关键过程质量控制程序
关键工序质量控制制度
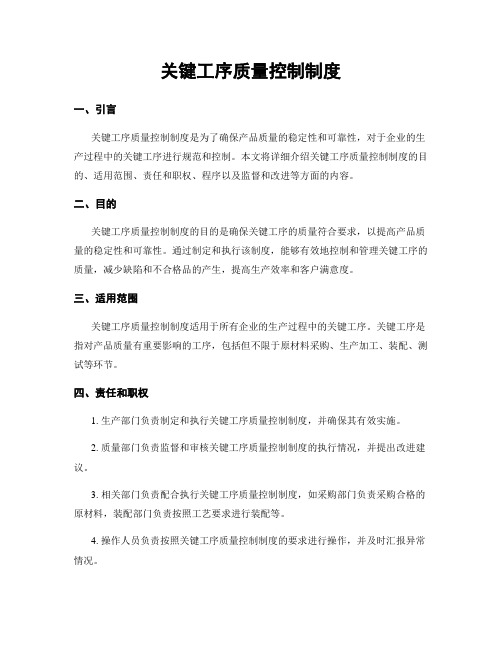
关键工序质量控制制度一、引言关键工序质量控制制度是为了确保产品质量的稳定性和可靠性,对于企业的生产过程中的关键工序进行规范和控制。
本文将详细介绍关键工序质量控制制度的目的、适用范围、责任和职权、程序以及监督和改进等方面的内容。
二、目的关键工序质量控制制度的目的是确保关键工序的质量符合要求,以提高产品质量的稳定性和可靠性。
通过制定和执行该制度,能够有效地控制和管理关键工序的质量,减少缺陷和不合格品的产生,提高生产效率和客户满意度。
三、适用范围关键工序质量控制制度适用于所有企业的生产过程中的关键工序。
关键工序是指对产品质量有重要影响的工序,包括但不限于原材料采购、生产加工、装配、测试等环节。
四、责任和职权1. 生产部门负责制定和执行关键工序质量控制制度,并确保其有效实施。
2. 质量部门负责监督和审核关键工序质量控制制度的执行情况,并提出改进建议。
3. 相关部门负责配合执行关键工序质量控制制度,如采购部门负责采购合格的原材料,装配部门负责按照工艺要求进行装配等。
4. 操作人员负责按照关键工序质量控制制度的要求进行操作,并及时汇报异常情况。
五、程序1. 制定关键工序质量控制制度:生产部门根据产品的特点和工艺要求,制定关键工序质量控制制度,并报批相关部门。
2. 培训和宣贯:生产部门组织相关人员进行关键工序质量控制制度的培训,并进行宣贯工作,确保所有操作人员理解和遵守该制度。
3. 实施关键工序质量控制制度:操作人员按照关键工序质量控制制度的要求进行操作,包括原材料检验、生产过程控制、装配过程控制、测试和检验等。
4. 异常处理:如果在关键工序中发现异常情况,操作人员应立即停止操作,并及时向上级汇报,由质量部门进行处理和分析,找出问题的原因并提出改进措施。
5. 记录和报告:操作人员应按照要求进行记录和报告,包括关键工序的质量数据、异常情况和处理结果等,以便后续的追溯和分析。
六、监督和改进1. 监督:质量部门定期对关键工序质量控制制度的执行情况进行监督和审核,包括现场检查、数据分析和人员培训等。
关键过程质量控制程序

关键过程质量控制程序关键过程质量控制程序1.介绍1.1 目的该文档旨在制定关键过程质量控制程序,确保组织在关键过程中能够持续提供高质量的产品和服务。
1.2 适用范围和参与者本程序适用于所有涉及组织关键过程的部门和员工。
所有关键过程的质量控制都必须按照该程序执行。
2.定义和缩写2.1 关键过程关键过程是指对组织产品和服务质量有重要影响的核心业务过程。
2.2 缩写●QC: 质量控制●SOP: 标准操作程序●KPI: 关键绩效指标3.关键过程识别和分类3.1 关键过程识别①组织需对所有业务过程进行分析和评估,以确定哪些过程属于关键过程。
②评估关键过程的标准包括对影响产品质量、客户满意度和企业效益等因素的分析。
3.2 关键过程分类①根据过程的功能和目标,将关键过程分为几个分类,例如生产过程、供应链过程、客户服务过程等。
②具体的分类方法应根据组织的实际情况进行确定。
4.关键过程质量控制流程4.1 流程概述关键过程质量控制流程包括关键过程规划、质量控制方案制定、质量控制实施、质量数据分析和改进。
4.2 关键过程规划①确定关键过程的质量目标和质量指标。
②制定关键过程的SOP,明确质量控制流程和责任。
4.3 质量控制方案制定①根据关键过程的特点,制定相应的质量控制方案。
②确定质量控制活动的频率和方法,制定相应的检查标准和抽样计划。
