支座铸造工艺课程设计-2
铸造工艺学课程设计案例

成果报告需以PDF格式提交,同时附上所有相关数据和图表。
报告内容
报告需包含设计思路、工艺流程、数据分析及结论等部分,要求 内容详实、逻辑清晰。
成果展示形式和内容安排建议
展示形式
鼓励采用多媒体形式进行展示,如PPT、视频等。
内容安排
建议按照设计背景、设计思路、工艺流程、数据 分析、结论与展望等顺序进行展示。
时间安排
每个小组展示时间不超过20分钟,需提前做好时 间规划。
课程设计评价标准及成绩评定方法
01
评价标准
将从设计创新性、实用性、技术 难度、报告质量等方面进行综合 评价。
02
成绩评定方法
03
优秀作品选拔
采用百分制评分,其中设计创新 性占30%、实用性占20%、技术 难度占20%、报告质量占30%。
铸造材料选择
根据零件使用要求、生产批量和成本 等因素,选择合适的铸造合金,如铸 铁、铸钢、铝合金等。
性能要求
铸造合金应具有良好的流动性、收缩 性、偏析倾向小等性能,以保证铸件 质量。同时,合金成分和性能应符合 相关标准或技术条件的规定。
03
案例分析:典型铸件生产工艺设计
铸件结构分析与设计优化建议
根据评分结果,选拔出优秀作品 进行表彰和奖励。
THANKS
感谢观看
推广新技术和新材料
积极推广先进的铸造技术和新材料,如3D打印技术、高性能铸造合 金等,提高铸件的精度和性能。
加强人才培养
加强铸造领域的人才培养和引进,提高从业人员的专业素质和技能水 平,为铸造行业的发展提供有力的人才保障。
06
课程设计成果展示与评价标准
课程设计成果提交要求说明
提交时间
所有成果需在课程结束前一周内提交,逾期将不予受理。
支座 铸造工艺课程设计
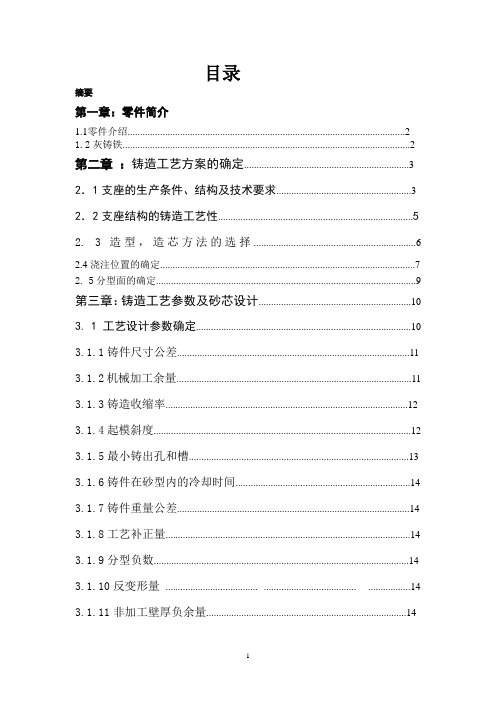
目录摘要第一章:零件简介1.1零件介绍 (2)1.2灰铸铁 (2)第二章:铸造工艺方案的确定 (3)2.1支座的生产条件、结构及技术要求 (3)2.2支座结构的铸造工艺性 (5)2. 3造型,造芯方法的选择 (6)2.4浇注位置的确定 (7)2. 5分型面的确定 (9)第三章:铸造工艺参数及砂芯设计 (10)3. 1 工艺设计参数确定 (10)3.1.1铸件尺寸公差 (11)3.1.2机械加工余量 (11)3.1.3铸造收缩率 (12)3.1.4起模斜度 (12)3.1.5最小铸出孔和槽 (13)3.1.6铸件在砂型内的冷却时间 (14)3.1.7铸件重量公差 (14)3.1.8工艺补正量 (14)3.1.9分型负数 (14)3.1.10反变形量 (14)3.1.11非加工壁厚负余量 (14)3. 2砂芯设计 (15)3.2.1芯头的设计 (16)3.2.2砂芯的定位结构 (16)3.2.3压环、防压环和集砂槽芯头结构 (16)3.2.4芯骨设计 (16)3.2.5砂芯的排气 (16)3.2.6砂芯负数 (16)第四章:浇注系统及冒口、冷铁、出气孔等设计4.1浇注系 (17)4.1.1选择浇注系统类型 (17)4.1.2计算浇注时间并核算金属上升速度 (17)4.1.3计算阻流截面积 (17)4.1.4确定浇口比 (18)4.1.5计算内浇道截面积 (18)4.1.6计算横浇道截面积 (18)4.1.7计算直浇道截面积 (19)4.1.8浇口窝的设计 (20)4.1.9浇口杯的设计 (20)4.2冒口的设计 (20)4.3冷铁的设计.....................................................................................................21.4.4出气孔的设计 (21)第五章砂型铸造设备选用 (21)5.1 造型工部设备选用 (21)5.2 制芯工部设备选用 (21)5.3 清理工部设备选用 (21)设计心得 (22)参考文献 (22)1.1零件介绍支座是指用以支承容器或设备的重量,并使其固定于一定位置的支承部件。
铸造工艺课程设计
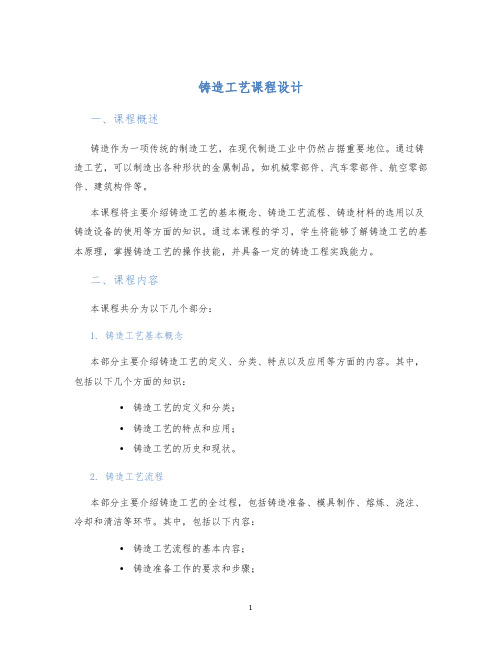
铸造工艺课程设计一、课程概述铸造作为一项传统的制造工艺,在现代制造工业中仍然占据重要地位。
通过铸造工艺,可以制造出各种形状的金属制品,如机械零部件、汽车零部件、航空零部件、建筑构件等。
本课程将主要介绍铸造工艺的基本概念、铸造工艺流程、铸造材料的选用以及铸造设备的使用等方面的知识。
通过本课程的学习,学生将能够了解铸造工艺的基本原理,掌握铸造工艺的操作技能,并具备一定的铸造工程实践能力。
二、课程内容本课程共分为以下几个部分:1. 铸造工艺基本概念本部分主要介绍铸造工艺的定义、分类、特点以及应用等方面的内容。
其中,包括以下几个方面的知识:•铸造工艺的定义和分类;•铸造工艺的特点和应用;•铸造工艺的历史和现状。
2. 铸造工艺流程本部分主要介绍铸造工艺的全过程,包括铸造准备、模具制作、熔炼、浇注、冷却和清洁等环节。
其中,包括以下内容:•铸造工艺流程的基本内容;•铸造准备工作的要求和步骤;•模具制作的原理和方法;•熔炼、浇注、冷却和清洁等环节的基本原理。
3. 铸造材料的选用本部分主要介绍铸造材料的概念、种类、性能和应用等方面的内容。
其中,包括以下几个方面的知识:•铸造材料的定义和分类;•铸造材料的性能和应用;•铸造材料的选用和配比原则。
4. 铸造设备的使用本部分主要介绍常用的铸造设备和工具,包括铸造炉、压铸机、铸型机、模具加热炉等设备以及测量、检验和修复工具等。
其中,包括以下内容:•铸造设备的分类和原理;•铸造设备的操作和维护;•铸造设备的选型和应用。
