木材干燥工艺
木材加工中的干燥工艺和控制
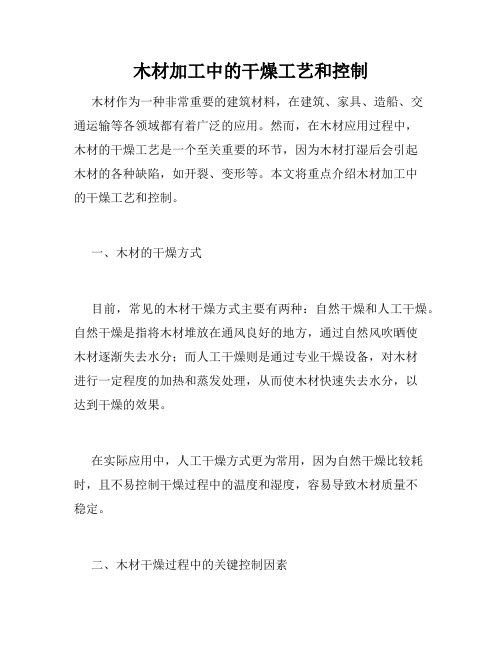
木材加工中的干燥工艺和控制木材作为一种非常重要的建筑材料,在建筑、家具、造船、交通运输等各领域都有着广泛的应用。
然而,在木材应用过程中,木材的干燥工艺是一个至关重要的环节,因为木材打湿后会引起木材的各种缺陷,如开裂、变形等。
本文将重点介绍木材加工中的干燥工艺和控制。
一、木材的干燥方式目前,常见的木材干燥方式主要有两种:自然干燥和人工干燥。
自然干燥是指将木材堆放在通风良好的地方,通过自然风吹晒使木材逐渐失去水分;而人工干燥则是通过专业干燥设备,对木材进行一定程度的加热和蒸发处理,从而使木材快速失去水分,以达到干燥的效果。
在实际应用中,人工干燥方式更为常用,因为自然干燥比较耗时,且不易控制干燥过程中的温度和湿度,容易导致木材质量不稳定。
二、木材干燥过程中的关键控制因素在进行人工干燥的过程中,需要掌握以下几个关键控制因素。
1.温度控制温度是木材干燥过程中的关键控制因素之一。
一般情况下,温度过低会造成干燥效率低下,时间过长影响生产效益;而温度过高则会导致木材变形、开裂等缺陷。
因此,在干燥过程中,需要掌握一个适宜的温度范围,使得木材能够快速干燥,同时又不会造成质量缺陷。
2.湿度控制湿度是影响人工干燥效果的另一个重要因素。
湿度过高会导致干燥不充分,木材质量下降;而湿度过低则会造成木材干燥过快,造成开裂等缺陷。
因此,在进行干燥过程中,需要控制干燥环境的湿度,确保在适宜的范围内。
3.压力控制在人工干燥过程中,还需要控制干燥设备的压力,以确保木材在干燥过程中不被压坏或变形。
同时,压力还可以调整干燥设备内空气的流动速度和方向,从而加快木材表面水分的蒸发速度,提高干燥效率。
4.干燥时间控制干燥时间是指木材从进入干燥设备开始,到完成干燥的时间长度。
干燥时间的控制需要结合温度、湿度、压力等因素进行考虑,以保证木材干燥的充分程度,并避免过度干燥导致木材的质量下降。
三、常见的木材干燥设备现代化的木材加工工厂中,一般采用以下几种常见的人工干燥设备。
木材干燥工艺

影响木材干燥速度之因子分析前言木材干燥时,其中所含水分(自由水,约束水,水蒸气)是利用不同的机构(me-chanism),经由不同的流通管道,自中心移至表面而蒸发。
在移动过程中,水分可能随木材中的实际状况自某一形式转换为另一形式(图2.8.)。
一般生材在常温下其约束水约占其全干重的30%,余者除极微量的水蒸气外,均为自由水。
以大叶桃花心木(Swietenia macrophylla)为例,其原始含水率约60%左右:故可粗估一半为约束水,一半为自由水。
