铸造质量控制
铸造生产过程的质量控制
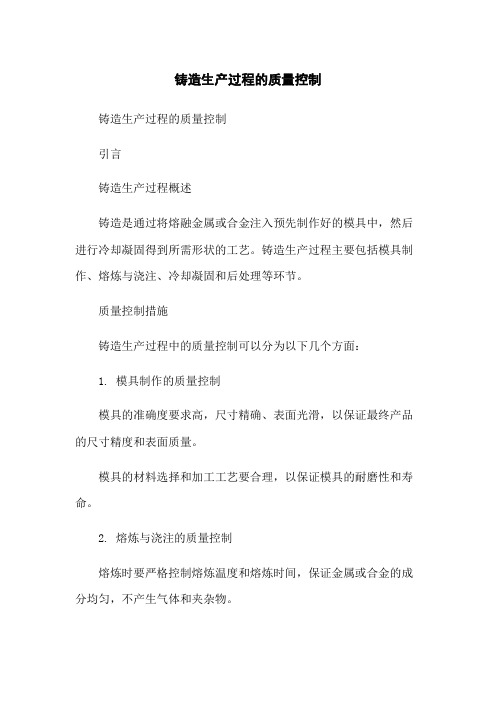
铸造生产过程的质量控制铸造生产过程的质量控制引言铸造生产过程概述铸造是通过将熔融金属或合金注入预先制作好的模具中,然后进行冷却凝固得到所需形状的工艺。
铸造生产过程主要包括模具制作、熔炼与浇注、冷却凝固和后处理等环节。
质量控制措施铸造生产过程中的质量控制可以分为以下几个方面:1. 模具制作的质量控制模具的准确度要求高,尺寸精确、表面光滑,以保证最终产品的尺寸精度和表面质量。
模具的材料选择和加工工艺要合理,以保证模具的耐磨性和寿命。
2. 熔炼与浇注的质量控制熔炼时要严格控制熔炼温度和熔炼时间,保证金属或合金的成分均匀,不产生气体和夹杂物。
浇注时要控制浇注温度和速度,避免产生气孔、夹渣和缩松等缺陷。
3. 冷却凝固的质量控制控制冷却速度和冷却方式,以避免产生组织缺陷,如晶粒过大、晶界不清晰等。
控制凝固过程中的温度变化,以避免产生应力和变形。
4. 后处理的质量控制清理杂质和缺陷,如夹渣、气孔等。
进行热处理、表面处理或机械加工,以改善产品的性能和表面质量。
质量控制方法为了有效控制铸造生产过程中的质量,可以采取以下几种方法:1. 设计质量控制在产品设计阶段,就应考虑产品的铸造性,合理设计产品的几何形状和壁厚,减少可能出现的缺陷和变形。
2. 工艺参数控制对每个工艺环节中的关键参数进行严格控制,如熔炼温度、浇注温度和速度等。
在铸造过程中,通过实时监测温度、压力和流速等参数,进行及时调整和控制。
3. 检测和检验使用各种检测设备和仪器,如X射线探伤仪、超声波检测仪等,对产品进行无损检测,以发现和排除可能存在的缺陷。
进行物理和化学性能的检验,如拉伸试验、硬度测试和成分分析等。
4. 信息化管理建立完善的质量管理体系,进行全过程的质量记录和数据分析,发现问题并采取措施进行改进。
运用信息化技术,实现数据的实时监控和追溯,提高生产过程的透明度和可控性。
结论铸造生产过程的质量控制是确保最终产品质量的重要环节。
通过合理的质量控制措施和方法,可以有效避免铸造过程中可能出现的缺陷和变形,提高产品的质量和性能。
铸造质量控制

铸造质量控制铸造质量控制是指在铸造过程中对产品质量进行管理和控制的一系列措施。
通过合理的质量控制措施,可以确保铸造产品的尺寸精度、表面质量、力学性能等指标达到设计要求,从而提高产品的质量和可靠性。
一、质量控制的目标和意义铸造质量控制的目标是确保产品质量达到设计要求,具体包括以下几个方面:1. 尺寸精度控制:通过控制铸件的收缩和变形,保证尺寸精度在允许范围内。
2. 表面质量控制:确保铸件表面光洁度、无气孔、夹杂物等缺陷。
3. 力学性能控制:保证铸件的强度、韧性等力学性能满足要求。
4. 成本控制:通过合理的质量控制措施,降低不合格品率,减少生产成本。
质量控制的意义在于:1. 提高产品质量:通过严格的质量控制,确保产品达到设计要求,提高产品的质量和可靠性。
2. 降低生产成本:通过减少废品率、减少返工率等手段,降低生产成本。
3. 提高企业竞争力:优质的产品能够提高企业的竞争力,赢得更多的市场份额。
二、质量控制的主要内容和方法1. 原材料控制:选择合适的原材料,确保其质量符合要求。
对原材料进行化学成分分析、物理性能测试等,确保铸件的化学成分和机械性能满足要求。
2. 铸型制备控制:控制铸型的制备工艺,确保铸型的密实性、耐火性等性能,避免铸型砂中的气孔、夹杂物等缺陷。
3. 浇注工艺控制:控制浇注温度、浇注速度、浇注时间等参数,确保熔融金属在铸型中充分填充,避免铸件出现冷隔、缩松等缺陷。
4. 熔炼工艺控制:控制熔炼温度、炉渣成分等参数,确保熔融金属的化学成分和纯净度符合要求。
5. 热处理工艺控制:对铸件进行热处理,提高其力学性能。
