铸造过程的质量控制3
铸造质量控制

铸造质量控制铸造质量控制是指在铸造过程中对产品质量进行管理和控制的一系列措施。
通过合理的质量控制措施,可以确保铸造产品的尺寸精度、表面质量、力学性能等指标达到设计要求,从而提高产品的质量和可靠性。
一、质量控制的目标和意义铸造质量控制的目标是确保产品质量达到设计要求,具体包括以下几个方面:1. 尺寸精度控制:通过控制铸件的收缩和变形,保证尺寸精度在允许范围内。
2. 表面质量控制:确保铸件表面光洁度、无气孔、夹杂物等缺陷。
3. 力学性能控制:保证铸件的强度、韧性等力学性能满足要求。
4. 成本控制:通过合理的质量控制措施,降低不合格品率,减少生产成本。
质量控制的意义在于:1. 提高产品质量:通过严格的质量控制,确保产品达到设计要求,提高产品的质量和可靠性。
2. 降低生产成本:通过减少废品率、减少返工率等手段,降低生产成本。
3. 提高企业竞争力:优质的产品能够提高企业的竞争力,赢得更多的市场份额。
二、质量控制的主要内容和方法1. 原材料控制:选择合适的原材料,确保其质量符合要求。
对原材料进行化学成分分析、物理性能测试等,确保铸件的化学成分和机械性能满足要求。
2. 铸型制备控制:控制铸型的制备工艺,确保铸型的密实性、耐火性等性能,避免铸型砂中的气孔、夹杂物等缺陷。
3. 浇注工艺控制:控制浇注温度、浇注速度、浇注时间等参数,确保熔融金属在铸型中充分填充,避免铸件出现冷隔、缩松等缺陷。
4. 熔炼工艺控制:控制熔炼温度、炉渣成分等参数,确保熔融金属的化学成分和纯净度符合要求。
5. 热处理工艺控制:对铸件进行热处理,提高其力学性能。
控制热处理温度、保温时间等参数,确保铸件的组织结构和性能达到设计要求。
6. 检测与检验:通过无损检测、化学成分分析、力学性能测试等手段,对铸件进行质量检测和检验,确保产品质量符合要求。
7. 过程控制:建立合理的工艺流程和操作规程,对每个工序进行严格控制,确保每一道工序的质量稳定可靠。
三、质量控制的指标和标准1. 尺寸精度指标:包括线性尺寸公差、平面度、垂直度等指标,根据产品设计要求和使用要求进行控制。
铸造工艺流程的质量控制方法
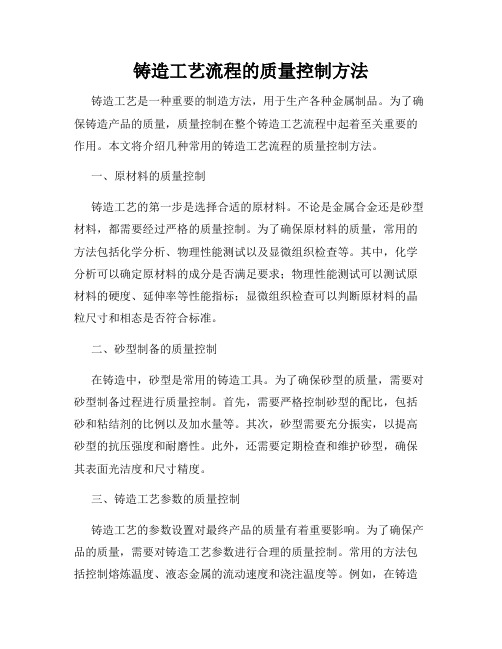
铸造工艺流程的质量控制方法铸造工艺是一种重要的制造方法,用于生产各种金属制品。
为了确保铸造产品的质量,质量控制在整个铸造工艺流程中起着至关重要的作用。
本文将介绍几种常用的铸造工艺流程的质量控制方法。
一、原材料的质量控制铸造工艺的第一步是选择合适的原材料。
不论是金属合金还是砂型材料,都需要经过严格的质量控制。
为了确保原材料的质量,常用的方法包括化学分析、物理性能测试以及显微组织检查等。
