玻璃钢管道制造工艺
缠绕玻璃钢管道技术特性及参数

缠绕玻璃钢管道技术特性及参数1、缠绕玻璃钢管道技术特性及参数:与其它材料的管道比较,往复交叉缠绕玻璃钢管道具有以下显著的特性:(1)耐腐蚀性强:玻璃钢材能抵酸、碱、盐、海水、未经处理的污水,腐蚀性土壤或众多化学介质的侵蚀,有一般情况下,钢管使用年限为15年,铸铁管为5-10年,而往复交叉缠绕玻璃钢管道则可使用50年以上。
(2)耐气候性、抗老化性能好:往复交叉缠绕玻璃钢管道可有-40C―80C的范围内长期使用,采用特殊配方的管道还在100C以温度正常工作。
(3)工程寿命长安全可靠:往复交叉缠绕玻璃钢管道设计安全系数为6,其工程寿命可长达50-100年。
(4)重量轻、强度高、运输安装方便:往复交叉缠绕玻璃钢管道的比重为1、6-2.0,管的环向拉伸强度为340Mpa,轴向拉伸强度为180Mpa,与相同的压力、相同管径的其他材质比较,重量约为铸铁管的1/4,约为混凝土管的1/10,因此,运输安装十分方便。
(5)摩阻小,输送能力高:往复交叉缠绕玻璃钢管道内壁非常光滑,糙率和摩阻力很小,计算水力学所采用哈森.威廉系数C可长期保持在145-150的范围内,糙率数为0.0084,测试得到的水流摩阻损失F=0.000915,与混凝土管F=0.00232和钢管F=0.00179相比,能显著减少沿程的液体压力损失,提输送能力20%以上。
因此在输送同等流量时,玻璃管径可比钢管、砼管缩小一个等级,若用动力输送介质,可节约能耗15%左右。
(6)设计灵活性大:纤维缠绕玻璃管制品,可以通过改变树脂系统或增强材料来调整玻璃钢管的物理和化学性能,以适应不同介质和工作条件的需要,通过结构层的设计来调整管的承载能力,制造不同压力等级和刚度等级的管道,或制造成具有某种特殊性能的产品。
这是其它管材相比,自身不生锈、不结垢、不滋生微生物、藻类物质对水质不造成二次污染。
往复交叉缠绕玻璃钢管道技术参数如下:A、管道:环向抗拉强度:340MPA,轴向抗拉模量:12.5GPA轴向抗拉强度:150MPA,剪切模量:7GPA面剪切强度:50MPA,比重:1.6-2.0垂直剪切强度:60MPA,环向拉伸最小极限应变:1.2%环向抗拉模量:25GPA,环向弯曲最小极限应变:1.5%B、管件:拉伸强度:140MPA,拉伸模量:9.5GPA弯曲强度:135MPA,弯曲模量:9.0GPA压缩强度:130MPAC、玻璃钢物理综合性能:巴柯尔硬度:40 断裂延伸率:0.8%泊松系数:0.3 氧指数:30%热膨胀系数粗糙率:0.00842、往复交叉缠绕玻璃钢管道加工工艺说明:(1)工艺方法:本公司生产工艺采采用目前世界流行的往复式纤维缠绕工艺方法生产夹砂和纯往复交叉缠绕玻璃钢管道及其制品,在这种工艺方法中,浸胶槽随转动的芯模作往复运动,纤维相对芯模铺放,辅放角(即缠绕角)受浸胶槽的移动速度和芯模转速按比例控制,浸胶槽的平移运动由计算机控制,缠绕过程中,缠绕层逐渐增加,达到设计壁厚为止,缠绕完成后,使制品中的树脂基体固化,固化后从往复交叉缠绕玻璃钢管道中脱出芯模,进入下一道工序。
