渗碳齿轮的接触疲劳与渗碳层深度
重载齿轮渗碳质量检验标准
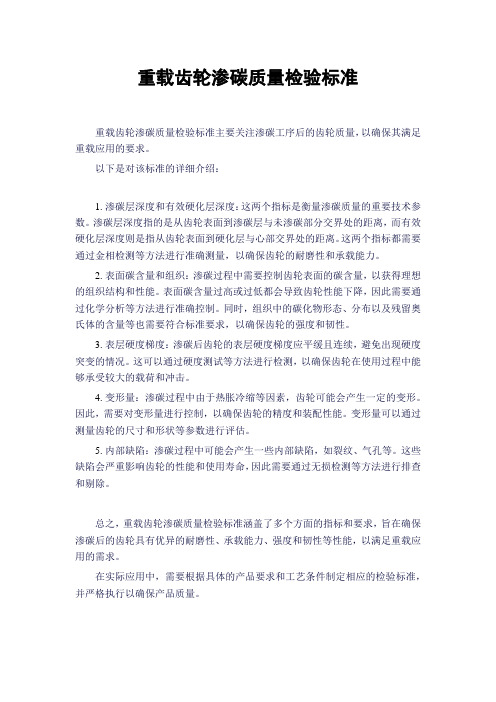
重载齿轮渗碳质量检验标准重载齿轮渗碳质量检验标准主要关注渗碳工序后的齿轮质量,以确保其满足重载应用的要求。
以下是对该标准的详细介绍:1.渗碳层深度和有效硬化层深度:这两个指标是衡量渗碳质量的重要技术参数。
渗碳层深度指的是从齿轮表面到渗碳层与未渗碳部分交界处的距离,而有效硬化层深度则是指从齿轮表面到硬化层与心部交界处的距离。
这两个指标都需要通过金相检测等方法进行准确测量,以确保齿轮的耐磨性和承载能力。
2.表面碳含量和组织:渗碳过程中需要控制齿轮表面的碳含量,以获得理想的组织结构和性能。
表面碳含量过高或过低都会导致齿轮性能下降,因此需要通过化学分析等方法进行准确控制。
同时,组织中的碳化物形态、分布以及残留奥氏体的含量等也需要符合标准要求,以确保齿轮的强度和韧性。
3.表层硬度梯度:渗碳后齿轮的表层硬度梯度应平缓且连续,避免出现硬度突变的情况。
这可以通过硬度测试等方法进行检测,以确保齿轮在使用过程中能够承受较大的载荷和冲击。
4.变形量:渗碳过程中由于热胀冷缩等因素,齿轮可能会产生一定的变形。
因此,需要对变形量进行控制,以确保齿轮的精度和装配性能。
变形量可以通过测量齿轮的尺寸和形状等参数进行评估。
5.内部缺陷:渗碳过程中可能会产生一些内部缺陷,如裂纹、气孔等。
这些缺陷会严重影响齿轮的性能和使用寿命,因此需要通过无损检测等方法进行排查和剔除。
总之,重载齿轮渗碳质量检验标准涵盖了多个方面的指标和要求,旨在确保渗碳后的齿轮具有优异的耐磨性、承载能力、强度和韧性等性能,以满足重载应用的需求。
在实际应用中,需要根据具体的产品要求和工艺条件制定相应的检验标准,并严格执行以确保产品质量。
齿轮渗碳厚度范围
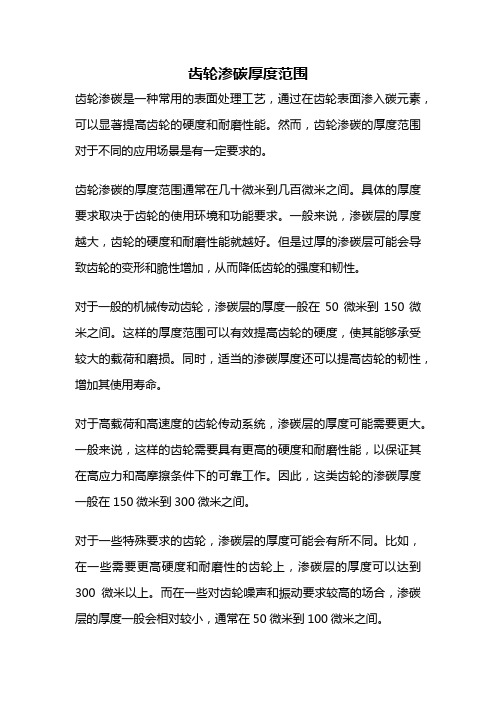
齿轮渗碳厚度范围
齿轮渗碳是一种常用的表面处理工艺,通过在齿轮表面渗入碳元素,可以显著提高齿轮的硬度和耐磨性能。
然而,齿轮渗碳的厚度范围对于不同的应用场景是有一定要求的。
齿轮渗碳的厚度范围通常在几十微米到几百微米之间。
具体的厚度要求取决于齿轮的使用环境和功能要求。
一般来说,渗碳层的厚度越大,齿轮的硬度和耐磨性能就越好。
但是过厚的渗碳层可能会导致齿轮的变形和脆性增加,从而降低齿轮的强度和韧性。
对于一般的机械传动齿轮,渗碳层的厚度一般在50微米到150微米之间。
这样的厚度范围可以有效提高齿轮的硬度,使其能够承受较大的载荷和磨损。
同时,适当的渗碳厚度还可以提高齿轮的韧性,增加其使用寿命。
对于高载荷和高速度的齿轮传动系统,渗碳层的厚度可能需要更大。
一般来说,这样的齿轮需要具有更高的硬度和耐磨性能,以保证其在高应力和高摩擦条件下的可靠工作。
因此,这类齿轮的渗碳厚度一般在150微米到300微米之间。
