复合材料结构及其成型原理
纤维缠绕复合材料成型原理及工艺
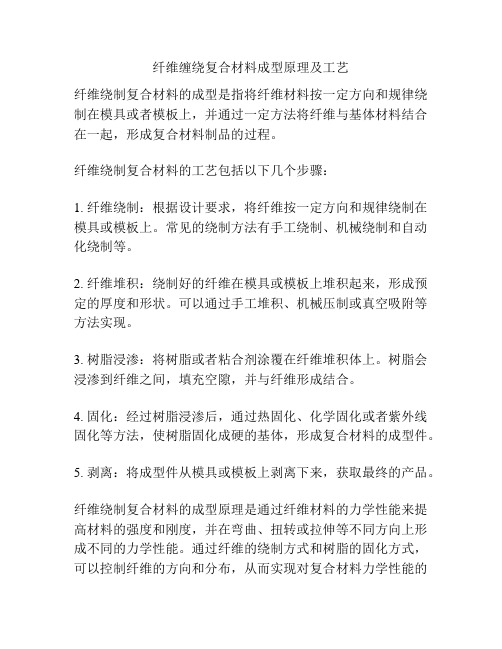
纤维缠绕复合材料成型原理及工艺
纤维绕制复合材料的成型是指将纤维材料按一定方向和规律绕制在模具或者模板上,并通过一定方法将纤维与基体材料结合在一起,形成复合材料制品的过程。
纤维绕制复合材料的工艺包括以下几个步骤:
1. 纤维绕制:根据设计要求,将纤维按一定方向和规律绕制在模具或模板上。
常见的绕制方法有手工绕制、机械绕制和自动化绕制等。
2. 纤维堆积:绕制好的纤维在模具或模板上堆积起来,形成预定的厚度和形状。
可以通过手工堆积、机械压制或真空吸附等方法实现。
3. 树脂浸渗:将树脂或者粘合剂涂覆在纤维堆积体上。
树脂会浸渗到纤维之间,填充空隙,并与纤维形成结合。
4. 固化:经过树脂浸渗后,通过热固化、化学固化或者紫外线固化等方法,使树脂固化成硬的基体,形成复合材料的成型件。
5. 剥离:将成型件从模具或模板上剥离下来,获取最终的产品。
纤维绕制复合材料的成型原理是通过纤维材料的力学性能来提高材料的强度和刚度,并在弯曲、扭转或拉伸等不同方向上形成不同的力学性能。
通过纤维的绕制方式和树脂的固化方式,可以控制纤维的方向和分布,从而实现对复合材料力学性能的
调控和优化。
纤维绕制复合材料的工艺具有成本低、成型灵活性高、制品尺寸稳定性好等优点,因此在航空航天、汽车、船舶、建筑等领域有着广泛的应用潜力。
复合材料结构及其成型原理
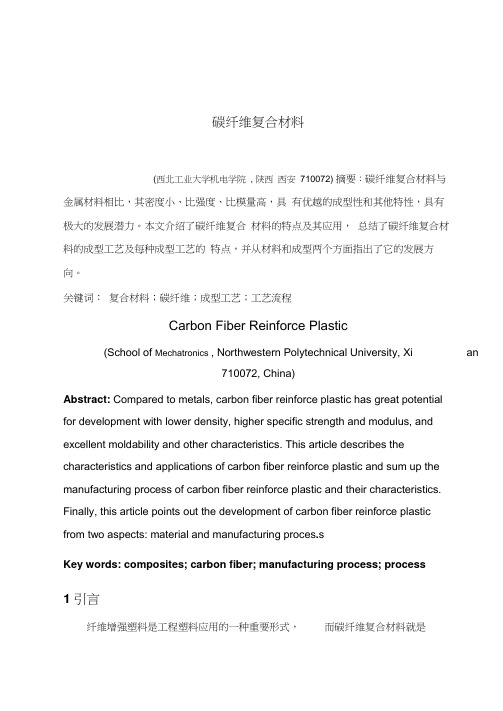
碳纤维复合材料(西北工业大学机电学院, 陕西西安710072) 摘要:碳纤维复合材料与金属材料相比,其密度小、比强度、比模量高,具有优越的成型性和其他特性,具有极大的发展潜力。
本文介绍了碳纤维复合材料的特点及其应用,总结了碳纤维复合材料的成型工艺及每种成型工艺的特点,并从材料和成型两个方面指出了它的发展方向。
关键词:复合材料;碳纤维;成型工艺;工艺流程Carbon Fiber Reinforce Plastic(School of Mechatronics , Northwestern Polytechnical University, Xian710072, China)Abstract: Compared to metals, carbon fiber reinforce plastic has great potentialfor development with lower density, higher specific strength and modulus, and excellent moldability and other characteristics. This article describes the characteristics and applications of carbon fiber reinforce plastic and sum up the manufacturing process of carbon fiber reinforce plastic and their characteristics. Finally, this article points out the