模具毕业设计Word版
(模具专业)毕业设计文献综述参考word
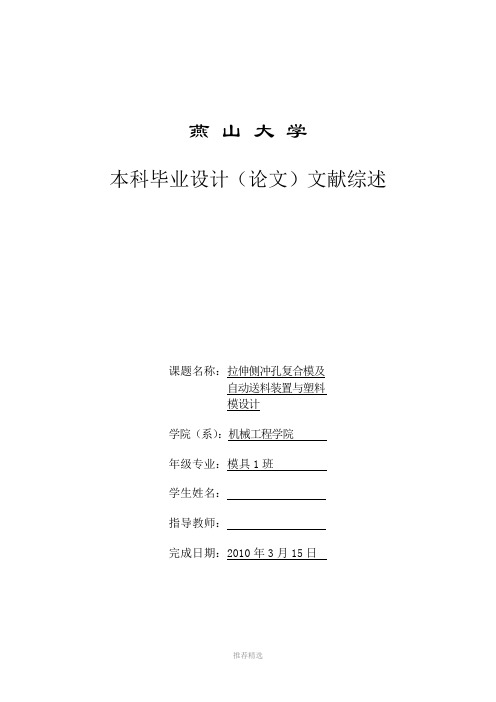
燕山大学本科毕业设计(论文)文献综述课题名称:拉伸侧冲孔复合模及自动送料装置与塑料模设计学院(系):机械工程学院年级专业:模具1班学生姓名:指导教师:完成日期:2010年3月15日一、课题国内外现状模具生产技术水平的高低,已成为衡量一个国家产品制造水平高低的重要标志[2]。
因为模具在很大程度上决定着产品的质量、效益和新产品的开发能力。
在电子、汽车、电机、电器、仪器、仪表、家电和通信等产品中60%—80%的零部件都要依靠模具成型。
用模具生产部件所具备的高精度、高复杂程度、高一致性、高生产率和代消耗,是其他加工制造方法所不能比拟的。
模具又是“效益扩大器”,用模具生产的最终产品的价值,往往是模具自身价值的几十倍、上百倍。
目前,全世界模具年产值约为600亿美元,日、美等工业发达国家的模具工业产值已超过机床工业。
我国的模具工业的发展,也日益受到人们的关注和重视。
近几年,我国模具工业一直以每年15%左右的增长速度发展。
二、研究主要成果现代模具设计的内容是:产品零件(常称为制件)成型工艺优化设计与力学计算,尺寸与尺寸精度确定与设计等,因此模具设计常分为制件工艺分析与设计、模具总体方案设计、总体结构设计、施工图设计四个阶段[7]。
(1)AD/CAE/CAM 计算机辅助设计、模拟与制造一体化CAD/CAE/CAM 一体化集成技术是现代模具制造中最先进、最合理的生产方式。
(2)设备在现代模具制造中的作用现代模具制造尽可能地用机械加工取代人工加工。
这就确定了先进设备在现代制造中的作用,尤其现在加工中心、数控高速成型铣床、数控铣床、数控车床、多轴联动机床、数控模具雕刻机、电火花加工机床、数控精密磨床、三坐标测量机、扫描仪等现代化设备在工厂中的广泛使用。
(3)代模具制造中的检测手段模具的零部件除了有高精度的几何要求外,其形位精度要求也较高,一般的量具是很难达到理想的目的,这时就要依赖精密零件测量系统。
这种精密零件测量系统简称C M M ,即Coordinate Measuring Machine ,是数控加工中心的一种变形。
模具专业毕业设计---精品模板

XX职业技术学院毕业设计门锁垫片复合模系部专业名称班级姓名学号指导教师年月日摘要本文介绍了门锁垫片冲压模工作零件设计与加工的全过程。
首先对制件进行分析、冲压工艺分析以及确定模具的总体结构、计算工作零件的工艺参数、搭边值等,确定了该冲压模的工作零件的结构形式以及加工工艺流程。
并对所设计的工作零件进行了分析说明。
采用UG软件绘制了冲压模具工作零件的三维图和CAXA软件绘制的非标准零件图,并用线切割电加工机床加工出工作零件.关键词:工作零件;冲压模;三维造型目录1绪论.......................................................................................................................................................... - 1 -2冲压件工艺分析 .................................................................................................................................... - 2 -2.1零件结构 ........................................................................................................................................... - 2 -2.2尺寸精度 ........................................................................................................................................... - 2 -2。
注塑模具毕业设计【范本模板】
