进口深孔钻机床切削液
卧式深孔钻操作方法
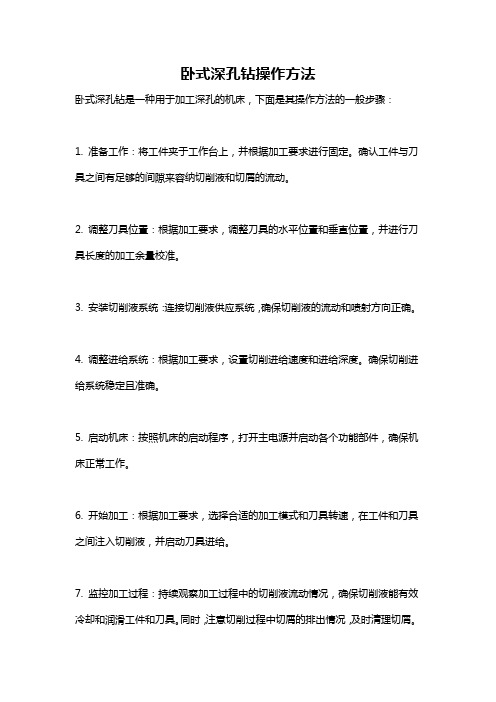
卧式深孔钻操作方法
卧式深孔钻是一种用于加工深孔的机床,下面是其操作方法的一般步骤:
1. 准备工作:将工件夹于工作台上,并根据加工要求进行固定。
确认工件与刀具之间有足够的间隙来容纳切削液和切屑的流动。
2. 调整刀具位置:根据加工要求,调整刀具的水平位置和垂直位置,并进行刀具长度的加工余量校准。
3. 安装切削液系统:连接切削液供应系统,确保切削液的流动和喷射方向正确。
4. 调整进给系统:根据加工要求,设置切削进给速度和进给深度。
确保切削进给系统稳定且准确。
5. 启动机床:按照机床的启动程序,打开主电源并启动各个功能部件,确保机床正常工作。
6. 开始加工:根据加工要求,选择合适的加工模式和刀具转速,在工件和刀具之间注入切削液,并启动刀具进给。
7. 监控加工过程:持续观察加工过程中的切削液流动情况,确保切削液能有效冷却和润滑工件和刀具。
同时,注意切削过程中切屑的排出情况,及时清理切屑。
8. 结束加工:当加工完成时,停止刀具进给并关闭切削液供应系统。
待刀具停止旋转后,关闭机床的电源,并进行清理和维护工作。
适用于数控机床的切削液选择

适用于数控机床的切削液选择数控机床作为现代制造业中不可或缺的设备之一,其切削液的选择和应用对于工件的加工质量、刀具寿命和设备性能都有着至关重要的影响。
本文将就适用于数控机床的切削液选择进行详细的探讨和分析,以帮助读者更好地了解如何选用合适的切削液,提升机床加工效率和性能。
1. 切削液的基本概念和作用切削液是指在数控机床加工过程中,用于冷却、润滑和清洗切削区域的一种液体。
它能有效地降低切削温度,减少工件和刀具的磨损,并促进切屑的排出,从而提高切削效率和加工质量。
切削液的主要作用包括:1.1 冷却切削区域:切削过程中会产生大量的热量,如果不及时冷却,会导致工件变形、刀具破裂等问题。
切削液通过吸收热量并迅速散热,保持切削区域的温度在适宜范围内。
1.2 润滑切削面:切削液能有效地润滑切削面,降低切削过程中的摩擦和热量产生,减少刀具的磨损和工件的表面粗糙度。
1.3 清洗切屑:切削液可以冲洗切屑,防止切屑在切削区域堆积,影响加工质量和刀具的寿命。
2. 切削液的选择原则2.1 适应材料和切削工艺:不同的切削液适用于不同的材料和切削工艺。
在选择切削液时,要充分考虑加工材料的种类和特性,以及切削工艺的要求,确保切削液能够与工件和刀具良好相容,并且满足特定的切削要求。
2.2 具备良好的散热性能:切削液在切削过程中要能够快速吸收和散热热量,降低切削区域的温度。
因此,切削液的导热系数和热传导性能是选择切削液时需要考虑的重要指标。
2.3 具有优异的润滑性能:切削液的润滑性能直接影响切削面的摩擦系数和磨损程度。
选择具有良好润滑性能的切削液可以有效地降低切削过程中的摩擦热量和刀具磨损,提高加工质量和刀具寿命。
2.4 对环境友好:在现代制造业追求绿色环保的潮流下,选择环境友好型的切削液也是一个重要的考虑因素。
环保性能包括切削液的挥发性、毒性和可降解性等方面。
