管理会计双语材料
管理会计 双语课件 Management accounting

01 会计信息的概念
Example
The following statements refer to qualities of good information:
(ⅰ) It should be communicated to the right person (ⅱ) It should always be completely accurate before it
关), Complete (完整 ), Accurate (准确 ), Clear (清楚), it should inspire confidence , it should be appropriately communicated , its volume should be manageable, it should be timely (及时 )and its cost (成本收
QUEห้องสมุดไป่ตู้TION
Accounting Information
C ONTENTS
1
信息的概念 The definition of
Information
2 信息的作用
The use of Information
3 案例
Case
01 会计信息的概念
Data and information
Data ( 数据 ) is the raw material for data processing.
01 会计信息的概念
Identify the users of TLC Daycare’s accounting information as internal(I) or external(E).
管理会计双语版学习辅助资料(doc 29页)

管理会计双语版学习辅助资料(doc29页)部门: xxx时间: xxx整理范文,仅供参考,可下载自行编辑管理会计Managerial Accounting(双语32)学习辅助资料2013-2014-1学期第一部分授课计划使用教材:Managerial Accounting(会计学--管理会计分册,James M. Reeve等,杜兴强改编),中国人民大学出版社,教育部高校工商管理类教学指导委员会双语教学推荐教材总计学时:32第二部分成绩评定第三部分主要内容Terminology------------专业术语(自查中文,了解术语的含义)Major Contents -------本章主要内容(给出的是教材上的一级和二级标题,加※的部分略看,其他需要精读)Questions----------------思考题(取自每一章课后的Eye Openers)School Assignments----作业题(需要做书面作业)Chapter 18 Managerial Accounting Concepts and PrinciplesTerminology:managerial accounting ( or management accounting ); financial accounting;financial statements;stakeholders;shareholders;creditor;government agencies;general public;line department;staff department;management process;planning; directing;controlling;improving;decision making;strategy planning;operational planning;management by exception;Generally Accepted Accounting Principles;service companies;merchandising companies;manufacturing companies;direct cost;indirect cost;period costs;product costs;manufacturing costs;cost object;direct materials cost;direct labor cost;factory overhead;prime costs;conversion costs;selling expenses;administrative expenses;cost of merchandise sold;cost of goods sold;materials inventory;work in process inventory;finished goods inventory;balance sheet;income statement;merchandise available for sale;cost of goods manufactured;cost of finished goods available for sale;statement of cost of goods manufactured.Major Contents:1. Managerial AccountingDifferences Between Managerial Accounting and Financial AccountingThe Management Accountant in the Organization ※Managerial Accounting in the Management Process2. Manufacturing Operations: Costs and TerminologyDirect and Indirect CostsManufacturing Costs3. Financial Statements for a Manufacturing BusinessBalance Sheet for a Manufacturing BusinessIncome statement for a manufacturing company4. Uses of Managerial Accounting ※Questions: (on page 20—21)Eye openers: 1, 4, 13, 14, 15, 16, 18, 20, 21.School assignments:No.Chapter 21 Cost Behavior and Cost-Volume-Profit AnalysisTerminology:cost behavioractivity baserelevant rangevariable costsvariable cost per unit or unit variable costfixed costsfixed cost per unitmixed costshigh-low methodvariable costingcost-volume-profit analysisselling pricesales volumeproduction volumeprofitincome from operationscontribution marginunit contribution margincontribution margin ratio or profit-volume ratiobreak-even pointbreak-even sales( units)break-even sales( dollars)target profitcost-volume-profit chartbreak-even chartprofit-volume chart“what if ”analysis or sensitivity analysissales mixoperating leveragemargin of safetymargin of safety(units)margin of safety(dollars)Major Contents:(★all should be read intensively)1.Cost Behavior。
管理会计参考文献英文

管理会计参考文献英文References for Management Accounting.1. Brimson, J. A., & Antos, D. L. (2015). Managementand cost accounting (14th ed.). McGraw-Hill Education.This textbook provides a comprehensive overview of management accounting principles and practices. It covers a wide range of topics, including cost behavior, cost-volume-profit analysis, budgeting, and performance evaluation. The authors present a clear and concise explanation of these concepts, making it an ideal reference for students and practitioners alike.2. Horngren, C. T., Datar, S. M., & Rajan, M. V. (2015). Cost accounting: A managerial emphasis (16th ed.). Pearson Education.This book is another excellent resource for understanding the fundamentals of management accounting. Itfocuses on the application of cost accounting techniques in decision-making, planning, and control. The authors present real-world examples and cases to illustrate the practical relevance of these concepts.3. Kaplan, R. S., & Norton, D. P. (2017). The balanced scorecard: Translating strategy into action (4th ed.). Harvard Business Review Press.This book introduces the balanced scorecard framework, which is a strategic planning and management system that helps organizations align their activities with their strategic goals. It provides a comprehensive guide to implementing the balanced scorecard approach, including step-by-step instructions and real-world examples.4. Johnson, H. T., & Kaplan, R. S. (2017). Relevance lost: The rise and fall of management accounting. Harvard Business Review Press.This book critically examines the current state of management accounting and