弯曲疲劳强度的工业经验
轮齿弯曲疲劳强度和齿面接触疲劳强度-(机械设计齿轮传动章节课件2)-2020329

(10-8),同时引入载荷系数
KH(见下一页),可得:
=
4 −
3
(公式10-9)
1 ± 1
2
=
1
1 ± 1
1
齿轮传动的计算
上式中:
-接触疲劳强度计算的载荷系数, = ,即PPT一开始提到的4个载荷系数;
载荷分布系数Kβ。
= α
(公式10-2)
齿轮传动的计算
1,使用载荷系数KA
是考虑齿轮啮合时外部因素引起的附加载荷影响的系数。这种附加载荷取决
于原动机和从动机械的特性、联轴器类型以及运动状态等。KA的实用值应针
对设计对象,通过实践确定。
1),原动机包括:电动机、均匀运转的蒸汽机、燃气轮机;蒸汽机、燃气轮机液压装置;
当接触位置连续改变时,显然对于零件上任一点处的接触应力只能在材料许用接触应力的范围内改变,因此接触变应
力是一个脉动循环变应力。在做接触疲劳计算时,极限应力也应是一个脉动循环的极限接触应力。
接触应力也称为赫兹应力,是为了纪念首先解决接触应力计算问题的科学家赫兹(H.Hertz)。
齿轮传动的计算
+用于外啮合
多缸内燃机;单缸内燃机。
2),载荷状态分为:均匀平稳、轻微冲击、中等冲击、严重冲击。
工作状态外在因素越恶劣, KA的取值越大。
齿轮传动的计算
使用载荷系数KA
原动机
载荷状态
工作机器
电动机、均匀运转的
蒸汽机、燃气轮机
蒸汽机、燃气
轮机液压装置
多缸内燃机
单缸内燃机
均匀平稳
发动机、均匀传送的带式输送机或板式输送机、
齿轮弯曲疲劳强度试验方法

齿轮弯曲疲劳强度试验方法全文共四篇示例,供读者参考第一篇示例:齿轮在机械设备中起着至关重要的作用,它们通过齿轮传动来实现机械运动,比如汽车的变速箱、风力发电机和其他机械设备都离不开齿轮。
齿轮在长时间运作中会受到各种力的作用,容易发生疲劳断裂,因此对齿轮的疲劳强度进行测试是非常重要的。
本文将介绍一种关于齿轮弯曲疲劳强度试验方法,以帮助读者了解如何对齿轮进行有效的疲劳强度测试。
一、试验原理齿轮在实际工作中常常处于扭转状态,因此齿轮齿面上会受到交替弯曲负载,导致齿轮的疲劳断裂。
齿轮弯曲疲劳强度试验就是通过加载一定应力的齿轮样品,进行一定次数的循环载荷,观察齿轮在经过一定循环次数后是否发生疲劳断裂,从而得到齿轮的弯曲疲劳强度数据。
二、试验步骤1. 制备齿轮样品:根据要测试的齿轮种类和规格,选择合适的齿轮样品进行测试。
确保齿轮样品的质量和尺寸符合要求。
2. 振动应力加载:将齿轮样品安装在试验设备上,施加振动应力加载进行弯曲疲劳试验。
根据所需的循环次数和载荷大小,设定试验参数。
3. 观察齿轮状态:在试验过程中,定期观察齿轮的状态,包括表面裂纹、变形等情况。
一旦发现齿轮有异常情况,立即停止试验,并对齿轮进行检查和修复。
4. 记录数据:记录齿轮样品在每个循环周期后的疲劳情况,包括疲劳寿命、发生裂纹的次数等数据。
5. 分析结果:根据试验数据分析齿轮的疲劳断裂情况,计算出齿轮的弯曲疲劳强度指标,评估齿轮的使用寿命和安全性。
三、试验注意事项1. 选用合适的试验设备和工具,确保试验过程中的准确性和可靠性。
2. 控制试验参数,包括载荷大小、循环次数等,确保试验结果具有可靠性。
3. 在试验过程中定期检查齿轮的状态,及时发现问题并采取措施修复。
4. 根据试验结果对齿轮进行评估和改进,提高其疲劳强度和使用寿命。
通过以上介绍,相信读者已经对齿轮弯曲疲劳强度试验方法有了一定的了解。
要保证齿轮的安全可靠运行,进行疲劳强度测试是非常关键的。
20crmnti弯曲疲劳极限 -回复

20crmnti弯曲疲劳极限-回复弯曲疲劳是材料在反复加载和卸载的循环荷载作用下导致的疲劳失效。
具体来说,当材料受到周期性的弯曲应力时,其内部会出现应力集中和微裂纹的形成。
随着循环次数的增加,微裂纹会逐渐扩展,最终导致材料的断裂。
掌握材料的弯曲疲劳极限有助于提高材料的使用寿命和安全性能。
在工程实践中,对材料的弯曲疲劳极限进行评估具有重要意义。
一般来说,评估弯曲疲劳极限需要进行以下步骤:第一步:确定试样的几何形状和尺寸。
试样的几何形状和尺寸应符合具体的工程要求和标准。
通常使用悬臂梁试样或屈服悬臂式试样进行疲劳弯曲实验。
第二步:确定试验加载方式和频率。
疲劳试验是通过施加特定的应力或应变水平来模拟实际工作条件下的循环载荷。
根据实际工况和试验目的,确定试验加载方式和频率非常重要。
第三步:进行预试验和应力水平选择。
预试验是为了确定合适的应力水平进行后续的疲劳弯曲试验。
在进行预试验的过程中,记录试样的载荷-应变曲线和弯曲疲劳寿命曲线。
第四步:疲劳试验。
按照预设的加载方式和频率进行疲劳试验。
在试验过程中,记录试样的应力-循环次数曲线和应力-挠度曲线。
第五步:数据处理和分析。
根据试验获得的数据,绘制应力-循环次数曲线和应力-挠度曲线。
通过对曲线上的数据进行拟合和分析,得到弯曲疲劳极限。
第六步:评估和使用寿命预测。
根据弯曲疲劳极限,评估材料的疲劳性能和使用寿命。
基于研究和试验得到的数据,可以预测材料在实际工况下的使用寿命,以确保材料能够安全可靠地工作。
总之,弯曲疲劳极限的评估是工程实践中不可或缺的一环。
通过合理选择试样的几何形状和尺寸、确定试验加载方式和频率、进行预试验和应力水平选择、进行疲劳试验,并通过数据处理和分析以及使用寿命预测,可以获得准确的弯曲疲劳极限,提高材料的使用寿命和安全性能。
《2024年铝合金车轮弯曲疲劳实验失效分析及工艺的研究》范文

《铝合金车轮弯曲疲劳实验失效分析及工艺的研究》篇一一、引言铝合金车轮因其轻量化、耐腐蚀性强和良好的成形性等特点,在汽车工业中得到了广泛应用。
然而,其在实际使用中经常面临弯曲疲劳的问题,导致失效和安全隐患。
因此,对铝合金车轮的弯曲疲劳实验失效分析及工艺的研究显得尤为重要。
本文旨在探讨铝合金车轮在弯曲疲劳实验中的失效模式,并对其工艺进行深入研究。
二、铝合金车轮弯曲疲劳实验方法及设备铝合金车轮的弯曲疲劳实验主要借助专用的实验设备进行,如轮毂弯曲测试机等。
通过设定一定的加载速度、位移、循环次数等参数,模拟车轮在实际使用中的受力情况。
在实验过程中,记录下数据,包括加载力、位移、循环次数等,以及车轮的形变情况。
三、铝合金车轮弯曲疲劳实验失效模式分析经过大量的实验数据收集与分析,铝合金车轮的弯曲疲劳失效模式主要有以下几种:1. 表面裂纹:在反复的弯曲过程中,车轮表面可能出现裂纹,这是由于材料表面受到的应力超过了其承受极限。
2. 内部断裂:由于材料内部存在缺陷或应力集中现象,导致在长时间的弯曲过程中出现内部断裂。
3. 形变过大:车轮在持续的弯曲作用下,其形状可能发生永久性的变化,超过了一定的范围。
四、铝合金车轮的工艺研究针对铝合金车轮的失效模式,我们需要对其生产工艺进行优化。
主要的工艺包括材料选择、铸造工艺、热处理等。
1. 材料选择:选择具有高强度、高韧性和良好抗疲劳性能的铝合金材料。
2. 铸造工艺:优化铸造过程中的温度控制、模具设计等,减少内部应力集中和缺陷的产生。
3. 热处理:对铸造后的车轮进行适当的热处理,提高材料的性能。
五、工艺优化建议与实验验证根据上述的工艺研究,我们提出以下优化建议:1. 选择更加优质的铝合金材料。
2. 对铸造过程进行精细化控制,如优化温度控制范围、模具材料及设计等。
3. 对车轮进行适当的热处理,如淬火和回火等,提高其力学性能和抗疲劳性能。
为了验证这些优化建议的有效性,我们进行了对比实验。
提高齿根弯曲疲劳强度的主要措施
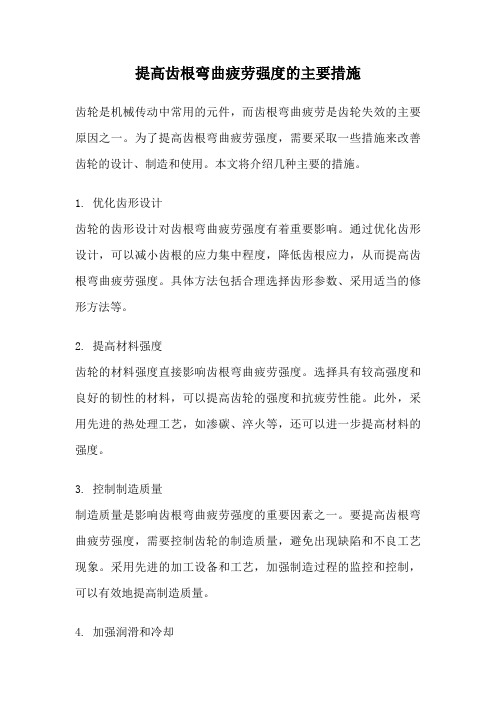
提高齿根弯曲疲劳强度的主要措施齿轮是机械传动中常用的元件,而齿根弯曲疲劳是齿轮失效的主要原因之一。
为了提高齿根弯曲疲劳强度,需要采取一些措施来改善齿轮的设计、制造和使用。
本文将介绍几种主要的措施。
