生产部各工序工艺标准
服装生产工艺流程(超详细)
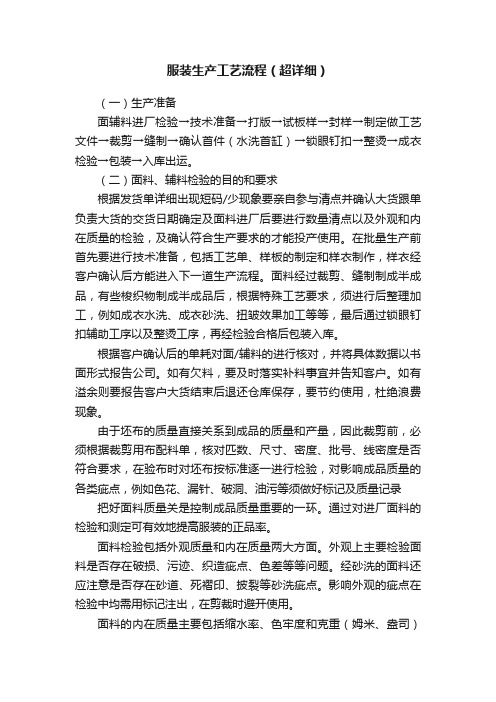
服装生产工艺流程(超详细)(一)生产准备面辅料进厂检验→技术准备→打版→试板样→封样→制定做工艺文件→裁剪→缝制→确认首件(水洗首缸)→锁眼钉扣→整烫→成衣检验→包装→入库出运。
(二)面料、辅料检验的目的和要求根据发货单详细出现短码/少现象要亲自参与清点并确认大货跟单负责大货的交货日期确定及面料进厂后要进行数量清点以及外观和内在质量的检验,及确认符合生产要求的才能投产使用。
在批量生产前首先要进行技术准备,包括工艺单、样板的制定和样衣制作,样衣经客户确认后方能进入下一道生产流程。
面料经过裁剪、缝制制成半成品,有些梭织物制成半成品后,根据特殊工艺要求,须进行后整理加工,例如成衣水洗、成衣砂洗、扭皱效果加工等等,最后通过锁眼钉扣辅助工序以及整烫工序,再经检验合格后包装入库。
根据客户确认后的单耗对面/辅料的进行核对,并将具体数据以书面形式报告公司。
如有欠料,要及时落实补料事宜并告知客户。
如有溢余则要报告客户大货结束后退还仓库保存,要节约使用,杜绝浪费现象。
由于坯布的质量直接关系到成品的质量和产量,因此裁剪前,必须根据裁剪用布配料单,核对匹数、尺寸、密度、批号、线密度是否符合要求,在验布时对坯布按标准逐一进行检验,对影响成品质量的各类疵点,例如色花、漏针、破洞、油污等须做好标记及质量记录把好面料质量关是控制成品质量重要的一环。
通过对进厂面料的检验和测定可有效地提高服装的正品率。
面料检验包括外观质量和内在质量两大方面。
外观上主要检验面料是否存在破损、污迹、织造疵点、色差等等问题。
经砂洗的面料还应注意是否存在砂道、死褶印、披裂等砂洗疵点。
影响外观的疵点在检验中均需用标记注出,在剪裁时避开使用。
面料的内在质量主要包括缩水率、色牢度和克重(姆米、盎司)三项内容。
在进行检验取样时,应剪取不同生产厂家生产的、不同品种、不同颜色具有代表性的样品进行测试,以确保数据的准确度。
同时对进厂的辅料也要进行检验,例如松紧带缩水率,粘合衬粘合牢度,拉链顺滑程度等等,对不能符合要求的辅料不予投产使用。
机械行业生产工艺标准

机械行业生产工艺标准一、引言机械行业是指通过机械设备来加工、制造和加工零件或组装成品的行业。
在机械制造过程中,生产工艺标准是确保产品质量和生产效率的重要因素。
本文将介绍机械行业常见的生产工艺标准,包括工艺流程、操作规范、材料选择和质量要求等方面。
二、工艺流程1. 设计和规划:在机械产品制造前,需要进行详细的设计和规划工作。
设计阶段要考虑产品的功能、结构和工艺要求,并进行必要的模拟和验证。
2. 材料准备:根据设计要求,选择合适的原材料,并进行相应的材料预处理,包括锻造、淬火、热处理等。
3. 加工工艺选择:根据产品的结构和要求,选择合适的加工工艺,包括铣削、车削、磨削、切削等。
4. 加工操作:按照工艺要求,进行具体的加工操作,包括工件的定位、夹紧、加工刀具的选择、切削速度和进给量的控制等。
