航空发动机典型静动密封关键技术及产业化
航空发动机用W型截面封严环新型成形工艺及有限元仿真

航空发动机用W型截面封严环新型成形工艺及有限元仿真王海波;桑贺【摘要】本文提出了一种新型 W型截面封严环成形工艺,即辊弯-弯圆-焊接成形工艺.将新工艺与传统工艺进行了对比,并在有限元软件 ABAQUS中建立了辊弯-弯圆成形有限元模型,通过对仿真结果进行成形机理分析探究金属板材在辊弯-弯圆成形过程中的变形行为.【期刊名称】《北方工业大学学报》【年(卷),期】2018(030)005【总页数】7页(P83-89)【关键词】W型截面封严环;辊弯成形;弯圆;有限元仿真;成形机理【作者】王海波;桑贺【作者单位】北方工业大学机械与材料工程学院,100144,北京;北方工业大学机械与材料工程学院,100144,北京【正文语种】中文【中图分类】TH1621 绪论1.1 国内外发展状况W型截面封严环是用于航空发动机上高速转动的密封环,是安装在两个法兰之间,用来保证在预定的使用寿命内两个法兰之间的密封性能的密封环.在国外,W型截面封严环核心加工技术只掌握在美国、加拿大等少数发达国家手中.国内尚未具备成熟、系统的设计分析和制造体系,应用于航空发动机上的封严环一直依赖进口.中航空天发动机研究院有限公司的朱宇和北京航空航天大学的万敏等人基于液压成形,提出动模外压成形方法,并建立了有限元模型,进行数值模拟和工艺试验,探讨了成形过程中环向失稳起皱等失效形式,提出了优化工艺参数.[1]南昌航空大学的陈希等利用有限元软件对其性能进行模拟分析,并计算了其在工作时的气体泄漏率,为设计封严环提供一定的理论依据及准则.[2]旋压或液压精密塑性成形是类似航空 W型截面封严环的“超薄、大变形、精密”环件加工的有效技术途径之一,也是值得深入研究发展的未来精密塑性成形技术的发展趋势.辊弯成形能保证零件质量、性能、使用要求[3],而且可以降低成本,提高零件的耐磨性及疲劳强度,具有成本低、效率高、可以生产复杂变截面产品等优点.[4]因此本文提出采用辊弯成形来制造此类薄壁复杂截面环件,开辟该类零件成形制造的另一种新方法.1.2 新型成形工艺简介W型截面封严环是航空发动机所用关键零件,在本文给出的新型W型截面封严环生产工艺中,其核心生产工艺为辊弯成形技术.辊弯成形是通过顺序配置的多道次成形轧辊,把金属板带不断地进行横向弯曲,以制成特定断面型材的工艺技术,是一种节材、节能、高效、先进适用的板金属成形工艺.[5-6]新型W型截面封严环生产工艺流程具体分为开卷、校直、辊弯、弯圆、焊接,工艺示意图如图1所示.金属板材经过校直之后进入辊弯生产线,得到直线形特定断面的零件.为获得符合形状的工艺产品,将直线形产品送入弯圆机.产品经过弯圆机成形之后变为端口未连接的环形件.最后将环形件的端口焊接在一起即可得到W型封严环.本文主要研究工艺为辊弯-弯圆连续成形工艺,未对焊接工艺进行探究.图1 工艺示意图2 新型W型截面封严环生产工艺有限元分析W型截面封严环的辊弯成形属于变截面辊弯成形,是大变形复杂非线性的成形过程.W型截面封严环材质为高温合金GH4169.在W型截面封严环成形过程中,轧辊自转,板料借助与轧辊之间的摩擦力的向前运动,发生形变.为了探究本文提出的新型W型截面封严环生产工艺中板材的变形行为,采用ABAQUS软件对该工艺进行有限元分析.本次仿真并未涉及焊接工艺.2.1 新工艺与传统工艺对比目前国内生产此类薄壁复杂截面密封环有两种工艺:一是中航空天发动机研究院有限公司的朱宇和北京航空航天大学的万敏等人基于液压成形,提出动模外压成形工艺[7],二是南昌航空大学提出的环形毛坯滚压成形工艺.[8]这两种工艺均能够生产符合要求的薄壁复杂截面密封环,技术发展较为成熟.新工艺核心技术为板材的辊弯成形,辊弯成形技术是一种节能、高效的金属成形工艺技术,节能意味着该成形工艺产生的能耗较低,高效意味着该工艺自动化程度较高,即由机械故障、能源失控以及人员操作失误所带来的风险程度较小.与传统工艺相比,本文提出的辊弯-弯圆成形工艺可以实现工件的连续性生产,在中航空天发动机研究院有限公司提出的动模外压成形工艺中,环形毛坯件需要置放于成形模具中,成形完毕后再取出,随后再置入新的毛坯件;南昌航空大学提出的滚压成形工艺需要将毛坯件在不同的成形道次间频繁取出、安置.相比较于这两种传统工艺,本文提出的新工艺能够将直线型板材连续、不间断地完成成形.工件成形完毕后,只需将板材切断,即可进行后续工件的成形.被切割的板材在完成焊接之后即为所需工件.