不锈钢管表面处理最有效的方法
不锈钢管钝化方案
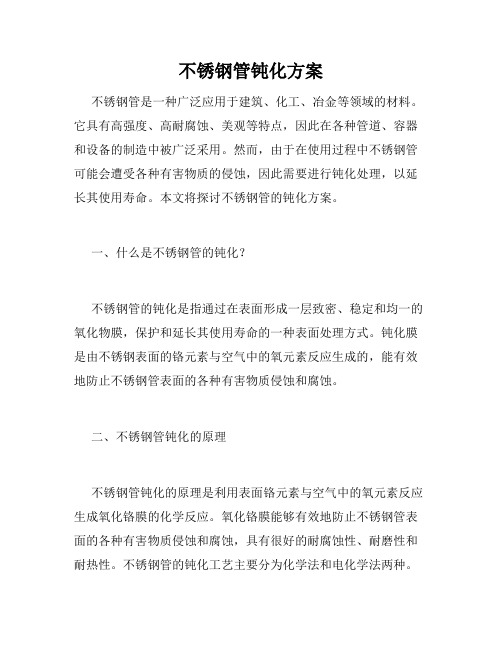
不锈钢管钝化方案不锈钢管是一种广泛应用于建筑、化工、冶金等领域的材料。
它具有高强度、高耐腐蚀、美观等特点,因此在各种管道、容器和设备的制造中被广泛采用。
然而,由于在使用过程中不锈钢管可能会遭受各种有害物质的侵蚀,因此需要进行钝化处理,以延长其使用寿命。
本文将探讨不锈钢管的钝化方案。
一、什么是不锈钢管的钝化?不锈钢管的钝化是指通过在表面形成一层致密、稳定和均一的氧化物膜,保护和延长其使用寿命的一种表面处理方式。
钝化膜是由不锈钢表面的铬元素与空气中的氧元素反应生成的,能有效地防止不锈钢管表面的各种有害物质侵蚀和腐蚀。
二、不锈钢管钝化的原理不锈钢管钝化的原理是利用表面铬元素与空气中的氧元素反应生成氧化铬膜的化学反应。
氧化铬膜能够有效地防止不锈钢管表面的各种有害物质侵蚀和腐蚀,具有很好的耐腐蚀性、耐磨性和耐热性。
不锈钢管的钝化工艺主要分为化学法和电化学法两种。
1. 化学法化学法主要是利用化学反应使不锈钢管表面产生工业氧化皮,使其颜色发生变化。
化学法钝化的优点在于成本低、效果好、操作简单等。
但是,缺点在于氧化皮涂层的厚度不易控制,其耐腐蚀性不如电化学钝化。
2. 电化学法电化学法是指在酸性或碱性溶液中使用外加电流的方法进行钝化处理。
通过外加电流可以控制不锈钢管表面的氧化皮厚度,并使钝化膜更加致密、均匀。
电化学钝化的优点在于可以控制钝化膜的厚度和质量,有较好的耐腐蚀性和美观性。
三、不锈钢管钝化的工艺不锈钢管的钝化工艺根据使用环境和需求分为两种:化学法和电化学法。
1. 化学法化学法钝化主要分为浸泡法和喷涂法。
因为化学法钝化处理的成本比较低,因此在工作环境相对较温和时仍然能够满足要求。
(1)浸泡法浸泡法需要将不锈钢管浸泡在强碱或强酸中,使钝化皮生成。
浸泡时间因酸碱的浓度不同而不同,而且在浸泡过程中还要设置循环过滤,以保证整个钝化工艺的均匀性和有效性。
(2)喷涂法喷涂法是利用特殊的喷涂设备喷涂钝化剂致力于发生化学反应,生成钝化皮。
不锈钢管表面处理工艺
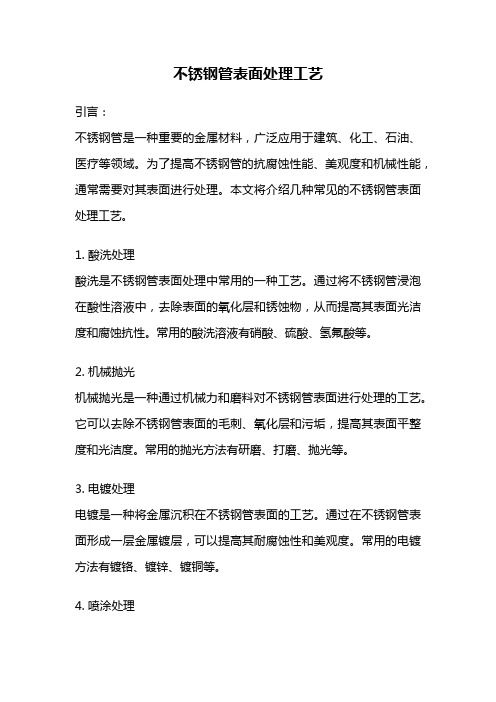
不锈钢管表面处理工艺引言:不锈钢管是一种重要的金属材料,广泛应用于建筑、化工、石油、医疗等领域。
为了提高不锈钢管的抗腐蚀性能、美观度和机械性能,通常需要对其表面进行处理。
本文将介绍几种常见的不锈钢管表面处理工艺。
1. 酸洗处理酸洗是不锈钢管表面处理中常用的一种工艺。
通过将不锈钢管浸泡在酸性溶液中,去除表面的氧化层和锈蚀物,从而提高其表面光洁度和腐蚀抗性。