三、课程设计本课程将以实践为主的方式进行教学,通过铸造工艺的实际操作,使学生了解铸造工艺的基本原理和实践技能,并培养学生的实际能力。
1. 实验项目本课程将设置若干个铸造实验项目,包括砂型铸造、压力铸造、重力铸造等不同类型的铸造实验。
通过实验,学生将深入了解铸造工艺的操作流程、特点和应用。
2. 课程报告本课程将要求学生完成若干篇课程报告,包括铸造工艺的概念、流程、材料和设备等不同方面的内容。
支座砂型铸造工艺设计说明书2

第一章简介1.1中国古代铸造技术发展中华文明大致经历了石器时代、铜器时代和铁器时代三个历史阶段,这三种材质的工具和技术的创造发明,随着人类的繁衍,不断推动人类文明向高级阶段发展,金属的应用使人类文明产生了根本性的飞跃,而铸造技术的运用和金属的发展紧密联系在一起。
对古代很多务农的人来说,铸造技术是一门手艺。
据历史考证,我国铸造技术开始于夏朝初期,迄今已有5000多年。
到了晚商和西周初期,青铜的铸造技术得到了蓬勃发展,形成了灿烂的青铜文化,遗留到今天的有一批铸造工艺水平较高的铸造产品。
中国古代的铸造方法有:石型即用石头或石膏制作铸型;泥型古称“陶范”;金属型古称“铁范”;失蜡型有出蜡法、走蜡法、脱蜡法或刻蜡法;砂型这种方法是伴随泥型一起产生的。
中国古代铸造中的精品有:沧州铁狮,司母戊方鼎,四羊方尊,曾侯乙尊盘,永乐大铜钟,大型铜编钟,铜车马仪仗队等。
1.2中国铸造技术发展现状尽管近年来我国铸造行业取得迅速的发展,但仍然存在许多问题。
第一,专业化程度不高,生产规模小。
我国每年每厂的平均生产量是815t,远远低于美国的4606t和日本的4878t。
第二,技术含量及附加值低。
我国高精度、高性能铸件比例比日本低约20个百分点。
第三,产学研结合不够紧密、铸造技术基础薄弱。
第四,管理水平不高,有些企业尽管引进了国外的先进的设备和技术,但却无法生产出高质量铸件,究其原因就是管理水平较低。
第五,材料损耗及能耗高污染严重。
中国铸铁件能耗比美国、日本高70%~120%。
第六,研发投入低、企业技术自主创新体系尚未形成。
1.3发达国家铸造技术发展现状发达国家总体上铸造技术先进、产品质量好、生产效率高、环境污染少、原辅材料已形成商品化系列化供应,如在欧洲已建立跨国服务系统。
生产普遍实现机械化、自动化、智能化(计算机控制、机器人操作)。
在大批量中小铸件的生产中,大多采用微机控制的高密度静压、射压或气冲造型机械化、自动化高效流水线湿型砂造型工艺。
HT200轴承支座的铸造工艺设计

HT200轴承支座的铸造工艺设计摘要本工艺方案的设计准则是:在保证铸件质量的前提下,尽量提高方案的经济性和可实施性。
在设计工艺方案过程中,我们结合铸件的实际情况,并从权威文献查找标准,将理论与实际相结合。
同时,用UG软件进行三维造型,用CAE软件进行模拟分析,在不断的尝试、改进中完善本方案。
在设计浇注系统和补缩系统中,考虑到铸件属于中大型铸钢件,容易产生缺陷。
所以为保证充型过程的平稳和铸件成品的质量,我们采用了开放式浇注系统,确保金属液稳定流动和充型。
同时,使用冒口和冷铁控制铸件自远离冒口的末端区向着冒口方向实现明显的“顺序凝固”。
然后我们使用CAE软件进行网格的剖分,充型、凝固的模拟。
在经历多次的方案优化后,我们最终成功消除铸件中的所有缩孔,并使缩松极少量的残存,使铸件达到合格的标准,最终我们的工艺出品率为80.5%。
关键词:HT200轴承支座顺序凝固设计和优化AbstractThe design criterion of this process scheme is to improve the economy and practicability of the scheme as far as possible on the premise of ensuring the casting quality. In the process of designing process plan, we combine the theory with practice by combining the actual situation of casting and searching standard from authoritative literature. At the same time, UG software was used for 3d modeling, and CAE software was used for simulation analysis, so as to improve the scheme through continuous attempts and improvements.In the design of casting system and feeding system, considering that the casting belongs to medium and large steel castings, it is easy to produce defects. Therefore, in order to ensure the smooth filling process and the quality of the casting products, we adopted an open casting system to ensure the stable flow of liquid metal and filling. At the same time, the riser