打孔机结构原理设计(机械系统设计大作业)
打孔机的工作原理和应用领域介绍
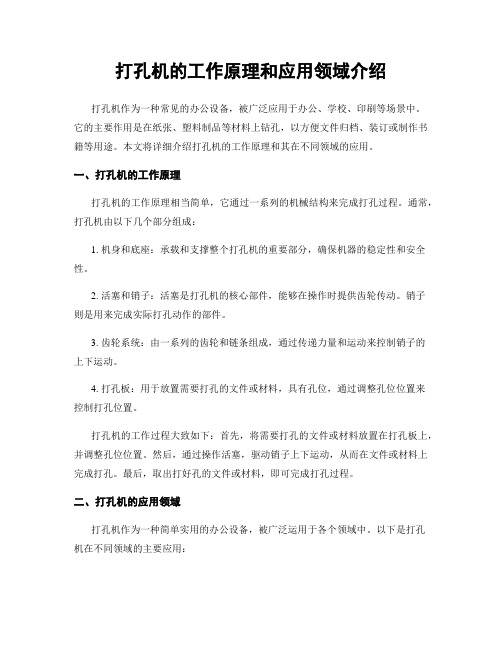
打孔机的工作原理和应用领域介绍打孔机作为一种常见的办公设备,被广泛应用于办公、学校、印刷等场景中。
它的主要作用是在纸张、塑料制品等材料上钻孔,以方便文件归档、装订或制作书籍等用途。
本文将详细介绍打孔机的工作原理和其在不同领域的应用。
一、打孔机的工作原理打孔机的工作原理相当简单,它通过一系列的机械结构来完成打孔过程。
通常,打孔机由以下几个部分组成:1. 机身和底座:承载和支撑整个打孔机的重要部分,确保机器的稳定性和安全性。
2. 活塞和销子:活塞是打孔机的核心部件,能够在操作时提供齿轮传动。
销子则是用来完成实际打孔动作的部件。
3. 齿轮系统:由一系列的齿轮和链条组成,通过传递力量和运动来控制销子的上下运动。
4. 打孔板:用于放置需要打孔的文件或材料,具有孔位,通过调整孔位位置来控制打孔位置。
打孔机的工作过程大致如下:首先,将需要打孔的文件或材料放置在打孔板上,并调整孔位位置。
然后,通过操作活塞,驱动销子上下运动,从而在文件或材料上完成打孔。
最后,取出打好孔的文件或材料,即可完成打孔过程。
二、打孔机的应用领域打孔机作为一种简单实用的办公设备,被广泛运用于各个领域中。
以下是打孔机在不同领域的主要应用:1. 办公场景:在办公室中,打孔机通常用于整理和归档文件,以便于装订或存档。
打孔机可以快速而准确地为文件打孔,使得文件可以放入文件夹或活页夹中,方便存储和查阅。
2. 学校教育:在学校、教育机构中,打孔机被广泛应用于学生的资料整理和装订。
教师可以使用打孔机为学生的作业、考试试卷等纸质资料打孔,方便学生存放和整理。
3. 印刷领域:对于印刷行业而言,打孔机也是一种必备工具。
在制作册子、书籍、画册等印刷品时,打孔机可以用来打孔以便装订。
通过打孔机,可以实现快速而精确的孔位设置,确保装订质量。
4. 工业制造:打孔机在一些工业制造过程中也有着广泛的应用。
例如,塑料制品、纸箱等行业,需要在制作过程中完成穿孔操作。
打孔机正是满足这一需求的理想设备,可以高效完成大批量的打孔任务。
打孔机的结构原理设计(机械系统设计大作业)
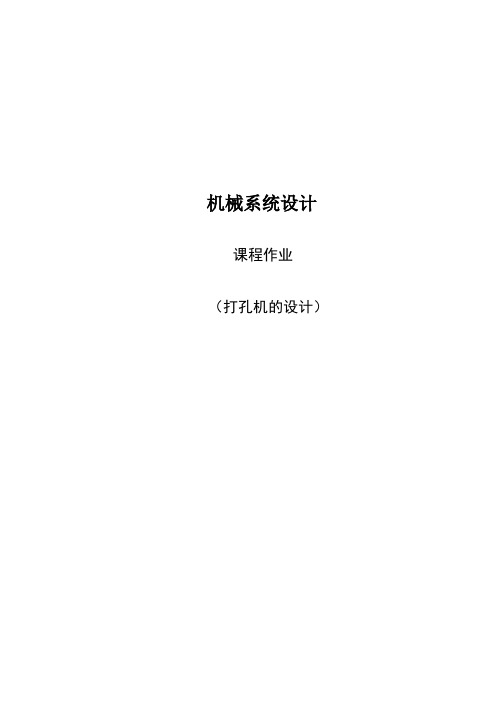
机械系统设计课程作业(打孔机的设计)一、设计任务书 (2)二、确定总共能(黑箱) (3)三、确定工艺原理 (3)(一)机构的工作原理: (3)(二)原动机的选择原理 (3)(三)传动机构的选择和工作原理 (4)四、工艺路线图 (4)五、功能分解(功能树) (5)六、确定每种功能方案,形态学矩阵 (6)七、系统边界 (7)八、方案评价 (7)九、画出方案简图 (7)十、总体布局图 (10)十一、主要参数确定 (11)十二、循环图 (14)一、设计任务书表1二、确定总共能(黑箱)(一)机构的工作原理:该系统由电机驱动,通过变速传动将电机的1450r/min降到主轴的2r/min,与传动轴相连的各机构控制送料,定位,和进刀等工艺动作,最后由凸轮机通过齿轮传动带动齿条上下平稳地运动,这样动力头也就能带动刀具平稳地上下移动从而保证了较高的加工质量。
(二)原动机的选择原理(1)原动机的分类原动机的种类按其输入能量的不同可以分为两类:A。