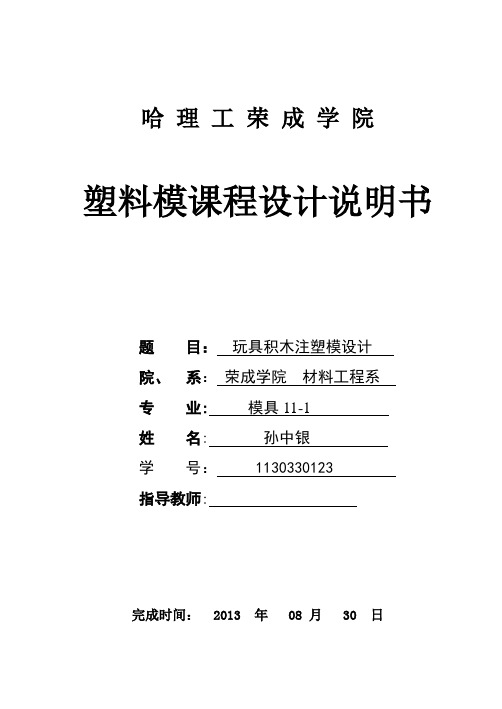
哈理工荣成学院塑料模课程设计说明书题目:玩具积木注塑模设计院、系:荣成学院材料工程系专业:模具11-1姓名: 孙中银学号: 1130330123指导教师:完成时间: 2013 年 08 月 30 日哈理工荣成学院塑料模课程设计任务书目录第1章塑件工艺分析 (3)1。
1 设计任务 (3)1.2 塑件工艺分析 (4)1。
2.1 材料工艺性分析 (4)1.2。
2 尺寸精度工艺性分析 (5)第2章模具结构设计 (6)2。
1模具总体方案确定 (6)2.1 成型设备的选择 (11)第3章模具材料及其热处理方案设计 (11)3.1 模具型芯型腔材料 (12)3.2 模具材料热处理方案 (12)第4章模具及注塑机的校核 (14)4。
1注塑机工艺参数的校核 (14)第5章模具总装图图5-1 (15)结论 (16)参考文献 (17)第1章塑件工艺分析1.1设计任务根据任务设计玩具积木三视图如下图1-11—1玩具积木三视图1-2玩具积木实物图已知技术参数:材料:ABS生产批量:大批量生产1.2塑件工艺分析1.2.1材料工艺性分析ABS是丙烯腈、丁二烯和苯乙烯三种单体聚合而成的非结晶型的高聚物.它是在聚丙乙烯基础上改性而发展起来的一种热塑性工程塑料。
由于聚苯乙烯的突出缺点是耐冲击性能较差,耐热性不够高,因而限制了它的应用范围。
而三种单体合成的ABS塑料是一种综合性能优良的在工程技术中广泛应用的新型塑料。
1.ABS塑料的使用性能:由于ABS是三种单体聚合而成的,因此它具有三种组成物的综合性能。
丙烯腈可使ABS具有较高的强度、硬度、耐热性及耐化学稳定性;丁二烯可使ABS具有弹性和较高的冲击强度;苯乙烯可使ABS具有优良的介电性能和成型加工性能。
由此可见,还可以通过改变组成物的比例,生产出不同品种的ABS塑料。
ABS塑料在一定的温度范围内具有较高的冲击强度和表面硬度及耐磨性;它的热变形温度为100℃左右,比聚苯乙烯、聚氯乙烯、聚酰胺都高;还具有一定的化学稳定性和良好的介电性能;此外它还有能与其他塑料和橡胶混溶等特性;其制品尺寸稳定性不好,表面光泽,可以抛光和电镀。
(完整版)冲压模具设计毕业设计

摘要本设计是对给定的产品图进行冲压模具设计。
冲压工序的选择是经查阅相关资料和对产品形状仔细分析的基础上进行的;冲压模具的选择是在综合考虑了经济性、零件的冲压工艺性以及复杂程度等诸多因素的基础上进行的;产品毛坯展开尺寸的计算是在方便计算但不影响模具成型的前提下简化为所熟悉的模型进行的。
文中还对冲压模具成型零件和其他相关零件的选择原则及选择方法进行了说明。
冲压件的设计首先要从冲压生产工艺上对所要设计的铁芯片进行冲压工艺的分析与计算,然后在分析计算的基础上并参看相关的冲压设计资料确定冲压工艺方案,再在此基础上确定各工序的复合关系后,再进入冲模各具体结构的设计。
在此基础上对各副冲压模具的主要零部件的尺寸进行设计与计算,期间要参考大量与冲压相关的资料和翻阅各种“冲压手册”,并通过计算以确定各副模具具体的结构及尺寸,通过不断的计算与修改,并在指导老师的悉心关怀和耐心指导下进行不间断的反复修改,最终确定画出了一副装配图和3副零件图和一张立体图。
通过这次毕业设计使我了解和掌握了许多实际的东西,结合我在生产实习中所看所想的一些东西,有了自己的一些收获。
在此特别感谢学院,学校各位老师给我的这次机会和悉心指导。
【关键词】冲压工序,冲压模具,冲压工艺,设计计算AbstractThe design of a given product plans for stamping die design. Stamping process is the choice of the available relevant information and a detailed analysis of the shape of the products on the basis of; stamping die option is considered in the economy, parts of the stamping process and the complexity of many factors, and so on the