and chill are used to control the casting from the end area away from the riser to the direction of the riser to achieve obvious "sequential solidification". Then we use CAE software for mesh subdivision, filling, solidification simulation. After several times of program optimization, we finally succeeded in eliminating all shrinkage holes in the casting and making a very small amount of residual shrinkage porosity, so that the casting reached the qualified standard, and the final production rate of our process was 80.5%.Keywords: sequential solidification design and optimization of bearing support目录摘要 (4)1 铸钢件初步分析 (5)1.1 基本信息 (5)1.2 实用性分析 (5)2可铸性分析 (4)2.1材料的化学成分及铸造性能 (7)2.2 最小壁厚 (7)2.3 临界壁厚 (8)2.4 铸件壁的过渡和连接 (8)2.5 加强肋分析 (9)3 铸造工艺方案的设计 (10)3.1 造型方法和材料选取 (10)3.1.1 呋喃树脂砂成分的选择 (10)3.1.2 铸造涂料的选择 (10)3.2 铸造工艺参数的确定 (11)3.2.1 铸件尺寸公差 (11)3.2.2 机械加工余量 (11)3.2.3 铸件收缩率 (12)3.2.4 起模斜度 (13)3.2.5 最小铸出孔和槽 (13)3.2.6 补充说明 (13)3.3 摆放位置与分型面 (13)3.3.1 摆放位置的确定 (13)3.3.2 分型面的确定 (14)3.4 浇注系统设计 (15)3.4.1 设计原则 (15)3.4.2 确定浇注位置 (16)3.4.3 各浇道截面计算 (17)3.4.4 浇口杯的选择 (19)3.5 冒口和冷铁设计 (20)3.5.1冒口的设计 (20)3.5.2冷铁的设计 (22)4 工艺方案优化 (23)4.1 铸件缺陷分析 (23)4.2缺陷改进 (25)5 砂芯及芯盒的设计 (27)5.1 制芯方法的确定 (27)5.2 芯头的定位和间隙 (27)5.3 芯骨的设计 (28)5.4 砂芯的排气 (28)5.5芯盒的设计 (29)6 铸造工艺工艺装备设计 (30)6.1 砂箱的选择与设计 (30)6.1.1 砂箱及其附件的材料 (30)6.1.2 砂箱各部分的机构和尺寸 (30)6.2 模样的设计 (36)6.3 铸型造型 (36)7熔炼和后处理 (37)7.1 铸钢的熔炼 (37)7.1.1 配料 (37)7.1.2 熔炼过程的技术要求 (37)7.2 铸件的清理 (40)7.2.1 铸件的落砂除芯 (40)7.2.2 浇冒口和毛刺的去除 (40)7.2.3 铸件的表面清理 (40)7.2.4 铸件的热处理 (40)7.3 气孔缺陷的防治 (41)8 参考文献 (42)1 铸钢件初步分析1.1 基本信息零件名称:HT200轴承支座材质:ZG310-570外形尺寸:1430mm×1160mm×810mm零件重量:2600Kg 生产规模:批量生产技术要求:(1)锐角倒钝。
铸造工艺课程设计指导书

铸造工艺课程设计指导书§1设计目的与要求1.通过铸造工艺课程设计巩固和加深铸造工艺课程及其它有关基础课程的知识;2.通过课程设计能较系统的掌握铸造工艺及工装的设计方法,锻炼运用铸造工艺手册及其它技术资料的基本技能,以达到培养学生分析和解决铸造生产实际问题的能力;3.通过课程设计使学生进一步提高图纸、文字表达能力;4.为专业课程的学习及以后工作打下基础。
§2设计任务学生要在规定的时间(2周)内,必须完成一个中等复杂程度的零件,采用手工造型的主要铸造技术文件编制工作。
采用CAD出图,铸件需要进行三维建模。
具体任务包括:1.铸件2D零件图一张2.铸造工艺图一张3.芯盒装配图一张4.铸型装配图一张5.设计说明书一份§3设计内容和步骤铸造工艺课程设计总的程序是:根据已下达的课题任务-零件图进行详细的工艺分析后,绘制出铸造工艺图。
然后以工艺图为依据,设计出模样图和芯盒图,然后再绘制铸型装配图(合箱图),最后编写设计说明书。
§3.1按设计步骤分别介绍各项主要内容与注意事项§3.1.1首先了解和熟悉铸造零件图纸通过阅读图纸,应着重了解以下各点:1.了解铸造零件的结构形状及各投影间的关系,建立零件形状的明确完整的立体概念,以保证工艺设计及各项设计制图工作的顺利进行;2.弄清零件图的各项尺寸,并着重记录铸造零件的重量,主要壁厚及最大壁厚,零件最大尺寸(长宽高轮廓尺寸),以供工艺设计使用;3.零件各项公差要求,零件加工位置及零件各项加工要求(包括表面粗糙度),并对加工方法做初步了解;4.零件材质及性能要求,以及图纸上指出的各项特殊技术要求。
§3.1.2了解和分析铸造零件在机器中的位置和作用进一步了解其负载情况及其工作条件,如了解零件所受载荷性质(静载荷,交变载荷,冲击载荷等)和载荷大小,并对受力情况做初步了解。