5. 检测和质量控制:在加工过程中,进行相应的检测和质量控制,包括尺寸测量、表面质量检查和功能性能测试等。
6. 组装和调试:完成加工后,根据产品的要求进行组装和调试,确保产品的性能和质量。
7. 成品检验和包装:对成品进行全面的检验,并进行相应的包装和标识,以满足产品出厂要求。
三、操作规范1. 安全操作规范:在机械制造过程中,操作人员必须遵守相关的安全操作规范,包括穿戴防护设备、正确使用机械设备、保持工作场所的整洁和安全等。
2. 加工工艺规范:在加工过程中,操作人员必须按照预定的工艺要求进行操作,包括合理布置工件和刀具、控制切削速度和进给量、定期清洁和保养设备等。
3. 检测和质量控制规范:在检测和质量控制过程中,操作人员必须按照标准的检测方法进行操作,确保检测结果的准确和可靠性。
4. 组装和调试规范:在组装和调试过程中,操作人员必须按照产品要求进行操作,包括正确组装零件、调试功能和性能等。
5. 成品检验和包装规范:在成品检验和包装过程中,操作人员必须按照标准的检验方法进行操作,确保成品的质量和可靠性。
四、材料选择1. 材料特性:根据产品的要求选择合适的材料,包括强度、硬度、耐磨性、耐蚀性、热稳定性等。
(完整版)工艺规程模板

盐酸林克霉素工艺规程目录1.主题内容 (2)2.适用范围 (2)3.定义 (2)4.职责 (2)5.产品概述 (2)6.工艺流程图 (3)7.生产处方与批量 (4)8.工艺与操作要求 (4)9.生产场所及设备说明 (4)10.关键工艺参数与质量控制点 (5)11.物料、产品规格及质量标准、技术参数及贮存要求 (5)12.物料平衡率、收率计算方法与限度 (6)13.原辅料消耗定额与产品生产周期 (7)14.综合利用和环境保护 (7)15.相关程序 (8)16.附件 (8)17.变更记载及原因 (8)1.主题内容本标准规定了原料药××××生产全过程的工艺技术、质量、物耗、安全、工艺卫生等内容,符合GMP规范要求。
本工艺规程具有技术法规作用。
2.适用范围本标准适用于原料药××××生产全过程,是各部门共同遵循的技术准则。
3.定义本品为链菌属链丝菌菌群生长时的产物,即一种林可胺类碱性抗生素。
主要通过抵制细菌的蛋白质合成而起作用。
4.职责起草:原料车间主任审核:生产工程部经理、质量部经理批准:质量副总执行批准:QA主任执行:各级生产质量管理人员及操作人员监督管理:生产质量管理人员5.产品概述5.1.产品名称、规格及代码-通用名称:盐酸林可霉素-汉语拼音:Yansuan Linkemeisu-英文名称:Lincomycin Hydrochloride-剂型:注射用无菌粉-规格:-包装规格:-产品代码:5.2.产品性状、成分及性质-性状:本品为白色结晶性粉末;有微臭或特殊臭;味苦。
-成分:-类别:抗生素药。
-贮藏:密封保存。
-有效期:24个月。
