先进控制技术及其在典型化工过程中的应用
控制工程在化工生产中的应用

控制工程在化工生产中的应用随着科技的不断发展和应用,在化学工业的生产管理中,控制工程扮演着越来越重要的角色。
控制工程对化工生产的监控和调整能力,已成为化工领域提高生产效率、降低生产成本和优化生产质量的重要手段。
本文将阐述控制工程在化工生产中的应用,包括控制工程的基本概念、在化工领域的应用、以及控制工程未来的发展趋势等方面。
一、控制工程的基本概念控制工程是一种通过测量与判断、比较与估算、输出指令、控制对象的状态等多种手段,对实体物质、能量和信息进行测量、传输、转换和控制的工程系统。
简单地说,控制工程是一种系统化的管理方法,通过用计算机化系统进行物质流、能量流和信息流量的测量、分析、处理、比较和反馈等操作,对化工生产进行管理。
二、控制工程在化工领域的应用1、过程控制过程控制是指在工业生产过程中,通过控制工程,对原材料加工、物料流动、反应过程、分离纯化、产品包装等多个领域的生产过程进行管理和调整。
过程控制在化工制造过程中,可以实现给定的质量要求、工艺流程和生产目标的控制和管理,确保产品的质量和稳定性。
在化工领域,自动化控制系统的推广和应用,使得工厂在工艺设计、产品研发和生产流程中更加自然、流畅和高效。
2、质量控制化工行业对产品质量的要求很高。
化学物质的性质复杂多变,而影响产品质量的环节又很多,例如实验室的装置选择、仪器使用技术、样品处理、数据分析等等。
通过控制工程,可以实现对各种参数如温度、压力、流量等的实时测量、控制和记录,从而完善生产监控和管理。
例如,化工厂可以通过控制电量和温度来掌控反应过程,从而保证产生优质的化学品。
3、信息控制在化学生产中,信息控制也是一个重要的方面。
通过信息控制可以收集、分析和处理化工原料和信息,结合生产数据进行实时监控、处理和调整,以实现对化工生产的协调、协同和优化管理。
例如,化工厂可以通过控制工程的信息控制模块,对燃料消耗、产品产额、环境污染、质量管理等进行实时监控和数据处理,从而统筹管理化工生产。
DCS系统在化工工艺控制中的应用案例和创新展望

DCS系统在化工工艺控制中的应用案例和创新展望DCS系统(Distributed Control System,分散控制系统)是一种广泛应用于工业自动化控制领域的先进技术。
该系统通过将控制功能分布在多个节点上,并实现节点之间的数据交互和信息共享,有效提高了工艺控制的可靠性和稳定性。
在化工行业中,DCS系统的应用不仅改善了现有工艺的控制效果,还为创新工艺的发展提供了有力支持。
本文将通过介绍化工行业中DCS系统的应用案例,并展望其在创新工艺中的潜力,探讨DCS系统在化工工艺控制中的重要作用。
一、DCS系统在化工工艺控制中的应用案例1. 控制系统集成DCS系统通过集成多个子系统,实现对整个工艺流程的全面控制。
以炼油厂为例,DCS系统可以集成分离、转化、处理等多个子系统,并通过先进的控制算法和优化策略,实时调整操作参数,提高产品质量和生产效率。
2. 数据监测与分析DCS系统可以实时采集和监测诸如温度、压力、流量等工艺参数的数据,并进行实时分析。
通过与先进的数据分析算法相结合,DCS系统可以帮助工程师及时发现潜在故障和异常情况,并采取相应的措施,有效降低事故风险和生产成本。
3. 过程控制优化DCS系统通过模型预测控制、模糊控制和自适应控制等先进控制算法,实现对工艺过程的优化控制。
通过精确的控制和优化策略,DCS 系统可以降低能耗、减少废料排放、提高产品质量,进而提升整个生产过程的可持续性和环境友好性。
二、DCS系统在化工工艺创新中的展望1. 多元化生产随着市场需求的变化,化工工艺需要灵活多样的生产方式。