§3.1.3了解设计任务所要求的生产批量在课程设计中,一般按成批或大量生产进行。
支座铸造工艺设计
热加工工艺课程设计圆形支座铸造工艺设计院系:机电工程学院专业:材料成型及控制工程班级:材料三班姓名:张文丁学号:1103040306指导老师:廖艳春时间:2014年6月13日摘要热加工技术是机械类个专业一门重要的综合性技术学科。
在机械制造过程中,由于加工过程十分复杂,加工工序繁多,工艺过程不仅有铸造成型,锻压成形,焊接成形,还有非金属的模压成形,挤压成形等。
因此选着合适的工艺是保证产品质量的重要依据。
本次课程设计,将进行铸造工艺的总结和学习。
铸造主要是将液态金属或合金浇注到与零件尺寸、形状相适应的铸型型腔里,待其冷却凝固后获得毛坯或零件的方法,是机械类零件和毛坯成型的主要工艺方法,尤其适合于制造内腔和外形复杂的毛坯或零件。
本文主要分析了支座的结构并根据其结构特点确定了它的铸造工艺,支座是支撑零部件的载体其主要承受了轴向的压缩作用的机械零件。
在日常生产中对支座的选用异常广泛,因为它具有经济型良好、结构稳定性好、结构简单美观实用等特点,所以在机器零件的设计,加工过程中支座都起着不可代替的作用。
确定支座的铸造工艺过程主要包括:1)铸型及方法选择、2)分型面选择、3)浇注位置的确定、4)工艺参数的确定、5)浇注系统的设计、7)绘制铸造工艺图、8)绘制铸件图型面,型芯的数量、形状、尺寸及固定方法,加工余量,收缩率,浇注系统,起模斜度,冒口和冷铁的尺寸和位置等。
目录绪论 (1)一、零件的简介 (2)1.1 零件的介绍 (2)1.2确定零件的材料及牌号 (2)二、铸造工艺方案的确定 (3)2.1铸件的结构特点 (3)2.2铸件的工艺分析 (4)2.3分型面选择 (4)2.4 确定出最佳浇注位置 (6)三、工艺参数确定 (8)3.1工艺参数的确定 (8)3.1.1铸件尺寸公差 (9)3.1.2 机械加工余量 (9)3.1.3铸造收缩率 (9)3.1.4起模斜度 (10)3.1.5铸造圆角 (10)3.1.6反变形量 (10)3.2 砂芯设计 (10)3.2.1 芯头的设计 (10)3.2.2 砂头的定位结构 (11)3.2.3 芯座 (11)四、浇注系统及冒口、冷铁、出气孔等设计 (11)4.1 浇注系统的设计 (11)4.1.1选择浇注系统类型 (12)4.1.2横浇道及内浇道 (12)4.2 冒口的设计 (12)4.3 冷铁的设计 (13)4.4 出气孔的设计 (13)五、铸造工艺图绘制 (14)六、铸件图的绘制 (15)七、支座铸造工艺卡 (16)总结 (17)致谢 (18)参考文献: (19)绪论热加工成型技术也叫材料成型技术,是机械制造生产过程的重要组成部分。
铸造工艺学课程设计案例
铸造工艺学课程设计题目:分工:学院:专业:班级:学号:姓名:前言铸造工艺学课程是培养学生熟悉对零件及产品工艺设计的基本内容、原则、方法和步骤以及掌握铸造工艺和工装设计的基本技能的一门主要专业课。
课程设计则是铸造工艺学课程的实践性教学环节,同时也是我们铸造专业迎来的第一次全面的自主进行工艺和工装设计能力的训练。
在这个为期两周的过程里,我们有过紧张,有过茫然,有过喜悦,从中感受到了学习的艰辛,也收获到了学有所获的喜悦,回顾一下,我觉得进行铸造工艺学课程设计的目的有如下几点:通过课程设计实践,树立正确的设计思想,增强创新意识,培养综合运用铸造工艺学课程和其他先修课程的的理论与实际知识去分析和解决实际问题的能力。
通过制定和合理选择工艺方案,正确计算零件结构的工作能力,确定尺寸,掌握了浇冒口的作用及其原理,具有正确设计浇冒口系统的初步能力;掌握铸造工艺和工装设计的基本技能。
熟悉型砂必须具备的性能要求,原材料的基本规格及作用,并初步具备分析和解决型砂有关问题的能力。
熟悉涂料的作用、基本组成及质量的控制;了解提高铸件表面质量和尺寸精度的途径。
了解合金在铸造过程中容易产生的铸造缺陷以及采取相关的防止途径,并初步具备分析、解决这类缺陷的基本解决途径学习进行设计基础技能的训练,例如:计算、绘图、查阅设计资料和手册等。
目录第一章零件铸造工艺分析 (4)1.1零件基本信息 (4)1.2材料成分要求 (4)1.3铸造工艺参数的确定 (4)1.3.1铸造尺寸公差和重量公差 (5)1.3.2机械加工余量 (5)1.3.3铸造收缩率 (5)1.3.4拔模斜度 (5)1.4其他工艺参数的确定 (5)1.4.1工艺补正量 (5)1.4.2分型负数 (5)1.4.3非加工壁厚的负余量 (5)1.4.4反变形量 (5)1.4.5分芯负数 (6)第二章铸造三维实体造型 (6)2.1上冠件图纸技术要求 (6)2.2上冠件结构工艺分析 (6)2.3基于UG零件的三维造型 (6)2.3.1软件简介 (6)2.3.2零件的三维造型图 (6)第三章铸造工艺方案设计 (7)3.1工艺方案的确定 (7)3.1.1铸造方法 (7)3.1.2型(芯)砂配比 (8)3.1.3混砂工艺 (8)3.1.4铸造用涂料、分型剂及修补材料 (8)3.2铸造熔炼 (8)3.2.1熔炼设备 (9)3.2.2熔炼工艺 (9)3.3分型面的选择 (9)3.4砂箱大小及砂箱中铸件数目的确定 (10)3.5砂芯设计及排气 (11)3.5.1芯头的基本尺寸 (11)3.5.2芯撑、芯骨的设计 (12)3.5.3砂芯的排气 (12)第四章浇冒系统的设计及计算 (12)4.1浇注系统的类型及选择 (12)4.2浇注位置的选择 (12)4.3浇注系统各部分尺寸的计算 (13)4.3.1合金铸造性能分析 (13)4.3.2铁液在型内的上升速度 (13)4.3.3浇注系统截面尺寸设计 (14)4.4冒口设计计算 (14)4.4.1铸件工艺出品率 (14)4.4.2出气孔 (15)4.4.3冒口的作用及位置确定 (15)4.5冷铁设计及尺寸计算 (15)4.5.1冷铁的选用及作用 (15)4.5.2冷铁的尺寸及放置位置的选择 (15)总结 (17)参考文献 (18)附图第一章零件铸造工艺分析1.1零件基本信息零件名称:上冠铸件。