1. 优化齿形设计齿轮的齿形设计对齿根弯曲疲劳强度有着重要影响。
通过优化齿形设计,可以减小齿根的应力集中程度,降低齿根应力,从而提高齿根弯曲疲劳强度。
具体方法包括合理选择齿形参数、采用适当的修形方法等。
2. 提高材料强度齿轮的材料强度直接影响齿根弯曲疲劳强度。
选择具有较高强度和良好的韧性的材料,可以提高齿轮的强度和抗疲劳性能。
此外,采用先进的热处理工艺,如渗碳、淬火等,还可以进一步提高材料的强度。
3. 控制制造质量制造质量是影响齿根弯曲疲劳强度的重要因素之一。
要提高齿根弯曲疲劳强度,需要控制齿轮的制造质量,避免出现缺陷和不良工艺现象。
采用先进的加工设备和工艺,加强制造过程的监控和控制,可以有效地提高制造质量。
4. 加强润滑和冷却良好的润滑和冷却条件对于提高齿根弯曲疲劳强度至关重要。
通过选择适当的润滑剂和冷却介质,并确保其充分供应和循环,可以降低齿根的摩擦和热量积聚,减小齿根的应力和温度,从而延长齿轮的使用寿命。
5. 合理设计载荷和工作条件合理的载荷设计和工作条件选择对于提高齿根弯曲疲劳强度至关重要。
在设计齿轮时,应根据实际工作条件和使用要求,合理选择载荷、转速等参数,避免超载和过高的工作温度,从而减小齿根的应力和疲劳损伤。
提高齿根弯曲疲劳强度的主要措施包括优化齿形设计、提高材料强度、控制制造质量、加强润滑和冷却,以及合理设计载荷和工作条件。
通过采取这些措施,可以有效地提高齿轮的抗疲劳性能,延长齿轮的使用寿命,确保机械传动的可靠性和安全性。
弯曲疲劳试验
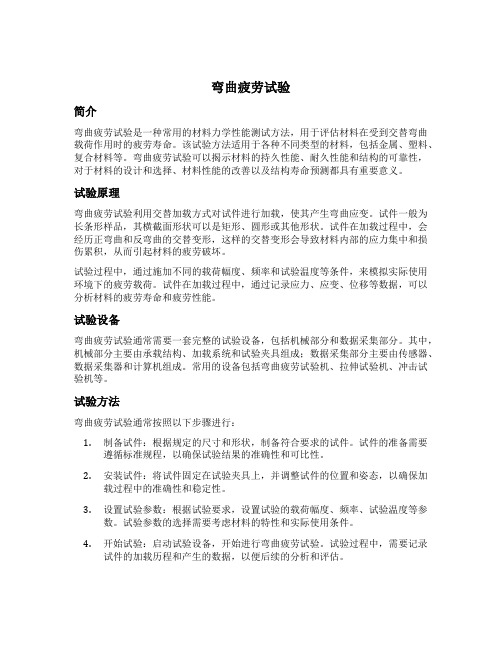
弯曲疲劳试验简介弯曲疲劳试验是一种常用的材料力学性能测试方法,用于评估材料在受到交替弯曲载荷作用时的疲劳寿命。
该试验方法适用于各种不同类型的材料,包括金属、塑料、复合材料等。
弯曲疲劳试验可以揭示材料的持久性能、耐久性能和结构的可靠性,对于材料的设计和选择、材料性能的改善以及结构寿命预测都具有重要意义。
试验原理弯曲疲劳试验利用交替加载方式对试件进行加载,使其产生弯曲应变。
试件一般为长条形样品,其横截面形状可以是矩形、圆形或其他形状。
试件在加载过程中,会经历正弯曲和反弯曲的交替变形,这样的交替变形会导致材料内部的应力集中和损伤累积,从而引起材料的疲劳破坏。
试验过程中,通过施加不同的载荷幅度、频率和试验温度等条件,来模拟实际使用环境下的疲劳载荷。
试件在加载过程中,通过记录应力、应变、位移等数据,可以分析材料的疲劳寿命和疲劳性能。
试验设备弯曲疲劳试验通常需要一套完整的试验设备,包括机械部分和数据采集部分。
其中,机械部分主要由承载结构、加载系统和试验夹具组成;数据采集部分主要由传感器、数据采集器和计算机组成。
常用的设备包括弯曲疲劳试验机、拉伸试验机、冲击试验机等。
试验方法弯曲疲劳试验通常按照以下步骤进行:1.制备试件:根据规定的尺寸和形状,制备符合要求的试件。
试件的准备需要遵循标准规程,以确保试验结果的准确性和可比性。
2.安装试件:将试件固定在试验夹具上,并调整试件的位置和姿态,以确保加载过程中的准确性和稳定性。
3.设置试验参数:根据试验要求,设置试验的载荷幅度、频率、试验温度等参数。
试验参数的选择需要考虑材料的特性和实际使用条件。
4.开始试验:启动试验设备,开始进行弯曲疲劳试验。
试验过程中,需要记录试件的加载历程和产生的数据,以便后续的分析和评估。
5.试验结束:根据试验设备的要求,试验结束后停止加载,并进行数据处理和分析。
记录试验结果,并根据需要进行统计和综合评价。
试验结果分析通过弯曲疲劳试验得到的结果可以进行多方面的分析,主要包括以下几个方面:1.疲劳寿命评估:通过疲劳曲线和疲劳寿命曲线,评估材料的疲劳寿命。
大齿轮和小齿轮齿根弯曲疲劳强度

大齿轮和小齿轮齿根弯曲疲劳强度下载提示:该文档是本店铺精心编制而成的,希望大家下载后,能够帮助大家解决实际问题。
文档下载后可定制修改,请根据实际需要进行调整和使用,谢谢!本店铺为大家提供各种类型的实用资料,如教育随笔、日记赏析、句子摘抄、古诗大全、经典美文、话题作文、工作总结、词语解析、文案摘录、其他资料等等,想了解不同资料格式和写法,敬请关注!Download tips: This document is carefully compiled by this editor. I hope that after you download it, it can help you solve practical problems. The document can be customized and modified after downloading, please adjust and use it according to actual needs, thank you! In addition, this shop provides you with various types of practical materials, such as educational essays, diary appreciation, sentence excerpts, ancient poems, classic articles, topic composition, work summary, word parsing, copy excerpts, other materials and so on, want to know different data formats and writing methods, please pay attention!大齿轮和小齿轮齿根弯曲疲劳强度引言大齿轮和小齿轮作为机械传动系统的核心组成部分,在工业生产中扮演着至关重要的角色。
弯曲疲劳试验方法

弯曲疲劳试验方法弯曲疲劳试验?嘿,这可是个超重要的测试方法!你知道不?先说说步骤吧!首先得准备好要测试的材料,就像要上战场的士兵,得把装备准备好。
然后把材料安装在特定的设备上,这一步可不能马虎,得像给宝贝找个安稳的家一样仔细。
接着启动设备,看着材料在那里被反复弯曲,就像在跳一支独特的舞蹈。
在这个过程中,要记录各种数据,这可关系到最后的结果呢!注意事项也不少哦!比如安装一定要牢固,不然材料飞出来咋办?那可就危险啦!还有数据记录要准确,不然就像在瞎忙活。
你说是不是?安全性和稳定性咋样呢?放心吧!只要按照正确的方法操作,就像走在平坦的大路上,不会有啥危险。
设备一般都很稳定,不会突然出啥幺蛾子。
就像一个可靠的伙伴,一直陪着你完成试验。
那弯曲疲劳试验都能用在啥场景呢?哎呀呀,可多啦!比如汽车零件的测试,这可重要啦!要是零件不耐用,在路上出问题咋办?弯曲疲劳试验就能帮我们找出那些不结实的家伙。
还有机械制造领域,各种零件都需要经过这个测试,就像给它们做一次严格的体检。
它的优势也很明显呢!能准确地检测出材料的性能,让我们知道哪些材料靠谱,哪些不行。
就像有一双火眼金睛,能看穿一切。
举个实际案例吧!有一家汽车制造公司,为了提高汽车的质量,对各种零件进行弯曲疲劳试验。
通过这个试验,他们发现了一些潜在的问题,及时进行了改进。
结果呢?汽车的质量大大提高,销量也蹭蹭往上涨。
你说,这效果牛不牛?再比如在建筑领域,一些关键的结构部件也需要进行弯曲疲劳试验。
要是这些部件不结实,房子塌了咋办?那可不得了!弯曲疲劳试验就能帮我们确保建筑的安全。
弯曲疲劳试验真的是个超棒的方法!它能让我们了解材料的性能,提高产品的质量。
赶紧用起来吧,让我们的生活更安全、更美好!。
- 1、下载文档前请自行甄别文档内容的完整性,平台不提供额外的编辑、内容补充、找答案等附加服务。
- 2、"仅部分预览"的文档,不可在线预览部分如存在完整性等问题,可反馈申请退款(可完整预览的文档不适用该条件!)。
- 3、如文档侵犯您的权益,请联系客服反馈,我们会尽快为您处理(人工客服工作时间:9:00-18:30)。