一次原动机此类原动机是把自然界的能源直接转变为机械能,称为一次原动机。
属于此类原动机的有柴油机,汽油机,汽轮机和燃汽机等。
B。
二次原动机此类原动机是将发电机等能机所产生的各种形态的能量转变为机械能,称为二次原动机.属于此类原动机的有电动机,液压马达,气压马达,汽缸和液压缸等.(2)选择原动机时需考虑的因素:1:考虑现场能源的供应情况。
2:考虑原动机的机械特性和工作制度与工作相匹配.3:考虑工作机对原动机提出的启动,过载,运转平稳等方面的要求.4:考虑工作环境的影响.5:考虑工作可靠,操作简易,维修方便。
6:为了提高机械系统的经济效益,须考虑初始成本和运转维护成本。
综上所述,在半自动钻床中最益选择二次原动机中的电动机作为原动件. (三)传动机构的选择和工作原理(1)传动机构的作用1、把原动机输出的转矩变换为执行机构所需的转矩或力。
2、把原动机输出的速度降低或提高,以适应执行机构的需要。
装订打孔机的设计原理
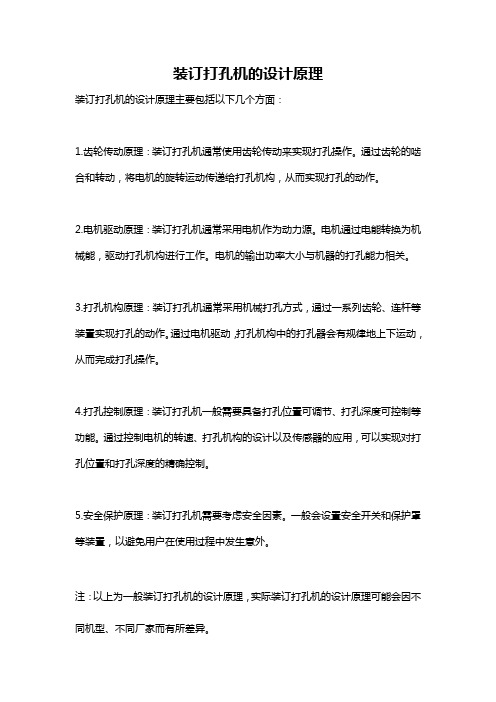
装订打孔机的设计原理
装订打孔机的设计原理主要包括以下几个方面:
1.齿轮传动原理:装订打孔机通常使用齿轮传动来实现打孔操作。
通过齿轮的啮合和转动,将电机的旋转运动传递给打孔机构,从而实现打孔的动作。
2.电机驱动原理:装订打孔机通常采用电机作为动力源。
电机通过电能转换为机械能,驱动打孔机构进行工作。
电机的输出功率大小与机器的打孔能力相关。
3.打孔机构原理:装订打孔机通常采用机械打孔方式,通过一系列齿轮、连杆等装置实现打孔的动作。
通过电机驱动,打孔机构中的打孔器会有规律地上下运动,从而完成打孔操作。
4.打孔控制原理:装订打孔机一般需要具备打孔位置可调节、打孔深度可控制等功能。
通过控制电机的转速、打孔机构的设计以及传感器的应用,可以实现对打孔位置和打孔深度的精确控制。
5.安全保护原理:装订打孔机需要考虑安全因素。
一般会设置安全开关和保护罩等装置,以避免用户在使用过程中发生意外。
注:以上为一般装订打孔机的设计原理,实际装订打孔机的设计原理可能会因不同机型、不同厂家而有所差异。
中心孔打孔机的设计
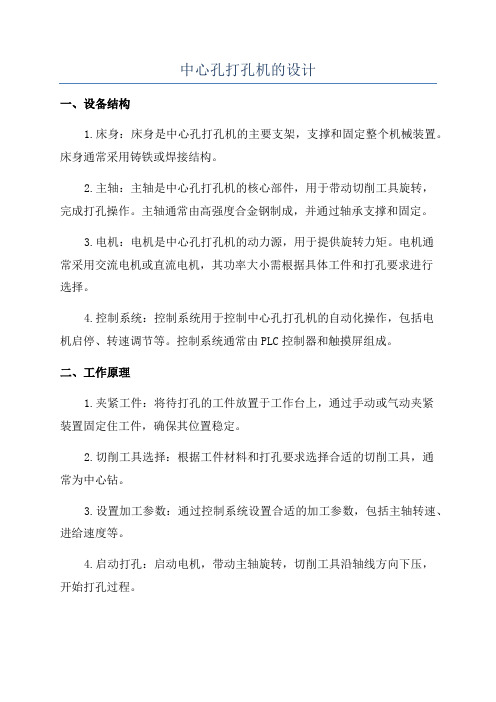
中心孔打孔机的设计一、设备结构1.床身:床身是中心孔打孔机的主要支架,支撑和固定整个机械装置。
床身通常采用铸铁或焊接结构。
2.主轴:主轴是中心孔打孔机的核心部件,用于带动切削工具旋转,完成打孔操作。
主轴通常由高强度合金钢制成,并通过轴承支撑和固定。
3.电机:电机是中心孔打孔机的动力源,用于提供旋转力矩。
电机通常采用交流电机或直流电机,其功率大小需根据具体工件和打孔要求进行选择。
4.控制系统:控制系统用于控制中心孔打孔机的自动化操作,包括电机启停、转速调节等。
控制系统通常由PLC控制器和触摸屏组成。
二、工作原理1.夹紧工件:将待打孔的工件放置于工作台上,通过手动或气动夹紧装置固定住工件,确保其位置稳定。
2.切削工具选择:根据工件材料和打孔要求选择合适的切削工具,通常为中心钻。
3.设置加工参数:通过控制系统设置合适的加工参数,包括主轴转速、进给速度等。
4.启动打孔:启动电机,带动主轴旋转,切削工具沿轴线方向下压,开始打孔过程。
5.打孔结束:达到打孔深度后,切削工具停止下压,主轴停止转动,完成打孔操作。