its relevance in today's businessenvironment. The authors argue that traditional management accounting practices are outdated and no longer sufficient to support strategic decision-making. They propose a new approach to management accounting that is more focused on providing relevant and actionable information to decision-makers.5. Drury, C. (2018). Management and cost accounting (11th ed.). Cengage Learning.This textbook is designed to introduce students to the principles and practices of management accounting. It covers a range of topics, including cost classification, budgeting, standard costing, and performance evaluation. The author presents a clear and accessible writing style that makes the material easy to understand.6. Atkinson, A. A., Banker, R. D., Potter, G., & Srivastava, A. (2018). Management accounting (16th ed.). Prentice Hall.This book offers a comprehensive overview of managementaccounting theory and practice. It covers a wide range of topics, including cost behavior, cost-volume-profit analysis, budgeting, performance evaluation, and decision-making. The authors provide a balance of theoretical concepts and practical applications, making it a useful resource for both students and practitioners.7. Horvath, M. A. (2019). Cost management: A strategic emphasis (6th ed.). Pearson Education.This textbook focuses on the strategic aspects of cost management in organizations. It explores the role of cost management in supporting strategic decision-making, planning, and control. The author presents a range of cost management techniques and tools, including activity-based costing, target costing, and life cycle costing.8. Brownell, P. (2020). Strategic management accounting: An integrated approach. McGraw-Hill Education.This book takes a strategic approach to management accounting, emphasizing its role in supportingorganizational strategy and competitive advantage. It covers a range of topics, including strategic costing, budgeting, performance evaluation, and decision-making. The author provides a comprehensive framework for integrating management accounting into the strategic planning and management process.These references provide a diverse range of perspectives on management accounting, covering both theoretical concepts and practical applications. They are suitable for use in academic settings as well as for professionals seeking to enhance their knowledge and skills in this field.。
《管理会计(双语)》atkinson6e REVISED (10)
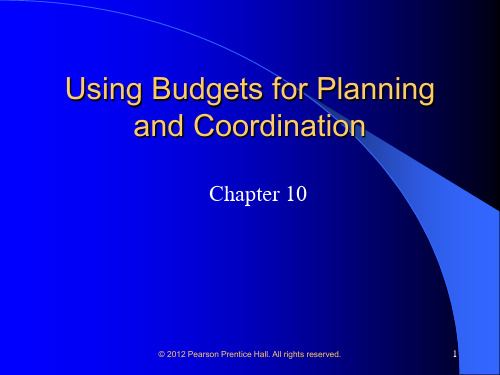
10
Operating Budgets
Labor hiring and training plan—specifies the number of people the organization must hire or release to achieve its activity objectives
– Financial budgets—identify the expected financial consequences of the activities summarized in the operating budgets
© 2012 Pearson Prentice Hall. All rights reserved.
© 2012 Pearson Prentice Hall. All rights reserved.
8
Budget Components
Two major types of budgets comprise the Master Budget:
– Operating budgets—summarize the level of activities such as sales, purchasing, and production
9
Operating Budgets
Sales plan—identifies the planned level of sales for each product
Capital spending plan—specifies the long-term capital investments that must be paid in the current budget period to meet activity objectives
《管理会计(双语)》课程 (1)

9
Behavioral Implications
As measurements are made on operations and especially on individuals and groups their behavior changes
When the measurements are used not only for information, planning, and decision-making, but also for control, evaluation, and reward, employees and managers place great pressure on the measurements themselves
– People react when they are being measured, and they react to the measurements
– They focus on the variables and behavior being measured and spend less attention on those not measured
Early 20th century – DuPont and General Motors expanded the focus to planning and control
1970’s – Japanese manufacturers developed new tools to report on quality, service, customer, and employee performance
《管理会计(双语)》章节 (7)

Management Accounting, 6e (Atkinson et al.)Chapter 7 Measuring and Managing Process PerformanceObjective 11) The theory of constraints focuses on long-term initiatives to increase operating income. Answer: FALSEExplanation: The theory of constraints maintains that operating income can be increased by carefully managing the bottlenecks in a process.Diff: 1Terms: theory of constraintsObjective: 1AACSB: Reflective thinking2) The theory of constraints:A) emphasizes long-term optimization.B) maintains that carefully managing production bottlenecks will increase operating income.C) helps managers make special one-time decisions.D) suggests that some component parts should be outsourced.Answer: BDiff: 1Terms: theory of constraintsObjective: 1AACSB: Reflective thinking3) Constraints from the theory of constraints may include:A) the availability of direct materials in manufacturing.B) linear square feet of display space for a retailer.C) direct labor in the service industry.D) All of the above are correct.Answer: DDiff: 1Terms: theory of constraintsObjective: 1AACSB: Reflective thinkingNarly