薄壁件
薄壁零件加工的特点

•摘要:在数控车加工过程中,经常碰到一些薄壁零件的加工。
本文详细分析了薄壁零件加工的特点、防止变形的工艺方法、车刀几何角度及切削参数的选择,结合在教学实践中的实例设计出加工方案。
关键词:薄壁零件工 ...•摘要:在数控车加工过程中,经常碰到一些薄壁零件的加工。
本文详细分析了薄壁零件加工的特点、防止变形的工艺方法、车刀几何角度及切削参数的选择,结合在教学实践中的实例设计出加工方案。
关键词:薄壁零件工艺分析加工方案1 薄壁工件的加工特点车薄壁工件时,由于工件的刚性差,在车削过程中,可跑产生以下现相。
1.1 因工件壁薄,在夹压力的作用下容易产生变形。
从而影响工件的尺寸精度和形状精度。
当采用如图1所示三爪卡盘夹紧工件加工内孔时,在夹紧力的作用下,会略微变成三角形,但车孔后得到的是一个圆柱孔。
当松开卡爪,取下工件后,由于弹性恢复,外圆恢复成圆柱形,而内孔则如图2所示变成弧形三角形。
若用内径千分尺测量时,各个方向直径D相等,但已变形不是内圆柱面了,这种现相称之为等直径变形。
1.2 因工件较薄,切削热会引起工件热变形,从而使工件尺寸难以控制。
对于线膨胀系数较大的金属薄壁工件,如在一次安装中连续完成半精车和精车,由切削热引起工件的热变形,会对其尺寸精度产生极大影响,有时甚至会使工件卡死在夹具上。
1.3 在切削力(特别是径向切削力)的作用下,容易产生振动和变形,影响工件的尺寸精度,形状、位置精度和表面粗糙度。
2 减少和防止薄壁件加工变形的方法2.1 工件分粗,精车阶段粗车时,由于切削余量较大,夹紧力稍大些,变形也相应大些;精车时,夹紧力可稍小些,一方面夹紧变形小,另一方面精车时还可以消除粗车时因切削力过大而产生的变形。
2.2 合理选用刀具的几何参数精车薄壁工件时,刀柄的刚度要求高,车刀的修光刃不易过长(一般取0.2~0.3mm),刃口要锋利。
2.3 增加装夹接触面如图3所示采用开缝套筒或一些特制的软卡爪。
使接触面增大,让夹紧力均布在工件上,从而使工件夹紧时不易产生变形。
浅谈薄壁件的机械加工
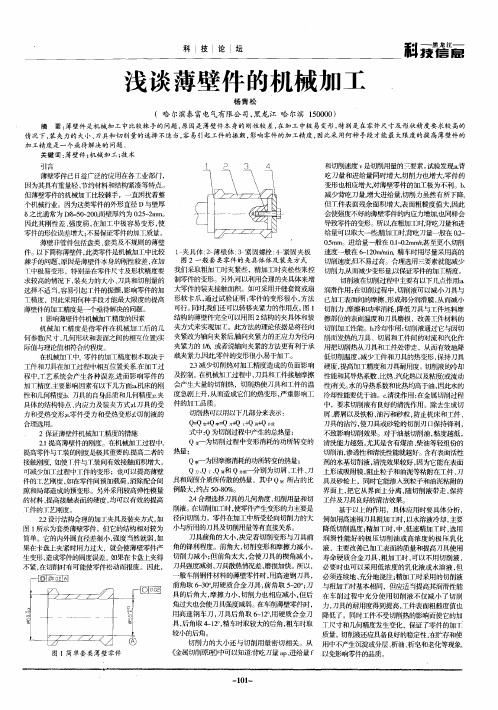
科 黑江 技信总 — 龙— — —ຫໍສະໝຸດ 浅谈薄壁件 的机械 加工
杨 青 松
(哈 尔滨泰富电气有限公 司, 黑龙 江 哈 尔滨 10 0 ) 50 0
摘 要: 薄壁件是机械加工 中比较棘 手的问题 , 因是 薄壁件本 身的刚性较 差,  ̄ - 原 在h . 中极 易变形 , y 特别是在零件尺寸及形状精度要求较高的 情况下 , 装夹力的大小、 刀具和切削量的选择 不适 当, 易引起 工件的振颤 , 容 影响零件的h .精度 ,  ̄- Y 因此采用何种手段才能最大限度的提高薄壁件的
加 工 精 度 是 一 个 亟待 解 决 的 问题
关键词 : 薄壁件 ; 机械加工 ; 术 技
1 2 3 4 和切削速度 v 是切削用量的三要素。 试验发现- 且 背 吃刀量和进给量同时增大, 切削力也增大, 零件的 薄壁零件已日益广泛的应用在各工业部门, 因为其具有重量轻 、 节约材料和结构紧凑等特点。 变形也相应增大对 薄壁零件的加工极为不利 。 . b 但薄壁零件的机械加丁比较棘手, 一直困扰着整 减少背吃刀量, 增大进给量, 切削力虽然有所下降, 个机械行业。因为这类零件的外形直径 D与壁厚 但T件表面残余面积增大, 表面粗糙度值大闺 此 会使强度不好的薄壁零件的内应力增加也 同样会 8 比通常为 D65 ~ 0, 之 r=0 2 0 而壁厚约为 0 5 2 . —mm。 2 因此其刚性差 、 强度弱 , 在加工中极容易变形 , 使 导致零件的变形。所以- 在粗加工时, 背吃刀量和进 =z = 零件的形位误差增大; 不易保证零件的加工质量。 给量可以取大一些; 精加工时、 背吃刀量一般在 O ~ 2 薄壁非管件包括盘类、 套类及不规则的薄壁 0r . m。进给量一般在 01 2 5 a . m 瞎£ 加- 至更小, 切削 2薄 3 4紧  ̄ mrn 精车时用尽量采用高的 2 a 件。 以下简称薄壁件 , 此类零件是机械加工中比较 卜夹 具 体 :- 壁 体 紧 固 螺栓 :- 固 夹板 速度一般在 6 10 /i, 图 2一 般 套 类零 件 的 夹具 体 体及 装 夹方 式 棘手的问题 , 原因是薄壁件本身的刚性较差 , 在加 切削速度, 但不易过高。