doi:10.1111/j.1460-2695.2010.01450.xIndustrial experiences of bending fatigue strength in table liner for cement millS.-H.BAEK,1S.-S.CHO 2and W.-S.JOO 31GraduateSchool of Mechanical Engineering,Dong-A University,840Hadan2-dong,Busan 604-714,Korea,2Department of Vehicle Engineering,College of Engineering,Kangwon National University,Samcheok,Gangwon-do 245-711,Korea,3Department of Mechanical Engineering,Dong-A University,840Hadan2-Dong,Busan 604-714,Korea Received in final form 17November 2009A B S T R A C T A table liner for the vertical roller mill has been used to grind natural limestone.Un-expected fatigue failure accidents have occurred during portland cement manufacturing process.The design life of a table liner is 4×107cycles,but the actual fatigue life of a table liner is 2×106to 8×106cycles.The fatigue crack of a table liner initiates from the outside edge of the grinding path of the limestone.When such a crack occurs,the table liner has to be replaced,and this requires 30%of the total maintenance cost of the vertical roller mill.Therefore,this study examines the fatigue failure of a table liner by plane-bending fatigue test,stress measurement test,finite element analysis and fatigue fracture analysis.Keywords bending fatigue strength;finite element analysis;Goodman diagram;stress-life curve;vertical roller mill.I N T R O D U C T I O NA vertical roller mill for cement production is far supe-rior than the existing tube mill with respect to energy efficiency.However,the table liner for a roller mill un-dergoes periodic repeated loading because it is a rotary machine.A fatigue function is expressed in terms of the stress ratio and mean ually,a fatigue function uses the Goodman diagram.1–3Stress ratio R in a fatigue cycle is defined as follows.4,5R =σmin σmax(1)where σmin is the minimum stress and σmax is the maximum stress in a fatigue stress cycle.Joo et al.6,7reported that the loads applied to a turbine blade are repeated bending load,torsional load and cen-trifugal load.According to X-ray fractography and the Goodman diagram,repeated bending stress is the major cause of turbine blade fatigue failure.Mandell et al.4,8,9proposed the Goodman diagram based on 13stress ratios.This method formulated the S-N behaviour considering the effect of mean stress.Correspondence :W.-S.Joo.E-mail:wsjoo@dau.ac.krFigure 1shows the photograph of the vertical roller mill analyzed in this study.The vertical roller mill consisted of two rolling tires and a table liner with eight steel plates.The table liner was made of SC450steel and had a plasma-sprayed WC-15%Co coating layer.The expected design fatigue life of the table liner was 4×107cycles,but the actual fatigue life was 2×106to 8×106cycles.The surface hardening layer of the table liner was subjected to wear and repeated bending tensile load.The prema-ture failure of the table liner can be ascertained from data on the contact fatigue.But,the surface hardening layer of the table liner was made of a big-particulate material.That is,the macrostructure of the material can relieve the stress concentration due to contact.A table liner is a rotary machine component with a very complex fail-ure pattern.Therefore,it is very difficult to simulate the in-service conditions of a table liner.In this study,the fatigue