basis of; Products rough start calculating the size is calculated at a convenient but does not affect mold forming on the premise familiar to simplify the model. The paper also forming part of the stamping dies and other relevant parts of the principle of choice and select the method described. Stamping parts from the design of the first stamping on the production process to be designed to cover iron of chipfor stamping process of analysis and calculation and then calculated on the basis of analysis and see stamping design information related to determine the programme stamping process, and on this basis The process of determining the relationship, and then entered the concrete structure of the die design. On this basis, all of the major parts stamping die design and size, the large number of reference during the relevant information with the press and read all kinds of "stamping Manual" and calculated to determine the specific mold of the structure and Size, by the calculation and constant changes in the careful guidance of teachers under the guidance of patient care and continuously repeated changes to draw the final 1 assembly and 3 parts map. Through this I graduated from design to understand and master the many practical things with my internship in the production of which would like to see some of the things, withsome of their own this special thanks to college, school teachers forgiving me this opportunity and the careful guidance.Key words:S tamping process, Stamping dies, Sheet metal forming technology, Designcalculation目录1绪论 ...........................................................1.1冲压的概念、特点及应用.........................................1.2冲压的基本工序及模具..........................................1.3冲压技术的现状及发展方向......................................2 冲裁件工艺性及材料分析............................................2.1冲裁件的工艺性分析............................................2.2冲裁件的精度与粗糙度..........................................2.3冲裁件的材料 (1)3冲压模具总体结构设计 (1)3.1模具类型 (1)3.2操作与定位方式 (1)3.3卸料与出件方式 (1)3.4模架类型及精度 (1)4冲压模具工艺与设计计算 (1)4.1排样设计与计算 (1)4.2设计冲压力与压力中心,初选压力机 (1)4.2.1冲裁力 (1)4.2.2 压力中心 (1)4.2.3计算凸凹模刃口尺寸及公差 (1)5模具的总体零件设计与图纸 (1)5.1铁芯片冲压模具装配图 (1)5.2模具的零件设计 (1)5.2.1 凹模设计 (1)5.2.2 凸模设计 (1)5.2.3选择坚固件及定位零件 (1)结论 (1)谢辞 (1)参考文献 (2)1绪论1.1冲压的概念、特点及应用冲压是利用安装在冲压设备(主要是压力机)上的模具对材料施加压力,使其产生分离或塑性变形,从而获得所需零件(俗称冲压或冲压件)的一种压力加工方法。
冲压模具毕业设计范本(doc 55页)

冲压模具毕业设计范本(doc 55页)固定夹冲压弯曲模设计目录1 绪论 (1)2 冲裁弯曲件的工艺设计 (1)3 确定工艺方案及模具的结构形式 (2)4 模具设计工艺计算 (3)4.1 计算毛坯尺寸 (3)4.2 排样、计算条料宽度及距的确定 (5)4.2.1 搭边值的确定............................................................ . (5)4.2.2 条料宽度的确定 (7)4.2.3 到料板间距的确定 (7)4.2.4 排样 (8)4.2.5 材料利用率的计算 (8)5 冲裁力的计算 (10)5.1 计算冲裁力的公式 (10)5.2 总的冲裁力、卸料力、推件力、顶件力、弯曲力和总的冲压力 (11)5.2.1 总的冲裁力 (11)5.2.2 卸料力FQ的计算 (12)5.2.3 推料力FQ1的计算 (12)5.2.4 顶件力FQ2的计算 (12)5.2.5 弯曲力F C的计算 (13)5.2.6 总冲压力的计算……………………................................................. ..146 模具压力中心与计算 (14)7 冲裁间隙的确定 (15)8 刃口尺寸的计算 (16)8.1 刃口尺寸计算的基本原则 (16)8.2 刃口尺寸的计算 (17)8.3 计算凸、凹模刃口的尺寸 (18)8.4 冲裁刃口高度 (21)8.5 弯曲部分刃口尺寸的计算 (21)8.5.1 最小弯曲半径 (21)8.5.2 弯曲部分工作尺寸的计算 (22)9 模具总的结构设计 (25)9.1 模具类型的选择 (25)9.2 定位方式的选择 (25)9.3 卸料方式的选择 (25)9.4 导向方式的选择 (25)10 主要零部件的设计 (26)10.1 工作零件的设计 (26)10.1.1 凹模的设计 (26)10.1.2 凸凹模的设计 (27)10.1.3 外形凸模的设计………………………………………………… ..2710.1.4 内孔凸模的设计 (28)10.1.5 弯曲凸模的设计 (28)10.2 卸料部分的设计 (29)10.2.1 卸料板的设计 (29)10.2.2 卸料弹簧的设计 (29)10.3 定位零件的设计 (31)10.4 模架及其他零部件的设计 (31)10.4.1 上下模座 (31)10.4.2 模柄 (32)10.4.3 模具的闭合高度 (32)11 模具总装图 (33)12 压力机的选择 (33)总结 (34)致谢 (35)摘要本文介绍的模具实例结构简单实用,使用方便可靠,首先根据工件图算工件的展开尺寸,在根据展开尺寸算该零件的压力中心,材料利用率,画排样图。
冲压模具毕业设计范文

冲压模具设计实例:选择合适的冲 压模具设计实例
模拟结果:观察模拟结果,分析模 具工作过程
添加标题
添加标题
添加标题
添加标题
模拟过程:使用计算机辅助设计软 件进行模拟
优化设计:根据模拟结果对冲压模 具设计进行优化
冲压模具设计优化