控制热处理温度、保温时间等参数,确保铸件的组织结构和性能达到设计要求。
6. 检测与检验:通过无损检测、化学成分分析、力学性能测试等手段,对铸件进行质量检测和检验,确保产品质量符合要求。
7. 过程控制:建立合理的工艺流程和操作规程,对每个工序进行严格控制,确保每一道工序的质量稳定可靠。
三、质量控制的指标和标准1. 尺寸精度指标:包括线性尺寸公差、平面度、垂直度等指标,根据产品设计要求和使用要求进行控制。
铸造质量控制

铸造质量控制引言概述:铸造是一种重要的创造工艺,广泛应用于各个行业。
铸造质量控制是确保铸件质量符合要求的关键步骤。
本文将从材料选择、工艺控制、设备维护、工艺改进和质量检测五个方面详细阐述铸造质量控制的重要性和方法。
一、材料选择1.1 确保原材料质量:选择合适的原材料是保证铸件质量的基础。
要求原材料符合国家标准,并进行严格的检验和测试。
1.2 控制合金成份:在铸造过程中,合金成份的控制对于铸件的性能至关重要。
通过精确的配料和严格的质量控制,确保合金成份符合设计要求。
1.3 优化材料熔化过程:材料熔化是铸造的关键步骤,要确保熔化温度、保温时间等参数符合要求,避免杂质温和体的夹杂。
二、工艺控制2.1 确定合适的铸造工艺:根据铸件的形状、尺寸和要求,选择合适的铸造工艺。
包括砂型铸造、金属型铸造、压铸等,确保铸造过程中能够得到良好的铸件质量。
2.2 控制铸造温度和速度:铸造温度和速度对于铸件的凝固过程和组织结构有重要影响。
通过控制熔体温度和冷却速度,避免铸件浮现缩孔、夹杂等缺陷。
2.3 优化浇注系统设计:浇注系统的设计对于铸件质量至关重要。
合理设计浇口、冷却水道等,确保熔体能够均匀地填充模型,避免气孔和缺陷的产生。
三、设备维护3.1 定期检查设备:定期检查铸造设备的状态,包括熔炉、模具、浇注设备等。
确保设备正常运行,避免因设备故障引起的铸件质量问题。
3.2 清洁和保养设备:保持设备的清洁和良好的工作状态对于铸造质量的控制至关重要。
定期清洗设备、更换磨损部件,确保设备的正常工作。
3.3 培训和提高操作技术:铸造工艺的操作技术对于铸件质量的控制有重要影响。
通过培训和提高操作技术,提高操作人员的技术水平,确保工艺的稳定性和一致性。
四、工艺改进4.1 分析和改进工艺缺陷:对于浮现的铸件缺陷,进行详细的分析和改进。
通过改进工艺参数、优化工艺流程等方式,减少缺陷的发生。
4.2 引进新工艺和技术:随着科技的发展,不断引进新的铸造工艺和技术,提高铸件质量和生产效率。
铸造工艺流程的质量控制方法
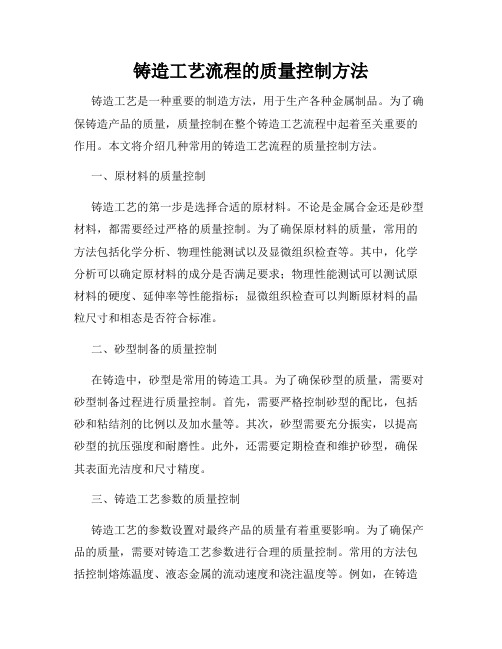
铸造工艺流程的质量控制方法铸造工艺是一种重要的制造方法,用于生产各种金属制品。
为了确保铸造产品的质量,质量控制在整个铸造工艺流程中起着至关重要的作用。
本文将介绍几种常用的铸造工艺流程的质量控制方法。
一、原材料的质量控制铸造工艺的第一步是选择合适的原材料。
不论是金属合金还是砂型材料,都需要经过严格的质量控制。
为了确保原材料的质量,常用的方法包括化学分析、物理性能测试以及显微组织检查等。
其中,化学分析可以确定原材料的成分是否满足要求;物理性能测试可以测试原材料的硬度、延伸率等性能指标;显微组织检查可以判断原材料的晶粒尺寸和相态是否符合标准。
二、砂型制备的质量控制在铸造中,砂型是常用的铸造工具。
为了确保砂型的质量,需要对砂型制备过程进行质量控制。
首先,需要严格控制砂型的配比,包括砂和粘结剂的比例以及加水量等。
其次,砂型需要充分振实,以提高砂型的抗压强度和耐磨性。
此外,还需要定期检查和维护砂型,确保其表面光洁度和尺寸精度。
三、铸造工艺参数的质量控制铸造工艺的参数设置对最终产品的质量有着重要影响。
为了确保产品的质量,需要对铸造工艺参数进行合理的质量控制。