development of carbon fiber reinforce plasticfrom two aspects: material and manufacturing proces.sKey words: composites; carbon fiber; manufacturing process; process1引言纤维增强塑料是工程塑料应用的一种重要形式,而碳纤维复合材料就是其中的佼佼者,它以其所具有的低密度、高比强度、高比模量和优越的成型性和其他物理、化学特性在军事、航天、航空、电子等领域被广泛地应用,具有极大的发展潜力。
复合材料制造工艺中的成型原理与模具设计

复合材料制造工艺中的成型原理与模具设计复合材料是由两种或多种不同材料组合而成的材料,具有轻质、高强度、耐腐蚀等优点,在各个领域得到广泛应用。
复合材料制造过程中的成型原理和模具设计起着至关重要的作用。
本文将探讨复合材料制造工艺中的成型原理以及与之相关的模具设计。
一、复合材料成型原理复合材料在成型过程中,可以选择多种方法,如手工制作、模压、拉伸成型、注塑等。
不同的成型原理适用于不同类型的复合材料。
下面将介绍几种常见的成型原理:1. 手工制作手工制作是一种常见的成型方法,适用于简单形状的复合材料制作。
成型过程中,可以使用刷涂法、浸渍法或者层叠法进行。
手工制作的优点是工艺简单,无需复杂的模具,适用于小批量生产或者样品制作。
2. 模压模压是一种常用的复合材料成型方法,适用于制作平面或者简单曲面的构件。
在模压过程中,需要将预浸料或者干布层叠压入模具中,然后通过压力和热固化使其成型。
模压可以分为开模压和闭模压两种形式,根据需要选择合适的模具。
3. 拉伸成型拉伸成型是制作复合材料板材或者管道的常用方法。
在拉伸成型过程中,需要将预浸料或者预浸布放置在拉伸机上,通过牵引力将其拉伸至所需尺寸,并通过加热或者热固化使其固化。
拉伸成型的优点是能够制作出较大的尺寸构件,并且具有较好的力学性能。
4. 注塑注塑是一种常见的成型方法,主要适用于复材的小型构件。
在注塑过程中,需要将预浸料加热至熔融状态,然后通过注射机将熔融料注入模具中,经过冷却固化成型。
注塑具有高效率、高精度的特点,可以制作出复杂形状的构件。
二、复合材料模具设计模具设计是复合材料制造中的重要环节,合理设计的模具能够提高生产效率和成品质量。
以下是一些常见的模具设计原则:1. 合理选择材料模具的选择应根据复合材料的成型温度、压力和化学性质等因素综合考虑。
模具材料应具有良好的耐热性、耐腐蚀性和机械强度,在长期高温、高压和化学介质的作用下不发生变形和破裂。
2. 确定模具结构模具结构的设计要考虑到复合材料的成型工艺和构件的尺寸要求。
复合材料----复合材料的复合原理及界面

复合材料
第二章复合材料的复合原理及界面
1、弥散增强和颗粒增强的原理
1)弥散增强:复合材料是由弥散颗粒与基体复合而成,荷载主要由基体承担,弥散微粒阻碍基体的位错运动,微粒阻碍基体位错运动能力越大,增强效果愈大,微粒尺寸越小,体积分数越高,强化效果越好。
2)颗粒增强:复合材料是由尺寸较大(直径大于1 m)颗粒与基体复合而成,载荷主要由基体承担,但增强颗粒也承受载荷并约束基体的变形,颗粒阻止基体位错运动的能力越大,增强效果越好;颗粒尺寸越小,体积分数越高,颗粒对复合材料的增强效果越好。
