钢材表面预处理通用工艺
钢结构表面处理及涂装作业

钢结构表面处理及涂装作业指导书编制部门:质量技术部钢结构制造有限公司二0一五年二月二十六日一、适用范围本作业指导书适用于建筑钢结构工程中钢结构的防腐蚀涂层涂装施工。
二、参考标准及规范1、《钢结构工程施工质量验收规范》50205-20012、《涂装前钢材表面锈蚀等级和除锈等级》89233、《钢结构防火涂料通用技术条件》14904、《钢结构防火涂料应用技术规程》24:90三、一般规定1、根据设计和施工图的要求,编制涂装工艺及技术交底等文件并进行技术交底。
技术资料应完整,操作人员经过技术培训。
2、构件成品或半成品,在涂装前表面预处理按设计和施工图规定的除锈等级进行,并达到规定的预处理等级。
3、各种底漆或防锈漆要求最低的除锈等级四、钢构件表面处理(抛丸)要求1、构件在进入抛丸机前应保持干燥且无油污。
抛丸机的抛丸直径为1.5~1.8。
构件的抛丸速度应在设备正常情况下控制在1.4m左右,摩擦试板及高强螺栓接触面的抛丸速度不应大于1.2m。
抛丸后的构件应色泽一致。
2、大型构件采用喷砂表面处理,砂采用石英砂或其它同等效果的材料,颗粒直径为1~4。
构件喷砂时空压机的工作压力应在62,喷砂速度应控制在42,对于摩擦试板及高强螺栓接触面喷砂速度应控制在53、涂装前的构件表面状态,应是在完全去切割边缘毛剌、焊渣和飞溅、不残留切割缺口、焊缝缺口、超标咬边、松散氧化皮、未包角焊和焊缝外形等缺陷,在除锈后若发现上述缺陷,必须在修补合格及表面预处理达到规定的等级并经专检确认合格后方可进行涂装。
4、构件的除锈等级、涂装漆膜厚度及涂装遍数应严格按照单项工程涂装工艺通知单进行。
5、涂装施工的环境应符合如下要求:环境温度宜为5—38。
C。
环境相对湿度不宜大于85%,或者钢材表面不应有结露,涂装后4小时内应保持免受雨淋。
在有雨、雾雪、风沙和较大灰尘时,禁止在户外涂装施工。
6、涂料的确认和贮存涂装前应对涂料名称、型号、颜色进行检查,确认是否与设计规定相符,产品出厂日期是否超过贮存期限,与规定不相符或超过贮存期的涂料不得使用。
钢材预处理工艺
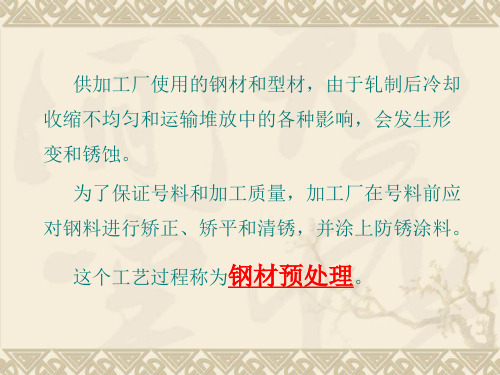
任务三:钢材预处理流水线
钢材预处理线简介:
二、表面清洁 表面清洁主要有升降刮板、吹扫机构、室体、除尘系统
等组成。 工作原理:钢板上料运行中,刮板可将钢板表面的块状
物及粉状废料分流至钢板两侧,从废料口进入废料桶收集, 钢板表面经刮扫后进入吹扫段,经喷吹后的钢板表面干净无 粉尘,达到钢板平前的清洁要求。喷吹过移产生的废气经除 尘器处理后达到环保排放标准要求。
覆盖层一般应满足下列基本要求:结构紧 密,完整无孔,不透电解质,附着力强,高强 度,耐磨,分布均匀。
任务三:钢材预处理流水线
任务三:钢材预处理流水线
任务三:钢材预处理流水线
加工厂把钢材输送、矫正、除锈、涂车间 底漆和烘干等工序所使用的机械装置,按工艺 流程用传送道连接起来,组成钢材预处理自动 流水线。
旋输送器、弹丸吹扫系统、供丸系统等组成。
任务三:钢材预处理流水线
钢材预处理线简介:
四、抛丸清理机 1、抛丸器 抛丸器是关键部件,对钢材清理质量及使用寿命,维护