其中,化学分析可以确定原材料的成分是否满足要求;物理性能测试可以测试原材料的硬度、延伸率等性能指标;显微组织检查可以判断原材料的晶粒尺寸和相态是否符合标准。
二、砂型制备的质量控制在铸造中,砂型是常用的铸造工具。
为了确保砂型的质量,需要对砂型制备过程进行质量控制。
首先,需要严格控制砂型的配比,包括砂和粘结剂的比例以及加水量等。
其次,砂型需要充分振实,以提高砂型的抗压强度和耐磨性。
此外,还需要定期检查和维护砂型,确保其表面光洁度和尺寸精度。
三、铸造工艺参数的质量控制铸造工艺的参数设置对最终产品的质量有着重要影响。
为了确保产品的质量,需要对铸造工艺参数进行合理的质量控制。
常用的方法包括控制熔炼温度、液态金属的流动速度和浇注温度等。
例如,在铸造过程中,如果熔炼温度过高,易导致铸件内部存在气孔和夹杂物;如果浇注温度过低,易导致铸件的收缩缺陷。
因此,合理控制这些参数可以有效提高铸件的质量。
四、铸造产品的检测与测试在铸造工艺流程中,对铸造产品进行质量检测和测试是不可或缺的环节。
常用的方法包括无损检测、机械性能测试以及尺寸测量等。
其中,无损检测可以通过X射线、超声波等方法检测产品是否存在缺陷;机械性能测试可以测试产品的抗拉强度、硬度等力学性能;尺寸测量则可以验证产品的尺寸精度是否符合要求。
五、质量记录与反馈为了总结经验并改进铸造工艺流程,需要对质量进行记录和反馈。
对于每个铸造批次,应该记录原材料、砂型、工艺参数以及产品质量等关键信息。
铸造质量控制

铸造质量控制1、铸造过程控制铸造过程控制是铸造质量控制的核心,它包括原料控制、工艺控制、设备控制等方面。
其中,工艺控制是最为重要的环节,需要制定详细的工艺控制文件,如作业指导书等。
作业指导书是铸造过程控制的重要文件,必须保证其准确、完整、具体、规范,避免“两张皮”和不协调现象的出现。
2、铸件产品质量控制铸件产品质量控制是指铸件产品在使用过程中所表现出的性能和质量水平,是评价铸造质量的基本指标。
为了保证铸件产品质量,需要从铸造过程控制入手,采取措施提高铸造过程的稳定性、耐用性和工艺性等指标,确保铸件在使用条件下的可靠性。
3、质量控制要点制定作业指导书是铸造质量控制的重要环节,需要注重以下问题:将生产工人的经验和技巧总结进去,与工序质量分析表相呼应,要求内容完整准确、详细具体,避免出现“见某某文件”等现象。
此外,还需要加强铸造过程控制,包括原料控制、工艺控制、设备控制等方面,提高铸造过程的稳定性和可靠性,保证铸件产品质量。
我们采用的改进方法有很多种,如QC、8D、六西格玛等等。
这些方法都是基于PDCA循环的过程,旨在持续改进项目。
我们可以从质量例会、新产品开发阶段异常检讨会议、产品审核、过程审核、内外部体系审核、检验中的异常现象、生产会议、设备会议、成本会议、年度报告、年度持续改进计划、提案、客诉等过程中提出的各项问题中,发现需要改进的方面。