3. 常见的切削液类型及其适应性3.1 油性切削液:油性切削液是最常用的一种切削液,其主要成分是矿物油或合成油。
深孔钻加工常见的10个常见问题和解决措施
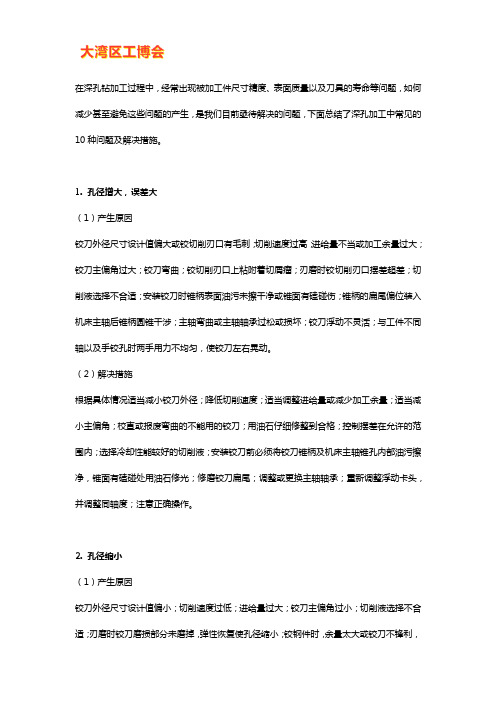
在深孔钻加工过程中,经常出现被加工件尺寸精度、表面质量以及刀具的寿命等问题,如何减少甚至避免这些问题的产生,是我们目前亟待解决的问题,下面总结了深孔加工中常见的10种问题及解决措施。
1. 孔径增大,误差大(1)产生原因铰刀外径尺寸设计值偏大或铰切削刃口有毛刺;切削速度过高;进给量不当或加工余量过大;铰刀主偏角过大;铰刀弯曲;铰切削刃口上粘附着切屑瘤;刃磨时铰切削刃口摆差超差;切削液选择不合适;安装铰刀时锥柄表面油污未擦干净或锥面有磕碰伤;锥柄的扁尾偏位装入机床主轴后锥柄圆锥干涉;主轴弯曲或主轴轴承过松或损坏;铰刀浮动不灵活;与工件不同轴以及手铰孔时两手用力不均匀,使铰刀左右晃动。
(2)解决措施根据具体情况适当减小铰刀外径;降低切削速度;适当调整进给量或减少加工余量;适当减小主偏角;校直或报废弯曲的不能用的铰刀;用油石仔细修整到合格;控制摆差在允许的范围内;选择冷却性能较好的切削液;安装铰刀前必须将铰刀锥柄及机床主轴锥孔内部油污擦净,锥面有磕碰处用油石修光;修磨铰刀扁尾;调整或更换主轴轴承;重新调整浮动卡头,并调整同轴度;注意正确操作。
2. 孔径缩小(1)产生原因铰刀外径尺寸设计值偏小;切削速度过低;进给量过大;铰刀主偏角过小;切削液选择不合适;刃磨时铰刀磨损部分未磨掉,弹性恢复使孔径缩小;铰钢件时,余量太大或铰刀不锋利,易产生弹性恢复,使孔径缩小以及内孔不圆,孔径不合格。
(2)解决措施更换铰刀外径尺寸;适当提高切削速度;适当降低进给量;适当增大主偏角;选择润滑性能好的油性切削液;定期互换铰刀,正确刃磨铰刀切削部分;设计铰刀尺寸时,应考虑上述因素,或根据实际情况取值;作试验性切削,取合适余量,将铰刀磨锋利。
3. 铰出的内孔不圆(1)产生原因铰刀过长,刚性不足,铰削时产生振动;铰刀主偏角过小;铰切削刃带窄;铰孔余量偏;内孔表面有缺口、交叉孔;孔表面有砂眼、气孔;主轴轴承松动,无导向套,或铰刀与导向套配合间隙过大以及由于薄壁工件装夹过紧,卸下后工件变形。
机械加工中切削液冷却液润滑液的选用
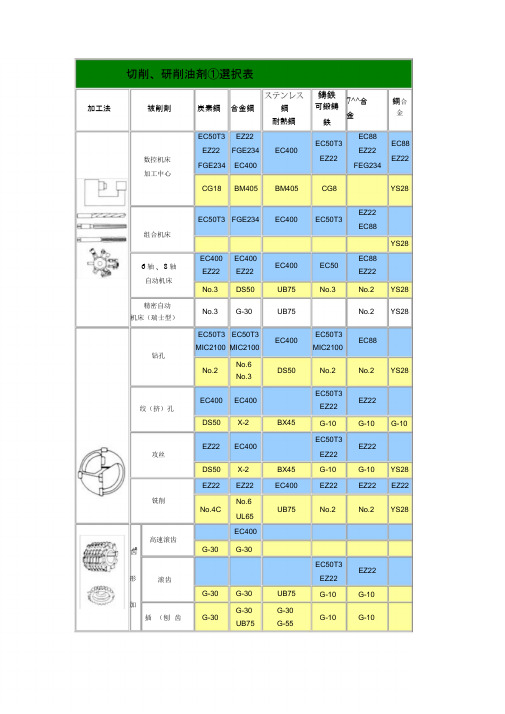
♦金属成型加工油
产品系列
特点及用途
代表产品
FL系列
速干型油品,适用于金属薄板的冲压,冲孔 及轻度拉伸工艺,在金属表面几乎不形成残留
FL6,FL2H,
FL7M,FL10
FM系列
适用于黑色金属及有色金属的中度冲压, 拉
伸等成型加工,一般适用于板厚为3mm以下
FM150,FM220
FD FE、FH系
DS50
UB75
UB100
No.3
No.2
滚压
No.7
UB75
UB75
®
研磨
H-35
H-35
G-55
H-35
齿轮研磨 螺纹研磨
G-55
G-55
■¥亠F* *r
超精研磨加工
SF33
SF33
SF33
SF33
外面磨削
SC46K
SC630
SC46K