三、设计要点在中心孔打孔机的设计过程中,需要考虑以下几个要点:1.稳定性:床身的结构设计应确保机械装置的稳定性,以避免因振动而影响打孔精度。
2.定位准确性:工作台和夹具的设计应保证工件的定位准确,以确保打孔位置的精确性。
3.切削工具的选择和安装:切削工具的选用应根据材料和打孔要求进行选择,并正确安装在主轴上。
4.自动化控制:控制系统的设计应注重简洁、易操作,以实现自动化的打孔操作。
5.安全性:设计应考虑到操作人员的安全,并加装相应的安全装置,如防护罩、急停按钮等。
四、应用领域综上所述,中心孔打孔机的设计应注重稳定性、准确性、自动化控制和安全性,以满足不同行业对打孔加工的需求。
钻孔机工作原理
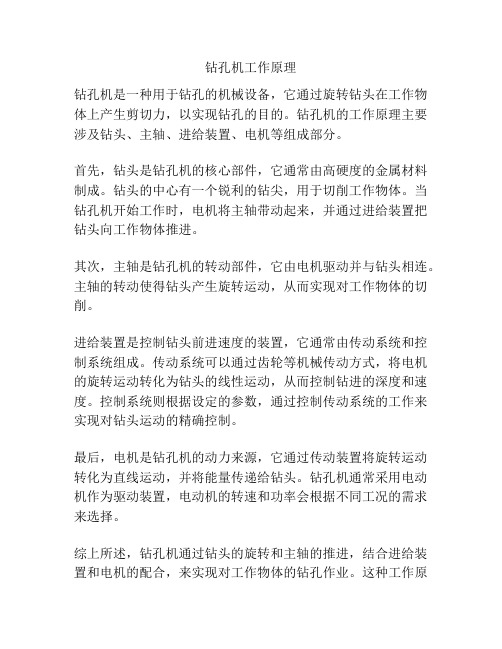
钻孔机工作原理
钻孔机是一种用于钻孔的机械设备,它通过旋转钻头在工作物体上产生剪切力,以实现钻孔的目的。
钻孔机的工作原理主要涉及钻头、主轴、进给装置、电机等组成部分。
首先,钻头是钻孔机的核心部件,它通常由高硬度的金属材料制成。
钻头的中心有一个锐利的钻尖,用于切削工作物体。
当钻孔机开始工作时,电机将主轴带动起来,并通过进给装置把钻头向工作物体推进。
其次,主轴是钻孔机的转动部件,它由电机驱动并与钻头相连。
主轴的转动使得钻头产生旋转运动,从而实现对工作物体的切削。
进给装置是控制钻头前进速度的装置,它通常由传动系统和控制系统组成。
传动系统可以通过齿轮等机械传动方式,将电机的旋转运动转化为钻头的线性运动,从而控制钻进的深度和速度。
控制系统则根据设定的参数,通过控制传动系统的工作来实现对钻头运动的精确控制。
最后,电机是钻孔机的动力来源,它通过传动装置将旋转运动转化为直线运动,并将能量传递给钻头。
钻孔机通常采用电动机作为驱动装置,电动机的转速和功率会根据不同工况的需求来选择。
综上所述,钻孔机通过钻头的旋转和主轴的推进,结合进给装置和电机的配合,来实现对工作物体的钻孔作业。
这种工作原
理能够高效地进行钻孔操作,并应用于各种需要钻孔的领域,如建筑、矿山、石油等。
打孔机的结构原理设计

打孔机的结构原理设计打孔机是一种用于在材料上打孔的机械设备。
它主要由机架、传动系统、控制系统和辅助系统四部分组成。
下面将详细介绍打孔机的结构、原理和设计。
1.机架打孔机的机架是整个机器的主要承载部分,它需要具备足够的刚性和稳定性。
机架通常由坚固的钢板焊接而成,保证机器在工作时不会产生明显的振动和变形。
2.传动系统打孔机的传动系统主要由电机、减速器和传动装置组成。
电机是打孔机的动力源,通过输出旋转运动的力来驱动整个机器。
减速器和传动装置则用于将电机输出的高速旋转转换为打孔机需要的低速高扭矩旋转。
3.打孔机构打孔机构是打孔机的核心部件。
它通常由主轴、刀具和导向装置等组成。
主轴是实现刀具旋转运动的主要部件,它需要具备足够的刚性和精度。
刀具则用于在材料上进行孔洞的切削,它通常由硬质合金材料制成,并根据需要采用不同形状的切削刃。
导向装置用于确保切削刀具在工作过程中的稳定性和精度。
4.控制系统打孔机的控制系统主要由PLC和人机界面组成。
PLC负责对打孔机的各个部件进行协调和控制,包括电机的启停、切削参数的设定等。
人机界面则用于操作员与打孔机进行交互,通过触摸屏或按钮等方式来实现对机器运行状态的监控和控制。