常用的方法包括控制熔炼温度、液态金属的流动速度和浇注温度等。
例如,在铸造过程中,如果熔炼温度过高,易导致铸件内部存在气孔和夹杂物;如果浇注温度过低,易导致铸件的收缩缺陷。
因此,合理控制这些参数可以有效提高铸件的质量。
四、铸造产品的检测与测试在铸造工艺流程中,对铸造产品进行质量检测和测试是不可或缺的环节。
常用的方法包括无损检测、机械性能测试以及尺寸测量等。
其中,无损检测可以通过X射线、超声波等方法检测产品是否存在缺陷;机械性能测试可以测试产品的抗拉强度、硬度等力学性能;尺寸测量则可以验证产品的尺寸精度是否符合要求。
五、质量记录与反馈为了总结经验并改进铸造工艺流程,需要对质量进行记录和反馈。
对于每个铸造批次,应该记录原材料、砂型、工艺参数以及产品质量等关键信息。
铸造质量控制

铸造质量控制1、铸造过程控制铸造过程控制是铸造质量控制的核心,它包括原料控制、工艺控制、设备控制等方面。
其中,工艺控制是最为重要的环节,需要制定详细的工艺控制文件,如作业指导书等。
作业指导书是铸造过程控制的重要文件,必须保证其准确、完整、具体、规范,避免“两张皮”和不协调现象的出现。
2、铸件产品质量控制铸件产品质量控制是指铸件产品在使用过程中所表现出的性能和质量水平,是评价铸造质量的基本指标。
为了保证铸件产品质量,需要从铸造过程控制入手,采取措施提高铸造过程的稳定性、耐用性和工艺性等指标,确保铸件在使用条件下的可靠性。
3、质量控制要点制定作业指导书是铸造质量控制的重要环节,需要注重以下问题:将生产工人的经验和技巧总结进去,与工序质量分析表相呼应,要求内容完整准确、详细具体,避免出现“见某某文件”等现象。
此外,还需要加强铸造过程控制,包括原料控制、工艺控制、设备控制等方面,提高铸造过程的稳定性和可靠性,保证铸件产品质量。
我们采用的改进方法有很多种,如QC、8D、六西格玛等等。
这些方法都是基于PDCA循环的过程,旨在持续改进项目。
我们可以从质量例会、新产品开发阶段异常检讨会议、产品审核、过程审核、内外部体系审核、检验中的异常现象、生产会议、设备会议、成本会议、年度报告、年度持续改进计划、提案、客诉等过程中提出的各项问题中,发现需要改进的方面。
同时,生产过程中遇到的各种问题也需要被纳入改进范畴。
需要强调的是,QC、8D、六西格玛的思路基本上是一致的,不同之处在于使用的工具不同。
这些改进方法并没有万能的钥匙,只有选择最合适的工具才能达到改进目标。
当然,我们也要避免死板的套用。
铸造质量控制
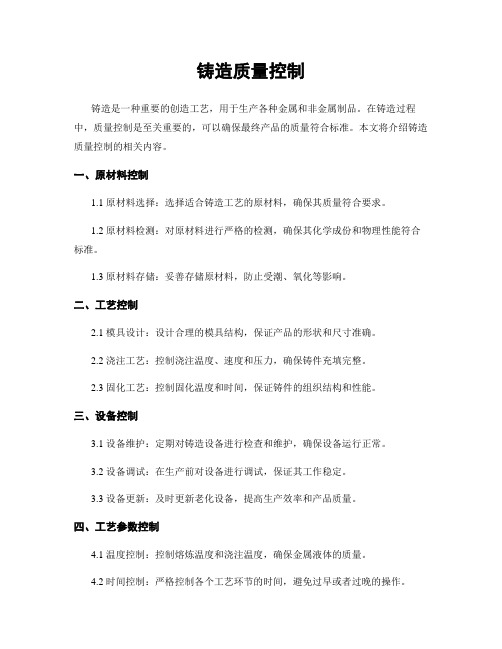
铸造质量控制铸造是一种重要的创造工艺,用于生产各种金属和非金属制品。
在铸造过程中,质量控制是至关重要的,可以确保最终产品的质量符合标准。
本文将介绍铸造质量控制的相关内容。
一、原材料控制1.1 原材料选择:选择适合铸造工艺的原材料,确保其质量符合要求。
1.2 原材料检测:对原材料进行严格的检测,确保其化学成份和物理性能符合标准。
1.3 原材料存储:妥善存储原材料,防止受潮、氧化等影响。
二、工艺控制2.1 模具设计:设计合理的模具结构,保证产品的形状和尺寸准确。
2.2 浇注工艺:控制浇注温度、速度和压力,确保铸件充填完整。
2.3 固化工艺:控制固化温度和时间,保证铸件的组织结构和性能。
三、设备控制3.1 设备维护:定期对铸造设备进行检查和维护,确保设备运行正常。
3.2 设备调试:在生产前对设备进行调试,保证其工作稳定。
3.3 设备更新:及时更新老化设备,提高生产效率和产品质量。
四、工艺参数控制4.1 温度控制:控制熔炼温度和浇注温度,确保金属液体的质量。
4.2 时间控制:严格控制各个工艺环节的时间,避免过早或者过晚的操作。
4.3 压力控制:根据产品要求控制浇注压力,确保铸件的密度和强度。