玻璃钢夹砂管道
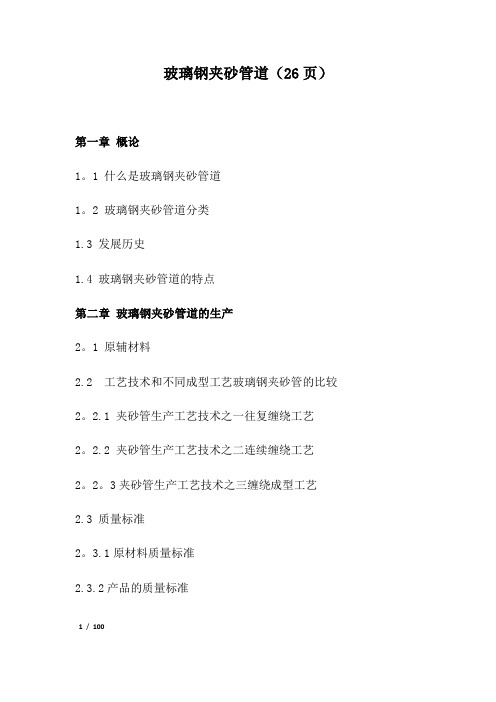
玻璃钢夹砂管道(26页)第一章概论1。
1 什么是玻璃钢夹砂管道1。
2 玻璃钢夹砂管道分类1.3 发展历史1.4 玻璃钢夹砂管道的特点第二章玻璃钢夹砂管道的生产2。
1 原辅材料2.2 工艺技术和不同成型工艺玻璃钢夹砂管的比较2。
2.1 夹砂管生产工艺技术之一往复缠绕工艺2。
2.2 夹砂管生产工艺技术之二连续缠绕工艺2。
2。
3夹砂管生产工艺技术之三缠绕成型工艺2.3 质量标准2。
3.1原材料质量标准2.3.2产品的质量标准1/ 100第三章质量检测3.1产品质量检测3。
2 产品缺陷及质量控制第四章管道安装技术4.1联接4。
2地下管道安装4.3地上管道安装第五章监控与维修5。
1 现阶段常用的监控技术与维修方式5.1.1 现阶段常用的监控技术5.1.2 现阶段常用的维修方式5。
2 未来智能管道---“让管道自己说话”第六章基本力学性能6。
1概述6。
2单层的刚度特性6。
3层合管壁刚度特性6。
4层合管壁的强度性能2/ 100第七章管道的水力计算7。
1概述7。
2摩阻损失的计算7.3简单管路的水力计算7。
4长输管道的水力瞬变第八章玻璃钢夹砂管道的结构分析8。
1概述8。
2地下管载荷与土压分析8.3地下夹砂管的内力分析8。
4地下夹砂管的弹性稳定性8.5地下夹砂管的刚度分析第九章玻璃钢夹砂管道应用现状1.1 国内与国外的应用情况比较1。
2 存在的问题1.3 常见问题的解决方案1。
4 未来玻璃钢夹砂管道的前景分析第十章玻璃钢夹砂管道的常用标准1。
1 国内标准3/ 1001。
2 国际主流标准第一章概论4/ 1001。
1 什么是玻璃钢夹砂管道玻璃纤维增强塑料夹砂管 glass fiber reinforced plastics mortar pipes (简称FWRPM)是以玻璃纤维及其制品为增强材料,以不饱和聚酯树脂等为基体材料,以石英砂及碳酸钙等无机非金属颗粒材料为填料,采用定长缠绕工艺、离心浇铸工艺、连续缠绕工艺方法制成的管道。
玻璃钢管分类

玻璃钢管是一种轻质、高强、耐腐蚀的非金属管道,广泛应用于石油、化工、排水、供水等领域。
根据不同的制造工艺和使用要求,玻璃钢管可以分为以下几类:
1. 手糊法玻璃钢管:采用手工制作的方法将玻璃纤维布和树脂糊在模具上成型,然后经过固化处理得到成品。
这种玻璃钢管具有较好的强度和刚度,但生产效率低,成本较高。
2. 缠绕法玻璃钢管:通过将玻璃纤维纱线缠绕在旋转的芯模上,再涂覆树脂糊进行固化处理得到成品。
这种玻璃钢管具有较好的耐腐蚀性和耐磨性,但强度相对较低。
3. 拉挤法玻璃钢管:将预先制备好的玻璃纤维增强材料放入拉挤机中,通过加热软化后挤出成型,再经过冷却固化得到成品。
这种玻璃钢管具有较好的强度和刚度,且生产效率高,成本较低。
4. 压力法玻璃钢管:将预先制备好的玻璃纤维增强材料放入压力机中,通过加压使其紧密贴合在一起,再经过固化处理得到成品。
这种玻璃钢管具有较好的耐腐蚀性和耐磨性,但生产工艺较为复杂。
