300kA系列电解槽阴极破损的现象_原因及对策
电解槽底部破损与应对
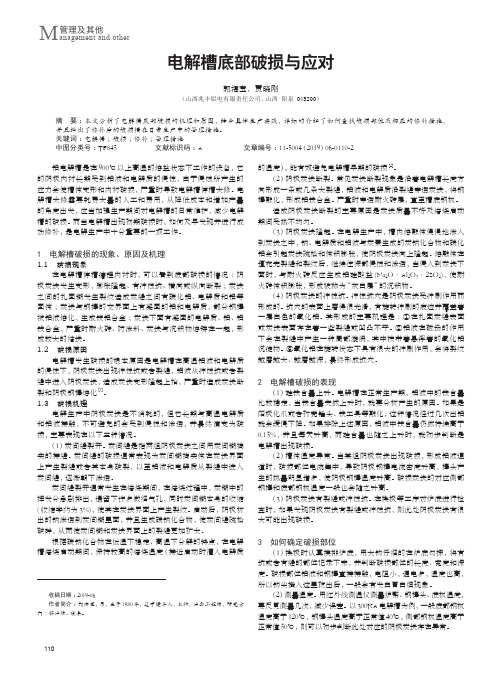
110管理及其他M anagement and other电解槽底部破损与应对郭福宝,贾晓刚(山西兆丰铝电有限责任公司,山西 阳泉 045200)摘 要:本文分析了电解槽底部破损的机理和原因,结合具体生产实践,详细的介绍了如何查找破损部位及相应的修补措施,并且给出了修补后的破损槽在日常生产中的管理措施。
关键词:电解槽;破损;修补;管理措施中图分类号:TF845 文献标识码:A 文章编号:11-5004(2019)06-0110-2收稿日期:2019-06作者简介:郭福宝,男,生于1980年,辽宁建平人,本科,冶金工程师,研究方向:铝冶炼、碳素。
铝电解槽是在900℃以上高温的熔盐状态下工作的设备,它的阴极内衬长期受到铝液和电解质的侵蚀,由于侵蚀所产生的应力会使槽体变形和内衬破损,严重时导致电解槽停槽大修。
电解槽大修需要耗费大量的人工和费用,从降低成本和增加产量的角度出发,应当加强生产期间对电解槽的日常维护,减少电解槽的破损。
而当电解槽出现初期破损时,如何及早发现并进行成功修补,是电解生产中十分重要的一项工作。
1 电解槽破损的现象、原因及机理1.1 破损现象在电解槽停槽清理内衬时,可以看到底部破损的情况:阴极炭块发生变形,膨胀隆起、有冲蚀坑、横向或纵向断裂;炭块之间的扎固糊发生裂纹造成炭缝之间有碳化铝、电解质和铝等固体;炭块与钢棒的交界面上有凝固的铝和电解质,部分钢棒被铝液熔化,生成铁铝合金;炭块下面有凝固的电解质、铝、铝铁合金,严重时耐火砖、防渗料、炭块与沉积物熔铸在一起,形成较大的结块。
1.2 破损原因电解槽发生破损的根本原因是电解槽在高温铝液和电解质的侵蚀下,阴极炭块出现冲蚀坑或者裂缝,铝液从冲蚀坑或者裂缝中进入阴极炭块,造成炭块变形隆起上抬,严重时造成炭块断裂和阴极钢棒熔化[1]。
1.3 破损机理电解生产中阴极炭块是不消耗的,但它长期与高温电解质和铝液接触,不可避免的会受到侵蚀和渗透,并最终演变为破损,主要表现在以下三种情况。
浅谈电解槽槽壳破损原因分析及修复方式
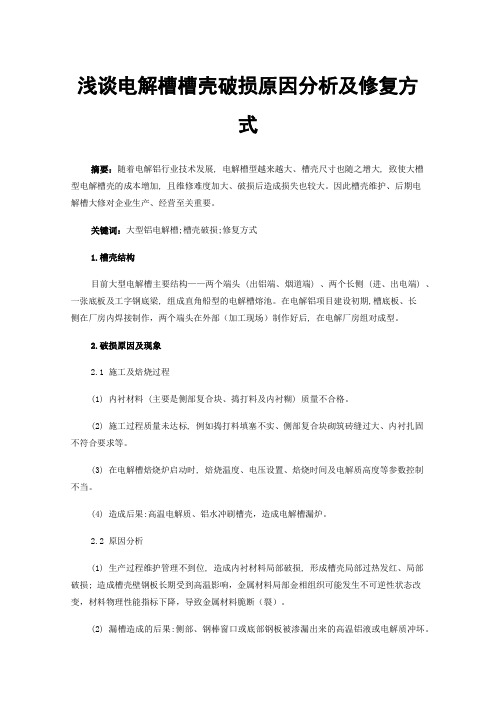
浅谈电解槽槽壳破损原因分析及修复方式摘要:随着电解铝行业技术发展, 电解槽型越来越大、槽壳尺寸也随之增大, 致使大槽型电解槽壳的成本增加, 且维修难度加大、破损后造成损失也较大。
因此槽壳维护、后期电解槽大修对企业生产、经营至关重要。
关键词:大型铝电解槽;槽壳破损;修复方式1.槽壳结构目前大型电解槽主要结构——两个端头 (出铝端、烟道端) 、两个长侧 (进、出电端) 、一张底板及工字钢底梁, 组成直角船型的电解槽熔池。
在电解铝项目建设初期,槽底板、长侧在厂房内焊接制作,两个端头在外部(加工现场)制作好后, 在电解厂房组对成型。