对于一些特殊要求的齿轮,渗碳层的厚度可能会有所不同。
比如,在一些需要更高硬度和耐磨性的齿轮上,渗碳层的厚度可以达到300微米以上。
而在一些对齿轮噪声和振动要求较高的场合,渗碳层的厚度一般会相对较小,通常在50微米到100微米之间。
齿轮渗碳的厚度范围是根据齿轮的使用环境和功能要求来确定的。
在实际应用中,需要根据具体情况选择合适的渗碳厚度,以保证齿轮的性能和可靠性。
同时,在进行齿轮渗碳处理时,还需要注意控制渗碳的工艺参数,以确保渗碳层的均匀性和一致性,从而提高齿轮的质量和使用寿命。
齿轮淬火深度

图片:齿轮淬火的“最佳”硬化层深与“适当”硬化层深戴忠森众所周知,齿轮的淬硬层深“过浅”,对接触和弯曲承载能力都不利。
但淬硬层也不是越深越好,最佳或适当的硬化层深度,可使齿面和齿根都具有较高的强度(承载能力)。
另外,不同的热处理方法,其“最佳”值也不是一样的。
二十世纪七、八十年代,随着齿轮强度计算方法ISO标准的公布,以及国内GB/3480“圆柱齿轮承载能力计算方法”标准的实施,特别是工业硬齿面齿轮的广泛采用,国内外齿轮工作者(专家、学者),就热处理硬化层深问题,进行了大量的试验研究和理论分析。
其实质都是基于接触(弯曲)疲劳强度,其核心问题是:疲劳裂纹发生(萌生)在何处?破坏后的形状是点蚀(pitting贝壳状),还是片蚀(剥落spalling)?研究表明,一般软齿面大多是点蚀,而硬齿面大齿轮大多是剥落(片蚀)。
疲劳裂纹的萌生,有可能在表面,也有可能在表层。
至今,有关硬齿面齿轮接触疲劳强度(剥落)计算的理论和方法,主要有:最大剪切应力τmax (τ45°);正交剪切应力(τyz);当量剪切应力(τeffa);深部接触应力;最大剪切应力/剪切强度的峰值;正交剪切应力/强度(硬度)(τyz/HV)max;当量剪切应力/强度的峰值等,通过理论计算可以确定接触疲劳强度(安全系数);或者确定最佳淬硬层深度。
这些理论和方法一直都有争议,因此至今也没有一个权威的理论和方法被大家所能完全接受。
所谓“最佳硬化层深”,其说法也是较含糊的,而且众说不一,以渗碳淬火齿轮为例,德国DIN3990,硬化(渗碳)层深度,给出一个经验公式:(推荐)Eht= 0.15mn(mn——法面模数)(1)。
该经验公式,有一个突出的问题,就是未考虑实际载荷的情况。
所以,对于轻载齿轮,允许比经验公式稍浅的硬化层深度。
Thomas Tobie近年来提出在用ISO/DIN 进行标准化承载能力计算时,考虑硬化层深度对承载能力的影响,引入了影响系数ZEht(接触承载能力影响系数);УEht(弯曲承载能力影响系数)。
渗碳齿轮热处理常见缺陷及预防措施

保持热处理过程中温度和冷却速度的稳定性、加强齿轮结构 设计等。
02
预防措施
选用高质量渗碳剂
确保渗碳剂质量
选用由正规厂家生产、质量稳定的渗 碳剂,避免因渗碳剂质量问题导致热 处理缺陷。
查验成分含量
避免混用不同牌号渗碳剂