除了以上几种常见的分类方法外,还有一些特殊的玻璃钢管类型,如夹砂玻璃钢管、泡沫玻璃钢管等。
这些类型的玻璃钢管在不同的应用场景下有着各自的优势和特点。
总之,选择合适的玻璃钢管类型需要根据具体的使用要求和条件进行综合考虑。
玻璃钢管道工艺流程

玻璃钢管道工艺流程一、概述玻璃钢管道是一种由玻璃纤维和树脂复合材料制成的管道,具有轻质、高强度、耐腐蚀等特点。
在工业、建筑、化工等领域广泛应用。
本文将详细介绍玻璃钢管道的制造工艺流程及相关要点。
二、原材料准备1.玻璃纤维:选用优质无碱玻璃纤维,并经过梳解、剪切等工艺处理,确保纤维长度、直径均匀。
2.树脂:常用的树脂有环氧树脂、不饱和聚酯树脂等,根据不同工艺要求选用合适的树脂。
3.辅助材料:如填充剂、催化剂、防腐剂等。
三、制备工艺1. 玻璃纤维预处理玻璃纤维预处理是为了提高其耐碱性和增强与树脂的粘结力。
1.清洗:将玻璃纤维浸泡在碱性洗涤剂中,去除杂质和油污。
2.除尘:使用吹风机或振动筛去除玻璃纤维表面的灰尘。
3.干燥:通过烘干设备,将玻璃纤维彻底干燥,确保其表面完全无水分。
2. 树脂配制根据不同工艺要求,将树脂与填充剂、催化剂等辅助材料按照一定比例混合搅拌,形成树脂基质。
3. 管道制造1.模具准备:根据需要制造的管道尺寸和形状,准备合适的模具。
2.涂布:在模具内部涂布一层薄薄的树脂基质,均匀覆盖整个模具表面。
3.玻璃纤维制盘:将处理好的玻璃纤维均匀撒布在模具内,形成一层纤维网格。
4.树脂浸渍:将树脂基质均匀浇注到模具内,使其充分浸渍玻璃纤维。
5.压实:用专用工具将树脂和玻璃纤维进行压实,确保其紧密结合。
6.固化:根据树脂类型和环境条件,进行一定时间的固化处理,使管道成型。
7.脱模:将固化好的管道从模具中取出,并对其表面进行必要的修整和抛光。
4. 后处理1.防腐处理:根据管道使用环境,可进行防腐处理,增加管道耐腐蚀性能。
2.检测:对管道进行尺寸、外观和物理性能等方面的检测,确保其质量符合要求。
3.维修和维护:根据管道使用情况,定期检查和维护,延长其使用寿命。
四、质量控制在玻璃钢管道制造过程中,需要严格控制以下几个方面的质量:1. 材料质量确保所用玻璃纤维、树脂和辅助材料的质量稳定,符合相关标准要求。
玻璃钢制造工艺

玻璃钢制造工艺
玻璃钢是一种使用特殊工艺将玻璃与金属结合制成的工程材料,具有轻质、高强度、耐腐蚀等优点,被广泛应用于建筑结构、机械制造等。
玻璃钢制造工艺主要由三个环节:基材处理、粘结处理和混凝土封层处理组成。
首先,在基材处理环节,玻璃和金属将被一一处理。
首先将玻璃磨细,以达到所需的细度,或者采用压制的方式精细地制成所需大小的玻璃。
接着,对金属进行加工,处理成要求形状和尺寸。
然后,粘结处理环节,将玻璃和金属使用适当的粘结剂粘在一起。
在粘结剂安装完成后,将玻璃和金属结合在一起,并采用热压工艺把他们完全熔合在一起。
熔合的玻璃钢材料将以各种尺寸和形状出现在市场上。
最后,混凝土封层处理环节,进行封层处理防止玻璃钢材料的腐蚀。