5.辅助系统打孔机的辅助系统包括润滑系统、冷却系统和除尘系统等。
润滑系统用于对打孔机的各个运动部件进行润滑,减少摩擦和磨损。
冷却系统用于对切削区域进行冷却,提高切削效率和刀具的使用寿命。
除尘系统则用于清除切削过程中产生的粉尘和切屑,保持工作环境的清洁和人员的健康安全。
在设计打孔机时,需要注意以下几点:1.根据工件材料的特性和要求,选择适合的切削方式和刀具。
不同的材料可能需要不同的切削参数和切削刃,需要根据实际情况进行调整。
2.考虑机器的稳定性和刚性。
在机架设计和选材时,要保证机器具备足够的稳定性和刚性,避免在工作时产生振动和变形。
3.选择合适的传动比和传动元件。
根据工件的大小、材料等要求,确定合适的传动比和传动元件,以确保机器具备足够的切削力和转速。
数控玻璃钻孔机床结构和控制系统设计
数控玻璃钻孔机床结构和控制系统设计数控玻璃钻孔机床是一种用于玻璃钻孔加工的专用设备,它能够根据预先设定的程序自动完成玻璃钻孔加工,具有高精度、高效率和稳定性等优点。
本文将从数控玻璃钻孔机床的结构和控制系统两方面进行设计分析。
1. 床身:床身是数控玻璃钻孔机床的主体部件,一般采用铸铁或焊接结构。
床身具有高刚性和高稳定性,能够承受加工过程中的各种力和振动。
床身上还配有T型槽,用于安装和固定工件夹具。
2. 主轴:主轴是数控玻璃钻孔机床的主要运动部件,其转速、进给速度和加工精度直接影响加工质量。
主轴通常采用高速电主轴,具有较大的转速范围和高刚性,能够满足不同直径和深度的钻孔加工需求。
3. 控制系统:控制系统是数控玻璃钻孔机床的关键部件,它能够根据预先设定的加工程序控制主轴、进给系统和冷却系统等各个部分的运动和工作状态。
控制系统一般采用PLC控制或数控系统,具有高稳定性和可靠性。
4. 进给系统:进给系统是数控玻璃钻孔机床的重要组成部分,它能够实现工件在X、Y、Z三个方向上的精确定位和进给运动。
进给系统通常采用直线导轨和高精度滚珠丝杠,能够实现高速、高精度的定位和运动。
5. 冷却系统:冷却系统用于对刀具和加工区域进行冷却,以防止刀具过热和工件出现变形等现象。
冷却系统一般采用喷淋式冷却和冷却液循环系统,能够有效提高加工质量和刀具寿命。
1. 硬件配置:数控玻璃钻孔机床的控制系统硬件包括主控制器、伺服驱动器、IO模块、人机界面等部件。
主控制器负责整个系统的控制和运行,伺服驱动器负责驱动主轴和进给系统的运动,IO模块用于输入输出信号的处理,人机界面用于操作和监控系统运行状态。
2. 软件系统:数控玻璃钻孔机床的控制系统软件包括系统运行软件、人机界面软件和加工程序编程软件等。
系统运行软件负责控制整个系统的运行和协调各个部分的工作,人机界面软件用于操作和监控系统运行状态,加工程序编程软件用于制定加工程序和参数设置。
3. 控制算法:数控玻璃钻孔机床的控制算法包括位置控制算法、速度控制算法和加工过程控制算法等。
打孔机原理
打孔机原理
打孔机是一种常见的办公设备,用于在纸张上打孔,以便将文件整齐地装订在
一起。
它的原理是通过机械力将刀具对准纸张并施加压力,从而在纸张上形成孔洞。
下面我们来详细了解一下打孔机的原理。
首先,打孔机通常由底座、压力手柄、刀具和废渣盒等部件组成。
底座是打孔
机的主体结构,用于支撑整个设备并固定纸张。
压力手柄则是用来施加压力的部件,通过手动操作可以让刀具对准纸张并施加所需的压力。
