齿轮表面渗碳及渗碳深度
重载齿轮渗碳质量检验标准
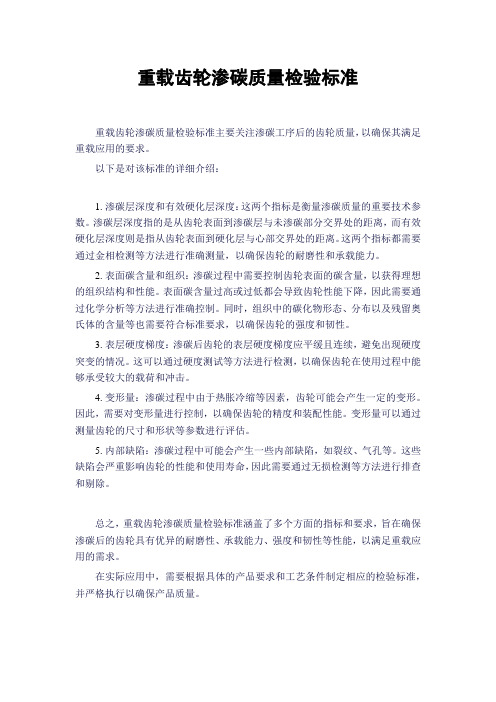
重载齿轮渗碳质量检验标准重载齿轮渗碳质量检验标准主要关注渗碳工序后的齿轮质量,以确保其满足重载应用的要求。
以下是对该标准的详细介绍:1.渗碳层深度和有效硬化层深度:这两个指标是衡量渗碳质量的重要技术参数。
渗碳层深度指的是从齿轮表面到渗碳层与未渗碳部分交界处的距离,而有效硬化层深度则是指从齿轮表面到硬化层与心部交界处的距离。
这两个指标都需要通过金相检测等方法进行准确测量,以确保齿轮的耐磨性和承载能力。
2.表面碳含量和组织:渗碳过程中需要控制齿轮表面的碳含量,以获得理想的组织结构和性能。
表面碳含量过高或过低都会导致齿轮性能下降,因此需要通过化学分析等方法进行准确控制。
同时,组织中的碳化物形态、分布以及残留奥氏体的含量等也需要符合标准要求,以确保齿轮的强度和韧性。
3.表层硬度梯度:渗碳后齿轮的表层硬度梯度应平缓且连续,避免出现硬度突变的情况。
这可以通过硬度测试等方法进行检测,以确保齿轮在使用过程中能够承受较大的载荷和冲击。
4.变形量:渗碳过程中由于热胀冷缩等因素,齿轮可能会产生一定的变形。
因此,需要对变形量进行控制,以确保齿轮的精度和装配性能。
变形量可以通过测量齿轮的尺寸和形状等参数进行评估。
5.内部缺陷:渗碳过程中可能会产生一些内部缺陷,如裂纹、气孔等。
这些缺陷会严重影响齿轮的性能和使用寿命,因此需要通过无损检测等方法进行排查和剔除。
总之,重载齿轮渗碳质量检验标准涵盖了多个方面的指标和要求,旨在确保渗碳后的齿轮具有优异的耐磨性、承载能力、强度和韧性等性能,以满足重载应用的需求。
在实际应用中,需要根据具体的产品要求和工艺条件制定相应的检验标准,并严格执行以确保产品质量。
20CrMnTi渗碳钢和40Cr对比

20CrMnTi 与40Cr力学性能对比分析报告一:20CrMnTi是一种渗碳钢,齿轮钢,合金结构钢。
渗碳齿轮钢通常为含碳量为0.17%-0.24%的低碳钢,多用于轴类零件并进行渗碳或进行调质但不能进行渗氮(注意渗氮常用于中合金钢,中碳含Cr钢,淬层深一般为0.1-0.3,表面硬度700-900HV),渗碳淬火后具有良好的耐磨性和抗弯强度,有较高的低温冲击韧度。
汽车上多用其制造传动齿轮,是中淬透性渗碳钢中Cr Mn Ti 钢系列。
其淬透性较高,在保证淬透情况下,具有较高的强度和韧性,常用于要求强度和韧性均较高的轴(如齿轮轴,蜗杆等)特别是具有较高的低温冲击韧性,但是在高温和腐蚀条件下工作的轴应选用耐热钢和不锈钢1Cr18Ni9Ti,在结构形状复杂的轴常选用球墨铸铁。
20CrMnTi表面渗碳硬化处理用钢,它具有良好的加工切削性,加工变形微小,抗疲劳性能相当好。
主要用途有:常用于齿轮,轴类,汽车三叉万向节,活塞类零配件以及汽车,飞机等各种特殊零件部位。