若为台湾杉(Talwanla cryptomerioides),因其原始含水率高达150%以上,故其自由水亦增为约束水的4倍以上。
约束水的含量永远是一常数(30%左右)。
水分移动的速率完全受制于下列因素。
物理因素温度、相对湿度、和空气循环等物理因素对木材水分移动的影响乃一深奥而复杂的学科,本文仅简要叙述其基本原理。
(1)温度热(heat)是木材水分蒸发时必须获得运动能量(kinetic energy)的根源,同时水分蒸发的快慢全赖单位时间内热能的供应情形以及加热媒体(空气)吸收水分的能力而定。
干燥是由木材表面逐渐向内层进行,假如温度一定,则蒸发率会随木材水分的减少以及空气中蒸气压力的增加而逐渐降低。
所以,欲保持稳定的蒸发率,必须能使木材水分获得附加热能(additional energy),或者降低干燥窑内的蒸气压力。
此可藉提高温度(更多的热能)或降低相对湿度(较低的蒸气压力)以达成。
故欲使温度在50℃(122下)时之蒸发率等于70℃(158oF)之蒸发率,则必须尽量降低相对湿度;藉增加干燥空气的水分亲和力(moisture affinity)来补偿热能的减少。
但如此处理可能会形成剧烈的水分梯度,使木材发生干裂而招致“贬质”(degrade)。
另一方面,提高温度可加速水分的移动,虽需维持较高的湿度以防干裂,但不致过份影响干燥速率。
谈到温度,有一事应牢记于心,即在干燥过程中窑内之干球温度必高于木材温度。
木材高温高压蒸汽干燥工艺
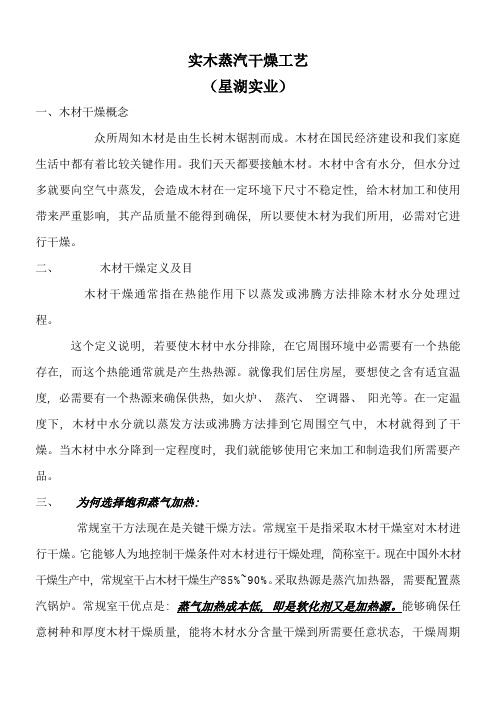
实木蒸汽干燥工艺(星湖实业)一、木材干燥概念众所周知木材是由生长树木锯割而成。
木材在国民经济建设和我们家庭生活中都有着比较关键作用。
我们天天都要接触木材。
木材中含有水分, 但水分过多就要向空气中蒸发, 会造成木材在一定环境下尺寸不稳定性, 给木材加工和使用带来严重影响, 其产品质量不能得到确保, 所以要使木材为我们所用, 必需对它进行干燥。
二、木材干燥定义及目木材干燥通常指在热能作用下以蒸发或沸腾方法排除木材水分处理过程。
这个定义说明, 若要使木材中水分排除, 在它周围环境中必需要有一个热能存在, 而这个热能通常就是产生热热源。
就像我们居住房屋, 要想使之含有适宜温度, 必需要有一个热源来确保供热, 如火炉、蒸汽、空调器、阳光等。
在一定温度下, 木材中水分就以蒸发方法或沸腾方法排到它周围空气中, 木材就得到了干燥。
当木材中水分降到一定程度时, 我们就能够使用它来加工和制造我们所需要产品。
三、为何选择饱和蒸气加热:常规室干方法现在是关键干燥方法。
常规室干是指采取木材干燥室对木材进行干燥。
它能够人为地控制干燥条件对木材进行干燥处理, 简称室干。
现在中国外木材干燥生产中, 常规室干占木材干燥生产85%~90%。