2、什么是混合法则,其反映什么规律
混合法则(复合材料力学性能同组分之间的关系):σc=σf V f+σm V m,E c=E f V f+E m V m式中σ为应力,E为弹性模量,V 为体积百分比,c、m和f 分别代表复合材料、基体和纤维;反映的规律:纤维基体对复合材料平均性能的贡献正比于它们各自的体积分数。
3、金属基复合材料界面及改性方法有哪些
金属基复合材料界面结合方式:
①化学结合
②物理结合
③扩散结合
④机械结合。
界面改性方法:
①纤维表面改性及涂层处理;
②金属基体合金化;
③优化制备工艺方法和参数。
4、界面反应对金属基复合材料有什么影响
界面反应和反应程度(弱界面反应、中等程度界面反应、强界面反应)决定了界面的结构和性能,其主要行为有:
①增强了金属基体与增强体界面的结合强度;
②产生脆性的界面反应产物;
③造成增强体损伤和改变基体成分。
热固性复合材料成型工艺

(2)过氯乙烯脱模剂 配方:过氯乙烯粉5~10份 甲苯+丙酮(1:1)95~90份 按比例将物料与溶剂混和搅拌,放入密闭容器中(不
能用塑料容器)等完全溶解后即可使用。 (3)聚苯乙烯溶液脱模剂
配方:聚苯乙烯粉 5份 甲苯 95份
称量混合,搅拌均匀后,密封放置7天左右,若完全溶 解,搅拌均匀即可使用。
缺点:
劳动密集型的成型方法,生产效率低—喷射成型工艺 制品质量与操作者的技术水平有关 生产周期长 制品力学性能较其他方法低—袋压成型工艺
原材料
玻璃纤维及其织物
选择依据:容易被树脂浸润 有较好的形变性 满足制品的性能要求 价格便宜
种类:无捻粗纱 无捻粗纱布 短切原丝毡 加捻布 玻璃布袋
MPa
袋压成型工艺
装袋 固化
复合材料夹层结构的制造
概述
夹层结构有两层薄而高强度的面板材料,其间夹着一层 厚而轻质的芯材,是为了满足轻质高强要求发展起来的 一种结构形式。
面板材料:复合材料板、塑料板、铝板、胶合板等 夹芯材料:蜂窝芯材、泡沫塑料、强芯毯、软木等 优点:比强度高,表面光洁,结构稳定性好,承载能力
模具的结构形式
模具的结构
单模 阳模 对模 阴模
拼装模
❖ 模具材料选择:
(1)木材
要求均质、无节。常用红松、银杏、枣木等。木材模 具表面需要封孔处理。其特点是质轻、易加工;但不耐久 。适合于小批量生产小型制品。
(2)石膏
用半水石膏成型。制造简便,造价低;不耐用,怕冲 击,适合于小批量生产形状复杂的制品。
原材料:⑴模具用胶衣树脂:①固化放热和收缩小; ②优异的耐断裂、耐冲击性能;③优良的耐 热性、光泽度和硬度;④良好的涂刷性;⑤ 与制品胶衣色调相反 ⑵增强层树脂:①固化收缩率小;②韧性好; ③有易操作的黏度;④耐热性好
复合材料低温成型工艺
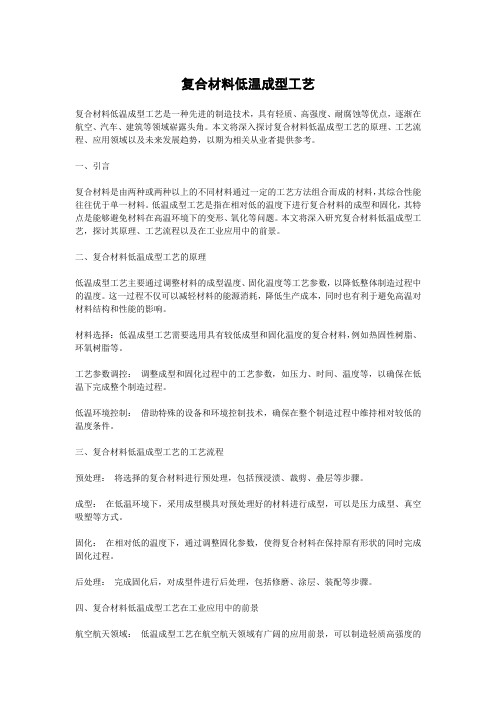
复合材料低温成型工艺复合材料低温成型工艺是一种先进的制造技术,具有轻质、高强度、耐腐蚀等优点,逐渐在航空、汽车、建筑等领域崭露头角。
本文将深入探讨复合材料低温成型工艺的原理、工艺流程、应用领域以及未来发展趋势,以期为相关从业者提供参考。
一、引言复合材料是由两种或两种以上的不同材料通过一定的工艺方法组合而成的材料,其综合性能往往优于单一材料。
低温成型工艺是指在相对低的温度下进行复合材料的成型和固化,其特点是能够避免材料在高温环境下的变形、氧化等问题。