2.破损原因及现象2.1 施工及焙烧过程(1) 内衬材料 (主要是侧部复合块、捣打料及内衬糊) 质量不合格。
(2) 施工过程质量未达标, 例如捣打料填塞不实、侧部复合块砌筑砖缝过大、内衬扎固不符合要求等。
(3) 在电解槽焙烧炉启动时, 焙烧温度、电压设置、焙烧时间及电解质高度等参数控制不当。
(4) 造成后果:高温电解质、铝水冲刷槽壳,造成电解槽漏炉。
2.2 原因分析(1) 生产过程维护管理不到位, 造成内衬材料局部破损, 形成槽壳局部过热发红、局部破损; 造成槽壳壁钢板长期受到高温影响,金属材料局部金相组织可能发生不可逆性状态改变,材料物理性能指标下降,导致金属材料脆断(裂)。
(2) 漏槽造成的后果:侧部、钢棒窗口或底部钢板被渗漏出来的高温铝液或电解质冲坏。
(3) 使用时间达到设计年限随着电解槽的运行槽龄不断增长, 液态电解质不断地向阴极碳块渗透, 由于熔盐渗透至熔体的凝固等温线时就生成凝固物, 或生成碳化铝促使碳块继续膨胀, 其过程是连续的、缓慢的,应力逐步向最弱的位置转移,导致槽壳变形和破损。
内衬受熔盐的侵蚀加重, 槽壳壁钢板也随之被腐蚀,在电解槽短侧最为常见,大概在电解槽沿板下方600mm—800mm左右。
(4)槽壳底板与斜侧壁之间焊缝开裂情况,可能是电解槽后续生产过程中内衬吸钠膨胀叠加在该处产生的应力集中导致。
300kA系列电解槽阴极破损的现象_原因及对策
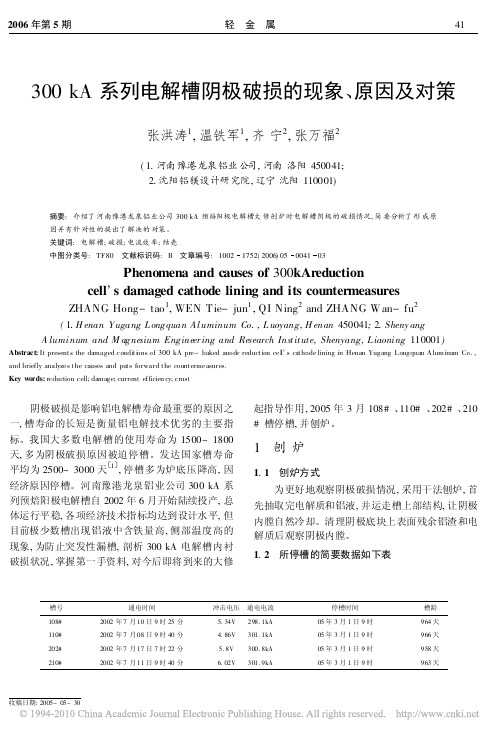
300kA系列电解槽阴极破损的现象、原因及对策张洪涛1,温铁军1,齐宁2,张万福2(1.河南豫港龙泉铝业公司,河南洛阳450041;2.沈阳铝镁设计研究院,辽宁沈阳110001)摘要:介绍了河南豫港龙泉铝业公司300kA预焙阳极电解槽大修刨炉时电解槽阴极的破损情况,简要分析了形成原因并有针对性的提出了解决的对策。
关键词:电解槽;破损;电流效率;结壳中图分类号:TF80 文献标识码:B 文章编号:10021752(2006)05004103Phenomena and causes of300kAreductioncell s damaged cathode lining and its countermeasuresZHANG Hong-tao1,WEN Tie-jun1,QI Ning2and ZHANG Wan-fu2(1.H enan Yugang L ongquan Aluminum Co.,L uoyang,H enan450041;2.Sheny angA luminum and M agnesium Engineer ing and Research Institute,Shenyang,L iaoning110001) Abstract:It presents the damaged conditi ons of300kA pre-baked anode reduction cel l s cathode