采取热源是蒸汽加热器, 需要配置蒸汽锅炉。
常规室干优点是: 蒸气加热成本低, 即是软化剂又是加热源。
能够确保任意树种和厚度木材干燥质量, 能将木材水分含量干燥到所需要任意状态, 干燥周期短, 设备操作灵活, 干燥条件易于掌握, 便于实现木材干燥生产机械自动化。
四、木材加工干燥优点(1)预防木材产生开裂和变形。
木材中水分在向空气中排除时, 尤其是当木材水分含量在木材纤维饱和点以下时, 就会引发木材体积收缩。
假如收缩不均匀, 木材就会出现开裂或变形。
若是将木材干燥到与使用环境相适应程度或使用要求状态, 就能保持木材体积尺寸相对稳定, 而且是经久耐用。
(2)提升木材力学强度, 改善木材物理性能和加工工艺条件。
木材的含水率与干燥工艺

测定方法:烘干法、电测法、 化学法等
控制目标:根据木材种类和用 途确定合适的含水率范围
控制措施:采用干燥设备、调 节温度和湿度等
效果评估:通过检测木材的含 水率、变形率和强度等指标来 评估控制效果
含水率标准:根据 木材种类、用途和 地区气候等因素确 定
控制方法:自然干 燥、人工干燥、化 学干燥等
干燥设备类型:蒸汽干燥、热风干燥、真空干燥等 技术参数:温度、湿度、风速、时间等 干燥效果:木材含水率、变形率、开裂率等 干燥工艺优化:根据木材种类、厚度、湿度等因素选择合适的干燥设备和技术参数
木材含水率与干燥 工艺的关系
含水率过高,干燥时 间延长,能耗增加
含水率适中,干燥效 果最佳,能耗最低
影响木材的化学性能: 含水率过高或过低都会 影响木材的耐腐蚀性、 耐久性等化学性能。
影响木材的加工性能: 含水率过高或过低都会 影响木材的加工性能, 如锯切、刨削、钻孔等。
影响木材的装饰性能: 含水率过高或过低都 会影响木材的装饰性 能,如涂饰、贴面等。
影响木材的环保性能: 含水率过高或过低都 会影响木材的环保性 能,如甲醛释放量等。
人工干燥的缺点:能耗高、成本高、对设 备要求高
自然干燥:利用自然 环境进行干燥,如阳
光、空气等
化学干燥:利用化学 药剂进行干燥,如防
腐剂、防霉剂等
人工干燥:利用人工 设备进行干燥,如干
燥室、干燥机等
物理干燥:利用物理 方法进行干燥,如真 空干燥、冷冻干燥等
预热阶段:将木材加热到一定的温度,使木材中的水分逐渐蒸发 等速干燥阶段:在恒定的温度和湿度下,木材中的水分迅速蒸发 降速干燥阶段:随着木材中的水分减少,蒸发速度逐渐降低 平衡干燥阶段:当木材中的水分达到一定的平衡状态时,干燥过程结束
木材干燥工艺流程
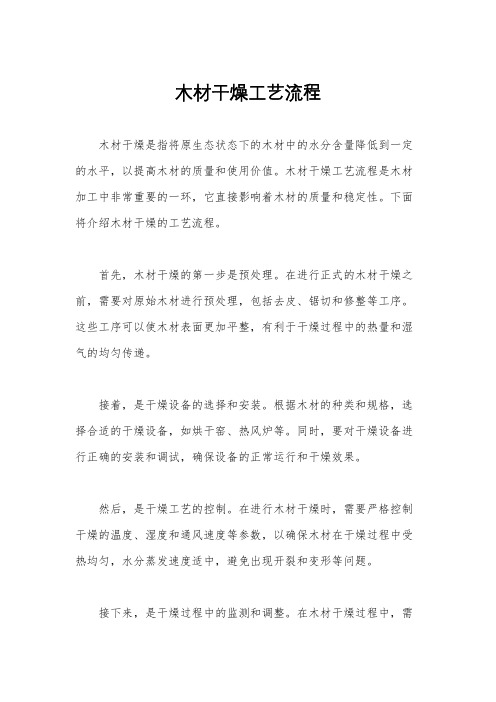
木材干燥工艺流程
木材干燥是指将原生态状态下的木材中的水分含量降低到一定的水平,以提高木材的质量和使用价值。
