圆形支座铸造工艺设计 (2)
圆筒铸造方案

圆筒铸造方案1. 引言本文档旨在提供一个圆筒铸造方案的详细描述,方便相关人员了解铸造过程的步骤和要求。
圆筒铸造是一种常见的铸造工艺,适用于制造各种圆筒形状的零部件。
本文将从铸模设计、原材料准备、熔炼操作、铸造工艺流程等多个方面进行介绍。
2. 铸模设计铸模设计是圆筒铸造的第一步,合理的铸模设计能够保证铸件的质量和尺寸精度。
下面是一些铸模设计的要点:•圆筒模具形状:圆筒模具应根据所需铸件形状进行设计,包括底部和顶部的开孔,以方便砂芯的设置和取出。
•砂芯设计:根据铸件的中空结构,需要在铸模中设置砂芯。
砂芯应具有足够的强度和耐高温性能。
•铸道和浇口设计:铸道和浇口的设计要考虑到金属液的流动和进入铸件的均匀性。
合理的铸道和浇口设计能够避免缺陷的产生。
3. 原材料准备在铸造前,需要准备好以下原材料:•铸造材料:常用的铸造材料包括铝合金、铜合金、铁合金等。
根据铸件的要求选择合适的材料。
•砂料:铸模中常用的砂料有石英砂、粘土等。
根据铸模的要求选择合适的砂料。
•砂芯材料:制作砂芯需要砂芯材料,通常使用粘土砂芯材料。
•熔炼材料:根据所选的铸造材料,需要准备相应的熔炼材料,例如铝合金需要准备铝锭。
4. 熔炼操作熔炼是将原材料熔化成金属液的过程,下面是熔炼操作的步骤:1.准备熔炉:根据所选的熔炼材料和熔炼方式,选择合适的熔炉。
确保熔炉干净,并根据需要预热。
2.称量和加入原材料:按比例称重所需的原材料,在炉内加入熔炼材料。
3.加热和熔化:启动熔炉,根据所选熔炼方式和材料的特性,进行适当的加热和熔化过程。
4.熔炼温度控制:根据所选材料的熔点和熔炼要求,控制熔炉温度。
5.除渣和净化:在熔炉中可能会产生杂质和渣滓,需要进行除渣和净化操作。
5. 铸造工艺流程铸造工艺流程是指从准备铸模到铸件冷却出模的整个铸造过程。
下面是圆筒铸造的典型工艺流程:1.铸模准备:根据前面的铸模设计,制作好铸模和砂芯,确保其完整和质量。
2.浸涂剂处理:在铸模和砂芯表面涂上一层浸涂剂,以增加其表面光滑度和耐高温性能。
支座铸造工艺课程设计-2

热加工工艺课程设计支座铸造工艺设计院系:工学院机械系专业:机械设计制造及其自动化班级:姓名:学号:指导老师:时间:黄河科技学院课程设计任务书工学院机械系机械设计制造及其自动化专业 2011级 1班学号姓名指导教师设计题目: 支座铸造工艺设计课程名称:热加工工艺课程设计课程设计时间:5 月 22 日至 6 月 6 日共 2 周课程设计工作内容与基本要求(已知技术参数、设计要求、设计任务、工作计划、所需相关资料)(纸张不够可加页)1、已知技术参数图1 支座零件图2、设计任务与要求1)设计任务1 选择零件的铸型种类,并选择零件的材料牌号。
2 分析零件的结构,找出几种分型方案,并分别用符号标出。
3 从保证质量和简化工艺两方面进行分析比较,选出最佳分型方案,标出浇注位置和造型方法。
4 画出零件的铸造工艺图(图上标出最佳浇注位置与分型面位置、画出机加工余量、起模斜度、铸造圆角、型芯及型芯头,图下注明收缩量)5 绘制出铸件图。
2)设计要求1设计图样一律按工程制图要求,采用手绘或机绘完成,并用三号图纸出图。
2 按所设计内容及相应顺序要求,认真编写说明书(不少于3000字)。
3、工作计划熟悉设计题目,查阅资料,做准备工作 1天确定铸造工艺方案 1天工艺设计和工艺计算 2天绘制铸件铸造工艺图 1天确定铸件铸造工艺步骤 2天编写设计说明书 3天答辩 1天4.主要参考资料《热加工工艺基础》、《金属成形工艺设计》、《机械设计手册》系主任审批意见:审批人签名:时间:2013年月日支座铸造工艺设计摘要铸造是指将液态金属或合金浇注到与零件尺寸、形状相适应的铸型型腔里,待其冷却凝固后获得毛坯或零件的方法。