Skateboards manufactures three different product lines, Base, Long, and Trick. Considerable market demand exists for all models. The following per unit data apply:4) Which model has the greatest contribution margin per unit?A) base modelB) long modelC) trick modelD) both the base model and the long modelAnswer: BExplanation: B) Base model 100-12-24-8= 56Long model 120-12-24-16=68*Trick model 140-12-48-16=64Diff: 2Terms: contribution margin, theory of constraintsObjective: 1AACSB: Analytical skills5) Which model has the greatest contribution margin per machine-hour?A) base modelB) long modelC) trick modelD) both the long model and the trick modelAnswer: AExplanation: A) Base model 56/2=28**Long model 68/4=17Trick model 64/4=16Diff: 2Terms: contribution margin, theory of constraintsObjective: 1AACSB: Analytical skills6) If there is excess capacity, which model is the most profitable to produce?A) base modelB) long modelC) trick modelD) both the base model and the long modelAnswer: BDiff: 2Terms: contribution margin, theory of constraintsObjective: 1AACSB: Analytical skills7) If there is a machine breakdown, which model is the most profitable to produce?A) base modelB) long modelC) trick modelD) both the long model and the trick modelAnswer: ADiff: 2Terms: contribution margin, theory of constraintsObjective: 1AACSB: Analytical skills8) How can the Vice-president of sales at Skate Magic encourage her salespeople to promote the more profitable model?A) Put all sales persons on salary.B) Provide higher sales commissions for higher priced items.C) Provide higher sales commissions for items with the greatest contribution margin per constrained resource.D) Provide higher sales commissions for higher priced items and items with the greatest contribution margin per constrained resource.Answer: CDiff: 2Terms: contribution margin, theory of constraintsObjective: 1AACSB: Analytical skillsObjective 21) There are two general types of facility designs: process layouts and product layouts. Answer: FALSEExplanation: There are three general types of facility designs: (1) process layouts, (2) product layouts, and (3) group technology.Diff: 1Terms: facility designsObjective: 2AACSB: Reflective thinking2) The operating costs considered by the theory of constraints are all direct manufacturing costs, including direct materials and direct labor.Answer: FALSEExplanation: The operating costs considered by the theory of constraints include all costs except for direct materials costs needed to obtain throughput production.Diff: 2Terms: operating costs, theory of constraintsObjective: 2AACSB: Reflective thinking3) The buildup of inventories decreases the cycle time of production.Answer: FALSEExplanation: The buildup of inventories increases the cycle time of productionDiff: 1Terms: cycle timeObjective: 2AACSB: Reflective thinking4) Process layouts are characterized by long production paths, high inventory levels and small batches of unique products.Answer: TRUEDiff: 1Terms: process layoutObjective: 2AACSB: Reflective thinking5) Processing cycle efficiency is calculated as processing time divided by the sum of processing time, moving time, storage time, and inspection time.Answer: TRUEDiff: 2Terms: processing cycle efficiencyObjective: 2AACSB: Reflective thinking6) In ________, all similar equipment or functions are grouped together.A) a process layoutB) a product layoutC) cellular manufacturingD) just-in-time productionAnswer: ADiff: 1Terms: process layoutObjective: 2AACSB: Reflective thinking7) Characteristics of a process layout include:A) continuous processing.B) long production paths.C) small amounts of inventory.D) no work-in-process storage areas.Answer: BDiff: 1Terms: process layoutObjective: 2AACSB: Reflective thinking8) In ________, equipment is organized to accommodate the production of a specific product.A) a process layoutB) a product layoutC) cellular manufacturingD) low-volume productionAnswer: BDiff: 1Terms: process layoutObjective: 2AACSB: Reflective thinking9) Characteristics of a product layout include:A) raw materials and purchased parts are delivered directly to the production line where they are needed.B) low-volume production.C) a U-shaped layout.D) small batches of unique products.Answer: ADiff: 1Terms: product layoutObjective: 2AACSB: Reflective thinking10) In ________, the plant is organized into areas where all machines used to manufacture a group of similar products are close to each other.A) a process layoutB) a product layoutC) cellular manufacturingD) just-in-time productionAnswer: CDiff: 1Terms: cellular manufacturingObjective: 2AACSB: Reflective thinking11) Characteristics of cellular manufacturing include:A) a layout that is usually circular like a cell.B) increasing the number of employees needed to produce a product.C) individual areas for employees so each can work independently without interruption.D) a flexible layout that can be easily adjusted to make a different product.Answer: DDiff: 1Terms: cellular manufacturingObjective: 2AACSB: Reflective thinkingVander Belt Manufacturing, Inc., is considering reorganizing its plant into manufacturing