优化目标:提高模 具寿命、降低成本、 提高生产效率
材料类型: 钢、铝、 铜、塑料 等
材料性能: 强度、硬 度、耐磨 性、耐腐 蚀性等
材料成本: 经济性、 可回收性 等
模具寿命: 耐用性、 维护成本 等
加工工艺: 铸造、锻 造、热处 理等
环保要求: 无毒、无 污染等
模具尺寸:根据冲压件的尺 寸和精度要求确定模具尺寸
模具材料:选择合适的模具 材料,如钢、铝、铜等
冲压模具毕业设计范 文
汇报人:
目录
冲压模具设计概述
冲压模具设计基础
冲压模具设计实例
冲压模具设计优化
冲压模具设计规范 与标准
冲压模具设计展望
冲压模具设计概述
冲压模具:用于将金属板材或非金属板材通过压力加工成所需形状的模具 定义:冲压模具是一种特殊的成型工具,用于将金属板材或非金属板材通过压力加工成所需形状 作用:冲压模具可以大大提高生产效率,降低生产成本,提高产品质量 应用领域:广泛应用于汽车、家电、电子、机械、航空航天等领域
模具类型:根据冲压工艺选 择合适的模具类型
模具精度:根据冲压件的精 度要求确定模具精度
模具寿命:根据冲压件的生产 数量和生产周期确定模具寿命
模具维护:定期对模具进行维 护和保养,保证模具的正常使
用
冲压模具设计实例
零件名称: 冲压模具
模具设计书毕业设计范文
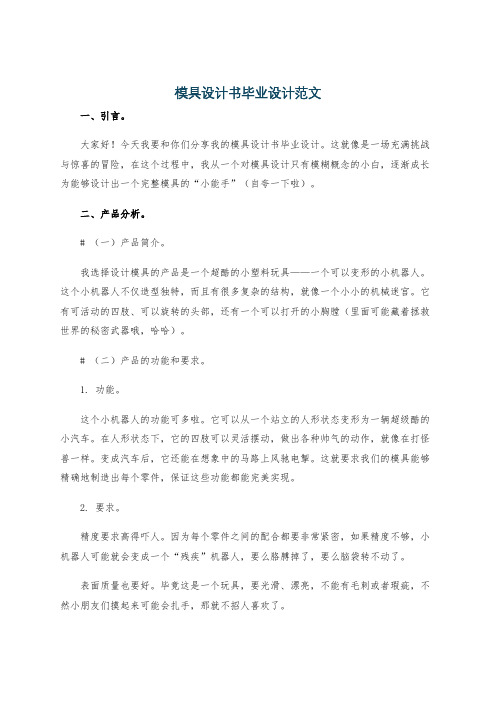
模具设计书毕业设计范文一、引言。
大家好!今天我要和你们分享我的模具设计书毕业设计。
这就像是一场充满挑战与惊喜的冒险,在这个过程中,我从一个对模具设计只有模糊概念的小白,逐渐成长为能够设计出一个完整模具的“小能手”(自夸一下啦)。
二、产品分析。
# (一)产品简介。
我选择设计模具的产品是一个超酷的小塑料玩具——一个可以变形的小机器人。
这个小机器人不仅造型独特,而且有很多复杂的结构,就像一个小小的机械迷宫。
它有可活动的四肢、可以旋转的头部,还有一个可以打开的小胸膛(里面可能藏着拯救世界的秘密武器哦,哈哈)。
# (二)产品的功能和要求。
1. 功能。
这个小机器人的功能可多啦。
它可以从一个站立的人形状态变形为一辆超级酷的小汽车。
在人形状态下,它的四肢可以灵活摆动,做出各种帅气的动作,就像在打怪兽一样。
变成汽车后,它还能在想象中的马路上风驰电掣。
这就要求我们的模具能够精确地制造出每个零件,保证这些功能都能完美实现。
2. 要求。
精度要求高得吓人。
因为每个零件之间的配合都要非常紧密,如果精度不够,小机器人可能就会变成一个“残疾”机器人,要么胳膊掉了,要么脑袋转不动了。
表面质量也要好。
毕竟这是一个玩具,要光滑、漂亮,不能有毛刺或者瑕疵,不然小朋友们摸起来可能会扎手,那就不招人喜欢了。
三、模具设计方案。
# (一)模具类型的选择。
经过深思熟虑(其实就是在图书馆翻了好多资料,还请教了老师之后),我决定采用注塑模具。
为什么呢?因为注塑模具可以高效地生产出我们需要的小机器人零件。
就像做小饼干一样,把塑料原料像面团一样注入模具里,然后就可以快速地得到我们想要的形状。
而且注塑模具还可以很好地保证产品的精度和质量,这对于我们这个复杂的小机器人来说是非常重要的。
# (二)分型面的确定。
分型面就像是模具的“分界线”,确定这个可费了我不少脑细胞。
我得考虑小机器人的外形、结构以及脱模的方便性。
我把分型面定在了小机器人身体的中间部分。
这样做的好处是,在脱模的时候,小机器人的上下部分可以很容易地分开,就像把一个汉堡包从中间切开一样简单。
模具设计毕业论文模板

模具设计毕业论文摘要本课题主要是针对盒盖的模具设计,通过对塑件进展工艺的分析和比拟,最终设计出一副注塑模。
该课题从产品结构工艺性,具体模具结构出发,对模具的浇注系统、模具成型局部的结构、顶出系统、冷却系统、注塑机的选择与有关参数的校核、都有详细的设计,同时并简单的编制了模具的加工工艺。
通过整个设计过程说明该模具能够到达此塑件所要求的加工工艺。
根据题目设计的主要任务是盒盖注塑模具的设计。
也就是设计一副注塑模具来生产盒盖塑件产品,以实现自动化提高产量。
针对盒盖的具体结构,该模具是点浇口的双分型面注射模具。
由于塑件内侧有四个小凸台,无法设置斜导柱,固采用活动镶件的结构形式。
其优点在于简化机构,使模具外形缩小,大大降低了模具的制造本钱。
通过模具设计说明该模具能到达盒盖的质量和加工工艺要求。