铸造成形是机械类零件和毛坯成形的重要工艺方法之一,尤以适合于制造内腔和外形复杂的毛坯或零件。
本文主要分析了支座的结构,并根据其结构特点确定了它的砂型铸造工艺。
支座是支撑其他零部件的重要承力零件,主要承受着径向压缩及轴向摩擦的作用,它具有结构稳定、形状简单、廉价实用等特点,故在机械零件的设计、加工制造中支座都起着不可替代的作用。
支座铸造工艺设计

一、零件铸造工艺要求及结构1.1 支座的生产条件、结构及技术要求●产品生产性质——大批量生产●零件材质——RuT300●零件的外型示意图如图2.1所示,支座的零件图如图2.2所示,支座的外形轮廓尺寸为160mm*135mm*100mm,主要壁厚18mm,最大壁厚20mm,为一小型铸件;铸件除满足几何尺寸精度及材质方面的要求外,无其他特殊技术要求。
图2.1 支座外型示意图图2.2 支座零件图1.2 支座结构的铸造工艺性零件结构的铸造工艺性是指零件的结构应符合铸造生产的要求,易于保证铸件品质,简化铸件工艺过程和降低成本。
审查、分析应考虑如下几个方面:1.铸件应有合适的壁厚,为了避免浇不到、冷隔等缺陷,铸件不应太薄。
2.铸件结构不应造成严重的收缩阻碍,注意薄壁过渡和圆角铸件薄厚壁的相接拐弯等厚度的壁与壁的各种交接,都应采取逐渐过渡和转变的形式,并应使用较大的圆角相连接,避免因应力集中导致裂纹缺陷。
3.铸件内壁应薄于外壁铸件的内壁和肋等,散热条件较差,应薄于外壁,以使内、外壁能均匀地冷却,减轻内应力和防止裂纹。
4.壁厚力求均匀,减少肥厚部分,防止形成热节。
5.利于补缩和实现顺序凝固。
6.防止铸件翘曲变形。
7.避免浇注位置上有水平的大平面结构。
对于支座的铸造工艺性审查、分析如下:支座的轮廓尺寸为160mm*135mm*100mm。
砂型铸造条件下该轮廓尺寸允许的最小壁厚查《铸造工艺学》表3-2-1得:最小允许壁厚为3~4 mm。
而设计支座的最小壁厚为10mm。
符合要求。
支座设计壁厚较为均匀,两壁相连初采用了加强肋,可以有效构成热节,不易产生热烈。
二、铸造工艺方案的确定2.1 造型,造芯方法的选择支座的轮廓尺寸为160mm*135mm*100mm,铸件尺寸较小,属于中小型零件且要大批量生产。
采用湿型粘土砂造型灵活性大,生产率高,生产周期短,便于组织流水生产,易于实现机械化和自动化,材料成本低,节省烘干设备、燃料、电力等,还可延长砂箱使用寿命。
支座铸造工艺设计

支座铸造工艺设计1. 引言支座是一种常见的结构零件,广泛应用于桥梁、建筑物和机械设备等领域。
支座的质量和性能对于保证结构的稳定性和安全性至关重要。
支座的制造过程中的铸造工艺设计是确保支座质量的重要环节之一。
本文将就支座铸造工艺设计进行详细介绍,并探讨其关键步骤。
2. 材料选型支座通常是由钢铁材料铸造而成。
选择合适的材料对于支座的性能和寿命具有重要影响。
常用的支座材料有碳钢、合金钢和不锈钢等。
在材料选型上,需要考虑支座的使用环境、承载能力和使用寿命等因素。
材料的选用需要满足相关标准和规范的要求。
3. 铸造工艺设计铸造工艺设计是支座制造过程中至关重要的一环,它直接影响支座的质量和性能。
铸造工艺设计包括模具设计、熔炼、浇注、冷却和清理等多个步骤。
3.1 模具设计模具设计是支座铸造工艺设计的第一步。
模具的设计应满足支座形状和尺寸的要求,同时要考虑到铸造过程中的收缩和变形。
模具的设计需要考虑到易于制造和使用,并能保证支座的精度和表面质量。
常用的模具材料有铁、铝和砂等。
3.2 熔炼熔炼是将所选材料加热至熔点,使其转化为液态的关键过程。
在支座铸造工艺中,通常采用电炉或高频感应炉进行熔炼。
熔炼过程中需要控制炉温、保持合适的熔化时间,并添加合适的熔剂和熔化助剂,以提高铸件的熔化质量和纯度。
3.3 浇注浇注是将熔融金属倒入模具中的步骤。
