铸造设备及其自动化-3
铸造及铸件检验培训资料三

• 4) 另外,高熔点合金压铸时,铸型寿命低,影响压铸生产的扩大应 用。
• 综上所述,压力铸造适用于有色合金,小型、薄壁、复杂铸件的生 产,考虑到压铸其它技术上的优点,铸件需要量为2000-3000件时, 即可考虑采用压铸。
压铸的特点
• 1. 压铸定义及特点 • 压力铸造〔简称压铸〕是在压铸机的压室内
• 1 普通砂型铸造,利用砂作为铸模材料,又 称砂铸,翻砂,包括湿砂型、干砂型和化学 硬化砂型3类,但并非所有砂均可用以铸造。 好处是本钱较低,因为铸模所使用的沙可重 复使用;缺点是铸模制作耗时,铸模本身不能 被重复使用,须破坏后才能取得成品。
• 1.1 砂型铸造方法:湿型砂机器造型方法、、 水玻璃砂造型制芯、干型和表干型、实型铸 造、负压造型、手工造型。
.砂型铸造的特征及工艺流程
• 配制型砂—造型 合型—浇注—冷却—落 • 配制芯砂—制芯—烘干 • 金属材料熔化 • 砂—清理—检查—热处理—检验—获得铸件
• 特征:使用型砂构成铸型并进行浇注的方 法,通常指在重力作用下的砂型铸造过程。
型砂
• 1、型砂类型: • 〔1〕机械粘结剂型芯----以粘土为粘结剂的粘土型芯
• 压力铸造是指金属液在其他外力〔不含重力〕 的作用下注入铸型的工艺。广义的压力铸造 包括压铸机的压力铸造和真空铸造、低压铸 造、离心铸造等;窄义的压力铸造专指压铸 机的金属型压力铸造,简称压铸。这几种铸 造工艺是目前有色金属铸造中最常用的、也 是相对价格最低的。
• 特种铸造,按造型材料又可分为以 天然矿产砂石为主要造型材料的特 种铸造〔如熔模铸造、泥型铸造、 壳型铸造、负压铸造、实型铸造、 陶瓷型铸造,消失模铸造等〕和以 金属为主要铸型材料的特种铸造〔 如金属型铸造、压力铸造、连续铸 造、低压铸造、离心铸造等〕两类 。
铸造机械设备生产过程自动化控制技术研究
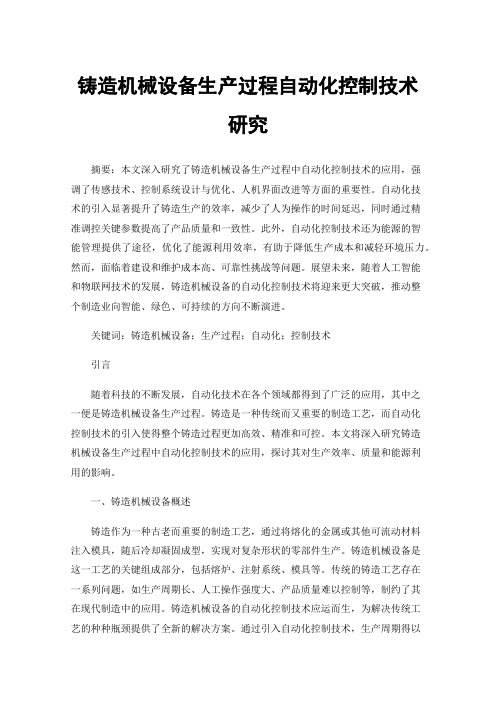
铸造机械设备生产过程自动化控制技术研究摘要:本文深入研究了铸造机械设备生产过程中自动化控制技术的应用,强调了传感技术、控制系统设计与优化、人机界面改进等方面的重要性。
自动化技术的引入显著提升了铸造生产的效率,减少了人为操作的时间延迟,同时通过精准调控关键参数提高了产品质量和一致性。
此外,自动化控制技术还为能源的智能管理提供了途径,优化了能源利用效率,有助于降低生产成本和减轻环境压力。
然而,面临着建设和维护成本高、可靠性挑战等问题。
展望未来,随着人工智能和物联网技术的发展,铸造机械设备的自动化控制技术将迎来更大突破,推动整个制造业向智能、绿色、可持续的方向不断演进。
关键词:铸造机械设备;生产过程;自动化;控制技术引言随着科技的不断发展,自动化技术在各个领域都得到了广泛的应用,其中之一便是铸造机械设备生产过程。
铸造是一种传统而又重要的制造工艺,而自动化控制技术的引入使得整个铸造过程更加高效、精准和可控。
本文将深入研究铸造机械设备生产过程中自动化控制技术的应用,探讨其对生产效率、质量和能源利用的影响。
一、铸造机械设备概述铸造作为一种古老而重要的制造工艺,通过将熔化的金属或其他可流动材料注入模具,随后冷却凝固成型,实现对复杂形状的零部件生产。