新工艺大大提高了生产效率,节约了时间成本.2.2 新工艺成形过程变形与缺陷分析新型W型截面封严环在成形过程中,板材发生了较大的弹塑性变形.在板材的横截面成形为W型的过程中,板材的运动方向以及横截面方向都发生了较大的弹塑性变形,这两个方向上的变形均是通过轧辊对板材施加载荷实现的,轧辊形状的改变会导致载荷施加的大小、位置发生改变,从而使板材在成形方向与截面方向发生复杂的、不均匀的变形,经过一系列的道次,将板材成形为目标形状.在弯圆成形时,W型截面的板料是受压的过程,利用材料的特性和辅助轧辊完成弯圆的成形.在辊弯成形过程中,板材在出现能够预计到的横向弯曲、纵向弯曲的同时,还会产生出一些额外的、多余的变形.这些多余的变形会导致板料产生翘曲、扭曲、边波、减薄、破损、撕裂等现象,这种变形被称为冗余变形,冗余变形会影响零件成品的质量.在辊弯成形所应用的板材中,板材的的横向尺寸与纵向尺寸差距较大.在板材受到轧辊的载荷时,板材的纵向与横向产生的应变容易分布不均,从而引起翘曲及边波等现象.[9]边波经常出现在道次间切换时.边波的出现既响了产品的质量,也会引起材料堆积等情况影响生产线的正常运行.[10]在本工艺中,板材的辊弯成形与弯圆成形是连续进行的.由于目标零件的半径较大,以及高温合金钢优良的力学性能,板材弯圆成形中不会出现很大的弯曲变形量.[11] 2.3 有限元建模新型W型截面封严环的成形是复杂的、非线性大变形过程.板材选择高温合金GH4169.选择ABAQUS中的Explicit求解模块进行计算.对板材主要变形区域进行网格细化,通过有限元计算结果分析板材在成形过程的变形行为,探究其成形机理.2.3.1 高温合金钢力学性能及零件尺寸表1为GH4169材料性能参数.[12]目标零件及截面形状如图2所示,板材总长为176 mm,宽度为 16.6 mm,板材厚度 0.3 mm,板材厚度方向的变形对于分析板材整体的变形行为影响不大,所以板材选取壳单元建模.表1 GH4169的材料性能参数高温合金密度/(kg·m-3)弹性模量/MPa 泊松比屈服强度/MPa 抗拉强度/MPa GH4169 8 200 203 100 0.3 286.6 844.2 图2 封严环及其截面形状W型截面封严环成形的过程中,板材一共经历了15个成形道次,第一道次为熨平道次,第2~6道次成形带有翼缘的U型截面,第7~13的成形W型截面,在这个过程中先将其两侧翼缘成形,随后将缘折弯,成形最终目标形状,第14、15道次为弯圆道次.2.3.2 成形工艺三维建模将板材与轧辊在有限元软件ABAQUS中装配在一起.轧辊间距为20 mm,第14道次与第15道次轧辊间距为12 mm,成形过程中,上下轧辊自身旋转,依靠摩擦力带动板料向前运动,摩擦系数0.3,这种建模方式符合实际生产情况.[13]第1道次为过压状态,其轧辊间隙为0.29 mm,第2、3道次为无间隙状态,其间隙为0.3 mm,第4 道次至第13 道次其间隙为0.35 mm.[14]图3 为W型截面封严环辊弯-弯圆成形工艺的三维简化模型装配图.模型网格划分:根据冷弯成形技术手册并借助Autocad绘图软件设计W型封严环成形轧辊,导入到有限元仿真软件ABAQUS草图模块中.在部件模块中将草图导入,通过旋转体选项完成轧辊的建模.板料网格全部为四边形,网格单元类型为S4R.在整个成形过程中,板材的变形相对于中线完全对称,所以对板材划分1/2的网格.这种划分方式既不影响仿真结果精度,又大大节省了仿真计算时间.上下轧辊采用离散刚体处理,网格单元类型为R3D4部分圆弧较大区域,网格给予细化处理.[15]图4为网格划分示意图.图3 装配示意图4 网格示意图3 新工艺仿真结果分析3.1 弯圆工艺应力分析根据仿真结果,对 W型截面封严环辊弯-弯圆连续成形中弯圆成形部分进行应力分析.对弯圆折弯弯角处(B、C),边腿边(A)的应力值进行分析.提取3个节点A、B、C如图5所示.图5 节点示意提取A、B、C的3个方向的应力如图6~8所示,板料在成形过程中的变形非常复杂,其应力值变化较大,反向加载应力比较大.图6 A点成形应力图7 B点成形应力图8 C点成形应力3.2 应力应变场分析有限元模型计算完成后,得到了板料的应力应变云图.图9为等效应力云图,图10为等效塑性应变云图.