都有很大影响。该系列机采用多台世界上先进的单园盘曲线 叶片高效抛丸器,弹丸由导入管流入,经分丸轮、定向套、 叶片抛出射出的高速密集弹丸,打击在工件的表面上,使工 件表面上的锈蚀层及其污物迅速脱落,获得一定粗糙度的光 洁表面,提高了漆膜与材料表面的附着力,提高了材料的抗 疲劳强度和抗腐蚀能力。该部件主要由叶轮、主轴及主轴承 座、分丸轮、定向套、护板、传动机构等组成。
任务三:钢材预处理流水线
钢材预处理线简介:
六、烘干室 烘干室是薄板箱形结构,它与喷漆室连接贯通。喷漆后的
工件在烘干室室内由板链输送进行烘干,由于工件与板链输送 辊之间没有相对运动,从而保证了工件下表面漆膜的完好。
烘干室上方设有通风除尘系统,被加热到40-50℃的热空气 管道闸门调节风量后送入烘干室内部,使被处理的工件达到漆 膜指干的要求。
船舶涂装通用工艺
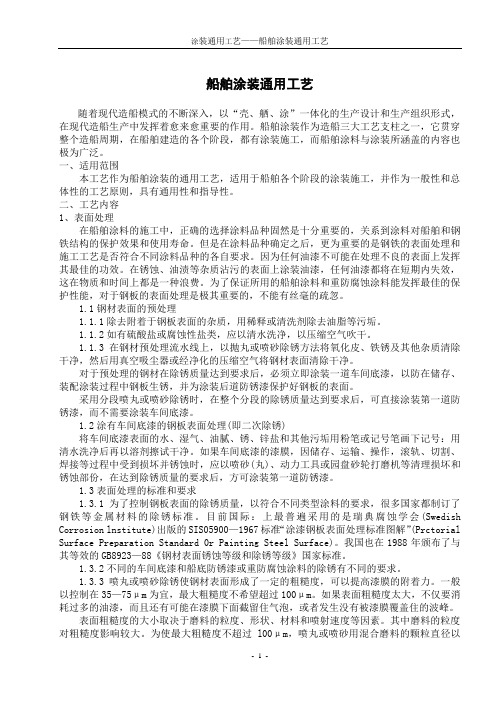
船舶涂装通用工艺随着现代造船模式的不断深入,以“壳、舾、涂”一体化的生产设计和生产组织形式,在现代造船生产中发挥着愈来愈重要的作用。
船舶涂装作为造船三大工艺支柱之一,它贯穿整个造船周期,在船舶建造的各个阶段,都有涂装施工,而船舶涂料与涂装所涵盖的内容也极为广泛。
一、适用范围本工艺作为船舶涂装的通用工艺,适用于船舶各个阶段的涂装施工,并作为一般性和总体性的工艺原则,具有通用性和指导性。
二、工艺内容1、表面处理在船舶涂料的施工中,正确的选择涂料品种固然是十分重要的,关系到涂料对船舶和钢铁结构的保护效果和使用寿命。
但是在涂料品种确定之后,更为重要的是钢铁的表面处理和施工工艺是否符合不同涂料品种的各自要求。
因为任何油漆不可能在处理不良的表面上发挥其最佳的功效。
在锈蚀、油渍等杂质沾污的表面上涂装油漆,任何油漆都将在短期内失效,这在物质和时间上都是一种浪费。
为了保证所用的船舶涂料和重防腐蚀涂料能发挥最佳的保护性能,对于钢板的表面处理是极其重要的,不能有丝毫的疏忽。
1.1钢材表面的预处理1.1.1除去附着于钢板表面的杂质,用稀释或清洗剂除去油脂等污垢。
1.1.2如有硫酸盐或腐蚀性盐类,应以清水洗净,以压缩空气吹干。
1.1.3在钢材预处理流水线上,以抛丸或喷砂除锈方法将氧化皮、铁锈及其他杂质清除干净,然后用真空吸尘器或经净化的压缩空气将钢材表面清除干净。
对于预处理的钢材在除锈质量达到要求后,必须立即涂装一道车间底漆,以防在储存、装配涂装过程中钢板生锈,并为涂装后道防锈漆保护好钢板的表面。
采用分段喷丸或喷砂除锈时,在整个分段的除锈质量达到要求后,可直接涂装第一道防锈漆,而不需要涂装车间底漆。
1.2涂有车间底漆的钢板表面处理(即二次除锈)将车间底漆表面的水、湿气、油腻、锈、锌盐和其他污垢用粉笔或记号笔画下记号:用清水洗净后再以溶剂擦试干净。
如果车间底漆的漆膜,因储存、运输、操作,滚轨、切割、焊接等过程中受到损坏并锈蚀时,应以喷砂(丸)、动力工具或园盘砂轮打磨机等清理损坏和锈蚀部份,在达到除锈质量的要求后,方可涂装第一道防锈漆。
钢材预处理0技术方案

一、设备用途本生产线主要用于钢板和各类型钢在加工前对其表面进行抛丸清理、喷漆和烘干。
钢材预处理的目的是为了清除钢材表面的锈蚀、氧化皮和污物,使钢材具有清洁和一定粗糙度的表面,以增强漆膜与钢材表面的附着力,从而提高产品的抗腐蚀能力和表面质量。
该设备一般用于工程机械、矿山机械、化工设备、压力容器、交通车辆、船舶制造及建筑型材等行业,用于提高产品的外观质量和其表面抗腐蚀能力。