铸造机械设备是这一工艺的关键组成部分,包括熔炉、注射系统、模具等。
传统的铸造工艺存在一系列问题,如生产周期长、人工操作强度大、产品质量难以控制等,制约了其在现代制造中的应用。
铸造机械设备的自动化控制技术应运而生,为解决传统工艺的种种瓶颈提供了全新的解决方案。
通过引入自动化控制技术,生产周期得以大幅缩短,因为系统能够更迅速、准确地执行各个生产环节。
同时,自动化控制技术有效降低了人工操作的强度,从而提高了生产线的安全性和稳定性。
其中,注射系统、熔炉和模具等关键部件得到了智能化的升级。
例如,在熔炉控制中,自动化系统通过温度传感器实时监测熔炉内部温度,精准控制金属的熔化状态,提高了熔炉的能效。
铸造工艺及设备
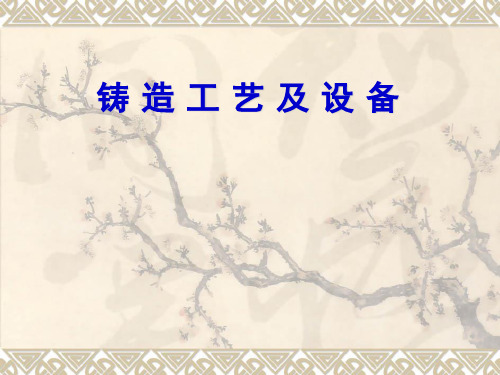
二、我国铸造技术的发展 铸造是世界历史上最悠久的工艺技术之一。
我国古代铸造技术居世界先进行列。
14 12 10 8 6 4 2 0 1995年 1996年 1997年 1998年 日本 中国 美国 德国
我国铸件年产量与美、日、德三国的对比
我国各行业用户消耗铸件的数量
铸 件 用 户
汽车 铁道和铁道车辆 拖拉机、柴油机、农业机械 机床 通用机械 冶金矿山机械 能源设备 纺织机械 铸铁管和管件 建筑工程及其配件 其它 合计
(单位:t)
1995年
1178000 714000 1940000 687000 426000 2026000 374000 200000 1836000 459000 1492000 11332000
1996年
1190000 700200 1901300 664000 407000 2005000 358000 123900 1674000 445000 1434785 10903185
一、铸造生产的工艺过程、特点及在制造业中的地位
铸造生产的工艺流程
铸造生产基本上由铸型制备、合金熔炼及浇注、落砂及清理等三个造方法的分类
湿型铸造 砂型铸造 干型铸造 表干型铸造 铸 造 熔模铸造 金属型铸造 特种铸造 离心铸造 压力铸造 有色合金铸造 铸钢铸造
第一章 本章概要:
造型材料
1.砂型铸造中所用原材料的成分和性质;
2.常用型(芯)砂的组成、配制工艺及性能控制; 3.相应的性能检测方法。 基本概念: 造型材料——凡用来制作铸型的原材料以及由各种原材
料所混制成的混合物统称为造型材料。
芯砂——制作砂型的混合物称为型砂,制作砂芯的混合 物称为芯砂。
涂料——涂敷在型腔或砂芯表面的混合物称为涂料。
大学本科-机械设计及其自动化专业-《机械制造基础》课后练习题(有答案和解析)

大学本科-机械设计及其自动化专业-《机械制造基础》课后练习题(有答案和解析)1.(单选题)下面的叙述正确的是( )。
A顺序凝固有利于防止铸造应力的产生B同时凝固有利于防止缩孔的产生C铸造时浇注温度越高越好D铸件的结构斜度应设置在非加工表面正确答案:D题目解析:铸件的结构斜度应设置在非加工表面,这是为了便于从模具中取出铸件,同时避免在加工表面上留下不必要的痕迹。