cells. The following estimates have been prepared to evaluate the benefits from the reorganization:Inventory carrying costs are estimated to be 11% per year.12) As a result of the layout reorganization, reduced levels of work-in-process inventory are projected to decrease inventory carrying costs annually by:A) $ 1,100.B) $ 3,750.C) $ 4,400.D) $5,500.Answer: AExplanation: A) (Before: $50,000 × 11%) less ( After: $40,000 × 11%) equals cost savings of $1,100.Terms: cellular manufacturingObjective: 2AACSB: Analytical skills13) As a result of the layout reorganization, incremental manufacturing costs are projected to:A) decrease by $11,400 annually.B) decrease by $12,500 annually.C) increase by $12,500 annually.D) increase by $20,000 annually.Answer: CExplanation: C) (Before: $250,000 × 40%) less (After: $375,000 × 30%) equals additional costs of $12,500Diff: 2Terms: cellular manufacturingObjective: 2AACSB: Analytical skills14) As a result of switching to a cellular manufacturing operation, total benefits are projected to increase annually by:A) $111,400.B) $113,600.C) $136,400.D) $138,600.Terms: cellular manufacturingObjective: 2AACSB: Analytical skills15) After the change, sales are projected to increase because:A) of shorter delivery lead times.B) of higher sales prices.C) of the ability to process larger batch sizes.D) All of the above are correct.Answer: ADiff: 2Terms: cellular manufacturingObjective: 2AACSB: Analytical skills16) After the change, work-in-process inventory carrying costs are projected to decrease because of:A) reduced costs in materials handling.B) lower financing costs.C) the decreased need for inventory storage.D) All of the above are correct.Answer: DDiff: 2Terms: cellular manufacturing, carrying costsObjective: 2AACSB: Analytical skills17) Carey Manufacturing, Inc., is considering reorganizing its plant into manufacturing cells. The following estimates have been prepared to evaluate the benefits from the reorganization:Before the change After the changeTotal annual sales $700,000 $850,000Costs as percentage of sales:Direct materials 10% 9%Direct labor 6% 4%Support costs 9% 7%Work-in-process inventory $200,000 $120,000Inventory carrying costs are estimated to be 12% per year.Required:a. Why do the layout reorganization estimates include1. a decrease in work-in-process inventory?2. a decrease in direct material costs as a percentage of sales?3. an increase in sales?b. As a result of the layout reorganization, what amount of annual change is projected1. from carrying reduced levels of work-in-process inventory?2. for incremental manufacturing costs?3. in total benefits?Answer:a.1. Layout reorganization estimates include a decrease in work-in-process inventory because cellular manufacturing streamlines production flows. When products flow immediately from one processing stage to the next, there is less build-up ofwork-in-process inventories.2. When products flow immediately from one processing stage to the next, workers downstream can identify an upstream problem in that component almostimmediately and correct it before it leads to the production of more defective components. Early detection of defective units reduces the amount of raw materials needed for rework, which results in decreased direct material costs as a percentage of sales.3. A streamlined manufacturing operation leads to reduced manufacturing cycle times, improved quality, and a shorter lead-time for orders. Quicker delivery to customersand higher quality products usually result in increased customer sales.b.1. Carrying reduced levels of work-in-process inventory results in a projected cost savings of $9,600.Before the change: $200,000 × 12% = $24,000After the change: $120,000 × 12% = 14,400Cost savings per year $ 9,6002. As a result of the layout reorganization, incremental manufacturing costs are projected to decrease by $5,000.Before the change: $700,000 × 25% =$175,000After the change: $850,000 × 20% =170,000Cost savings per year $ 5,0003. As a result of switching to a cellular manufacturing operation, total benefits are projected to increase by $164,600 per year.Before the After theChange Change Difference Sales $700,000 $850,000 $150,000Manufacturing costs* (175,000) (170,000) 5,000WIP inventory carrying costs** (24,000) (14,400) 9,600 Total benefits per year $501,000 $665,600 $164,600 * Before the change: $700,000 × (10% + 6% + 9%) = $175,000After the change: $850,000 × (9% + 4% + 7%) = $170,000** Before the change: $200,000 × 12% = $24,000After the change: $120,000 × 12% = $14,400Diff: 3Terms: cellular manufacturingObjective: 2AACSB: Analytical skillsMAL: This question is not available in MyAccountingLab.18) Explain the differences between a process layout, a product layout, and cellular manufacturing.Answer: In process layouts, all similar equipment and functions are grouped together. Process layouts occur typically in organizations in which production is done in small batches of unique products. In process layouts, products are moved and processed from one area to another until the product is completed. It is also characterized by a long production path and high