齐、居中对齐等。
在设计布局时,应该选择一种对齐方式,并在整个页面中保持一致。
3. 留白:留白是布局设计中常用的一种技巧。
合理的使用留白可以增加页面的可读性和美感。
留白可以将不同的元素分隔开,使页面内容更易于理解和阅读。
但是,留白也应该适度使用,过多的留白会使页面显得空洞和无聊。
4. 分组:将相关的元素分组放置在一起,可以帮助用户快速找到需要的信息。
分组可以通过使用边框、背景色或者间距来实现。
例如,一个购物网站的商品列表可以按照类别进行分组,使用户可以更方便地浏览和筛选商品。
5. 反馈:布局设计中应提供及时的反馈信息,告诉用户他们的操作是否成功。
例如,在用户提交表单后,应该显示一个成功的提示信息,让用户知道他们的操作已经成功完成。
反馈信息可以使用颜色、图标或者文本来表示。
6. 可访问性:在设计布局时,应考虑到不同用户的特殊需求,确保页面可以被尽可能多的用户访问。
例如,为视力障碍者提供文字描述的图片,为听力障碍者提供字幕等。
同时,应该遵循无障碍设计的原则,使页面内容能够被屏幕阅读器等辅助技术解析和理解。
7. 响应式设计:随着移动设备的普及,响应式设计已经成为布局设计的重要原则之一。
响应式设计可以使页面在不同的设备上都能够良好地显示和使用。
通过使用媒体查询和弹性布局,可以使页面根据设备的大小和分辨率进行自适应调整。
layout设计规则
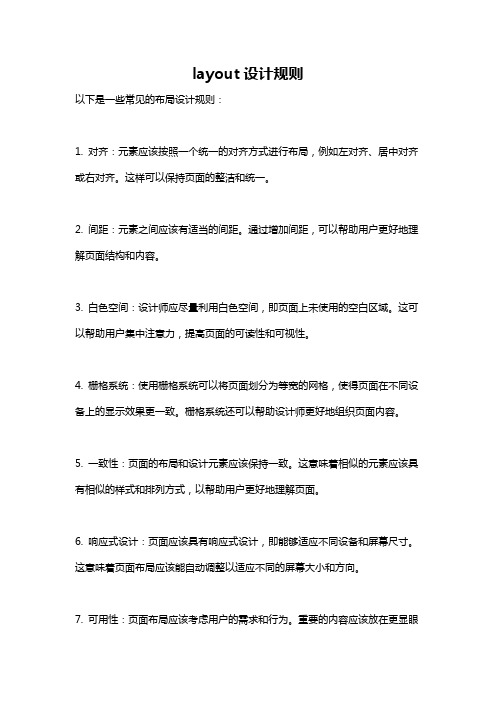
layout设计规则以下是一些常见的布局设计规则:1. 对齐:元素应该按照一个统一的对齐方式进行布局,例如左对齐、居中对齐或右对齐。
这样可以保持页面的整洁和统一。
2. 间距:元素之间应该有适当的间距。
通过增加间距,可以帮助用户更好地理解页面结构和内容。
3. 白色空间:设计师应尽量利用白色空间,即页面上未使用的空白区域。
这可以帮助用户集中注意力,提高页面的可读性和可视性。
4. 栅格系统:使用栅格系统可以将页面划分为等宽的网格,使得页面在不同设备上的显示效果更一致。
栅格系统还可以帮助设计师更好地组织页面内容。
5. 一致性:页面的布局和设计元素应该保持一致。
这意味着相似的元素应该具有相似的样式和排列方式,以帮助用户更好地理解页面。
6. 响应式设计:页面应该具有响应式设计,即能够适应不同设备和屏幕尺寸。
这意味着页面布局应该能自动调整以适应不同的屏幕大小和方向。
7. 可用性:页面布局应该考虑用户的需求和行为。
重要的内容应该放在更显眼的位置,页面导航应该清晰易用。
8. 可访问性:页面布局应该考虑到不同用户的能力和需求。
例如,应该使用明确的标签和易于理解的语言,以帮助视觉障碍用户和屏幕阅读器用户更好地理解页面内容。
9. 流程和方向:页面布局应该遵循自然的浏览习惯,使得用户可以顺利浏览页面。
重要的内容应该放在页面的上方,用户的视线自然会从上向下浏览。
10. 导航:页面应该具有清晰的导航结构,使得用户能够快速找到所需的信息。
导航菜单应该易于理解和使用,并且与页面布局相协调。
以上是一些常见的布局设计规则,根据具体情况和设计需求,还可以根据实际情况进行调整和修改。
- 1、下载文档前请自行甄别文档内容的完整性,平台不提供额外的编辑、内容补充、找答案等附加服务。
- 2、"仅部分预览"的文档,不可在线预览部分如存在完整性等问题,可反馈申请退款(可完整预览的文档不适用该条件!)。
- 3、如文档侵犯您的权益,请联系客服反馈,我们会尽快为您处理(人工客服工作时间:9:00-18:30)。
Layout设计与改善的六大原则
1)统一原则
在布局设计与改善时,必须将各工序的人、机、料、法4要素有机结合起来并保持充分的平衡。
因为,四要素一旦没有统一协调好,作业容易割裂,会延长停滞时间,增加物料搬运的次数。
2)最短距离原则
在布局设计与改善时,必须要遵循移动距离、移动时间最小化。
因为移动距离越短,物料搬运所花费的费用和时间就越小。
3)人流、物流畅通原则
在进行Layout设计与改善时,必须使工序没有堵塞,物流畅通无阻。
在Layout设计时应注意:尽量避免倒流和交叉现象,否则会导致一系列意想不到的后果,如品质问题、管理难度问题、生产效率问题、安全问题等。
4)充分利用立体空间原则
随着地价的不断攀升,企业厂房投资成本也水涨船高,因此,如何充分利用立体空间就变得尤其重要,它直接影响到产品直接成本的高低。
5)安全满意原则
在进行Layout设计与改善时,必须确保作业人员的作业既安全又轻松,因为只有这样才能减轻作业疲劳度。
请切记:材料的移动、旋转动作等可能会产生安全事故,抬升、卸下货物动作等也可能会产生安全事故。
6)灵活机动原则
在进行Layout设计与改善时,应尽可能做到适应变化、随机应变,如面对工序的增减、产能的增减能灵活对应。
为了能达成灵活机动原则,在设计时需要将水、电、气与作业台分离、不要连成一体,设备尽量不要落地生根而采用方便移动的装置。