DCS系统具有良好的模块化和可扩展性,可以满足不同工艺的需求,支持多个产品同时生产。
未来,DCS系统将进一步发展,实现更加复杂的工艺控制和生产调度,以满足工艺创新的要求。
2. 智能化运维DCS系统可以通过集成人工智能和机器学习技术,实现对工艺过程的智能化运维。
通过大数据分析和模型建立,DCS系统可以预测工艺的变化趋势和故障潜在风险,并自动调整控制参数,实现智能化的运维管理。
化工生产中的过程控制技术与优化方案

化工生产中的过程控制技术与优化方案随着工业化进程的加速,化工行业在全球的发展越来越迅速,成为了各国经济的重要组成部分。
同时,随着全球经济的飞速发展,企业在化工生产过程中需要对技术进行不断地优化,提高生产效率,降低成本,保证产品的质量和安全。
因此,过程控制技术成为了必不可少的一部分。
本文将介绍化工生产中过程控制技术的应用和优化方案。
一、化工生产中的过程控制技术1.传统过程控制传统的化工生产过程控制措施主要使用PID控制技术,这种技术包括了比例、积分、微分等控制算法。
其基本思想是通过调节控制系统的输出信号以达到期望的工艺控制效果。
传统PID控制技术虽然简单易懂,但由于其控制精度不高,需要大量的工程经验和对特定过程的深入了解,因此需要人们不断探索新的过程控制技术以提高控制精度和抗干扰性。
2.先进过程控制技术进入21世纪以后,先进的过程控制技术逐步发展起来,如多变量模型预测控制(MPC)、先进的自适应控制(AAC)等。
同时,传感技术、人工智能的运用和数字化技术的发展等都为过程控制技术的升级提供了支撑。
这些技术的优势在于其能提高过程控制精度,抑制变量交互干扰,增大控制执行器的动态范围等。
二、化工生产过程控制技术的应用过程控制技术作为化工行业中的重要一环,对于生产效率的提升、运营成本的控制和产品质量的保证都有显著的作用。
通常,化工生产过程控制技术的应用可以从以下几个角度来考虑:1.质量控制随着化工行业的不断发展,对产品质量的需求也越来越高。
在化工生产过程控制中,通过数据采集、分析,实时跟踪工艺变量等手段,对生产中的关键环节进行精确控制和监控,以使产品质量稳定、一致。
2.成本控制成本控制是化工企业长期面临的重要问题。
随着劳动力成本、能源使用成本的不断攀升,对于如何控制成本、提高生产效率等问题,过程控制技术在其中起到了重要作用。
传统PID控制技术通过参数调整,最大限度地减少生产过程中的浪费和能源的消耗。
而高级过程控制技术则为企业在生产过程控制上提供了更精确的手段。
先进控制技术及其在典型化工过程中的应用

显 然 .采 用 先 进 控 制 技 术 改 善 PT 装 置 整体 的 A
操 作 水 平 .提 高 装 置 的 经 济 效 益 是 必 要 的 和 紧
迫 的。
PTA 装 置 先 进 控 制 系统 采 用高 级 多 变量 鲁
棒预 测 控制 软 件 AP C—A C n和智 能软 测量 与 工 dO
f
I
箧 M… 鲫
c e
维普资讯
该 系 统 的 成 功 投运 .明显 提 高 了 P 装 置 A T 的 平 稳 性 .改 善 了产 品 质 量 在 此 基 础 上 实 施
” 边 控制 ” 卡 .达 到 了 提 高 了 装 置 产 能 , 明显 降
建立 了氧化单元 4cBA 软测量模型 、精制单元
PTA 平 均粒 径 软 测量 模型 和 0D 的 工 艺 计 算 模 型 。 并 针 对 PTA 装 置 的 特 殊 要 求 .为 氧 化 单 元 的 负 荷 优 化 和 自动 升 降 负 荷 制 定 并 实 施 了特 殊
维普资讯
维普资讯
维普资讯
企 一 业 蠲 息 幽