合理选用三要素就能减少 [ 1中极易变形,特别是在零件尺寸及形状精度要 我们采取粗加—时夹紧些 ,精加工时夹松些来控 切削力从 而减少变形量, : 以保证零件的加工精度。 可以利用合理 的夹具体来增 求较高的情况下 , 装夹力的大小 、 刀具和切削量的 制零件的变形。另外, 切削液在切削过程中主要有 以下几 作用a 选择不适 当, 容易引起T件的振颤 , 影响零件的加 大零件的装夹接触面积。如可采用开缝套筒或扇 润滑作用 : 在切削过程中, 切削液可以减小刀具与 通过试验证 明: 零件 的变形很小 , 方法 已 工精度 ,因此采用何种手段才能最大限度的提高 形软卡爪 , 加工表面间的摩擦 , 形成部分润滑膜 , 从而减小 可行。 同时我们还可以转移夹紧力的作用点。图 1 切削力、 薄壁件的加 工精度是—个亟待解决的问题。 摩擦和功率消耗, 降低刀具与工件坯料摩 结构的薄壁件完全可以用图 2结构的夹具体和装 擦部位的表面温度和刀具磨损 ,改善工件材料的 1影响薄壁件件机械加下精度的因素 i f_ 机械加 精度是指零件在机械加工后的几 夹方式来实现自 T 。此方法的理论依据是将径向 切削加工性能。b . 冷却作用 : 切削液通过它与因切 夹紧后轴 向夹紧力的正应力为径向 削而发热 刀具 、切屑和工件间的对流和汽化作 何参数 寸 、 几何形状和表面之间的相互位置) 实 夹紧改为轴向 夹紧力的 1 , / 或者说轴 向夹紧的方法更有利于承 用把切削热从刀具和工件处带走 ,从而有效地降 6 际值与理论值相符合的程度。 易于加T。 在机械加工中 零件的加1精度根本取决于 载夹紧力闵此零 件的变形很小, 二 低切削温度, 减少工件和刀具的热变形 , 保持刀具 2 3减少切削热对加工精度造成的负面影响 硬度 , 工件和刀具在加工过程中相互位置关系. T过 在加 提高加_精度和刀具耐用度。 T 切削液的冷却 . 在机械加丁过程中, 刀具和T件接触摩擦 性能和其导热系数 、 程中, 丁艺系统会产生各种误差, 进而影响零件的 及控制 . 比热 、 汽化热以及粘度溅 流动 加T精度. 主要影响因素有 以下几方面:机床的刚 会产生大量的切削热,切削热使刀具和工件的温 性洧 关。 a 水的导热系数和比 热均高于油, 因此水的 从而造成它们的热变形 , 严重影响工 冷却性能要优于油。c 性和几何精度扣 刀具的自 . 身品质和几何精度 . 夹 度急剧上升, . 清洗作用: 在金属切削过程 具体的结构特点 、 内应力及装夹方式I刀具的受 件的加工品质。 d . 中, 要求切削液有良好的清洗作用 。除去生成切 切削热可以用以下几部分来表示: 力和受热变形. e . 零件受力和受热变形; 削液的 f = 切 屑、 磨屑以及铁粉、 油污和砂粒 , 防止机床和工件 、 QQ = = + 『Q』Q Q月Q + + 合理选用。 刀具的沾污 , 使刀具或砂轮的切削刃 口 保持锋利 , 式中: O为切削过程中产生的总热量; 2保证薄壁件机械加丁精度的措施 不致影响切削效果。对于油基切削油, 粘度越低, Q _ 为切削过程中变形消耗的功所转变的 清洗能力越强, 2 提高薄壁件的刚度。在机械加工过程中, . 1 尤其是含有煤油、 柴油等轻组份的 提高零件与T装的刚度是极其重要的. 提高二者的 热 量 : 切削油, l 渗透 生 和清洗陆能就越好。 含有表面活陛 Q 一为因摩擦消耗的功所转变的热量 ; 接触刚度, 如使T件与T装间 有效接触面积增大 , 剂的水基切削液 , 清洗效果较好, 因为它能在表面 Q月Q Q 、 、 和 Q —分别为切屑、 工件 、 刀 上形成吸附膜, 可减少加工过程中T件的变形 ;也可以提高薄壁 阻止粒子和油泥等粘附在工件 、 刀 件的工艺刚度, 如在零件间预加载荷 , 消除配合间 具和周围介质所传散的热量,其中Q 所占的比 具及砂轮上,同时它能渗入到粒子和油泥粘附的 约占5 -0 0. %。 8 隙和局部造成的预变形。另外采用较高弹l 生模量 例最大, 界面上 , 把它从界面上分离 , 随切削液带走 , 保持 2 - 4合理选择刀具的几何角度 、 切削用量和切 工件及刀具 良好的清洁效果。 