4.4 质量控制实施①按照质量控制方案执行质量控制活动。
②收集质量数据,记录和报告关键过程质量指标。
4.5 质量数据分析①分析质量数据,评估关键过程的质量状况。
②根据分析结果,识别质量问题和改进机会。
4.6 改进①制定改进计划,包括纠正措施和预防措施。
②实施改进措施,并记录改进过程和效果。
5.相关附件6.法律名词及注释●质量法规:法律对产品和服务质量的要求和规定。
●ISO 9001:国际标准化组织制定的质量管理体系标准。
食品生产关键质量控制点操作控制程序

食品生产关键质量控制点操作控制程序食品生产的关键质量控制点非常重要,可以保证产品的质量和安全。
在食品生产的过程中,不同的生产环节都存在着关键质量控制点,需要在每个环节中都建立相应的操作控制程序,进行严格的管理和控制,以确保整个生产过程的质量和安全。
以下是一份针对食品生产的关键质量控制点操作控制程序,包含以下几个方面:1.原材料采购控制在采购原材料时,必须严格按照公司的采购标准及要求对供应商进行评估,并对供应商的产品质量进行检测。
对于每次采购的原材料,都必须建立入库检验程序,包括质量检测和数量检测。
进行检测的同时,还要记录和保留检测结果,以便后续使用。
2.生产过程控制在生产过程中,需要对每个关键环节建立严格的操作控制程序,确保每个步骤都符合公司制定的标准。
比如,在加工中应该使用标准的生产设备,并且要进行日常维护;在制作过程中需要严格控制温度、湿度等因素,以保证产品质量和安全。
此外,在生产过程中还需要对关键参数进行检测和监控,如温度、压力、湿度、pH值等,以确保生产出的产品符合质量要求。
针对生产中常见的问题,还需要建立相应的纠正和预防控制措施。
3.包装和贮存控制在食品生产过程中,包装和贮存环节也非常关键,建立严格的操作控制程序是必须的。
对于包装材料,需要检查其质量是否合格,对每批产品都要进行严格的质量检测。
在贮存过程中,必须注意存储条件,如温度、湿度、通风等,以保证产品的质量。
对于不同的产品,还需要制定相应的贮存期限和贮存方法。
4.产品检测在生产过程结束后,还需要对产品进行最终检测,确保产品符合质量标准。
针对不同的产品,需要制定相应的检测方法和标准。
对于检测结果不合格的产品,必须按照公司制定的程序进行处理,并进行相应的改进。
以上是针对食品生产的关键质量控制点操作控制程序,通过建立这些程序和措施,可以确保产品的质量和安全,提高消费者对产品的信任和满意度。
关键工序质量控制点控制程序

中铁十一局集团桥梁有限公司咸安制梁场关键质量控制点控制程序《关键质量控制点控制程序》主要包括下列内容:1、目的2、适用范围 03、主要引用标准 04、箱梁预制关键质量控制点 04.1箱梁预制的关键质量点 04。
2关键质量控制要点 04.2.1 钢筋闪光对焊施工质量控制点 04.2。
2预应力孔道及保护层厚度控制 (1)4.2.2.1预应力孔道控制 (1)4.2.2。
2保护层厚度控制 (1)4。
2.3混凝土施工质量控制点 (2)4.2。
3。
1原材料控制 (2)4.2。
3.2计量控制 (2)4。
2。
3。
3浇筑检查 (2)4.2。
3。
4取样检查 (2)4。
2.3.5混凝土入模温度控制 (3)4。
2.3.6混凝土浇筑控制 (3)4.2.3.7混凝土养护检查 (3)4.2.3。
8混凝土养护控制 (4)4.2。
3。
9模板检验控制程序 (4)4.2.4张拉质量控制要点控制程序 (4)4。
2.4。
1钢绞线及相关附件 (4)4.2。
4。
2钢绞线数目 (5)4。
2。
4。
