纺纱(细纱)实用工艺单
细纱操作法..

(6)绕导纱钩和卡头:插好管后放开刹锭,右手同时绕导纱钩(弧度越小越好)并结合处,食、中、无名指稍成品字形,拇指压住纱条绷紧卡头,卡出的头挺直,长度符合标准(16mm —22mm)。
风箱花
30分钟清1次
30分钟清1次
30分钟清1次
手掏
机头、机尾
交班前清
交班前清
交班前清
毛扫
(2)落纱工:
清洁项目
清洁时间
清洁工具
早
中
晚
绒辊
9:30
17:30
清洁枪
升降、清洁器、隔纱板
10:30
18:30
2:30
清洁枪
锭脚
11:30
19:30
3:30
清洁枪
叶子板
14:40
22:40
6:40
油漆扫
机脚
15:00
⑹巡回氨纶机台时,目光一定要运用好,注意氨纶张力轮是否在转动,如发现张力轮没有正常转动时,表示氨纶丝已断头或氨纶丝移位、偏离皮辊中心位,必须纱线打断,将没氨纶丝的纱线拉掉,以防影响质量。
⑺氨纶纱断头时将纱果拔出检查是否有氨纶丝包在中间,必须取另一支筒管重新生头,不准采用接头方式直接接上。
⑻氨纶纱绕皮辊严重时,应将相邻的纱果打断,打起摇架,拿下皮辊,用手剥干净皮辊绕花,不能使用钩刀,以防钩伤皮辊。
四、操作
1、基本操作
细纱单项操作主要有细纱接头、细纱生头两项基本功。
细纱接头:50″/10个细纱生头:40″/10个
(完整版)细纱工艺

细纱工艺一、细纱工序的任务1.牵伸:将粗纱牵伸到所要求的特数。
2.加捻:给牵伸后的纱条加上一定的捻度,使之具有一定的强力、弹性和光泽。
3.卷绕:卷绕成管纱,便于运输和后加工。
二、细纱工艺设计概要在确定细纱工艺时,应考虑以下一些方面。
(1)细纱机在向大牵伸方间发展。
为了加大细纱机的牵伸倍数,可采用不同的牵伸机构.改善在牵伸过程中对须条的控制,合理确定牵伸工艺,获得理想的效果。
在加压形式上,目前大多采用弹簧摇架加压和气动加压。
在加大细纱机的牵伸倍数、缩短前纺工序和减少并合数的同时,必须注意改进喂入半制品的质量。
(2)细纱捻度直接影响成纱的强力、捻缩、伸长、光泽和毛羽、手感,而且捻度对细纱机的产量和用电等经济指标的关系很大,因此,必须全面考虑,合理选择捻系数。
(3)在加强机械保全保养工作的基础上,保证最大限度地提高车速,选择合适的钢领、钢丝圈、筒管直径和长度等。
(4)加大细纱管纱卷装可以有效地提高劳动生产率。
在确定管纱卷装时,应考虑最大限度地增加卷绕密度,但必须使络筒时发生的脱圈现象减少到最低限度,否则会降低劳动生产率。
三、细纱牵伸工艺(一)细纱总牵伸倍数在保证和提高产品质量的前提下,提高细纱机的牵伸倍数,在经济上获得较大的效益。
目前细纱机的牵伸倍数一般在30—50倍。
总牵伸倍数的能力首先决定于细纱机的机械工艺性能,但总牵伸倍数也因其他因素而变化。
当所纺棉纱线密度较粗时,总牵伸能力较低;当所纺棉纱线密度较细时,总牵伸能力较高;在纺精梳棉纱时,由于粗纱均匀、结构较好、纤维伸直度好、所含短绒率也较低,牵伸倍数一般可高于同线密度非精梳棉纱;纱织物和线织物用纱的牵伸倍数也可有所不同,这是因为单纱经并线加捻后,可弥补若干条干和单强方面的缺陷,但也必须根据产品质量要求而定。
总牵伸倍数过高,产品质量将恶化,棉纱条干不匀率和单强不匀率高,细纱机的断头率也增高。
但总牵伸倍数过小,对产品质量未必有利,反而增加前纺的负担,造成经济上的损失。
纱线设计工艺单-最终版

顶梳~皮锟
140
400
14.6
5.7
10~11
0.38
22
25
0.8
并条工艺
道别
机型
条子干定量
并合数
总牵伸倍数
各区牵伸倍数分配
前罗拉转速
机械
实际