同时,生产过程中遇到的各种问题也需要被纳入改进范畴。
需要强调的是,QC、8D、六西格玛的思路基本上是一致的,不同之处在于使用的工具不同。
这些改进方法并没有万能的钥匙,只有选择最合适的工具才能达到改进目标。
当然,我们也要避免死板的套用。
铸造质量控制
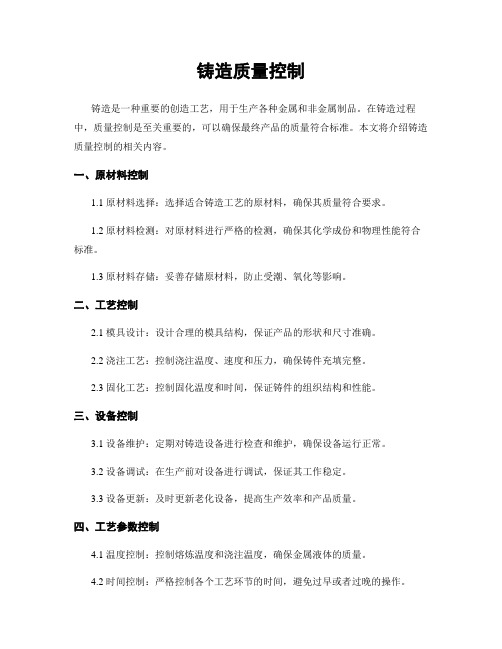
铸造质量控制铸造是一种重要的创造工艺,用于生产各种金属和非金属制品。
在铸造过程中,质量控制是至关重要的,可以确保最终产品的质量符合标准。
本文将介绍铸造质量控制的相关内容。
一、原材料控制1.1 原材料选择:选择适合铸造工艺的原材料,确保其质量符合要求。
1.2 原材料检测:对原材料进行严格的检测,确保其化学成份和物理性能符合标准。
1.3 原材料存储:妥善存储原材料,防止受潮、氧化等影响。
二、工艺控制2.1 模具设计:设计合理的模具结构,保证产品的形状和尺寸准确。
2.2 浇注工艺:控制浇注温度、速度和压力,确保铸件充填完整。
2.3 固化工艺:控制固化温度和时间,保证铸件的组织结构和性能。
三、设备控制3.1 设备维护:定期对铸造设备进行检查和维护,确保设备运行正常。
3.2 设备调试:在生产前对设备进行调试,保证其工作稳定。
3.3 设备更新:及时更新老化设备,提高生产效率和产品质量。
四、工艺参数控制4.1 温度控制:控制熔炼温度和浇注温度,确保金属液体的质量。
4.2 时间控制:严格控制各个工艺环节的时间,避免过早或者过晚的操作。
4.3 压力控制:根据产品要求控制浇注压力,确保铸件的密度和强度。
五、质量检验控制5.1 外观检验:对铸件的表面质量进行检查,包括气孔、裂纹等缺陷。
5.2 尺寸检验:测量铸件的尺寸和几何形状,确保符合设计要求。
5.3 化学成份检验:对铸件的化学成份进行分析,确保符合标准。
综上所述,铸造质量控制是确保铸件质量的关键环节,需要在原材料、工艺、设备、工艺参数和质量检验等方面进行全面控制。
惟独做好质量控制,才干生产出满足客户需求的优质铸件。
铸件质量控制计划
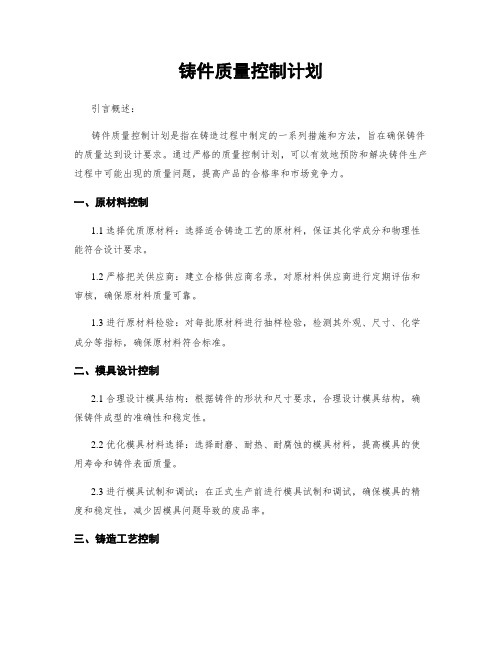
铸件质量控制计划引言概述:铸件质量控制计划是指在铸造过程中制定的一系列措施和方法,旨在确保铸件的质量达到设计要求。
通过严格的质量控制计划,可以有效地预防和解决铸件生产过程中可能出现的质量问题,提高产品的合格率和市场竞争力。
一、原材料控制1.1 选择优质原材料:选择适合铸造工艺的原材料,保证其化学成分和物理性能符合设计要求。
1.2 严格把关供应商:建立合格供应商名录,对原材料供应商进行定期评估和审核,确保原材料质量可靠。