封层的方式可以涂敷涂料、滴灌混凝土或拉铆混凝土等多种方式,但是涂料处理时注意不要过量,并检查材料表面无裂缝,确保质量。
定长缠绕与离心浇铸工艺的比较
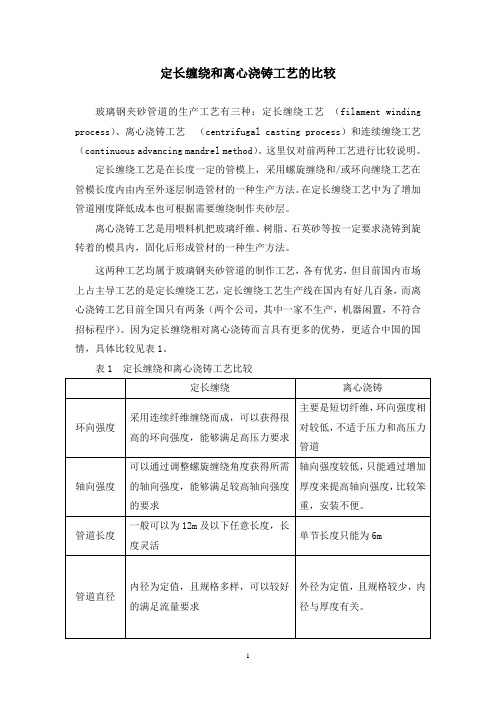
定长缠绕和离心浇铸工艺的比较
玻璃钢夹砂管道的生产工艺有三种:定长缠绕工艺(filament winding process)、离心浇铸工艺(centrifugal casting process)和连续缠绕工艺(continuous advancing mandrel method)。
这里仅对前两种工艺进行比较说明。
定长缠绕工艺是在长度一定的管模上,采用螺旋缠绕和/或环向缠绕工艺在管模长度内由内至外逐层制造管材的一种生产方法。
在定长缠绕工艺中为了增加管道刚度降低成本也可根据需要缠绕制作夹砂层。
离心浇铸工艺是用喂料机把玻璃纤维、树脂、石英砂等按一定要求浇铸到旋转着的模具内,固化后形成管材的一种生产方法。
这两种工艺均属于玻璃钢夹砂管道的制作工艺,各有优劣,但目前国内市场上占主导工艺的是定长缠绕工艺,定长缠绕工艺生产线在国内有好几百条,而离心浇铸工艺目前全国只有两条(两个公司,其中一家不生产,机器闲置,不符合招标程序)。
因为定长缠绕相对离心浇铸而言具有更多的优势,更适合中国的国情,具体比较见表1。
表1 定长缠绕和离心浇铸工艺比较。
玻璃钢导静电管

玻璃钢导静电管一、引言玻璃钢导静电管是一种新型的管材,具有导电、防腐、耐磨等特点,广泛应用于化工、电力、石油等行业。
本文将对玻璃钢导静电管的定义、特点、应用以及制造工艺进行详细介绍。
二、定义玻璃钢导静电管是一种由玻璃纤维和树脂组成的复合材料管道,具有良好的导电性能和防腐性能。
其内壁采用特殊的表面处理技术,使其具有较好的抗静电能力。
三、特点1. 导电性能良好:玻璃钢导静电管内壁采用特殊处理技术,使其具有较好的导电性能,可以有效地防止静电积聚。
2. 防腐性能优异:由于其主要成分是树脂和玻璃纤维,因此具有很强的耐腐蚀性能,在化学品等恶劣环境下使用寿命长。
3. 耐磨性能好:玻璃钢导静电管表面光滑平整,不易积聚污物,具有较好的耐磨性能。
4. 施工方便:玻璃钢导静电管重量轻、强度高、切割方便,可以根据实际需要进行加工和安装。
四、应用1. 化工行业:玻璃钢导静电管广泛应用于化工行业中的输送管道、储罐等设备中。
由于其防腐性能好,可以在各种化学品的输送中起到良好的作用。
2. 电力行业:在电力行业中,玻璃钢导静电管被广泛应用于输电线路和变电站等设备中。
由于其导电性能好,可以有效地防止静电积聚,降低了事故发生的风险。
3. 石油行业:在石油行业中,玻璃钢导静电管被广泛应用于油气输送管道等设备中。
由于其防腐性能好,可以延长设备使用寿命。
五、制造工艺1. 材料准备:将树脂和玻璃纤维按一定比例混合均匀。
2. 模具制作:根据产品尺寸要求制作模具。
3. 布料:将混合好的材料均匀涂布在模具内,压实并使其充分贴合模具表面。
4. 固化:在一定温度下进行固化处理,使其达到一定的硬度。