前张力
1-2
2-3
3-4
涤预并
SFA2071
14.48
5
5.15
5
1.0
3
1
1.67
960
棉预并
SFA2071
15.59
6
7.97
7
1.01
240
.5
细纱工艺
机型
细纱干定量g/100m
公定回潮率%
总牵伸倍数
捻向
后区牵伸倍数
计算捻度/10cm
捻系数
罗拉中心距mm
机械
实际
1-2
3-4
三罗拉细纱机
1.356g/100m
3.24%
31.58
30
Z
1.3
93.56
350
43
51
罗拉加压N
罗拉直径mm
转速r/min
皮圈钳口mm
钢领
0.18
0.36x0.3x0.3x0.3x0.36
0.13
0.84X1.09
1.09x0.66
-3.2
72
0.41
4.8
0.79
0.18
0.18
0.2x0.18x0.15x0.15x0.18
0.13
0.66x0.84
0.84x0.56
条并卷工艺
机型
细纱操作法..

(3)换批的机台要严格按工艺要求开车,并认真观察质量情况。
(4)接班时要严格检查机台,防止产生机械疵点,防止用错粗纱及细纱筒管。
(5)发现机器有故障、听见机器有异响、闻到有异味时要及时停机,通知保全工检修,防止出质
(3)引纱:小纱由纱管底引出,大、中纱由纱管上部引出,纱的长度越短越好(一般不超过四个锭距、五个锭子)。
(4)挂钢丝圈:左手拿纱管略带倾斜,大纱管底部向锭杆、小纱管顶部向锭子、纱管尽量靠近钢领板,用右手的食指将钢丝圈从里向外带出,位置在钢领板右前方,食指尖紧扣钢丝圈,同时拇指第一关节轻压纱条将纱挂入钢丝圈内。
作业指导书
标题:细纱操作法
文件编号:JS-FS-ZD-YZ-005
修改状态:A/0
页次:4/7
⑶粗纱的分段,是根据粗纱的定量、定长和细纱的定量、定长和细纱的定量、车速计算出宝塔分段规定的数量和时间,逐步调整好宝塔。一般在车头(或车尾)留3—4节罗拉范围专门处理小粗纱,以保证粗纱宝塔分段整齐。
⑷换粗纱时,根据机器车速、看锭多少和巡回时间,合理掌握粗纱圈数,既减少不必要的浪费,又防止空粗纱。一般粗纱底层要少于15cm才可以除下更换。
(3)检查机台风口,地面清洁情况,回花,粗纱头,绒辊花,回丝,下脚是否收清,
(4)工具是否齐全,机台零部件是否缺损。
(5)主动问清上班的工艺情况,机械运转情况,生产、质量情况、平揩车情况等。
四、操作
1、基本操作
细纱单项操作主要有细纱接头、细纱生头两项基本功。
细纱接头:50″/10个细纱生头:40″/10个
(2)交清机器运转情况:如零部件是否有损坏、机械故障等。
细纱工序操作指导书(doc 16页)

XXX棉纺织企业有限公司文件名称:细纱工序操作指导书文件编号:MY3—031版本号:A编制:审批:日期:2004/7/5 日期:2004/7/9修订记录1 目的便于生产部的生产管理,培训细纱工序的操作者的技能技巧,掌握在生产过程中应知的常识,让安全优质生产得以顺利进行。
2 范围适用于细纱工序生产作业操作规程及在生产中应注意的事项。
3 职责由生产部制定和修改,操作工执行。
4 工作内容4.1 交接班工作交接班工作是生产员工的第一项工作,要作好此工作,交接双方提前十五分钟对岗开车交接,交班者以主动交清为主,接班者以检查为主,做到相互合作又分清责任。
4.2 设备操作4.2.1 开机前准备工作4.2.1.1 检查机头是插“正常”或“维修”牌。
4.2.1.2 检查机台是否符合工艺要求。
4.2.1.3 关好机门。
4.2.1.4 确信机台机电正常。
4.2.1.5 将机台彻底清洁干净。