常用的酸洗溶液有硝酸、硫酸、氢氟酸等。
2. 机械抛光机械抛光是一种通过机械力和磨料对不锈钢管表面进行处理的工艺。
它可以去除不锈钢管表面的毛刺、氧化层和污垢,提高其表面平整度和光洁度。
常用的抛光方法有研磨、打磨、抛光等。
3. 电镀处理电镀是一种将金属沉积在不锈钢管表面的工艺。
通过在不锈钢管表面形成一层金属镀层,可以提高其耐腐蚀性和美观度。
常用的电镀方法有镀铬、镀锌、镀铜等。
4. 喷涂处理喷涂是一种将涂料喷射在不锈钢管表面的工艺。
通过喷涂不同颜色的涂料,可以改变不锈钢管的外观和美观度,同时还能提高其耐腐蚀性。
常用的喷涂方法有喷漆、喷粉等。
5. 氧化处理氧化是一种通过在不锈钢管表面形成氧化层来改变其颜色和外观的工艺。
通过控制氧化层的厚度和颜色,可以实现不同的装饰效果。
常用的氧化方法有阳极氧化、化学氧化等。
6. 增饰处理增饰是一种通过在不锈钢管表面进行雕刻、刻纹等工艺来提高其装饰效果的方法。
通过增饰处理,可以使不锈钢管更具艺术感和独特性。
常用的增饰方法有雕刻、刻纹、喷砂等。
7. 超声波清洗超声波清洗是一种利用超声波振动来去除不锈钢管表面的污垢和杂质的工艺。
通过在清洗液中产生超声波,可以将污垢从不锈钢管表面剥离,提高其清洁度和表面光洁度。
结论:不锈钢管表面处理工艺多种多样,每种工艺都有其适用的领域和优势。
在实际应用中,根据不同的要求和目的,可以选择合适的表面处理工艺来提高不锈钢管的性能和外观。
通过精细的表面处理工艺,可以使不锈钢管更加耐腐蚀、美观和功能完善。
不锈钢管钝化方案
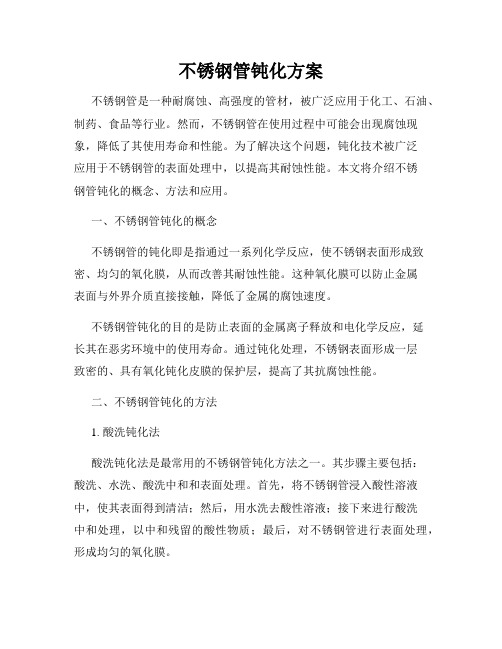
不锈钢管钝化方案不锈钢管是一种耐腐蚀、高强度的管材,被广泛应用于化工、石油、制药、食品等行业。
然而,不锈钢管在使用过程中可能会出现腐蚀现象,降低了其使用寿命和性能。
为了解决这个问题,钝化技术被广泛应用于不锈钢管的表面处理中,以提高其耐蚀性能。
本文将介绍不锈钢管钝化的概念、方法和应用。
一、不锈钢管钝化的概念不锈钢管的钝化即是指通过一系列化学反应,使不锈钢表面形成致密、均匀的氧化膜,从而改善其耐蚀性能。
这种氧化膜可以防止金属表面与外界介质直接接触,降低了金属的腐蚀速度。
不锈钢管钝化的目的是防止表面的金属离子释放和电化学反应,延长其在恶劣环境中的使用寿命。
通过钝化处理,不锈钢表面形成一层致密的、具有氧化钝化皮膜的保护层,提高了其抗腐蚀性能。
二、不锈钢管钝化的方法1. 酸洗钝化法酸洗钝化法是最常用的不锈钢管钝化方法之一。
其步骤主要包括:酸洗、水洗、酸洗中和和表面处理。
首先,将不锈钢管浸入酸性溶液中,使其表面得到清洁;然后,用水洗去酸性溶液;接下来进行酸洗中和处理,以中和残留的酸性物质;最后,对不锈钢管进行表面处理,形成均匀的氧化膜。