木材干燥工艺流程是木材加工中非常重要的一环,它直接影响着木材的质量和稳定性。
下面将介绍木材干燥的工艺流程。
首先,木材干燥的第一步是预处理。
在进行正式的木材干燥之前,需要对原始木材进行预处理,包括去皮、锯切和修整等工序。
这些工序可以使木材表面更加平整,有利于干燥过程中的热量和湿气的均匀传递。
接着,是干燥设备的选择和安装。
根据木材的种类和规格,选择合适的干燥设备,如烘干窑、热风炉等。
同时,要对干燥设备进行正确的安装和调试,确保设备的正常运行和干燥效果。
然后,是干燥工艺的控制。
在进行木材干燥时,需要严格控制干燥的温度、湿度和通风速度等参数,以确保木材在干燥过程中受热均匀,水分蒸发速度适中,避免出现开裂和变形等问题。
接下来,是干燥过程中的监测和调整。
在木材干燥过程中,需
要不断监测木材的含水率和温度变化情况,及时调整干燥参数,以保证干燥效果和木材的质量。
最后,是干燥后的处理和储存。
在木材干燥完成后,需要对木材进行冷却处理,使木材温度逐渐降低,然后进行包装和储存,以防止木材再次吸湿和变形。
总之,木材干燥工艺流程是一个复杂的过程,需要综合考虑原始木材的种类、湿度、温度和干燥设备的选择和控制等因素。
只有严格按照正确的工艺流程进行操作,才能保证木材干燥的效果和木材的质量。
木材烘干工艺
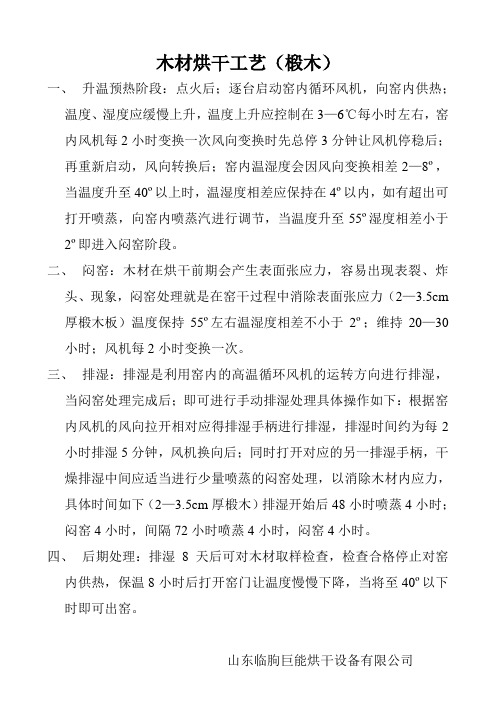
木材烘干工艺(椴木)
一、升温预热阶段:点火后;逐台启动窑内循环风机,向窑内供热;
温度、湿度应缓慢上升,温度上升应控制在3—6℃每小时左右,窑内风机每2小时变换一次风向变换时先总停3分钟让风机停稳后;
再重新启动,风向转换后;窑内温湿度会因风向变换相差2—8º,当温度升至40º以上时,温湿度相差应保持在4º以内,如有超出可打开喷蒸,向窑内喷蒸汽进行调节,当温度升至55º湿度相差小于2º即进入闷窑阶段。
二、闷窑:木材在烘干前期会产生表面张应力,容易出现表裂、炸
头、现象,闷窑处理就是在窑干过程中消除表面张应力(2—3.5cm 厚椴木板)温度保持55º左右温湿度相差不小于2º;维持20—30小时;风机每2小时变换一次。
三、排湿:排湿是利用窑内的高温循环风机的运转方向进行排湿,
当闷窑处理完成后;即可进行手动排湿处理具体操作如下:根据窑内风机的风向拉开相对应得排湿手柄进行排湿,排湿时间约为每2小时排湿5分钟,风机换向后;同时打开对应的另一排湿手柄,干燥排湿中间应适当进行少量喷蒸的闷窑处理,以消除木材内应力,具体时间如下(2—3.5cm厚椴木)排湿开始后48小时喷蒸4小时;
闷窑4小时,间隔72小时喷蒸4小时,闷窑4小时。
四、后期处理:排湿8天后可对木材取样检查,检查合格停止对窑