通过观察两幅云图可以看到,板材的折弯区域等效塑性应变较大,出现了轻微的材料堆积现象,同时在折弯区域少量节点处出现应力集中现象,以上现象与轧辊与板料间隙有关.3.3 成形力分析图9 等效应力云图图10 等效塑性应变云图从W型截面封严环成形过程有限元模型的仿真计算结果中提取各个道次的轧辊成形力,由于第1道次为熨平道次,所以轧辊的成形力从第2道次开始提取,可以得出如下规律:第2道次和第3道次的轧辊成形力增加幅度不大,说明板料在该阶段变形程度不大,随着板料成形角度的增加,变形程度逐渐加剧,轧辊成形力逐渐增大;直到完成类似“U”形件时轧辊力开始下降,继续成形边腿成形时,轧辊成形力的变化趋势不大,进行完成“W”型截面成形时轧辊力迅速增大,达到轧辊成形力的最大值.3.4 封严环厚度减薄分析传统滚压式封严环生产工艺会导致封严环成品厚度减薄较为严重,影响产品使用.辊弯成形工艺中,板材主要发生横向弯曲,厚度方向变形较小,因此材料减薄情况较轻.在有限元仿真结果中选取26个节点作为典型截面,如图11所示.通过提取第一、第二主应变计算板材减薄率[16],进而求得板材成形之后的厚度.将成形厚度与原始厚度进行对比,如图12,发现在辊弯成形中,由于材料不断进行横向弯曲,材料流动较为明显,在第12~14节点处材料厚度发生较明显改变.图11 节点示意图图12 板材厚度对比3.5 成形全过程分析根据以上应力应变云图以及板材厚度变化,在图12中选取厚度减薄较为明显的3个单元节点(其减薄率分别为 26.4% 、26.7% 、26.1% ),分析节点在完整的成形过程中应力、应变变化.根据仿真结果提取3个节点的全程应力应变数据,发现在成形过程中其最大应力分别为837.7 MPa、829.9 MPa、829.1 MPa,均未超过材料的抗拉强度,说明板材在成形过程中未出现断裂情况.提取3个节点的等效塑性应变数据,发现在成形过程中最大等效塑性应变分别为 0.7,0.67,0.58.通过观察动态云图发现,3个节点应力值达到最大时,其处于第6道次.在本工艺中,板材在完成前6道次的变形后,板材截面已经由“一”型变成了带有翼缘的“U”型,3个节点处于翼缘的过渡区域,板材在变形中纵向高度变化较大,导致材料流动现象明显.通过仿真结果探究板材的变形行为:在前6个道次中,板材发生变形的主要区域为“U”型截面底部板材以及翼缘过渡区域板材,这两区域的材料流动较为剧烈,具体表现为“U”型截面底部板材加厚,翼缘过渡区域板材减薄.第7~9道次中,板材变形区域为翼缘部分,板材变形均匀.第10~12道次中,板材主要变形区域为翼缘过渡区域,该区域板材将进行折弯,将板材截面成形为“W”型.直线型板材的成形完毕后,板材进入弯圆道次中完成最后的成形,在弯圆道次中,主要变形区域为“W”型截面3处折弯区域,由于这3处区域在前12道次中同样进行了较大程度的材料变形,所以这3处区域的板材的等效塑性应变最大(见图10).通过对仿真结果的研究发现,虽然板材在完整的成形工艺过程中未发生断裂情况,但是在1~6道次中的“U”型截面底部板材以及翼缘过渡区域板材成形应力已经接近板料的抗拉极限,在将板材进行折弯时,翼缘部分受到轧辊的挤压也产生了较大的成形应力.总结这两处现象发现,在本工艺中,当板材在进行纵向落差较大的成形时,成形应力上升明显,接近材料的抗拉强度.为避免成形应力高于抗拉强度导致板材断裂,应增加相对应的成形道次,缓解由于板材纵向高度变化引起的成形应力的增加,使板材更加平稳地过渡到相邻道次,保证产品的质量.4 结语本文提出了一种新型W型截面封严环生产工艺,即辊弯-弯圆-焊接成型工艺.将新工艺与传统工艺对比后发现,本文所提出的新工艺是具有节能、高效、成本低等优点的金属成形工艺技术,有着不可忽视的发展潜力,为国内生产薄壁复杂截面密封环形件提供了新的思路.对新工艺的核心工艺——辊弯-弯圆连续成形进行了有限元模拟.通过对有限元仿真结果的分析可以验证新工艺的可行性,板材在整个成形过程中并未出现拉裂、破损等情况,证明了新工艺可以用于生产W型截面封严环.同时指出了新工艺的需要改进之处,并给出优化方案.有限元模型的仿真计算结果中,通过对 W型截面封严环辊弯-弯圆连续成形的等效应力云图、等效塑性应变云图、轧辊成形力的成形规律以及板材厚度变化等方面的研究,研究了板材的变形行为.在新工艺中,板材的变形较大的区域为“W”型截面折弯处,板材在辊弯成形工艺中纵向高度变化较大,成形应力明显上升,3处弯角处变形程度最大;板材在弯圆成形工艺中变形程度较为均匀,所以在完整的成形工艺中,“W”型截面折弯处变形最为剧烈.折弯处板材最大成形应力接近于板材的抗拉强度.为了避免出现材料拉裂、破损等情况,应相应地增加成形道次,以保证产品的质量.参考文献【相关文献】[1][7] 朱宇,万敏.航空发动机薄壁W形封严环动模外压成形 [J].航空学报,2015,36(7):2457-2467[2][8] 陈希.