二、设备主要技术规格1、处理工件规格:(1)处理钢板板厚:δ=5-60mm宽度: B≤3000mm长度: L=4000~12000mm(2)处理型材高度: H≤300mm长度: L=1600~12000mm2、输送辊道(1)辊道最大负荷: 2t/m(2)输送速度: 0.5-6.5m/min(变频无级调速)处理钢板速度: 1.5-5m/min处理型钢速度: 1-2m/min(3)驱动减速机: BWED2718-121-4(两台)(4)电机功率:4kw×2(5)滚轮直径: 180mm(6)滚轮有效宽度: 3500mm(7)辊道上平面高度:800mm(8)滚轮间距:抛丸室外635mm,抛丸室508mm3、抛丸清理机(1)抛丸器: 8台型号: Q035抛射速度: 72m/s抛丸量: 280kg/min电机功率: 18.5kw(2)纵向螺旋输送机:型号: GX300输送能力: 144t/h驱动装置: BWY22-29-7.5转速: 50rmp功率: 7.5kw(3)横向螺旋输送机:型号: GX300输送能力: 144t/h驱动装置: BWY22-29-5.5转速: 50rmp功率: 5.5kw(4)斗式提升机型号: D450提升能力: 144t/h料斗运行速度: 1.25m/s驱动装置: BWY22-17-11输出转速: 88rpm功率: 11kw(5)丸砂分离器分离能力: 120t/h分离区风速: 4-5m/s通风量: 10000m3/h驱动装置: BWY22-29-4功率: 4kw(6)清丸装置清扫滚直径: 900mm滚刷材质:四氟乙烯(进口刷丝)驱动装置: BLY18-23-3清丸风机: 9-19-6.3A风机功率: 15kw(7)清丸升降装置:提升高度: 500mm驱动电机: XWED63-289-3(电磁制动)电机功率: 3kw4、设备除尘系统(1)除尘通风量: 28000 m3/h(2)除尘器型号: MC-48(3)离心通引风机型号:4-72-8C(4)电机功率: 30kw(5)过滤风速: 0.4~0.8m/min5、自动喷漆装置:(1)喷漆形式:高压无气喷漆喷漆泵型号: 241-84R45:1高压喷涂机压力比: 45:1排量: 13L进气压力: 0.2~0.6MPa数量: 1(2)喷枪喷枪型号: 206-513自动喷枪喷枪到工件距离: 300mm(根据工件高度调整)喷枪数量: 4+1支(一把为手动喷枪,用于补漆或需要手动喷漆)(3)输送小车喷枪移动速度: 20m/min-50m/min(变频调速)数量: 2台(上下各一)(4)风动搅拌器: S-100型(5)G-01型油漆过滤器:25L6、烘干房(1)加热装置:采用燃油加热,30万大卡蒸汽加热器或电烘干加热风机功率: 15kw(2)通风机:结构:内置式耐热风机型号: GW-8C功率: 15kw(3)板链输送机:输送速度: 0.5~6m/min驱动装置: BWEY3322-121-5.5电机功率: 5.5kw7、漆物处理装置(1)风机:型号: B4-72 No8C左90º处理风量: 13000 m3/h风压: 1507Pa功率: 11kw(2)漆雾滤纸: 500×500×358、电气控制:采用控制面板集中控制,9、抛丸清理后的工件表面质量:Sa2.5级 GB8923-8810、喷漆漆膜厚度: 15-25µm(涂料为无机硅酸锌)11、烘干区温度: 40-70℃12、设备最大外形尺寸(长、宽、高):48000mm 、10000mm、10000mm13、年处理钢板量: 100000t14、设备最大功率:约280KW三、工作原理及工艺流程钢板被吊放至上料辊道,由上料辊道直接送到抛丸清理室进行清理,利用抛丸器高速抛射出的弹丸将工件表面进行清理;然后利用弹丸清扫装置(收丸刮板、清丸滚刷、高压吹管等)将工件表面的积丸和灰尘吹扫干净;除锈后的钢材直接进入喷漆室,通过装在上、下喷漆小车上的喷枪,将车间保养底漆涂在工件表面上,再进入烘干室,使钢材表面漆膜达到指干状态后由输出辊道输送出,进行下料。