3油压千斤顶与油表校正报告 (5)4。
2.4.4后张法预应力施张检查 (5)4.2.4。
5梁体变形检查 (5)4.2.5管道压浆施工质量控制要点控制程序 (5)4。
2.5.1原材料控制 (5)4.2.5。
2计量控制 (5)4.2。
5.3施工检查 (6)4。
2.5。
4取样检查 (6)关键质量控制点控制程序1、目的通过本程序和相关文件的控制旨在对箱梁预制施工各关键质量控制点的施工进行有效的控制、管理和改进,以确保产品符合设计要求,达到预期的质量目标,满足工程质量总目标的要求。
2、适用范围本程序适用于中铁十一局集团桥梁有限公司咸安制梁场箱梁预制施工全过程。
3、主要引用标准TB10210-2001《铁路混凝土与砌体工程施工规范》JGJ18-2003《钢筋焊接及验收规程》TB10415—2007《铁路桥涵工程施工质量验收标准》TB10424—2007《铁路混凝土与砌体工程施工质量验收标准》科技基[2005]101号《客运专线高性能混凝土暂行技术条件》客运专线预应力混凝土预制梁暂行技术条件企业内控标准4、箱梁预制关键工序及质量控制点4.1 箱梁预制的关键工序箱梁预制施工的关键工序有:钢筋闪光对焊;预应力孔道及保护层;混凝土配制、拌和、浇筑、养护、强度;张拉;管道压浆.以上工序只能依据依时间、仪器、仪表、试验报告等判定并由具有合格资质的人员进行作业。
质量控制程序
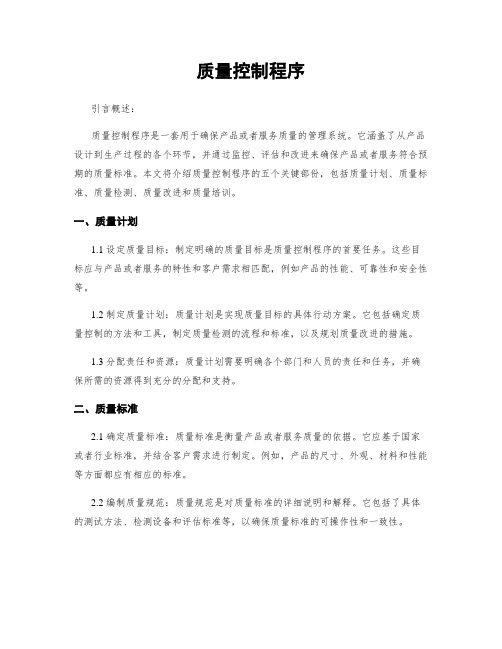
质量控制程序引言概述:质量控制程序是一套用于确保产品或者服务质量的管理系统。
它涵盖了从产品设计到生产过程的各个环节,并通过监控、评估和改进来确保产品或者服务符合预期的质量标准。
本文将介绍质量控制程序的五个关键部份,包括质量计划、质量标准、质量检测、质量改进和质量培训。
一、质量计划1.1 设定质量目标:制定明确的质量目标是质量控制程序的首要任务。
这些目标应与产品或者服务的特性和客户需求相匹配,例如产品的性能、可靠性和安全性等。
1.2 制定质量计划:质量计划是实现质量目标的具体行动方案。
它包括确定质量控制的方法和工具,制定质量检测的流程和标准,以及规划质量改进的措施。
1.3 分配责任和资源:质量计划需要明确各个部门和人员的责任和任务,并确保所需的资源得到充分的分配和支持。
二、质量标准2.1 确定质量标准:质量标准是衡量产品或者服务质量的依据。
它应基于国家或者行业标准,并结合客户需求进行制定。
例如,产品的尺寸、外观、材料和性能等方面都应有相应的标准。
2.2 编制质量规范:质量规范是对质量标准的详细说明和解释。
它包括了具体的测试方法、检测设备和评估标准等,以确保质量标准的可操作性和一致性。
2.3 更新和改进标准:质量标准应与市场需求和技术进步相适应,定期进行评估和更新。
同时,对于存在质量问题的产品或者服务,应及时改进标准以提高质量水平。
三、质量检测3.1 确定检测方法:根据产品或者服务的特性,确定适合的质量检测方法。
例如,对于电子产品可以采用功能测试、可靠性测试和环境测试等方法。
3.2 设计检测流程:制定质量检测的具体流程和步骤,包括样品的选取、测试的频率和检测的标准等。
同时,确保检测设备的准确性和可靠性。
3.3 进行质量检测:按照设定的检测流程进行质量检测,并记录和分析检测结果。
对于不合格的产品或者服务,及时采取纠正措施以防止质量问题的扩大。
四、质量改进4.1 分析质量问题:对于浮现的质量问题,进行详细的分析和调查,找出问题的原因和影响因素。
关键过程控制程序
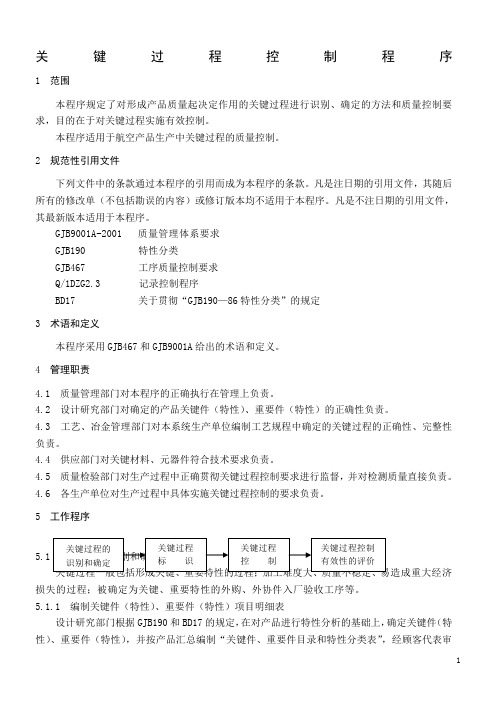