支座铸造设
河南机电高等专科学校毕业论文毕业论文题目:支座铸造工艺设计系部:材料工程系专业: 材料成形于控制技术班级:材料成形于控制技术121班学生姓名:***学号:*********指导教师:***2015年4 月 10日支座铸造工艺设计摘要:本支座为一小型铸件,铸件材质 HT200,结构简单,无复杂的型腔和阻碍起模的凸起。
铸件的外形尺寸为 200mm× 110mm× 120mm,主要壁厚为 15m m,壁厚均匀。
支座采用 HT200 是一种较高强度铸铁,基体为珠光体,强度、耐磨性、耐热性均较好,减振性也良好,铸造性能较好。
从支座的整体结构特点出发,进行铸造工艺设计分析,确定铸造方案,并进行铸造工艺参数和砂芯的设计,在此基础上再根据铸件的材质重量和浇注系统性能设计补缩系统。
采用粘土砂手工造型、制芯、金属摸样和半封闭加注系统,设计时应综合考虑各方面因素,浇注系统不是简单地金属液流动通道,用 proe 三维造型后,采用华铸 CAE 软件对设计方案进行浇注、凝固模拟计算。
结果显示,浇注系统设计合理,但凝固时铸件上表面有明显的缩孔缩松,经仔细观察此缩孔在铸件刚开始凝固时都已经产生,分析原因是因为铸件为湿型,开始凝固时吸收较多的热量,使上表面先凝固下沉,产生凹坑阻碍金属液补缩,为了避免此缺陷的产生减少热量散失浇筑前铸件进行预热,改进工艺后再次运用华铸 CAE 模拟铸件无明显缺陷。
由于铸件模数较小 M=1.5cm,HT200 凝固时伴随着石墨的析出与膨胀,铸件以层状-糊状方式凝固,其共晶膨胀压力小,加之石墨片尖端伸向铁液的生长方式,使其有很好的“自补”能力,需要的补缩金属液较少,件工艺出品率为 75%。
关键词:支座;工艺设计;华铸 CAESupport casting process designAbstract: This bearing is a small-sized castings, casting material HT200, structure is simple, no complicated cavity and hinder the draw. The shape of the casting size for 200 mmx110mmx120mm, main wall thickness is 15 mm, wall thickness uniformity. Bearing adopts HT200 is a kind of high strength cast iron, for pearlite matrix, and the strength, abrasion resistance and heat resistance are good, vibration is also good; Casting performance is good. Starting from the overall structure of the bearing characteristics, analysis of casting process design, casting solution is determined, and the casting process parameters and the design of sand core, on this basis, according to the material weight of casting and pouring system and feeding system design performance. Using clay sand handmade molding and core making, metal touch kind and semi-closed charging system, gating system design should be considered when factors not simply metal fluid flow channels, after using proe 3 d modelling, the China casting CAE software is adopted to design plans for pouring and solidification simulation. , according to the results of gating system design is reasonable, but the casting surface has obvious shrinkage on the shrinkage, carefully observe the shrinkage in casting solidification have been produced at first, analysis the reason is because the casting for wet and solidifies when absorbs more heat, making