选项A错误,因为顺序凝固并不能完全防止铸造应力的产生;选项B错误,因为同时凝固容易导致缩孔的产生;选项C错误,因为浇注温度过高会导致铸件产生缺陷。
2.(单选题)钢套镶铜轴承是一个双金属结构件,能够方便的铸造出该件的铸造方法是( )。
A金属型重力铸造B熔模铸造C离心铸造D低压铸造正确答案:C题目解析:离心铸造是一种利用离心力将液态金属浇入旋转的铸型中,使金属液在离心力的作用下贴紧铸型壁,从而获得各种形状的中空回转体铸件的铸造方法。
钢套镶铜轴承是一个双金属结构件,内层为钢套,外层为铜套,可以采用离心铸造的方法将两种金属材料结合在一起。
因此,答案为C。
3.(单选题)下面属于压焊的是( )。
A电渣焊B缝焊C氩弧焊D埋弧焊正确答案:B题目解析:缝焊是一种压焊方法,它使用旋转的滚轮电极对搭接的工件施加压力并进行焊接。
在焊接过程中,滚轮电极与工件接触部位产生电阻热,加上滚轮电极的挤压作用,形成连续的焊缝。
因此,正确的选项是B。
4.(单选题)在低碳钢焊接接头的热影响区中,力学性能最好的区域是( )。
A熔合区B正火区C部分相变区D过热区正确答案:B题目解析:在低碳钢焊接接头的热影响区中,正火区的力学性能最好。
正火区是焊接时焊缝两侧的金属正处于相变重结晶温度范围内,冷却后得到均匀细小的铁素体和珠光体组织,其力学性能优于母材。
相比之下,熔合区的化学成分和组织性能极不均匀,力学性能较差;部分相变区的组织不均匀,力学性能也不好;过热区的晶粒粗大,力学性能也较差。
因此,答案为B。
第六章 落砂清理及环保设备
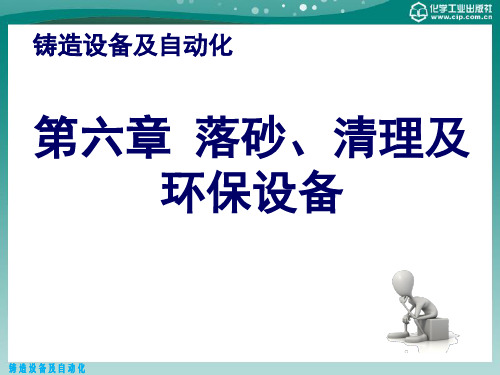
批量生产中清 理铸件时,喷 丸常用于铸铁 和铸钢件;喷 砂多用于非铁 合金铸件
铸造设备及自动化
6.2.1 铸件表面清理方法及设备概述
续上表 表面清 所用设备(工具)与特点 理方法 机械手 1. 采用预编程序的程序控制或模拟随动遥控操 自动打 纵机器人或机械手对铸件进行自动打磨和表面 磨系统 清理 2. 使铸件清理工作从高温、噪声、粉尘等恶劣 的工作环境及繁重体力劳动中解放出来 3. 操作者必须具备较高的技术素质,投资大, 维护保养严格 4. 须进行开发性设计研究 应用范围 用于成批或 大量流水生 产的各类铸 件
铸造设备及自动化
6.2.4 喷砂清理设备
2)影响抛丸清理质量因素 ① 抛丸速度 ② 抛丸量
③ 叶片与分丸器扇形体之间的相对位置
④ 弹丸的散射及分布 ⑤ 弹丸的材质及大小
铸造设备及自动化
6.2.4 喷砂清理设备
图6-16 抛丸速度与抛射距离间的关系
铸造设备及自动化
6.2.4 喷砂清理设备
图6-17 弹丸的散射图
效果的指标有:
1)撞击比能e 2)铸型跳高h 3)落砂效果量度E
w n E fH H H (mm ) s 2 60
(6-1)
铸造设备及自动化
6.1.1 振动落砂机
(1) 惯性类振动落砂机
图6-1 单轴惯性振动落砂机结构简图 1-弹簧 2-栅床 3-主轴 4-偏心块 5-铸型
铸造设备及自动化
6.2.3 喷丸清理设备
图6-10 Q2014B型喷丸器示意图 (a)喷射位置 (b)停止喷射位置 1-混合室 2-转轴 3-喷头 4-底座 5-下室 6-下室阀 7-上室 8-上室阀 9-上罩10-转换开关 11-三通阀 12-转换开关活塞 13、14-直通开关 15-压力表 16-闭锁蝶阀