关键词塑料模具盒盖模具Abstract This topic mainly aimed at the mold design of plastic lid. Through the analysis and parison of the plastic product , the plastic mold was designed. This topic came from the technology capability of product, the structure of the mold embarks, the pours system, the injection molding system and the related parameter examination, the mold took shape the partial structures, the against system, the cooling system all had the detailed design, at the same time , the processing craft of the mold were simply established. Through the entire process of the design indicated this mold can achieve the processing craft which the plastic lid requested.Key words plastic mold the plastic lid mold1 前言随着中国当前的经济形势的日趋好转,在“实现中华民族的伟大复兴〞口号的倡引下,中国的制造业也日趋蓬勃开展;而模具技术已成为衡量一个国家制造业水平的重要标志之一,模具工业能促进工业产品生产的开展和质量提高,并能获得极大的经济效益,因而引起了各国的高度重视和赞赏。
- 1、下载文档前请自行甄别文档内容的完整性,平台不提供额外的编辑、内容补充、找答案等附加服务。
- 2、"仅部分预览"的文档,不可在线预览部分如存在完整性等问题,可反馈申请退款(可完整预览的文档不适用该条件!)。
- 3、如文档侵犯您的权益,请联系客服反馈,我们会尽快为您处理(人工客服工作时间:9:00-18:30)。
B34天津轻工职业技术学院毕业设计(论文)课题:盒上盖注塑模具设计专业模具设计与制造班级 12模具设计与制造二班学生姓名张玉轩学生学号 12指导教师赵秀文郭卉提交日期成绩答辩日期 2015.4.25 答辩成绩答辩教师总评成绩摘要从分析塑料零件注塑模具设计的全过程,并从其加工工艺性出发,选取了较为合理的设计方案,经工艺计算并初步确定模具结构方案,最后进行模具各个部分零件的设计。
模具采用的是一模两腔的设计,通过对抽芯机构的计算和设计,同时把握模具相关运动部件的设计,其中包括定位零件和成型零件尺寸的计算和校核。
该模具采用了一次分型,使制件的主流道凝料和分流道凝料从模具的成型板中脱出,最后利用推杆推出作用,使制件脱离型芯,达到制件的生产。
同时,本模具的亮点和难点在于有两个带角度的内侧抽芯和其型芯型腔的加工复杂性上,但通过比较合理的斜顶装置可以很完善的达到内抽的效果,并且该机构制造相对简单,可降低模具成本。
在一些零件的选用上也是尽量选取标准件以降低模具造价,型芯和型腔都采用镶拼式的结构,同时运用直通式冷却水道,降低加工难度和成本。
关键词:注塑模分型面型芯型腔浇注系统目录第一章塑件的原始资料 (6)第二章型腔数目的决定及排布 (7)第三章注射机的选择 (8)第四章模具设计 (9)4.1分型面确定 (9)4.2模架的选择 (10)4.3型腔的内径计算 (11)4.4型腔的深度尺寸计算 (11)4.5型芯的计算 (12)4.6浇注系统的初步计算 (13)4.7导向机构的设计 (13)4.8推出机构的组成 (14)第五章注塑机与模具型腔型芯强度校核 (15)参考文献 (16)总结 (17)致谢 (18)第一章塑件的原始资料塑件名称:盒上盖,如图1.1材料:ABS产量:中等批量生产如图1-1所示图1.1塑件塑件的工作条件对精度要求一般,因为塑件图中未注公差,所以根据ABS能可选择其塑件的精度等级为7级精度。