20CrMnTi 淬火+低温回火后,综合力学性能和低温冲击韧度良好,渗碳后具有良好的耐磨和抗弯强度,热处理工艺简单,热加工和冷加工性较好,但高温回火时有回火脆性倾向。
20CrMnTi工艺路线为:下料,锻造,正火,粗加工,(渗碳,淬火+低温回火,)或调质,精加工或磨削。
(锻造件优于同等条件下的铸件)一般渗碳层深度为0.8-1.2毫米,深度渗碳可达2毫米或更深,渗碳后表面硬度可达HRC58-63,心部硬度可达HRC30-42,渗碳可提高零件强度,耐磨性和冲击韧性,以延长零件寿命。
渗碳层深度范围工艺参数:1.热处理后不需磨制零件:0.7-1.1;1.0-1.4;1.2-1.6mm2.热处理后需磨制零件:0.6-1.0;0.8-1.2;1.0-1.4轴表面淬火处理后的淬硬层深度与性能要求,工作条件及淬硬层深度之间的关系:1.用于耐磨,载荷型不大条件下,淬硬层深度0.5-1.5;2.用于耐磨载荷较大或有冲击载荷下,淬硬层深度2.0-6.53.用于抗疲劳,周期性弯曲或扭转下,淬硬层深度3.0-12.2. 20CrMnTi特性及适用范围:是性能良好的渗碳钢,淬透性较高,经渗碳+淬火+低温回火后具有硬而耐磨的表面与坚韧的心部,具有较高的低温冲击韧性,焊接性中等,正火后可切削性良好。
齿轮渗碳淬火变形原因及控制措施研究

齿轮渗碳淬火变形原因及控制措施研究摘要:齿轮零件在前期加工期间若是遭受到热处理变形作用,将会导致其获取的精度遭受到严重的影响,一旦出现变形即使是使用校直及磨齿等先进的修形技术也难以达到恢复的效果。
尤其是齿轮在遭受到渗碳淬火之后会出现变形情况,具有较大的变形量,该种变形无法通过控制来实现,并且变形过大,也会增加磨削成本及磨削量,对齿轮制造精度会造成极大的影响,承载能力显著降低,寿命也会随之而下降。
本文着重分析齿轮渗碳淬火变形原因,并提出合理化的变形控制措施。
关键词:齿轮渗碳淬火;变形原因;控制措施前言:在制造硬齿面汽车齿轮期间,目前所使用的主流工艺是渗碳淬火,但是在使用之后不得不面对的问题便是出现变形情况,会对齿轮的加工质量造成极大的影响。
有相关的研究报告显示,之所以会导致碳淬火齿轮出现变形,与锻造质量、原材料质量、齿轮的结构设计、毛坯预备热处理有直接关系,并且以上几种因素之间彼此也会出现相互影响的情况,进而增加了上述因素的控制难度。
现如今,在汽车齿轮制造中控制变形量已经成为一项需要解决的重难点问题。
一、齿轮渗碳淬火变形原因(一)渗碳件变形原因渗碳低碳钢,经过对原始相结构进行分析可知,由少量珠光体组织及铁素体共同来构成,经过对整个体积的占比情况进行了解可知,铁素体量的占比高达80%,当加温到AC1以上温度之后,珠光体会向奥氏体进行转变。
当温度为900℃时,铁素体会向奥氏体进行转变。
当渗碳的温度为920℃-940℃时,零件表面的奥氏体区碳浓度的升高度为0.6%-1.2%,碳浓度比较高的奥氏体区碳浓度会增加至0.6%-1.2%,当奥氏体的温度冷却到600-650℃时,会向索氏体及珠光体进行转变[1]。