在支座铸造过程中,浇注需要控制浇注速度和温度,以避免产生气孔和夹渣等缺陷。
浇注过程中需要确保熔融金属能够充分填满模具腔体,并尽量避免产生温度梯度,以减少应力和变形。
3.4 冷却铸造完成后,支座需要进行冷却过程。
冷却速度的控制对于支座的组织结构和性能具有重要影响。
较快的冷却速度可能导致铸件硬化过深,影响其力学性能;而较慢的冷却速度可能会产生过大的晶粒,导致铸件的强度下降。
因此,需要通过合理控制冷却速度来获得理想的支座性能。
3.5 清理清理是支座铸造工艺中的最后一个步骤。
在清理过程中,需要将模具和浇注系统中的残留物清除,以及对铸件的表面进行抛光和清洗。
支座砂型铸造工艺设计说明书2

第一章简介1.1中国古代铸造技术发展中华文明大致经历了石器时代、铜器时代和铁器时代三个历史阶段,这三种材质的工具和技术的创造发明,随着人类的繁衍,不断推动人类文明向高级阶段发展,金属的应用使人类文明产生了根本性的飞跃,而铸造技术的运用和金属的发展紧密联系在一起。
对古代很多务农的人来说,铸造技术是一门手艺。
据历史考证,我国铸造技术开始于夏朝初期,迄今已有5000多年。
到了晚商和西周初期,青铜的铸造技术得到了蓬勃发展,形成了灿烂的青铜文化,遗留到今天的有一批铸造工艺水平较高的铸造产品。
中国古代的铸造方法有:石型即用石头或石膏制作铸型;泥型古称“陶范”;金属型古称“铁范”;失蜡型有出蜡法、走蜡法、脱蜡法或刻蜡法;砂型这种方法是伴随泥型一起产生的。
中国古代铸造中的精品有:沧州铁狮,司母戊方鼎,四羊方尊,曾侯乙尊盘,永乐大铜钟,大型铜编钟,铜车马仪仗队等。
1.2中国铸造技术发展现状尽管近年来我国铸造行业取得迅速的发展,但仍然存在许多问题。
第一,专业化程度不高,生产规模小。
我国每年每厂的平均生产量是815t,远远低于美国的4606t和日本的4878t。
第二,技术含量及附加值低。
我国高精度、高性能铸件比例比日本低约20个百分点。
第三,产学研结合不够紧密、铸造技术基础薄弱。
第四,管理水平不高,有些企业尽管引进了国外的先进的设备和技术,但却无法生产出高质量铸件,究其原因就是管理水平较低。
第五,材料损耗及能耗高污染严重。
中国铸铁件能耗比美国、日本高70%~120%。
第六,研发投入低、企业技术自主创新体系尚未形成。
1.3发达国家铸造技术发展现状发达国家总体上铸造技术先进、产品质量好、生产效率高、环境污染少、原辅材料已形成商品化系列化供应,如在欧洲已建立跨国服务系统。
生产普遍实现机械化、自动化、智能化(计算机控制、机器人操作)。
在大批量中小铸件的生产中,大多采用微机控制的高密度静压、射压或气冲造型机械化、自动化高效流水线湿型砂造型工艺。
HT200轴承支座的铸造工艺设计

HT200轴承支座的铸造工艺设计摘要本工艺方案的设计准则是:在保证铸件质量的前提下,尽量提高方案的经济性和可实施性。
在设计工艺方案过程中,我们结合铸件的实际情况,并从权威文献查找标准,将理论与实际相结合。
同时,用UG软件进行三维造型,用CAE软件进行模拟分析,在不断的尝试、改进中完善本方案。
在设计浇注系统和补缩系统中,考虑到铸件属于中大型铸钢件,容易产生缺陷。
所以为保证充型过程的平稳和铸件成品的质量,我们采用了开放式浇注系统,确保金属液稳定流动和充型。
同时,使用冒口和冷铁控制铸件自远离冒口的末端区向着冒口方向实现明显的“顺序凝固”。
然后我们使用CAE软件进行网格的剖分,充型、凝固的模拟。
在经历多次的方案优化后,我们最终成功消除铸件中的所有缩孔,并使缩松极少量的残存,使铸件达到合格的标准,最终我们的工艺出品率为80.5%。