strength of a table liner is estimated by stress mea-surement,finite element analysis (FEA),bending fatigue test and the Goodman diagram.M A T E R I A L A N D E X P R I M E N T A L P R O C E D U R E SMaterial and test specimenFigure 2shows the failure pattern of the table liner exam-ined in this study.Crack initiated from the corner of the358c 2010Blackwell Publishing Ltd.Fatigue Fract Engng Mater Struct 33,358–364Fatigue & Fracture ofEngineering Materials & StructuresBENDING FATIGUE STRENGTH IN TABLE LINER FOR CEMENT MILL359Fig.1Vertical rollermill.Fig.2Sampling directions of tensile and bending specimens and fracture process of table liner.Fig.3Tensile test specimen configuration.table liner and grew in the cylindrical and axial directions.To test the mechanical properties of a table liner,the test specimen should reflect the damage pattern of the table liner.Therefore,the principal stress direction of the test specimen was made to coincide with the radial direction of the table liner.Six tensile test specimens and 18fatigue test specimens were prepared.Figure 3shows a tensile test specimen made according to ASTM E8M-94a.10An electro-mechanical system of 98kN capacity (Instron,model 1337,USA)was used to carry out the tensile tests.An extensometer was calibrated to an accuracy of under 2μm.It had a standard deviation of 2.5μm.11Poisson’s ratio was measured by a strain gauge of 5mm in length (Kyowa,KFC-5-D16-23,Japan)and a strain measurement device (Kyowa,UCOM-93,Japan).Table 1Mechanical properties of SC450steel PropertiesUnused Used Yield strength (MPa)238.2241.6Ultimate tensile strength (MPa)480474Poisson’s ratio 0.30.306Elongation (%)2422.7Young’s modulus (GPa)203206The test specimens were made of materials taken from an unused table liner and a fractured table liner,respec-tively.Table 1shows the results of the tensile test.The mechanical properties of the fractured table liner showed hardly any difference from those of the unused table liner.We could expect the table liner to be in an elastic state.Plane bending fatigue testFigure 4shows theSchenck-type bending fatigue test-ing machine (Mori testing machine,model 5171,Japan)and a fatigue test specimen.The configuration of the fa-tigue test specimen was determined,considering Peter-son’s stress concentration factor and the grip size of theFig.4Configuration of test specimen used in Schenck-type bending fatigue tests.c 2010Blackwell Publishing Ltd.Fatigue Fract Engng Mater Struct 33,358–364360S.-H.BAEK etal.Fig.5Fracture aspect of table liner for vertical mill.testing machine.12The stress concentration factor and curvature radius of the fatigue testing specimen were 1.05and 39mm,respectively.The maximum bending mo-ment,the loading speed and the test temperature were 20N m,1500rpm and room temperature,respectively.F A T IG U E S T R E N G TH A N A L Y SI S O F T H E T A B L E L I N E RFailure accident of the table linerThe diameter of the vertical roller mill was 6240mm,and the radius of the table liner was 2390mm.The driv-ing power and grinding volume of the limestone were 4250kW and 5.5MN/hr,respectively.Figure 5shows the failure pattern of the vertical roller mill.A table liner is used to prevent the mill table from being worn by lime-stone.The top of the table liner were made from SC450steel and the bottom of the table