刀具是打孔机的核心部件,它通常由一组钢制的圆柱形刀片组成,可以在施加压力的同时将纸张上的部分材料切割出来,形成孔洞。
废渣盒则用来收集打孔过程中产生的废渣,保持工作环境整洁。
在使用打孔机时,首先需要将纸张放置在底座上,并确保位置正确。
然后,通
过操作压力手柄,使刀具对准纸张并施加压力。
在施加压力的同时,刀具会切割纸张上的部分材料,形成孔洞,并将废渣排出到废渣盒中。
完成打孔后,可以取下纸张进行下一步的操作。
打孔机的原理非常简单,但在实际使用中需要注意一些问题。
首先,需要根据
不同规格的纸张选择合适的打孔机,以确保打孔的效果和质量。
其次,在使用过程中需要注意安全,避免手部被刀具割伤。
另外,定期清理废渣盒和保养刀具也是保持打孔机性能的重要步骤。
总的来说,打孔机通过机械力将刀具对准纸张并施加压力,从而在纸张上形成
孔洞。
它的原理简单而有效,广泛应用于办公和学习等场合。
希望通过本文的介绍,读者对打孔机的原理有了更清晰的了解。
钻孔机工作原理
钻孔机工作原理
钻孔机是一种利用旋转力将物质制成孔洞的机器。
其工作原理主要由以下几个方面组成:
1. 主轴和钻头:钻孔机的主轴是一个中空管道,内部安装有钻头,通过电机或者液压系统提供动力。
钻头通常由一组硬质合金刀片组成,用于切割和磨削工件。
2. 切削液:在钻孔过程中,切削液起着冷却和润滑的作用。
它可以降低钻头和工件的摩擦,减少磨损,并帮助将切屑排出孔洞。
3. 进给系统:钻孔机通常具有进给系统,可以控制钻头的下压力和进给速度。
这些参数的选择根据材料的性质和所需的孔洞尺寸。
4. 钻刀提升系统:当钻孔机完成一个孔洞的钻削后,钻刀提升系统会将钻头从孔洞中抬起,以便更换或检查钻头。
5. 动力系统:钻孔机的动力可以来自电动机、液压系统或气压系统。
根据使用的材料和工作环境的不同,选择适当的动力系统以实现高效的钻孔。
综上所述,钻孔机通过旋转主轴和切削液的辅助,在物质表面形成孔洞。
进给系统和钻刀提升系统可以控制孔洞的尺寸和钻削的质量。
动力系统为钻孔机提供所需的动力。
这些组成部分相互配合,实现钻孔机的正常工作。
打孔机的结构原理设计
打孔机的结构原理设计打孔机是一种用于在材料上进行孔设计或加工的设备。
它具有高效率、精确度高、操作简单等特点。
打孔机的结构原理设计主要包括机身结构、传动系统、控制系统等几个方面。
一、机身结构:打孔机的机身结构通常由底座、立柱、主轴箱、工作台等组成。
1.底座:底座是打孔机的基础结构,一般采用铸造或焊接方法制成,以确保机器的稳定性和刚性。
底座上通常设有调节螺钉,可以调节机器的水平度和平稳度。
2.立柱与横梁:立柱与横梁是打孔机的固定和支撑结构。
立柱在底座上固定,而横梁则与立柱连接,支撑主轴箱和工作台。
3.主轴箱:主轴箱是打孔机的核心部件,它包含主轴、滑座、推杆等。
主轴通过滑座与横梁相连,可以实现上下运动。
主轴上设有夹具,用于夹持刀具,完成孔的加工。
4.工作台:工作台是打孔机的工作平台,位于主轴下方。
工作台具有平整的工作面和固定夹具,用于放置待加工材料。
在工作台上通常还设有定位孔或T型槽,以方便固定材料。
二、传动系统:打孔机的传动系统是控制主轴运动的关键部件,主要包括电机、皮带、链条、齿轮等。
1.电机:电机是驱动主轴旋转的动力源。