通 过 0PC 标 准 接 口来 实 现 的 。典 型 化 工 过 程 先 进 控制系统硬件结构如 图 2所 示。 制 上 的 带 来 困难 。 同 时 .由 于 许 多 关 键 工 艺 参
数 .如 :反应 器 温 度 、尾 氧 等 .需 要 手 动 调 节 . 加上 4 一cB 等 关 键 质量 指 标难 以直 接测 量 .生 A
巨集 一 线 先 器 统 I
帅参
产过 程 中存在着 控制 不及 时和操作 不一致 等 问
题 . 因此 难 以保 证 装 置 长 期 平 稳 与 经 济 运 行 。
PLC在化工生产中的应用案例

PLC在化工生产中的应用案例随着现代工业的发展,电子技术也得到了许多重要的突破。
PLC(可编程逻辑控制器)作为一种面向工业环境的控制器,可以对整个生产过程进行自动化控制,提高生产效率和质量。
在化工行业中,PLC 也发挥着重要的作用。
PLC在化工生产中具有诸多的优势。
首先,PLC可以实现对化工生产过程中的各种参数进行精准的控制,如温度、压力、流量、液位等。
其次,PLC还可以快速地响应生产过程中的异常情况,并作出及时的调整,从而保证生产过程的平稳和可靠。
而且,PLC的模块化结构设计和可编程性质可以适应不同的化工生产需求,实现高度定制化的控制。
下面我们将具体介绍PLC在化工生产中的应用案例。
一、化工生产过程中的流程控制PLC可以实现化工生产过程中的流程控制。
例如,化工厂生产溶剂的过程中,需要对压力、流量、温度、液位等参数进行严格的控制,以保证生产过程的稳定性。
PLC可以实现这些参数的监测和控制,并且可以按照预设的流程进行连续的自动化生产。
例如,在生产酸洗溶剂时,PLC可以根据不同种类的物料和不同温度、压力等条件进行配比,并对过程中的液位、温度等参数进行精准的控制,从而实现高质量的生产。
二、化工产品的质量控制PLC可以实现化工生产过程中对产品质量的严格控制。
例如,在生产橡胶中,需要对反应过程中的温度、压力、流量等参数进行一系列的实时控制,以保证产品的质量和成品率。
PLC可以实时监测这些参数,并根据预设的控制方案进行调整。
而且,在生产过程中PLC还可以进行数据采集和分析,以检测过程中的异常和优化生产参数,从而进一步提高生产的质量和效率。
三、化工生产过程中的安全控制化工生产过程中安全工作十分重要。
PLC可以实现对生产过程中的安全控制,如防爆、防火、压力控制、液位控制等。
例如,在生产炼油过程中,需要对石油的净化、分离、加氢等复杂过程进行控制。
PLC 可以实时监测炉膛温度、压力、流量等参数,并根据预设的安全控制方案进行调整。
先进控制技术及其在典型化工过程中的应用

先进控制技术及其在典型化工过程中的应用随着科学技术的不断发展,控制技术在各个领域都得到了广泛应用。
在化工领域中,先进控制技术的应用对于提高生产效率、降低能耗、改善产品质量等方面都起到了重要作用。
本文将介绍先进控制技术的概念、发展现状,以及在典型化工过程中的应用。
一、先进控制技术的概念和发展现状先进控制技术是指利用先进的自动控制理论和技术手段,对复杂大规模系统进行优化控制的技术。
先进控制技术主要包括模型预测控制(MPC)、多变量控制(MVC)、智能控制、优化控制等。
这些技术能够充分考虑系统的非线性、时变性和大规模性,通过建立系统模型、预测系统未来的变化趋势,从而实现对系统的优化控制。
在化工领域中,先进控制技术的应用已经比较广泛。
随着计算机技术的不断进步和控制理论的不断完善,先进控制技术已经成为现代化工生产过程中不可或缺的一部分。
在许多化工生产过程中,特别是高温、高压、易燃易爆的工艺过程中,采用先进控制技术能够有效地提高生产效率、降低成本、减少事故风险,对于提高企业的竞争力和可持续发展具有重要意义。