河科大铸造机械化课后习题答案

第一章 1.用平板压实时,砂型内的应力大体如何分布?在没有模样情况下,平板压实后,砂型内哪些点的紧实度较低,哪些点的紧实度较高? 平板慢速压实时,在砂型中心的高度上,紧实度的差别不大,在大约相当于砂型宽度2/3的深度上,出现极大值。
在砂型的边角处,紧实度上高下低,特别是下边模板的边角处,紧实度很低。
平板高速压实时,紧实度分布呈C 形,顶部及底部应力高,中部应力较低。
型砂下面模板的边角处和砂型中心最高处紧实度较低,砂型宽度2/3深度紧实度较高。
2.为什么减小压缩比的差别能使压实紧实度均匀化?有哪些减小压缩比的方法? 1)210δδδ分别为压实前的紧实度以及压实后模样四周及模样顶上型砂平均紧实度,其中1δ=0δ+0δh/H 2δ=2δ+0δh/(H-m)。
h/H 和h/(H-m) 为砂柱的压缩比。
由上式可以看出减小压缩比能使1δ约等于2δ,也即是砂型紧实度均匀化。
2)方法:用油脂作粘结剂或流态砂等湿强度很低的型砂;提高模样顶上砂柱的高度比B=hs/bmin 使B 大于等于1—1.25;适当的提高压实比 3.有哪一些因素能影响射砂时型砂从射砂孔顺利射出? 影响射砂的因素:(1)射砂气压及气压梯度:提高射砂气压,能提高气压梯度,加强气流渗透,使砂能顺利射出。
(2)型砂性能与射砂筒中型砂的紧实:型砂性能 粘结力小,流动性好(油砂,树脂砂);湿强度高,粘结力大的型砂,流动性差,不易出砂,易搭棚。
射筒中型砂的紧实,型砂越紧实,气流渗透阻力越大。
(3)进气方式:采用均匀进气时,有利于射砂。
这时气压梯度密集在锥型射砂孔处,增强气流渗透有利于射砂。
射头边上的等压线比中心密不易搭棚。
但均匀进气的射砂机构设计制造较复杂。
(4)锥型射头与射孔大小:锥形射头使射砂筒的气流向射头集中,增大渗透速度。
有利于射砂。
射孔不易过小,小射孔孔壁对砂粒的射出阻力相对增大,使渗透气流速度减小,不利于射砂,射孔足够大,利于射砂。
4.为什么气冲第一阶段紧实过程可以视为为初实层形成、扩展及冲击过程? 在低紧实度范围内,紧实力提高不大,可使型砂的紧实度提高很多,所以在气压差的作用下,ab 区间的型砂迅速形成一层紧实度较高,对空气渗透阻力较大,对上面下来的气流渗透有一定隔离作用的砂层,这一隔绝层使气体对砂层的推动力变大,使以后的气冲过程成为这一砂层推动下面砂层向下运动及扩大的过程。
低压 、挤 压铸 造机改为挤压 压铸机 彻底解决铸件缩
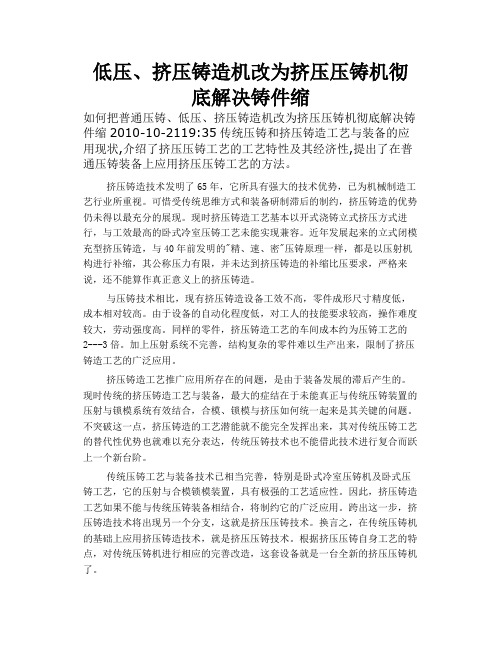
低压、挤压铸造机改为挤压压铸机彻底解决铸件缩如何把普通压铸、低压、挤压铸造机改为挤压压铸机彻底解决铸件缩2010-10-2119:35传统压铸和挤压铸造工艺与装备的应用现状,介绍了挤压压铸工艺的工艺特性及其经济性,提出了在普通压铸装备上应用挤压压铸工艺的方法。
挤压铸造技术发明了65年,它所具有强大的技术优势,已为机械制造工艺行业所重视。
可惜受传统思维方式和装备研制滞后的制约,挤压铸造的优势仍未得以最充分的展现。