五、质量检验控制5.1 外观检验:对铸件的表面质量进行检查,包括气孔、裂纹等缺陷。
5.2 尺寸检验:测量铸件的尺寸和几何形状,确保符合设计要求。
5.3 化学成份检验:对铸件的化学成份进行分析,确保符合标准。
综上所述,铸造质量控制是确保铸件质量的关键环节,需要在原材料、工艺、设备、工艺参数和质量检验等方面进行全面控制。
惟独做好质量控制,才干生产出满足客户需求的优质铸件。
铸造质量控制
铸造质量控制铸造质量控制是指在铸造过程中,通过一系列的控制措施和检测手段,确保铸件的质量符合设计要求和客户需求的过程。
本文将详细介绍铸造质量控制的标准格式,包括质量控制的目标、方法、流程和关键要点。
一、质量控制的目标铸造质量控制的目标是确保铸件的尺寸精度、组织结构、力学性能等质量指标符合设计要求和客户需求,同时降低废品率,提高生产效率。
二、质量控制的方法1. 原材料控制:选择合格的原材料,包括金属合金、砂型、熔炼剂等。
对原材料进行化学成分分析、物理性能测试等,确保原材料的质量稳定。
2. 工艺控制:制定合理的铸造工艺,包括砂型制备、熔炼、浇注、冷却等环节。
严格控制砂型的湿度、砂型的硬度、浇注温度、浇注速度等参数,确保铸件的凝固过程稳定。
3. 设备控制:对铸造设备进行定期维护和检修,确保设备的正常运行。
同时,配备先进的铸造设备,如自动浇注机、温度控制系统等,提高铸造的稳定性和一致性。
4. 检测控制:采用合适的检测手段,对铸件进行全面的检测。
包括尺寸测量、金相组织观察、力学性能测试等,确保铸件的质量指标符合要求。
常用的检测方法包括X射线检测、超声波检测、磁粉检测等。
三、质量控制的流程1. 原材料检验:对原材料进行化学成分分析、物理性能测试等,确保原材料的质量稳定。
2. 工艺参数设定:根据铸件的要求,制定合理的铸造工艺参数,包括砂型制备、熔炼、浇注、冷却等环节。
3. 设备调试:对铸造设备进行调试,确保设备的正常运行。
4. 首件检验:对首件进行全面的检测,包括尺寸测量、金相组织观察、力学性能测试等,确保首件质量符合要求。
5. 在线检验:在铸造过程中,对铸件进行抽检,确保铸件的质量稳定。
6. 最终检验:对最终产品进行全面的检测,确保产品的质量指标符合要求。
四、质量控制的关键要点1. 制定严格的质量控制标准和工艺规范,确保每个环节都有明确的要求和控制措施。
2. 建立完善的质量管理体系,包括质量责任制、质量培训、质量记录等,确保质量控制的有效实施。
铸造过程的质量控制
铸造过程的质量控制铸造是一种古老的制造技术,广泛应用于各个行业。
然而,铸造过程中存在着许多影响产品质量的因素,因此质量控制显得尤为重要。
本文将探讨铸造过程的质量控制,以确保最终产品的质量和性能符合要求。
一、原材料控制铸造原材料是铸造产品质量的基础。
因此,必须严格控制原材料的质量。
应选择符合要求的优质材料,并进行严格的进货检验。
应合理储存和使用原材料,以防止材料受到污染或变质。
二、工艺控制铸造工艺是影响铸造产品质量的另一个重要因素。
工艺控制包括制定合理的铸造工艺流程、控制浇注温度、冷却速度等参数。
还应进行工艺验证,以确保工艺的稳定性和可靠性。
三、设备控制铸造设备是实现铸造工艺的关键。
设备控制包括设备的选型、维护和保养。
应定期检查设备是否处于良好状态,并对其进行必要的维修和更换。
四、环境控制铸造环境是影响铸造产品质量的另一个因素。
环境控制包括控制车间的温度、湿度和清洁度等参数。
应保持车间整洁,定期清理和消毒,以确保产品不受污染。
五、检验控制检验是保证铸造产品质量的重要手段。
应制定严格的检验计划,并对产品进行首检、过程检和终检。
对于不合格的产品,应及时进行返工或报废,以免影响整体质量。
六、持续改进持续改进是保证铸造产品质量的关键。
应通过收集和分析质量数据,找出存在的问题和改进点,并采取相应的措施进行改进。