1.3 进行原材料检验:对每批原材料进行抽样检验,检测其外观、尺寸、化学成分等指标,确保原材料符合标准。
二、模具设计控制2.1 合理设计模具结构:根据铸件的形状和尺寸要求,合理设计模具结构,确保铸件成型的准确性和稳定性。
2.2 优化模具材料选择:选择耐磨、耐热、耐腐蚀的模具材料,提高模具的使用寿命和铸件表面质量。
2.3 进行模具试制和调试:在正式生产前进行模具试制和调试,确保模具的精度和稳定性,减少因模具问题导致的废品率。
三、铸造工艺控制3.1 严格控制浇注温度:根据铸件材料和结构要求,控制浇注温度,避免因温度过高或过低导致铸件缺陷。
3.2 控制浇注速度和压力:合理控制浇注速度和压力,确保铸件充型充实,避免气孔和夹杂等缺陷。
3.3 采取适当的冷却措施:在铸造结束后,采取合适的冷却措施,避免因快速冷却或过慢冷却导致铸件内部应力过大。
四、热处理控制4.1 选择合适的热处理工艺:根据铸件的材料和使用要求,选择适合的热处理工艺,提高铸件的强度和硬度。
4.2 严格控制热处理参数:在热处理过程中,严格控制温度、时间和冷却速度等参数,确保热处理效果稳定可靠。
4.3 进行热处理质量检验:对热处理后的铸件进行硬度测试、金相分析等检验,确保热处理效果符合设计要求。
五、表面处理控制5.1 选择适合的表面处理方法:根据铸件的用途和要求,选择合适的表面处理方法,提高铸件的耐腐蚀性和美观度。
5.2 严格控制表面处理工艺:在表面处理过程中,严格控制处理时间、温度和液体浓度等参数,确保表面处理效果均匀一致。
铸造生产过程质量控制点
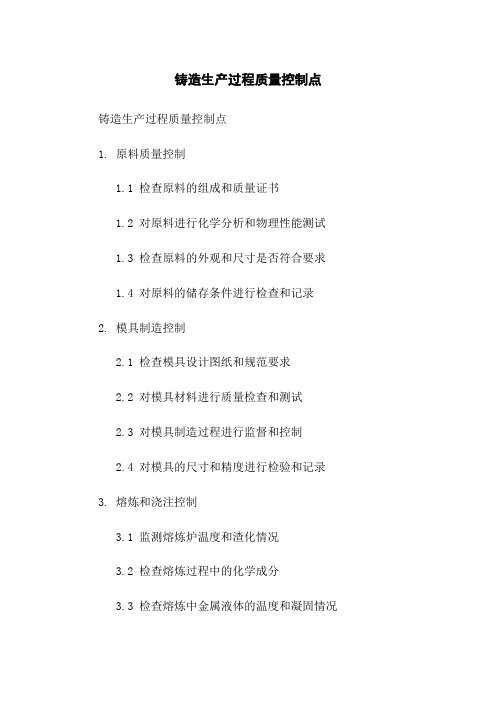
铸造生产过程质量控制点铸造生产过程质量控制点1. 原料质量控制1.1 检查原料的组成和质量证书1.2 对原料进行化学分析和物理性能测试 1.3 检查原料的外观和尺寸是否符合要求1.4 对原料的储存条件进行检查和记录2. 模具制造控制2.1 检查模具设计图纸和规范要求2.2 对模具材料进行质量检查和测试2.3 对模具制造过程进行监督和控制2.4 对模具的尺寸和精度进行检验和记录3. 熔炼和浇注控制3.1 监测熔炼炉温度和渣化情况3.2 检查熔炼过程中的化学成分3.3 检查熔炼中金属液体的温度和凝固情况3.4 对铸件的浇注过程进行监控和记录4. 铸造件外观和尺寸控制4.1 对铸件外观进行目测和检验4.2 使用光谱仪和显微镜对铸件进行化学成分和微观结构的分析4.3 使用激光扫描仪等设备对铸件的尺寸进行测量和记录4.4 对铸件进行外观和尺寸的合格判定5. 热处理控制5.1 对铸件进行退火、正火、淬火等热处理工艺的控制5.2 监测热处理过程中的温度和时间5.3 对热处理后的铸件进行硬度测试和金相分析5.4 对热处理后的铸件进行尺寸和外观的检验和记录6. 