liner had a built-up welding layer.Figure 6shows the hardening layer crack that formed after the built-up welding.The average diameter of the cracks was 6.5mm.These cracks occurred during the welding process but not when the table liner was in service.Also,particulate cracks minimized the welding residual stress anddelamination.Fig.6Macrostructure of hardfacing layer in table liner.The surface hardening layer of the table liner had a life of less than 4×107cycles.If the life of the table liner exceeds 4×107cycles,the surface hardening layer would reach its wear limit.But,more than 80%of table liners are replaced by fatigue fracture and not by wear.Fatigue crack was initiated at the interface between the surface hardening layer and the base metal of the ta-ble liner.Also,the fatigue crack grew in the radial and the thickness direction from the edge of the table liner.Ahmed et al.13proposed that the rolling contact fatigue crack in a WC-15%Co sprayed material initiates due to the shear stress in the base metal as well as the difference in the mechanical properties between the coating layer and the base metal.Static structural analysisFigure 7shows the results of the plane bending fatigue test for stress ratio –1.Unfractured test conditions appear104105106107160180200220240260280300320S t r e s s a m p l i t u d e σ (M P a )Cycles to failure N (cycle)Fig.7S-N curve of SC450steel.c 2010Blackwell Publishing Ltd.Fatigue Fract Engng Mater Struct 33,358–364BENDING FATIGUE STRENGTH IN TABLE LINER FOR CEMENT MILL361Fig.8Finite element model of vertical rollermill.Fig.9Von-Mises stress distribution of table liner for vertical roller mill.upon more than 1×107cycles.The endurance limit obtained from the staircase test method was 185MPa.FEA of the vertical style roller mill was performed with ANSYS R8.0.14An 8-node hexahedron element was used.The numbers of elements and nodes were 88149and 100638,respectively.The finite element model exam-ined a quarter of the mill.The boundary condition for the mill was set to the axisymmetric condition.The ap-plied load was determined by using the static equilibrium relation between the rolling tire and the table liner (See Fig.8).Based on this assumption,the applied force on the inner and outer contact region is 1.1MN and 2.9MN,respectively.15,16Figure 9shows the FEA of the table liner.The maximum principal stress of 222.3MPa was obtained at the loading point.The minimum principal stress of 28.94MPa was obtained at 90◦from the loading point.To examine the FEA results,static stress measurement tests were performed by using a hydraulic pressurepistonFig.10Location of strain gauge used at static stress measurement.Photography of strain gauge attached to table liner.2400210018001500120090060030006080100120140160180200220240260280V o n -M i s e s s t r e s s (M P a )Radius from center of table (mm)Fig.11Radial stress distribution of the table liner.