航空发动机用金属封严环设计与性能分析研究[D].南昌航空大学,2014:1-9[3] 张若青,李凯,景作军.单轴变截面冷弯成型系统设计[J].机械设计与制造,2011(11):44-46[4] 刘化民,赵振山.冷弯型钢在板材深加工中的应用[C].全国钢材深加工研讨会.2014:111-115[5] 林军.高效节能连续油管关键制造技术研究[D].济南:山东大学,2010:3-9[6] 刘冰,张若青.多通道信号采集与分析系统在冷弯机组中的应用[J].中国仪器仪表,2012(3):43-46[9] 陈静.基于有限元分析的变高度定模动辊辊弯成形工艺研究[D].北京:北方工业大学,2016:15-17[10] 刘建伟,史建鹏,石朝亮.轻量化技术在汽车上的应用分析[J].汽车科技,2012(6):10-14[11] 胡星星,裘乐淼,张树有,等.基于混合响应面法的滚压成型回弹角预测控制及应用[J].浙江大学学报,2013,47(11):2010-2019[12] 郭凯云.高温合金复杂截面圆环多道次滚压不均匀变形行为研究[D].江西:南昌航空大学,2015:23[13] 刘江林,杨晓明,文建峰.有限元在冷弯型钢中的应用[J].精密成形工程,2011,3(2):60-62[14] 付磊.用数值模拟的方法分析轧辊间距对冷弯成型的影响[J].四川理工学院学报,2011,24(2):224-227[15] 陈兰,张新洲,孙宇,等.大型船用卷板机卷板成形过程的数值模拟[J].锻压技术,2011,36(5):76-80[16] Wang Haibo,Yan Yu,Han Fei,et al.Experimental and theoretical investigations of the forming limit of 5754O aluminum alloy sheet under different combined loading paths[J].International Journal of Mechanical Sciences,2017:133。
航空发动机产业政策
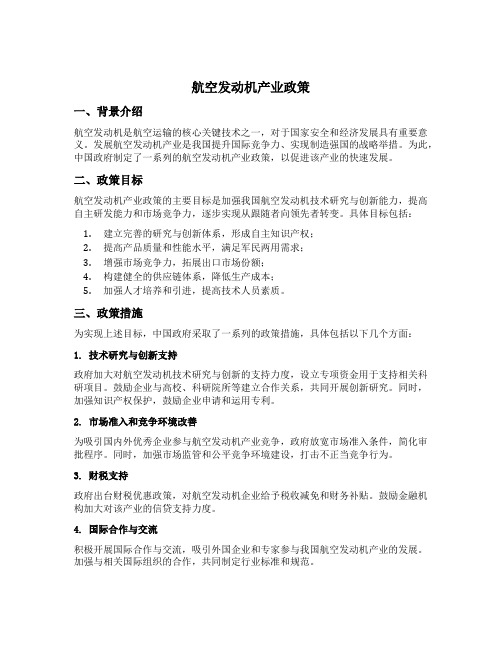
航空发动机产业政策一、背景介绍航空发动机是航空运输的核心关键技术之一,对于国家安全和经济发展具有重要意义。
发展航空发动机产业是我国提升国际竞争力、实现制造强国的战略举措。
为此,中国政府制定了一系列的航空发动机产业政策,以促进该产业的快速发展。
二、政策目标航空发动机产业政策的主要目标是加强我国航空发动机技术研究与创新能力,提高自主研发能力和市场竞争力,逐步实现从跟随者向领先者转变。
具体目标包括:1.建立完善的研究与创新体系,形成自主知识产权;2.提高产品质量和性能水平,满足军民两用需求;3.增强市场竞争力,拓展出口市场份额;4.构建健全的供应链体系,降低生产成本;5.加强人才培养和引进,提高技术人员素质。
三、政策措施为实现上述目标,中国政府采取了一系列的政策措施,具体包括以下几个方面:1. 技术研究与创新支持政府加大对航空发动机技术研究与创新的支持力度,设立专项资金用于支持相关科研项目。
鼓励企业与高校、科研院所等建立合作关系,共同开展创新研究。
同时,加强知识产权保护,鼓励企业申请和运用专利。
2. 市场准入和竞争环境改善为吸引国内外优秀企业参与航空发动机产业竞争,政府放宽市场准入条件,简化审批程序。
同时,加强市场监管和公平竞争环境建设,打击不正当竞争行为。
3. 财税支持政府出台财税优惠政策,对航空发动机企业给予税收减免和财务补贴。
鼓励金融机构加大对该产业的信贷支持力度。
4. 国际合作与交流积极开展国际合作与交流,吸引外国企业和专家参与我国航空发动机产业的发展。
加强与相关国际组织的合作,共同制定行业标准和规范。
5. 人才培养与引进加大人才培养和引进力度,设立专门的人才项目,吸引优秀科研人员和工程师参与航空发动机产业。
鼓励高校开设相关专业课程,并提供奖学金和实习机会。
四、政策效果自实施航空发动机产业政策以来,我国航空发动机产业取得了显著成就。
具体表现在以下几个方面:1.技术水平大幅提升:我国航空发动机技术水平实现了重大突破,多款自主研发的发动机已经进入市场应用阶段。
航空发动机空气密封技术的研究与应用

航空发动机空气密封技术的研究与应用航空发动机在飞行中需要不断地吸取大量的空气以维持燃烧,同时也需要将排放的废气排至大气之中。
为了保证发动机的高效性和燃烧效率,航空工程师们不断地探索着新的方法,其中空气密封技术就是其中之一。