4.2.1.6 按工艺和生产要求上粗纱,钢丝圈,插好细纱管等,并分段上粗纱(1100m 、1400m 、1800m 、2500m),穿粗纱时将粗纱条引出穿过导纱棒(杆)喂入喇叭口,粗纱经过喇叭口进入牵伸部件。
内 容 重 点 要 求 1.机台和台面彻底清洁 按清洁进度表 2.生产情况1)前后供应平衡 按生产平衡要求 2)工艺变更机台落实 3)平揩车 填写停台时间 4)空锭 不允许人为空锭 5)转批情况 批号、支数清楚准确。
3.设备情况1)坏机原因清楚 2)流动风机吹、吸风清洁效果好3)皮辊、皮圈是否完好 皮辊无钩伤,皮圈破损。
4.2.2 开机操作要点及注意事项4.2.2.1 将机台总开机键推至“I”。
4.2.2.2 拉开机头安全钮,红灯闪动。
4.2.2.3 开机前打V1+V2档。
机尾挂黄牌(挑纱脚牌)。
4.2.2.4 将机台的摇架分一段距离按下2个(毎隔三个机台支架)。
4.2.2.5 将机台罗拉座的粗纱绕好(以免粗纱绕罗拉)。
4.2.2.6 确保机台两边人员安全才按绿色开机键。
2纺纱工艺流程(PPT32页)
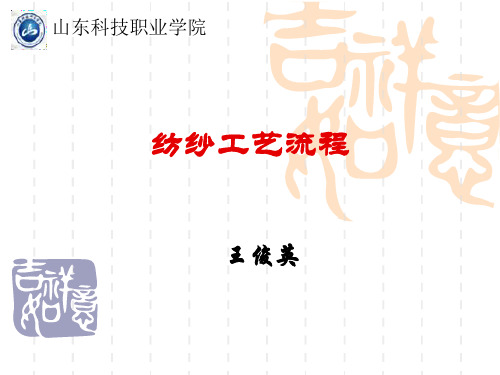
(二)梳棉工序的任务
分梳 除杂 均匀混和 成条
(三)精梳工序的任务
排除生条中的短绒 清除生条中残留的棉结和杂质。 使纤维进一步伸直、平行和分离。 制成条干均匀的精梳棉条。
(四)并条工序的任务
并合 牵伸 混合 成条
(五)粗纱工序的任务
牵伸 加捻 卷绕成形
山东科技职业学院
纺纱工艺流程
王俊英
一、纱线生产过程
纺纱:把纺织纤维加工成纱的过程
1、原棉(进厂) 2、棉卷或棉层 3、棉条 4、粗纱 5、细纱 6、筒纱(出厂)
棉包 开清棉工序 梳棉工序和并条工序 粗纱工序 细纱工序 络筒工序
二、棉纺工艺流程
1、普梳工艺流程 (1) 普梳纯纺工艺流程 (2) 普梳混纺工艺流程 2、精梳工艺流程 (1)精梳纯棉工艺流程 (2)精梳涤棉混纺工艺流程
开清棉——梳棉——精梳准备——精梳— —并条(二道)——粗纱——细纱——后
加工
(4)精梳涤棉混纺工艺流程
棉:开清棉——梳棉——精梳准备——精梳— 涤:开清棉——梳棉——涤予并——————
——并条(混三道)——粗纱——细纱
——后加工
三、各工序的任务
(一)开清棉工序的任务 开松 除杂 混和 均匀成卷
(1)普梳纯纺工艺流程
开清棉——梳棉——并条(二道)—— 粗纱——细纱——后加工
(2)普梳混纺品种工艺流程 (以T/C品种为例)
棉:开清棉——梳棉—————— 涤:开清棉——梳棉——涤予并—
——并条(混三道)——粗纱——细纱
——后加工
(3)精梳纯棉工艺流程
(六)细纱工序的任务
牵伸 加捻 卷绕成形
细纱工序操作指导书

细纱工序操作指导书细纱工序操作指导书一、背景介绍细纱工序是制作高品质纱线的关键工序之一。
本操作指导书旨在详细介绍细纱工序的操作流程和注意事项,以确保产品质量和生产效率。
二、设备准备1.纺纱机:按照制造商的说明书检查纺纱机的各项参数和功能是否正常。
2.原材料:准备好经过均质处理的纤维原材料。
3.辅助设备:准备好纺纱工作所需的各种辅助设备,如称重器、纱锭和纺纱辅助液等。
三、操作流程1.纺纱机启动a.将纺纱机接入电源,并确保电源稳定。
b.检查机器上的各个按钮和开关是否处于正确的位置。
c.启动纺纱机,并等待其正常运行。
2.原材料处理a.将纤维原材料装入料筒中,确保原材料的纤维长度和含水量符合要求。
b.使用称重器对原材料进行准确称重,并记录下称重结果。
3.选择纺纱参数a.根据产品要求,选择适当的纺纱参数,包括纺纱速度、纱锭速度和纺纱张力等。