2. 化学钝化法化学钝化法是通过在不锈钢表面形成一层具有抗腐蚀性能的化学物质,来改善其钝化性能。
常见的化学钝化剂有铬酸钠、硫酸铜等。
通过浸泡、喷涂或刷涂等方式将钝化剂施加到不锈钢管表面,形成钝化层。
三、不锈钢管钝化的应用1. 化工行业化工行业中常用一些腐蚀性强的介质,如酸碱溶液等。
为了延长不锈钢管在此类介质中的使用寿命,钝化处理是必不可少的。
不锈钢管经过钝化处理后,可以有效降低与腐蚀性介质接触时的腐蚀速度,提高其使用寿命。
2. 石油行业石油行业中,不锈钢管广泛用于输送油气、化学品等。
在高温、高压、腐蚀性环境下,不锈钢管容易发生腐蚀,导致破损和泄漏。
通过钝化处理,不锈钢管可以形成均匀的、具有较强抗腐蚀性的氧化膜,提高其耐蚀性和抗压能力。
3. 制药行业制药行业对管材的要求非常严格,要求不锈钢管不仅要具有耐腐蚀性,而且要符合卫生标准。
不锈钢方管镜面做法
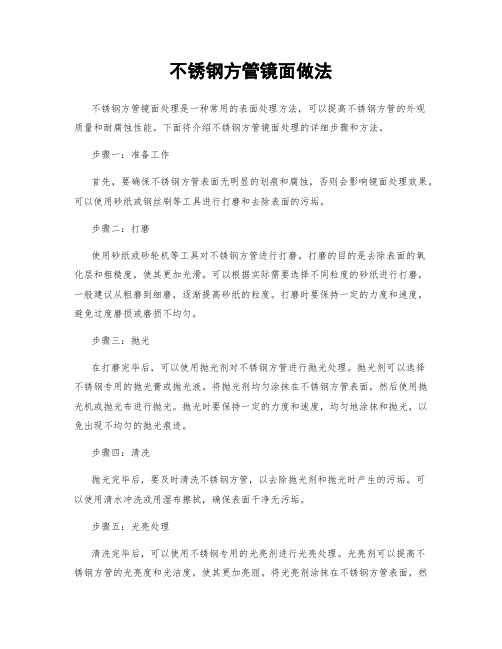
不锈钢方管镜面做法不锈钢方管镜面处理是一种常用的表面处理方法,可以提高不锈钢方管的外观质量和耐腐蚀性能。
下面将介绍不锈钢方管镜面处理的详细步骤和方法。
步骤一:准备工作首先,要确保不锈钢方管表面无明显的划痕和腐蚀,否则会影响镜面处理效果。
可以使用砂纸或钢丝刷等工具进行打磨和去除表面的污垢。
步骤二:打磨使用砂纸或砂轮机等工具对不锈钢方管进行打磨。
打磨的目的是去除表面的氧化层和粗糙度,使其更加光滑。
可以根据实际需要选择不同粒度的砂纸进行打磨,一般建议从粗磨到细磨,逐渐提高砂纸的粒度。
打磨时要保持一定的力度和速度,避免过度磨损或磨损不均匀。
步骤三:抛光在打磨完毕后,可以使用抛光剂对不锈钢方管进行抛光处理。
抛光剂可以选择不锈钢专用的抛光膏或抛光液。
将抛光剂均匀涂抹在不锈钢方管表面,然后使用抛光机或抛光布进行抛光。
抛光时要保持一定的力度和速度,均匀地涂抹和抛光,以免出现不均匀的抛光痕迹。
步骤四:清洗抛光完毕后,要及时清洗不锈钢方管,以去除抛光剂和抛光时产生的污垢。
可以使用清水冲洗或用湿布擦拭,确保表面干净无污垢。
步骤五:光亮处理清洗完毕后,可以使用不锈钢专用的光亮剂进行光亮处理。
光亮剂可以提高不锈钢方管的光亮度和光洁度,使其更加亮丽。
将光亮剂涂抹在不锈钢方管表面,然后使用抛光机或抛光布进行光亮处理。
处理时要均匀涂抹光亮剂,保持一定的力度和速度。
步骤六:最后清洗光亮处理完毕后,要再次清洗不锈钢方管,以去除光亮剂和处理时产生的污垢。
同样可以使用清水冲洗或用湿布擦拭,确保表面干净无污垢。
不锈钢方管镜面处理是一项精细的工艺,需要耐心和细致的操作。