lining in Henan Yugang Longquan Aluminum Co., and briefly analyzes the causes and puts forward the countermeasures.Key words:reduction cell;damage;current efficien cy;crust阴极破损是影响铝电解槽寿命最重要的原因之一,槽寿命的长短是衡量铝电解技术优劣的主要指标。
300kA铝电解预焙槽侧部破损原因及对策
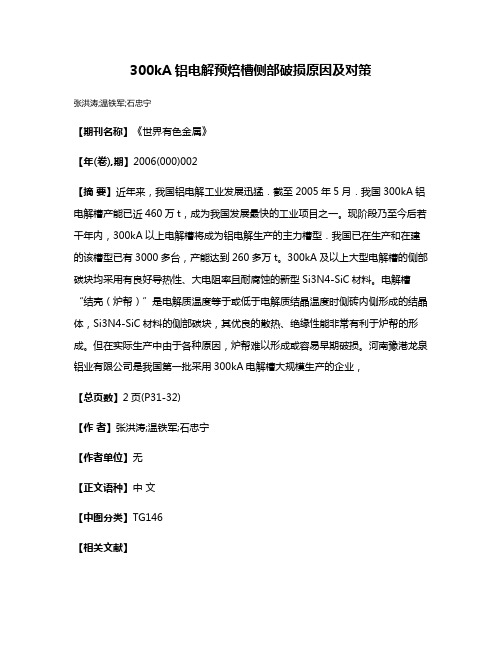
300kA铝电解预焙槽侧部破损原因及对策
张洪涛;温铁军;石忠宁
【期刊名称】《世界有色金属》
【年(卷),期】2006(000)002
【摘要】近年来,我国铝电解工业发展迅猛.截至2005年5月.我国300kA铝电解槽产能已近460万t,成为我国发展最快的工业项目之一。
现阶段乃至今后若干年内,300kA以上电解槽将成为铝电解生产的主力槽型.我国已在生产和在建的该槽型已有3000多台,产能达到260多万t。
300kA及以上大型电解槽的侧部碳块均采用有良好导热性、大电阻率且耐腐蚀的新型Si3N4-SiC材料。
电解槽“结壳(炉帮)”是电解质温度等于或低于电解质结晶温度时侧砖内侧形成的结晶体,Si3N4-SiC材料的侧部碳块,其优良的散热、绝缘性能非常有利于炉帮的形成。
但在实际生产中由于各种原因,炉帮难以形成或容易早期破损。
河南豫港龙泉铝业有限公司是我国第一批采用300kA电解槽大规模生产的企业,
【总页数】2页(P31-32)
【作者】张洪涛;温铁军;石忠宁
【作者单位】无
【正文语种】中文
【中图分类】TG146
【相关文献】
1.大型预焙铝电解槽侧部破损原因分析及控制措施 [J], 欧阳全胜;王进良;张松江
2.大型铝电解槽侧部破损原因分析及对策 [J], 黄继勇;张虎;苏宝峰
3.300kA铝电解槽侧部修补实践 [J], 石英超;杨新峰;
4.铝电解槽内衬破损原因分析及对策 [J], 王海
5.200KA预焙铝电解槽侧部炉帮过空发红现象的分析及对策 [J], 王来存;金四明因版权原因,仅展示原文概要,查看原文内容请购买。
铝电解槽内衬破损原因分析及对策
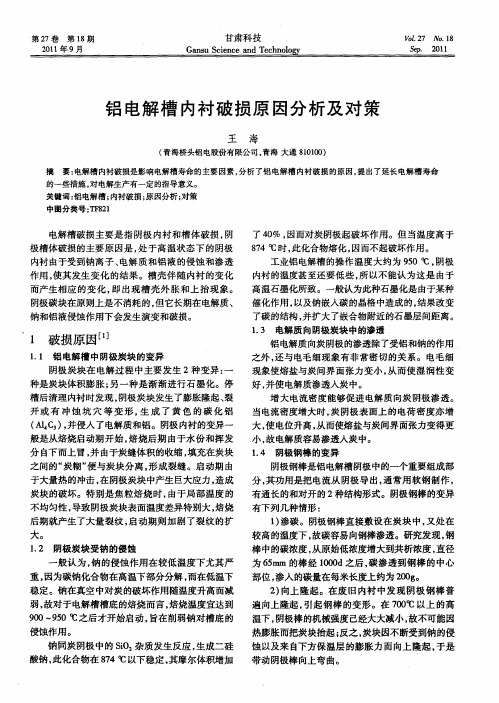
现象使熔盐与炭间界 面张力变小 , 从而使 湿润性变 好, 并使 电解质渗透入炭中。
增大电流密度能够促进电解质 向炭阴极渗透 。 当电流密度增大时, 炭阴极表面上 的电荷密度亦增
开或 有 冲蚀 坑 穴 等 变形 , 成 了 黄 色 的碳 化 铝 生 ( C ) 并 侵入 了电解 质和 铝 。 阴极 内衬 的变异一 ,, 般是从焙烧启动期开始 , 焙烧后期 由于水份和挥发 分自 下而上冒 , 由于炭缝体积的收缩 , 并 填充在炭块
12 阴极炭块受钠的侵蚀 .