5.3.产品处方依据与制法-依据:-批准文号:-处方与制法:××××6.工艺流程图7.生产处方与批量7.1投料:盐酸林可霉素 20kg纯化水 5kg活性炭 0.164kg95%乙醇 43kg丙酮 70kg7.2批量:8.工艺与操作要求8.1溶解过滤工序在100L反应罐中,按批生产指令的批量加入纯化水和95%乙醇,搅匀,升温至50~55℃,再加入盐酸林可霉素,搅拌、溶解(澄清),保温至50~55℃。
家具生产各工序工艺品质标准(图片)
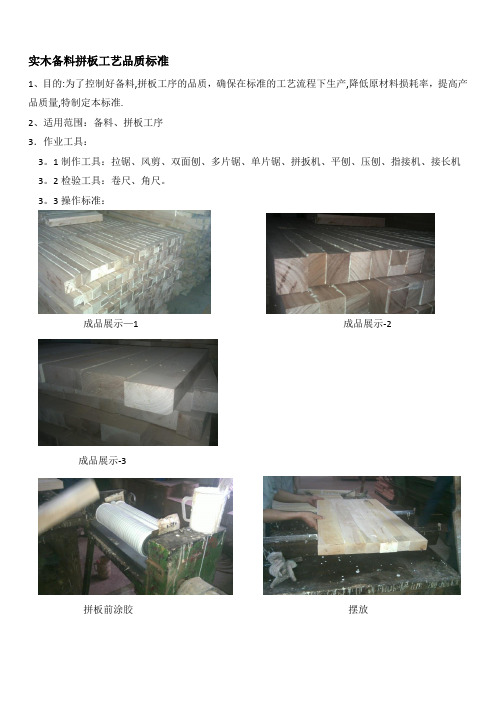
实木备料拼板工艺品质标准1、目的:为了控制好备料,拼板工序的品质,确保在标准的工艺流程下生产,降低原材料损耗率,提高产品质量,特制定本标准.2、适用范围:备料、拼板工序3.作业工具:3。
1制作工具:拉锯、风剪、双面刨、多片锯、单片锯、拼扳机、平刨、压刨、指接机、接长机3。
2检验工具:卷尺、角尺。
3。
3操作标准:成品展示—1 成品展示-2成品展示-3拼板前涂胶摆放固定成型3.4拼板前期准备:断料(下料)修边机双面刨4.品质工艺要求:4.1按照生产技术部门指定的图纸规格尺寸、数量、质量要求,根据板材的长度、宽度及厚度合理搭配用材。
4。
2面料选用树种统一、颜色接近、无虫眼、无死节、无油眼、无爆裂、无腐朽、无钝棱、无红、黑树芯的木材,含水率12%以下,按材质好坏。
分为面料、垫料、填芯料及颜色要求的筛选。
不符合用料要求及标准的材料不予加工。
垫料选用不能做面料的材料,填芯料选用不能做垫料的材料.锯路要求平面、光滑、角度正常。
4.3拼板料的拼接面要求平整光滑、底面与拼接面要成直角,不允许有不同木材、颜色、木质、木纹方向的料拼成一个整体,相邻两块板料的湿度不超过2%.同一块拼板料中,料与料之间厚度差不得超过2MM,长度差不得超过3MM.4.4拼缝线的宽度不允许超过0.2MM,涂胶量且要双面,涂抹均匀不得单面厚凃,以加压有均匀胶水刚挤出为宜。
4。
5常规替代材料:胡桃木使用楸木、桦桃木(需要擦底色)樱桃木使用桦桃木、赤杨,黄杨实木椅类用橡胶木橡木使用白栓木4.6封边实木代替:奥古曼、椴木、赤杨、黄杨4。
7硬木类(水曲柳、桦木、橡胶木等)加压压力要求12—15kg/cm2,软木类(奥古曼、黄杨、赤杨等)加压压力要求8—12kg/ cm2加压3小时以上(25度以上)卸压8小时后才可进行二次深加工。
4。
8所有须经车枳和雕刻的台脚或立柱不允许拼松软木质,以免在车床因紧固松紧程度不同影响工艺线大小不一致或因木质松软无法加工。
食用菌菌种制作工艺流程及各工序生产规程
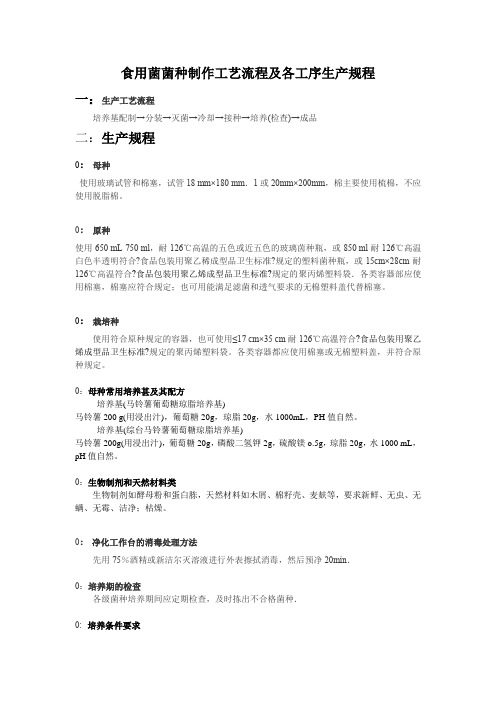
食用菌菌种制作工艺流程及各工序生产规程一:生产工艺流程培养基配制→分装→灭菌→冷却→接种→培养(检查)→成品二:生产规程0:母种使用玻璃试管和棉塞,试管18mm×180mm.1或20mm×200mm,棉主要使用梳棉,不应使用脱脂棉。
0:原种使用650mL-750ml,耐126℃高温的五色或近五色的玻璃茵种瓶,或850ml耐126℃高温白色半透明符合?食品包装用聚乙稀成型品卫生标准?规定的塑料菌种瓶,或15cm×28cm耐126℃高温符合?食品包装用聚乙烯成型品卫生标准?规定的聚丙烯塑料袋.各类容器部应使用棉塞,棉塞应符合规定;也可用能满足滤菌和透气要求的无棉塑料盖代替棉塞。