关键过程控制程序1 范围本程序规定了对形成产品质量起决定作用的关键过程进行识别、确定的方法和质量控制要求,目的在于对关键过程实施有效控制。
本程序适用于航空产品生产中关键过程的质量控制。
2 规范性引用文件下列文件中的条款通过本程序的引用而成为本程序的条款。
凡是注日期的引用文件,其随后所有的修改单(不包括勘误的内容)或修订版本均不适用于本程序。
凡是不注日期的引用文件,其最新版本适用于本程序。
GJB9001A-2001 质量管理体系要求GJB190 特性分类GJB467 工序质量控制要求Q/1DZG2.3 记录控制程序BD17 关于贯彻“GJB190—86特性分类”的规定3 术语和定义本程序采用GJB467和GJB9001A给出的术语和定义。
4 管理职责4.1 质量管理部门对本程序的正确执行在管理上负责。
4.2 设计研究部门对确定的产品关键件(特性)、重要件(特性)的正确性负责。
4.3 工艺、冶金管理部门对本系统生产单位编制工艺规程中确定的关键过程的正确性、完整性负责。
4.4 供应部门对关键材料、元器件符合技术要求负责。
4.5 质量检验部门对生产过程中正确贯彻关键过程控制要求进行监督,并对检测质量直接负责。
4.6 各生产单位对生产过程中具体实施关键过程控制的要求负责。
5 工作程序损失的过程;被确定为关键、重要特性的外购、外协件入厂验收工序等。
5.1.1 编制关键件(特性)、重要件(特性)项目明细表设计研究部门根据GJB190和BD17的规定,在对产品进行特性分析的基础上,确定关键件(特性)、重要件(特性),并按产品汇总编制“关键件、重要件目录和特性分类表”,经顾客代表审签同意后归档分发给各生产单位和工艺管理、冶金管理、质量管理、质量检验、供应等部门及顾客代表。
5.1.2 编制关键、重要外购器材项目表供应部门根据设计研究部门编发的“关键件、重要件目录和特性分类表”和产品图样,对确定为关键特性、重要特性的外购器材,汇总编制“关键、重要外购器材项目表”,复制分发质量管理、质量检验、冶金管理部门和顾客代表。
生产过程质量控制程序

生产过程质量控制程序一、引言生产过程质量控制程序是为了确保产品质量的稳定性和一致性而制定的一套标准化操作流程。
本文将详细介绍生产过程质量控制程序的各个环节和步骤,以确保产品的质量符合预期要求。
二、质量控制流程1. 前期准备在开始生产前,需要进行充分的前期准备工作,包括:- 制定生产计划和排程,明确生产目标和任务;- 确定生产所需的原材料和设备,并进行采购和检验;- 建立生产过程中所需的各项记录和档案。
2. 原材料检验原材料是产品质量的基础,因此需要对原材料进行严格的检验,包括:- 检查原材料的外观、尺寸、重量等物理特性;- 进行化学成分分析,确保原材料符合产品要求;- 进行必要的机械性能测试,如强度、硬度等。
3. 生产过程控制生产过程控制是确保产品质量稳定的关键环节,包括:- 设定生产工艺参数,如温度、压力、速度等;- 对关键工序进行监控和记录,如注塑、焊接、装配等;- 进行过程中的质量检查,如尺寸、外观、功能等;- 及时调整生产参数,以确保产品质量符合要求。
4. 产品检验与测试在生产过程中,需要对产品进行全面的检验和测试,包括:- 对成品进行外观检查,如表面光洁度、涂层质量等;- 进行尺寸测量,确保产品尺寸符合设计要求;- 进行功能测试,如电气性能、机械性能等;- 进行可靠性测试,如寿命测试、环境适应性测试等。