当低碳奥氏体处于心部区时,若是在900℃的高温下会将其转变为铁素体,当冷却到550℃时,会全部转变完成。
比容增大的过程是心部奥氏体向铁素体进行转变的过程,而通过对表层奥氏体冷却情况进行探究可知,可将热缩量增加变化的整个过程呈现出来,在冷却期间,在生成心部铁素体时,会遭受到表层高碳奥氏体区的压力影响[2]。
齿轮渗碳厚度范围
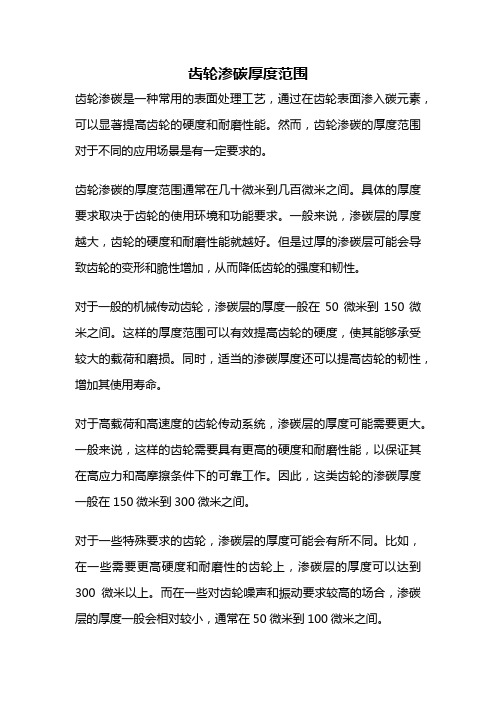
齿轮渗碳厚度范围
齿轮渗碳是一种常用的表面处理工艺,通过在齿轮表面渗入碳元素,可以显著提高齿轮的硬度和耐磨性能。
然而,齿轮渗碳的厚度范围对于不同的应用场景是有一定要求的。
齿轮渗碳的厚度范围通常在几十微米到几百微米之间。
具体的厚度要求取决于齿轮的使用环境和功能要求。
一般来说,渗碳层的厚度越大,齿轮的硬度和耐磨性能就越好。
但是过厚的渗碳层可能会导致齿轮的变形和脆性增加,从而降低齿轮的强度和韧性。
对于一般的机械传动齿轮,渗碳层的厚度一般在50微米到150微米之间。
这样的厚度范围可以有效提高齿轮的硬度,使其能够承受较大的载荷和磨损。
同时,适当的渗碳厚度还可以提高齿轮的韧性,增加其使用寿命。
对于高载荷和高速度的齿轮传动系统,渗碳层的厚度可能需要更大。
一般来说,这样的齿轮需要具有更高的硬度和耐磨性能,以保证其在高应力和高摩擦条件下的可靠工作。
因此,这类齿轮的渗碳厚度一般在150微米到300微米之间。
对于一些特殊要求的齿轮,渗碳层的厚度可能会有所不同。
比如,在一些需要更高硬度和耐磨性的齿轮上,渗碳层的厚度可以达到300微米以上。
而在一些对齿轮噪声和振动要求较高的场合,渗碳层的厚度一般会相对较小,通常在50微米到100微米之间。
齿轮渗碳的厚度范围是根据齿轮的使用环境和功能要求来确定的。
在实际应用中,需要根据具体情况选择合适的渗碳厚度,以保证齿轮的性能和可靠性。
同时,在进行齿轮渗碳处理时,还需要注意控制渗碳的工艺参数,以确保渗碳层的均匀性和一致性,从而提高齿轮的质量和使用寿命。
渗碳齿轮制造流程

一、零件分析齿轮类零件按功能可分为运动传输齿轮和动力传动齿轮,其中动力传动齿轮常采用渗碳硬化以获得高硬度、高耐磨性的表层,而芯部仍保留塑性和良好的韧性使零件能够承受一定的冲击载荷。
与渗氮相比,渗碳硬化的优点是渗层深度范围更大、允许预留较大尺寸公差以精加工齿形,现已被广泛应用于我厂传动系统的齿轮、轴销等零件。
我厂承制的某输出齿轮属于典型的外齿+内花键短轴型零件(见图1),材料牌号S82(低碳合金结构钢),渐开线外齿径节18,齿数39,压力角25°,精度等级为AGMA8级(相当于GB10095规定的7级)。
内渐开线花键齿数16,径节20/40,压力角30°,ANSI标准圆角根侧配合,7级精度。
图1 零件结构示意该零件要求齿轮齿顶、齿面、齿根及齿侧渗碳硬化至700HV以上(HRC≥62),其余表面不渗碳。
首次设计工艺方案时考虑到非渗碳表面及芯部在淬回火后硬度达到HRC42~47,而我厂加工花键的粉末冶金刀具所能应对的零件极限硬度不超过HRC42。