通常采用交流电机或直流电机,其功率和转速根据打孔机的需求进行选择。
2.皮带与链条:通过皮带或链条将电机与主轴箱连接起来,实现转动的传递。
皮带与链条具有一定的弹性和韧性,可以缓解由于转动不平稳造成的冲击和振动。
3.齿轮:齿轮是打孔机传动系统中常用的传动装置。
通过不同规格的齿轮组合,可以实现主轴的多速度调节,满足不同孔径的加工需求。
三、控制系统:打孔机的控制系统用于控制机器的运行和加工过程,主要包括控制面板、传感器、液压系统等。
1.控制面板:控制面板上设有开关、按钮、旋钮等,用于启动和停止机器,调节主轴的转速和运动方向,控制加工步骤等。
面板上通常还设有显示屏,用于显示加工参数和工艺状态。
2.传感器:传感器用于监测机器的工作状态和加工过程。
例如,通过光电传感器可以实现自动定位和自动停止,确保孔的准确定位和加工质量。
- 1、下载文档前请自行甄别文档内容的完整性,平台不提供额外的编辑、内容补充、找答案等附加服务。
- 2、"仅部分预览"的文档,不可在线预览部分如存在完整性等问题,可反馈申请退款(可完整预览的文档不适用该条件!)。
- 3、如文档侵犯您的权益,请联系客服反馈,我们会尽快为您处理(人工客服工作时间:9:00-18:30)。
机械系统设计课程作业(打孔机的设计)一、设计任务书 (1)二、确定总共能(黑箱) (2)三、确定工艺原理 (3)(一)机构的工作原理: (3)(二)原动机的选择原理 (3)(三)传动机构的选择和工作原理 (3)四、工艺路线图 (4)五、功能分解(功能树) (4)六、确定每种功能方案,形态学矩阵 (5)七、系统边界 (6)八、方案评价 (6)九、画出方案简图 (7)十、总体布局图 (9)十一、主要参数确定 (10)十二、循环图 (14)一、设计任务书表1二、确定总共能(黑箱)(一)机构的工作原理:该系统由电机驱动,通过变速传动将电机的1450r/min降到主轴的2r/min,与传动轴相连的各机构控制送料,定位,和进刀等工艺动作,最后由凸轮机通过齿轮传动带动齿条上下平稳地运动,这样动力头也就能带动刀具平稳地上下移动从而保证了较高的加工质量。
(二)原动机的选择原理(1)原动机的分类原动机的种类按其输入能量的不同可以分为两类:A.一次原动机此类原动机是把自然界的能源直接转变为机械能,称为一次原动机。
属于此类原动机的有柴油机,汽油机,汽轮机和燃汽机等。
B.二次原动机此类原动机是将发电机等能机所产生的各种形态的能量转变为机械能,称为二次原动机。
属于此类原动机的有电动机,液压马达,气压马达,汽缸和液压缸等。
(2)选择原动机时需考虑的因素:1:考虑现场能源的供应情况。
2:考虑原动机的机械特性和工作制度与工作相匹配。
3:考虑工作机对原动机提出的启动,过载,运转平稳等方面的要求。
4:考虑工作环境的影响。
5:考虑工作可靠,操作简易,维修方便。
6:为了提高机械系统的经济效益,须考虑初始成本和运转维护成本。
综上所述,在半自动钻床中最益选择二次原动机中的电动机作为原动件。
(三)传动机构的选择和工作原理(1)传动机构的作用1、把原动机输出的转矩变换为执行机构所需的转矩或力。
2、把原动机输出的速度降低或提高,以适应执行机构的需要。
3、把原动机输出的等速回转运动转变4、实现由一个或多个动力机驱动或若干个速度相同或不同的执行机构。