关键词:HT200轴承支座顺序凝固设计和优化AbstractThe design criterion of this process scheme is to improve the economy and practicability of the scheme as far as possible on the premise of ensuring the casting quality. In the process of designing process plan, we combine the theory with practice by combining the actual situation of casting and searching standard from authoritative literature. At the same time, UG software was used for 3d modeling, and CAE software was used for simulation analysis, so as to improve the scheme through continuous attempts and improvements.In the design of casting system and feeding system, considering that the casting belongs to medium and large steel castings, it is easy to produce defects. Therefore, in order to ensure the smooth filling process and the quality of the casting products, we adopted an open casting system to ensure the stable flow of liquid metal and filling. At the same time, the riser and chill are used to control the casting from the end area away from the riser to the direction of the riser to achieve obvious "sequential solidification". Then we use CAE software for mesh subdivision, filling, solidification simulation. After several times of program optimization, we finally succeeded in eliminating all shrinkage holes in the casting and making a very small amount of residual shrinkage porosity, so that the casting reached the qualified standard, and the final production rate of our process was 80.5%.Keywords: sequential solidification design and optimization of bearing support目录摘要 (4)1 铸钢件初步分析 (5)1.1 基本信息 (5)1.2 实用性分析 (5)2可铸性分析 (4)2.1材料的化学成分及铸造性能 (7)2.2 最小壁厚 (7)2.3 临界壁厚 (8)2.4 铸件壁的过渡和连接 (8)2.5 加强肋分析 (9)3 铸造工艺方案的设计 (10)3.1 造型方法和材料选取 (10)3.1.1 呋喃树脂砂成分的选择 (10)3.1.2 铸造涂料的选择 (10)3.2 铸造工艺参数的确定 (11)3.2.1 铸件尺寸公差 (11)3.2.2 机械加工余量 (11)3.2.3 铸件收缩率 (12)3.2.4 起模斜度 (13)3.2.5 最小铸出孔和槽 (13)3.2.6 补充说明 (13)3.3 摆放位置与分型面 (13)3.3.1 摆放位置的确定 (13)3.3.2 分型面的确定 (14)3.4 浇注系统设计 (15)3.4.1 设计原则 (15)3.4.2 确定浇注位置 (16)3.4.3 各浇道截面计算 (17)3.4.4 浇口杯的选择 (19)3.5 冒口和冷铁设计 (20)3.5.1冒口的设计 (20)3.5.2冷铁的设计 (22)4 工艺方案优化 (23)4.1 铸件缺陷分析 (23)4.2缺陷改进 (25)5 砂芯及芯盒的设计 (27)5.1 制芯方法的确定 (27)5.2 芯头的定位和间隙 (27)5.3 芯骨的设计 (28)5.4 砂芯的排气 (28)5.5芯盒的设计 (29)6 铸造工艺工艺装备设计 (30)6.1 砂箱的选择与设计 (30)6.1.1 砂箱及其附件的材料 (30)6.1.2 砂箱各部分的机构和尺寸 (30)6.2 模样的设计 (36)6.3 铸型造型 (36)7熔炼和后处理 (37)7.1 铸钢的熔炼 (37)7.1.1 配料 (37)7.1.2 熔炼过程的技术要求 (37)7.2 铸件的清理 (40)7.2.1 铸件的落砂除芯 (40)7.2.2 浇冒口和毛刺的去除 (40)7.2.3 铸件的表面清理 (40)7.2.4 铸件的热处理 (40)7.3 气孔缺陷的防治 (41)8 参考文献 (42)1 铸钢件初步分析1.1 基本信息零件名称:HT200轴承支座材质:ZG310-570外形尺寸:1430mm×1160mm×810mm零件重量:2600Kg 生产规模:批量生产技术要求:(1)锐角倒钝。
支座铸造工艺设计
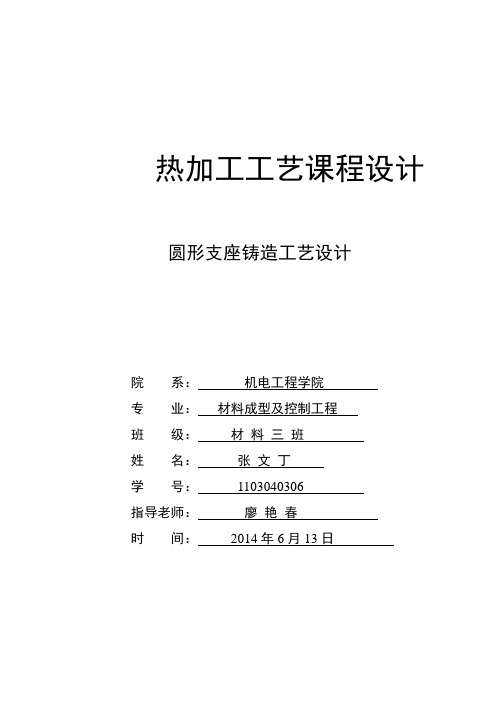
热加工工艺课程设计圆形支座铸造工艺设计院系:机电工程学院专业:材料成型及控制工程班级:材料三班姓名:张文丁学号:1103040306指导老师:廖艳春时间:2014年6月13日摘要热加工技术是机械类个专业一门重要的综合性技术学科。
在机械制造过程中,由于加工过程十分复杂,加工工序繁多,工艺过程不仅有铸造成型,锻压成形,焊接成形,还有非金属的模压成形,挤压成形等。
因此选着合适的工艺是保证产品质量的重要依据。
本次课程设计,将进行铸造工艺的总结和学习。
铸造主要是将液态金属或合金浇注到与零件尺寸、形状相适应的铸型型腔里,待其冷却凝固后获得毛坯或零件的方法,是机械类零件和毛坯成型的主要工艺方法,尤其适合于制造内腔和外形复杂的毛坯或零件。
本文主要分析了支座的结构并根据其结构特点确定了它的铸造工艺,支座是支撑零部件的载体其主要承受了轴向的压缩作用的机械零件。
在日常生产中对支座的选用异常广泛,因为它具有经济型良好、结构稳定性好、结构简单美观实用等特点,所以在机器零件的设计,加工过程中支座都起着不可代替的作用。
确定支座的铸造工艺过程主要包括:1)铸型及方法选择、2)分型面选择、3)浇注位置的确定、4)工艺参数的确定、5)浇注系统的设计、7)绘制铸造工艺图、8)绘制铸件图型面,型芯的数量、形状、尺寸及固定方法,加工余量,收缩率,浇注系统,起模斜度,冒口和冷铁的尺寸和位置等。