一
般认为 , 的侵蚀作用在较低温度下尤其严 钠
重, 因为碳钠化合物在高温下部分分解 , 而在低温下 稳定。钠在真空中对炭的破坏作用随温度升高而减 弱, 故对 于电解槽槽底 的焙烧而言 , 焙烧温度宜达到 90 90o之后才开始启动 , 0 ~ 5 C 旨在削弱钠对槽底的
之间的“ 炭糊” 便与炭块分离 , 形成裂缝 。启动期 由 于大量热 的冲击 , 在阴极炭块 中产生巨大应力 , 造成 炭块的破坏。特别是焦粒焙烧时 , 由于局部温度的 不均匀性 , 导致阴极炭块表面温度差异特别大 , 焙烧 后期就产生了大量裂纹 , 启动期则加剧 了裂纹的扩
大。
大, 使电位升高 , 从而使熔盐与炭问界面张力变得更
小, 故电解质容易渗透人炭中。 14 阴极钢 棒 的变异 . 阴极钢棒是铝电解槽阴极中的一个重要组成部 分, 其功用是把电流从 阴极导出 , 通常用软钢制作 ,
有通长的和对开的 2种结构形式 。阴极钢棒的变异
有下列几种情形 :
1 渗碳 。阴极钢棒直接敷设在炭块中 , ) 又处在 较高的温度下 , 故碳容易向钢棒渗透。研究发现 , 钢 棒中的碳浓度 , 从原始低浓度增大到共析浓度 , 直径 为6m 5 m的棒经 10 d之后 , 00 碳渗透到钢棒的中心 部位 , 渗入的碳量在每米长度上约为 20 。 0 g 2 向上 隆起。在废 旧内衬 中发现 阴极钢 棒普 ) 遍向上隆起 , 引起钢棒 的变形 。在 70C以上的高 0o
铝电解预焙槽侧部破损原因及对策

书山有路勤为径,学海无涯苦作舟铝电解预焙槽侧部破损原因及对策一、电解槽侧部破损现象1、侧部破损的判定电解生产的特殊性使侧部炉帮形成不良初期破损较难判定,尤其是300kA 大型槽的生产实践在我国尚属初期,对该种情况下研究较少,大部分借鉴过去小槽型的经验管理,但是由于300kA 级以上槽均使用Si3N4-SiC 侧部碳块,为我们提供了新的科学判定依据。
在原铝品质化验中Si 含量的高低可直接作为判断尤其是早期判定的依据,一般原铝Si 含量在0.03%左右,如果超过0.05%我们就应该认为是该槽子炉帮形成不好,侧部碳块已经开始腐蚀,应尽快找准原因采取措施。
如果一个生产系列200 多台电解槽中,硅含量有5 台以下硅含量达到或者是超过0.05%,应从技术条件保持和操作质量中查找原因,采取措施控制,如果有10-20 台Si 含量超过0.05%,那么我们就应该从设计角度查找原因,炉帮局部发红也是电解槽侧部损坏的判定依据。
2、电解槽侧部破损宏观现象在进行电解槽大修过程中发现,电解槽侧部炉帮形成不良或受损坏严重,侧部碳块人造伸腿上沿铝液、电解质液界面处腐蚀尤其严重,形成长条断裂空洞带。
二、原因分析及对策“炉帮”形成不良或易遭破损的原因从对停槽大修的电解槽炉膛解剖,特别是正常生产中炉帮不良槽子看,侧部碳块直接和电解质溶液接触,有的地方还粘少许酥状的电解质固体,Si3N4-SiC 侧砖已经粉化,沿铝液面的炉膛明显有深的冲刷条沟。
有的侧部裸露部分已经形成粉末状物,对于炉帮形成不良或形成的炉帮易遭破损的原因主要为:1、电解槽预热启动影响电解槽预热启动期,升、降温曲线梯度时间控制得不好,分子比低或技术条件组合失误,导致电解槽初期没有形成良好的坚固的炉帮,因为早期坚实基础炉帮的建立对后期正常生产、炉帮的维护起到重要的保障作用。
2、生产技术条件对侧部炉帮的影响对炉帮损毁的因素很多,在生产中主要反映为电解质温度、溶液流速。
电解槽内衬早期破损原因及修理方法
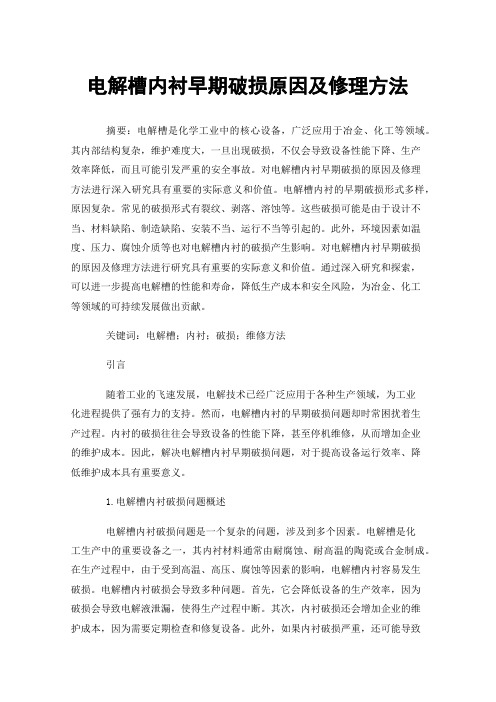