(RG 400/180-550).The strain gauge used in the stress measurement test was the delta rosette gauge (Kyowa-KFG-5-120-D17-11).The length of the strain gauge was set to 5mm considering the area of the table liner.Figure 10shows the attachment locations of the strain gauges.These locations were the “most dangerous”areas according to the FEA result and were most likely to cause failure accidents of the table liner.Strain gauges were attached at 15◦intervals from location A.Experimental principal stresses were obtained from the strain gauges.Figure 11shows the radial direction stress distribution in the table liner.A sine stress waveform was obtained in the radial direction.In the grinding path,the outside stress distribution was 1.3times higher than the inner stress distribution.Therefore,the stress concentrated on the outer grinding path.Stresses at 45◦and 90◦from location A appeared to be lower than the stresses at 0◦c 2010Blackwell Publishing Ltd.Fatigue Fract Engng Mater Struct 33,358–364362S.-H.BAEK et al.360330300270240210180150120906030P r i n c i p a l s t r e s s (M P a )Circumferential angle (degree)Fig.12Comparison of principal stress distribution of circumferential direction.from location A.From the above results,the maximum stress in the table liner was produced at location A on the outside grinding path.Figure 12shows the cylindrical directional stress distri-bution at intervals of 15◦around the maximum principle stress.The solid line is the maximum principal stress re-gression curve,which was generated from measurements given by the strain gauges,and the dotted line is the maxi-mum principal stress regression curve obtained from FEA.The difference between the FEA and strain gauge meth-ods themselves generated an error of 12%of the maxi-mum principal stress values.But,the distribution of the principal stress obtained from the FEA was similar with that obtained from the strain gauge.Therefore,the stress waveform of the table linerwas similar to that of the rotary machine such as a pump and gear.17The stress pattern of the table liner indicated a symmetric structure with re-spect to 180◦.The table liner was subjected to two repeat bending stress per one revolution.Figure 13shows the location of the maximum principal stress and the location of actual failure from the centre of the outside grinding path of the table liner.The maximum principal stress was measured experimentally at 10locations in the high stressC e n t e r o f v e r t i c a l r ol l e r m i l lFig.13Fracture position at the outside grinding path by visual examination and FEA.S t r e s s a m p l i t u d e σa (M P a )Mean stress σm (MPa)Fig.14Goodman diagram for table liner.Note that the Goodman line endpoint is the UTS from an axial tensile test.distribution area.The experimental maximum principal stress was located between 118mm and 358mm from the centre of the outside table liner.The analytic maximum principal stress was located 257mm from the centre of the outside table liner.Therefore,the maximum princi-pal stress region was found to be the area that fractured most frequently in the table liner.Fatigue strength estimationThe Goodman diagram 1–3,18is used to evaluate fatigue failure of parts under repeated load.Figure 14shows the operation condition of the table liner in the Goodman diagram.A safe domain was bounded by a limit line in the form of a straight line through two limit points taken from the ultimate tensile strength of 474MPa and the fatigue limit of 185MPa.The line was a solid line.Stress ratio in table liner is 0.5.The endurance limit line given above doesn’t consider the mean stress effect.Therefore,the effect of the mean stress on life can be estimated by ap-plying the modified Goodman expression to an equivalent reversed value for the stress at the notch.