work-in-process inventories.In contrast, in product layouts, equipment is organized to accommodate the production of a specific product. Product layouts are most effective for companies producing high-volume products. Typically products are moved and are processed along an assembly line. The placement of equipment of processing units is made to reduce the distance that products travel. Meanwhile, cellular manufacturing involves the organization of a plant into a number of cells. Within each cell, machines that are needed to manufacture a group of similar products are arranged close to one another. The organization reduces production cycle time, which is the time from receipt of raw materials from the supplier to delivery of the finished goods to the customers and distributors.Diff: 2Terms: process layout, product layout, cellular manufacturingObjective: 2AACSB: Reflective thinkingMAL: This question is not available in MyAccountingLab.Objective 31) Value is defined as any action or process for which a customer would be willing to pay. Answer: TRUEDiff: 1Terms: lean manufacturing, valueObjective: 3AACSB: Reflective thinking2) In lean manufacturing, any resource spending that does not create value for the end customer is wasteful and must be eliminated.Answer: TRUEDiff: 1Terms: lean manufacturingObjective: 3AACSB: Reflective thinking3) The quality movement was pioneered by:A) Eli Whitney.B) Henry Ford.C) Edwards Deming.D) Frederick Taylor.Answer: CDiff: 1Terms: lean manufacturingObjective: 3AACSB: Reflective thinking4) Lean manufacturing:A) has a central philosophy that resource spending that does not add value must be eliminated.B) defines value as any action or process for which the customer is willing to pay.C) is derived from the Toyota Production System.D) All of the above are correct.Answer: DDiff: 1Terms: lean manufacturing, just-in-timeObjective: 3AACSB: Reflective thinkingObjective 41) Global competition led to the development of international quality standards such as ISO 9000 Standards.Answer: TRUEDiff: 1Terms: ISO 9000Objective: 4AACSB: Reflective thinking2) Quality engineering costs are an example of:A) prevention costs.B) appraisal costs.C) internal failure costs.D) external failure costs.Answer: ADiff: 1Terms: prevention costsObjective: 4AACSB: Reflective thinking3) Inspection costs of purchased parts and materials are examples of:A) prevention costs.B) appraisal costs.C) internal failure costs.D) external failure costs.Answer: BDiff: 1Terms: appraisal costsObjective: 4AACSB: Reflective thinking4) The cost of reworking defective components is an example of:A) prevention costs.B) appraisal costs.C) internal failure costs.D) external failure costs.Answer: CDiff: 1Terms: internal failure costsObjective: 4AACSB: Reflective thinking5) Warranty costs are an example of:A) prevention costs.B) appraisal costs.C) internal failure costs.D) external failure costs.Answer: DDiff: 1Terms: external failure costsObjective: 4AACSB: Reflective thinking6) ________ include the cost of raw-materials inspections and assembly-line inspections.A) Prevention costsB) Appraisal costsC) Internal failure costsD) External failure costsAnswer: BDiff: 1Terms: appraisal costsObjective: 4AACSB: Reflective thinking7) Distinguish between internal failure costs and external failure costs. Give examples of each. Answer: Internal failure costs and external failure costs are both costs of quality. Internal failure costs result when defects are discovered before the product ships to the customer. The cost to rework the product are internal failure costs. Other examples are the cost of downtime, waste, and net scrap cost. External failure costs result when the customer discovers the defect. The costs of correcting the defect include warranty, repair, and service costs, product liability recalls, product liability lawsuits, and product returns.Diff: 1Terms: internal failure costs, external failure costsObjective: 4AACSB: Reflective thinkingMAL: This question is not available in MyAccountingLab.Objective 51) A processing cycle efficiency (PCE) of 14% indicates better efficiency than a PCE of 50%. Answer: FALSEExplanation: A processing cycle efficiency (PCE) of 14% indicates poorer efficiency than a PCE of 50%.Diff: 2Terms: processing cycle efficiencyObjective: 5AACSB: Reflective thinking2) When using a just-in-time manufacturing, a problem anywhere in the system can stop all production.Answer: TRUEDiff: 1Terms: just-in-time manufacturingObjective: 5AACSB: Reflective thinking3) Implementing a just-in-time manufacturing system requires a major cultural change for an organization.Answer: TRUEDiff: 1Terms: just-in-time manufacturingObjective: 5AACSB: Reflective thinking4) High levels of inventory result in all EXCEPT:A) high moving, handling, and storage costs.B) increased product obsolescence and damage.C) increased financing costs.D) idle facilities.Answer: DDiff: 1Terms: idle facilitiesObjective: 5AACSB: Reflective thinking5) The implementation of just-in-time production results in all of the following EXCEPT:A) decreased cycle times.B) reduced amount of waste.C) a slower pace for employees.D) structural