0:栽培种使用符合原种规定的容器,也可使用≤17cm×35cm耐126℃高溫符合?食品包装用聚乙烯成型品卫生标准?规定的聚丙烯塑料袋。
各类容器都应使用棉塞或无棉塑料盖,并符合原种规定。
0:母种常用培养甚及其配方培养基(马铃薯葡萄糖琼脂培养基)马铃薯200 g(用浸出汁),葡萄糖20g,琼脂20g,水1000mL,PH值自然。
培养基(综台马铃薯葡萄糖琼脂培养基)马铃薯200g(用浸出汁),葡萄糖20g,磷酸二氢钾2g,硫酸镁o.5g,琼脂20g,水1000 mL,pH值自然。
0:生物制剂和天然材料类生物制剂如酵母粉和蛋白胨,天然材料如木屑、棉籽壳、麦麸等,要求新鲜、无虫、无螨、无霉、洁净;枯燥。
0:净化工作台的消毒处理方法先用75%酒精或新洁尔灭溶液进行外表擦拭消毒,然后预净20min.0:培养期的检查各级菌种培养期间应定期检查,及时拣出不合格菌种.0:培养条件要求不同种类或不同品种应分区培养。
根据培养物的不同生长要求,给予其适宜的培养温度〔多在室温20℃~24℃〕,保持空气相对湿度在75%以下,通风,避光。
0:灭菌效果的检查方法培养基配制后应在4h内进锅灭菌。
母种培养基灭菌0.11MPa~0.12MPa,30min。
印刷生产制程各工序损耗放数标准

生产制程各工序损耗放数标准
一.印刷放耗标准
二.表面处理:
(1)过油磨光: 10+3‰(尺寸超800*800mm 5‰+15张)
(2)UV : 10+4‰(尺寸超800*800mm 6‰+15张)
(3)过胶 : 30+6‰
(4)烫金: 10+(1~3)‰
三.裱纸: 5+2‰张(尺寸超800*800mm 5+5‰)
四.啤盒:10+3‰张(尺寸超800*800mm10+ 5‰)(开模数多或复杂的由工艺评审加放数)
五.手工部:(1)粘盒: 5+1.5‰(2)钉箱: 5+1.5‰
(3)擦胶丝: 2+1‰(4)骑马钉: 5+1‰
(5)胶装: 30+6‰(6)折页: 5+1.5‰
六.精品:(1)面纸:5000以下 5+6‰5000以上 5+5‰
(2)衬纸:5000以下 5+6‰5000以上 5+5‰
七.外发:(1)局部UV:30 +5‰(200g以下) 30+1‰(200g以上)
(2)压纹: 10+1‰
(3)外发印刷:在本厂放耗基数上加50~100张(对开);超大尺寸加100张
八. 以上放耗为最大放耗量(特种纸、特殊工艺由工艺评审时或审核工单时加放数)。
备注:BA01、AA01、AA03、AA02、DA03、EA03、或产品为满版实地大墨位、蓝紫绿系列(实地+平网四色撞印)、浅灰平网等在实际印刷中,确实难度系数较大,对其放耗在原基数上可由开单员适当增加75----150张,但必须经过工程技术经理级以上人员审核确认。
九.本规定自年月日开始执行。
编制:审核:批准:。
工艺流程标准