的材料 、 提高接触表面的硬度 , 均可以有效 的提高 削液。在切削加丁时, 使零件产生变形的力主要是 T件 的丁艺 刚 度。 基于以上的作用 , 具体应用时要具体分析 , 径向切削 力。零件在加工中所受径向切削力的大 例如用高速钢刀具粗加工时 , 以水溶液冷却 , 主要 2 设i 构合理的加丁夹具及装夹方式。 . 2 结 如 图1 所示为套类薄壁零件,但它的结构相对较为 小与所用的刀具及切削用量等有直接关系。 降低切削温度 ; 精加T时, 低速精加T时 , 中、 选用 刀具前角的大小 , 决定着切削变形与刀具前 润滑性能好 的极压切削油或 高浓度 的极乐乳化 简单。它的内外圆直径差很小 , 强度当然就弱 , 如 切削变形和摩擦力减小, 液 ,主要改善已加工表面的质量和提高刀具使用 果在卡盘上夹紧时用力过大,就会使薄壁零件产 角的锋利程度。前角大, 但前角太大 , 会使刀具 的楔角减小 , 寿命硬质合金刀具 , 生变形, 造成零件的圆度误差。如果在卡盘上夹得 切削力减小; 粗加工时 , 可以不用切 削液 , 刀具散热情况差, 磨损船决。所以, 必要时也可以采用低浓度 的乳化液或水溶液 , 不紧, 在切削时有可能使零件松动而报废。因此, 刀具强度减弱, 但 般车削钢件材料的薄壁零件时 , 用高速钢刀具 , 必须连续地 、 充分地浇注; 精加工时采用 的切削液 前角取 6 3  ̄  ̄ 0 用硬质合金刀具, , 前角取 52 。刀 与粗加丁时基本相同, - 0; 但应适当提高其润滑性能 具 的后角大 , 摩擦力小 , 切削力也相应减小 , 但后 在车削过程中充分使用切削液不仅减小了切 削 角过大也会使刀具强度减弱。 在车削薄壁零件时, 力 , 刀具的耐用度得到提高, 工件表面粗糙度值也 用高速钢车刀 , 刀具后角取 6 1o ~2, 用硬质合金刀 降低了。同时工件不受切削热的影响而使它的加 具, 后角取 4 1。精车时取较大的后角 ,  ̄ 2, 粗车时取 T尺寸和几何精度发生变化,保证了零�
防止和减少薄壁件变形及振动的方法

防止和减少薄壁件变形及振动的方法
❖ 增加工艺肋
有些薄壁工件在其装夹部位特制几 个工艺肋,以增强此处刚性,使夹 紧力作用在工艺肋上,以减少工件 的变形,加工完毕后,再去掉工艺 肋,如图10-4-5所示。
图10-4-5 增加工艺肋减少变形
防止和减少薄壁件变形及振动的方法
❖ 浇注充分切削液
降低切削温度,减少工件热变形。
❖ 增加弹性心轴安装
胀力心轴胀力心轴依靠材料弹性变形所产生的胀力来固定工件,如图104-4所示。胀力心轴的圆锥角最好为30°左右,最薄部分壁厚6mm。为 了使胀力均匀,槽可做成三等分。长期使用的胀力心轴可用弹簧钢制成。 胀力心轴装卸方便,定心精度高,故应用广泛。
图10-4-4 用弹性胀力心轴装夹工件
❖ 应用轴向夹紧装置
车薄壁工件时,尽量不使用径向夹紧,而优先选用轴向夹紧的方法,如 图10-4-3所示。工件1靠螺母2的端面实现轴向夹紧,由于夹紧力F沿工 件轴向分布,而工件轴向刚度大,不易产生夹紧变形。
图10-4-3 薄壁套的夹紧 a)错误 b)正确 1-工件 2-螺母
防止和减少薄壁件变形及振动的方法
❖ 合理选择刀具的几何参数
精车薄壁工件时,刀柄的刚度要求高,车刀的修光刃不易过长(一般取 0.2~0.3mm),刃口要锋利。 • 外圆精车刀 kr=90°~93°,k`r=15°,αo=14°~16°,αol=15°, γo适当增大。 • 内孔精车刀 kr=60°,k`r=30°,γo=35°,αo=14°~16°, αol=6°~8°,λs=5°~6°。 • 刀尖圆弧半径要小。
防止和减少薄壁件变形及振动的方法
❖ 增加装夹接触面积
采用开缝套筒和特质的软卡爪,使接触面积增大,让夹紧力均布在工件 上,如图10-4-2所示,因而夹紧时工件不易产生变形。
航空薄壁件加工技巧
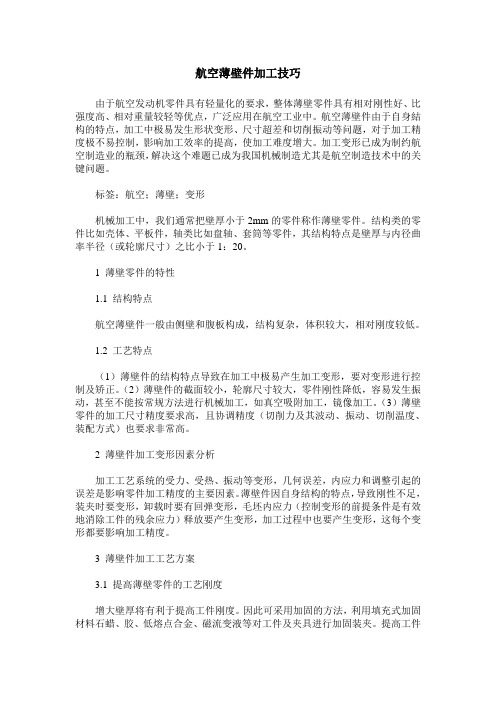
航空薄壁件加工技巧由于航空发动机零件具有轻量化的要求,整体薄壁零件具有相对刚性好、比强度高、相对重量较轻等优点,广泛应用在航空工业中。