不同牌号的渗碳剂成分和性能有所差 异,避免混用以免影响热处理效果。
对渗碳剂的成分含量进行严格检验, 确保其符合工艺要求。
渗碳剂的选用和调整
选用
根据齿轮的材质和热处理需求,选择合适的渗碳剂。
调整
根据实际操作情况,对渗碳剂的成分和比例进行适当调整,以确保齿轮能够获得理想的 渗碳效果。
渗碳过程的控制
温度控制
保持渗碳炉内的温度稳定 ,以避免齿轮在渗碳过程 中出现不均匀的温度分布 。
时间控制
渗碳过程应控制在适当的 温度和时间下进行,以确 保齿轮能够充分吸收碳元 素。
淬火过程的控制
温度控制
保持淬火炉内的温度稳定,以避 免齿轮在淬火过程中出现不均匀 的温度分布。
时间控制
淬火过程应控制在适当的温度和 时间下进行,以确保齿轮能够获 得理想的硬度和耐磨性。
冷却控制
淬火后的冷却过程也需严格控制 ,以避免齿轮出现裂纹或其他淬 火缺陷。
04
渗碳齿轮热处理质量检测方法
渗碳层深度检测
预防措施
提高渗碳温度、延长渗碳时间、优化 炉内气氛等。
渗碳层碳浓度不均匀
原因
渗碳层碳浓度不均匀可能是由于渗碳过程中温度波动大、炉内气氛不稳定、渗碳剂分布不均匀等原因引起的。
预防措施
保持渗碳过程中温度稳定、优化炉内气氛、均匀分布渗碳剂等。
齿轮表面粗糙
原因
齿轮表面粗糙可能是由于渗碳后表面残渣未清理干净、热处理过程中氧化脱碳严重等原因引起的。
小模数齿轮渗碳层深度设计
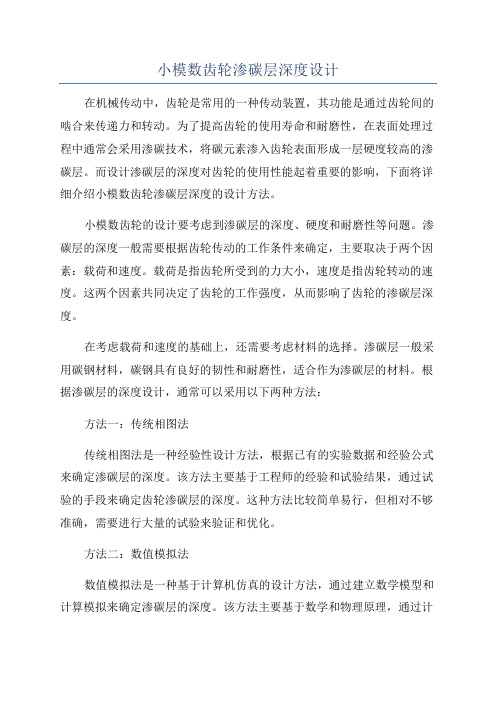
小模数齿轮渗碳层深度设计在机械传动中,齿轮是常用的一种传动装置,其功能是通过齿轮间的啮合来传递力和转动。
为了提高齿轮的使用寿命和耐磨性,在表面处理过程中通常会采用渗碳技术,将碳元素渗入齿轮表面形成一层硬度较高的渗碳层。
而设计渗碳层的深度对齿轮的使用性能起着重要的影响,下面将详细介绍小模数齿轮渗碳层深度的设计方法。
小模数齿轮的设计要考虑到渗碳层的深度、硬度和耐磨性等问题。
渗碳层的深度一般需要根据齿轮传动的工作条件来确定,主要取决于两个因素:载荷和速度。
载荷是指齿轮所受到的力大小,速度是指齿轮转动的速度。
这两个因素共同决定了齿轮的工作强度,从而影响了齿轮的渗碳层深度。
在考虑载荷和速度的基础上,还需要考虑材料的选择。
渗碳层一般采用碳钢材料,碳钢具有良好的韧性和耐磨性,适合作为渗碳层的材料。
根据渗碳层的深度设计,通常可以采用以下两种方法:方法一:传统相图法传统相图法是一种经验性设计方法,根据已有的实验数据和经验公式来确定渗碳层的深度。
该方法主要基于工程师的经验和试验结果,通过试验的手段来确定齿轮渗碳层的深度。
这种方法比较简单易行,但相对不够准确,需要进行大量的试验来验证和优化。
方法二:数值模拟法数值模拟法是一种基于计算机仿真的设计方法,通过建立数学模型和计算模拟来确定渗碳层的深度。
该方法主要基于数学和物理原理,通过计算机编程来模拟和计算齿轮渗碳层的深度。