电解槽内衬早期破损原因及修理方法摘要:电解槽是化学工业中的核心设备,广泛应用于冶金、化工等领域。
其内部结构复杂,维护难度大,一旦出现破损,不仅会导致设备性能下降、生产效率降低,而且可能引发严重的安全事故。
对电解槽内衬早期破损的原因及修理方法进行深入研究具有重要的实际意义和价值。
电解槽内衬的早期破损形式多样,原因复杂。
常见的破损形式有裂纹、剥落、溶蚀等。
这些破损可能是由于设计不当、材料缺陷、制造缺陷、安装不当、运行不当等引起的。
此外,环境因素如温度、压力、腐蚀介质等也对电解槽内衬的破损产生影响。
对电解槽内衬早期破损的原因及修理方法进行研究具有重要的实际意义和价值。
通过深入研究和探索,可以进一步提高电解槽的性能和寿命,降低生产成本和安全风险,为冶金、化工等领域的可持续发展做出贡献。
关键词:电解槽;内衬;破损;维修方法引言随着工业的飞速发展,电解技术已经广泛应用于各种生产领域,为工业化进程提供了强有力的支持。
然而,电解槽内衬的早期破损问题却时常困扰着生产过程。
内衬的破损往往会导致设备的性能下降,甚至停机维修,从而增加企业的维护成本。
因此,解决电解槽内衬早期破损问题,对于提高设备运行效率、降低维护成本具有重要意义。
1.电解槽内衬破损问题概述电解槽内衬破损问题是一个复杂的问题,涉及到多个因素。
电解槽是化工生产中的重要设备之一,其内衬材料通常由耐腐蚀、耐高温的陶瓷或合金制成。
在生产过程中,由于受到高温、高压、腐蚀等因素的影响,电解槽内衬容易发生破损。
电解槽内衬破损会导致多种问题。
首先,它会降低设备的生产效率,因为破损会导致电解液泄漏,使得生产过程中断。
其次,内衬破损还会增加企业的维护成本,因为需要定期检查和修复设备。
此外,如果内衬破损严重,还可能导致安全事故,对员工和工厂安全构成威胁。
电解槽内衬破损问题的原因有很多。
其中,设备材料质量不好、设备安装不当、生产操作不当、设备长时间使用等是最常见的因素。
因此,为了解决这个问题,需要从多个方面入手,包括选用高质量的内衬材料、规范设备安装和生产操作、定期检查和维护设备等。
浅谈铝电解槽的破损及维修

浅谈铝电解槽的破损及维修【摘要】在电解铝生产实践过程中由于电解槽侧部散热不良、槽炉帮形成不好等一系列问题,使得电解槽侧部破损,从而降低电解槽的使用寿命。
本文对电解槽的破损原因进行了归纳分析,并提出了电解槽破损的检查与维修方法。
【关键词】铝电解槽;阴极内衬;破损;维护1、铝电解槽常见破损形式及原因通常所说的电解槽的破损是指其阴极内衬的破损,铝电解槽的阴极内衬使用期不到1年,称为早期破损。
槽内铝液中的铁含量连续增加,一般情况下,是槽底部阴极钢棒受铝液侵蚀熔化所致,往往是阴极炭块破损的征兆。
当铝液中的铁含量连续超过1%时,表示阴极炭块已发生严重破损。
电解槽阴极内衬破损可归纳为如下几种形式:1.1阴极炭块及保温绝热结构的变异阴极内衬的变异主要有:阴极炭块发生变形—膨胀、隆起、裂开或有冲蚀坑穴;炭块之间的炭糊接缝发生裂纹,其中侵渍着碳化铝、电解质和铝;炭块中的钢棒弯曲变形,一部分被铝熔解侵蚀,形成亮晶晶的铝铁合金;炭块下而的耐火砖层局部变质,向上隆起,呈凸棱镜状;侧部炭块受到侵蚀,其中渗透着铝和电解质,体积膨胀;槽壳变形,侧壁向外鼓出,四角上抬,底部呈船形。
阴极内衬的变异,一般是从焙烧启动期开始。
由于水分和挥发成分自下而上冒出,并由于炭缝体积收缩,填充在炭块之间的“炭糊”便与炭块分离,形成裂纹。
加入电解质开始电解之后,组织也开始酥松,给电解质和铝液的侵入创造了条件。