1. 炼油过程中的模型预测控制炼油是化工行业中非常重要的一个环节,而炼油过程本身运行的复杂性和非线性使得传统的控制手段无法满足需求。
采用模型预测控制技术能够较好地解决这一难题。
模型预测控制技术通过构建系统的动态数学模型,预测未来一段时间内的系统行为,并基于这些预测进行优化控制。
在炼油过程中,利用模型预测控制技术能够实现对精细化工艺的精确控制,提高产品质量,降低能耗,增加生产效率。
2. 化工生产过程中的多变量控制在许多化工生产过程中,往往存在多个相互关联的变量,传统的PID控制往往不能满足对这些变量复杂关系的控制要求。
多变量控制技术能够同时考虑多个变量之间的相互影响,通过建立系统的数学模型,运用现代优化算法对系统进行优化控制。
在化工生产过程中,利用多变量控制技术能够实现对多个关键参数的协调控制,提高产品质量,降低原料消耗,降低排放量,达到节能减排的目的。
化工自动化控制系统的应用与发展

化工自动化控制系统的应用与发展化工自动化控制系统是利用先进的控制技术和电子技术对化工工艺过程进行实时监测、调节和控制的系统。
它能够有效地提高化工工艺的安全性、生产效率和生产质量。
随着科技的不断进步和化工工艺的不断发展,化工自动化控制系统得到了广泛的应用和发展。
应用方面,化工自动化控制系统已经被应用到各种化工工艺生产过程中,例如炼油、化纤、氯碱、煤化工、精细化工等。
它可以实时监测生产过程中的工艺参数,及时反馈给控制系统,使其能够及时地进行判断、调整和控制,从而达到精准控制生产过程的目的。
通过对化工过程的智能化控制,可以减少人为因素的影响,使得产品质量更加稳定、生产效率更高、制造成本更低。
同时,化工自动化控制系统也可实现远程控制和实时监测,使得工程师和管理人员能够实时掌握生产情况,做出及时的反应和决策,提高生产的安全性和效率。
发展方面,化工自动化控制系统的最大的发展趋势就是智能化、数字化和网络化。
智能化是指化工自动化控制系统通过对生产数据进行处理,可以根据实时数据动态调整控制系统的控制策略,提高自动化系统的反应和适应能力,进一步提升化工生产的稳定性和生产效率。
数字化则是指利用先进的软件技术,使得化工自动化控制系统的各个生产环节能够互相联系和交互,构成数字化的化工生产流程,从而减少人为干预和控制,提高化工生产流程的透明度和安全性。
网络化是指利用现代互联网技术,将化工自动化控制系统与其他信息系统集成,实现生产数据的共享和交互,成为一个智能化的生产过程信息体系。
总之,化工自动化控制系统在化工工艺生产过程中扮演着越来越重要的角色。
随着科技的不断发展和技术的不断升级,化工自动化控制系统也将会不断地提高其自动化、智能化和网络化的水平,为化工工业的高质量、高效率、高安全运作提供更好的保障。
先进过程控制技术在化工行业的应用前景如何
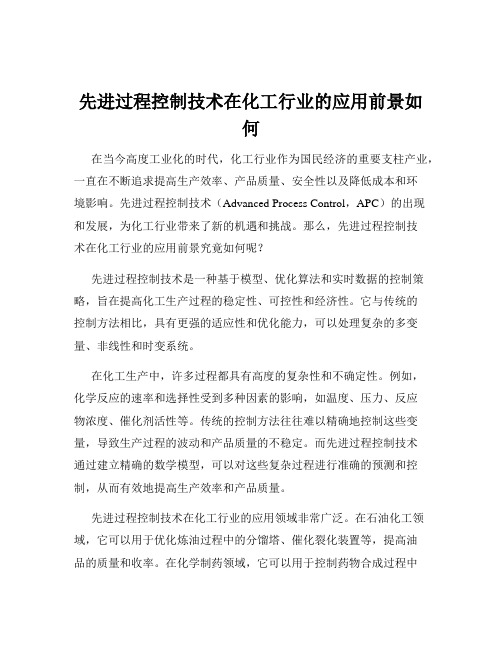
先进过程控制技术在化工行业的应用前景如何在当今高度工业化的时代,化工行业作为国民经济的重要支柱产业,一直在不断追求提高生产效率、产品质量、安全性以及降低成本和环境影响。
先进过程控制技术(Advanced Process Control,APC)的出现和发展,为化工行业带来了新的机遇和挑战。
那么,先进过程控制技术在化工行业的应用前景究竟如何呢?先进过程控制技术是一种基于模型、优化算法和实时数据的控制策略,旨在提高化工生产过程的稳定性、可控性和经济性。
它与传统的控制方法相比,具有更强的适应性和优化能力,可以处理复杂的多变量、非线性和时变系统。