changes.Answer: CDiff: 1Terms: just-in-timeObjective: 5AACSB: Reflective thinking6) Characteristics of just-in-time manufacturing include all of the following EXCEPT:A) the ability to process items in large batches.B) making a product only when the customer requires it.C) no work-in-process inventories.D) a problem anywhere can stop production.Answer: ADiff: 1Terms: just-in-timeObjective: 5AACSB: Reflective thinking7) Measures of JIT (just-in-time) manufacturing reliability include all of the following EXCEPT:A) defect rates.B) labor and machine utilization ratios.C) cycle times.D) percent of on-time deliveries.Answer: BDiff: 1Terms: just-in-timeObjective: 5AACSB: Reflective thinking8) A motorcycle manufacturer is currently using a conventional processing system. Recently work-in-process inventory has been piling up at two stations along the assembly line. To eliminate this problem, management discussed the possibility of implementing just-in-time manufacturing. Discuss the advantages and concerns of implementing JIT.Answer: The advantages of implementing just-in-time manufacturing include fewerwork-in-process inventories, which generally result in reduced cycle time, improved product quality, and reduced material waste and rework costs, increased sales, and decreased carrying cost-of-work-in-process inventories.Concerns include establishing and maintaining good relations with reliable suppliers and the structural and cultural change in the work environment.Diff: 1Terms: just-in-time manufacturingObjective: 5AACSB: Reflective thinkingMAL: This question is not available in MyAccountingLab.9) In a just-in-time management system, explaina. why suppliers become very important to the overall manufacturing process, andb. what incentives can be offered to reward good suppliers.Answer:a. In a just-in-time inventory system, suppliers are very important because if good quality raw materials are not delivered in a timely manner, the entire processing system will shut down.b. Incentives that can be offered to reward good suppliers include prompt payment and guaranteed total purchase volume contracts to purchase fixed amounts over a certain period of time.Diff: 1Terms: just-in-time manufacturingObjective: 5AACSB: Reflective thinkingMAL: This question is not available in MyAccountingLab.10) Why is a cost-of-quality report useful?Answer: 1) It illustrates the financial magnitude of quality factors; 2) it helps managers set priorities for the quality issues and problems they should address; 3) it allows managers to see the big picture of quality issues; and 4) it allows managers to try to find the root causes of their quality problems.Diff: 2Terms: cost-of-qualityObjective: 5AACSB: Reflective thinkingMAL: This question is not available in MyAccountingLab.11) Discuss cost reductions that can result from reducing work-in-process inventory. Answer: Decreasing work-in-process inventory results in reduced financing costs, decreased storage and handling costs, and increased sales due to faster manufacturing cycle times and shorter lead-time for orders.Diff: 1Terms: work-in-process, just-in-timeObjective: 5AACSB: Reflective thinkingMAL: This question is not available in MyAccountingLab.Objective 61) Under kaizen costing, cost reduction targets are set and applied monthly and continuous improvement (kaizen) methods are applied all year long to meet targets.Answer: TRUEDiff: 2Terms: kaizen costingObjective: 6AACSB: Reflective thinking2) Under traditional costing, supervisors and engineers are assumed to have superior knowledge about how to improve processes because they actually work with the manufacturing processes used to produce products.Answer: FALSEExplanation: Under kaizen costing, workers are assumed to have superior knowledge about how to improve processes because they actually work with the manufacturing processes used to produce products.Diff: 1Terms: kaizen costingObjective: 6AACSB: Reflective thinking3) The goal of standard costing is to reduce costs through small, incremental changes. Answer: FALSEExplanation: The goal of kaizen costing is to reduce costs through small, incremental changes. Diff: 1Terms: kaizen costingObjective: 6AACSB: Reflective thinking4) Kaizen costing assumes engineers and managers possess the best knowledge to improve processes and reduce costs.Answer: FALSEExplanation: Kaizen costing assumes workers possess the best knowledge to improve processes and reduce costs.Diff: 1Terms: kaizen costingObjective: 6AACSB: Reflective thinking5) Kaizen costing requires relevant financial results to be shared with front-line employees. Answer: TRUEDiff: 1Terms: kaizen costingObjective: 6AACSB: Reflective thinking6) Kaizen costing includes:A) cost control system concept.B) standards set annually or semiannually.C) continuous improvement.D) comparing actual costs to standard costs.Answer: CDiff: 2Terms: Kaizen costingObjective: 6AACSB: Reflective thinking7) One goal of ________ is to design costs out of products in the research, development, and engineering stage.A) cost-plus pricingB) target costingC) Kaizen costingD) traditional costingAnswer: BDiff: 