所以编制工艺规程时延用了传统的“镀铜-渗碳-除铜”方案——精加工齿坯后插内花键,镀铜后车去齿顶与齿侧的铜层,滚齿时预留磨齿余量,并在热处理过程中用铜层保护非渗碳面与活性碳元素隔离,流程如下图所示:图首批试制工艺方案首批产品加工完成后,在汇总检验工序计量内花键齿跳时发现合格率低于30%。
复查热处理前插齿工序的计量报告结果均合格。
分析导致超差的原因有:a)热处理后经过研中心孔、外磨两道工序,测量基准变动。
b)机械加工及热处理过程中产生的各种内应力高于材料的屈服强度,应力释放导致零件发生不可逆转的塑性变形。
通常应对以上两项影响的方法有以下几种:1) 合理分配冷加工尺寸公差,适当提高内花键加工精度,用富裕的尺寸和形状精度弥补热处理畸变。
2) 采用循环保温、冰冷处理等去应力手段,尽可能消除机械加工中产生的残余应力。
3) 热处理过程中严格控制升温速度,采用较低的渗碳和淬火加热温度,减少热处理过程中产生的热应力;在不影响渗碳质量的前提下,将齿轮的表面碳浓度和渗碳层深度控制在下限范围。
齿轮加工技术要求
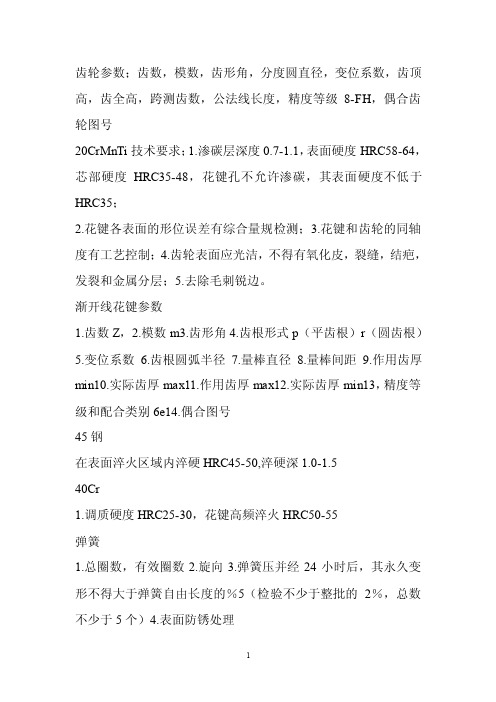
齿轮参数;齿数,模数,齿形角,分度圆直径,变位系数,齿顶高,齿全高,跨测齿数,公法线长度,精度等级8-FH,偶合齿轮图号20CrMnTi技术要求;1.渗碳层深度0.7-1.1,表面硬度HRC58-64,芯部硬度HRC35-48,花键孔不允许渗碳,其表面硬度不低于HRC35;2.花键各表面的形位误差有综合量规检测;3.花键和齿轮的同轴度有工艺控制;4.齿轮表面应光洁,不得有氧化皮,裂缝,结疤,发裂和金属分层;5.去除毛刺锐边。
渐开线花键参数1.齿数Z,2.模数m3.齿形角4.齿根形式p(平齿根)r(圆齿根)5.变位系数6.齿根圆弧半径7.量棒直径8.量棒间距9.作用齿厚min10.实际齿厚max11.作用齿厚max12.实际齿厚min13,精度等级和配合类别6e14.偶合图号45钢在表面淬火区域内淬硬HRC45-50,淬硬深1.0-1.540Cr1.调质硬度HRC25-30,花键高频淬火HRC50-55弹簧1.总圈数,有效圈数2.旋向3.弹簧压并经24小时后,其永久变形不得大于弹簧自由长度的%5(检验不少于整批的2%,总数不少于5个)4.表面防锈处理35CrMo调质处理25-30,花键高频淬火HRC45-50HT200箱体1.铸件应消除内应力,硬度HB170-2412.未注铸造圆角R3-5,铸造拔模斜度2-3度3.铸件表面应光洁,彻底清除毛刺,砂型和其他杂物4.非加工表面允许有直径不大于5,深度不大于2,总数不超过10个的孔眼,两间距不小于30,孔眼边缘至铸件边缘或加工边缘不小于105.同一加工表面上,允许有直径不大于3,深度不大于1.5,总数不超过5个的清洁孔眼存在,两间距不小于30,孔眼边缘至铸件边缘或加工边缘不小于5;6.内壁非加工表面涂耐油油漆20CrMnTi轴1.花键渗碳高频淬火HRC55-60,淬硬深度0.7-1.1,余部机械性能大于等于800牛每平方毫米。