这种方法比较准确和可靠,可以有效地减少试验的数量和时间成本。
在小模数齿轮渗碳层深度的设计过程中,可以根据具体情况选择合适的设计方法。
传统相图法适用于比较简单和常见的齿轮设计,而数值模拟法适用于复杂和特殊的齿轮设计。
根据渗碳层深度的设计结果,可以进行试验验证和优化,以确保齿轮设计的准确性和可靠性。
综上所述,小模数齿轮渗碳层深度的设计需要考虑载荷、速度和材料等因素,可以采用传统相图法和数值模拟法来确定。
在设计过程中应注意选择合适的设计方法,并进行试验验证和优化,以确保设计结果的准确性和可靠性。
磨齿酸洗质量标准
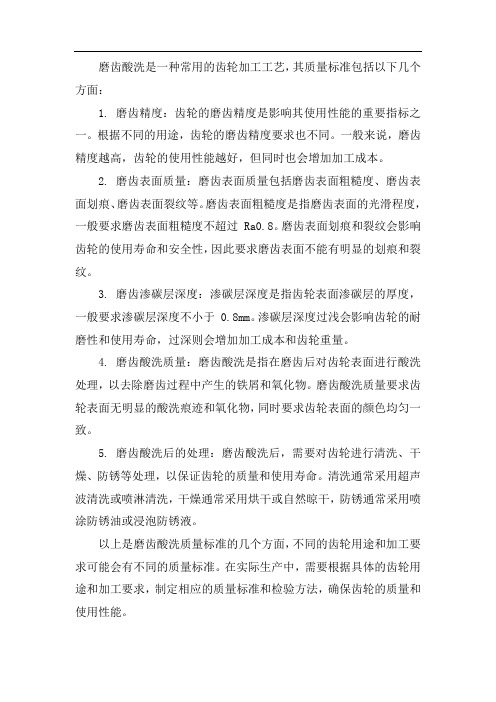
磨齿酸洗是一种常用的齿轮加工工艺,其质量标准包括以下几个方面:
1. 磨齿精度:齿轮的磨齿精度是影响其使用性能的重要指标之一。
根据不同的用途,齿轮的磨齿精度要求也不同。
一般来说,磨齿精度越高,齿轮的使用性能越好,但同时也会增加加工成本。
2. 磨齿表面质量:磨齿表面质量包括磨齿表面粗糙度、磨齿表面划痕、磨齿表面裂纹等。
磨齿表面粗糙度是指磨齿表面的光滑程度,一般要求磨齿表面粗糙度不超过 Ra0.8。
磨齿表面划痕和裂纹会影响齿轮的使用寿命和安全性,因此要求磨齿表面不能有明显的划痕和裂纹。
3. 磨齿渗碳层深度:渗碳层深度是指齿轮表面渗碳层的厚度,一般要求渗碳层深度不小于 0.8mm。
渗碳层深度过浅会影响齿轮的耐磨性和使用寿命,过深则会增加加工成本和齿轮重量。
4. 磨齿酸洗质量:磨齿酸洗是指在磨齿后对齿轮表面进行酸洗处理,以去除磨齿过程中产生的铁屑和氧化物。
磨齿酸洗质量要求齿轮表面无明显的酸洗痕迹和氧化物,同时要求齿轮表面的颜色均匀一致。
5. 磨齿酸洗后的处理:磨齿酸洗后,需要对齿轮进行清洗、干燥、防锈等处理,以保证齿轮的质量和使用寿命。
清洗通常采用超声波清洗或喷淋清洗,干燥通常采用烘干或自然晾干,防锈通常采用喷涂防锈油或浸泡防锈液。
以上是磨齿酸洗质量标准的几个方面,不同的齿轮用途和加工要求可能会有不同的质量标准。
在实际生产中,需要根据具体的齿轮用途和加工要求,制定相应的质量标准和检验方法,确保齿轮的质量和使用性能。
Nb微合金化对渗碳齿轮钢组织演变及接触疲劳性能的影响

表面技术第51卷 第1期 ·358· SURFACE TECHNOLOGY 2022年1月收稿日期:2021-02-27;修订日期:2021-08-09 Received :2021-02-27;Revised :2021-08-09 基金项目:工信部工业强基项目(TC180A3Y1)Fund :Supported by Industrial Strong Foundation Engineering (TC180A3Y1) 作者简介:杨少朋(1989—),男,博士研究生,主要研究方向为特殊钢。