本文将重点探讨航空发动机空气密封技术的研究与应用。
一、空气密封技术的意义和作用航空发动机需要吸取大量的空气以维持燃烧,但也需要保证发动机内的空气流动畅通,这也就意味着,在发动机运转时,必须保证发动机内部和外部的密闭性,否则就会导致气流的泄漏,降低了发动机的效率和功率。
空气密封技术就是解决这个问题的方法。
简单来说,空气密封技术就是一种在发动机和外部环境之间创造一个密闭的接触面,能够减少气流泄漏,从而提高发动机的效率和功率。
二、空气密封技术的分类空气密封技术主要分为动密封和静密封两种类型。
动密封主要是通过发动机内部转轴上的旋转部件对气体进行密封,例如采用机械密封、弹簧密封等技术,在旋转部件转动的过程中,通过旋转部件与密封件或轴承之间的摩擦进行密封。
静密封则主要采用非旋转部件,通过气体静力和摩擦力来进行密封。
比如采用O型环、拟合密封等技术进行气密封,这些密封件主要采用高弹性材料制成,当气体进入密封件时,它们可以随着密封面改变而产生变形,从而形成密封。
三、航空发动机空气密封技术的发展航空发动机空气密封技术在过去几十年中已经不断地得到发展和应用。
早在20世纪50年代,人们就开始应用空气密封技术,当时主要采用的是静密封技术,其原理就是在发动机的外部和内部之间添加一层隔热材料,从而降低进入发动机的空气温度,从而提高燃烧效率。
随着科技和理论的发展,人们开始探索动密封技术的应用,并不断地进行改进和发展。
现在,航空工程师们可以采用一系列密封件来保证气密性,如机械密封、液体密封,甚至是精密空气流控制系统等。
四、空气密封技术的应用航空发动机空气密封技术的应用范围非常广泛,在大型民用飞机、军用飞机和民用运输机等各种航空器中,都需要应用到空气密封技术。
parkercq密封技术手册
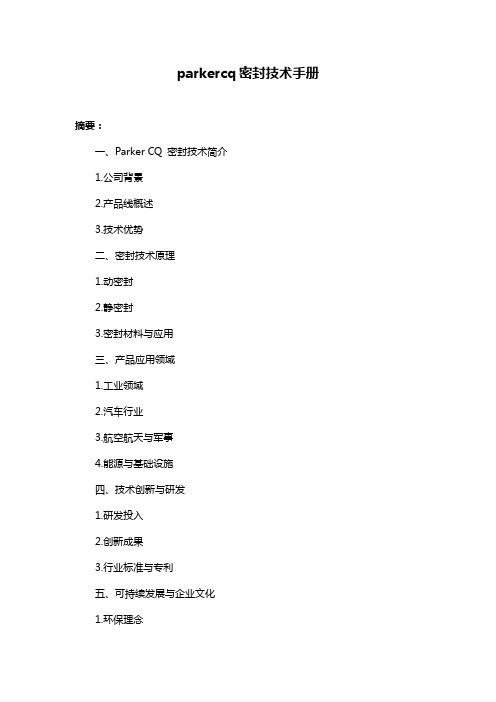
parkercq密封技术手册摘要:一、Parker CQ 密封技术简介1.公司背景2.产品线概述3.技术优势二、密封技术原理1.动密封2.静密封3.密封材料与应用三、产品应用领域1.工业领域2.汽车行业3.航空航天与军事4.能源与基础设施四、技术创新与研发1.研发投入2.创新成果3.行业标准与专利五、可持续发展与企业文化1.环保理念2.社会责任3.员工培养与团队建设六、中国市场与合作伙伴1.我国市场需求2.合作伙伴介绍3.发展前景展望正文:一、Parker CQ 密封技术简介1.公司背景Parker CQ 是一家全球领先的密封技术制造商,致力于为客户提供高性能、可靠的密封产品。
成立于1990年,公司凭借不断创新和精湛工艺,已成为行业佼佼者。
2.产品线概述Parker CQ 密封技术涵盖各类动密封、静密封产品,包括O型圈、填料、油封、密封圈等。
产品广泛应用于工业、汽车、航空航天、军事、能源等领域。
3.技术优势Parker CQ 密封技术具备以下优势:(1)高品质材料:采用高性能、耐磨损、抗老化材料,提高产品使用寿命。
(2)精湛工艺:严格控制生产工艺,确保产品尺寸和性能的一致性。
(3)技术创新:不断研发新型密封材料和结构,满足客户多样化需求。
二、密封技术原理1.动密封动密封主要用于旋转轴,如油封、填料等。
通过摩擦副的设计,实现轴与密封件之间的密封,防止润滑油泄漏。
2.静密封静密封主要用于静态接缝,如O型圈、密封胶等。
通过材料弹性和变形,实现接缝的密封。
3.密封材料与应用Parker CQ 提供多种密封材料,如氟橡胶、硅胶、聚氨酯等。
不同材料具有不同性能,可根据应用场景选择合适的产品。
三、产品应用领域1.工业领域:密封技术在化工、冶金、水处理等行业中发挥着重要作用。
2.汽车行业:密封件应用于发动机、变速器、刹车系统等关键部件,确保汽车安全可靠。
3.航空航天与军事:为飞行器、导弹、舰船等提供高性能密封产品。
机械设计中的密封技术与应用
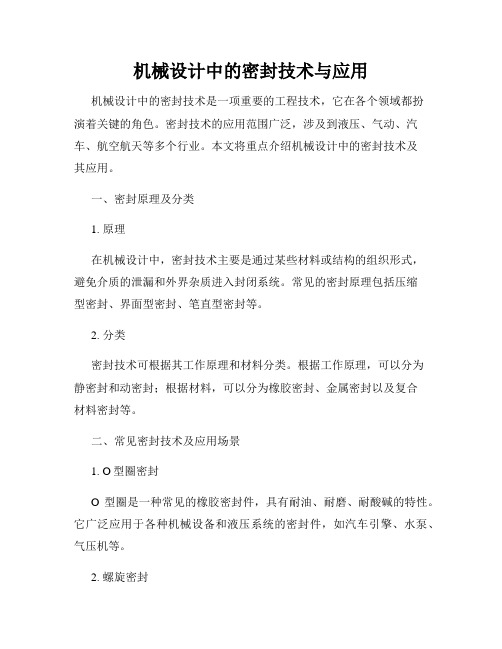
机械设计中的密封技术与应用机械设计中的密封技术是一项重要的工程技术,它在各个领域都扮演着关键的角色。
密封技术的应用范围广泛,涉及到液压、气动、汽车、航空航天等多个行业。
本文将重点介绍机械设计中的密封技术及其应用。
一、密封原理及分类1. 原理在机械设计中,密封技术主要是通过某些材料或结构的组织形式,避免介质的泄漏和外界杂质进入封闭系统。
常见的密封原理包括压缩型密封、界面型密封、笔直型密封等。
2. 分类密封技术可根据其工作原理和材料分类。
根据工作原理,可以分为静密封和动密封;根据材料,可以分为橡胶密封、金属密封以及复合材料密封等。