σar =σa1−σmσu (2)where σar is the equivalent completely reversed stress am-plitude,σm is the mean stress (=125MPa),σa is the stress amplitude (=125MPa)and σu is the ultimate strength (=480MPa).Fatigue notch factor k f =1is employed in this study because notch has a large radius and SC450steel is ductile material.The dotted line represents the endurance limit line in the form of a straight line through two limit points taken from the ultimate tensile strength of 474MPa and the equivalent completely reversed stress amplitude of 169MPa.c 2010Blackwell Publishing Ltd.Fatigue Fract Engng Mater Struct 33,358–364BENDING FATIGUE STRENGTH IN TABLE LINER FOR CEMENT MILL363The dash dotted line marked the region where the mean stress was equal to the stress amplitude;that is,this line means the region where stress ratio equals0.The mean stress and stress amplitude of the table liner were deter-mined from the maximum and minimum stress obtained by FEA.The table liner can move to the structurally dan-gerous area easily due to the in-service conditions because the stress condition of the table liner existed on the bound-ary of the Goodman diagram.The fatigue limit used in the Goodman diagram was measured in the controlled test conditions.The fatigue limit of a machine part depends strongly on its various conditions(surface roughness,material struc-ture,residual stress,and processing method).The cor-relation of the fatigue limit and some of the factors can be expressed by the empirical equation.To account for the important of these conditions,we employ a variety of modifying factors,each of which is intended to account for a single ing this idea,we may writeSe=C load C size C surf C temp C residual C reliab S e(3) where S e is fatigue limit of the table liner and S e is fatigue limit of SC450steel(R=−1).Cho et al.16proposed some strength reduction factors in the table liner.These are as follows.C load=1,C size=0.6,C surf0.814,C temp=1,C reliab=0.897(4)Residual stress in the surface layer of table liner plays an important role in the overall fatigue properties of the part.In this study,we may consider the induced residual stress at table liner surface as tensile stress.Grover et al.19 proposed that the residual stress factor C residual had0.52 for the worst welded test condition.We obtain C residual= 0.52.If we substitute above factors into Eq.(3),we obtainmodified fatigue limit38.5MPa.When all the modifying factors are considered,fatigue limit dropped by77.2%. From the above test result,the fatigue limit in the stress amplitude axis was set to38.5MPa.The fatigue limit line was represented with a dotted line in Fig.14.The results from FEA and strain gauge analysis exist in the dangerous area of the Goodman diagram.Therefore, the fatigue limit of the table liner should be determined by considering the fatigue strength reduction factors of the table liner.C O N C L U S I O N SThis study investigated the fatigue strength estimation of a table liner for a vertical roller mill by using the plane-bending fatigue test,stress measurement,FEA and the Goodman diagram.1Fatigue crack was initiated at the interface between the surface hardening layer and the base metal of the table liner.Also,the fatigue crack grew in the radial