内供热,保温8小时后打开窑门让温度慢慢下降,当将至40º以下时即可出窑。
山东临朐巨能烘干设备有限公司。
木材烘干技术工艺技术
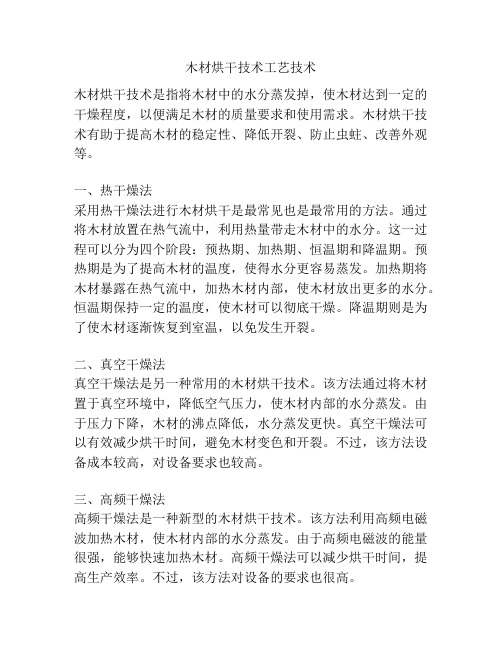
木材烘干技术工艺技术木材烘干技术是指将木材中的水分蒸发掉,使木材达到一定的干燥程度,以便满足木材的质量要求和使用需求。
木材烘干技术有助于提高木材的稳定性、降低开裂、防止虫蛀、改善外观等。
一、热干燥法采用热干燥法进行木材烘干是最常见也是最常用的方法。
通过将木材放置在热气流中,利用热量带走木材中的水分。
这一过程可以分为四个阶段:预热期、加热期、恒温期和降温期。
预热期是为了提高木材的温度,使得水分更容易蒸发。
加热期将木材暴露在热气流中,加热木材内部,使木材放出更多的水分。
恒温期保持一定的温度,使木材可以彻底干燥。
降温期则是为了使木材逐渐恢复到室温,以免发生开裂。
二、真空干燥法真空干燥法是另一种常用的木材烘干技术。
该方法通过将木材置于真空环境中,降低空气压力,使木材内部的水分蒸发。
由于压力下降,木材的沸点降低,水分蒸发更快。
真空干燥法可以有效减少烘干时间,避免木材变色和开裂。
不过,该方法设备成本较高,对设备要求也较高。
三、高频干燥法高频干燥法是一种新型的木材烘干技术。
该方法利用高频电磁波加热木材,使木材内部的水分蒸发。
由于高频电磁波的能量很强,能够快速加热木材。
高频干燥法可以减少烘干时间,提高生产效率。
不过,该方法对设备的要求也很高。
四、微波干燥法微波干燥法是一种较新的木材烘干技术。
该方法利用微波加热木材,使木材内部的水分蒸发。
由于微波的特殊性质,木材可以均匀受热,烘干效果更好。
微波干燥法可以快速烘干木材,保持木材的原色和形状。
不过,该方法的设备成本较高,操作复杂。
总之,木材烘干技术是一项重要的工艺技术,通过合理选择合适的烘干方法和设备,可以提高木材的质量和使用效果。
未来,随着科技的进步,木材烘干技术将会不断发展和创新,为木材行业带来更多的可能性。
木材烘干工艺流程
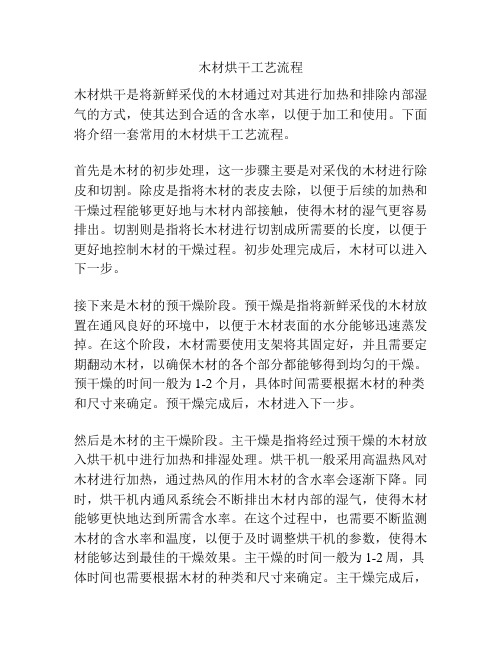
木材烘干工艺流程木材烘干是将新鲜采伐的木材通过对其进行加热和排除内部湿气的方式,使其达到合适的含水率,以便于加工和使用。
下面将介绍一套常用的木材烘干工艺流程。
首先是木材的初步处理,这一步骤主要是对采伐的木材进行除皮和切割。
除皮是指将木材的表皮去除,以便于后续的加热和干燥过程能够更好地与木材内部接触,使得木材的湿气更容易排出。
切割则是指将长木材进行切割成所需要的长度,以便于更好地控制木材的干燥过程。
初步处理完成后,木材可以进入下一步。
接下来是木材的预干燥阶段。
预干燥是指将新鲜采伐的木材放置在通风良好的环境中,以便于木材表面的水分能够迅速蒸发掉。