还应定期对质量控制体系进行审查和更新,以适应市场和客户需求的变化。
铸造过程的质量控制是确保最终产品质量的必要手段。
通过控制原材料、工艺、设备、环境、检验和持续改进等方面,可以有效地提高铸造产品的质量和性能。
铸造生产过程质量控制点铸造作为产品制造的重要环节,其生产过程的质量控制至关重要。
质量控制点的设立和监控是保证铸造产品质量的关键。
一、材料控制1、原材料:确保使用符合设计要求的原材料,如金属、砂型、涂料等,并对这些材料进行质量检验,避免不合格材料进入生产流程。
2、辅助材料:如孕育剂、球化剂、增碳剂等,这些材料的质量也直接影响铸件的质量,需严格控制其质量和添加量。
铸造质量控制
铸造质量控制一、引言铸造是一种重要的金属加工方式,广泛应用于各个领域。
铸造质量的好坏直接影响到铸件的性能和使用寿命。
因此,建立科学的铸造质量控制标准是必不可少的。
本文将详细介绍铸造质量控制的标准格式,包括质量控制的目的、范围、术语定义、质量控制方法以及质量控制的责任与要求。
二、质量控制的目的铸造质量控制的目的是确保铸件的质量符合设计要求,并满足客户的需求。
通过建立科学的质量控制标准,可以有效地减少铸造缺陷,提高产品的可靠性和稳定性,降低生产成本,增强企业竞争力。
三、质量控制的范围铸造质量控制的范围包括但不限于以下几个方面:1.原材料的质量控制:包括铸造原料的选择、检验和验收标准等。
2.铸造工艺的质量控制:包括模具创造、熔炼、浇注、冷却等各个环节的控制要求。
3.铸件表面质量的控制:包括铸件的外观、尺寸、几何形状等方面的要求。
4.铸件内部质量的控制:包括铸件的组织结构、缺陷检测、力学性能等方面的要求。
5.质量记录与检验:包括质量记录的保存、质量检验的方法和标准等。
四、术语定义1.铸造缺陷:指在铸造过程中产生的不符合设计要求的缺陷,如气孔、夹杂、砂眼等。
2.模具:用于创造铸件形状的工具,可以是金属模具、砂型、蜡模等。
3.熔炼:将金属原料加热至液态,并进行铸造准备的过程。
4.浇注:将熔融金属倒入模具中,使其冷却凝固成型的过程。
5.冷却:铸件在浇注后,通过自然冷却或者其他冷却方式使其降温凝固的过程。
五、质量控制方法1.原材料的质量控制方法:(1)选择合适的原材料供应商,并建立长期稳定的合作关系。
(2)对原材料进行严格的检验,包括外观、化学成份、物理性能等指标。
(3)制定原材料验收标准,明确合格和不合格的判定标准。
2.铸造工艺的质量控制方法:(1)制定详细的工艺流程和作业指导书,明确每一个环节的工艺参数和操作要求。
(2)对模具进行定期检查和维护,确保其精度和使用寿命。
(3)严格控制熔炼过程中的温度、时间、搅拌等参数,确保金属液的质量。
铸造质量控制
铸造质量控制引言概述:铸造是一种重要的创造过程,用于创造各种金属和合金的零件和构件。
铸造质量控制是确保铸造产品质量的关键步骤。
本文将从五个大点来阐述铸造质量控制的重要性和方法。
正文内容:1. 材料选择1.1 材料性能要求:铸造材料的性能直接影响到最终产品的质量。
在铸造质量控制中,首先要选择合适的材料,确保其具有所需的力学性能、化学成份和热处理性能。
1.2 原材料质量控制:铸造过程中使用的原材料也需要进行质量控制。
这包括对原材料的化学成份、杂质含量和物理性能进行检测和分析,以确保原材料的质量符合要求。
2. 设计和模具创造2.1 铸造产品设计:在铸造质量控制中,产品设计是至关重要的一环。
合理的产品设计可以减少铸造缺陷的发生,提高产品的质量。
设计时需要考虑到材料的收缩率、热胀冷缩等因素,以确保产品的尺寸和形状符合要求。
2.2 模具创造:模具的创造质量直接影响到铸造产品的质量。
在铸造质量控制中,需要对模具的材料、尺寸和表面质量进行控制。
同时,还需要进行模具的定期维护和保养,以确保模具的使用寿命和铸件的质量。