SC630
MIC2100
EZ22
SC46K
EZ22
EE66
平面磨削
SC46K
SC630
SC46K
SC630
MIC2100
EZ22
SC46K
EZ22
EE66
£
内面磨削
S90
S90
MIC2100
SC46K
EZ22
EE66
'k
无心磨削
SC46K
SC630
SC46K
SC630
S90
SC46K
EZ22
EE66
精抛光
SC46K
SC46K
No.2
No.2
以上选型仅供参考,用户在选用产品时以我公司实际推荐为准
常用加工方法及切削液的选用

常用加工方法及切削液的选用1)车削、镗削(1)粗车:粗车时加工余量较大,因而切削深度和进给量都较大,切削阻力大,产生大量切削热,刀具磨损也较严重,主要应选择用以冷却作用为主并具有一定清洗、润滑和防锈作用的水基切削液,将切削热及时带走,降低切削温度,从而提高刀具耐用度,一般选用极压乳化液效果更好。
极压乳化液除冷却性能好之外,还具备良好的极压润滑性,可明显延长刀具使用寿命,提高切削效率,使用水基切削液要注意机床导轨面的保养,下班前要将工作台上的切削液擦干,涂上润滑油。
(2)精车:精车时,切削余量较小,切削深度只有0.05~0.8mm,进给量小,要求保证工件的精度和粗糙度。
精车时由于切削力小,温度不高,所以宜采用高浓度(10%以上)的乳化液和含油性添加剂的切削液为宜。
对于精度要求很高的车削,如精车螺纹,要采用菜籽油、豆油划其他产品作润滑液才能达到精度要求。
正如上面所提到的,由于植物油稳定发差,易氧化,有的工厂采用了精密切削润滑剂全损耗系统用油作为精密切削油,效果很好。
(3)镗削:镗削机理与车削一样,不过它是内孔加工,切削是和切削速度均不大,但散热条件差,可采用乳化液作切削液,使用时应适当增加切削液的流量和压力。
2)铣削:铣削是断续切削,每个刀齿的切削深度时刻变化,容易产生振动和一定和冲击力,所以铣削条件比车削条件差。
用高速刀具高速平铣或高速端铣时,均需要冷却性好,并有一定润滑性能的切却液,如极压乳化液。
在低速铣削时,要求用润滑性好的切削油,如精密切削油和非活性极压油。
对不锈钢和耐热合金钢,可用含硫、氯极压添加剂的切削油。
3)螺纹加工:切削螺纹时,刀具与切削材料成楔形接触,刀刃三面被切削材料所包围,切削力矩大排屑较困难,热量不能及时由切屑带走,刀具容易磨损,切屑碎片挤塞并且容易产生振动。
尤其车螺纹和攻螺纹时切削条件更苛刻,有时会出现崩刃和断丝锥,要求切削液同时具备较低的摩擦系数和较高的极压性,以减少刀具的摩擦阻力和延长刀具使用寿命,一般应选用同时含有油性剂和极压剂的复合切削液。
TBT枪钻的使用
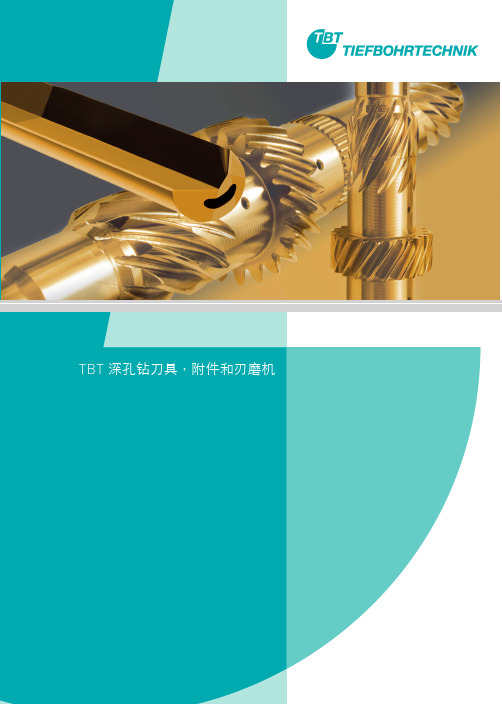
TBT枪钻刃部直径范围从0.8mm到50mm(工差直径可以精确到 0.001mm),枪钻总长可达6000mm。
加工前需要先了解被加工工件的材质,所用机床及具体加工要求,我们可 以对您的刀具进行改进和优化,根据实际情况建议您采用不同的枪钻,如 标准枪钻、扩孔钻、阶梯钻、成型钻、涂层/非涂层枪钻、PCD刀片镶入 式枪钻等。