在这个阶段,木材需要使用支架将其固定好,并且需要定期翻动木材,以确保木材的各个部分都能够得到均匀的干燥。
预干燥的时间一般为1-2个月,具体时间需要根据木材的种类和尺寸来确定。
预干燥完成后,木材进入下一步。
然后是木材的主干燥阶段。
主干燥是指将经过预干燥的木材放入烘干机中进行加热和排湿处理。
烘干机一般采用高温热风对木材进行加热,通过热风的作用木材的含水率会逐渐下降。
同时,烘干机内通风系统会不断排出木材内部的湿气,使得木材能够更快地达到所需含水率。
在这个过程中,也需要不断监测木材的含水率和温度,以便于及时调整烘干机的参数,使得木材能够达到最佳的干燥效果。
主干燥的时间一般为1-2周,具体时间也需要根据木材的种类和尺寸来确定。
主干燥完成后,木材进入下一步。
最后是木材的冷却阶段。
冷却是指将经过主干燥的木材放入冷却室中进行自然冷却。
在这个阶段,木材的表面温度会逐渐降低,湿气也会进一步排出。
通过冷却,木材的含水率可以得到进一步的降低,以达到所需的含水率。
冷却的时间一般为1-2天,具体时间也需要根据木材的种类和尺寸来确定。
冷却完成后,木材的烘干过程就基本完成了。
综上所述,木材烘干的工艺流程包括初步处理、预干燥、主干燥和冷却。
通过这个工艺流程,新鲜采伐的木材可以在较短的时间内达到合适的含水率,以便于加工和使用。
- 1、下载文档前请自行甄别文档内容的完整性,平台不提供额外的编辑、内容补充、找答案等附加服务。
- 2、"仅部分预览"的文档,不可在线预览部分如存在完整性等问题,可反馈申请退款(可完整预览的文档不适用该条件!)。
- 3、如文档侵犯您的权益,请联系客服反馈,我们会尽快为您处理(人工客服工作时间:9:00-18:30)。
图 干燥基准推荐图
• 依据木材的初含水率,根据图确定介质的平衡含 水率。
• 当锯材的含水率在纤维饱和点以上时,介质的平 衡含水率取定值,一般在14%~18%的范围内。
• 木材的含水率在纤维饱和点以下时,介质的平衡 含水率状态随木材含水率的变化而变化,但它们 的比例关系表征干燥基准软硬程度的干燥梯度基 本保持不变,此值由树种和干燥速度要求确定 (P162),同时可得介质的平衡含水率值,结合 推荐的干燥温度由下图确定干燥基准。
木材的干燥特性一般包括:木材的基本密度、弦 径向干缩系数和比率、干燥速度;
与干燥有关的构造特征有:木射线的粗细和数量、 细胞壁的壁厚和其上纹孔的数量和性质、内含物 分布和数量等。
3)图表法 : 可以通过图表直接查到干燥基准。 这种方法是根据木材的含水率规定干燥介质的平衡含 水率和干燥梯度。
图 干燥基准推荐图
干燥前准备工作 干燥室壳体及设备的检查 锯材的堆积
干燥基准 干燥基准的分类 干燥基准的制定