the surface solidification down first, the pits producing metal liquid feeding, in order to avoid the defect of reduce the heat lost preheated before pouring casting, improve the process after casting CAE simulation casting again using China has no obvious defects. Due to casting modulus of 1.5 cm, smaller HT200 with graphite precipitation and solidification of casting, solidification in layered - paste way, its eutectic expansion pressure is small, and flake graphite tip to the growth of iron liquid, so that it is a very good ability to "repair", and need less feeding metal, pieces of craft production rate was 75%.Key words: Support; process planning; Hua Zhu CAE目录毕业论文 (1)1 绪论 (5)1.1国内铸造现状及发展趋势 (5)1.1.1国内铸造的现状 (5)2设计任务 (7)2.1 铸造方案的确定 (8)2.2支座结构的铸造工艺性分析 (8)2.3造型造芯方法的选择 (10)2.4浇注位置的选择 (10)2.5支座分型面的选择 (11)2.6砂箱中铸件数目的确定 (14)3 铸造工艺参数的确定 (15)3.1 铸件的尺寸公差 (15)3.2 机械加工余量 (15)3.3 铸件收缩率 (15)3.4 起模斜度 (15)3.5 最小铸出的孔和槽 (16)3.6 工艺补正量 (16)3.7 浇注温度和铸件在铸型中的冷却时间 (16)4 砂芯的设计 (17)4.1 芯头的设计 (17)4.2 砂芯的定位结构 (17)4.3 压环、防压环和集砂槽的尺寸 (18)4.4 芯骨 (18)4.5 芯撑 (18)4.6 砂芯的排气 (18)5 浇注系统及冒口、冷铁、出气孔的设计 (19)5.1 浇注系统类型的选择 (19)5.2 浇注时间的计算 (19)5.3 阻流元截面积的计算及各阻流原件的比例关系的确定 (20)5.4.确定内浇道的截面积 (20)5.5 确定横浇道截面积 (21)5.6 确定直浇道的截面积 (21)5.7直浇道窝的设计 (22)5.8 浇口杯的设计 (22)5.9 冒口的设计 (23)5.10 冷铁的设计 (23)5.11 出气孔的设计 (23)6 支座浇注、凝固过程模拟分析 (24)6.1 华铸 CAE 简介 (24)6.2 华铸 CAE 模拟分析的步骤 (24)6.3 华铸 CAE 模拟支座浇注、凝固过程分析报告 (24)7 铸造工艺装备的设计 (27)7.1 模板的设计 (27)7.2 芯盒的设计 (27)8 总结 (28)8.1 铸造工艺图 (28)8.2 铸造工艺卡 (28)9 结论 (29)10 致谢 (30)参考文献 (31)1 绪论铸造行业是制造也的重要组成本部分,对国民经济发展起着重要的作用。
轴承支座铸造工艺设计 (全套图纸)
轴承支座铸造工艺设计目录摘要 (4)1 铸钢件初步分析 (5)1.1 基本信息 (5)1.2 实用性分析 (5)2可铸性分析 (4)2.1材料的化学成分及铸造性能 (7)2.2 最小壁厚 (7)2.3 临界壁厚 (8)2.4 铸件壁的过渡和连接 (8)2.5 加强肋分析 (9)3 铸造工艺方案的设计 (10)3.1 造型方法和材料选取 (10)3.1.1 呋喃树脂砂成分的选择 (10)3.1.2 铸造涂料的选择 (10)3.2 铸造工艺参数的确定 (11)3.2.1 铸件尺寸公差 (11)3.2.2 机械加工余量 (11)3.2.3 铸件收缩率 (12)3.2.4 起模斜度 (13)3.2.5 最小铸出孔和槽 (13)3.2.6 补充说明 (13)3.3 摆放位置与分型面 (13)3.3.1 摆放位置的确定 (13)3.3.2 分型面的确定 (14)3.4 浇注系统设计 (15)3.4.1 设计原则 (15)3.4.2 确定浇注位置 (16)3.4.3 各浇道截面计算 (17)3.4.4 浇口杯的选择 (19)3.5 冒口和冷铁设计 (20)3.5.1冒口的设计 (20)3.5.2冷铁的设计 (22)4 工艺方案优化 (23)4.1 铸件缺陷分析 (23)4.2缺陷改进 (25)5 砂芯及芯盒的设计 (27)5.1 制芯方法的确定 (27)5.2 芯头的定位和间隙 (27)5.3 芯骨的设计 (28)5.4 砂芯的排气 (28)5.5芯盒的设计 (29)6 铸造工艺工艺装备设计 (30)6.1 砂箱的选择与设计 (30)6.1.1 砂箱及其附件的材料 (30)6.1.2 砂箱各部分的机构和尺寸 (30)6.2 模样的设计 (36)6.3 铸型造型 (36)7熔炼和后处理 (37)7.1 铸钢的熔炼 (37)7.1.1 配料 (37)7.1.2 熔炼过程的技术要求 (37)7.2 铸件的清理 (40)7.2.1 铸件的落砂除芯 (40)7.2.2 浇冒口和毛刺的去除 (40)7.2.3 铸件的表面清理 (40)7.2.4 铸件的热处理 (40)7.3 气孔缺陷的防治 (41)8 参考文献 (42)零件图铸件图摘要本工艺方案的设计准则是:在保证铸件质量的前提下,尽量提高方案的经济性和可实施性。