钢材预处理

钢材表面的预处理航行于海洋上的船舶或海洋结构,一直处于强腐蚀性介质之中,其腐蚀问题十分突出。
由此而引起的经济损失是相当严重的。
因此,必须采取有效的防腐措施,以减少这种腐蚀损失。
对于船舶和钢结构来说,涂刷防护涂层,仍然是当今防止其腐蚀的主要手段之一。
钢材表面所涂防腐涂层的有效保护寿命与许多因素有关,如涂装前钢材表面处理的质量,所采用的涂料种类、涂膜厚度、涂装的工艺条件等。
其中钢材表面处理质量的好坏对涂层有效保护影响程度大50%多。
因此,钢材表面处理的质量控制是确保防腐涂层性能最关键的环节。
涂装前钢材表面处理,俗称除锈,他不仅除去钢材表面的铁锈,而且还包括除去覆盖在钢材表面的氧化皮、旧涂层以及沾污的油脂、焊渣、灰尘等污物。
此外,除锈之后钢材表面还形成一定的粗糙度。
所谓钢材表面的质量主要是上述污物的清除程度,或称“清洁度”,以及除锈之后钢材表面形成的粗糙度的大小。
国家标准GB8923是等效采用国际标准ISO8501-1: 该标准将未涂装过的钢材表面原始锈蚀程度分为四个“锈蚀等级”,将未涂装过的钢材表面及全面清楚过原有涂层的钢材表面除锈后的质量分为若干各“除锈等级”。
除锈前,钢材表面原始锈蚀状态对除锈后的表面外观质量评定具有一定影响。
同时不同锈蚀程度钢材,欲达到同一除锈等级,所花费的清理费用也不同。
因此,该标准根据钢材表面氧化皮覆盖程度和锈蚀状况将其分为四个等级,分别以A、B、C和D表示。
A 全面的覆盖着氧化皮而几乎没有铁锈的钢材表面;B 已发生锈蚀,并且部分氧化皮已经剥落的钢材表面;C 氧化皮已因锈蚀而剥落,或者可以刮除,并且有少量点蚀的钢材表面;D 氧化皮已因锈蚀而全面剥离,而且已普遍发生点蚀的钢材表面。
除锈等级,该标准对喷丸(砂)或抛丸除锈、手工和动力工具除锈以及火焰除锈的钢材表面清洁度规定了除锈等级,并且分别以字母“Sa”、“St”、和“F1”表示。
字母后面的阿拉伯数字则表示清除氧化皮、铁锈和油脂涂层等附着物的程度等级。
QB/CHEC·GY·004—2006 产品表面除锈、涂装通用技术条件

本标准主要起草人杨方源。 本标准审稿人叶阜、任改运、江兆华。 本标准由王汝贵总工程师批准。 本标准从 2006 年 1 月 1 日起实施。
2
QB/CHEC·GY·004—2006
1 应用范围 1.1 本标准规定了本公司金属结构件表面的除锈﹑涂装通用技术条件。如遇业主 有特殊要求;则按相关的合同和技术协议执行。 1.2 本标准适用于对涂装无特殊要求的卸船机,堆﹑取料机等产品的钢铁表面的 涂装。涂装防腐年限 3~5 年。 2 引用标准 2.1 GB/T3181-1995 漆膜颜色标准 2.2 GB/T8923-88 涂装前钢材表面锈蚀等级和除锈等级 3 技术要求 3.1 涂装前的预整理:铸﹑锻件及焊接结构件待涂装的表面应光整,应去除浇冒 口﹑披缝﹑飞边和毛刺 3.2 涂装前的表面处理:除锈等级为 Sa2.5 级。