航空薄壁件由于自身結构的特点,加工中极易发生形状变形、尺寸超差和切削振动等问题,对于加工精度极不易控制,影响加工效率的提高,使加工难度增大。
加工变形已成为制约航空制造业的瓶颈,解决这个难题已成为我国机械制造尤其是航空制造技术中的关键问题。
标签:航空;薄壁;变形机械加工中,我们通常把壁厚小于2mm的零件称作薄壁零件。
结构类的零件比如壳体、平板件,轴类比如盘轴、套筒等零件,其结构特点是壁厚与内径曲率半径(或轮廓尺寸)之比小于1:20。
1 薄壁零件的特性1.1 结构特点航空薄壁件一般由侧壁和腹板构成,结构复杂,体积较大,相对刚度较低。
1.2 工艺特点(1)薄壁件的结构特点导致在加工中极易产生加工变形,要对变形进行控制及矫正。
(2)薄壁件的截面较小,轮廓尺寸较大,零件刚性降低,容易发生振动,甚至不能按常规方法进行机械加工,如真空吸附加工,镜像加工。
(3)薄壁零件的加工尺寸精度要求高,且协调精度(切削力及其波动、振动、切削温度、装配方式)也要求非常高。
2 薄壁件加工变形因素分析加工工艺系统的受力、受热、振动等变形,几何误差,内应力和调整引起的误差是影响零件加工精度的主要因素。
薄壁件因自身结构的特点,导致刚性不足,装夹时要变形,卸载时要有回弹变形,毛坯内应力(控制变形的前提条件是有效地消除工件的残余应力)释放要产生变形,加工过程中也要产生变形,这每个变形都要影响加工精度。
3 薄壁件加工工艺方案3.1 提高薄壁零件的工艺刚度增大壁厚将有利于提高工件刚度。
因此可采用加固的方法,利用填充式加固材料石蜡、胶、低熔点合金、磁流变液等对工件及夹具进行加固装夹。
提高工件的工艺刚度还可以从下面几个方面着手,一是提高工件与工装接触定位面的加工精度和表面光洁度,二是提高接触刚度(增强接触面硬度或采用高弹性模量材料)。
薄壁工件的概念和作用

薄壁工件的概念和作用薄壁工件是指壁厚较薄的零件或制品。
在工业生产中,薄壁工件是常见的一种。
因为薄壁工件结构简单,重量轻,制造成本低,所以在很多领域都有广泛的应用,如汽车工业、建筑业、电子业、航空航天等工业领域。
薄壁工件的作用主要有以下几个方面:1. 减轻重量:薄壁工件的壁厚相对减薄,使得制品整体重量减轻。
比如,汽车的车身和发动机盖等就采用了薄壁工件的设计,以便减轻整车重量。
2. 提高强度:薄壁工件的设计可以在一定程度上增强其强度。
用薄壁工件替代厚壁构件,可以在保证强度的情况下减轻重量。
薄壁工件材料的选择和加工工艺的控制也可以增强其强度和刚度,以满足使用的要求。
3. 降低成本:薄壁工件的制造成本相对较低。
因为薄壁工件的制造涉及到的加工工艺比较简单,也需要的材料量比较少,所以可以在生产过程中降低成本。
4. 提升精度:薄壁工件的制造工艺和材料的选择能够保证其制品的尺寸和形状精度,漏水、漏气和漏电的情况得到了有效的控制。
5. 优化设计:薄壁工件的设计可以使得产品的结构更为紧凑、简单,具有更高的效率,具有降低噪音和振动的能力,同时也具有良好的节能减排性能。
尽管薄壁工件在很多领域都有广泛的应用,但是在其制造和使用过程中也面临着许多问题和挑战。
首先,薄壁工件的制造技术要求较高,生产过程中必须保证材料的质量和工艺的精细度。
其次,在使用过程中薄壁工件的结构易受环境因素的影响,容易出现变形和破损等问题。
因此,制造和使用薄壁工件需要注意加强工艺控制,提高产品的质量和使用寿命。
总之,薄壁工件是一种重要且常见的构件,具有重要的作用和意义。
通过提高薄壁工件的制造和使用技能,我们可以更好地应对生产和生活的需求,推动相关领域的科技进步和发展。
薄壁工件的加工特点(精)

薄壁工件的加工特点
2 3 2 2 5 3
游标卡尺 薄壁工件的加工特点
加工步骤 百分表 工件在花盘上的装夹
Produced by Мiss Хiè
薄壁工件的加工特点
1.因薄壁工件刚度很低,在夹紧力的作用下,容易产生 变形,常态下工件的弹性复原能力将直接影响工件的尺寸精度 和形状精度。如图所示,工件在夹紧后,因受夹紧力作用,略 微变形成弧形三边形,车孔后得到的是一个圆柱孔。当松开卡 爪取下工件后,由于工件的弹性恢复,外圆恢复成圆柱形,而 内孔则变成如图所示弧形三边形。这种用三爪自定心卡盘装夹, 车削薄壁件,当松开卡爪后,外圆为圆柱形内孔呈弧状三边形 的变形称为等直径变形。