本文将深入研究复合材料低温成型工艺,探讨其原理、工艺流程以及在工业应用中的前景。
二、复合材料低温成型工艺的原理低温成型工艺主要通过调整材料的成型温度、固化温度等工艺参数,以降低整体制造过程中的温度。
这一过程不仅可以减轻材料的能源消耗,降低生产成本,同时也有利于避免高温对材料结构和性能的影响。
材料选择:低温成型工艺需要选用具有较低成型和固化温度的复合材料,例如热固性树脂、环氧树脂等。
工艺参数调控:调整成型和固化过程中的工艺参数,如压力、时间、温度等,以确保在低温下完成整个制造过程。
低温环境控制:借助特殊的设备和环境控制技术,确保在整个制造过程中维持相对较低的温度条件。
三、复合材料低温成型工艺的工艺流程预处理:将选择的复合材料进行预处理,包括预浸渍、裁剪、叠层等步骤。
成型:在低温环境下,采用成型模具对预处理好的材料进行成型,可以是压力成型、真空吸塑等方式。
固化:在相对低的温度下,通过调整固化参数,使得复合材料在保持原有形状的同时完成固化过程。
后处理:完成固化后,对成型件进行后处理,包括修磨、涂层、装配等步骤。
四、复合材料低温成型工艺在工业应用中的前景航空航天领域:低温成型工艺在航空航天领域有广阔的应用前景,可以制造轻质高强度的结构件,提高航空器性能。
汽车制造:在汽车制造中,低温成型工艺可以用于制造车身结构、内饰件等,降低整车重量,提高燃油效率。
建筑领域:低温成型工艺可以制造建筑中的结构件、外墙板材等,具有耐腐蚀、耐候性好的特点,增加建筑材料的寿命。
复合材料成型新工艺——热胀成型法
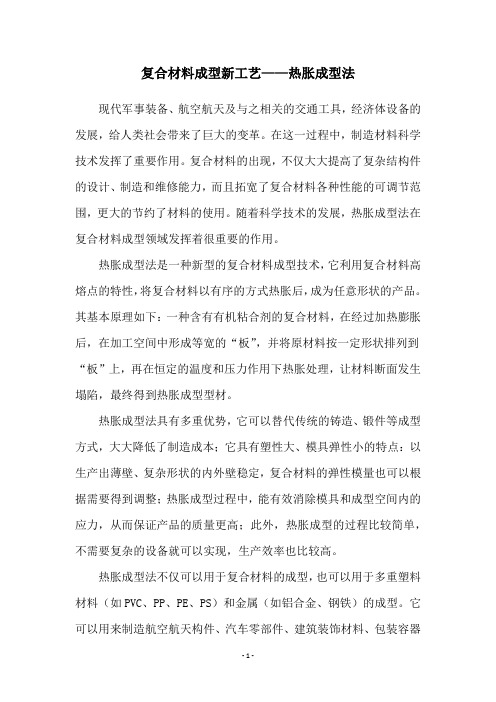
复合材料成型新工艺——热胀成型法现代军事装备、航空航天及与之相关的交通工具,经济体设备的发展,给人类社会带来了巨大的变革。
在这一过程中,制造材料科学技术发挥了重要作用。
复合材料的出现,不仅大大提高了复杂结构件的设计、制造和维修能力,而且拓宽了复合材料各种性能的可调节范围,更大的节约了材料的使用。
随着科学技术的发展,热胀成型法在复合材料成型领域发挥着很重要的作用。
热胀成型法是一种新型的复合材料成型技术,它利用复合材料高熔点的特性,将复合材料以有序的方式热胀后,成为任意形状的产品。
其基本原理如下:一种含有有机粘合剂的复合材料,在经过加热膨胀后,在加工空间中形成等宽的“板”,并将原材料按一定形状排列到“板”上,再在恒定的温度和压力作用下热胀处理,让材料断面发生塌陷,最终得到热胀成型型材。
热胀成型法具有多重优势,它可以替代传统的铸造、锻件等成型方式,大大降低了制造成本;它具有塑性大、模具弹性小的特点:以生产出薄壁、复杂形状的内外壁稳定,复合材料的弹性模量也可以根据需要得到调整;热胀成型过程中,能有效消除模具和成型空间内的应力,从而保证产品的质量更高;此外,热胀成型的过程比较简单,不需要复杂的设备就可以实现,生产效率也比较高。
热胀成型法不仅可以用于复合材料的成型,也可以用于多重塑料材料(如PVC、PP、PE、PS)和金属(如铝合金、钢铁)的成型。
它可以用来制造航空航天构件、汽车零部件、建筑装饰材料、包装容器等各种产品,为人类生活带来巨大贡献。
热胀成型技术的发展还有很多改进的空间,表面涂层技术和模具设计技术的深入应用,可以更大的拓展热胀成型的使用范围,更大的提升产品的性能,为人类是无穷的贡献。