二、常见密封技术及应用场景1. O型圈密封O型圈是一种常见的橡胶密封件,具有耐油、耐磨、耐酸碱的特性。
它广泛应用于各种机械设备和液压系统的密封件,如汽车引擎、水泵、气压机等。
2. 螺旋密封螺旋密封是一种界面型密封,由螺旋形金属或非金属材料制成。
它具有良好的密封性能和耐腐蚀性,广泛应用于化工设备、煤气轮机等高温高压场合。
3. 气密封气密封是一种特殊的动密封技术,用于控制气体的漏失。
它主要应用于航空航天领域,如航空发动机的气密封和航天器的舱门密封等。
4. 液体密封液体密封是通过液体介质形成的密封,常见的应用场景包括输油管道、水力发电站等液体工程设备。
三、密封技术的优化与发展为了提高密封技术的可靠性和密封效果,研究人员不断进行技术优化和创新。
目前,一些新型材料的应用在密封技术领域呈现出良好的前景。
1. 纳米材料纳米材料具有独特的物理和化学特性,能提高密封件的力学性能和耐化学侵蚀性能。
因此,在密封技术领域,纳米材料被广泛应用于新型密封件的研发。
2. 润滑材料润滑材料的应用可以减少摩擦和磨损,提高密封件的使用寿命。
研究人员不断寻求新型的润滑材料来满足工程需求。
3. 三维打印技术三维打印技术的发展为密封件的设计和制造提供了新的途径。
通过三维打印技术,可以实现复杂结构密封件的快速制造,提高生产效率。
高压动密封
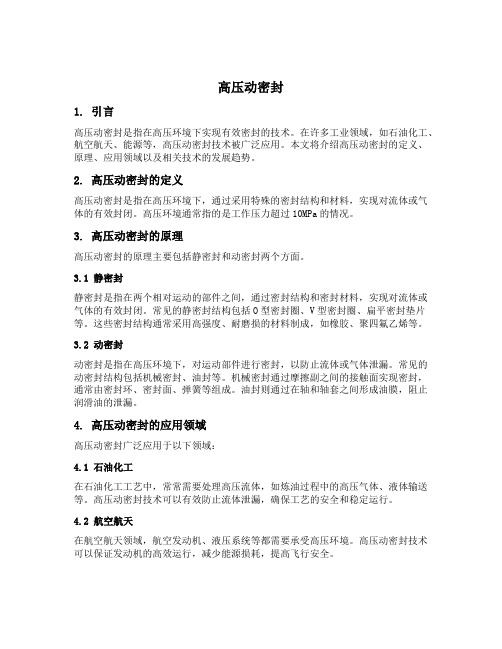
高压动密封1. 引言高压动密封是指在高压环境下实现有效密封的技术。
在许多工业领域,如石油化工、航空航天、能源等,高压动密封技术被广泛应用。
本文将介绍高压动密封的定义、原理、应用领域以及相关技术的发展趋势。
2. 高压动密封的定义高压动密封是指在高压环境下,通过采用特殊的密封结构和材料,实现对流体或气体的有效封闭。
高压环境通常指的是工作压力超过10MPa的情况。
3. 高压动密封的原理高压动密封的原理主要包括静密封和动密封两个方面。
3.1 静密封静密封是指在两个相对运动的部件之间,通过密封结构和密封材料,实现对流体或气体的有效封闭。
常见的静密封结构包括O型密封圈、V型密封圈、扁平密封垫片等。
这些密封结构通常采用高强度、耐磨损的材料制成,如橡胶、聚四氟乙烯等。
3.2 动密封动密封是指在高压环境下,对运动部件进行密封,以防止流体或气体泄漏。
常见的动密封结构包括机械密封、油封等。
机械密封通过摩擦副之间的接触面实现密封,通常由密封环、密封面、弹簧等组成。
油封则通过在轴和轴套之间形成油膜,阻止润滑油的泄漏。
4. 高压动密封的应用领域高压动密封广泛应用于以下领域:4.1 石油化工在石油化工工艺中,常常需要处理高压流体,如炼油过程中的高压气体、液体输送等。
高压动密封技术可以有效防止流体泄漏,确保工艺的安全和稳定运行。
4.2 航空航天在航空航天领域,航空发动机、液压系统等都需要承受高压环境。
高压动密封技术可以保证发动机的高效运行,减少能源损耗,提高飞行安全。
4.3 能源在能源生产和输送过程中,常常需要处理高压气体或液体。
高压动密封技术可以保证能源设备的正常运行,提高能源利用效率。
5. 高压动密封技术的发展趋势随着科技的进步和工业的发展,高压动密封技术也在不断创新和改进。
以下是高压动密封技术的发展趋势:5.1 材料的改进随着材料科学的发展,新型的高强度、耐磨损材料不断涌现。
这些材料具有更好的密封性能和耐高压性能,可以满足更严苛的工作环境要求。
发动机封严技术浅析

发动机封严技术浅析孙勇中国航空发动机集团有限公司,北京 100097摘要:高性能且可靠的封严技术一直是航空发动机研发的重点。
先进的封严技术可满足人们对发动机推力、油耗的不断追求。
通过采取先进的、适合使用环境的封严技术,可以大大降低发动机的内流系统的泄漏量,从而提高发动机的性能和效率。
本文针对航空发动机的几种典型封严技术,详细地介绍了在发动机中常用的石墨封严、篦齿封严、刷式封严等密封技术,对它们的特征和优缺点进行描述。
对目前广泛应用的刷式封严提出了改进意见。
关键词:航空发动机;燃气轮机;封严装置中图分类号:TK05 文献标识码:A经过几十年的迅速发展,航空发动机及在其基础上衍生的舰船用和地面用燃气轮机技术已经达到了较高的水平。
随着人们对军用航空发动机高推重比和民用发动机低耗油率的不断追求,发动机的压比和温度都不断升高,这对整机效率的要求越来越高。
材料和加工工艺与工业基础有很大关系,在目前的材料和加工工艺无法满足航空发动机的需求时,已经无法大幅度提高燃烧室出口温度这一影响功率的关键参数。