工艺流程标准工艺流程标准是制定和规范企业生产过程的指导性文件,它描述了从原材料采购到成品交付的流程步骤和要求。
以下是一个典型的工艺流程标准的例子:1. 原材料采购:从可靠的供应商采购原材料,并确保其符合国家和行业的质量标准。
采购部门应与供应商签订合同,并对原材料进行检验和验收。
2. 物料准备:根据生产计划和产品要求,对原材料进行加工和准备。
确保物料的数量和质量满足生产需要。
3. 生产工序:根据产品的制造工艺和工序要求进行生产。
各个工序应按照规定的标准操作程序进行,并记录生产过程中的关键参数和数据。
4. 质量控制:在生产过程中,对各工序的出产进行严格的质量控制。
各个工序的质检人员应根据质量检验标准对产品进行抽样检验和测试,确保产品符合质量要求。
5. 中间检验:在生产过程中,进行中间检验,以确保产品达到指定的质量要求。
检验结果应及时记录,如有问题应及时采取纠正措施。
6. 成品检验:在产品生产完成之后,对成品进行全面检验。
成品检验人员应对产品的外观、尺寸、性能等进行检测和测试,只有合格的产品才能被接受。
7. 包装和标识:将符合质量要求的产品进行包装和标识。
包装应符合产品运输和贮存的要求,标识应包括产品名称、规格、生产日期、批次号等必要信息。
8. 成品交付:将包装完好、标识齐全的产品按照订单要求交付给客户。
必要时,还需提供产品合格证明和相关技术文件。
9. 质量管理记录:各个工序和环节的关键数据和记录应及时整理和归档,以便质量管理部门进行质量追溯和分析。
10. 不合格品处理:对于不符合质量要求的产品,应按照不合格品处理程序进行处理。
有关部门应对问题进行调查和分析,并采取相应的纠正和预防措施。
以上只是一个典型的工艺流程标准,具体的标准内容和步骤可能会因不同企业和产品而有所差异。
工艺流程标准的制定和执行对于确保产品质量和提高生产效率非常重要,企业应根据实际情况不断完善和改进标准,以满足市场需求和提高竞争力。
生产工艺流程控制的规程

生产工艺流程控制的规程(草稿)一、目的为加强企业的生产工艺流程控制,全面提升产品的制作质量,降低生产成本,各相关部门和人员按照优化5M1E(注1)的原则进行生产活动,增强企业的竞争力,特制订本规程。
—-注1:5M1E分别是英文—人员、机器、材料、方法、测量和环境的单词首位字母。
二、使用范围本集团下属各公司的应依据本规程来制订、执改进行、生产工艺流程、对其结果进行考核、奖惩,除另有规定外,均以本规程执行;三、规程的内容:1、工艺流程涉及的部门(体系化)工艺流程涉及的部门有:各公司的技术部、生产部、质检部、和集团采购部.2、管理责任(制度化)(1)各公司技术部责任a,制定合理的工艺流程文件各公司的技术部依据产品任务单,制定生产工艺流程的文件,工艺流程文件的主要是以下三种类:-—工艺过程卡片;-—工序卡片;——操作说明书;工艺流程的卡片和操作说明书中应包含:图纸(加工的工件图纸以及关键步骤和重要环节都有图纸说明)、加工工序、加工方法及对环境的要求、检验及方法、产品的包装、工时定额、材料和物耗定额、使用的设备和工装