在进行镜面处理时,要注意保护自己的安全,避免受伤。
另外,镜面处理后的不锈钢方管要避免与硬物碰撞,以免刮伤表面。
如果需要长期保持不锈钢方管的镜面光亮度,可以定期进行清洗和光亮处理。
总结起来,不锈钢方管镜面处理的步骤包括准备工作、打磨、抛光、清洗、光亮处理和最后清洗。
通过正确的操作方法和选择合适的工具和材料,可以使不锈钢方管的表面光洁度和光亮度得到有效提高。
不锈钢管道表面处理方式
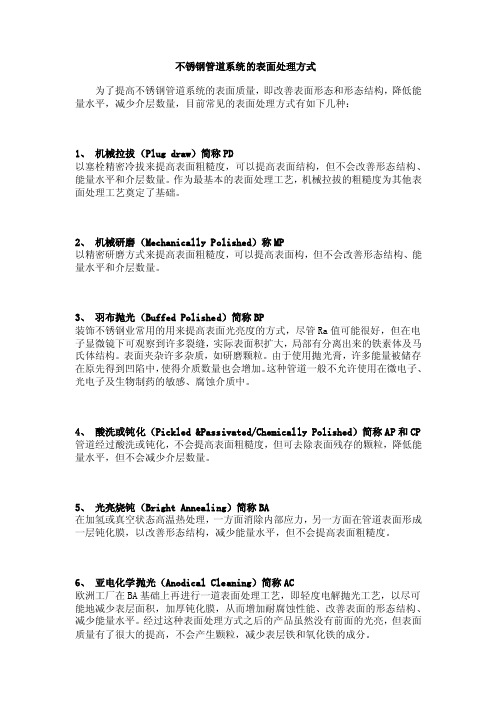
不锈钢管道系统的表面处理方式为了提高不锈钢管道系统的表面质量,即改善表面形态和形态结构,降低能量水平,减少介层数量,目前常见的表面处理方式有如下几种:1、机械拉拔(Plug draw)简称PD以塞栓精密冷拔来提高表面粗糙度,可以提高表面结构,但不会改善形态结构、能量水平和介层数量。
作为最基本的表面处理工艺,机械拉拔的粗糙度为其他表面处理工艺奠定了基础。
2、机械研磨(Mechanically Polished)称MP以精密研磨方式来提高表面粗糙度,可以提高表面构,但不会改善形态结构、能量水平和介层数量。
3、羽布抛光(Buffed Polished)简称BP装饰不锈钢业常用的用来提高表面光亮度的方式,尽管Ra值可能很好,但在电子显微镜下可观察到许多裂缝,实际表面积扩大,局部有分离出来的铁素体及马氏体结构。
表面夹杂许多杂质,如研磨颗粒。
由于使用抛光膏,许多能量被储存在原先得到凹陷中,使得介质数量也会增加。
这种管道一般不允许使用在微电子、光电子及生物制药的敏感、腐蚀介质中。
4、酸洗或钝化(Pickled &Passivated/Chemically Polished)简称AP和CP 管道经过酸洗或钝化,不会提高表面粗糙度,但可去除表面残存的颗粒,降低能量水平,但不会减少介层数量。
5、光亮烧钝(Bright Annealing)简称BA在加氢或真空状态高温热处理,一方面消除内部应力,另一方面在管道表面形成一层钝化膜,以改善形态结构,减少能量水平,但不会提高表面粗糙度。
6、亚电化学抛光(Anodical Cleaning)简称AC欧洲工厂在BA基础上再进行一道表面处理工艺,即轻度电解抛光工艺,以尽可能地减少表层面积,加厚钝化膜,从而增加耐腐蚀性能、改善表面的形态结构、减少能量水平。
经过这种表面处理方式之后的产品虽然没有前面的光亮,但表面质量有了很大的提高,不会产生颗粒,减少表层铁和氧化铁的成分。
7、电化抛光(Electro-Polished)简称EP通过电化学抛光,可以极大地提高表面形态及结构,使表层实际面积得到最大程度的减少。
不锈钢管镜面抛光方法