在化工生产中,许多过程都具有高度的复杂性和不确定性。
例如,化学反应的速率和选择性受到多种因素的影响,如温度、压力、反应物浓度、催化剂活性等。
传统的控制方法往往难以精确地控制这些变量,导致生产过程的波动和产品质量的不稳定。
而先进过程控制技术通过建立精确的数学模型,可以对这些复杂过程进行准确的预测和控制,从而有效地提高生产效率和产品质量。
先进过程控制技术在化工行业的应用领域非常广泛。
在石油化工领域,它可以用于优化炼油过程中的分馏塔、催化裂化装置等,提高油品的质量和收率。
在化学制药领域,它可以用于控制药物合成过程中的反应条件,保证药品的纯度和活性成分的含量。
在聚合物生产领域,它可以用于控制聚合反应的温度、压力和物料配比,生产出具有特定性能的高分子材料。
随着化工行业的不断发展和市场竞争的日益激烈,企业对于提高生产效率和降低成本的需求越来越迫切。
先进过程控制技术可以通过优化生产过程,减少原材料的消耗和能源的浪费,从而降低生产成本。
同时,它还可以提高设备的利用率和生产能力,增加企业的经济效益。
此外,环保要求的日益严格也推动了先进过程控制技术在化工行业的应用。
通过精确控制生产过程中的污染物排放,可以有效地减少对环境的污染,实现化工行业的可持续发展。
然而,尽管先进过程控制技术在化工行业具有广阔的应用前景,但在实际应用中仍然面临一些挑战。
- 1、下载文档前请自行甄别文档内容的完整性,平台不提供额外的编辑、内容补充、找答案等附加服务。
- 2、"仅部分预览"的文档,不可在线预览部分如存在完整性等问题,可反馈申请退款(可完整预览的文档不适用该条件!)。
- 3、如文档侵犯您的权益,请联系客服反馈,我们会尽快为您处理(人工客服工作时间:9:00-18:30)。
先进控制技术及其在典型化工过程中的应用
先进控制技术(Advanced control technology)是指运用先进的计算机技术与自动化控制技术相结合,采用非线性控制、智能化控制和优化控制等手段,对复杂、非线性、时变的工业过程进行控制和优化,以实现系统的高效运行与优化。
在过去的几十年中,随着计算机技术、通讯技术、传感器技术等的不断发展,先进控制技术得到了广泛的应用和推广,被认为是现代化工过程优化和控制的核心技术之一。
在典型化工过程中,先进控制技术可以被广泛应用,以提高生产效率、产品质量和资源利用率,并减少能源消耗、环境污染等不良影响。
以下是几个典型的应用案例:
1. 炼油过程中的先进控制
炼油过程中包含多个复杂的化工过程单元,如裂化、脱硫、催化裂化等。
这些过程单元涉及到多个参数的调节和控制,如温度、压力、流量、浓度等。
石油精细化工厂通常采用先进控制技术进行整个生产过程的优化调度,以实现更高效的炼油过程、更高质量的产品和更优化的资源利用率。
化肥制造通常包括氨制造、尿素制造等过程,这些过程涉及多个参数的调节和控制,如温度、压力、流量、浓度等。
采用先进控制技术可以实现精确的控制和优化,提高生产效率并减少原材料和能源的消耗。
冶金工业中的高炉、炼钢等工艺过程涉及到复杂的非线性过程,很难通过传统的PID 控制实现精确控制。
采用先进控制技术可以将非线性控制、模型预测控制和优化控制等手段相结合,从而实现更高效的冶金生产过程,提高产品质量并减少资源消耗。
污水处理过程涉及到多个环节的控制和调节,如进水、沉淀、曝气、过滤、消毒等。
采用先进控制技术可以优化污水处理过程,提高处理效率和降低能源消耗、化学品消耗等成本,同时减少对环境的污染。
总之,先进控制技术在化工行业中的应用是广泛的,可以帮助工厂实现更高效的生产过程、更高质量的产品和更优化的资源利用率,从而降低成本和环境污染,提高整体竞争力。