第二章型腔数目的决定及排布已知的体积V塑或质量W塑,又因为此产品属大批量生产的小型塑件,但制件尺寸、精度、表面粗糙度一般,综合考虑生产率和生产成本及产品质量等各种因素,以及注射机的型号选择,初步确定采用一模二腔对称性排布。
分流道直径可选1.5~9.5mm。
本设计取值4mm。
由塑件的外形尺寸和机械加工的因素,确定采用潜浇口,排布图如下图示:图2.1型腔数目及排布第三章 注射机的选择由于采取的是一模二腔的方案,故其注射总体积及质量就是塑件的体积及质量的二倍:假设:g G 8=废,由注射机最大注射量公式得:废件公利G G G K +≥ (3.1)其中:公G —注射机的公称质量注射量;K —注射机最大注射量的利用系数,取0.3;件G —塑件的总质量;废G —浇注系统废料的质量。
由《塑料模具技术手册》查得注射机的型号为XS-ZY-125国产注塑机,其主要技术参数如下:结构型式:卧式 理论注射容量:125cm 3 螺杆直径:42mm 注射压力:150MPa 注射速率:60g/S 塑化能力:11.8g/s 螺杆转速:14~200r/min 锁模力:900KN拉杆内间距:370×320mm 移模行程:270mm 最大模具厚度:300mm 最小模具厚度:200mm 锁模型式:双曲肘式 模具定位孔直径:100mm第四章模具设计4.1分型面确定由于分型面受到塑件在模具中的成型位置、浇注系统设计、塑件的结构工艺性及精度、嵌件位置形状以及推出方法、模具的制造、排气、操作工艺等多种因素的影响,因此在选择分型面时应综合分析比较,从几种方案中优选出较为合理的方案[13]。
选择分型面时一般应遵循以下几项原则:(1)分型面应选在塑件外形最大轮廓处,不要选在制品光亮平滑的外表面或带圆弧的转角处;(2)便于塑件顺利脱模,尽量使塑件开模时留在动模一边;(3)保证塑件的精度要求,保证制件相关部位的同心度;(4)满足塑件的外观质量要求;(5)便于模具加工制造;(6)考虑对成型面积的影响;(7)考虑对排气效果的影响;(8)考虑将抽芯或分型距离长的一边放在动、定模开模的方向上。
其中最重要的是第2、第5和第8点。
为了便于模具加工制造,应尽是选择平直分型面工易于加工的分型面。
如下图4.1所示,采用这样一个平直的分型面,由于制件的使用要求一般,精度要求不高,因此只设计一个分型面,即模具具有唯一分型面。
如图4-1所示图4.1分型面4.2模架的选择1、型腔壁厚的计算对小尺寸型腔,强度不足是主要问题,应按强度条件计算,得型腔侧壁最小厚度:(3.2)其中:r —凹模型腔内孔或凸型芯外圆的半径;p σ—材料许用应力;m P —模腔压力。
成型零件材料选T12,淬火,低温回火,硬度大于55HRC ,其pσ为700Mpamm t c 6643.3)11002700700(20≈-⨯-⨯=2、凹模型腔底部高度mm r P t pm h 97.14700361001.11.122≈⨯⨯==σ3、模架的选择由前面对型腔的最小壁厚和底部厚度可以估算得型腔的最小外形尺寸: 最小宽度为:20+3.6643=23.6643mm以还要考虑导柱导套的安放位置,且查得标准值,再由于塑件采取推件板推出,因此选择模架为基本类型中的A 3的派生模架,为了方便分型时定位,增加了限位杆。
设置推件板推出机构,它适合于薄壁壳体型塑件,脱模力大以及塑件表面不允最小厚度为:36+14.79=50.79mm但是考虑到加工方便,采用组合式凹模,所许留有顶出痕迹的注射成型模。
选择模架规格为:A 3-200200-33-Z 2,GB/T12556-90 具体尺寸如下如下: 定模坐板厚度:A=43mm 中间板厚度:B=24mm)12(--=mp p c P r t σσ模板:直径=150mm推板:直径=142.2mm ,高度=32mm 型心固定板:高度=48mm 动模座板:厚度=69mm 模具闭合厚度:H=517 导柱:d=20mm 导套:d 1=20mm 限位杆:d=20mm4.3型腔的内径计算[]z zx l s L s m δδ++∆-+=00)1( (4.1)其中:m L —型腔内形尺寸;s l —塑件外径基本尺寸;∆—塑件公差;s —塑件的平均收缩率,取0.4%; x —综合修正系数,取x=0.5~0.75;z δ—模具制造公差,取∆)6/1~3/1(。