5. 脱模:将固化后的产品从模具中取出,进行后续的加工和处理。
六、结论玻璃钢导静电管是一种新型的管材,具有导电、防腐、耐磨等特点,广泛应用于化工、电力、石油等行业。
其制造工艺简单,施工方便,可以满足不同领域的需求。
玻璃钢制作工艺简介
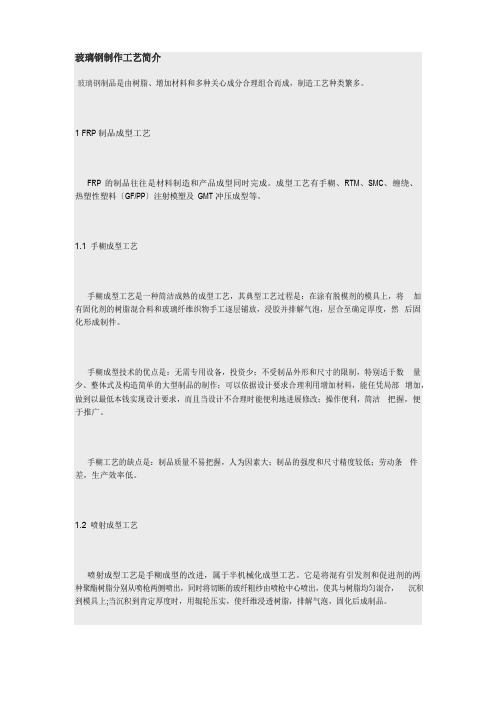
玻璃钢制作工艺简介玻璃钢制品是由树脂、增加材料和多种关心成分合理组合而成,制造工艺种类繁多。
1FRP 制品成型工艺FRP 的制品往往是材料制造和产品成型同时完成。
成型工艺有手糊、RTM、SMC、缠绕、热塑性塑料〔GF/PP〕注射模塑及GMT 冲压成型等。
1.1手糊成型工艺手糊成型工艺是一种简洁成熟的成型工艺,其典型工艺过程是:在涂有脱模剂的模具上,将加有固化剂的树脂混合料和玻璃纤维织物手工逐层铺放,浸胶并排解气泡,层合至确定厚度,然后固化形成制件。
手糊成型技术的优点是:无需专用设备,投资少;不受制品外形和尺寸的限制,特别适于数量少、整体式及构造简单的大型制品的制作;可以依据设计要求合理利用增加材料,能任凭局部增加,做到以最低本钱实现设计要求,而且当设计不合理时能便利地进展修改;操作便利,简洁把握,便于推广。
手糊工艺的缺点是:制品质量不易把握,人为因素大;制品的强度和尺寸精度较低;劳动条件差,生产效率低。
1.2喷射成型工艺喷射成型工艺是手糊成型的改进,属于半机械化成型工艺。
它是将混有引发剂和促进剂的两种聚酯树脂分别从喷枪两侧喷出,同时将切断的玻纤粗纱由喷枪中心喷出,使其与树脂均匀混合,沉积到模具上;当沉积到肯定厚度时,用辊轮压实,使纤维浸透树脂,排解气泡,固化后成制品。
喷射成型的优点是:用玻纤粗纱代替织物,可降低材料本钱;生产效率比手糊的高2~4倍;产品整体性好,无接缝,层间剪切强度高,树脂含量高,耐腐蚀、耐渗漏性好;产品尺寸、外形不受限制。
喷射成型的缺点是:树脂含量高,制品强度低;产品只能做到单面光滑;污染环境,有害工人安康。
1.3SMC 及BMC 成型工艺片状模塑料〔Sheet Molding Comp,SMC〕和团状模塑料〔Bulk Molding Compoun,BMC〕是由树脂糊浸渍纤维或短切纤维毡,两边掩盖聚乙烯薄膜而制成的一类片状模压料,属于预浸毡料范围。
使用时,将两面的薄膜撕去,按制品的尺寸裁剪、叠层,放入金属模具中加温加压,即得所需要的制品。
- 1、下载文档前请自行甄别文档内容的完整性,平台不提供额外的编辑、内容补充、找答案等附加服务。
- 2、"仅部分预览"的文档,不可在线预览部分如存在完整性等问题,可反馈申请退款(可完整预览的文档不适用该条件!)。
- 3、如文档侵犯您的权益,请联系客服反馈,我们会尽快为您处理(人工客服工作时间:9:00-18:30)。
玻璃钢管道制造工艺说明
一、玻璃钢管壁结构说明:
玻璃钢管壁结构从内到外分别为:玻璃钢内衬层、玻璃钢次内衬层、玻璃钢缠绕层、玻璃钢外部保护层。
玻璃钢内衬层、玻璃钢次内衬层起防腐、防渗作用,缠绕层担负起管道的强度和刚度作用,外保护层起抗老化、防腐蚀、抗日晒的作用。