b.设置纺纱机上的各项参数,并进行必要的调试和校准。
4.纺纱过程a.将原材料缆线连接到纺纱机上的进纱装置,确保原材料的顺畅进入纺纱区。
b.监控纺纱机的运行状态,注意纱线的质量和纤维的均匀性。
c.定期检查纺纱机上的各个部件,确保它们的正常运行。
5.纱锭更换a.当纺纱机上的一个纱锭耗尽时,及时更换新的纱锭。
b.清洁和检查旧纱锭,确保其可重复使用或进行维修。
6.纺纱结束a.根据纺纱工作的进展和产品需求,决定纺纱结束的时间。
b.停止纺纱机,并逐步关闭相关设备和机器。
四、注意事项1.纺纱过程中,注意纱线的质量和纤维的均匀性,及时调整参数和设备以保证纺纱效果。
2.定期检查纺纱机的部件,如皮带、滑轮和纱锭等,确保其正常运行。
3.清洁并维护纺纱机,保持其干净和无尘,以防止纤维污染和质量问题。
附件:本文档不涉及附件。
法律名词及注释:1.《劳动法》:指中华人民共和国劳动法,是中华人民共和国的基本劳动法律。
2.《产品质量法》:指中华人民共和国产品质量法,是保障产品质量和保护消费者权益的法律。
细纱工艺计算tex实例

细纱工艺计算细纱工艺计算:18tex 纯棉纱为例表7-7 细纱工艺单(1)总牵伸倍数W%=8.5%细纱干定量为初步拟定粗纱特数为600tex 实际牵伸机械牵伸)所以,根据设备传动得:=252625261672.21z 632529255010871795735z z z =∙⨯⨯⨯⨯⨯⨯⨯⨯根据设备说明书选择m E '=33.42;牵伸成对变换齿轮齿数Z 25/Z 26取68/66T ; 修正实际总牵伸倍数:粗纱特数:/(2)后区牵伸倍数 后区牵伸倍数,初步拟定为1.25倍根据设备传动得:根据设备说明书选择=1.25;后牵伸变换齿轮齿数取28T 。
2、锭速18tex 纱的折合单产实际产量16.2096.0963.13838d =⨯=⨯=影响系数折合率Q (kg/千锭时)折合率、影响系数参见《棉纺手册》第1194~1195页表7-1-7与表7-1-8⨯=L Q Qd 时间效率 时间效率参见《棉纺厂设计》第95页表6.3.2-1,选用96%20.16=96.0⨯L Q 得L Q =21.00因为L Q =10001000100060⨯⨯⨯⨯Vf Nt 所以21.00=100060f 18⨯⨯V 得Vf =19.44m/min Nt---纱线特数 Vf---前罗拉线速度(m/min) 设计捻系数为375 因为实t α=设t α×时间效率 所以实t α=375×0.96=360又因因为2t 1001d n n T s fπ⨯⨯=,而21000n d v f f π⨯=nf---前罗拉转速(r/min ) 所以10t ⨯=f sv n T 所以1044.19n 91.84s ⨯= 得s n=16506.50(r/min )初步拟定sn =16000(r/min)[《棉纺手册》第592表3-1-1A]1D —主电动机皮带轮节径(mm)2D —主电动机皮带轮节径(mm) :锭带厚度(本机为0.6mm ):滚盘直径(250mm ):锭盘直径(可选18、19.5、22、24mm ,本机采用22mm )查表得: 1D =180, 2D =180, n s ’=16411 r/min 3、捻度选定细纱实际捻系数为360,则捻度为:由设备传动图得: 捻度=查设备说明书,得、取46、42T ;捻度修正为:因为2t 1001d n n T s fπ⨯⨯=则,修正前罗拉转速)(min /r 54.2442514.349.8510016411100n 2''=⨯⨯⨯=⨯⨯=d T n t s fπ 4、卷绕密度本机选定卷绕圈距为纱线直径的4倍,则有:由设备传动得到,钢领板一次升降时前罗拉输出纱条长度应等于同一时间管纱卷绕长度,即有:..