Biography :YANG Shao-peng (1989—), Male, Doctoral candidate, Research focus: special steel. 通讯作者:王毛球(1970—),男,博士研究生,教授级高级工程师,主要研究方向为合金结构钢。
Corresponding author :WANG Mao-qiu (1970—), Male, Doctoral candidate, Professor-level senior engineer, Research focus: alloy structural steel. 引文格式:杨少朋, 胡芳忠, 尉文超, 等. Nb 微合金化对渗碳齿轮钢组织演变及接触疲劳性能的影响[J]. 表面技术, 2022, 51(1): 358-367. YANG Shao-peng, HU Fang-zhong, YU Wen-chao, et al.Effect of Niobium Microalloying on Microstructure Evolution and Rolling Contact Nb 微合金化对渗碳齿轮钢组织演变及接触疲劳性能的影响杨少朋1,2,胡芳忠2,尉文超1,汪开忠2,吕皓天3,4,王毛球1,张弛3,4(1.钢铁研究总院特殊钢研究所,北京 100081;2.马鞍山钢铁股份有限公司 技术中心,安徽 243000;3.教育部先进材料重点实验室,北京 100084;4.清华大学 材料学院,北京 100084) 摘 要:目的 研究Nb 微合金化后渗碳层和基体的显微组织变化规律,及Nb 微合金化对接触疲劳性能的影响,以实现齿轮的接触疲劳长寿命。
关于渗碳层深度的几个问题

关于渗碳层深度的几个问题
·39 ·
关于渗碳层深度的几个问题
青海齿轮厂 (810021) 陈春怀
根据尺寸链的计算公式
m
n- 1
L 0 ,max = 6 L i ,max - 6 L j ,min
i=1
j=m+1
m
n- 1
L 0 ,min = 6 L i ,min - 6 L j ,max
i=1
j=m+1
图 3 所形成的尺寸链示意图
式中 : L 0 ,max ; L 0 ,min ———封闭环最大及最小极 限尺寸 ; L i ,max ; L i ,min ———增环最大及 最 小 极 限 尺寸 ; L i ,max ; L i ,min ———减环最大及 最 小 极 限 尺寸 。 因而可列出 L 0 ,max = L 2 ,max + L 3 ,max - L 1 ,min 。
即 1. 25 + 0. 15
=
L 2 ,max +
1 2
( 119. 5 + 0. 10
-
120)
,因为是半径尺寸
,故乘以
1 2
。
L 2 ,max = 1. 60
同样地
L 0 ,min = L 2 ,min + L 3 ,min - L 1 ,max
1 . 25 - 0. 15 =
L 2 ,min +
2 如何由试棒渗层深度推知试块渗层深度