Sa2.5 为非常彻底的喷射或抛射除 锈。钢材表面应无可见的油脂﹑污垢﹑氧化皮﹑铁锈﹑飞溅和油漆涂层等附着物, 任何残留的痕迹应仅是点状或条纹状的轻微色斑。 3.3 卸船机,堆取料机等金属构件﹑附属结构,这些零部件,可以进喷丸间的, 都必须喷丸,如结构件太长,应调头分两次喷丸,以确保除锈质量。弹丸直径不 得大于 1.2mm。为增加除锈效果,可加入适量钢丝段,经喷丸后的构件表面应用 压缩空气吹净。 3.4 钢板预处理:堆﹑取料机等的门架﹑转台﹑臂架等,卸船机的大梁、门架等 主要金属结构件均需进行钢板预处理,在工艺及材料、辅料汇总表上注明,预处 理涂料为 704 无机硅酸锌车间底漆,干膜厚度 20μm,室外防腐期为 3 个月,因 此预处理板必须在 3 个月内进行制作,过期预处理失效。 3.5 涂料的选用:见表 1~3 涂料选用表。 3.6.油漆生产厂家有特殊要求有的,应遵照油漆生产厂家标准执行。
钢材预处理

钢材表面的预处理航行于海洋上的船舶或海洋结构,一直处于强腐蚀性介质之中,其腐蚀问题十分突出。
由此而引起的经济损失是相当严重的。
因此,必须采取有效的防腐措施,以减少这种腐蚀损失。
对于船舶和钢结构来说,涂刷防护涂层,仍然是当今防止其腐蚀的主要手段之一。
钢材表面所涂防腐涂层的有效保护寿命与许多因素有关,如涂装前钢材表面处理的质量,所采用的涂料种类、涂膜厚度、涂装的工艺条件等。
其中钢材表面处理质量的好坏对涂层有效保护影响程度大50%多。
因此,钢材表面处理的质量控制是确保防腐涂层性能最关键的环节。
涂装前钢材表面处理,俗称除锈,他不仅除去钢材表面的铁锈,而且还包括除去覆盖在钢材表面的氧化皮、旧涂层以及沾污的油脂、焊渣、灰尘等污物。
此外,除锈之后钢材表面还形成一定的粗糙度。
所谓钢材表面的质量主要是上述污物的清除程度,或称“清洁度”,以及除锈之后钢材表面形成的粗糙度的大小。
国家标准GB8923是等效采用国际标准ISO8501-1: 该标准将未涂装过的钢材表面原始锈蚀程度分为四个“锈蚀等级”,将未涂装过的钢材表面及全面清楚过原有涂层的钢材表面除锈后的质量分为若干各“除锈等级”。
除锈前,钢材表面原始锈蚀状态对除锈后的表面外观质量评定具有一定影响。
同时不同锈蚀程度钢材,欲达到同一除锈等级,所花费的清理费用也不同。
因此,该标准根据钢材表面氧化皮覆盖程度和锈蚀状况将其分为四个等级,分别以A、B、C和D表示。
A 全面的覆盖着氧化皮而几乎没有铁锈的钢材表面;B 已发生锈蚀,并且部分氧化皮已经剥落的钢材表面;C 氧化皮已因锈蚀而剥落,或者可以刮除,并且有少量点蚀的钢材表面;D 氧化皮已因锈蚀而全面剥离,而且已普遍发生点蚀的钢材表面。
除锈等级,该标准对喷丸(砂)或抛丸除锈、手工和动力工具除锈以及火焰除锈的钢材表面清洁度规定了除锈等级,并且分别以字母“Sa”、“St”、和“F1”表示。
字母后面的阿拉伯数字则表示清除氧化皮、铁锈和油脂涂层等附着物的程度等级。
钢材的表面预处理与矫正

矫正的方法与设备: 矫正可分为热矫和冷矫两种。通常都采用冷
矫,热矫仅在材料塑性较差或变形严重或设备能 力不足等不能采取冷矫的情况下使用。 对不锈钢类钢材一般不宜采用热矫,倘要必须热 矫,则必须采用相应的热处理措施。
砂布(纸)、砂轮等工具,进行敲、铲、磨、刮等除 掉锈污.这种方法的优点是简单易行、成本低;缺点 是劳动强度大、工作效率低、质量不稳定、劳动环 境差.