(1)因为:成形凸轮转速前罗拉速度纱圈平均长度=凸轮升降比=1:3由于22)2(22sind D H d D -+-=α将上述5式代入(1)式中得到:本机=25mm ,钢领直径42mm ,为39mm ,d 为19mm ,H 为57mm ,为9.95°因此查设备说明书得18tex 纱线对应的卷绕齿轮5、钢领板级升钢领板级升距y 与纱线特数存在联系,钢领板一次升降绕纱长度的重量应等于同一时间纱管上卷绕的纱线重量,则有:即:带值计算得:y=0.088由于棘轮每撑过N齿钢领板级升距为:Y=所以,N=。
- 1、下载文档前请自行甄别文档内容的完整性,平台不提供额外的编辑、内容补充、找答案等附加服务。
- 2、"仅部分预览"的文档,不可在线预览部分如存在完整性等问题,可反馈申请退款(可完整预览的文档不适用该条件!)。
- 3、如文档侵犯您的权益,请联系客服反馈,我们会尽快为您处理(人工客服工作时间:9:00-18:30)。
细纱工艺表一、细纱工艺设计的相关知识 1.细纱定量【参照GB/T398-2008】---棉纱 100m 纱线的标准干燥质量:85.1010%)5.81(t t TT G =⨯+=细纱2.牵伸工艺设计(1) 总牵伸倍数表1-1 细纱机总牵伸倍数参考围表1-2 纺纱条件对总牵伸倍数的影响(2) 后牵伸区工艺表1-3 后牵伸区工艺参数3.捻系数表1-4 影响捻系数的因素表1-5 常用细纱品种捻系数参考围%100-(%)⨯=前罗拉输出须条长度加捻成纱长度前罗拉须条输出长度捻缩率表1-6 捻缩率与捻系数的关系比例4.锭速表1-7 不同纺纱特数的参考围5.卷绕圈距△△是指卷绕层的圈距,一般△为细纱直径的4倍;δtT d 03568.0=当纱条单位体积质量为0.8g/cm 3时,纱线直径为:t T d 04.0≈△ =t T 16.0 6.钢领板级升距)2/sin(1202γρtT m =式中:ρ---管纱卷绕密度,在一般卷绕力条件下为0.55g/cm 3 2/γ---成形半锥角有关卷绕的其他参数如图所示,参考值见下表: 表1-8 细纱机卷绕部分其他参数7.纲领与钢丝圈(1) 平面纲领与钢丝圈型号的选配表1-9(2) 锥面纲领与钢丝圈型号的选配表1-10(3) 钢丝圈号数的选择表1-11 纯棉纱钢丝圈号数选用围(4) 钢丝圈轻重的掌握表1-128.罗拉中心距(1)前区罗拉中心距表1-13 前牵伸区罗拉中心距与浮游区长度(2)后区罗拉中心距表1-14后牵伸区罗拉中心距的参考围9.胶圈钳口隔距表1-15 胶圈钳口隔距参考围注:在条件许可下,采用较小的上下销钳口隔距,有利于改善成纱质量。
表1-16纺纱条件对胶圈钳口隔距的影响10.罗拉加压表1-17 罗拉加压参考围11.前区集合器表1-18产品:cJ9.8T 二、任务实施1. 计算细纱定量及牵伸倍数 (1) 计算细纱定量根据所纺细纱的线密度9.8tex ,公定回潮率为8.5%,实际回潮率为6.3%(在实际生产中,细纱的回潮率控制在6.0%~6.5%)细纱定量为:)100/(9032.010%)5.81(8.910%)5.81(m g T G t =⨯+=⨯+=细纱)100/96.0%3.619032.0%3.61m g G G ()()(细纱细纱湿=+⨯=+⨯=(2) 确定牵伸倍数设FA506型细纱机的牵伸配合率为1.02(在实际生产中,工厂根据机械牵伸倍数与实际牵伸倍数计算获得,是个统计值,多数情况为1.02-1.06)。