Produced by Мiss Хiè
Produced by Мiss Хiè
薄壁工件的加工特点
2.因工件壁薄,由于切削热的产生,引起工件的受热 变形严重,加之加工条件的变化,使车削时工件受热膨胀变 形的规律不易掌握,使工件车削尺寸难以保证。对于线膨胀 系数较大的金属薄壁工件,影响尤为显著。 3.因工件壁薄,在车削过程中,薄壁工件在切削力(特 别是径向切削分力)的作用下,容易产生振动和变形,影响 工件的尺寸精度、形状精度、位置精度和表面粗糙度值。
Produced by Мiss Хiè
薄壁工件的加工特点
Hale Waihona Puke Produced by Мiss Хiè
薄壁工件的加工特点
2.因工件壁薄,由于切削热的产生,引起工件的受热 变形严重,加之加工条件的变化,使车削时工件受热膨胀变 形的规律不易掌握,使工件车削尺寸难以保证。对于线膨胀 系数较大的金属薄壁工件,影响尤为显著。 3.因工件壁薄,在车削过程中,薄壁工件在切削力(特 别是径向切削分力)的作用下,容易产生振动和变形,影响 工件的尺寸精度、形状精度、位置精度和表面粗糙度值。
薄壁零件的车削方式
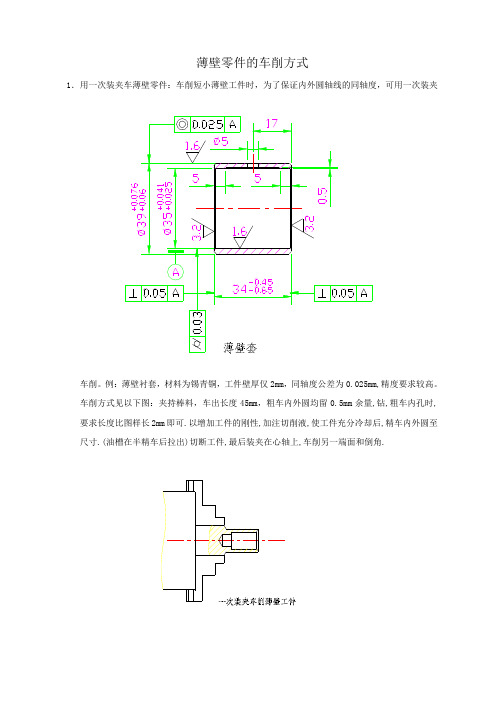
薄壁零件的车削方式1.用一次装夹车薄壁零件:车削短小薄壁工件时,为了保证内外圆轴线的同轴度,可用一次装夹车削。
例:薄壁衬套,材料为锡青铜,工件壁厚仅2mm,同轴度公差为0.025mm,精度要求较高。
车削方式见以下图:夹持棒料,车出长度45mm,粗车内外圆均留0.5mm余量,钻,粗车内孔时,要求长度比图样长2mm即可.以增加工件的刚性,加注切削液,使工件充分冷却后,精车内外圆至尺寸.(油槽在半精车后拉出)切断工件,最后装夹在心轴上,车削另一端面和倒角.2.用扇形卡爪及心轴装夹薄壁工件:例:薄壁套筒如图,车削方式:粗车留精车余量1~1.5mm,精车时,装夹在扇形软卡中,精车内孔及φ72H7,外圆φ及端面A符合图样要求,然后之内孔和大端面为基准,夹在弹性胀力心轴上,即可精车外圆.3.在花盘上车削薄壁工件:直径较大,尺寸精度和形位精度都较高的圆盘薄壁工件.可装夹在花盘上加工.车削方式:先装夹在三爪卡盘上粗车内孔及外圆,各留1~1.5mm余量,长度尺寸车至92++,并精磨两头面至长度92.然后装夹在花盘上精车内孔及外圆,精车内孔的装夹方式见图.先在花盘端面上车出一凸台,凸台的直径和工件之间留~1mm的间隙,(不用作定心).用螺栓,压板压紧工件端面,压紧力要均匀.找正后,即可车削φ132H7, φ262H7内孔及内端平面.精车外圆时的方式见以下图:将三点接触压板(压板上有三条槽以让开压板)适当压紧,松开并取下压板及螺钉,即可车削外圆,使之符合图样要求.上面的压紧方式,因为压紧力在轴向,因此不容易引发变形.4.在专用夹具上车削薄壁零件:如图,工件装上夹具后,当拧紧螺钉2时,压紧圈1便沿着斜面将工件压紧,即可车削工件的内孔,外圆及端面.5.增加辅助支承车削薄壁零件:车削内孔精度要求高的薄壁零件时,可采纳辅助支承来增加工件的刚性.6.增加工艺肋车削薄壁工件.在工件的装夹部位特制几根工艺支撑肋,使夹紧力作用在肋上,可减少变形.二.减少工件变形的方式:1.工件分粗精车,排除粗车时切削力过大而产生的变形,粗车后,使工件取得自然冷却,排除在精车时可能产生的热变形。
薄壁件的三种加工方法
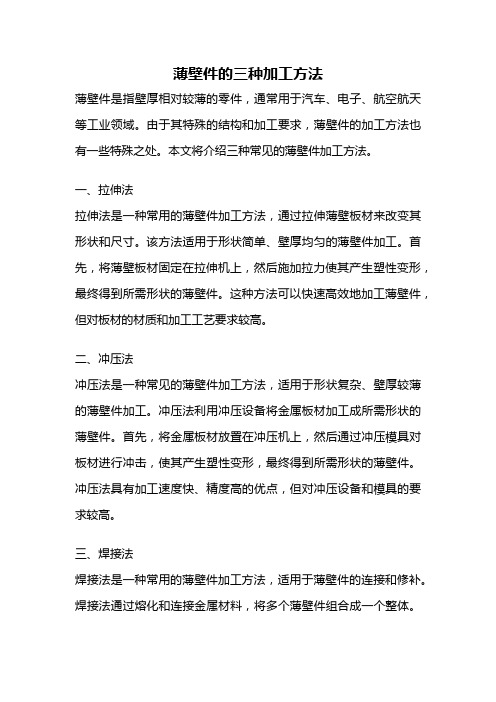
薄壁件的三种加工方法
薄壁件是指壁厚相对较薄的零件,通常用于汽车、电子、航空航天等工业领域。
由于其特殊的结构和加工要求,薄壁件的加工方法也有一些特殊之处。
本文将介绍三种常见的薄壁件加工方法。
一、拉伸法
拉伸法是一种常用的薄壁件加工方法,通过拉伸薄壁板材来改变其形状和尺寸。
该方法适用于形状简单、壁厚均匀的薄壁件加工。
首先,将薄壁板材固定在拉伸机上,然后施加拉力使其产生塑性变形,最终得到所需形状的薄壁件。
这种方法可以快速高效地加工薄壁件,但对板材的材质和加工工艺要求较高。
二、冲压法
冲压法是一种常见的薄壁件加工方法,适用于形状复杂、壁厚较薄的薄壁件加工。
冲压法利用冲压设备将金属板材加工成所需形状的薄壁件。