目录绪论 (1)一、零件的简介 (2)1.1 零件的介绍 (2)1.2确定零件的材料及牌号 (2)二、铸造工艺方案的确定 (3)2.1铸件的结构特点 (3)2.2铸件的工艺分析 (4)2.3分型面选择 (4)2.4 确定出最佳浇注位置 (6)三、工艺参数确定 (8)3.1工艺参数的确定 (8)3.1.1铸件尺寸公差 (9)3.1.2 机械加工余量 (9)3.1.3铸造收缩率 (9)3.1.4起模斜度 (10)3.1.5铸造圆角 (10)3.1.6反变形量 (10)3.2 砂芯设计 (10)3.2.1 芯头的设计 (10)3.2.2 砂头的定位结构 (11)3.2.3 芯座 (11)四、浇注系统及冒口、冷铁、出气孔等设计 (11)4.1 浇注系统的设计 (11)4.1.1选择浇注系统类型 (12)4.1.2横浇道及内浇道 (12)4.2 冒口的设计 (12)4.3 冷铁的设计 (13)4.4 出气孔的设计 (13)五、铸造工艺图绘制 (14)六、铸件图的绘制 (15)七、支座铸造工艺卡 (16)总结 (17)致谢 (18)参考文献: (19)绪论热加工成型技术也叫材料成型技术,是机械制造生产过程的重要组成部分。
支座压铸模具毕业设计
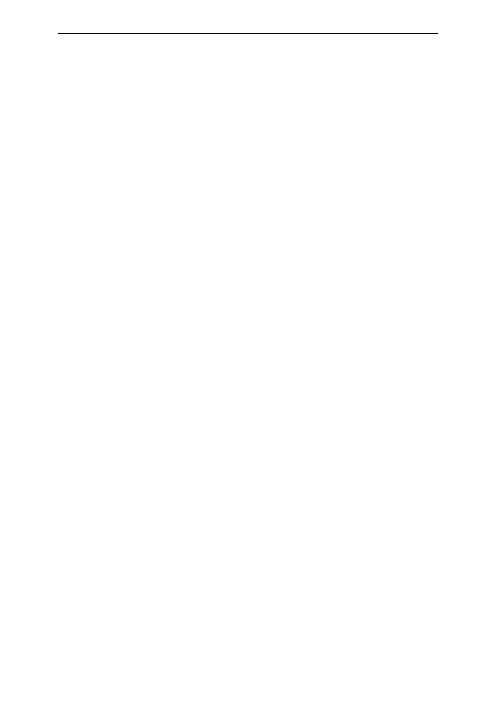
压力铸造是目前成型有色金属铸件的重要成型工艺方法,压铸的工艺特点是铸件的强度和精度较高,形状较为复杂且铸件壁较薄,而且生产力极高。
压铸模具是压力铸造的生产关键,压铸模具的质量决定着压铸件的质量和精度,而且模具设计直接影响着模具的质量和寿命。
因此,模具设计是模具技术进步关键,也是模具发展的重要因素。
根据零件的结构和尺寸设计了完整的模具。
设计内容主要包括:浇注系统设计,成型零件设计,抽芯机构设计,推出机构设计及模体结构设计。
根据铸件的形状特点,零件尺寸及精度,选定了合适是我压铸机,通过准确的计算并查阅设计手册,确定了成型零件以及模体是我尺寸及精度,在材料的选取及热处理要求上也做了详细说明,并在结合理论的基础上,借助于计算机辅助软件绘制了各部分零件及装配体的立体图和工程图,以保障模具的加工制造。
关键词:压力铸造,压铸模具,模具设计前言 (1)摘要 (I)目录 (I)1、压铸件的工艺分析 (1)1.1对压铸件的结构分析 (3)1.2压铸件材料的分析 (3)2、设备型号及其相关参数 (3)3、分析模具结构 (4)3.1浇注系统的设计 (4)3.2溢流槽和排气槽的设计 (4)3.3分型面的设计 (4)3.4型腔和型芯尺寸的确定 (4)3.5导柱与导套 (5)3.6推杆的结构设计 (5)3.7模具的冷却 (5)4、压铸工艺参数的选择 (5)4.1压射比压 (5)4.2压铸温度 (5)4.3压铸模温度 (5)4.4保压时间 (6)4.5留模时间 (6)4.6压射速度 (6)5、涂料的种类 (7)5.1压铸涂料 (7)6、型芯与型腔的选材 (7)7、校核 (7)8、零件图和装配图 (7)致谢 (11)参考文献 (12)结论 (13)前言国内外模具发展现状现代模具工业有“不衰亡工业”之称。
世界模具市场总体上供不应求,市场需求量维持在600亿至650亿美元,同时,我国的模具产业也迎来了新一轮的发展机遇。
近几年,我国模具产业总产值保持13%的年增长率中国模具行业发展现状:目前,中国17000多个模具生产厂点,从业人数约50多万。
- 1、下载文档前请自行甄别文档内容的完整性,平台不提供额外的编辑、内容补充、找答案等附加服务。
- 2、"仅部分预览"的文档,不可在线预览部分如存在完整性等问题,可反馈申请退款(可完整预览的文档不适用该条件!)。
- 3、如文档侵犯您的权益,请联系客服反馈,我们会尽快为您处理(人工客服工作时间:9:00-18:30)。
湖南科技大学课程设计课程设计名称:圆形支座铸造工艺设计学生姓名:学院:专业及班级:学号:指导教师:ﻩ年月日铸造工艺课程设计任务书一、任务与要求1.完成产品零件图、铸件铸造工艺图各一张,铸造工艺图需要三维建模(完成3D图).2.完成芯盒装配图一张。
3.完成铸型装配图一张.4。
编写设计说明书一份(15~20页),并将任务书及任务图放置首页。