侵入炭块和炭缝中的铝液,继续向下渗透,直到炭块下而并淤积在那里。
NaF成分是阴极界而上的表而活性物质,它首先入侵,故在炭块下而发现柱状结晶的氟化钠。
侵入炭块下的电解质和钠还同耐火砖层发生化学作用,使其变质而体积胀大。
一旦铝侵入阴极钢棒区,则铁被熔解。
由于钠、电解质和铝先后侵入阴极内衬中,引起炭块和耐火层体积膨胀,于是炭块向上隆起。
在电解槽启动后6个月内,隆起高度不超过2cm,以后则逐渐增大,在36个月内达到10cm,以后趋于稳定。
当炭块隆起增大时,会引起电流偏流和电压降增大,铝的纯度降低,槽膛有效深度减小,造成电解槽操作困难,甚至停槽。
- 1、下载文档前请自行甄别文档内容的完整性,平台不提供额外的编辑、内容补充、找答案等附加服务。
- 2、"仅部分预览"的文档,不可在线预览部分如存在完整性等问题,可反馈申请退款(可完整预览的文档不适用该条件!)。
- 3、如文档侵犯您的权益,请联系客服反馈,我们会尽快为您处理(人工客服工作时间:9:00-18:30)。
300kA系列电解槽阴极破损的现象、原因及对策张洪涛1,温铁军1,齐宁2,张万福2(1.河南豫港龙泉铝业公司,河南洛阳450041;2.沈阳铝镁设计研究院,辽宁沈阳110001)摘要:介绍了河南豫港龙泉铝业公司300kA预焙阳极电解槽大修刨炉时电解槽阴极的破损情况,简要分析了形成原因并有针对性的提出了解决的对策。
关键词:电解槽;破损;电流效率;结壳中图分类号:TF80 文献标识码:B 文章编号:10021752(2006)05004103Phenomena and causes of300kAreductioncell s damaged cathode lining and its countermeasuresZHANG Hong-tao1,WEN Tie-jun1,QI Ning2and ZHANG Wan-fu2(1.H enan Yugang L ongquan Aluminum Co.,L uoyang,H enan450041;2.Sheny angA luminum and M agnesium Engineer ing and Research Institute,Shenyang,L iaoning110001) Abstract:It presents the damaged conditi ons of300kA pre-baked anode reduction cel l s cathode lining in Henan Yugang Longquan Aluminum Co., and briefly analyzes the causes and puts forward the countermeasures.Key words:reduction cell;damage;current efficien cy;crust阴极破损是影响铝电解槽寿命最重要的原因之一,槽寿命的长短是衡量铝电解技术优劣的主要指标。
我国大多数电解槽的使用寿命为1500~1800天,多为阴极破损原因被迫停槽。
发达国家槽寿命平均为2500~3000天1!,停槽多为炉底压降高,因经济原因停槽。
河南豫港龙泉铝业公司300kA系列预焙阳极电解槽自2002年6月开始陆续投产,总体运行平稳,各项经济技术指标均达到设计水平,但目前极少数槽出现铝液中含铁量高,侧部温度高的现象,为防止突发性漏槽,剖析300kA电解槽内衬破损状况,掌握第一手资料,对今后即将到来的大修起指导作用,2005年3月108#、110#、202#、210 #槽停槽,并刨炉。