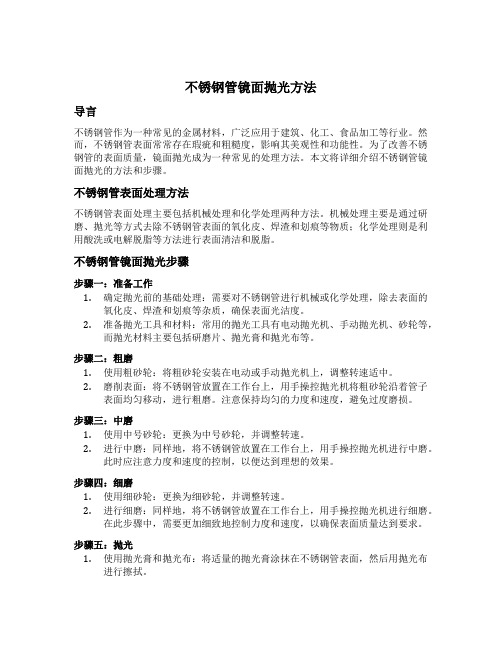
不锈钢管镜面抛光方法导言不锈钢管作为一种常见的金属材料,广泛应用于建筑、化工、食品加工等行业。
然而,不锈钢管表面常常存在瑕疵和粗糙度,影响其美观性和功能性。
为了改善不锈钢管的表面质量,镜面抛光成为一种常见的处理方法。
本文将详细介绍不锈钢管镜面抛光的方法和步骤。
不锈钢管表面处理方法不锈钢管表面处理主要包括机械处理和化学处理两种方法。
机械处理主要是通过研磨、抛光等方式去除不锈钢管表面的氧化皮、焊渣和划痕等物质;化学处理则是利用酸洗或电解脱脂等方法进行表面清洁和脱脂。
不锈钢管镜面抛光步骤步骤一:准备工作1.确定抛光前的基础处理:需要对不锈钢管进行机械或化学处理,除去表面的氧化皮、焊渣和划痕等杂质,确保表面光洁度。
2.准备抛光工具和材料:常用的抛光工具有电动抛光机、手动抛光机、砂轮等,而抛光材料主要包括研磨片、抛光膏和抛光布等。
步骤二:粗磨1.使用粗砂轮:将粗砂轮安装在电动或手动抛光机上,调整转速适中。
2.磨削表面:将不锈钢管放置在工作台上,用手操控抛光机将粗砂轮沿着管子表面均匀移动,进行粗磨。
注意保持均匀的力度和速度,避免过度磨损。
步骤三:中磨1.使用中号砂轮:更换为中号砂轮,并调整转速。
2.进行中磨:同样地,将不锈钢管放置在工作台上,用手操控抛光机进行中磨。
此时应注意力度和速度的控制,以便达到理想的效果。
步骤四:细磨1.使用细砂轮:更换为细砂轮,并调整转速。
2.进行细磨:同样地,将不锈钢管放置在工作台上,用手操控抛光机进行细磨。
在此步骤中,需要更加细致地控制力度和速度,以确保表面质量达到要求。
步骤五:抛光1.使用抛光膏和抛光布:将适量的抛光膏涂抹在不锈钢管表面,然后用抛光布进行擦拭。
2.进行抛光:用手操控抛光机,以适当的速度和力度对不锈钢管进行抛光。
注意保持均匀的力度和速度,避免过度磨损。
步骤六:清洁1.清洗表面:使用清水或清洗剂彻底清洁不锈钢管表面,去除残留的抛光膏和杂质。
2.干燥管子:用干净的毛巾或吹风机将不锈钢管表面彻底擦干。
不锈钢管件表面处理方式

不锈钢管件表面处理方式摘要:1.不锈钢管件概述2.不锈钢管件表面处理的重要性3.不锈钢管件的表面处理方式a.抛光处理b.喷涂处理c.电镀处理d.化学镀处理e.热处理4.各种表面处理方式的优缺点5.选择合适的表面处理方式正文:不锈钢管件是工业领域中广泛应用的一种零部件,其质量的好坏直接影响到设备的运行效率和寿命。
而不锈钢管件的表面处理则是影响其质量和性能的关键因素。
不锈钢管件的表面处理不仅可以提高其抗腐蚀能力,延长使用寿命,还能提高产品的美观度,满足不同场合的装饰需求。
因此,选择合适的表面处理方式至关重要。