室干过程的检测与干燥质量检测 干燥缺陷
一、干燥室壳体及设备的检查
➢ 干燥室壳体及大门的检查 全砖砌体干燥室、全金属壳体干燥室
➢ 通风机系统的检查 ➢ 供热系统的检查
加热器和蒸汽管路:是否漏气、开关和调整是否灵活 ➢ 调湿系统的检查
✓隔条的尺寸: 长度:与材堆的宽度一致。 宽度:35~45mm
表 板材厚度与隔条厚度之间的关系
板材厚度(mm)
隔条厚度(mm)
10
15
15-24
20
25-35
25
a
40-50
30
适合材间风速较高 的情况
50-70 70-100
35 40
30以下
13
30-40
20
b
40-60
25
适合材间风速较低
60-80
喷蒸管和进排气道:是否漏气及正常喷射、开关和调 整是否灵活 ➢ 回水系统的检查 疏水器、维修阀门、旁通阀控制系统的检查 ➢ 检测系统的检查 干湿球温度计、平衡含水率传感器、木材含水率传感
器、控制柜上的显示仪表、电流表、电压表和电度表
二、锯材的堆积
单元小材堆和轨车材堆
1.堆积方法: •1)板材与板材之间靠紧,不流空隙的密集排列:
松、云杉、冷杉、雪松
Ⅰ
Ⅱ
Ⅲ
Ⅴ
Ⅵ
桦木、白杨
Ⅱ
Ⅲ
Ⅳ
Ⅵ
-
落叶松
Ⅳ
Ⅴ
Ⅵ
Ⅶ
-
• (2)时间干燥基准
把整个干燥过程所需要的时间分成若干段,每一时 间段对应一种介质温、湿度。参考附录10.1。
基准 序号
5
干燥 阶段
1 2 3
干球 温度 ℃
90
100
110
湿球 温度 ℃
70 70 68
相对 湿度 %
43 29 18
30
的情况
80以上
40
• 对隔条的要求(经久耐用,厚度偏差为1~2mm 等)
• 隔条在高度方向上要垂直,并且应落在材堆底部
的支撑横梁上,以免板材因受到隔条的压力引起
弯曲。
• 隔条的根数与支撑横梁的根 数不同时,就必须采用棚架
隔条的方法,使隔条由横梁
上逐层依次地向正确位置移
动,如图中“跑条错半”,
上下层隔条不允许位移过多,
85
终了处理2h
90 86
➢ (4)干燥梯度基准 干燥梯度:指木材平均含水率与介质平衡含水率之比。
⒊ 干燥基准的选用及编制
➢⑴制定干燥基准的• 选用性质与该树种接近的已有干燥基准的树种的 干燥基准作为参考基准,并进行适当的修改,将 修改后的基准作为试验基准(初步干燥基准)。
上层隔条必须压在下层隔条
一半的位置上,防止全压在
下层板而引起板材的弯曲,
这样材堆的压力就可以通过
隔条由支撑梁承担。
• 隔条应伸出材堆侧面20-30mm,以增加材堆的稳 定性,减少材堆两边板材变形,且有利于码垛, 但隔条不能伸出材堆太长,以防止材堆不能进出 干燥室。
3.材堆堆积的注意事项及尺寸