首先,将金属板材放置在冲压机上,然后通过冲压模具对板材进行冲击,使其产生塑性变形,最终得到所需形状的薄壁件。
冲压法具有加工速度快、精度高的优点,但对冲压设备和模具的要求较高。
三、焊接法
焊接法是一种常用的薄壁件加工方法,适用于薄壁件的连接和修补。
焊接法通过熔化和连接金属材料,将多个薄壁件组合成一个整体。
焊接法可以用于不同材质、不同厚度的薄壁件的连接,具有连接牢固、结构简单的优点。
常见的焊接方法包括电弧焊、气体保护焊、激光焊等。
焊接法的缺点是加工过程中会产生热变形和应力集中等问题,需要通过控制焊接参数和采取适当的焊接工艺来解决。
薄壁件的加工方法包括拉伸法、冲压法和焊接法。
不同的加工方法适用于不同形状、不同壁厚的薄壁件加工。
在实际应用中,需要根据具体的要求和条件选择合适的加工方法,以确保薄壁件的质量和性能。
- 1、下载文档前请自行甄别文档内容的完整性,平台不提供额外的编辑、内容补充、找答案等附加服务。
- 2、"仅部分预览"的文档,不可在线预览部分如存在完整性等问题,可反馈申请退款(可完整预览的文档不适用该条件!)。
- 3、如文档侵犯您的权益,请联系客服反馈,我们会尽快为您处理(人工客服工作时间:9:00-18:30)。
学位论文作者签名:姜涛
指导教师签名:陈明
日期: 2009 年 6 月 5 日
日期:2009 年 6 月 5 日
上海交通大学硕士学位论文
第一章 绪论
第一章 绪论
1.1 选题的意义和目的
波导器件是机载雷达非常重要的部件(图 1-1) ,作为传输微波工具的单、双脊 异型波导器件因具有工作频带宽、等效阻抗低等特性,在通讯微波发射设备、电子 对抗和超宽带雷达领域得到广泛应用。这类零件的加工精度、表面质量直接影响波 导器件和组件的电气性能,尤其是异型腔体类波导器件,而随着雷达技术的发展, 对这类零件的加工质量提出了更高的要求。因此,先进、可靠的工艺技术是实现其 设计性能的重要保证。波导器件中包含许多形状复杂的高精度薄壁型腔体类零件, 其特点是结构复杂、壁薄、精度要求高。对于该类零件的加工制造存在以下问题: 夹紧力、切削力以及切削热都会引起零件的变形,引起零件尺寸超差,造成零件的 废品率较高,严重影响了型号的研制周期。随着雷达技术的应用向毫米波甚至更高 频段发展,波导器件的结构尺寸越变越小,尺寸精度、形位要求及表面质量不断提 高,对波导器件的加工精度和质量提出了更高的要求。为了保证先进装备研制和生 产的顺利进行,必须对其关键部件—波导器件的精密加工进行研究。
4
上海交通大学硕士学位论文
第一章 绪论
1.2.2 高速切削技术及其发展现状 1.2.2.1 高速切削的概念 高速切削加工的理念从 20 世纪 30 年代提出以来,经历 50 多年的理论与实验研 究和探索推动了刀具和机床技术的研究与发展,到 90 年代以后,随着高速切削机床 和各种新型高速切削刀具等投入市场,使得高速切削加工技术在世界发达国家从理 论与实验研究进入工业应用阶段并迅速发展,它是先进制造技术的一项全新的共性 基础技术,具有广阔的应用前景。 高速切削理论[1]是 1931 年 4 月德国物理学家 Carl. J. Salomon 提出的。他指出, 在常规切削速度范围内,切削温度随着切削速度的提高而升高,但切削速度提高到 一定值后,切削温度不但不升高反会降低,且该切削速度值与工件材料的种类有关。 对每一种工件材料都存在一个速度范围,在该速度范围内,由于切削温度过高,刀 具材料无法承受,使切削加工不可能进行,称该区为“死谷” ,如图 1-4 所示。虽然 由于实验条件的限制,当时无法付诸实践,但这个思想给后人一个非常重要的启示, 即如能越过这个“死谷” ,在高速区工作,有可能使用现有刀具材料进行高速切削, 切削温度与常规切削基本相同,从而可以大幅度提高生产效率。
学位论文作者签名:姜涛
日期:2009 年 6 月 5 日
上海交通大学 学位论文版权使用授权书
本学位论文作者完全了解学校有关保留、使用学位论文的规定, 同意学校保留并向国家有关部门或机构送交论文的复印件和电子版, 允许论文被查阅和借阅。 本人授权上海交通大学可以将本学位论文的 全部或部分内容编入有关数据库进行检索,可以采用影印、缩印或扫 描等复制手段保存和汇编本学位论文。 保密□,在 本学位论文属于 不保密√。 (请在以上方框内打“√” ) 年解密后适用本授权书。