1Terms: target costingObjective: 6AACSB: Reflective thinking8) ________ starts with the estimated product costs and next determines the estimated selling price.A) Standard costingB) Target costingC) Kaizen costingD) Traditional costingAnswer: DDiff: 1Terms: traditional costingObjective: 6AACSB: Reflective thinking9) ________ starts with the estimated product costs and next adds the expected profit margin.A) Cost-plus pricingB) Target costingC) Kaizen costingD) Standard costingAnswer: ADiff: 1Terms: cost-plus pricingObjective: 6AACSB: Reflective thinking10) All the statements below are true regarding Kaizen costing EXCEPT that:A) cost-variance analysis compares target Kaizen costs with actual cost reduction amounts.B) cost reductions apply to all variable costs.C) workers are assumed to have the best knowledge to improve processes and reduce costs.D) cost reduction targets are set and applied on an annual basis.Answer: DDiff: 1Terms: Kaizen costingObjective: 6AACSB: Reflective thinking11) Concerns about Kaizen costing include:A) radical process improvements.B) excessive pressures are put on employees.C) focus is on the overall system.D) grace periods may be granted.Answer: BDiff: 1Terms: Kaizen costingObjective: 6AACSB: Reflective thinking12) Standard costing includes:A) continuous improvement.B) monthly cost reduction targets.C) the assumption that workers closest to the process know best.D) goals to meet performance standards.Answer: DDiff: 2Terms: standard costingObjective: 6AACSB: Reflective thinkingDJK Enterprises are using the Kaizen approach to budgeting for 2011. The budgeted income statement for January 2011 is as follows:Under the Kaizen approach, cost of goods sold and variable operating expenses are budgeted to decline by 1% per month.13) What is the budgeted cost of goods sold for March 2011?A) $294,030B) $294,000C) $300,000D) $297,000Answer: AExplanation: A) $300,000 × 0.99 × 0.99 = $294,030Diff: 2Terms: Kaizen costingObjective: 6AACSB: Analytical skills14) What is the budgeted gross margin for March 2011?A) $196,020B) $198,000C) $204,020D) $205,970Answer: DExplanation: D) $500,000 - $294,030 = $205,970Diff: 2Terms: Kaizen costingObjective: 6AACSB: Analytical skills15) Bingington Corporation is using the Kaizen approach to budgeting for 2011. The budgeted income statement for the month ended January 31, 2011 is as follows:Sales (360,000 units) $1,080,000Less: Cost of goods sold 720,000Gross margin 360,000Operating expenses (includes $54,000 of fixed costs) 270,000Net income $ 90,000Under the Kaizen approach, cost of goods sold and variable operating expenses are budgeted to decline by 2% per month.Required:Prepare a Kaizen-based budgeted income statement for the month ended February 28, 2011. Assume sales are constant each month.Answer: Sales $1,080,000Less: Cost of goods sold ($720,000 × 0.98) 705,600Gross margin 374,400Operating expenses [($216,000 × 0.98) + $54,000] 265,680Net income $ 108,720Diff: 2Terms: Kaizen costingObjective: 6AACSB: Analytical skillsMAL: This question is not available in MyAccountingLab.16) Allscott Company is developing its budgets for 2012 and, for the first time, they will use the Kaizen approach. The initial 2012 income statement, based on static data from 2011, is as follows:Sales (140,000 units) $420,000Less: Cost of goods sold 280,000Gross margin 140,000Operating expenses (includes $28,000 of depreciation) 112,000Net income $28,000Selling prices for 2012 are expected to increase by 8%, and sales volume in units will decrease by 10%. The cost of goods sold as estimated by the Kaizen approach will decline by 10% per unit. Other than depreciation, all other operating costs are expected to decline by 5%. Required:Prepare a Kaizen-based budgeted income statement for the year ended December 31, 2012. Answer: Sales (126,000 × $3.24) $408,240Less: COGS (126,000 × $1.80) 226,800Gross margin 181,440Operating expenses ($28,000 + $79,800) 107,800Net income $ 73,640Diff: 1Terms: Kaizen costingObjective: 6AACSB: Analytical skillsMAL: This question is not available in MyAccountingLab.Objective 71) Benchmarking requires that organizational members first look to the best practices of other organizations for guidance on improving and then understand their current operations and approaches to conducting business,Answer: FALSEExplanation: Benchmarking requires that organizational members first understand their current operations and approaches to conducting business and then look to the best practices of other organizations for guidance on improving.Diff: 2Terms: benchmarkingObjective: 7AACSB: Reflective thinking。
管理会计(双语)-3

Cost of finished goods unsold sold Income statement
Inventory costs Bal. sheet
Costs of good sold
Profit statement under marginal costing
A £4.00 C £4.77 B D £4.27 £6.50
3.A company produces a single unit of product for which the variable production cost is $6 per unit. Fixed production overhead is $10000 per month. The selling price is $10 per unit. Suppose that in a particular month, production was in fact 5000units with 4800 units sold and 1200 units left in closing stock. Assume all costs were as budgeted.