渗碳齿轮热处理常见缺陷及预防措施

保持热处理过程中温度和冷却速度的稳定性、加强齿轮结构 设计等。
02
预防措施
选用高质量渗碳剂
确保渗碳剂质量
选用由正规厂家生产、质量稳定的渗 碳剂,避免因渗碳剂质量问题导致热 处理缺陷。
查验成分含量
避免混用不同牌号渗碳剂
不同牌号的渗碳剂成分和性能有所差 异,避免混用以免影响热处理效果。
对渗碳剂的成分含量进行严格检验, 确保其符合工艺要求。
渗碳剂的选用和调整
选用
根据齿轮的材质和热处理需求,选择合适的渗碳剂。
调整
根据实际操作情况,对渗碳剂的成分和比例进行适当调整,以确保齿轮能够获得理想的 渗碳效果。
渗碳过程的控制
温度控制
保持渗碳炉内的温度稳定 ,以避免齿轮在渗碳过程 中出现不均匀的温度分布 。
时间控制
渗碳过程应控制在适当的 温度和时间下进行,以确 保齿轮能够充分吸收碳元 素。
淬火过程的控制
温度控制
保持淬火炉内的温度稳定,以避 免齿轮在淬火过程中出现不均匀 的温度分布。
时间控制
淬火过程应控制在适当的温度和 时间下进行,以确保齿轮能够获 得理想的硬度和耐磨性。
冷却控制
淬火后的冷却过程也需严格控制 ,以避免齿轮出现裂纹或其他淬 火缺陷。
04
渗碳齿轮热处理质量检测方法
渗碳层深度检测
预防措施
提高渗碳温度、延长渗碳时间、优化 炉内气氛等。
渗碳层碳浓度不均匀
原因
渗碳层碳浓度不均匀可能是由于渗碳过程中温度波动大、炉内气氛不稳定、渗碳剂分布不均匀等原因引起的。
预防措施
保持渗碳过程中温度稳定、优化炉内气氛、均匀分布渗碳剂等。
齿轮表面粗糙
原因
齿轮表面粗糙可能是由于渗碳后表面残渣未清理干净、热处理过程中氧化脱碳严重等原因引起的。
小模数齿轮渗碳层深度设计
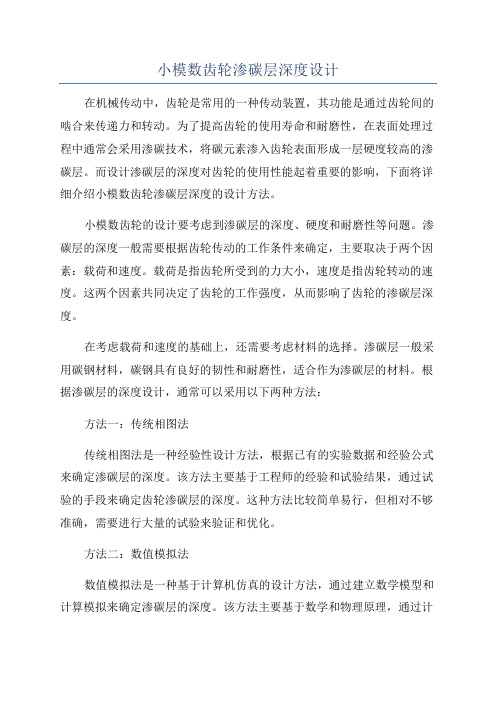
小模数齿轮渗碳层深度设计在机械传动中,齿轮是常用的一种传动装置,其功能是通过齿轮间的啮合来传递力和转动。
为了提高齿轮的使用寿命和耐磨性,在表面处理过程中通常会采用渗碳技术,将碳元素渗入齿轮表面形成一层硬度较高的渗碳层。
而设计渗碳层的深度对齿轮的使用性能起着重要的影响,下面将详细介绍小模数齿轮渗碳层深度的设计方法。
小模数齿轮的设计要考虑到渗碳层的深度、硬度和耐磨性等问题。
渗碳层的深度一般需要根据齿轮传动的工作条件来确定,主要取决于两个因素:载荷和速度。
载荷是指齿轮所受到的力大小,速度是指齿轮转动的速度。
这两个因素共同决定了齿轮的工作强度,从而影响了齿轮的渗碳层深度。
在考虑载荷和速度的基础上,还需要考虑材料的选择。
渗碳层一般采用碳钢材料,碳钢具有良好的韧性和耐磨性,适合作为渗碳层的材料。
根据渗碳层的深度设计,通常可以采用以下两种方法:方法一:传统相图法传统相图法是一种经验性设计方法,根据已有的实验数据和经验公式来确定渗碳层的深度。