二、设计内容为2周1. 绘制产品零件图、铸造工艺图及工艺图的3D图(2天).2。
铸造工艺方案设计:确定浇注位置及分型面,确定加工余量、起模斜度、铸造圆角、收缩率,确定型芯、芯头间隙尺寸.(1天)。
3。
绘制芯盒装配图(1天).4.绘制铸型装配图、即合箱图(包括流道计算共2天).5。
编制设计说明书(4天)。
三、主要参考资料1。
张亮峰,材料成形技术基础[M],高等教育出版社,2011.2。
丁根宝, 铸造工艺学上册[M] ,机械工业出版社,1985。
3。
铸造手册编委会,铸造手册:第五卷[M],机械工业出版社,1996。
4.沈其文, 材料成形工艺基础(第三版)[M],华中科技大学出版社,2003.摘要支座是支撑零部件的载体其主要承受了轴向的压缩作用的机械零件。
在日常生产中对支座的选用异常广泛,因为它具有经济型良好、结构稳定性好、结构简单美观实用等特点.本文主要分析了支座的结构,并根据其结构特点确定了铸造工艺,确定了支座的铸造工艺过程,绘制了芯盒装配图,铸造装配图等。
关键词:圆形支座;砂型铸造;铸造工艺设计;装配图目录一、造型材料选择1。
铸造合金的选用 (1)2。
造型和造芯材料 (1)二、浇注位置及分型面的确定············································2三、铸造工艺参数设计1.加工余量的选择 (5)2.铸件孔是否铸出的确定 (5)3.起模斜度的确定 (5)4。
铸造圆角的确定 (6)5。
铸造收缩率的确定 (7)6.反变形量 (8)四、造型方法的设计 (8)五、木模的设计 (10)六、浇注系统的设计1.浇口杯·····························································122.浇注系统的尺寸····················································12七、冒口的设计 (14)八、铸型装配图设计 (15)心得体会 (17)参考文献································································18一、造型材料选择1. 铸造合金的选用灰铸铁的力学性能与基体的组织和石墨的形态有关.灰铸铁中的片状石墨对基体的割裂严重,在石墨尖角处易造成应力集中,使灰铸铁的抗拉强度、塑性和韧性远低于钢,但抗压强度与钢相当,也是常用铸铁件中力学性能最差的铸铁。
同时,基体组织对灰铸铁的力学性能也有一定的影响,铁素体基体灰铸铁的石墨片粗大,强度和硬度最低,故应用较少;珠光体基体灰铸铁的石墨片细小,有较高的强度和硬度,主要用来制造较重要铸件;铁素体一珠光体基体灰铸铁的石墨片较珠光体灰铸铁稍粗大,性能不如珠光体灰铸铁。
故工业上较多使用的是珠光体基体的灰铸铁。
灰铸铁具有良好的铸造性能、良好的减振性、良好的耐磨性能、良好的切削加工性能、在铸造过程中,应选用的金属材料种类是灰铸铁,因为此铸件结构基本为左右对称,最大截面为地面,因此可以采用整体造型进行铸造。
灰铸铁的流动性好,易浇注,且收缩率最小。
并随含碳量的增加而减少,使铸件易于切削加工。
铸铁材料还可以减少噪音。
在浇注时,浇注温度为1200-1380℃。
采用砂型铸造方法,操作简便,工艺性好,提高了工作效率。
灰铸铁材料抗压能力强,保证了铸件的使用性能。
因为支座是指用以支承容器或设备的重量,并使其固定于一定位置的支承部件。
还要承受操作时的振动与地震载荷,而且此铸件为290×120mm的灰铸铁,其型号应为HT250.2. 造型和造芯材料由于本次课程设计的铸件是中等批量生产,所以造型和造芯的方法应采用灵活多样,适应性强的手工造型.但它有生产率低,劳动强度大,铸件质量不易稳定的缺点。