现时挤压铸造工艺基本以开式浇铸立式挤压方式进行,与工效最高的卧式冷室压铸工艺未能实现兼容。
近年发展起来的立式闭模充型挤压铸造,与40年前发明的"精、速、密"压铸原理一样,都是以压射机构进行补缩,其公称压力有限,并未达到挤压铸造的补缩比压要求,严格来说,还不能算作真正意义上的挤压铸造。
与压铸技术相比,现有挤压铸造设备工效不高,零件成形尺寸精度低,成本相对较高。
由于设备的自动化程度低,对工人的技能要求较高,操作难度较大,劳动强度高。
同样的零件,挤压铸造工艺的车间成本约为压铸工艺的2---3倍。
加上压射系统不完善,结构复杂的零件难以生产出来,限制了挤压铸造工艺的广泛应用。
挤压铸造工艺推广应用所存在的问题,是由于装备发展的滞后产生的。
现时传统的挤压铸造工艺与装备,最大的症结在于未能真正与传统压铸装置的压射与锁模系统有效结合,合模、锁模与挤压如何统一起来是其关键的问题。
不突破这一点,挤压铸造的工艺潜能就不能完全发挥出来,其对传统压铸工艺的替代性优势也就难以充分表达,传统压铸技术也不能借此技术进行复合而跃上一个新台阶。
传统压铸工艺与装备技术已相当完善,特别是卧式冷室压铸机及卧式压铸工艺,它的压射与合模锁模装置,具有极强的工艺适应性。
因此,挤压铸造工艺如果不能与传统压铸装备相结合,将制约它的广泛应用。
跨出这一步,挤压铸造技术将出现另一个分支,这就是挤压压铸技术。
换言之,在传统压铸机的基础上应用挤压铸造技术,就是挤压压铸技术。
压力铸造设备及其工艺

压铸的三要素—压铸模:
压铸模的结构
就是由优质钢材围成的可以形成零件的空腔。
就是将合金液引入成型系统,并排除气体和杂质的通道。
由结构钢组成的用以支撑、定位、导向的结构。
保证模具的工作温度。(保证模具的温度符合工艺的要求,提高模具的寿命;包括冷却水道、软管铜管、接头、模温机等。铝合金压铸模 预热温度:150~200℃ 工作温度:180~225℃ )
通常主要按机器结构和压射室(以下简称压室)的位置及其工作条件加以分类: 压铸机分热压室压铸机和冷压室压铸机两大类。 冷压室压铸机按其压室结构和布置方式又分卧式、立式两种形式。
压铸机的分类及其工作方式:
热压室压铸机 冷压室压铸机 热压室压铸机与冷压室压铸机的合模机构是一样的,其区别在于压射、浇注机构不同。热压室压铸机的压室与熔炉紧密地连成一个整体,而冷压室压铸机的压室与熔炉是分开的。 立式压铸机
压铸工艺的过程:
集中融化 机边保温 配置涂料 压铸操作循环
压铸过程
压铸过程
压铸过程
压铸过程
压铸过程
压铸过程
压铸过程
压铸的三要素--原材料;
压铸的三要素--压铸模;
压铸的三要素--压铸机;
压铸的三要素:
压铸的三要素--原材料:
对原材料的要求
满足两方面要求
良好的成型工艺性 包括: 1.铸造成型工艺性; 2.切削加工性; 3.焊接性能; 4.电镀性能; 5.热处理性能等;
合模机构
PART ONE
液压系统 电气系统
压铸机的工作方式: (1)合拢模具; (2)将金属液以人工或自动方式浇入压室(多数以自动方式); (3)压射冲头按预定的速度和一定的压力推送金属液填充进入模具型腔; (4)填充完毕,冲头保持一定的压力,直至金属液完全凝固成为压铸件为止; (5)打开模具,冲头与开模动作同步移动,从而推着余料饼随着压铸件和浇口一同留在动模而脱离定模,到达一定的距离时,冲头便返回复位; (6)开模后,压铸件、浇口和余料饼留在动模上,随即顶出并取出压铸件; 至此,完成一次压铸循环。