(2)传动机构选择的原则1:对于小功率传动,应在考虑满足性能的需要下,选用结构简单的传动装置,尽可能降低初始费用。
2:对大功率传动,应优先考虑传动的效率,降低运转费用和维修费用。
3:当执行机构要求变速时,若能与动力机调速比相适应,可直接连接或采用定传动比的传动装置;当执行机构要求变速范围大,用动力机调速不能满足机械特性和经济性要求时,则应采用变传动比传动;除执行机构要求连续变速外,尽量采用有级变速。
4:执行机构上载荷变化频繁,且可能出现过载,这时应加过载保护装置。
四、工艺路线图图2五、功能分解(功能树)图 3半自动打孔机送料 进刀 刀头旋转 定位夹紧 电动机齿轮齿条带传动 减速箱 电动机启停 过载保护人机交互六杆机构六、确定每种功能方案,形态学矩阵1.减速传动功能选用经济成本相对较低,而且具有传动效率高,结构简单,传动比大的特点,可满足具有较大传动比的工作要求,故我们这里就采用行星轮系来实现我设计的传动。
2.定位功能由于我们设计的机构要有间歇往复的运动,有当凸轮由近休到远休运动过程中,定位杆就阻止了工件滑动,当凸轮由远休到近休运动过程中可通过两侧的弹簧实现定位机构的回位,等待送料,凸轮的循环运动完成了此功能。
、3.进料功能进料也要要求有一定的间歇运动,我们可以用圆锥齿轮来实现换向,然后通过和齿轮的啮合来传递,再在齿轮上安装一个直动滚子从动件盘型凸轮机构,用从动件滚子推杆的直线往复运动实现进料。
4.进刀功能采用凸轮的循环运动,推动滚子使滚子摆动一个角度,通过杠杆的摆动弧度放大原理将滚子摆动角度进行放大.可增大刀具的进给量,在杠杆的另一端焊接一个圆弧齿轮,圆弧齿轮的摆动实现齿轮的转动,齿轮的转动再带动动力头的升降运动实现进刀.用形态学矩阵法创建机械系统运动方案根据系统的运动转换功能图可构成形态学矩阵如表。
由表3-3所示的形态学矩阵可以求出半自动钻床系统运动方案数为:N=3×3×3×3×3=243表 2七、系统边界室温20℃噪音小进入系统的是被加工的工件,出去的是已完成钻孔的工件八、方案评价根据功能原理,工艺分解过程及执行机构的选择,确定了以下两种运动方案: 方案一:A1+B3+C3+D3+E2方案二:A1+B2+C1+D3+E2定轴轮系传动;传动比很大,要用多级传动。
由于在空间上轴与轴之间的距离较大,但四杆的曲柄滑块机构行程太小。
故优先选用六杆机构综合评价,所以选择方案一九、画出方案简图1.减速机构:由于电动机的转速是1450r/min,而设计要求的主轴转速为2r/min,利用行星轮进行大比例的降速,然后用圆锥齿轮实现方向的转换。
图42.进刀机构采用一个摆动滚子从动件盘行凸轮机构来传递齿轮齿条机构.用摆动滚子从动件盘行凸轮机构来传递齿轮机构,当进刀的时候,凸轮在推程阶段运行,很容易通过机构传递带动齿轮齿条啮合.带动动刀头来完成钻孔,摆杆转动的幅度也是等于齿廓转动的幅度,两个齿轮来传动也具有稳性。
图53. 送料系统:采用六杆机构来代替曲柄滑块机构,由于设计的钻床在空间上传动轴之间的距离有点大,故一般四杆机构很难实现这种远距离的运动。
再加上用四杆机构在本设计中在尺寸上很小。
所以考虑到所设计的机构能否稳定的运行因此优先选用了如下图的六杆机构来实现。
由于本设计送料时不要求在传动过程中有间歇,所以不需要使用凸轮机构。