综上所述,热胀成型法可以用于复合材料和各种塑料材料,并且它的特点是易于成型、低成本、高生产效率等优点,正在广泛应用于航空航天构件、汽车零部件、建筑装饰材料、包装容器等等,为人类社会带来了巨大发展。
未来,热胀成型技术将发展得更快,为人类社会的更多领域作出更多的贡献。
多腔室复合材料结构件的气囊整体成型研究

多腔室复合材料结构件的气囊整体成型研究引言多腔室复合材料结构件是一种在工程应用中广泛使用的轻质高强材料,其制造过程中采用气囊整体成型技术能够实现复合材料结构件的良好成型效果。
本文将详细探讨多腔室复合材料结构件的气囊整体成型技术在制造过程中的关键问题和改进方法。
背景多腔室复合材料结构件是由多个腔室组成的结构体,以提供更好的结构刚度和耐力。
气囊整体成型是一种先进的制造技术,其基本原理是在复合材料结构件的内部放置气囊,并通过充气或者真空来实现整体成型。
气囊整体成型技术可以提高复合材料结构件的成型质量和生产效率,同时减少工艺复杂度和材料浪费。
气囊整体成型的优势•成型质量高:气囊整体成型过程中,气囊能够对复合材料进行均匀的外界压力施加,以达到更好的成型效果。
•生产效率高:气囊整体成型过程中,由于气囊能够提供内外压力,减少了复合材料结构件的梳理和复合工序,从而提高了生产效率。
•工艺简单:相对于其他制造方法,气囊整体成型的工艺流程较为简单,且适应性强,可适用于多种复合材料结构件的制造。
•材料利用率高:气囊整体成型过程中,气囊能够有效支撑复合材料,避免材料过度挤压或受损,从而提高了材料的利用率。
关键问题与改进方法在多腔室复合材料结构件的气囊整体成型过程中,存在一些关键问题,如气囊布置、成型工艺控制、气囊材料选择等,需要通过改进方法来解决。
气囊布置对于多腔室复合材料结构件,气囊的布置是非常关键的。
合理的气囊布置可以保证气囊能够对复合材料结构件进行均匀的外界压力施加,从而实现整体成型。
改进方法包括以下几点: 1. 根据复合材料结构件的形状和内部腔室的分布,合理确定气囊的形状和尺寸。
2. 采用多个气囊进行布置,以保证整体成型的均匀性。
3. 在气囊与复合材料结构件的接触面加装胶垫或硅胶等材料,增加气囊与复合材料结构件的粘附力,避免气囊在成型过程中移位。
成型工艺控制在气囊整体成型过程中,成型工艺的控制是关键的。
合理的成型工艺控制可以保证复合材料结构件的成型质量。
- 1、下载文档前请自行甄别文档内容的完整性,平台不提供额外的编辑、内容补充、找答案等附加服务。
- 2、"仅部分预览"的文档,不可在线预览部分如存在完整性等问题,可反馈申请退款(可完整预览的文档不适用该条件!)。
- 3、如文档侵犯您的权益,请联系客服反馈,我们会尽快为您处理(人工客服工作时间:9:00-18:30)。
碳纤维复合材料(西北工业大学机电学院, 陕西西安710072)摘要:碳纤维复合材料与金属材料相比,其密度小、比强度、比模量高,具有优越的成型性和其他特性,具有极大的发展潜力。
本文介绍了碳纤维复合材料的特点及其应用,总结了碳纤维复合材料的成型工艺及每种成型工艺的特点,并从材料和成型两个方面指出了它的发展方向。