- 1、下载文档前请自行甄别文档内容的完整性,平台不提供额外的编辑、内容补充、找答案等附加服务。
- 2、"仅部分预览"的文档,不可在线预览部分如存在完整性等问题,可反馈申请退款(可完整预览的文档不适用该条件!)。
- 3、如文档侵犯您的权益,请联系客服反馈,我们会尽快为您处理(人工客服工作时间:9:00-18:30)。
图2-1 Z145B震压造型机总图
1-机身 2-按压阀 3-起模同步架 4-震击气缸 5-起模导向杆 6-起模顶杆 7-起模液压缸 8-振动器 9-转臂动力缸 10-转臂中心轴 11-垫块 12-压板机构 13-工作台 14-起模架
图2-3 震击气缸的工作工程示意图
1—震击活塞; 2—进气孔; 3—排气孔
•Δ1 ——弹簧的压缩量
•P′——弹簧刚度
•Fz—震击活塞的截面积
(b) 膨胀行程Sr 气缸即不进气也不排气,压缩空气膨胀,继续推着活塞及 工作台上升。 •(c) 排气上升行程Si
排气孔打开,气缸排气,缸内气压迅速下降,但活塞及工作 台因惯性上升。通常Si≈(0.6~0.7)Se。
•(d) 排气下降行程
• 活塞下降时一定满足 •(e) 压缩行程 当下降的活塞关闭排气孔后,气缸内的气压随活塞快速下降而 有所升高,直至撞击工作台,此时缸内气压一般要比A΄点的气压 低一些,工作台因有撞击时的回弹力,所以可以反弹上升,运动 构成一个循环。
ZB148A造型机的气动微震机构为弹簧垫式气动微震机构,工 作原理如下: (1)原始位置 工作台下沿和压实活塞上沿间,留有一定的间隙 Δ, Δ一般为15~20mm。 (2)预震 加砂后、压实之前震击活塞和震铁两者发生撞击。
(3)压震 压实的同时进行震击。
5. 起模机构
三.微震机构的运动分析
震铁在压震过程中的受力状态
•假设缸内气压为P时,活塞上升距离为ds,则气体对活塞所做 的功为: •在上升行程AB中,气体对活塞单位截面所作的功为:
W A
B A
( p 1105 Pa)dS
A
B
• 整个上升行程中气体对活塞单位截面积所作的功可用面积 ABCD41 A表示。同样,在活塞下落过程中,活塞对气体所作 的功可用面积AFED41 A表示。因而,在每一循环中,气体对 活塞的单位截面积所作的净功为:
p 0 D 2 pF Q R
(2)导向限位装置 (3)压板架 压板可以绕中心轴旋转 •4.起模机构 为了保证起模质量,起模运动要缓慢平稳,因而用气压油驱动
二、其他震击及震压造型机
1.Z148型震压造型机 最大砂箱内尺寸为800mm×475mm。 2.震击造型机 如Z2310型翻台震实造型机,其砂箱尺寸为:
震击总高度S是影响砂型紧实度的主要工艺参数之一,S一 般可在0.04~0.08 m之间选取,小型造型机取低值,大型造型机 取高值。其它参数如下: 进气行程Se约为Se=(0.4~0.5)S 膨胀行程Sr约为Sr =(0.2~0.4)Se 余隙高度S0约为(0.7~1.0)S 进气孔总截面积为Aj=(0.005~0.007)A 排气孔的总截面积约为Ap=(0.03~0.05)A