特殊工艺控制6.1 对特殊工艺参数进行监控和调整6.2 对特殊工艺工序进行质量检查和控制6.3 对特殊工艺产品的性能进行测试和验证附件:1. 铸造原料的质量证书样本2. 模具设计图纸和规范要求范本3. 铸造工艺流程图4. 铸造件外观和尺寸检验记录表5. 热处理工艺参数记录表6. 特殊工艺工序质量检查表法律名词及注释:1. 质量证书:指由生产厂商或供应商提供的证明原料质量合格的文件。
2. 模具设计图纸:指铸造过程中用于指导模具制造的图纸和规范要求。
3. 化学成分:指铸件材料中各元素的含量。
4. 光谱仪:用于分析金属材料化学成分和物理性能的仪器。
5. 显微镜:用于观察和分析铸件的微观结构和缺陷的仪器。
6. 激光扫描仪:用于测量和记录铸件尺寸的仪器。
7. 退火:指通过加热和冷却的方式改变金属材料的组织结构和性能的工艺。
铸造质量控制
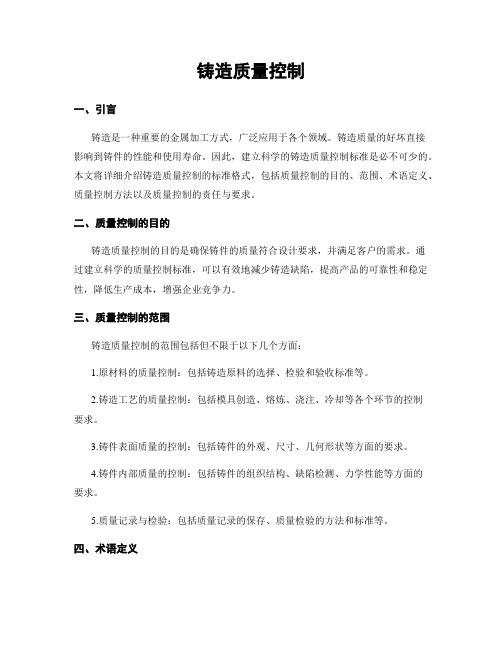
铸造质量控制一、引言铸造是一种重要的金属加工方式,广泛应用于各个领域。
铸造质量的好坏直接影响到铸件的性能和使用寿命。
因此,建立科学的铸造质量控制标准是必不可少的。
本文将详细介绍铸造质量控制的标准格式,包括质量控制的目的、范围、术语定义、质量控制方法以及质量控制的责任与要求。
二、质量控制的目的铸造质量控制的目的是确保铸件的质量符合设计要求,并满足客户的需求。
通过建立科学的质量控制标准,可以有效地减少铸造缺陷,提高产品的可靠性和稳定性,降低生产成本,增强企业竞争力。
三、质量控制的范围铸造质量控制的范围包括但不限于以下几个方面:1.原材料的质量控制:包括铸造原料的选择、检验和验收标准等。
2.铸造工艺的质量控制:包括模具创造、熔炼、浇注、冷却等各个环节的控制要求。
3.铸件表面质量的控制:包括铸件的外观、尺寸、几何形状等方面的要求。
4.铸件内部质量的控制:包括铸件的组织结构、缺陷检测、力学性能等方面的要求。
5.质量记录与检验:包括质量记录的保存、质量检验的方法和标准等。
四、术语定义1.铸造缺陷:指在铸造过程中产生的不符合设计要求的缺陷,如气孔、夹杂、砂眼等。
2.模具:用于创造铸件形状的工具,可以是金属模具、砂型、蜡模等。
3.熔炼:将金属原料加热至液态,并进行铸造准备的过程。
4.浇注:将熔融金属倒入模具中,使其冷却凝固成型的过程。
5.冷却:铸件在浇注后,通过自然冷却或者其他冷却方式使其降温凝固的过程。
五、质量控制方法1.原材料的质量控制方法:(1)选择合适的原材料供应商,并建立长期稳定的合作关系。
(2)对原材料进行严格的检验,包括外观、化学成份、物理性能等指标。
(3)制定原材料验收标准,明确合格和不合格的判定标准。
2.铸造工艺的质量控制方法:(1)制定详细的工艺流程和作业指导书,明确每一个环节的工艺参数和操作要求。