✓材堆的外型尺寸可参考如下经验数据: 材堆外型:与门框之间的间隙为75~100mm; 与顶板或室顶的间隙为200mm;与侧墙之间的距 离为400~ 600mm、500~ 800mm(侧风型); 材堆底部与轨面的距离为300mm。
三、干燥基准
⒈干燥基准:在干燥过程中根据干燥时间和木材 的状态(含水率、应力)的变化而编制的干燥介 质温度和湿度变化的程序表。
⒉分类:
• (1)含水率干燥基准 在整个干燥过程中按含水率阶段的幅度划分成几 个阶段,每一阶段确定出相应的介质温、湿度。
• 双段或三段干燥基准 在整个干燥过程中根据含水率划分成二段或三段, 并确定相应的介质温、湿度;
• 波动干燥基准 含水率基准各阶段介质温度作“升温-降温-恒 温”反复波动变化;
• 半波动干燥基准 在干燥前段(M>25%)逐渐升高,而在后段作 波动变化。
表 双段干燥基准表
试
干燥介质参数
验
第一阶段(W>20%)
号
t
△t
φ
第二阶段(W<20%)
t
△t
φ
Ⅰ
130
30
0.35
130
Ⅱ
120
20
0.50
130
Ⅲ
115
15
0.58
125
Ⅳ
112
12
0.65
120
Ⅴ
110
10
0.69
118
Ⅵ
108
8
0.75
115
Ⅶ
106Leabharlann 60.81112
30
0.35
30
0.35
25
0.42
20
0.50
18
0.53
15
0.58
12
0.65
表 双段干燥基准选择表
树种
锯材厚度(mm)
22以下 22~30 30~40 40~50 50~60
• 如果在小型试验设备中进行,干燥基准可以从硬 开始,如果在大型设备中开始,干燥基准应从软 开始。
• 试验过程中应经常检测木材的含水率变化和应力 变化,并记录干燥缺陷发生的时间和程度。
➢2)分析研究法:
如果被干树种没有现成的干燥基准可以参考,干 燥基准的制定先从研究木材的干燥特性和构造特 征开始,然后用分析和试验相结合的方法在实验 室进行干燥工艺试验。
时间 系数
%
30
20
50
➢ (3)连续升温干燥基准
在锯材的干燥过程中,通过匀速升高介质的温度,使木材 温度和介质温度之间的温差为常数,从而使干燥速度基本 为常数。
表 连续升温基准表(50mm厚红松)
工艺过程 空气参数
开始
升温速度
最高
干球温度(℃)
45
湿球温度(℃)
37
1.5 ℃/h
118
1.0 ℃/h
适用各种周期式 强制循环干燥室
•2)板材与板材之间留有空隙:
适用各种周期式 强制循环干燥室
•3)在材堆中央部分留有较大空隙:
适用自然循环或弱 强制循环干燥室
⒉ 隔条(drying finger)
隔条的作用:使相邻两层锯材均匀隔开 1)在材堆高度方向上形成水平气流循环通道;2) 使材堆在宽度方向上稳定; 3)使材堆的各层木料相互挟持,防止和减轻木 材的翘曲。