不同于枪钻专机,加工中心很少采用 钻套进行导向。因此,要在加工中心 上使用枪钻,首先要在被加工工件上 预钻一个导向孔。
为了能达到较好的加工效果,导向孔 必须满足孔径公差,孔深等方面的要 求。我们建议您从TBT的产品中选出适 合您的产品,如单刃枪钻、阶梯钻或 整体硬质合金枪钻等。
第1步 | 引导孔 工件
进给
Ø 18,00 - 24,99 mm
0,080 - 0,110 0,080 - 0,110 0,080 - 0,110 0,080 - 0,110 0,080 - 0,110 0,080 - 0,100 0,080 - 0,110 0,080 - 0,100
0,080 - 0,100
0,080 - 0,110 0,100 - 0,130 0,100 - 0,130 0,090 - 0,120 0,060 - 0,100
zertifiziertes
ISO 9001
Qualitätsmanagement
ERTIFIZIER
ERTIFIZIER
zertifiziertes
VDA 6.4
Qualitätsmanagement
ERTIFIZIER
ERTIFIZIERT
zertifiziertes
ISO 14001
巴索切削液瑞士最大的润滑液制造商
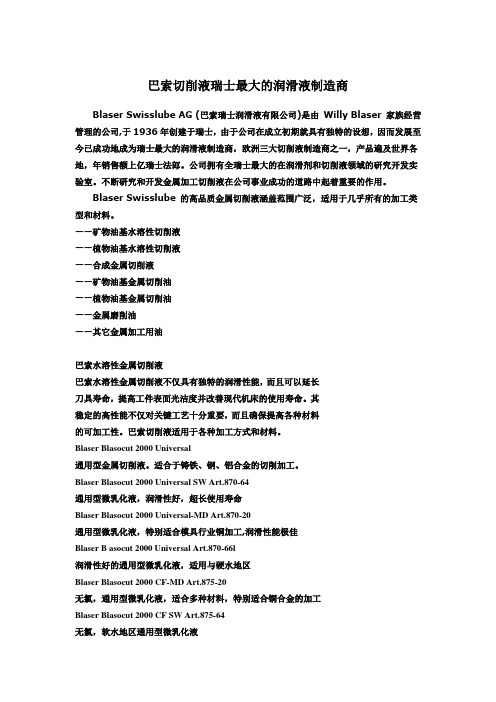
巴索切削液瑞士最大的润滑液制造商Blaser Swisslube AG (巴索瑞士润滑液有限公司)是由Willy Blaser 家族经营管理的公司,于1936年创建于瑞士,由于公司在成立初期就具有独特的设想,因而发展至今已成功地成为瑞士最大的润滑液制造商,欧洲三大切削液制造商之一,产品遍及世界各地,年销售额上亿瑞士法郎。
公司拥有全瑞士最大的在润滑剂和切削液领域的研究开发实验室。
不断研究和开发金属加工切削液在公司事业成功的道路中起着重要的作用。
Blaser Swisslube 的高品质金属切削液涵盖范围广泛,适用于几乎所有的加工类型和材料。
——矿物油基水溶性切削液——植物油基水溶性切削液——合成金属切削液——矿物油基金属切削油——植物油基金属切削油——金属磨削油——其它金属加工用油巴索水溶性金属切削液巴索水溶性金属切削液不仅具有独特的润滑性能,而且可以延长刀具寿命,提高工件表面光洁度并改善现代机床的使用寿命。
其稳定的高性能不仅对关键工艺十分重要,而且确保提高各种材料的可加工性。
巴索切削液适用于各种加工方式和材料。
Blaser Blasocut 2000 Universal通用型金属切削液。
适合于铸铁、钢、铝合金的切削加工。
Blaser Blasocut 2000 Universal SW Art.870-64通用型微乳化液,润滑性好,超长使用寿命Blaser Blasocut 2000 Universal-MD Art.870-20通用型微乳化液,特别适合模具行业铜加工,润滑性能极佳Blaser B asocut 2000 Universal Art.870-66l润滑性好的通用型微乳化液,适用与硬水地区Blaser Blasocut 2000 CF-MD Art.875-20无氯,通用型微乳化液,适合多种材料,特别适合铜合金的加工Blaser Blasocut 2000 CF SW Art.875-64无氯,软水地区通用型微乳化液Blaser Blasocut 2000 CF Art.875-66无氯,硬水地区通用型微乳化液Blaser Blasocut 2000 CF HDD Art.875-72硬盘加工专用切削液。