CURRENT YEAR 10000000 8625000 300000 500000 575000 1000 units 160000 units 100000 units 61000 units
12000000 10800000 300000 600000 300000 1000 units 120000 units 120000 units 1000 units
Current year 100 86.25 50 15 21.25 10 11.25 5
管理会计英语英文版课件
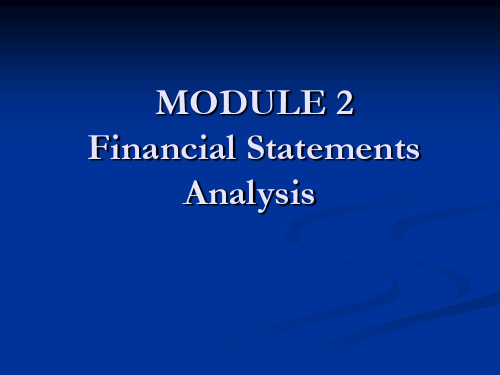
Balance Sheet
As you know, the balance sheet reports assets, liabilities, and owners’ equity at a moment in time. The income statement summarizes revenue and expense transactions that occur during a period of time. Since revenue and expense transactions affect
Ex. assume that a machine has a cost of $4,900, an economic life of five years, and an estimated residual value of $400.
Annual depreciation expense=($4,900 - $400)/
There are several commonly used methods: straight-line, units-of-production , sum-of-theyears’ digits and declining-balance.
Methods of Calcine Method
The straight-line (SL) method allocates an equal
- 1、下载文档前请自行甄别文档内容的完整性,平台不提供额外的编辑、内容补充、找答案等附加服务。
- 2、"仅部分预览"的文档,不可在线预览部分如存在完整性等问题,可反馈申请退款(可完整预览的文档不适用该条件!)。
- 3、如文档侵犯您的权益,请联系客服反馈,我们会尽快为您处理(人工客服工作时间:9:00-18:30)。
149
150
INTERNATIONAL ADVANCES IN ECONOMIC RESEARCH
An important aspect of cost management is the integration of accounting data in the strategic planning process. Strategic cost management focuses upon the role of developing and implementing internal accounting information useful in strategic planning. A cost management system must provide financial and nonfinancial data to support the strategy of the organization, and customer demands of quality, flexibility, service, and cost. Shank [1989, p. 50] defines strategic cost management as the blending of three underlying themes: value chain analysis; strategic positioning analysis; and cost driver analysis [Shank, 1989, p. 50]. Underlying the concept of strategic cost management is value chain analysis. The value chain has been defined as " . . . the linked set of value-creating activities all the way from basic raw material sources for component suppliers through the ultimate end-use product delivered into the final consumer's hands [Shank, 1989, p. 50]." The value chain broadens the traditional internal focus of managerial accounting while focusing on exploiting linkages with customers and suppliers. Creating product value encompasses quality, price, service, and other relevant factors. Knowledge of the cost structure and value chain of the organization allows examination of the major cost elements of each value added activity. Another underlying theme of strategic cost analysis is cost driver analysis [Shank, 1989]. The emphasis is on determining the causes of costs. Establishing cause and effect relationships of costs with their cost drivers provides a basis for elimination or reduction of non-value-added costs, while also providing a basis for the integration of cost information into strategic planning. Cost driver analysis can also be expanded to other activities within the organization, thereby moving away from the limited traditional cost accounting focus of inventory valuation to the broader based cost management. Numerous studies have examined the content of the management/cost accounting curriculum in the United States and Asia (for example, Lander and Reinstein; Bromwich and Wang; AnyaneNtow) to determine if educators are responding to the needs of practitioners. Generally these studies have focused on the views of accounting practitioners and/or educators concerning the importance of selected management accounting topics, or desirable knowledge and skills that should be included in the Common Body of Knowledge (CBOK) for management accounting. The results of this study provide information for educators and practitioners, in both the United States and Asia, by examining the importance and use of various management accounting practices and techniques. METHODOLOGY The purpose of this study is to examine trends in the adoption of new management accounting techniques and practices by manufacturing firms in the Asian Pacific rim region. The study involved mailing a questionnaire (in both English and Chinese to those countries with large Chinese populations) to a sample of 550 manufacturing firms in the major developing and developed economies of the Asian Pacific Region. The practices and techniques used in the survey were taken from topical coverage at recent professional conferences, and domestic and international practitioner and academic accounting journals. The questionnaire consisted of two pages and asked respondents about general demographic data, as well as the perceived importance of both traditional and "cutting edge" management accounting techniques and practices. The questionnaire also asked respondents to indicate whether various innovative practices and techniques were being currently used in their companies, and if they were not being currently used, would they be used in the near future. At the time of this writing, completed questionnaires were still being received from the respondents and a total of 41 usable responses, representing a 7.4 percent response ratio, had been received.
Trends in Management AccounIHOLLAH ~ Z A E E , JOSEPH Z. SZENDI, CONNIE SHUM, AND ROBERT C. ELMORE* INTRODUCTION The usefulness of the traditionalmanagement accounting information system has been challenged by a changing economic environment coupled with increased global competition and the emergence of new manufacturing technologies.