、加工工具、对特殊工件的吊装位置及方法、包装方法、加工的起始时间、责任者的签名等,总之应当是实际工作中涉及的工序和各个工序中要点(5M1E)都要简约地反映在流程中; -—注2:工时定额和物耗定额:在实际中灵活应用和执行,对于首件和单件生产可以是定性管理;对于3-5件的小批量生产应当是首件完成后,对出其余件进行的半定量管理,就是给个范围值;对于成熟的大批量生产件应当是定量管理,就是应当给出固定的定额;—-注3:可以有空项,按实际生产中需要的项目编写,应当简要全面部不应当有漏项;各个公司在制定工艺流程时,可以是表格式、卡片式、文字表述式,只要能在实际生产中,对生产的产品有以下作用即可-—加工的指导、检验指导、记录完整(可以追溯产品的加工历史);b,根据生产出现的问题,可以用工艺流程附加单的形式进行补充及修改,必要时废除老工艺,重新制定新工艺;c,会同质检部门处理质量异常问题.(2)各公司生产部责任a,生产操作者应当随时自我查对,检查是否符合流程的规定与相关的质量标准,即开展自检工作。
- 1、下载文档前请自行甄别文档内容的完整性,平台不提供额外的编辑、内容补充、找答案等附加服务。
- 2、"仅部分预览"的文档,不可在线预览部分如存在完整性等问题,可反馈申请退款(可完整预览的文档不适用该条件!)。
- 3、如文档侵犯您的权益,请联系客服反馈,我们会尽快为您处理(人工客服工作时间:9:00-18:30)。
1、 目的
为规范公司的管理,提升产品质量,保持高标准的生产工艺,特
制定本规定。
2、 各工序工艺标准
3、 切割
3.1 切割作业标准
3.1.1 按交货期顺序切割作业,做到当日单,当日切割完毕。
3.1.2 切割顺序:先红单(补片单)绿单(加急单)后正常单,必要时
应做到“立等切割”和“另架专送”。
..3 配对玻璃切割:(指玻璃厚度不同配对、颜色不同配对、品种不同配对)严格按流程单顺序切割,与其相对应的玻璃也
必须相同对应。
..4 切成玻璃应擦去玻璃粉,贴上标签。
标签贴在玻璃正中位置。
3.2 切割质量标准
3.2.1 磨边位:4~6㎜玻璃为3㎜;8~10㎜玻璃为4㎜;12㎜玻璃为5
㎜;15、19㎜玻璃为6㎜;
..2 对角线:允许值为<2㎜;
3.2.3 撕边(爆边)<2㎜;
3.2.4 无瑕疵:无结石、无气泡、无划痕、无纸纹、无发霉。
同一客户
同一批玻璃无色差。
3.3 玻璃的摆放、移送、交接、生产日报表填写、界区卫生等按本岗位
作业指导书执行。
4、磨边
4.1 磨边作业标准
4.1.1 磨边作业按交货期顺序,进入辖区的玻璃确保48小时加工完毕并移送。
4.1.2 遇红单(补片单)绿单(加急单)应优先安排加工。
4.2 磨边质量标准
4.2.1 磨边成品规格标准:+0-2,对角线<2㎜;遇中空、夹胶和配对玻
璃时,应严格控制规格标准。
..2 磨边成品倒边标准:4~10㎜玻璃为:1~1.5㎜;12~19㎜玻璃为1.5~2㎜;弯G玻璃倒大边为4~5㎜。
..3 磨边外观质量标准:
直边机与双边机:全部机磨到位,直边与边缘经抛光,表面