- 1、下载文档前请自行甄别文档内容的完整性,平台不提供额外的编辑、内容补充、找答案等附加服务。
- 2、"仅部分预览"的文档,不可在线预览部分如存在完整性等问题,可反馈申请退款(可完整预览的文档不适用该条件!)。
- 3、如文档侵犯您的权益,请联系客服反馈,我们会尽快为您处理(人工客服工作时间:9:00-18:30)。
热加工工艺课程设计支座铸造工艺设计院系:工学院机械系专业:机械设计制造及其自动化班级:姓名:学号:指导老师:时间:黄河科技学院课程设计任务书工学院机械系机械设计制造及其自动化专业 2011级 1班学号姓名指导教师设计题目: 支座铸造工艺设计课程名称:热加工工艺课程设计课程设计时间:5 月 22 日至 6 月 6 日共 2 周课程设计工作内容与基本要求(已知技术参数、设计要求、设计任务、工作计划、所需相关资料)(纸张不够可加页)1、已知技术参数图1 支座零件图2、设计任务与要求1)设计任务1 选择零件的铸型种类,并选择零件的材料牌号。
2 分析零件的结构,找出几种分型方案,并分别用符号标出。
3 从保证质量和简化工艺两方面进行分析比较,选出最佳分型方案,标出浇注位置和造型方法。
4 画出零件的铸造工艺图(图上标出最佳浇注位置与分型面位置、画出机加工余量、起模斜度、铸造圆角、型芯及型芯头,图下注明收缩量)5 绘制出铸件图。
2)设计要求1设计图样一律按工程制图要求,采用手绘或机绘完成,并用三号图纸出图。
2 按所设计内容及相应顺序要求,认真编写说明书(不少于3000字)。
3、工作计划熟悉设计题目,查阅资料,做准备工作 1天确定铸造工艺方案 1天工艺设计和工艺计算 2天绘制铸件铸造工艺图 1天确定铸件铸造工艺步骤 2天编写设计说明书 3天答辩 1天4.主要参考资料《热加工工艺基础》、《金属成形工艺设计》、《机械设计手册》系主任审批意见:审批人签名:时间:2013年月日支座铸造工艺设计摘要铸造是指将液态金属或合金浇注到与零件尺寸、形状相适应的铸型型腔里,待其冷却凝固后获得毛坯或零件的方法。
铸造成形是机械类零件和毛坯成形的重要工艺方法之一,尤以适合于制造内腔和外形复杂的毛坯或零件。
本文主要分析了支座的结构,并根据其结构特点确定了它的砂型铸造工艺。
支座是支撑其他零部件的重要承力零件,主要承受着径向压缩及轴向摩擦的作用,它具有结构稳定、形状简单、廉价实用等特点,故在机械零件的设计、加工制造中支座都起着不可替代的作用。
本文设计了支座的砂型铸造工艺,包括铸型(型芯)及造型方法的选择、分型面选择和浇注位置的确定、浇注系统及冒口的设置、落砂清理及检验等。
绘制了铸件的零件图及铸造工艺图。
本文还对支座的铸造质量指标(包括加工余量、拔模斜度、收缩率及变形等)进行了分析与评估,以便于工艺更好的完善。
关键词:砂型铸造,浇注,加工余量,拔模斜度,收缩率目录1 绪论 (1)2支座的结构及工艺性分析 (2)铸件的结构分析 (2)铸件的尺寸分析铸件的工艺分析 (2)3支座的结构与分析 (3)支座的分析 (3)支座的工艺分析 (3)4支座具体设计方案步骤 (4)铸型及方法选择 (4)分型面选择 (5)浇注位置的确定 (6)铸造工艺参数的确定 (7)浇注系统设置 (8)铸造工艺图绘制 (9)铸件图绘制 (11)5支座铸造工艺卡 (12)总结.................................................................................... . (13)致谢.................................................................................... . (13)参考文献 (14)1 绪论铸造是人类掌握比较早的一种金属热加工工艺,已有约6000年的历史。
中国约在公元前1700~前1000年之间已进入青铜铸件的全盛期,工艺上已达到相当高的水平。
铸造是指将固态金属溶化为液态倒入特定形状的铸型,待其凝固成形的加工方式。
被铸金属有:铜、铁、铝、锡、铅等,普通铸型的材料是原砂、黏土、水玻璃、树脂及其他辅助材料。
特种铸造的铸型包括:熔模铸造、消失模铸造、金属型铸造、陶瓷型铸造等。
(原砂包括:石英砂、镁砂、锆砂、铬铁矿砂、镁橄榄石砂、兰晶石砂、石墨砂、铁砂等)。
我国古代铸造技术居世界先进行列。
由于过长的封建社会影响了科学技术的发簪,阻滞了铸造技术前进的步伐。
心中过成立以来的50多年中,自20世纪50年代初至今,几乎从零开始,逐步发展到现在这样的规模,成绩是巨大的。
现在铸造在我国是一个很大的行业,产量居世界第二位,达年产1000万-1200万吨,厂点多大2万多个,职工100-130万人,其中工程技术人员约占%,已经成为了国家重要的的基础工业之一。
支座铸造工艺设计的总体思路是:首先确定支座的铸造工艺方案,分析铸件的结构,然后选定铸件材料、确定铸型(型芯)的造型(制芯)方法、确定浇注位置、绘制铸造工艺图。
重点考虑浇注位置,铸型分型面,型芯的形状、尺寸和数量及固定方法,加工余量,收缩率,浇注系统,起模斜度,冒口和冷铁的尺寸和位置等。
铸件材料是依据支座的强度、刚度以及使用寿命、加工精度等方面的要求来选择,本设计中支座材料选用HT150。
另外,型砂和芯砂的配制和使用直接影响铸件质量和成本,铸型材料选粘土砂,型芯则采用树脂砂。