该方法主要基于工程师的经验和试验结果,通过试验的手段来确定齿轮渗碳层的深度。
这种方法比较简单易行,但相对不够准确,需要进行大量的试验来验证和优化。
方法二:数值模拟法数值模拟法是一种基于计算机仿真的设计方法,通过建立数学模型和计算模拟来确定渗碳层的深度。
该方法主要基于数学和物理原理,通过计算机编程来模拟和计算齿轮渗碳层的深度。
这种方法比较准确和可靠,可以有效地减少试验的数量和时间成本。
在小模数齿轮渗碳层深度的设计过程中,可以根据具体情况选择合适的设计方法。
传统相图法适用于比较简单和常见的齿轮设计,而数值模拟法适用于复杂和特殊的齿轮设计。
根据渗碳层深度的设计结果,可以进行试验验证和优化,以确保齿轮设计的准确性和可靠性。
综上所述,小模数齿轮渗碳层深度的设计需要考虑载荷、速度和材料等因素,可以采用传统相图法和数值模拟法来确定。
在设计过程中应注意选择合适的设计方法,并进行试验验证和优化,以确保设计结果的准确性和可靠性。
- 1、下载文档前请自行甄别文档内容的完整性,平台不提供额外的编辑、内容补充、找答案等附加服务。
- 2、"仅部分预览"的文档,不可在线预览部分如存在完整性等问题,可反馈申请退款(可完整预览的文档不适用该条件!)。
- 3、如文档侵犯您的权益,请联系客服反馈,我们会尽快为您处理(人工客服工作时间:9:00-18:30)。
仪器在400倍以上的放大倍数下测量压痕。
测定应在各方约定的位置上,在制备好的试样表面上的两条或更多条硬化线上进行,并绘制出每一条线的硬度分布曲线
二.齿轮固体渗碳工艺
(一)渗碳剂的成份及其作用:
固体渗碳剂主要是由木炭粒和碳酸盐(BaCO3或Na2CO3等组成。
木炭粒是主渗剂,碳酸盐是催渗剂。
木炭颗粒均匀,并要求3—6mm左右的占80%,1—3mm左右占20%左右,1mm以下的不大于1%,如果是大零件渗碳,大颗粒木炭应多些,小零件,小颗粒应多些。
常用的渗碳剂成份如表1所示。
常用渗碳剂的成份
渗碳加热时,炭与其间隙中的氧作用(不完全燃烧),生成一氧化碳。
2C+O2—→2CO 一氧化碳在渗碳条件下,是不稳定的。
活性碳原子被钢件表面吸收,并向内部扩散。
整个反反应过程可用下式示意表示:C+CO2—→2CO—→CO2+[C]单独用木炭进行渗碳,周期长,效果差,为了增加渗碳剂的活性,增加活性碳原子数量,一般加入一定数量的碳酸盐作为催渗剂。
催渗剂在高温下与木碳产生如下反应:BaCO3+C—→BaO2+CO Na2CO3 + C(木炭) —→ Na2O + 2CO 2CO —→ CO2 + [C]渗碳过程中,木炭受到了烧损,但催渗剂分解氧化物,在开箱冷却时与空气接触,如按下方程式进行还原,这使催渗剂消耗大为减少。
BaO+CO2—→BaCO3,Na2O+CO2—→Na2CO3 为了提高催渗剂再生效果,在此介绍一种有效的方法,即将高温下倒出来的渗碳剂,立刻用水喷洒(水的重量是渗碳剂重量的4—5%)。