目前,不锈钢管件的表面处理方式主要有以下几种:1.抛光处理:通过机械或化学方法去除不锈钢管件表面的微小凸起和划痕,使其表面变得光滑。
抛光处理可以提高不锈钢管件的抗腐蚀性和美观度,但耐磨性较差。
2.喷涂处理:在不锈钢管件表面涂上一层或多层涂料,以提高其抗腐蚀性、耐磨性和美观度。
喷涂处理可以根据需要选择不同类型的涂料,但耐候性较差。
3.电镀处理:在一定条件下,将一种金属沉积在不锈钢管件表面,形成一层保护膜。
电镀处理可以提高不锈钢管件的抗腐蚀性和耐磨性,但成本较高。
4.化学镀处理:通过化学方法在不锈钢管件表面形成一层金属膜,以提高其抗腐蚀性和耐磨性。
化学镀处理具有成本低、环保等优点,但耐候性较差。
5.热处理:通过改变不锈钢管件的温度和处理方式,改变其内部结构,提高其力学性能和抗腐蚀性。
热处理可以提高不锈钢管件的性能,但可能会影响其尺寸和形状。
总之,在选择不锈钢管件表面处理方式时,需要根据实际需求和使用环境,综合考虑各种处理方式的优缺点,选择最合适的表面处理方式。
不锈钢管的处理状态
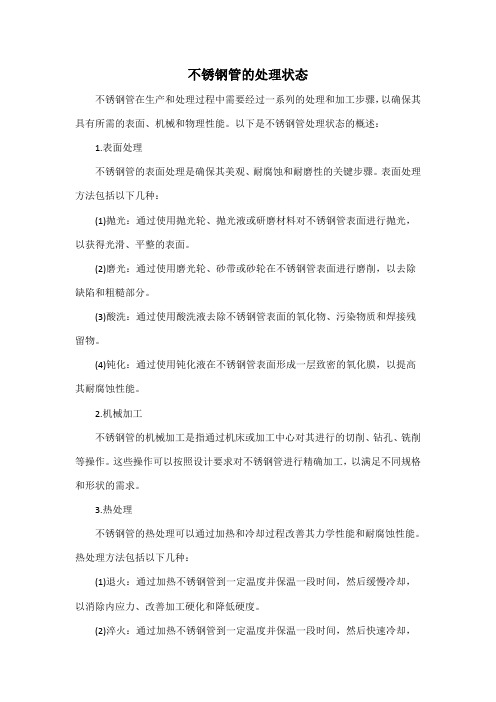
不锈钢管的处理状态不锈钢管在生产和处理过程中需要经过一系列的处理和加工步骤,以确保其具有所需的表面、机械和物理性能。
以下是不锈钢管处理状态的概述:1.表面处理不锈钢管的表面处理是确保其美观、耐腐蚀和耐磨性的关键步骤。
表面处理方法包括以下几种:(1)抛光:通过使用抛光轮、抛光液或研磨材料对不锈钢管表面进行抛光,以获得光滑、平整的表面。
(2)磨光:通过使用磨光轮、砂带或砂轮在不锈钢管表面进行磨削,以去除缺陷和粗糙部分。
(3)酸洗:通过使用酸洗液去除不锈钢管表面的氧化物、污染物质和焊接残留物。
(4)钝化:通过使用钝化液在不锈钢管表面形成一层致密的氧化膜,以提高其耐腐蚀性能。
2.机械加工不锈钢管的机械加工是指通过机床或加工中心对其进行的切削、钻孔、铣削等操作。
这些操作可以按照设计要求对不锈钢管进行精确加工,以满足不同规格和形状的需求。
3.热处理不锈钢管的热处理可以通过加热和冷却过程改善其力学性能和耐腐蚀性能。
热处理方法包括以下几种:(1)退火:通过加热不锈钢管到一定温度并保温一段时间,然后缓慢冷却,以消除内应力、改善加工硬化和降低硬度。
(2)淬火:通过加热不锈钢管到一定温度并保温一段时间,然后快速冷却,以提高其硬度和耐磨性。
(3)回火:通过加热不锈钢管到一定温度并保温一段时间,然后缓慢冷却,以调整其力学性能、消除应力集中和改善韧性。
4.防腐处理不锈钢管的防腐处理是提高其耐腐蚀性能的重要步骤。
防腐处理方法包括以下几种:(1)电镀:通过在管材表面电镀一层金属或合金,以提供一层保护层,抵抗氧化和腐蚀。