光滑。
倒棱与粗磨:边部无毛刺不刮手,呈白色状态。
粗磨无暗裂,全部呈白色状态,符合钢化条件。
玻璃表面无划痕刮伤。
4.3 玻璃的摆放移送、交接、生产日报表填写、界区卫生等按本岗位作业指导书执行。
5、钻孔(异形)
5.1 钻孔(异形)作业按交货期顺序,遇红单(补片单)绿单(加急
单)应优先安排加工。
加工完毕应及时移送。
5.2 钻孔质量标准:
孔径4~40㎜,其孔位偏移允许值范围±1㎜;
孔径40~200㎜,其孔位偏移允许值范围±1.5~2㎜;
钻孔作业要求画线准确,下钻平稳,不爆孔,玻璃表面无划
痕。
遇“夹”或“缺”时,有模板、配件的,要注意察看或套用
模板、配件。
5.3 异形加工质量标准:
5.3.1 异形加工规格标准为+0-5㎜;异形加工有模板时,一定要套用模板。
5.3.2 异形加工边缘部质量标准:
边缘部圆滑、顺畅,无明显接头
粗磨、抛光,达到光亮
玻璃表面无划痕、无划伤。
5.4 玻璃的摆放移送、交接、生产日报表填写、界区卫生等按本岗位作业指导书执行。
6、清洗
6.1 进入辖区的玻璃当日应全部清洗完毕,遇镀膜玻璃应第一时间清
洗,缩短在本岗位停留时间。
6.2 清洗质量标准:
6.2.1 清洗后的玻璃:玻璃表面干净、无玻璃粉、无残留物、无水分。
6.2.2 清洗后的玻璃:应符合钢化条件“下片台使用灯光照明检出爆
边、爆孔、爆角、暗伤、裂纹、水纹、纸纹、发霉等。
6.3 清洗玻璃分类标准:
6.3.1 按玻璃厚度分类
6.3.2 按交货期分类,每一铁架上摆放的玻璃交货期只限连续2天。
6.3.3 按玻璃品种分类,即白玻与色玻分类,普通玻璃与特种玻璃分类。
6.4 玻璃的的摆放、移送、交接、生产日报表填写、界区卫生等按本岗
位作业指导书执行。
7、钢化
7.1 钢化作业标准:
7.1.1 钢化炉实行定人操作,行车实行有证操作。
7.1.2 钢化成品率>99%,钢化破片,应及时、准确补片。
7.1.3 所有入炉玻璃均应检验。
内容有:核对尺寸、孔位、孔径、孔
数、孔夹、缺位置。
玻璃有无结石、气泡、划痕、裂纹、暗伤、
纸纹、水纹、发霉等。
7.2 钢化操作参数:
玻璃厚度 ㎜456810121519冬夏季
温度 ℃730730730715705690670665/
加热时间
(秒)
15020023037050071012001500/冷却与急冷
(秒)
60110130280420540900100±50
7.3 成品玻璃质量标准:
7.3.1 成品玻璃形状完整、不爆边、不掉角。
7.3.2 玻璃表面无辊痕、麻点、无波纹、彩虹。
7.3.3 平板玻璃弯曲度<0.5%,即1m<5㎜。
7.3.4 成品玻璃主要性能达到钢化玻璃标准(抗冲击强度、抗弯强度、碎片颗粒)
7.4 成品玻璃入库标准:
7.4.1 入库玻璃全部贴有标签,两片玻璃间垫塑胶片或垫纸。
7.4.2 入库玻璃应制作生产日报表,“单、物”相符,按规定交接签收。
7.4.3 入库玻璃应分类摆放,即散客户玻璃规格在>2000㎜×1600㎜以
内。