3. 铸造工艺控制3.1 浇注系统设计:合理的浇注系统设计可以有效地控制铸造过程中的气孔、夹杂和缩孔等缺陷。
在铸造质量控制中,需要考虑到浇注系统的形状、尺寸和流动性,以确保熔体能够均匀地填充模腔。
3.2 浇注温度和速度控制:铸造过程中的浇注温度和速度对产品的质量有着重要影响。
在铸造质量控制中,需要根据材料的特性和产品的要求,合理控制浇注温度和速度,以避免热裂纹和冷隔离等缺陷的发生。
4. 检测和分析4.1 检测方法选择:在铸造质量控制中,需要选择合适的检测方法来检测铸件的质量。
常用的检测方法包括金相检测、尺寸检测、硬度检测和无损检测等。
4.2 缺陷分析:在铸造质量控制中,对铸件的缺陷进行分析是非常重要的。
通过对缺陷的分析,可以找出产生缺陷的原因,并采取相应的措施进行改进和修复。
5. 质量管理体系5.1 质量标准制定:在铸造质量控制中,需要制定相应的质量标准,明确产品的质量要求和检测方法。
- 1、下载文档前请自行甄别文档内容的完整性,平台不提供额外的编辑、内容补充、找答案等附加服务。
- 2、"仅部分预览"的文档,不可在线预览部分如存在完整性等问题,可反馈申请退款(可完整预览的文档不适用该条件!)。
- 3、如文档侵犯您的权益,请联系客服反馈,我们会尽快为您处理(人工客服工作时间:9:00-18:30)。
一、铸件质量控制铸件质量决定于每一道工艺过程的质量。
对铸件质量进行控制,实际上是全过程质量控制(%&’),将过程处于严格控制之中,不出现系统误差(由异常原因造成的误差)。
过程中由随机原因产生的随机误差,其频率分布是有规律的。
这种利用数理统计方法将铸造过程中系统误差和随机误差区分开来是质量控制的基本方法。
这种方法又称之为统计过程控制(()’)。
·+$*# ·第一章铸件质量铸件质量控制首先在于稳定生产过程,避免系统误差的出现和随机误差的积累。
其次要提高工艺过程精度,缩小误差频率分布范围或分散程度。
过程控制包括技术准备过程、图样和验收条件的制订;铸造工艺、工装设计的验证;原材料验收;设备检查;工装几何形状、尺寸精度和装配关系检查等;另外,还包括熔炼、配砂、造型、制芯等工艺参数的控制。
控制方法是定期记录工艺参数进行统计分析,判断车间参数误差频率分布及性质,对每一中间工序的结果进行检查。
图! " # " $ 表示出铸铁车间的铸造工艺过程质控站(%&)及整个控制程序。
图! " # " $ 铸铁件生产过程质控站(%&)布置建立过程质量控制站(简称质控站)或管理站是质量管理中行之有效的措施。
质控站能为缺陷分析提供生产过程背景材料以及原始记录和统计资料,凡是对铸件质量特性有重大影响的工序或环节,一般都应设置质控站。
质控站还应贯彻并使操作者严格执行操作规程。
工厂考核铸件质量,按铸件产生缺陷的原因,追究个人或生产小组的责任。
由于铸件产生缺陷的原因是多方面的和复杂的,有些缺陷是由多个因素引起的,故不容易划分各自应承担责任的百分比。
为了解决由于划分不公引起争端,应该加强中间检查,应对每一道工序的质量(特别是主要工艺参数和执行操作规程的情况)进行严格的控制,从而确定个人或小组的质·’)(’ ·第九篇铸造生产质量检验与铸件缺陷分析处理量责任。
例如质控站按规程抽查型砂的性能,如果不符合标准的规定,就应当根据超过标准的百分数来衡量配制型砂者的工作质量,并据此来决定奖惩的程度。
影响铸件质量的因素众多,加强质控站的中间检查的另一好处是将所有影响因素都置于严格控制之下,任何一道不合格操作,都消除在最后形成铸件之前。
过程中出现的问题就是铸件发生缺陷,一般都按!(计划)、"(实行)、#(检查)、$(处理)质量体系活动模式的步骤进行改进。
除此外,分析具体的铸件缺陷时还需要明确问题、分析数据和设计试验等。
二、铸件质量保证质量保证(%$)因生产铸件质量要求而有差别。