5. 不合格品处理如果在检验和测试过程中发现不合格品,需要及时处理,包括:- 对不合格品进行分类和记录,如外观不良、尺寸超差等;- 进行原因分析,找出不合格的根本原因;- 采取相应的纠正措施,如调整生产参数、更换原材料等;- 对纠正措施进行验证,确保问题得到解决。
6. 数据分析与改进通过对生产过程中的数据进行分析,可以发现潜在问题并进行改进,包括:- 对生产过程中的各项数据进行统计和分析;- 发现异常数据和趋势,及时采取措施进行纠正;- 进行质量管理评审,确定改进措施并制定实施计划;- 对改进措施进行跟踪和验证,确保问题得到解决。
关键过程质量控制程序

关键过程质量控制程序
关键过程质量控制程序是一种通过管理和监控关键过程,以确保产品或服务质量达到预期要求的程序。
以下是一个基本的关键过程质量控制程序的步骤:
1. 确定关键过程:,需要明确哪些过程是整个生产流程中最关键和关键的过程。
这些关键过程对产品或服务的质量有直接影响,需要重点管理和控制。
2. 制定质量标准:制定明确的质量标准,以确定产品或服务需要达到的质量要求。
这些标准可以包括尺寸、外观、性能等方面的要求。
3. 设计质量控制计划:根据关键过程和质量标准,制定详细的质量控制计划。
该计划应包括实施质量检查的时间、方法和责任人员。
4. 实施质量控制措施:按照质量控制计划,执行相应的质量控
制措施。
这包括监督关键过程,确保其按照标准进行操作,并采取
必要的纠正措施。
5. 进行质量检查:定期进行质量检查,以确保关键过程达到质
量要求。
检查可以在关键过程进行时进行,也可以在过程完成后进行。
6. 分析并纠正问题:如果发现关键过程存在问题或不符合质量
要求,需要进行分析,并采取纠正措施。
这可能包括调整过程、修
复设备或重新培训员工等措施。
7. 持续改进:根据质量检查和问题分析的结果,推动持续改进。
通过改善关键过程,提高产品或服务的质量水平。
8. 文档和记录:对于所有的质量控制活动,应进行文档和记录。
这包括记录关键过程的操作和检查结果,以及相关的纠正和改进措施。
以上是一个基本的关键过程质量控制程序的步骤,具体的程序可以根据组织的需求和特定行业的要求进行定制。
- 1、下载文档前请自行甄别文档内容的完整性,平台不提供额外的编辑、内容补充、找答案等附加服务。
- 2、"仅部分预览"的文档,不可在线预览部分如存在完整性等问题,可反馈申请退款(可完整预览的文档不适用该条件!)。
- 3、如文档侵犯您的权益,请联系客服反馈,我们会尽快为您处理(人工客服工作时间:9:00-18:30)。
Q/KF
KF X X X集团有限公司企业标准
Q/KF·10L·CX715-2011
代替Q/KF·10L727-2007 关键过程质量控制程序
编制:校核:审定:
标准化检查:复审:批准:
2011-07-15发布2011-08-01实施
XXXX集团有限公司发布
Q/KF·10L·CX715-2011
关键过程质量控制程序
1 范围
本程序规定了产品在实现过程中关键过程质量控制要求。
本程序适用于产品试制和生产的关键过程。
2 规范性引用文件
下列文件对于本文件的应用是必不可少的。
凡是注日期的引用文件,仅注日期的版本适用于本文件。
凡是不注日期的引用文件,其最新版本适用于本文件。
GJB467A-2008 生产提供过程质量控制
GJB 909A-2005 关键件和重要件的质量控制
3 术语和定义
3.1 关键过程
对形成产品质量起决定作用的过程。
注:关键过程一般包括形成关键、重要特性的过程;加工难度大、质量不稳定、易造成重大经济损失的过程等。
[GJB 1405A-2006,定义4.1]
4 职责