and the thickness direction from the edge of the table liner.2The table liner was subjected to two repeat bending stress per one revolution.3The table liner exists in the structurally“dangerous”area because the stress condition of the table liner exists out of the boundary of the Goodman diagram.4Fatigue strength reduction factors are useful in explaining the premature failure of the table liner. AcknowledgmentThis work was supported by the research fund of Dong-A University.R E F E R E N C E S1Goodman,J.(1899)Mechanics Applied to Engineering.Longmans,Green,and Co.,London.2Shen,M.-H.H.(1999)Reliability assessment of high cycle fatigue design of gas turbine blades using the probabilisticGoodman diagram.Int.J.Fatigue21,699–708.3Wang,S.,Dixon,M.W.,Huey,C.O.and Chen,S.(2000) The clemson limit stress diagram for ductile parts subjectedto positive mean fatigue loading.ASME J.Mech.Des.122,143–146.4Sutherland,H.J.and Mandell,J.F.(2004)Effect of mean stress on the damage of wind turbine blades.ASME J.Sol.Energy Eng.126,1041–1049.5Park,S.J.,Kim,K.S.and Kim,H.S.(2007)Ratcheting behaviour and mean stress considerations in uniaxiallow-cycle fatigue of Inconel718at649◦C.Fatigue Fract.Engng.Mater.Struct.30,1076–1083.6Hong,S.H.,Lee,D.W.,Cho,S.S.and Joo,W.S.(2005)A study on the failure analysis of turbine blade under fatigueload using X-ray n Pacific Conference onFracture and Strength;Advances in Fracture and Strength.Jeju,Korea,pp.1095–1101.7Lee,D.W.,Cho,S.S.,Hong,S.H.and Joo,W.S.(2008) Failure analysis of turbine blade in atomic power plant.J.Mech.Sci.Technol.22,864–870.8Mandell,J.F.,Samborsky,D.D.,Wang,L.and Wahl,N.K.(2003)New fatigue data for wind turbine blade materials.ASME J.Sol.Energy Eng.125,506–514.9Sutherland,H.J.and Mandell,J.F.(2005)Optimized constant-life diagram for the analysis of fiber glass composites used in wind turbine blades.ASME J.Sol.Energy Eng.127,563–569.10ASTM Standard E8M-94a.(1994)Standard Test Methods for Tension Testing of Metallic Materials.ASTM Standards Section3.3,pp.81–100.11ASTM E399-90.(1994)Standard Test Method for Plane-Strain Fracture Toughness of Metallic Materials.Annual Book ofASTM Standards.03.10,pp.407–437.12Peterson,R.E.(1953)Stress Concentration Design Fracture.John Willey&Sons,Canonsburg,PA,USA,p.44.13Ahmed,R.and Hadfield,M.(1999)Failure modes of plasma sprayed WC-15%Co coated rolling elements.Wear230,39–55.c 2010Blackwell Publishing Ltd.Fatigue Fract Engng Mater Struct33,358–364364S.-H.BAEK et al.14ANSYS Release8.0.(2003)ANSYS User’s and Theory Manual.ANSYS,Inc.New York,USA.15Baek,S.H.,Cho,S.S.,Kim,H.S.and Joo,W.S.(2006) Trade-off analysis in multi-objective optimization usingChebyshev orthogonal polynomials.J.Mech.Sci.Technol.20, 366–375.16Lee,D.W.,Cho,S.S.and Joo,W.S.(2008)Safety evaluation of table liner for vertical roller mill by modifiedfatigue limit.Eng.Fail.Anal.15,989–999.17Norton,R.L.(1999)Machine Design:An Integrated Approach.Prentice Hall,New Jersey,USA.18Kluger,K andŁagoda,T.(2004)Application of the Dang-Van criterion for life determination under uniaxialrandom tension–compression with different mean values.Fatigue Fract.Eng.Mater.Struct.27,505–512.19Grover,H.J.,Gordon,S.A.and Jackson,L.R.(1954)Fatigue of Metals and ernment Printing OfficeWashington,D.C.c 2010Blackwell Publishing Ltd.Fatigue Fract Engng Mater Struct33,358–364。