发动机自身的消耗越来越引起人们的关注,内部空气系统的消耗尤其重要。
经过多种型号数百台发动机的运行数据表明,仅仅把发动机内部关键部位的泄漏量减少一半,就可以使推力增大1~3%,耗油率降低3~5%。
因此各大航空发动机及改型燃气轮机厂商都在深入研究如何减少发动机内部空气系统的损失,以提高发动机性能。
对于军用发动机来说,可以有效提高推重比,提升3%的推重比对于军用发动机来说具有里程碑式的意义。
对于民用发动机来说可以较大幅度的提升效率,减少油耗,有效增加航程。
发动机的封严装置本身就会随着运行时数的增加而磨损,选择适当的封严结构同时可以增加发动机的寿命。
1 封严对发动机的影响封严技术是指对发动机中的转动部件和静子部件间的泄漏进行控制,并不是完全限制其流动。
广义的封严也包括对转子叶尖和机匣的间隙,即叶尖间隙控制,但这部分内容在发动机领域有单独的专业进行深入研究,在本文中不包含这部分内容。
当代胶粘技术在航空发动机领域的应用与创新
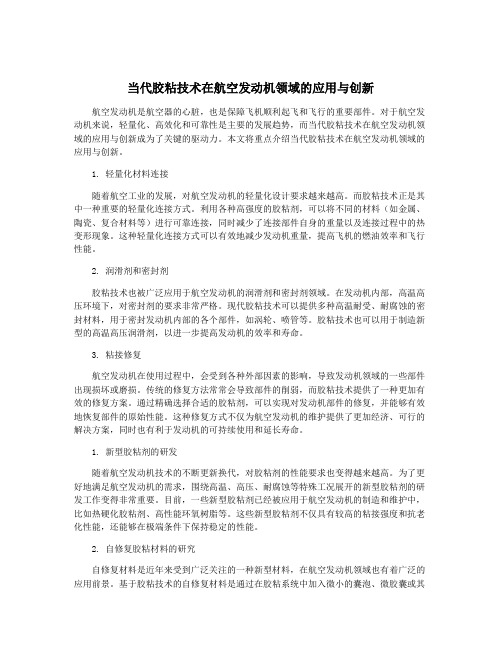
当代胶粘技术在航空发动机领域的应用与创新航空发动机是航空器的心脏,也是保障飞机顺利起飞和飞行的重要部件。
对于航空发动机来说,轻量化、高效化和可靠性是主要的发展趋势,而当代胶粘技术在航空发动机领域的应用与创新成为了关键的驱动力。
本文将重点介绍当代胶粘技术在航空发动机领域的应用与创新。
1. 轻量化材料连接随着航空工业的发展,对航空发动机的轻量化设计要求越来越高。
而胶粘技术正是其中一种重要的轻量化连接方式。
利用各种高强度的胶粘剂,可以将不同的材料(如金属、陶瓷、复合材料等)进行可靠连接,同时减少了连接部件自身的重量以及连接过程中的热变形现象。
这种轻量化连接方式可以有效地减少发动机重量,提高飞机的燃油效率和飞行性能。
2. 润滑剂和密封剂胶粘技术也被广泛应用于航空发动机的润滑剂和密封剂领域。
在发动机内部,高温高压环境下,对密封剂的要求非常严格。
现代胶粘技术可以提供多种高温耐受、耐腐蚀的密封材料,用于密封发动机内部的各个部件,如涡轮、喷管等。
胶粘技术也可以用于制造新型的高温高压润滑剂,以进一步提高发动机的效率和寿命。
3. 粘接修复航空发动机在使用过程中,会受到各种外部因素的影响,导致发动机领域的一些部件出现损坏或磨损。
传统的修复方法常常会导致部件的削弱,而胶粘技术提供了一种更加有效的修复方案。
通过精确选择合适的胶粘剂,可以实现对发动机部件的修复,并能够有效地恢复部件的原始性能。
这种修复方式不仅为航空发动机的维护提供了更加经济、可行的解决方案,同时也有利于发动机的可持续使用和延长寿命。
1. 新型胶粘剂的研发随着航空发动机技术的不断更新换代,对胶粘剂的性能要求也变得越来越高。
为了更好地满足航空发动机的需求,围绕高温、高压、耐腐蚀等特殊工况展开的新型胶粘剂的研发工作变得非常重要。
目前,一些新型胶粘剂已经被应用于航空发动机的制造和维护中,比如热硬化胶粘剂、高性能环氧树脂等。
这些新型胶粘剂不仅具有较高的粘接强度和抗老化性能,还能够在极端条件下保持稳定的性能。
- 1、下载文档前请自行甄别文档内容的完整性,平台不提供额外的编辑、内容补充、找答案等附加服务。
- 2、"仅部分预览"的文档,不可在线预览部分如存在完整性等问题,可反馈申请退款(可完整预览的文档不适用该条件!)。
- 3、如文档侵犯您的权益,请联系客服反馈,我们会尽快为您处理(人工客服工作时间:9:00-18:30)。
航空发动机典型静动密封关键技术及产业化
一、引言
航空发动机是飞机的“心脏”,发动机的性能直接关系到飞机的安全性、经济性和环保性。
发动机的密封技术是影响其性能的重要因素之一,特别是静动密封技术在发动机中起着至关重要的作用。
本文将从
航空发动机典型静动密封关键技术及产业化这一主题出发,对发动机
密封技术进行全面评估,探讨其深度和广度,以期更全面地理解这一
重要的技术领域。
二、航空发动机静动密封技术的重要性
静动密封技术是指在发动机内部隔离高压气体和低压气体,使其不相
互混合,以及在发动机外部阻止润滑油和冷却剂外泄的技术。
在航空
发动机中,由于工作环境的特殊性,静动密封技术的重要性愈发凸显。
密封不严会导致气体泄露,影响发动机的性能和效率;另密封不合格
会导致润滑油和冷却剂外泄,对环境和安全构成威胁。
航空发动机静
动密封技术的重要性不言而喻。
三、航空发动机静动密封关键技术
1. 材料技术