关键词:复合材料;碳纤维;成型工艺;工艺流程Carbon Fiber Reinforce Plastic(School of Mechatronics, Northwes tern Polytechnical University, Xi’an710072, China)Abstract: Compared to metals, carbon fiber reinforce plastic has great potential for development with lower density, higher specific strength and modulus, and excellent moldability and other characteristics. This article describes the characteristics and applications of carbon fiber reinforce plastic and sum up the manufacturing process of carbon fiber reinforce plastic and their characteristics. Finally, this article points out the development of carbon fiber reinforce plastic from two aspects: material and manufacturing process.Key words: composites; carbon fiber; manufacturing process; process1引言纤维增强塑料是工程塑料应用的一种重要形式,而碳纤维复合材料就是其中的佼佼者,它以其所具有的低密度、高比强度、高比模量和优越的成型性和其他物理、化学特性在军事、航天、航空、电子等领域被广泛地应用,具有极大的发展潜力。
尤其是在航空领域,碳纤维复合材料构件是航空航天结构中重要的组成部分,常用于飞机的内部骨架以及发动机等零件的固定支架。
所以,进一步研究碳纤维复合材料对发展我国制造业尤其是航空制造业具有重要的意义。
本文从碳纤维复合材料的特点及其应用出发,总结了它的成型工艺及每种成型工艺的特点,并从材料和成型两个方面指出了它的发展方向。
2碳纤维复合材料及其应用2.1碳纤维的结构碳纤维主要是由碳元素组成的一种特种纤维,其含碳量随种类不同而异,一般在90%以上。
碳纤维具有一般碳素材料的特性,如耐高温、耐摩擦、导电、导热及耐腐蚀等,但与一般碳素材料不同的是,其外形有显著的各向异性、柔软、可加工成各种织物,沿纤维轴方向表现出很高的强度。
碳纤维比重小,因此有很高的比强度。
碳纤维是由含碳量较高,在热处理过程中不熔融的人造化学纤维,经热稳定氧化处理、碳化处理及石墨化等工艺制成的。
碳纤维是一种力学性能优异的新材料,它的比重不到钢的1/4,碳纤维树脂复合材料抗拉强度一般都在3500Mpa 以上,是钢的7~9倍,抗拉弹性模量为23000~43000Mpa亦高于钢。
因此CFRP的比强度即材料的强度与其密度之比可达到2000Mpa/(g/cm3)以上,而A3钢的比强度仅为59Mpa/(g/cm3)左右,其比模量也比钢高。
与此同时,其力学性能又是其它纤维无法比拟的。
表l给出了碳纤维的力学性能与其它种类纤维的比较。