4.1 工艺部门负责关键过程识别,确定关键工序及关键工序控制点,编制关键工序文件及规定控制方法。
4.2 生产单位负责管理及控制关键工序,设备、采购、检验和人力资源等部门协助实施。
5 工作程序
5.1 关键工序的识别
工艺部门按以下原则对关键过程进行识别:
a)形成关键、重要零部件的关键尺寸、部位的过程;
b)加工难度大,质量不稳定,重复出现质量问题的过程;
c)加工周期长、原材料昂贵,一旦出现不合格品经济损失大的过程;
d)关键、重要零部件的外协、外购件的入厂检验过程;
e)有特殊工艺要求,对下道工序或装配有重大影响的过程。
5.2 关键过程的工艺质量控制
5.2.1 关键过程的工艺规程必须编制《关键工序及管理点明细表》及《关
1
Q/KF·10L·CX715-2011
键工序质量控制卡片》,并经检验部门、质量管理部门会签,必要是顾客代表会签。
5.2.2 《关键工序质量控制卡片》应明确规定控制的项目及具体的控制内容和方法。
5.2.3 关键过程的工艺规程和工序图表应分别加盖“关键工序”的印章。
对有可追溯性的零部件,工艺规程应明确规定标识办法。
5.2.4 关键过程的工艺规程对关键重要尺寸要进行特性标识。
5.3 关键过程质量控制要求
5.3.1 人员的控制:
a)关键过程必须实行“三定”,即定工序、定人员、定设备。
生产单
位填写《关键工序三定卡片》(见附录A),并经工艺部门、人力资
源部门、质量管理部门、设备部门、检验部门认可。
变动时,重
新填写关键工序三定卡片;
b)操作者、检验员应具有适用的知识和专业技能,并熟悉和掌握本
工序的技术要求。
操作者、检验员需经培训、考试合格上岗;
c)操作人员必须严格遵守工艺纪律,认真执行工艺规程,检验人员
严格执行检验规程。
5.3.2 设备的控制:
a)关键过程使用的设备、工艺装备、计量器具必须符合工艺规程规
定,且必须具有合格证明文件并标识,按检定周期检定或校验,
保持其精度;
b)新制造或修理后的设备、工艺装备、计量器具,必须经过试用或
鉴定,确保能保证产品的质量后,方可正式投入使用。
5.3.3 材料的控制:
a)转入本工序的材料(原材料、毛坯、半成品、元器件、零件、组
件、部件、外购件及辅助材料等)必须具有上道工序的检验合格
证明文件;
b)代用材料必须具有按规定程序办理的审批文件。
5.3.4 环境的控制:
a)关键过程的实施场所应有明确的标识,其工作场地的环境条件,
应符合工艺技术文件和现场管理标准的规定;
b)成品、半成品、在制品,应按不同的要求分别摆放在指定位置;2
Q/KF·10L·CX715-2011
返工品、返修品、报废品应及时隔离。
5.3.5 按照工艺文件要求在生产现场设置关键过程控制点,明确关键工序控制项目和要求、控制方法、类型、工具和图表、检测频次和方法以及实施控制的人员,使用必要的设施、设备对过程参数和产品关键或重要特性进行有效监视和控制。
5.3.6 关键过程实行批次管理,并经顾客代表认可。
5.4 检验控制
5.4.1 关键过程应设专职检验员对产品进行检验,并对生产过程进行监督检查,填写控制记录。
5.4.2 严格执行首件自检、专检制度,并填写实测记录。
5.4.3 可行时,对产品关键或重要特性实施百分之百检验,由于产品特点和批量不能实施百分之百检验时,可采取抽样方案或用其它方法验证。
5.5 适用时,运用统计技术识别和确定、控制、改进过程,确保过程满足要求,并进一步提升过程能力。
6 报告及记录
关键工序三定卡片(附录A)。
3
Q/KF·10L·CX715-2011
4
附录A
关键工序三定卡片。