关键词:高速铣削,薄壁件,加工变形,刀具路径,有限元模拟
i
上海交通大学硕士学位论文
ABSTRACT
EXPERIMENTAL STUDY AND FINITE ELEMENT ANALYSIS ON DEFORMATION OF SIDE MILLING ALUMINUM THIN WALLED COMPONENT
3000
LF
3A21、 3A06 ,高抗蚀性、抗 疲劳性、良好的塑性 、焊接性
飞机油箱、油管
6000
LDBiblioteka 6A02, 6016, 硬度高,良好的耐腐蚀性 ,
制造发动机零件 、 接头
铸造铝合金
图 1-3 航空铝合金分类及应用 Fig.1-3 Classification and application of aerospace aluminium alloys
(1)硬铝:即铝-铜-镁系合金,是应用最为广泛的航空铝合金,以 2 系列铝合金为 主,常用 2024、2017A 等。该类铝合金强度较高,韧性、抗疲劳性较好,塑性好, 主要用来制造飞机蒙皮、隔框、翼肋等。 (2)超硬铝:即铝-锌-镁-铜系合金,以 7 系列铝合金为主,常用 7075、7A09、7750 等。该类铝合金强度极限和屈服强度高,承受载荷大,主要用来制造机翼上翼面蒙 皮、大梁等。 (3)防锈铝合金:以 3 系列铝镁合金为主,常用 3A21、3A06 等。该类铝合金具有 较高的抗蚀性、抗疲劳性、良好的塑性、焊接性,主要用来制造油箱、油管等。 (4)锻造铝合金:以 6 系列铝合金为主,常用 6A02,6016 等。该类铝合金具有硬 度高,良好的耐腐蚀性,主要用于制造发动机零件、接头等。 (5)铸造铝合金:该类铝合金具有比重小,抗蚀性、耐热性高的优点,主要用于制 造发动机机匣等。
上海交通大学 硕士学位论文 铝合金薄壁零件精密加工铝合金薄壁零件精密加工 姓名:姜涛 申请学位级别:硕士 专业:机械工程 指导教师:陈明;张永强 20090501
上海交通大学硕士学位论文
摘要
铝合金薄壁零件精密加工变形分析及实验研究 摘 要
高速加工以其切削力小、切削热变形低、切削速度高、单位时间去除材 料率大、加工精度高等特点,在切削加工弱刚度工件时与其他加工方式相比 有着明显的优势。本文依托某科研项目展开工作,基于高速加工理论,采用 理论分析、计算机模拟与试验相结合的方法,研究了波导类薄壁铝合金件侧 壁切削加工变形的问题。对加工参数的选择、加工路径优化等内容进行了详 细讨论。 本文针对典型薄壁件铣削加工中的变形问题,通过建立有限元变形分析 模型,结合铣削加工试验,并利用 DEFORM 有限元分析软件,获得典型薄壁件 加工变形的基本规律,得到一些具有指导意义的结论,为提高产品质量和进 一步研究控制薄壁件加工变形提供了依据。在理论分析和数值仿真的基础上, 针对薄板侧壁及薄壁腔体件,在不同的切削参数组下进行铣削加工试验,验 证了有限元仿真计算模型的有效性。
图 1-2 航空整体结构件对高效加工系统的要求 Fig. 1-2 Demands of machining aerospace monolithic structure components on HPM system
2
上海交通大学硕士学位论文
第一章 绪论
1.2 国内外研究现状分析
航空航天制造业是制造业重要的组成部分之一,是高新技术最为富集的产业, 代表了一个国家最高制造业水平和和技术实力。我国近年来在航空航天领域获得了 较快的发展, “神舟”系列载人航空飞船的成功研制, “翔凤”支线客机的首飞都标 志我国航空航天事业进入了一个快速发展的阶段。大量新材料、新技术首先在航空 制造业得到应用,为了降低飞机自重,提高结构强度,一些大型复杂结构零件,尤 其是主承力结构件(如飞机的大梁、隔框、壁板等)普遍采用了整体化结构设计, 结构整体化是新一代大型客机的发展趋势,已经成为现代先进大型飞机设计制造领 域的一个重要标志,对研发周期、生产效率和制造成本等具有非常重要的影响。采 用整体构件可以大幅降低连接装配工作量,零件数量少,整体重量可减重 10-30% , 密封性能好,结构整体性好。大型客机的带筋整体壁板、整体框、整体肋和梁缘条 等复杂形状构件的加工均采用高速切削技术。