(2)对模具进行定期检查和维护,确保其精度和使用寿命。
(3)严格控制熔炼过程中的温度、时间、搅拌等参数,确保金属液的质量。
铸造质量控制

铸造质量控制一、概述铸造质量控制是指通过一系列的措施和方法,确保铸造件在制造过程中达到预期的质量要求。
本文将从铸造工艺、质量控制方法和质量控制指标三个方面详细介绍铸造质量控制的标准格式文本。
二、铸造工艺1. 铸型制备:铸造件的质量直接受到铸型的影响,因此应根据铸造件的形状、尺寸和材料特性,选择合适的铸型材料和制备工艺。
铸型制备应符合相关标准和规范,确保铸型的精度和表面质量。
2. 熔炼与浇注:熔炼是铸造过程中的关键环节,应严格控制熔炼温度、熔炼时间和熔炼材料的质量。
浇注过程中,应注意铸液的温度控制、浇注速度和浇注方式,以避免铸造缺陷的产生。
3. 凝固与冷却:凝固过程是铸造件形成的关键阶段,应根据铸件的结构特点和材料性能,合理控制凝固速度和冷却方式,以获得理想的组织结构和性能。
4. 除砂与清洁:铸件出模后,应进行除砂和清洁工作,以去除铸件表面的砂粒和杂质,确保铸件的表面光洁度和尺寸精度。
三、质量控制方法1. 工艺参数控制:通过对铸造工艺参数的控制,如熔炼温度、浇注速度、凝固时间等,来影响铸件的质量。
可以通过设定合理的参数范围、监测和调整参数数值,以达到质量控制的目的。
2. 检测与检验:采用合适的检测与检验方法,对铸件的尺寸、形状、组织结构和性能进行评估。
常用的检测方法包括尺寸测量、金相分析、硬度测试、无损检测等。
3. 过程监控:通过实时监测铸造过程中的关键参数和指标,如铸液温度、浇注速度、凝固时间等,及时发现异常情况并采取相应措施,以确保铸件的质量稳定。
4. 环境管理:铸造过程中的环境条件对铸件的质量也有一定影响。
应通过控制环境温度、湿度和灰尘等因素,来减少外界环境对铸件质量的影响。
四、质量控制指标1. 尺寸精度:铸件的尺寸精度是衡量其质量的重要指标之一。
应根据铸件的设计要求和使用环境,制定合理的尺寸公差,并通过尺寸测量和检验来评估尺寸精度。
2. 表面质量:铸件的表面质量直接影响其外观和使用寿命。
应通过除砂、清洁和表面处理等措施,确保铸件表面的光洁度和无裂纹、气孔等缺陷。
- 1、下载文档前请自行甄别文档内容的完整性,平台不提供额外的编辑、内容补充、找答案等附加服务。
- 2、"仅部分预览"的文档,不可在线预览部分如存在完整性等问题,可反馈申请退款(可完整预览的文档不适用该条件!)。
- 3、如文档侵犯您的权益,请联系客服反馈,我们会尽快为您处理(人工客服工作时间:9:00-18:30)。
铸造过程的质量控制
铸造是我们通过熔炼金属,制造铸型,并将熔炼金属液浇入铸型,凝固后获得具有一定形状、尺寸和性能金属零件毛坯的成型方法。