航空发动机内部和外部的密封件要求具有良好的耐高温、耐腐蚀、耐磨损等特性,因此材料技术是静动密封技术的关键之一。
高温合金、特种陶瓷、聚合物材料等在航空发动机密封件中的应用,将对密封技术起到积极推动作用。
2. 结构设计技术
发动机内部的结构设计对于静动密封技术至关重要,合理的结构设计可以减少气体泄露的可能性,提高发动机的效率和性能。
在密封环、密封垫、密封腔等方面的结构设计技术将成为发展的重点。
3. 加工工艺技术
精密的加工工艺是保证静动密封件性能的重要保障。
高精度的加工技术可以提高密封件的密封性能和寿命,减少气体泄露和润滑油外泄的可能性。
4. 润滑和冷却技术
润滑和冷却技术对于静动密封技术同样至关重要。
密封件在长期高温高速运转下,容易出现磨损和老化,因此润滑和冷却技术的改进将极大地提高密封件的使用寿命。
四、航空发动机静动密封技术的产业化现状
目前,航空发动机静动密封技术的产业化水平不断提高,国际航空发
动机制造商在这一领域进行了大量的研发和应用。
我国航空发动机制
造商也在积极跟进,加大对静动密封技术的研究和产业化推进力度。
具体表现在材料技术、结构设计技术、加工工艺技术和润滑、冷却技
术的进步,为航空发动机静动密封技术的产业化奠定了基础。
五、对航空发动机静动密封技术的个人观点和理解
航空发动机静动密封技术的发展是航空发动机技术发展的重要方向之一,其在提高发动机性能、延长使用寿命、减少维护成本等方面具有
重要意义。
而在产业化方面,我认为国内航空发动机制造商应该加大
技术研发力度,提高自主研发的水平,以实现对静动密封技术的自主
掌控和应用。
航空发动机典型静动密封关键技术及产业化是一个值得深入研究和探
讨的领域,其发展将对航空工业的发展产生深远影响。
我希望通过这
篇文章,更深入地了解航空发动机静动密封技术,并将其应用于实际
生产中。
总结
文章中对航空发动机典型静动密封关键技术及产业化进行了全面评估,探讨了其深度和广度,而且多次提到了指定的主题文字。
文章指出航
空发动机静动密封技术在航空发动机中起着至关重要的作用,对其重
要性进行了明确的阐述。
介绍了航空发动机静动密封关键技术的重要
技术领域,并对产业化现状进行了简要分析。
文章共享了对航空发动
机静动密封技术的个人观点和理解,并提出了在产业化方面的建议。
整体而言,本文符合要求,全面、深入、灵活地探讨了相关主题。
航
空发动机典型静动密封关键技术及产业化的发展与应用
六、航空发动机静动密封技术的发展趋势
随着航空工业的快速发展,航空发动机的要求也越来越高。
在这样的
背景下,航空发动机静动密封技术也在不断发展。
未来,航空发动机
静动密封技术的发展趋势主要是以下几个方面:
1. 高温材料的应用
随着发动机工作温度的提高,对密封件材料的要求也越来越高。
未来,高温合金、陶瓷等高温材料的应用将得到进一步扩大,并且将会有更
多新材料的涌现,以满足未来发动机的需求。
2. 高性能密封结构设计
未来航空发动机的密封结构设计将更加注重性能的提升。
通过设计更
合理的密封结构,可以进一步减少气体泄露和润滑油外泄的可能性,
提高发动机的效率和性能。
3. 数字化制造技术的应用
随着数字化制造技术的发展,未来航空发动机的密封件制造将更加精
密化和个性化。
数字化制造技术可以实现对密封件的精确加工,提高
制造效率和降低成本。
4. 绿色环保技术的应用
未来航空发动机的密封技术将更加注重环保性能。
绿色环保技术的应
用将有助于减少对环境的影响,提高密封件的安全性和可靠性。
七、航空发动机静动密封技术的产业化推进
为了加快航空发动机静动密封技术的产业化进程,需要从以下几个方
面进行推进:
1. 加大研发投入
航空发动机制造商和科研机构应加大对静动密封技术研发的投入,不
断开拓新的材料、结构、加工工艺和润滑、冷却技术,提高技术水平。
2. 加强产学研合作
产业界、学术界和研究机构应加强合作,充分发挥各自优势,共同推
进航空发动机静动密封技术的产业化进程。
3. 推动标准化建设
制定统一的技术标准,加强对静动密封技术的认证和监管,推动产业
规范化和标准化发展。
4. 加强人才培养
加强对静动密封技术人才的培养和引进,培养一批高水平的技术人才,推动产业化进程。
五、结语
航空发动机静动密封技术的发展与应用是一个复杂而重要的领域,对
于航空工业的发展具有重要意义。
本文从航空发动机典型静动密封关
键技术及产业化的角度对这一领域进行了全面的评估和探讨,并对其
发展趋势和产业化推进进行了展望。
希望本文能够对相关领域的研究
和实践有所启发,推动航空发动机静动密封技术的健康发展和应用。