图 64.定位夹紧系统:定位系统采用的是一个偏置直动滚子从动件盘型凸轮,因为定位系统要有间歇,所以就要使用凸轮机构,但如果是平底推杆从动件,则凸轮就会失真,若增加凸轮的基圆半径,那么凸轮机构的结构就会很大,也不求实际,所以就采用一个偏置直动滚子从动件盘型凸轮,它就可以满足我们的实际要求了。
图 7十、总体布局图图81-电机 2-带传动 3-减速箱 4-送料装置 5-钻头 6-夹紧装置 7-定位装置8-进刀装置十一、主要参数确定1.送料机构机构采用如下分析送料连杆机构:采用如下机构来送料,根据要求,进料机构工作行程为40mm,可取ABCD4杆机构的极位夹角为12度,则由1)1( 180+-⨯=K Kθ得K=1.14,急回特性不是很明显,但对送料机构来说并无影响。
各杆尺寸:AB=8.53 BC=84.42 CD=60 DA=60 CE=40 EF=8该尺寸可以满足设计要求,即滑块的左右运动为40,ABCD的极位夹角为12度。
图 92.凸轮摆杆机构的设计:由进刀规律,我们设计了凸轮摆杆机构,又以齿轮齿条的啮合来实现刀头的上下运动;用凸轮摆杆机构和圆弧形齿条所构成的同一构件,凸轮摆杆从动件的摆动就可以实现弧形齿条的来回摆动,从而实现要求;采用滚子盘行凸轮,且为力封闭凸轮机构,利用弹簧力来使滚子与凸轮保持接触.刀具的运动规律就与凸轮摆杆的运动规律一致;弧形齿条所转过的弧长即为刀头所运动的的距离。
具体设计步骤如下:=40mm,中心距A=80mm,1.根据进刀机构的工作循环规律,设计凸轮基圆半径r摆杆长度d=65mm,最大摆角β为18°,凸轮转角λ=0-60°,β=0°;凸轮转角λ=60°-270°,刀具快进,β=5°,凸轮转角λ=270°-300°;凸轮转角λ=300°-360°,β=0°2.设计圆形齿条,根据刀头的行程和凸轮的摆角,设计出圆形齿轮的半径r=l/β,由β=18 。
l=20mm,3.得到r=63.69mm,图 103.凸轮推杆机构的设计:凸轮机构采用直动滚子盘行凸轮,且为力封闭凸轮机构,利用弹簧力来使滚子与凸轮保持接触,实现定位功能。
只要适当地设计出凸轮的轮廓曲线,就可以使推杆得我们所需要的运动规律,满足加工要求,而且响应快速,机构简单紧凑。
具体设计如下:设计基圆半径r0=40mm,偏心距e=25凸轮转角λ=0°-100°,定位机构休止,推杆行程h=0mm;凸轮转角λ=100°-285°,定位机构快进,推杆行程h=25mm;凸轮转角λ=285°-300°,定位机构休止,推杆行程h=0mm;凸轮转角λ=300°-360°,定位机构快退,推杆行程h=-25mm;设计偏心距e=25的原因是因为此凸轮执行的是定位,其定位杆的行程为25故如此设计。
4.行星轮系的计算:(1)用定轴轮系传动传动比=n输入/n输出=700 传动比很大,要用多级传动。
(2)用行星轮系传动图11Z1=35 Z2=20 Z2’=20 Z3=35 传动比iH3=700根据行星轮传动公式:i(H3)=1-i(31)H=1-Z2’Z1/Z3Z2由i(1H)=1-Z2'Z1/Z3Z2,考虑到齿轮大小与传动的合理性,经过比较设计皮带传动机构与齿轮系传动机构的相应参数如下表:皮带轮参数名称皮带轮1 皮带轮2半径(mm)100 100表4齿轮参数模数(mm)压力角(°)齿数(个)直径(mm)齿轮1 2. 20 35 70齿轮2 2 20 20 40齿轮2’ 2 20 20 40齿轮3 2 20 35 70表 5十二、循环图图11。