2. 压实机构
(1)压实气缸
压实缸直径的计算应按所需的压实推力确定,可用下式计算
4 Q: 工作台、活塞、砂箱、型砂和模板等的总重量:Q=(1.3~1.8)×104F(N) P: 压实比压(常为250~300kPa) p0 : 工作气压 (常为500~600kP a) R: 气缸壁对活塞运动的摩擦阻力,其值不大,可以略去。 P
四 .弹簧式微震机构示功图气动微震压实造型机的微震机构撞击效果的优劣,功能转换 是否经济,主要参数选择得是否适当,都可以通过测试得出 的示功图进行评定。 弹簧式气动微震机构的工作方式和示功图与震击式造型机 类似,所不同的是在压震过程中,由于弹簧恢复力随震铁位移 而变化,故示功图有其特殊性,需要时可参考其它相关书籍。
铸造设备及其自动化-3
宋延沛 教授 2014.6
•第二章 粘土砂造型设备及生产线
• 第一节 震压造型机 • -、Z145 震压造型机
• • • • 1. Z145 震压造型机的结构及工作过程 2.震击机构及震击循环 (1)震击机构 (1)震击循环
• (2)示功图 描述了缸内气压p与活塞行程S间的相互关系。 • (a)进气行程Se • 当 时活塞受气压推动开始上升。
•撞击工作台的比能 e= e。+e′ •震击比能 •反跳比能
显然,撞击比能e越大,震击效果就越好。设撞击的弹性 恢复系数为k,则e与e'的关系为e'=k2e。对于一般的震击造 型机,k=0.3~0.4,所以反跳能约为撞击能的0.1~0.15。
(3)影响震击循环的因素 1)进气行程Se及膨胀行程Sr: 进气行程Se及膨胀行程Sr越大, 则示功图的面积也越大。 2)余隙高度S。: 余隙体积过大,压缩空气进入气缸时,须 先把这一体积填满,于是气压升高速度减慢,而在排气时,需 排出的空气量多,占用时间较长,这些都可能导致震击过程减 缓,并且多消耗压缩空气。 V0 S •设余隙体积为V0,气缸的截面积为A,则 0 A 3)管路气压:管路气压低,能使振击减弱。若气压减低到一 定限度以下,或工作负荷过大,震击循环会出现双重撞击现象。 •4)进气孔和排气孔的大小: 若进气孔太小,进气过慢,也容 易出现双重撞击现象。如果排气孔不够大,惯性行程后,缸内 气体不能及时排出,则活塞下落时,缸内仍有相当大的气压, 会影响震击的力量。
图2-4 震击循环的示功图
•产生双重撞击的原因:
•(1)管路气压低; •(2)工作负荷过大。
•(3)进气孔太小,进气过慢。
结构方式: 不断进气司气方式 优点: 结构简单。 缺点: 空气浪费大。
图2-6 压板高度的调整 1—防尘罩 2—调整手轮 3—调整螺杆 4—导向及锁紧螺钉 5—压板
•图a是静止状态; •图 b 是震击缸刚刚开 始进气时的状态; •图 c 是震铁向下走完 全部行 程 S 时 的 状 态 ;
五.弹簧气动微震机构的设计
要实现压震,缸内气压需要克服:(实现压震的条件) 1. 活塞、工作台和有效负荷的重力; 2. 由于消除工作台与压实活塞上沿间的间隙△而增加的弹簧恢 复力; 3. 震铁移动进气行程Se、膨胀行程Sr及惯性行程Si所产生的弹 簧恢复力。