二、玻璃钢管道制作工艺流程
→玻璃钢模具准备
→设备调试、原材料准备
→玻璃钢管道内衬制作
→远红外固化站内衬固化
→玻璃钢管道内衬质量检验
→玻璃钢管道增强层缠绕
→远红外管道整体固化
→玻璃钢管道外观及主要尺寸检验
→玻璃钢管道脱模
→1.5倍工作压力水压试验及其它标准要求的检测项目
→玻璃钢管道包装入库
三、玻璃钢管道工艺详细说明:
(1)准备工序
a、设备调试。
首先认真检查设备运转及工作部位是否正常,特别要细心检查树脂-固化剂双组分泵是否有堵塞现象,之间配比是否达到设计要求;要确保制衬、缠绕、修整、脱模等设备的运行稳定和工作精度;
b、清理模具。
要求模具表面无坑凹、粉尘、杂物及其他附着物,模具要作到表面平滑,有问题及时修理、维护;
c、缠聚酯薄膜。
为方便管道脱模,在模具表面应包覆1层聚酯薄膜,薄膜搭接宽度1~2㎝,厚度为40um之间。
要求薄膜无破损,无皱折,两面光滑洁净。
薄膜产品质量满足GB 13950-1992的要求。
(2)制衬工序
a、内衬树脂配制。
按质检部门根据当时的工作环境、温度条件作出的树脂配方体系进行内衬树脂配兑,配料量要根据制造进度合理掌握。
当现场情况发生变化时,质检部门和制造部门应及时调整配方,并按新配方配制需用的树脂;
b、增强材料准备。
按设计要求将制作内衬需用的增强材料运送到指定位置,并对一些宽幅面的增强材料先裁切加工到设计宽度;
c、内衬层制作。
按设计要求的铺层步骤进行内衬层制作,各单层铺设过程中应施加合理的张力,相互之间适量搭接,并用组合压辊反复滚压赶出气泡以保证纤维完全浸透。
并要求各增强材料层达到设计的树脂含量要求;
d、初步自检。
按设计要求铺覆完各层后,要求操作工人进行初步的质量检测:内衬是否达到设计厚度,局部是否有贫胶、挂胶现象,是否有白斑、气泡,是否有等,若发生上述情况应及时汇报并采取处理措施;
e、进入内衬远红外深度固化工序。
(3)远红外深度固化
我厂生产制造的玻璃钢管道都必须进行远红外深度固化处理,目的是:可以提高内衬层的固化度,改善管道的抗腐耐温性能;
(4)过程质量检验
在缠绕前再次确认内衬无气泡、气孔,无杂质,表面平整,树脂含量合理,无白斑和局部固化不良等现象。
必须认真检查内衬是否合格,不合格的严禁上机缠绕。
(5)缠绕工序
将设计好的参数输入微机,待内衬固化后,由微机控制用无碱无捻玻璃纤维进行往复式缠绕直至缠绕层厚度。
按规定厚度外敷100%树脂含量的外保护层。
缠绕层的树脂含量一般为35%左右,其厚度取决于管道设计的强度和刚度的综合。
(6)红外线固化
管道进入固化养护阶段。
在固化过程中应以适宜的转速保持模具滚动,使其均匀固化。
固化过程中应注意监控管体温度,合理调整固化方案。
(7)修整、脱模:
待管道的巴氏硬度大于30时,对管道端口进行修整。
然后用液压脱模机将管道和模具分离,并在其管道中间部分按要求作标记。
(8)管道水压试验及摆放:
每批管道按规定进行水压试验,注满水,均匀升压至管道设计压力的1.5倍,并保持不低于2分钟,仔细检查管道的表面和压力表。
试压合格后二点支撑摆放管。