我们制造成型的金属零件毛坯铸件,在许多领域已成为重要构件,并占有一定的比例。
在汽车制动配件、减速机箱体、阀门配件、管道修配件、电梯配件是我们的主导产品。
铸造过程质量是从原材料进厂到合格铸件出厂的铸造全过程质量,它包括铸造过程中每一个生产环节的质量,如原材料的质量、铸造工艺装备的质量、型砂芯砂的配制质量、造型制芯与合箱的质量、熔炼与浇注的质量、落砂清理与后期处理的质量等。
铸造原材料质量是保证铸件质量的先决条件,通过原材料进厂检验,获得合格的原材料和外购件。
铸造用造型原材料:新砂应符合GB/T9442标准要求;膨润土应符合JB/T9227标准要求;煤粉应符合JB/T9222标准要求。
铸造用熔炼原材料:铸造用生铁应符合GB/T718;球墨铸铁用生铁应符合GB/T1412标准要求;废钢铁应符合GB4223标准要求。
几十年的经验告诉我们,这对保证铸件材质质量特别重要。
每批原材料必须经化验确认合格后,方可交付车间使用,不经检验的原材料不准卸车。
化验不合格的原材料不准使用,并隔离存放予以退货处理。
铸造工艺装备的质量优劣,直接影响到铸件毛坯的质量,是生产合格毛坯铸件的关键。
依据模样图、制模工艺规程、模样技术要求和标准,对模具、芯盒和砂箱的材料、尺寸、结构及技术要求进行控制验收,有效地保证铸件的毛坯形状公差。
型砂的配制质量,其性能是否符合要求,也直接影响铸件质量。
为了获得优质铸件,对型砂性能予以控制:①具有良好的成形性,包括良好的流动性、可塑性韧性和不粘模性;②足够的强度,包括常温湿强度、硬度和高温强度;③一定的透气性、较小的吸湿性,较低的发气量;④较高的耐火度,较好的热化学稳定性,较小的膨胀率与收缩率;⑤较好的退让性、溃散性和耐用性。
我们通过每小时对型砂含水量、湿透气性、湿压强度、紧实率检测一次,有效控制了型砂的性能。
芯砂的质量要求同型砂的质量要求基本相同,通常,根据芯砂类型不同,其检验项目与检验方法亦不同。
树脂自硬砂通过对其可使用时间、流动性和强度的检测,保证了树脂自硬砂的性能;通过对树脂砂型涂料物理性能、工艺性能、工作性能和流变特性的质量控制,降低了树脂沙铸件表面粗糙度值、防止或减少铸件粘砂缺陷、提高了铸件落砂和清整效率。
造型前应对模具等工艺装备的精度进行检查,不符合要求的模具和砂箱,不准使用。
造型操作人员严格按造型工艺规程操作,定时对砂型硬度、尺寸和形状进行检查,不符合要求的砂型,要予以损坏不准下芯合箱。
制芯前应对芯盒等工艺装备的精度进行检查,不符合要求的芯盒不准使用。
严格按照制芯工艺规程、烘干或硬化规范操作,对砂芯强度、刚度、排气、尺寸和形状进行检查,不符合要求的芯子不准使用。
下芯子时,要检查砂芯间及砂芯与砂型的相对位置和配合间隙、芯头紧固、砂箱定位以及出气孔和排气道等。