常见的电镀层包括镍、铬和锌等。
(2)喷涂:通过在管材表面喷涂防腐涂料,以提供一层隔离层,防止腐蚀介质渗透。
常见的防腐涂料包括环氧树脂、聚氨酯和防锈漆等。
5.性能检验不锈钢管在处理完成后需要进行性能检验,以确保其符合设计要求和质量标准。
性能检验方法包括以下几种:(1)外观检验:检查不锈钢管的表面质量、光滑度、氧化膜厚度等是否符合要求。
- 1、下载文档前请自行甄别文档内容的完整性,平台不提供额外的编辑、内容补充、找答案等附加服务。
- 2、"仅部分预览"的文档,不可在线预览部分如存在完整性等问题,可反馈申请退款(可完整预览的文档不适用该条件!)。
- 3、如文档侵犯您的权益,请联系客服反馈,我们会尽快为您处理(人工客服工作时间:9:00-18:30)。
随着我国经济的持续发展,国家大力发展能源行业,长输油气管线是能源保障的重要方式,在输油(气)管线防腐施工过程中,不锈钢管表面处理是决定管线防腐使用寿命的关键因素之一,它是防腐层与不锈钢管能否牢固结合的前提。
经研究机构验证,防腐层的寿命除取决于涂层种类、涂覆质量和施工环境等因素外,不锈钢管的表面处理对防腐层寿命的影响约占50%,因此,应严格按照防腐层规范对钢管表面的要求,不断探索和总结,不断改进钢管表面处理方法。
1、清洗
利用溶剂、乳剂清洗不锈钢材表面,以达到去除油、油脂、灰尘、润滑剂和类似的有机物,但它不能去除钢材表面的锈、氧化皮、焊药等,因此在防腐生产中只作为辅助手段。
2、工具除锈
主要使用不锈钢钢丝刷等工具对钢材表面进行打磨,可以去除松动或翘起的氧化皮、铁锈、焊渣等。
手动工具除锈能达到Sa2级,动力工具除锈可达到Sa3级,若钢材表面附着牢固的氧化铁皮,工具除锈效果不理想,达不到防腐施工要求的锚纹深度。
3、酸洗
一般用化学和电解两种方法做酸洗处理,管道防腐只采用化学酸洗,可以去除氧化皮、铁锈、旧涂层,有时可用其作为喷砂除锈后的再处理。
化学清洗虽然能使表面达到一定的清洁度和粗糙度,但其锚纹浅,而且易对环境造成污染。
4、喷(抛)射除锈
喷(抛)射除锈是通过大功率电机带动喷(抛)射叶片高速旋转,使钢砂、钢丸、铁丝段、矿物质等磨料在离心力作用下对钢管表面进行喷(抛)射处理,不仅可以彻底清除铁锈、氧化物和污物,而且不锈钢管在磨料猛烈冲击和磨擦力的作用下,还能达到所需要的均匀粗糙度。
喷(抛)射除锈后,不仅可以扩大管子表面的物理吸附作用,而且可以增强防腐层与管子表面的机械黏附作用。
因此,喷(抛)射除锈是管道防腐的理想除锈方式。
一般而言,喷丸(砂)除锈主要用于管子内表面处理,抛丸(砂)除锈主要用于管子外表面处理。
采用喷(抛)射除锈应注意几个问题。
4.1除锈等级