第一步:计算实际牵伸倍数 53.389032.01048.310=⨯=⨯=细纱粗纱实际G G E (查看一下,是否在参考围) 表2 细纱机总牵伸倍数参考围第二步:计算机械牵伸倍数32.3902.153.3802.1=⨯=⨯=实际机械估E E细纱机的总牵伸倍数是指前罗拉与后罗拉之间的牵伸倍数。
如图所示:由其传动图求其总牵伸倍数。
31310129.927372823271045935d Z Z d Z Z d Z Z d Z Z E N J M K N J M K ⨯⨯⨯⨯⨯=⨯⨯⨯⨯⨯⨯⨯⨯⨯⨯⨯⨯=机械选定2869=N M Z Z ,则7816.1690129.92857.390129.9=⨯⨯=⨯⨯=M N J K Z Z E Z Z 机械估 故选定48,85==J K Z Z (7708.14885= ) 最终: 33.392528482569850129.9=⨯⨯⨯⨯⨯=机械E式中:K Z --39、43、48、53、59、66、73、81~89;取85 J Z --39、43、48、53、59、66、73、81~89;取48(K Z J Z ---总牵伸变换齿轮(轻重牙) M Z --牵伸变换齿轮齿数,有69、59;取69 N Z --牵伸变换齿轮齿数,有28、46;取28 1d --前罗拉直径,mm ,25 3d --后罗拉直径,mm ,25第三步:计算后区牵伸倍数中罗拉和后罗拉间的牵伸倍数(结合表3)表3 后牵伸区工艺参数37.12540257826.547826.542336353232~=⨯⨯=⨯⨯=⨯⨯⨯⨯=d Z d d Z de H H 后罗拉中罗拉(是否符合,根据其用途)式中:H Z --后区牵伸变换齿轮齿数,有36、38、40、42、44、48、50;取402d --中罗拉直径,mm ,25 2.设计捻度第一步:初步选取捻系数根据表1-4,参考表1-5,初步设计细纱的捻系数为350. 第二步:计算捻度 (1) 计算细纱的捻度: )10/(80.1118.9350cm T T tt t 捻回估估===α(2) 根据传动图,细纱的捻度为: EC A DB EC AD B tex Z Z Z Z Z Z Z Z d Z Z D T ⨯⨯⨯⨯=⨯⨯⨯⨯⨯⨯⨯+⨯⨯⨯⨯⨯⨯+=74.2422253228)(100375971)(3πδδ)10/(16.112368045807574.2422cm 捻回=⨯⨯⨯=式中:3D --滚盘直径,mm ,250mmd--锭盘直径,mm ,24mm 、22mm 、20.5mm ;取22mm δ--锭带厚度,0.8mmB A Z Z /--捻度变换成对齿轮齿数,有38/82、45/75、52/68、60/60、68/52、75/45、82/38;取45/75C Z --捻度变换齿轮(中心牙)齿数,有80、85、87;取80D Z --捻度变换齿轮(中心牙)齿数,有77、80、85;取80E Z --捻度变换齿轮齿数(与锭盘直径有关),33()24mm φ、)22(36mm φ、)mm 5.2039φ(,取36第三步:计算细纱的捻系数12.3518.916.112=⨯=⨯=t tex t T T α根据表1-6,确定捻缩率为2.26%,为方便操作,捻向设计为Z 向。