通过这样的处理,碳酸盐可得较完全的再生,其原因是:BaO+CO2—→BaCO3这个过程随温度下降而缓慢,如果在高温下喷水,就能使BaO变成氢氧化钡,而氢氧化钡向碳酸钡转变
不受温度的限制。
其反应如下:BaO+H2O—→Ba(OH)2 Ba(OH)2+CO2—→BaCO3+H2O 喷水还可以减少木炭的烧损和促进少量甲烷发生,甲烷吸附在木炭的孔隙中,也能加速渗碳。
经过喷水处理的渗碳剂,加少量新渗碳剂便可使用。
(二)固体渗碳的操作方法:1配制渗碳剂:由于全新的渗碳剂催渗作用过于强烈,易导致零件渗碳后表层浓度过高和出现粗大或网状碳化物。
因此,一般新旧混合使用,其中新渗碳剂占20—40%,旧渗碳剂占60—80%。
回收的旧渗碳剂应筛去灰粉后,才能与新渗碳剂配合使用。
⒉渗碳零件,渗碳前的准备处理:要渗碳的零件,表面应尽可能洁净,不应有严重锈斑及油垢,以免影响渗碳正常进行,造成零件渗碳后深度不均匀和产生软点。
对于要求局部渗碳的零件,要认真进行防渗,常见的防渗方法有如下几种:①预留余量切除法②涂料法③镀铜法⒊装箱:渗碳箱一般用钢板焊成或铸铁铸成,渗碳箱不宜过大,其外形尺寸应尽可能适合工件的要求,箱子最好与炉底板架空,受热均匀。
⒋装炉与升温:零件可在低温入炉并用分段升温的方法。
但对于连续生产,这种方法不经济,故通常采用高温入炉的方法。
由于固体渗碳时零件装于密封的渗碳箱内,热量要通过箱壳及箱内渗碳剂传递到零件上,如果控制不当,容易造成炉温与零件实际温度或箱内表层和中心的温度差很大,零件渗碳深度不均匀。
因此,一般制定工艺时,均在炉温升到820—850℃范围保温一段时间,使备部分温度均匀一致后,才以缓慢的加热速度升至900—930℃的渗碳温度。
测其渗碳层深度可用金相法,即将试样经等温退火得到平衡组织,在光学显微镜下放大100倍测量,渗碳层深度相当于原始组织至表面距离。
以下是所查阅资料
1.化学工业出版社《金属热处理原理与工艺》
2.石家庄市减速机厂高荣翠刘福深孙岭青
3.闵淑辉。
钟亚茜中南林学院,湖南长沙410004
4.刘志儒1,闫牧夫2,刘成友3,张国良4,赵新5,潘巍6
(1.哈尔滨工业大学材料学院,黑龙江哈尔滨 150010; 2.哈尔滨工业大学材料学院,黑龙江哈尔滨 150010; 3.哈尔滨意锋稀土材料开发有限公司,黑龙江哈尔滨 150076; 4.哈尔滨意锋稀土材料开发有限公司,黑龙江哈尔滨 150076; 5.上海新跃仪表厂,上海 200056; 5.上海新跃仪
表厂,上海 200056)
5.黄锡恺.机械原理.人民教育出敷社, 1981.
6.李瑞彬(齐重数控装备股份有限公司,黑龙江齐齐哈尔161005)
7.余华俐1 , 1 兰州工业高等专科学校机械工程系,甘肃兰州730050 ;杨宾崇2 兰拖集团有限责任公司,甘肃兰州730050
8.齿轮气体热处理工艺及其质量控制(JB/T 7516-94)
9.金属热处理工艺学中国矿业大学材料学院 2006 6
10、王晨(西北矿冶研究院钎具厂,甘肃白银730900)。