(二)机械除锈法 工业生产中常用的机械除锈方法包括:风动或电动砂轮、钢丝
刷、喷丸、喷砂等。其中喷丸除锈发展较快,已实现机械化操作, 效率高,除锈效果好。喷砂除锈法因粉尘污染环境,劳动条件差而 被逐渐淘汰。
钢材的矫正
钢材在使用前,其表面常存有不平、弯曲、扭曲、波浪形等缺陷,这 些缺陷使钢材在下料划线时,不可能获得所需要的下料精度,造成零件 尺寸的偏差,从而影响后续工序的顺利进行。
所以,钢材在下料和成形加工之前,必须对钢材进行矫正。
钢材变形的原因:
1.钢板轧制引起的变形 在轧制钢板时,当轧辊沿其长度方向受热不均匀,或者由于轧滚弯曲,轧辊调 整设备失常等各种原因,都将造成轧辊之间的间隙不一致,从而导致钢材在宽度 方向的压缩不均匀,于是钢材的每根纤维沿着长度方向的延伸就不相同。
2.运输、存放引起的变形 钢材在运输、存放过程中的不当也会产生局部皱曲。
变形的表现:表面凹凸不平、弯曲、扭曲、波浪形等
钢材的矫正原理: 矫正就是使钢板或工件在外力的作用下产生与原来变形相
反的塑性变形,以消除弯曲、扭曲、皱折、表面不平等变形, 从而获得正确形状的过程。
钢材的任何一种变形都是由于其中一部分纤维比另一部分纤维缩 得短些或是伸得长些所致。
- 1、下载文档前请自行甄别文档内容的完整性,平台不提供额外的编辑、内容补充、找答案等附加服务。
- 2、"仅部分预览"的文档,不可在线预览部分如存在完整性等问题,可反馈申请退款(可完整预览的文档不适用该条件!)。
- 3、如文档侵犯您的权益,请联系客服反馈,我们会尽快为您处理(人工客服工作时间:9:00-18:30)。
钢材车间预处理通用工艺
目的与适用范围
1范围
1.1本工艺适用于钢材,包括钢板和型材的抛丸预处理流水线。
2定义
2.1钢材进厂后,在加工前对钢材的原材料进行处理,除去表面的氧化皮和锈蚀,涂上车
间底漆以确保钢材在加工过程中不继续腐蚀,这一阶段的钢材表面处理,称之为钢材的表面预处理。
2.2造船用钢材预处理的方式有抛射磨料处理、喷射磨料处理和酸洗处理三种方式。
其中要
获得高效率的自动化流水作业,目前还只有抛射磨料处理方式。
抛射磨料处理亦称为抛丸处理。
二、工艺内容
1 钢板校平
造船用钢板,在运输过程中或经过长期的堆积后,会产生形变。
形变的钢板在分段落
料加工时会影响加工精度,形变严重的钢板将影响船体的线型。
因此,钢板的预处理之前或之后,应对钢板作校平处理。
2 预热
预热是为了在抛丸前将钢板升温,除去表面水分、部分油污,使钢板升温至一定的温度以利于喷漆后的干燥。
预热应使钢板升温至40 左右。
升温太低,不利于除去水分、油污,不利于而后喷涂的车间底漆的干燥;升温过高,则多耗能量,又易使车间底漆在干燥过程中产生起泡的弊病。
3抛丸及磨料
抛丸用于清除钢材表面的氧化皮与锈蚀,并使钢材产生一定的粗糙度。
理想的抛丸处理磨料是钢丸加钢丝段或钢丸加钢砂,前后两者的比例为1:1到1:2范围之内。
4 喷漆抛丸处理后的钢材表面需立即涂覆车间底漆。
涂漆以自动化方式进行。
5烘干
钢材喷漆后应进入烘干炉,促使快速干燥以利迅速搬运。
烘干炉可以远红外辐射或蒸