可能导致不能压震的原因: (1)运动部件(活塞、震铁和震击缸)的加工精度低; (2)运动部件配合过紧或进气通道阻力过大; (3)弹簧恢复力(或弹簧刚度)过大。 在设计压震机构时,必须对微震弹簧的刚度进行认真的核算。 为了保证震铁实现压震,要 求震铁在打开排气孔前,一直 是在加速下降,亦即作用于震 铁上外力的合力的方向始终向 下,惯性力Sn方向向上。 根据动静法,可得震铁受力 平衡方程式: pP Az+GT+Sn=N+R 因为打开排气孔前Sn≤0,代入上式有
P
'
p p Az R (Qy Qz ) Se S r
摩擦力可取R=αpP Az; 根据实测数据:α=0.05~0.15,上式又 可写成:
P
'
(1 a) p p Az (Qy Qz ) Se S r
根据有关实验,膨胀行程终了时,缸内气压一般为 250~350kPa 。按此值确定的弹簧刚度是保证能够顺利打开排气 孔的,但刚度偏小,震击力相应也小,对撞击不利。 经对现有的震击效果较好的造型机的震击机构进行验算表明, 取pp=300~350kPa代入是比较恰当的。在弹簧下设置可换垫片可 以调整Δ的大小,从而也可起到调整弹簧恢复力的作用。
W •=面积ABCD41A一面积AFED41A=面积ABCDEFA A
•一次震击循环中活塞实际所得到的震击能量,还必须从 气体对活塞所做的功W中减去运动摩擦所消耗的功,即:
•循环一次气体对活塞所作的功
•震击能量
•震击比能
e0 A W 2RS
•活塞的总行程
•活塞截面积 •活塞的运动摩擦阻力•设活塞在撞击后回弹时具 Nhomakorabea反跳比能e′
1000mm×800mm×300mm,
•第二节 低压微震压实造型机
•微震压实的优点: 1)对地基的震动较小;
2)可以实现微震、压震等不同紧实方法组合,紧实度分布比较 均匀; 3)工作震动频率较高,因而生产率比震击造型机高。
一、ZB148A半自动低压气动徽震压实造型机
1.概况 2.压头 压头的支承采用支承点结构; 压头的回转是通过两只气缸实现的。为了防止回转终 了时的冲击,设有缓冲液压缸 。 3.震压机构及起模机构 震压机构是弹簧垫式微震压实机构 为防止起模时工作台浮动,装有工作台卡紧器 4.工作程序
ppAz+GT ≥ N+R
N ≤ ppAz+GT –R
式中: pp为膨胀行程终了时缸内气压
膨胀行程终了时弹簧恢复力为:N=N0+(Δ+Se十Sr)P' 式中 N0——预震开始前弹簧的恢复力;
•N0=Qy+Qz+GT 有效负荷重量 震铁重 震击机构升起部分自重
N≤ ppAz+GT-R
•N=Qy+Qz+GT+(Δ+Se十Sr)P′
•图 d 是膨胀行程终了, 即将打开排气孔时的 状态。
1. 缸内气压产生向下推力pFz, 2. 震铁重力GT,方向始终向 下,大小不变。 3. 弹簧恢复力N,方向始终向 上,大小与震铁行程成正 比, 它是一个规则变化的外力。 4. 摩擦阻力R,它的方向总是 逆着震铁运动的方向,大 小一 般可视为常数 还有一个与上述外力的 合力相平衡的假想力—— 惯性力Sn ,惯性力的方向与 加速度方向相反。 震铁的运动是这四种外力 综合作用的结果。