表1 碳纤维与其它纤维力学性能的比较纤维种类 密度3/cm g 拉伸强度GPa 拉伸弹性模量GPa 性能高强碳纤维 1.50 5.70 280 质轻、高强,大丝束成本低聚乙烯纤维 0.97 2.59 120 超高分子量玄武岩纤维 2.80 3.00~4.80 79~93 耐酸碱,耐高温,密度大E-玻璃纤维 2.55 3.40 72.40 主流增强材料,密度大,模量偏低,耐湿热性能较差 S-玻璃纤维 2.50 4.50 86.92.2 碳纤维复合材料尽管碳纤维可单独使用发挥,但它毕竟属于脆性材料,只有将它与基体材料牢固地结合在一起时,才能有效地发挥其优异的力学性能。
因此,碳纤维可用作复合材料中的增强相[2] ,以提高产品得强度、减轻结构的质量、延长使用寿命和增加安全可靠性。
因此,从国防军工到民用工业,包括航空航天、土木建筑、交通运输等领域,碳纤维复合材料都获得了进一步的应用。
碳纤维在复合材料中用作增强材料时,根据使用目的不同可选用不同的基体材料和复合方式达到要求的复合效果。
碳纤维可用来增强树脂、水泥、橡胶、碳、金属等,而目前使用最多、最广泛的就是树脂基复合材料。
在碳纤维增强树脂基复合材料中,碳纤维起到增强作用,而树脂基体则使复合材料成型为承载外力的整体,并通过界面传递载荷于碳纤维。
所用基体树脂主要分为两大类,一类是热固性树脂(Thermo settings ,TS),另一类是热塑性树脂(Thermo plastics,TP)。
热固性树脂由反应性、低分子量预聚体或带有活性基团高分子量聚合物组成。
成型过程中,在固化剂或热作用下进行交联、缩聚,形成不熔不溶的交联体型结构。
常用的有环氧树脂、酚醛树脂、双马来亚酰胺树脂等。
热塑性树脂由线型高分子量聚合物组成,在一定条件下溶解和熔融,只发生物理变化。
常用的有聚乙烯、尼龙、聚醚醚酮等。
2.3碳纤维复合材料的应用碳纤维的主要用途是与树脂、金属、陶瓷等基体复合,制成结构材料。
碳纤维增强环氧树脂复合材料,其比强度、比模量综合指标,在现有结构材料中是最高的。
在密度、刚度、重量、疲劳特性等有严格要求的领域,在要求高温、化学稳定性高的场合,碳纤维复合材料都颇具优势。
碳纤维是50年代初应火箭、宇航及航空等尖端科学技术的需要而产生的,现在还广泛应用于体育器械、纺织、化工机械及医学领域。
随着尖端技术对新材料技术性能的要求日益苛刻,促使科技工作者不断努力提高。
80年代初期,高性能及超高性能的碳纤维相继出现,这在技术上是又一次飞跃,同时也标志着碳纤维的研究和生产已进入一个高级阶段。
由碳纤维和环氧树脂结合而成的复合材料,由于其比重小、刚性好和强度高而成为一种先进的航空航天材料。
因为航天飞行器的重量每减少1公斤,就可使运载火箭减轻500公斤。
所以,在航空航天工业中争相采用先进复合材料。
有一种垂直起落战斗机,它所用的碳纤维复合材料已占全机重量的1/4,占机翼重量的1/3。
据报道,美国航天飞机上3只火箭推进器的关键部件以及先进的MX导弹发射管等,都是用先进的碳纤维复合材料制成的。
现在的F1(世界一级方程锦标赛)赛车,车身大部分结构都用碳纤维材料。
顶级跑车的一大卖点也是周身使用碳纤维,用以提高气动性和结构强度碳纤维可加工成织物、毡、席、带、纸及其他材料。
传统使用中碳纤维除用作绝热保温材料外,一般不单独使用,多作为增强材料加入到树脂、金属、陶瓷、混凝土等材料中,构成复合材料。