造型方法可选用砂箱造型,其操作方便,无论是大、中、小型铸件,还是大量、成批和单件生产均可采用。
型砂选择:铸铁用的型砂和泥心砂,其主要的组成部分是石英砂和耐火粘土。
作为造型材料的沙子性质,由砂粒形状和大小,氧化硅的含量,以及沙子中存在的各种混合物来确定。
该铸件型砂选用瘦沙(粘土含量2—10%)来代替石英砂。
在湿模造型时,小型和中小型铸铁件泥心砂可以采用小颗粒的半肥沙(粘土含量10—20%)作为附加物加入石英砂中.加入的耐火粘土,其工艺试样的抗压强度应为0。
5—0。
6kg/mm2。
耐火粘土应该是白色或者淡灰色的,不应有可被肉眼看出的混杂物,如砂子、矿石、石灰等。
碎粘土所含水分不应超过2%。
(铸件材料是铸铁时,制造湿砂型的粘土砂所用粘土为膨润土,湿抗压强度一般为80—120kPa。
含水量为4.5—5.5%,透气性为60-100,型砂配比70/140目占33,100/200目占17%, 红砂占50%。
芯砂选择油砂或水玻璃砂。
)造芯的方法可采用芯盒造芯和刮板造芯,前者用于造各种形状、尺寸和批量的砂芯,后者用于造单件小批量生产,形状简单或回转体砂芯.二、浇注位置及分型面的确定分型面是指上、下砂型的接触面或铸造模样的分合面,分型面的选择应在保证质量前提下,尽量简化工艺过程,节省人力物力。
对于零件质量要求不高、外形复杂且批量不大的支撑台铸件,为简化工艺操作,可优先考虑分型面,并找出零件的可分型方案。
选择分型面时应注意一下原则:1)应使铸件全部或大部分置于同一半型内2)应尽量减少分型面的数目3)分型面应尽量选用平面4)便于下芯、合箱和检测5)不使砂箱过高6)受力件的分型面的选择不应削弱铸件结构强度7)注意减轻铸件清理和机械加工量该零件可能的分型方案有三种.a)以支架的底面为分型面(如图2-1所示)图2—1b)以凸台为分型面(如图2—2所示)图2-2c)以对称中心线为分型面(如图2-3所示)图2—3分析比较各方案的特点并确定方案1)以支架的底面为分型面这种分型方法只需外加一活块造型,其分型面数量不仅少而且铸件全部放在下型,既便于型芯安放和检验,又可以使上型高度减低而便于合箱和检验壁厚,还有利于起模及翻箱操作。
而且底面可以向下放,以保证其表面粗糙度,分型面为底面时便于起模。
2)以凸台为分型面不利于起模及翻箱操作.3)以对称中心线为分型面需采用两箱造型造型复杂,容易造成错箱,从而影响铸件精度。
三、铸造工艺参数设计确定铸造工艺参数必须以零件尺寸为依据,零件的详细尺寸如图3-1所示.图3—1零件图1.加工余量的选择该支座为单件、小批量生产,可采用手工造型和造芯.由《材料成形技术基础》P54表1.10查得尺寸公差等级CT应为13—15级,选13级,加工余量等级为MA为F-H,应选G。
由课程设计题目知基本尺寸φ290mm,查《材料成形技术基础》第三版P56表1.13与尺寸公差配套使用的灰铸铁机械加工余量,并由确定加工余量中“顶面(相对于浇注位置)的加工余量等级应比底、侧面加工余量等级降一级选用"的规定查得,顶面加工余量应按照CT14级、MA-H级;底面、侧面的加工余量为CT13级、MA-G级。
则顶面的加工余量取5mm,底面和侧面的加工余量取3。
5mm。
所以顶面的加工余量取5mm,底面和侧面的加工余量取 3.5mm。
加工余量如图3-2所示.图3-2 加工余量图2。
铸件孔是否铸出的确定因为该铸件材料是HT250,单件、小批量生产,孔径15mm,但是查得铸件的最小铸出孔直径是30mm-50mm,则该六个孔没必要铸出。
所以该孔径为15mm的六个孔没必要铸出。
3.起模斜度的确定根据标准《铸件模样起模斜度》中的规定,该铸件选用增加铸件厚度的起模斜度形式如图3—3:图3-3起模斜度用手工方法加工模具时用宽度标注,该铸件模具是木模,高度120mm,由《材料成形技术基础》P57表1。