汽为热源,不能采用明火直接加热。
烘干炉应设排风装置,防止炉内溶剂气体积聚而引起燃爆事故。
6抛丸预处理流水线工艺要求
6.1车间底漆一般采用无机硅酸锌涂料。
6.2普通钢板及型材采用灰色的车间底漆,特殊强度的钢材则采用浅绿色车间底漆加以区
分。
6.3钢材在进行预处理前必须采用清洁剂擦洗及高压淡水冲洗等方法去除钢材表面的油
污等杂物(如有任何污物)。
6.4—般厚度介于6mm与 40mn之间的钢板,需经钢板预处理流水线抛丸队锈,除锈标准
为ISO8501-1: 1988中规定的Sa2.5级(除锈标准均采用ISO标准),粗糙度必须控制在40—70微米范围,相当于ISO8503Medium Grade至Course Grade的表面粗糙
度。
厚度小于6mm或大于40mm的钢板和型材一般采用喷砂处理。
6.5抛丸过程中钢板的走速在预处理时应根据钢板的不同锈蚀等级来调节钢板的走速。
A 级大于3m/min
B 级大于2.5m/min
C 级大于2m/min
D 级按实际要求而定
6.6由于在抛丸过程中,磨料磨擦和破损等原因,磨料会不断的消耗,所以要定期加入新
的磨料来补充,加入量应符合磨料的消耗量。
6.7为了与涂料的运输速度相配及防止过多的变叠层出现,在喷涂时需及时检查喷枪的扇型
面和喷枪速度,如需要应及时更换喷嘴。
6.8涂料的稀释和混合
6.8.1按不同的温度稀释涂料,如15C时,约加入专用稀释剂8%(土5C加入土1-2% 的
稀释剂)。
6.8.2基料和固化剂必须彻底的分开搅拌,然后慢慢地把固化剂倒入锌粉里,并不断地
搅拌,不能反相进行。
6.8.3在喷涂过程或在停转过程中,涂料必须不断地搅拌,直到用完为止。
6.8.4涂料必须在下列情况下进行施工:
温度范围:0-40 C 相对湿度:必须超过50%(若低于50%,用水雾喷在室内,以增加相对湿度)
6.8.5涂料混合后必须在20小时内(25C)用完,一旦超过使用时间,则此涂料不能使
用。
6.9加热装置的调节
6.9.1加热装置的调节是按照从加热区域出来的温度而定,钢板温度不能超过40C (如果
温度过高,将会引起涂料的开裂)。
6.9.2钢板不能放在加热区域内超过4分钟,如果是进行修补,则需待钢板出来后进行修
补,但钢板温度不能超过40°C。
7车间底漆的修补
7.1钢板或型钢车间底漆漏涂的地方,必须进行修补。
7.2修补前钢板表面必须无油脂,污物等,并且修补前是干燥的。
7.3修补用涂料也必须搅拌,防止锌粉可能沉积在漆桶的底部。
8磁性铁盘
由于钢板从流水线中出来,涂料不能完全固化,因此必须检查磁性吸铁盘的清洁情况,确保其无油脂、油腻,以防污染已涂好的表面涂层。
9车间底漆的检验方法
9.1检验车间底漆露底的方法
9.1.1用放大镜观察漆膜表面
9.1.2用100*400的玻璃片喷涂后,对光观察透明度
9.2测量车间底漆膜厚的方法
9.2.1用70*300 平整光滑的铁片置于钢板上,喷涂干燥后,测量出其表面上的干燥厚
度,其数值即被认为是钢板表面的漆膜厚度。
9.2.2用干膜测厚仪直接测量干燥后的钢板表面的漆膜厚底,其数值应为真实膜厚的60%左
右。