碳纤维增强的复合材料可用作飞机结构材料、电磁屏蔽除电材料、人工韧带等身体代用材料以及用于制造火箭外壳、机动船、工业机器人、汽车板簧和驱动轴等。
表2为碳纤维的重点开发应用领域;图2为最近几年世界碳纤维的需求量;图3为世界碳纤维按应用领域需求的统计和预测。
表2 碳纤维的重点开发应用领域图2 世界碳纤维的需求量图3 世界碳纤维按应用领域需求的统计3碳纤维复合材料成型工艺成型工艺是将原材料转化为结构件的关键工艺步骤。
碳纤维复合材料的加工成型工艺很多,不同的成型加工技术对制品的性能会带来较大的影响。
目前常用的碳纤维复合材料加工成型工艺主要有:手糊成型(Hand Laying-up)、喷射成型(Spray Moulding)、真空袋成型法、团状模塑料(Dough Molding Compound,DMC)成型、片状模塑料(Sheet Molding Compound,SMC)成型、层压成型(Lamination Process)、热膨胀成型、树脂传递模塑成型(Resin Transfer Molding,RTM)、缠绕成型(Winding Process)、反应注射成型(Reaction Injection Molding,RIM)和拉挤成型(Puhrusion Process)等。
本文重点介绍手糊成型工艺、真空袋成型工艺、热膨胀成型工艺、拉挤成型工艺、RTM成型工艺模压成型工艺。
3.1手糊成型手糊成型[3]是指在模具型腔表面涂布或铺迭脱模剂、胶衣、粘度适中的树脂(胶衣凝胶后涂覆)和碳纤维,手持辊子或刷子使环氧树脂浸渍碳纤维,并驱除气泡,压实基层。
铺层操作反复多次,直到达到制品的设计厚度。
具体工艺流程如图4所示。
图4 手糊成型流程图该工艺的主要优点是:可室温成型;设备投资少,模具折旧费低;上马快,技术较易掌握;无论构件尺度大小,造型如何复杂,都可以制作出来。
主要缺点是:属于劳动密集型生产,制品质量由工人技术熟练程度决定;手糊用树脂分子量低,通常可能较分子量高的树脂对人的健康和安全有害。
3.2真空袋成型真空袋成型法是指在环氧树脂固化时,通过抽真空的方式使袋内复合材料坯件受到均匀压力来制备复合材料制品的成型方法。
其过程为:将手糊或喷射好的积层在环氧树脂的A阶段与模具在一起,在积层上覆以真空袋,周边密封,然后抽真空形成负压,大气通过真空袋对毛坯加压,使积层受到不大于101 kPa的压力而被压实、成型。
真空袋用延展性好、强度高的尼龙膜等材料制成,用粘性的密封胶条与模具粘结在一起,真空袋内通常要放有导气毡以使真空通路畅通。
固化完全后卸模取出制件。
真空袋法封装示意图如图5所示。
图5真空袋法封装示意图其工艺流程如图6所示。
图6 真空袋成型工艺流程图真空袋成型工艺简单,不需要专用设备,常用来制造室温固化的制件,也可在固化炉内成型高、中温的制件。
由于真空袋法产生的压力小,较适用于环氧和聚酯树脂,通常可获得高碳纤维含量的复合材料,碳纤维可较好地浸渍环氧树脂,制出的制品表面光滑,精度较高。
主要缺点是额外的工艺过程增加了劳动力和成本,并且要求操作人员有较高的技术水平;生产效率不高[56] 。
3.3热膨胀成型热膨胀工艺是指复合材料预浸料在闭合刚性阴模中通过硅橡胶芯模的热膨胀来实现对复合材料加压固化的成型工艺方法。
它以热膨胀系数较大的材料为芯模,刚体材料为阴模,复合材料置于芯模与阴模之间。