因为制件图样上未注公差尺寸的允许偏差,所以采用7级公差精度,查表得72.0=∆,24.03=∆=z δ所以:24.00088.2272.04322)4.01(=⎥⎦⎤⎢⎣⎡⨯-⨯+=+z m L δ4.4型腔的深度尺寸计算()[]zS zm x H s H δδ++∆-+=001 (4.2)其中:m H —型腔深度尺寸;s H —塑件高度其本尺寸;∆—塑件公差;s —塑料平均收缩率,取0.4%; x —综合修正系数,取x=0.5~0.75;z δ—模具成型尺寸设计公差3/s m ∆=∆。
查表得8.0=∆,所以H=58mm4.5型芯的计算1、型芯的外径计算如图4-2所示为型芯结构图。
图4.2型芯的结构图()[]001zz x ls s l δδ--∆++= (4.3)式中:0zl δ-—型芯外形尺寸;s l —塑件内径基本尺寸;∆—塑件的公差;s —塑料平均收缩率0.4%; x —综合修正系数,取x=0.5~0.75;z δ—模具成型尺寸设计公差,取3/s m ∆=∆。
查表得:72.0=∆,024.00072.18--=z s l δ2、型芯的高度计算()[]01zz x h s h s m δδ--∆++= (4.4)式中:zm h δ-—凸模高度尺寸;s h —塑件内形深度基本尺寸;∆—塑件公差;s —塑料平均收缩率0.4%; x —综合修正系数,取x=0.5~0.75;z δ—模具成型尺寸设计公差,3/s m ∆=∆。
查表得:8.0=∆,所以0267.00144.36--=z m h δ4.6浇注系统的初步计算浇注系统一般由主流道、分流道、浇口和冷料穴等四部分组成[14]。
浇注系统的设计应保证塑件熔体的流动平稳、流程应尽量短、防止型芯变形、整修应方便、防止制品变形和翘曲、应与塑件材料品种相适用、冷料穴设计合理、尽量减少塑料的消耗。
根据塑件的形状采用推板推出。
由于本塑件是圆筒状制品所以尽可能采取中心进料,所以选择潜浇口,单分型面,分流道采用半圆形截面,分流道开设在定模板上,在浇道板上采用浇口套,设置冷料穴和拉料杆。
如图4-3所示图4.3浇注系统的结构根据塑件的外形尺寸和质量等决定影响因素,初步取值如下:d=5mm ,D=8mm ,R=16mm ,h=5mm ,d 1=0.2mm ,H 1=4mm ,l=50mm ,L=43mm ,a=2,a1=10,L 1=36mm ,Ra=0.63μm主流道呈圆角半径r=2mm ,以减小料流转向时渡时的阻力。
主流衬套选用45#制造,表面淬火大于55HRC 。
4.7导向机构的设计1、导柱导向机构的作用(1)定位件用:模具闭合后,保证动定模或上下模位置正确,保证型腔的形状和尺寸精确,在模具的装配过程中也起定位作用,便于装配和调整[15]。
(2)导向作用:合模时,首先是导向零件接触,引导动定模或上下模准确闭合,避免型芯先进入型腔造成成型零件损坏。
(3)承受一定的侧向压力。
2、导柱导套的选择一般在注射模中,动、定模之间的导柱既可设置在动模一侧,也可设置在定模一侧,视具体情况而定,通常设置在型芯凸出分型面最长的那一侧。
因为限位杆已经设置在定模上,所以导柱应该设置在动模上,而且这样还可以保护型心不受损伤。
如图4-4所示。
图4.4导柱导套的结构定端与模板间用H7/m6或H7/k6的过渡配合,导向部分通常采用H7/f7或H8/f7的间隙配合。
4.8推出机构的设计1、推出机构的组成推出机构由推出零件、推出零件固定板和推板、推出机构的导向与复位部件组成。
即推件板、推件板紧固螺钉、推板固定板、推杆垫板、顶板导柱、顶板导套以及推板紧固螺钉[16]。
第五章 注射机与模具型腔型芯强度校核1、注射机的校核 (1)最大注射量校核:由度件公利G G G K +≥得:7432.215.708.0+≥⨯,符合要求。
(2)注射压力的校核:由MpaP Mpa P 100150注公=>=,符合要求。
(3)注射速率的校核:由 注公V V ≥,可以用螺杆转速来校核min /200min /28min /14r r r ≤≤。
(4)锁模力的校核 由分注损锁A P K F ≥, (8.2)取k=1.1~1.2,得 MpaP 20=注即KN 57.3684.15231002.1150=⨯⨯≥,符合要求。
(5)模具闭合厚度校核: 由H min ≤H ≤H max ,得150≤291≤300 符合要求。