采用恰当的工艺措施可控制铸件质量,明显提高生产率,降低成本。
2支座的结构及工艺性分析支座的结构及尺寸分析支座是机械工程中最为常用的一种零件,其工作环境也相对比较复杂,可能受到各种力的的作用,在这些力中对支座影响最大的是收到了轴向的压缩作用,为了防止其受到这些因素而发生裂纹或破坏,我们在选择材料进行浇注加工时尤为注意选择能使在工作过程中不至于受压破坏。
而铸造件在铸造的时候必须严格按照铸造工艺手册中正确的操作方式对支座零件进行有效的铸造操作使其能有效的符合我实用时的标准,是经济性实用性大大的提升。
对于要求更高的支座可通过对其相应的处理使其得更好的力学性能。
同时用铸件做零件毛坯可以减少用材,和二次切削所浪费的材料,不仅节约材料也大大的提高了经济性。
合理的铸件结构是获得优质铸件的前提,也是简化铸造工艺、提高生产率和降低成本的根本保证。
需要铸造的零件的结构不仅要满足工作性能和力学性能的要求,同时还应该满足铸造工艺、方法和砂型铸造性能的基本要求,还能在很小改动下使铸件结构与这些要求相适应,力求工艺简单,能够经济、迅速的生产出合格的铸件。
铸件具有以下几个优越性:1)可以制成形状复杂的,特别是复杂内嵌的毛坯、2)由于是直接用液态金属浇注形成的形状复杂各异的铸件。
此机架铸件以中心轴为对称轴有一个尺寸为50mm的空心圆柱,长为200mm。
两边有两个凸台,每个凸台中都有一个尺寸我Φ15的空心圆柱,此两空心圆柱线间的距离为145mm。
凸台高30mm,表面粗糙度为.支架为120mm,下底面表面粗糙度为,上顶面表面粗糙度为,支架大圆为Φ80mm。
铸件的特点是通过制作出各种形状复杂的金属结构材料模型,然后融化金属材料对模型进行系统性的浇注,然后冷却、凝固从而获得所需的具有复杂结构特点的毛坯、零件。
这样所得的铸件具有稳定性好,结构性强,经济性好等特点。
铸造方法可分为:砂型铸造、熔模铸造、金属型铸造、压力铸造、低压铸造、离心铸造等,其中砂型铸造是最为常见的也是最基本的工艺方法,它适用于各种形状、大小、批量及各种合金铸件的生产。
掌握砂型铸造是合理选择铸造方法和正确设计铸件的基础。
确定好铸造方式后还要对其进行造型及造芯的选择等,其中造型的方法包含了:砂箱造型、劈箱造型、叠箱造型、刮板造芯等。
在制定工艺方案之前,对熟悉图样和铸件的使用要求,掌握实际生产的现有条件,以图样技术要求、生产批量和使用信息为依据,分析铸件结构,选择铸型种类、确定造型和造芯的方法等,以便为铸造工艺的拟定奠定基础。
支座的工艺分析根据支座的工作条件,综合考虑支座的结构及其在经济性、工艺性和使用性等方面的要求,对支座的工艺性进行深入的分析。
支座零件结构的铸造工艺性是指零件的结构应符合铸造生产的要求,易于保证铸件品质,简化铸件工艺过程和降低成本。
审查、分析应考虑如下几个方面:(1)铸件应有合壁厚,为了避免浇不到、冷隔等缺陷,铸件不应太薄;(2)铸件结构不应造成严重的收缩阻碍,注意薄壁过渡和圆角铸件薄厚壁的相接拐弯等厚度的壁与壁的各种交接,都应采取逐渐过渡和转变的形式,并应使用较大的圆角相连接,避免因应力集中导致裂纹缺陷;(3)铸件内壁应薄于外壁,铸件的内壁和肋等,散热条件较差,应薄于外壁,以使内、外壁能均匀地冷却,减轻内应力和防止裂;(4)壁厚力求均匀,减少肥厚部分,防止形成热节;(5)利于补缩和实现顺序凝固;(6)防止铸件翘曲变形;(7)避免浇注位置上有水平的大平面结构。
3支座铸造工艺方案设计铸型及造型方法的选择图支座三维图(外形图)支座零件具有支座底平面、紧固孔、与支座底平面相垂直的支承孔及支承孔两端面等。
支座的外形图如图所示,支座的零件图如图所示,支座的外形轮廓尺寸为200mm*110mm*120mm,主要壁厚26mm,最小壁厚15mm,为一小型铸件;铸件除满足几何尺寸精度及材质方面的要求外,无其他特殊技术要求.支座零件具有内腔、小空、圆角、凸台、以及锥角,形状复杂,其表面无特殊要求。
零件的最大轮廓尺寸为200mm,零件较复杂,应选砂型铸造成型,采用单件小批量生产。
中小型铸件尽量选择湿型,因此铸件的铸型种类为湿砂型铸造。
由于支座零件为回转体结构件,产品生产性质适合于做批量生产。
零件材料选用HT150.图支座的零件图分型面的选择分型面的选择应遵循以下几点:(1)应使铸件全部或大部分位于同一砂型内,或使主要加工面与加工的基准面处于同一砂型中,以防错型,保证铸件尺寸精度,便于造型和合型操作。
若铸件的加工面很多,又不可能都与基准面放在分型面的同一侧时,则应使加工基准面与大部分加工面处在分型面的同一侧。
(2)应尽量减少分型面的数量,最好只有一个分型面。
这样可简化操作过程,提高铸件精度 (因多一个分型面,铸型就增加一些误差)(3)应尽量使型腔和主要型芯处于下型,以便于造型,下芯,合型及检验型腔尺寸。
但下型的型腔不宜过深,并避免使用吊芯和大的吊砂。
(4)应尽量选用平直面作分型面,少用曲面,以简化制模和造型工艺。
(5)应尽量减少型芯和活块的数量,以简化制模、造型、合型等工序。
(6)分型面应选在铸件的最大截面处,以保证从铸型中取出模样,而不损坏铸型。
具体选择铸件分型面时,为保证铸件质量,应尽量避免合型后翻转砂型。
一般应首先确定浇注位置,再考虑、分型面。
对于质量要求不高的铸件,应先选择能使工艺简化的分型面,而浇注位置的选择则处于次要地位。
本设计选择分型面主要考虑使铸件全部或大部分置于同一半型内,并尽量减少分型面的数目,且分型面应尽量选用平面,以便于下芯、合箱和检测,不使砂箱过高,受力件的分型面的选择不应削弱铸件结构强度,注意减轻铸件清理和机械加工量。