有专用木货架的应上架,没有专用木货架的应集中放置在专
用铁架上。
8、 夹胶
8.1 夹胶作业按交货期顺序,遇红单(补片单)绿单(加急单)应优先安排加工。
8.2 夹胶的工作标准:
8.2.1 上片时应检查玻璃内侧,确保无灰尘、无杂物、无水分。
8.2.2 夹胶作业铁夹不得超出胶条位置。
8.2.3 使用的胶水应是合格品,需确保无杂质、无沉淀物、不进水。
8.2.4 收片时要清洁玻璃外表,确保不残留胶水。
8.3 成品外观质量标准:
8.3.1 玻璃表面不允许有气泡、脱胶现象。
8.3.2 不允许有裂纹。
8.3.3 爆边的长度或宽度不超过玻璃厚度。
8.3.4 直径500㎜圆内杂质3㎜<2个。
8.3.5 直径300㎜圆内气泡1~2㎜<2个。
8.3.6 合片后10㎜以下玻璃,边长1200~2400,±1㎜;10㎜以上玻璃,
边长1200×2400,±2㎜;
8.4 夹胶作业的时间控制标准:
8.4.1 4~6㎜:夏季晴天2~3小时,阴天3小时;冬季晴天4~5小时,阴
天5~6小时。
8.4.2 8㎜以上:夏季晴天3~4小时,阴天4小时;冬季晴天5~6小时,
阴天6~7小时。
8.4.3 有色玻璃:夏季14:00以前生产完毕,冬季13:10以前生产完毕。
8.5 玻璃的摆放、移送交接、生产日报表填写、界区卫生等按本岗位作业指导书执行。
9、中空
9.1 中空作业按交货期顺序,遇红单(补片单)绿单(加急单)应优先安排生产。
9.2 中空作业标准:
9.2.1 上片(清洗)时应核对尺寸,检查对角线,允许值为<2㎜。
9.2.2 合并时,两片玻璃应对齐,标签贴于玻璃左上角。
9.2.3 下片放置铁架时,两片玻璃间应垫泡沫胶片。
9.2.4 双组份胶按规定配制,生产作业时掌握好使用量,杜绝浪费。
9.3 中空成品质量标准:
9.3.1 外观尺寸:
玻璃长度 ㎜允许偏差 ㎜
<1000+1.0 -2.0
1000~2000+1.0 -2.5
2000~3000+1.5 -3.0 ..2 中空玻璃密封:
中空玻璃密封为双道密封
外层为密封胶,胶深6㎜,密封胶表面光滑饱满、无裂缝现
象。
中空的固化时间:密封胶4小时,结构胶7天。
内层为丁基胶,打胶应均匀、饱满、连线无空隙。
9.3.3 中空玻璃表面:
外表面干净、无污物、玻璃无划痕。
内表面透视良好,无污迹及胶粘剂飞溅现象。
合成片后两片玻璃边沿部整齐,标签牢固粘贴在左上方。
9.4 中空检测和建档:
9.4.1 中空玻璃检测采用浸泡法检测漏气。
9.4.2 中空玻璃检测必须是成品后6小时进行,每周二、五检测。
9.4.3 中空玻璃检测是将玻璃浸泡容器中,水深200㎜以上,浸泡时间72
小时以上。
浸泡后玻璃内部不结露为合格。
..4 建档:检测应做记录,按格式化表格内容详细记录,注明检测时间、受检客户、检测人姓名。
..5 检测内容必须客观、真实、数据准确。
..6 检测发现不良品或不合格品应反映上报。
10、本制度自2008年4月15日起实施,未尽事宜在执行中不断完善,如有
不明之处请向生产部咨询。