切削液常识-使用方法

切削液常识-4 切削液的使用方法切削液的使用方法对刀具寿命和加工质量都有很大影响,即使是最好的切削液,如果不能有效地输送到切削区域也不能起到应有的作用,因此,选用润滑为主的切削液时,(如切削油,应当把它输送到能在摩擦表面生成油膜的部位。
相反,如果选用切削液以冷却为主(如水基切削液),就应当使切削液接近刀具的刀刃部。
这种条件下通常要用压力法强迫切削液进入切削区,从而把刀具、工件、切屑由于摩擦和变形所产生的热量带走。
连续应用切削液比间断应用切削液好,间断应用切削液会产生热循环,从而导致硬而脆的材料(如硬质合金刀具)产生裂纹和崩刀刃。
间断使用切削液除了缩短刀具寿命外,还会使工件表面粗糙度不均匀。
正确使用切削液的另一个好处是有效地排除切屑,这也是有助于刀具寿命的延长。
如适当安放切削喷嘴,可防止铣刀和钻头的排屑槽被切屑堵塞或排屑不畅。
对于一些大工件的加工,或大进给量的强力切削、磨削,采用二排或多排的冷却液喷嘴,使之能充分冷却,有利于提高加工效率,保证加工质量。
1)手工加油法:固体或膏状润滑剂可以用毛笔、刷子将润滑剂或涂或滴落到刀具或工件上(主要是攻螺纹、板牙套螺纹时)。
最近还研制出手提式供液器,通过加热将润滑剂雾化,喷到刀具和工件上。
在没有配量冷却系统的机床上,如果钻孔或攻螺纹的数量不多,用手工加油是有效的方法。
当在同一机床上要完成两种不同加工时,用手工加油可以与机床上的溢流冷却系统配合起来使用。
2)溢流法:最常见的使用切削液的方法是溢流法。
用低压泵把切削液打入管道中,经过阀门从喷嘴流出,喷嘴安装在接近切削区域。
切削液流过切削区后再流到机床的不同部位上,然后汇集到集油盘内,再从集油盘流回切削液箱中,循环使用。
因此,切削液箱应有足够的容积,使切削液有时间冷却并使切屑及磨粒等沉降。
视加工种类的不同切削液的容积为20~200L,个别加工则更大,如钻深孔及强力磨削等,切削液箱可达500~1000L或更大。
在集油盘内应设有粗的过滤器,防止大的切屑进入切削液箱。
- 1、下载文档前请自行甄别文档内容的完整性,平台不提供额外的编辑、内容补充、找答案等附加服务。
- 2、"仅部分预览"的文档,不可在线预览部分如存在完整性等问题,可反馈申请退款(可完整预览的文档不适用该条件!)。
- 3、如文档侵犯您的权益,请联系客服反馈,我们会尽快为您处理(人工客服工作时间:9:00-18:30)。
进口深孔钻机床切削液
MB113进口深孔钻机床切削液,具有产品品质稳定,环保,对机床和人体无害使用寿命长,低排放的特点。
优异的润滑性、冷却性、清洗性、极压性、防锈性提高刀具的使用寿命、降低生产成本,满足工序间的防锈性能显著地浮油浮污和沉降性,通过国际SGS认证。