1 刨炉1.1 刨炉方式为更好地观察阴极破损情况,采用干法刨炉,首先抽取完电解质和铝液,并运走槽上部结构,让阴极内膛自然冷却。
清理阴极底块上表面残余铝渣和电解质后观察阴极内膛。
1.2 所停槽的简要数据如下表槽号通电时间冲击电压通电电流停槽时间槽龄108#2002年7月10日9时25分 5.34V298.1kA05年3月1日9时964天110#2002年7月08日9时40分 4.86V301.1kA05年3月1日9时966天202#2002年7月17日7时22分 5.8V300.8kA05年3月1日9时958天210#2002年7月11日9时40分 6.02V301.9kA05年3月1日9时963天412006年第5期 轻 金 属收稿日期:2005-05-302 阴极破损情况2.1 阴极内膛4台槽A、B大加工面阴极内膛侧壁结壳较少,槽端头小加工面侧壁结壳约50mm。
A、B大加工面在人造伸腿上沿,铝液与电解质液界面处,SiC-SiN 侧块腐蚀严重,形成断裂空洞带(见图1);四台槽阴极底块表面均有沉淀覆盖;108#槽阴极底块表面有一大冲蚀坑,坑长450m m,宽80mm,深200mm。
槽膛有数条横向裂缝,缝宽35mm。
底块表面隆起,最高处隆起92mm;110#槽有局部凹坑,有数条横向裂纹。
202#槽有局部浅凹坑。
210#槽有大面积凹坑,最深处105mm。
2.2 内衬破损现象108#槽阴极底块间缝和底块端头与浇注料接触面处有多处渗漏且渗铝较多,A5、B6阴极钢棒在浇注料中已熔断,A6、A7、A8、B7钢棒在底块中已大部分熔化并形成空洞和合金。
熔体在干式防渗料中形成不同成分的熔固体。
其中碳化铝层较厚,阴极底块向上隆起,熔体有三处已浸入保温砖层中(见图2)。
110#槽阴极底块间缝和底块端头与浇注料接触面处有多处渗漏,部分阴极钢棒有被浸蚀现象,阴极底块下熔固体在A23处渗漏至保温砖层中约0. 8m。
B4、A23阴极钢棒窗口处槽壳钢板局部烧穿, B8、B9阴极窗口处槽壳侧板、槽壳斜板大面积烧穿,铝水从槽壳和硅酸钙板漏入槽底硅酸钙板层中,形成大面积铝板层和网状铝层。
202#槽阴极底块间缝和底块端头与浇注料接触面处有少数几处渗漏。
部分阴极钢棒被腐蚀、有空洞,B8、B9阴极钢棒处槽侧板局部烧穿,铝液从槽壳与硅酸钙板中漏入槽底硅酸钙板层中,在B5、B6、B7、B8、B9处硅酸钙板中形成网状铝层,最长2100mm,宽1700mm。
210#槽阴极底块间缝和底块端头与浇注料接触面处渗漏几乎没有。
阴极底板下干式防渗料形成的结晶层较均匀,较薄,约100mm。
3 槽壳变形4台槽槽壳在A、B大面外凸变形均小于15mm,但在两端固定摇篮架与活动摇篮架大间距处,槽侧钢板均向外凸起,最大45mm。
4 形成原因根据刨炉状况、生产实践和相关理论研究表明,电解槽破损原因和现象不是孤立的而是互相制约、相互联系的。
图1Fig.1图2Fig.2∀从刨炉看侧部碳块破损严重,从人造伸腿上沿,铝液和电解质液两界面处形成长条断裂空洞,直至露出槽侧钢板。
4台槽均已小修更换过侧部碳块。
由于A、B加工面为300m m,电解质温度960#,分子比2.4,电解质在侧部碳块上不易结壳,此处碳块受两液面波动和旋流直接冲刷,腐蚀较快,加之侧部碳块渗氮层较薄,易部分粉化,侧部硅酸钙板受热易形成碎块,侧部漏铝就容易从槽壳与侧块及硅酸钙板的缝隙漏入阴极钢棒或槽底板。
∃阴极炭块质量,停炉的4台槽为两个厂家产品,其中一家炭素厂供应的两台槽阴极炭块一台破损,一台冲蚀情况明显多于其它两台槽,炭块质量问题不能排除。