对于钢管常用的环氧类、乙烯类、酚醛类等防腐涂料的施工工艺,一般要求钢管表面达到近白级(Sa2.5)。
实践证明,采用这种除锈等级几乎可以除掉所有的氧化皮、锈和其他污物,锚纹深度达到40~100μm,充分满足防腐层与不锈钢管的附着力要求,而喷(抛)射除锈工艺可用较低的运行费用和稳定可靠的质量达到
近白级(Sa2.5)技术条件。
4.2喷(抛)射磨料
为了达到理想的除锈效果,应根据不锈钢管表面的硬度、原始锈蚀程度、要求的表面粗糙度、涂层类型等来选择磨料,对于单层环氧、二层或三层聚乙烯涂层,采用钢砂和钢丸的混合磨料更易达到理想的除锈效果。
钢丸有强化钢表面的作用,而钢砂则有刻蚀钢表面的作用。
钢砂和钢丸的混合磨料(通常钢丸的硬度为40~50HRC,钢砂的硬度为50~60HRC可用于各种钢表面,即使是用在C 级和D级锈蚀的不锈钢表面上,除锈效果也很好。
4.3磨料的粒径及配比
为获得较好的均匀清洁度和粗糙度分布,磨料的粒径及配比设计相当重要。
粗糙度太大易造成防腐层在锚纹尖峰处变薄;同时由于锚纹太深,在防腐过程中防腐层易形成气泡,严重影响防腐层的性能。
粗糙度太小会造成防腐层附着力及耐冲击强度下降。
对于严重的内部点蚀,不能仅靠大颗粒磨料高强度冲击,还必须靠小颗粒打磨掉腐蚀产物来达到清理效果,同时合理的配比设计不仅可减缓磨料对管道及喷嘴(叶片)的磨损,而且磨料的利用率也可大大提高。
通常,钢丸的粒径为0.8~1.3mm,钢砂粒径为0.4~1.0mm,其中以0.5~1.0mm为主要成分。
砂丸比一般为5~8。
应该注意的是在实际操作中,磨料中钢砂和钢丸的理想比例很难达到,原因是硬而易碎的钢砂比钢丸的破碎率高。
为此,在操作中应不断抽样检测混合磨料,根据粒径分布情况,向除锈机中掺入新磨料,而且掺人的新磨料中,钢砂的数量要占主要的。
4.4除锈速度
不锈钢管的除锈速度取决于磨料的类型和磨料的排量,即单位时间内磨料施加到钢管的总动能E及单颗粒磨料的动能E1。
式中:
m——磨料的喷(抛)量;
V——磨料运行速度;
m1——单颗粒磨料的质量。
m的大小与磨料破碎率有关,破碎率大小直接影响表面处理作业的成本及除锈设备的费用。
当设备固定不变后,m为常数,y为常数,所以E也是一个常数,但由于磨料破碎,m1发生变化,因此,一般应选择损耗率较低的磨料,这样有
利于提高清理速度和长叶片的寿命。
4.5清洗和预热
在喷(抛)射处理前,采用清洗的方法除去不锈钢管表面的油脂和积垢,采用加热炉对管体预热至40一60℃,使钢管表面保持干燥状态。
在喷(抛)射处理时,由于钢管表面不含油脂等污垢,可增强除锈的效果,干燥的不锈钢管表面也有利于钢丸、钢砂与锈和氧化皮的分离,使除锈后的不锈钢管表面更加洁净。