3.设计速度 (1) 前罗拉速度%9827375971273228146021⨯⨯⨯⨯⨯⨯⨯⨯⨯⨯⨯⨯⨯⨯=D B E C A Z Z D Z Z Z D n 前罗拉min)/(77.160807520036804518027.827.821r Z Z D Z Z Z D D B E C A =⨯⨯⨯⨯⨯⨯=⨯⨯⨯⨯⨯⨯=式中:1D --电动机带盘节径,mm ,170mm 、180mm 、190mm 、200mm 、210mm ;取180mm2D --主轴带盘节径,mm ,180mm 、190mm 、200mm 、210mm 、220mm 、230mm 、240mm ;取200mm(2) 锭子速度min)/(14165200)8.022(180)8.0250(8.1430%98)()(1460213r D d D D n =⨯+⨯+⨯=⨯⨯+⨯+⨯=δδ锭子4.设计卷绕圈距 第一步:预测卷绕圈距)(5009.08.916.016.0mm T t =⨯=⨯=∆估 第二步:计算卷绕圈距如图所示,钢领板每升降一次,前罗拉输出长度等于同一时间管纱卷绕长度。
2sin3)(342273720251271042025352201γπππ⨯∆⨯-⨯=⨯∆⨯⨯-=⨯⨯⨯⨯⨯⨯⨯⨯⨯⨯⨯⨯o m m F G d d A d d Z Z d2sin3)(62.4426202γπ⨯∆⨯-⨯=⨯d d Z Z m FG2sin)(0001355.0202γ⨯∆-⨯=d d Z Z m FG2247.10sin 5009.0)1835(0001355.0⨯-⨯=F G Z Z 式中:m d --管纱直径,mm ,35mm o d --管纱直径,mm ,18mm 2/γ--成形半锥角,047.10 式中个数据从表1-8中选取。
122=+F G Z Z ,所以52,70==F G Z Z ,则: )(50.07047.10sin 52)1835(0001355.02sin)(0001355.002222mm Z Z d d GFo m =⨯⨯-⨯=⨯⨯-⨯=∆γ5.设计钢领板级升距 第一步:预测钢领板级升距 )(2610.047.10sin 55.01208.9)2/sin(12002mm T m t=⨯⨯==γρ估式中:ρ--管纱绕纱密度,在一般卷绕力条件下为0.553/cm g 第二步:计算钢领板级升距由传动图可知,钢领板每升降一次,级升距变换棘轮n Z 撑过n 齿,从而获得级升距2m 。
1301304014014015462⨯⨯⨯⨯⨯⨯=⨯⨯⨯⨯⨯⨯=ππn n Z n D D Z D n m2557.04319556.109556.10=⨯=⨯=n Z n 式中:4D --上分配轴左端轮直径,mm ,130mm 5D --钢领板牵吊轮直径,mm ,130mm 6D --卷绕论直径,mm ,140mmn Z --43、45、48、50、55、60、65、70、72、75、80,取43 6.选取纲领与钢丝圈参考表1-9、表1-10、表1-11、表-12,选择纲领、钢丝圈如下: 纲领:PG1/2,直径38mm 。
钢丝圈型号:2.6Elf 。
钢丝圈号数:15/0。
7.设计罗拉中心距根据FA506型细纱机的牵伸形式(长短胶圈牵伸),纤维、粗纱及所纺纱的情况,设计罗拉中心距如下:前区罗拉中心距采用43mm 。
后区罗拉中心距采用54mm 。
8.设计其他工艺参数 (1)罗拉加压(N/双锭)根据设计的罗拉速度、中心距、定量,选择罗拉的加压为:后罗拉:中罗拉前罗拉⨯⨯ 140100140⨯⨯(2)胶圈原始钳口隔距由于细纱的线密度为9.8tex ,根据表1-15,表1-16,选择胶圈原始钳口隔距为2.4mm 。
(3)前区集合器由于细纱的线密度为9.8tex,根据表1-18,选择细纱机的前区集合器开口尺寸为1.6mm。
9.细纱工艺设计表表1-19 细纱工艺设计表。