超级合金铸件同无牌号铸铁件相比较,它们的质量要求当然不同,但是它们在不同质量要求或规格前提下,生产质量均需稳定,因而要在不同水平上建立起保证体系。
这种体系主要是由用户对铸件生产者一方提出:要求了解铸件承制方质量保证体系水平是否与对铸件的要求相适应。
如质量保证的水准低于铸件质量所要求的,则不能保证铸件质量的可靠性。
在这种情况下,承制方得不到信任,应被更换。
质量保证体系构成分软件和硬件两部分,在软件上要求承制方:(&)质量管理机构健全。
(’)质量责任制度明确。
(()质量信息网络全面、灵敏和功能齐全。
())有完善的标准化组织。
(*)计量工作完备。
(+)对从业人员的质量教育经常化。
(,)产品的技术档案详细,管理机能好。
技术档案的内容因铸件的要求而不同,对特别重要的铸件,应容许用户查到从事造型、合型、熔炼及浇注的人员,甚至可查到热处理、探伤、焊修者的操作记录,以及焊修人员所用焊条的牌号和批次。
承制方拥有的基本设施和技术,也是保证铸件质量要求的必需手段。
例如满足出口要求的铸钢件,浇冒口断口痕迹必须用碳弧气刨清除平整,并把它列入生产过程作为一道工序,以保证铸件质量。
这方面的要求还有:(&)生产设备应围绕铸件质量要求进行调整。
铸件精度要求高,造型设备水平应相应提高。
(’)工艺装备,企业应具有一定的工装设计水平及制造与维修的、保养和管理的能力。
(()生产过程中的监控是实施质量管理所需数据的来源,要求质控点足够,布置合理和符合经济生产的原则。
·’+*( ·第一章铸件质量(!)产品检验手段完备,防止不合格铸件漏检出厂,是完成质量保证体系中的关键环节。
除上述软硬件内容外,一个企业中从业人员的素质往往在质量保证体系中起决定性作用,应该通过培训和教育,予以保证和提高。
第六节铸件缺陷检查为确保铸件质量,应根据铸件不同用途和要求,采用不同的检查方法,及时检出所不允许的缺陷。
缺陷检查普遍采用的有以下一些方法。
一、外观检查铸件可见部位的外观检查,常以目视法进行。
对表面粗糙度的检查,应在合适的光线条件下以目测———手触样块,凭感觉进行表面状况的鉴定,借助测量工具获得铸件尺寸数据,用统计方法确定铸件精度方面缺陷率。
目视方法不限于对外观检查,也可对断口进行检查。
人类器官不单眼睛广泛用于检验,根据某类铸件的特性,还可藉嗅觉和听觉进行质量检查。
例如球墨铸铁新折断口臭味和敲击后滞振度,可辅助检验员对球化不良缺陷的程度进行判断。
二、化学分析对所有的铸件,化学成分是十分重要的,因而在大多数情况下,化学成分就是验收指标。
化学成分也间接决定了铸件的力学性能与缺陷发生与否。
例如球墨铸铁中残留镁量低于"#"$%,球墨的球化率必然会受到影响,出现球化不良的缺陷。
化学成分因炉次而异,取样化验结果称为炉次分析,其结果也因分析方法不同而不同。
按国际标准“铸钢件交货通用技术条件”(&’(!))")以湿法化学分析所得结果为准,标准也规定应自铸件毛坯表面以下至少*++ 处取屑状样品。
标准规定出铸件用户为核对分析与炉次分析间允差,如表) , - , . 所列。
重要部件为了了解偏析程序,从两端取样,往往还要分析气体、夹杂物及微量杂质元素的含量。
表) , - , . 核对分析对炉次分析标准允差碳钢元素碳硅锰硫和磷范围(%)!"#$ !"#/ !-#! 0 "#"$/允差1 "#"$ 1 "#"/ 1 "#"* 1 "#""/·2*/! ·第九篇铸造生产质量检验与铸件缺陷分析处理湿法分析缺点是过程慢,如化验铝合金一天都出不来结果。
仪器分析出结果较快,例如! 射线荧光分析仪(!"#)和光发射分光仪($%&),化验一个元素约’ ( )*+,。
前者在-.’/ ( 0-/浓度范围较准,后者则在-. ---’/ ( 1. -/浓度范围较准。
仪器分析要求元素呈固溶态存在于激冷试样中。