整体薄壁结构件的毛坯材料有 90%以 上由刀具切除,因而客观上要求材料去除率高,高速切削技术是近年来迅速崛起的 一项以高切速、大进给为主要特征的加工工艺,可以满足高效加工的要求;整体薄 壁结构件刚性差,切削力、切削热及切削振动等均容易导致零件变形,降低加工精 度和加工表面质量,而高速切削技术具有独特的加工机理和技术优势,如切削力大 幅度降低、切削热大部分由切屑带走从而降低切削温度,较高的主轴转速使得刀具 的激振频率避开薄壁结构工艺系统的振动频率范围,从而避免切削振动,所以高速 切削技术是航空整体薄壁零件实现高效精密加工的主要工艺,成为航空制造领域核 心关键技术。实现航空整体结构件的高精度、高效率和高可靠性的切削加工一直是 航空制造业面临的一个重要课题。
1.2.1 航空铝合金的性能及应用 铝合金按照生产工艺可分为变形铝合金和铸造铝合金两大类, 如图 1-3 所示。 航 空铝合金与普通铝合金相比,具有强度高、硬度高、韧性好、耐腐蚀、抗疲劳等特 点。用于飞机制造的航空铝合金主要有铝-铜-镁系合金与铝-锌-镁-铜系合金,详细应
3
上海交通大学硕士学位论文
KEY WORDS: high speed milling, thin walled component, machining deformation, tool path, finite element analysis
i
上海交通大学 学位论文原创性声明
本人郑重声明:所呈交的学位论文,是本人在导师的指导下,独 立进行研究工作所取得的成果。除文中已经注明引用的内容外,本论 文不包含任何其他个人或集体已经发表或撰写过的作品成果。 对本文 的研究做出重要贡献的个人和集体,均已在文中以明确方式标明。本 人完全意识到本声明的法律结果由本人承担。
ABSTRACT
Owing to its small cutting force, low cutting temperature, high cutting speed, large material removal rate and high machining precision, high speed machining gains advantages compared to other machining process in machining low rigid components. In this paper, deformations in side milling of aluminum alloy thin walled components were studied based on the high speed machining theory and the combination of simulations and experiments. Optimization of cutting tools and tool path were detail discussed. Focusing on the deformations in milling of typical thin walled component, analysis based on the finite element model and milling experiments were conducted to know the basic regulation of machining deformation. According to the results, the machining quality was improved and the deformations were controllable. Then, experiments were conducted on the thin walled components and thin walled pocket under different machining parameters so as to validate the simulation results and the deformation controlling strategy.