一.性能:
MB113进口深孔钻机床切削液原液颜色为浅黄色,稀释后变成浅色透明。
是一种优质高效切削液,采用进口润滑添加剂、防锈剂、有色金属缓蚀剂和泡沫抑制剂等高温调制而成,不含硫、亚硝酸钠和酚类等有害物质,通过相关环保认证,属于新型环保型半合成切削液,适用于进口深孔钻机床、进口数控机床、加工中心等设备使用。
产品使用范围:合金钢、碳钢、铸铁、铝、铝合金、铜等金属材料的车,铣,钻,磨,刨,冲等加工
二.进口深孔钻机床切削液使用方法:
1_将机床水箱清理干净后,在常温下,进口机床切削液的浓缩液加入水中,搅拌均匀直至形成稳定的稀释液。
推荐使用自来水。
2_金属加工过程中及时补充水和原液,忌只加水不加原液,确保适当的稀释浓度。
本品直接采用自来水稀释配制,3%—10%的稀释浓度,(即1KG原液加10-30倍左右的水),循环均匀即可使用。
三.相关推荐:
MD-231高速切削油
产品型号:MD-231
产品外观:黄色
产品运动粘度(m²/sV40℃):25
产品性能及用途:
MD-231高速切削油:重负荷中粘度油,用于加工硬质金属、抗磨效果极佳,刀具寿命长,工件平滑,特别适合高速操作
四.进口深孔钻机床切削液注意事项:
1_本产品应禁止与乳化油、皂化液等混用,日常使用中尽量避免其他润滑油、液压油等混入,若混入后应及时清除,以免滋生细菌等,影响了进口机床切削液的性能。
2_使用本进口机床切削液加工完成的零部件避免雨水及酸雾侵蚀,停机后,用干抹布将机床残留切削液擦干净。
3_初次使用本进口深孔钻机床切削液应彻底清洗机床切削液循环系统。
将废液全部排出后,擦除各处油污,使用清水再次循环清洗2-3次即可,必要时可使用杀菌剂。
六、美科进口深孔钻机床切削液小知识分享:
切削液喷雾供液法的应用
一般说来喷雾供液可用于所有加工方法,但特别适合于对小面积加工局部供液的情形。
用立铣刀端齿加工时经常应用。
在加工中心和组合机床上,一般均有独立的液箱和供液系统供应某种稀释后的水基切削液,这种切削液适合于多数加工方式。
对于某些加工工序,如铰孔、攻螺纹等,稀释后的通用切削液往往不能满足润滑性能要求,这时可用喷雾供液法直接供给该种切削液的高浓度稀释液甚至原液。
如果使用的通用切削液是乳化切削液,由于其原液与油基切削液有同等程度的润滑性,所以更容易解决上述问题。
而且乳化液原液本身就是水溶性油剂,即便是混入机床的切削液箱中也不会将其污损。
切削液喷雾供液法可应用于车削、端铣、自动机床加工、数控机床加工。
带有电磁阀控制的喷雾装置适用于在数控机床上攻螺纹、铰孔。
在使用数控机床、组合机床等设备的自
动化加工中,在操作者不需要接近机床的场合使用喷雾供液法是受欢迎的。
切削液喷雾供液对操作者而言有吸入危害,若长期进行这种作业,会有损于健康,所以应用时必须特别注意考虑操作者的健康和环境问题。
七、美科进口深孔钻机床切削液每日格言分享:
自由是做法律所许可的一切事情的权利。
孟德斯鸠
在人生的任何场合都要站在第一线战士的行列里。
奥斯特洛夫斯基
首先是最崇高的思想,其次才是金钱;光有金钱而没有最崇高的思想的社会是会崩溃的。
陀思妥耶夫斯基。