三、力学性能检测硬度试验是最早用来检验铸件是否发生缺陷的手段,本世纪初美国曾有人在落砂工段逐个检验浇出的铸件缸盖,如硬度超过一定值则认为铸件必然存在裂纹应予报废。
这种方法简单易行。
拉伸性能和韧性(冲击韧度或伸长率)是常用的检验项目。
试样通常自试块上截取试棒加工而成。
试样的规格应按适用的标准选取,依照检验要求获得合格数据。
这种检验不仅从性能数据可以发现材质存在的问题,而且金属疏松、夹杂物、裂纹、粗晶及回火脆性等缺陷往往可在试样断口上得到反映。
四、低倍检验(宏观检查)用目视或低倍放大镜检查铸件表面或截面的宏观组织或缺陷,以确定它们的性质和严重程度的方法称为低倍检验。
它具有视域大、适用范围广和试验方法简便等优点,与微观组织检验配合能较全面地反映铸件的质量问题。
酸蚀、印痕(硫印、磷印)和断口检验是常用的低倍检验项目(表2 3 ’ 3 2)。
酸蚀可以显示成分偏析、夹杂物和孔洞类铸件宏观缺陷。
印痕可以显示硫、磷在截面上的分布情况。
断口检查可以发现印痕、酸蚀所不能显露的缺陷。
例如沿奥氏体晶界大量析出氮化物或其他金属间化合物,具有银灰色岩石形貌的石状断口等(表2 3 ’ 3表2 3 ’ 3 2 酸蚀、硫印操作规程硫印:’)将已曝光的溴化银印相纸浸在’/ ( )/浓度的硫酸水溶液中,静浸’ ( 1*+,,取出晾干1)将试样用氯化碳擦净,使相纸药面与试样净面紧贴,并压紧,用棉花在相纸反面进行拭擦滚压’ ( 1.4*+,(不许相纸在磨面上移动)酸蚀:’)配制4/的盐酸水溶液,并加热至5- 6 471)将试样放入(待观察面要朝上)保留)- ( 8-*+,))取出试样用热水冲洗或以稀释的碱(4/)水溶液冲洗后,再用热水冲洗,并迅速干燥8)用肉眼和放大镜观察·1044 ·第一章铸件质量表! " # " #$ 铸钢宏观缺陷的断口特征缺陷断口形貌偏析短杆状,较光滑的条带(高倍呈成串夹杂)气孔单个或成束,内壁光滑的条形(外露时带有氧化色)长针形针孔条形孔洞,内壁光滑,不外露的则呈银灰色缩孔呈管状,表面粗糙,严重氧化,常见发达的树枝晶和夹杂物缩松内壁粗糙,不外露的则可见树枝晶热裂纹外露的则氧化严重;表面起伏,圆滑冷裂纹未氧化的呈灰色纤维状或沿奥氏体晶界开裂呈岩石状非金属夹杂成堆分布的颗粒群,有的呈黄绿色五、金相检验(金相显微镜检验)用光学显微镜在放大%$ & ’$$$ 倍下观察抛光的金属表面,试样在未经侵蚀条件下进行夹杂物检查(利用明、暗场及偏光、干涉和显微硬度等多种功能参照()*$%+#—,! 评级),经侵蚀后进行组织及晶粒度检查。
这种方法广泛用于检查微观缺陷,也常用于研究宏观缺陷的微观特征。
上述的化学分析、性能试验和金相检验所取得的试样只能代表局部区域。
为了了解铸件整体的质量情况,须从具有代表性的各个部位选取试样,数量愈多,范围愈广,对发生的铸件缺陷了解愈近全貌,有利于下一步分析。
六、无损检验(无损探伤)对缺陷进行非破坏性检查,根据工作原理不同有以下几类:!光学检查法(目测检查法、渗透探伤检查法-./0 " 1#+%);"放射线检查法(2 线透射检查法、断层摄影(3/)检查法);#电磁检查法(磁力探伤检查法、涡流探伤检查法(-./0 " 14$!));$声波检查法(超声波探伤检查法、-1“声发射”法);%热传导检查法(物质表面温度分布图象显示法)。
其中,目测法、渗透探伤法(5.647%’)、磁粉探伤法、涡流探伤法等,只能用于铸件表面或表层部分缺陷的检查,对铸件深部缺陷的检查,必须使用2 线透射法(5.6%%8!)、断层摄影法和超声波探伤法。
无损检验近年来发展很快,由于数据处理好和硬件趋向于便携式,大大提高了检查的可靠性和灵活性。
2 线透射检查法可提供铸件检测部位有无缺陷及缺陷尺寸的照片。
美国材料试验协会(-./0)发布了一系列适用于铸件检验的射线照相参考标准,它们按缺陷种类和数量分类,为使用者对缺陷可否接受提供判断依据。