依据作业指导书和工艺规程,通过目视、手感对合箱质量进行检查,并对零件号、金属液牌号进行标识。
熔炼前的正确备料与配料,不仅可以减少废品,保证铸件质量,还可以降低炉料的消耗。
开炉前操作人员依据原材料标准、理化检验报告单,对炉料目视检
查,严格依据熔炼配料单的规定配料称重,并试算化学成分的含量。
操作者依据熔炼工艺规程,每包次用电热偶测温仪测量炉内铁水温度,用炉前快速分析仪检验铁液的碳、硅含量。
当化学成分或温度不确定时,即刻再取样进行快速光谱分析复检,并及时调整成分和铁水温度;金相检验员依据工艺规程,对每包次金相组织,采用快速金相显微镜进行检验。
通过检验,保证出炉铁水的化学成分、金相组织和温度符合技术条件规定的要求。
浇注工艺是否合理、浇注工作组织的好坏,都直接影响铸件的质量,有些铸件产生的缺陷许多与浇注的质量有关。
为了获得质量良好的铸件,根据铸件的牌号、铸件的重量和壁厚以及结构复杂程度等因素,来确定和重点控制适宜的浇注温度和浇注速度。
浇注温度对铸件质量影响较大,浇注温度的高低,是根据具体情况来控制,总的原则是在保证铸件成型的前提下,浇注温度越低越好。
一般情况下,金属液粘度大的、铸件重量小、壁薄、结构复杂的,浇注温度应高些;反之,则应低些。
每包铁水浇注过程中,由专人对浇注温度进行测量记录。
浇注速度在一定程度上是靠浇铸工人的操作来控制,总的原则是浇注速度不能太快也不能太慢,是根据铸件的具体情况来定。
对薄壁铸件和结构复杂的铸件,采用快速浇注,避免浇不到;铸件有较大的上平面也要采取快速浇注,避免铸型上平面受高温烘烤作用而起皮,导致铸件产生夹砂;反之,形状简单的厚实铸件,要采取慢速浇注。
根据铸件的不同情况,车间检验人员用计时器对每个铸型的浇注速度检查,浇注速度要符合工艺文件的规定。
铸件落砂除芯的控制重点是铸件的出型温度,是为了保证铸件在落砂除芯时有足够的强度和韧性。
铸件的出炉温度,是通过铸件在型内的冷却时间控制的,其冷却时间与铸件的重量、壁厚、复杂程度、牌号、铸型性质和生产条件等因素有关。
一般铸铁件为300-500℃;易产生冷裂和变形的铸铁件为200-300℃;易产生热裂的铸铁件为800-900℃,且开箱后应立即去除浇冒口和砂芯,再用热砂覆盖缓慢冷却。
按铸件重量在型内的冷却时间为5-10KG冷却10-15min、10-30KG 冷却12-30min、30-50KG冷却20-50min、50-100KG冷却30-70min、
100-250KG冷却40-90min.
铸件清理质量的控制重点是保证铸件外表面平整光洁,内腔干净,并且应以不影响机械加工的定位和零件的装配以及外表美观为原则;铸件非加工表面和机械加工基准面上的内浇道残留量、飞边毛刺等应打磨至与铸件表面平齐,加工表面上所有残留量应符合允许范围。
李自红。