%防渗料在焙烧时随炭块底部温度升高而产生物相变化,在伴有少量电解质的参与下形成一层致密的结壳层,能有效地阻止液体渗漏,但如在电解槽在焙烧启动时,温度过高,渗漏的电解质越多,结壳也越厚,挤压了干式防渗层的空间,减少了干式防渗层的可压缩性。
形成很大的膨胀力,对阴极炭块将产生巨大的应力,使炭块变形形成裂纹。
42张洪涛,温铁军,齐宁,张万福:300kA系列电解槽阴极破损的现象、原因及对策 2006年第5期&焙烧启动时期,炭块发生变异一是体积膨胀,二是进行石墨化2!,焙烧温度、时间不适宜,使阴极炭块温差过大,电流分布不匀,加剧钠和电解质铝液等的浸入,逐渐下渗产生膨胀。
∋焙烧温度控制不当也是引起漏槽的主要原因,侧部伸腿中热捣糊主要为沥青成分,焙烧温度在250#~300#时底糊仍然保持塑性,随温度升高至500#~1000#时,开始固化,引发收缩,收缩率0. 4%~1.0%之间3!,因此在焙烧预热阶段,要保持适宜温度,采用分子比2.8以上的电解质配料以形成高温、高分子比的炉帮和伸腿,保护人造伸腿。
焙烧时间也是影响阴极变化的重要原因,要保持80~ 96h的焙烧预热期,减缓对阴极的热冲击。
(形成沉淀的主要原因是由于正常生产过程中电解质水平偏低或铝水平偏高造成的。
因为电解质水平偏低,电解质的总量小,溶解氧化铝的量也相应的减少,因而下到电解槽中的氧化铝有一部分溶解不了而直接沉到槽底形成沉淀。
当铝液水平保持过高,铝量偏大,通过铝液散失的热量就大,会使槽底发冷,使槽底的沉淀硬化成结壳。
)阴极表面冲蚀、剥落不是阴极破损的主要因素,多为换阳极时捞沉淀形成的。
∗铁含量不是判定停槽的唯一依据。
四台槽的其中一台破损槽,从停槽前210天,铁含量上升超过0.2,至停槽前100天时达到最高0.76,以后均在0.3~0.6间徘徊。
所以运行半年多没发生漏炉。
要想在铁含量上升判断是否是漏槽,还须看阴极电流分布。
5 内衬设计及筑炉改进措施∀增加槽壳散热,在槽壳上焊接散热片,位置在两摇篮架之间,这样有利于形成结实的侧部结壳,保护侧部碳块。
∃槽内衬结构的改进+阴极炭块侧部改用防渗浇铸料,避免侧部发生渗漏时,铝液和电解质渗入阴极碳块内而造成的阴极破损。
,炭化硅结合氮化硅砖表面渗氮层刨炉观察仅15m m,因此侧部炭化硅结合氮化硅砖厚度选用90~100mm,(不主张采用复合碳砖),这样既易散热,以利炉帮形成又增强抗腐蚀性。
−取消钢棒间的保温砖,避免形成空间,渗漏铝液。
.阴极钢棒在浇铸料处包一层0.02mm厚的薄膜,预留钢棒膨胀间隙。
/选用合格的阴极炭块。
0保证扎糊质量尤其是炭间糊的扎固质量1伸腿压阴极炭块必需2cm以上。
6 结语提高电解槽寿命是系统的工程,与槽型结构、筑炉材料及质量、焙烧启动及工艺操作等有关,通过本次刨炉剖析,我们认为提高槽寿命应注意以下几点:∀严把筑炉质量关,注重材料选择;∃加强电解槽焙烧启动管理,焙烧时间80~96小时以上,科学控制升温曲线,及时处理偏流现象。
在启动时槽内必须有一定量的电解质液。
采用湿法无效应启动,避免炭块巨大的热冲击。
严格执行焙烧启动程序规程。
%正常生产期间要严格管理,尽量保持系列电流的稳定,注意保持合理稳定的技术参数,改进计算机控制技术。
参考文献:1!、2!邱竹贤.预焙槽炼铝M!.冶金工业出版社,2005,3.3!何允平、董民杰.铝电解寿命研究M!.东北工学院出版社,1991. 4!梁汉.三论电解槽槽底破损的早期定位监测J!.轻金属,2004,2, P24-273.(责任编辑 郝文儒)432006年第5期 轻 金 属。