不同切削用量对加工表面粗糙度的影响
机械加工表面粗糙度的影响因素
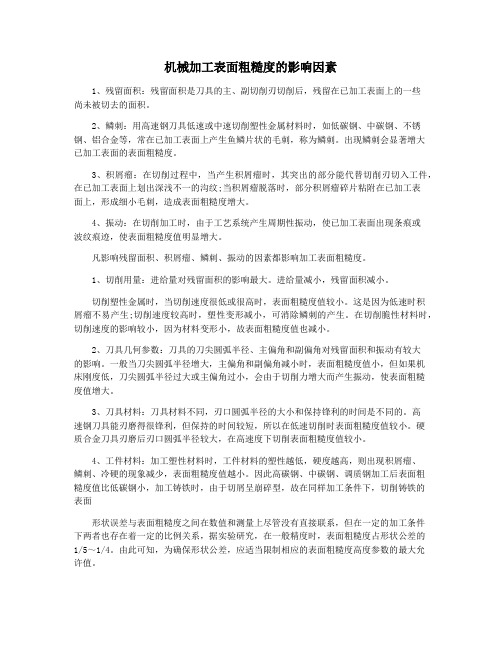
机械加工表面粗糙度的影响因素1、残留面积:残留面积是刀具的主、副切削刃切削后,残留在已加工表面上的一些尚未被切去的面积。
2、鳞刺:用高速钢刀具低速或中速切削塑性金属材料时,如低碳钢、中碳钢、不锈钢、铝合金等,常在已加工表面上产生鱼鳞片状的毛刺,称为鳞刺。
出现鳞刺会显著增大已加工表面的表面粗糙度。
3、积屑瘤:在切削过程中,当产生积屑瘤时,其突出的部分能代替切削刃切入工件,在已加工表面上划出深浅不一的沟纹;当积屑瘤脱落时,部分积屑瘤碎片粘附在已加工表面上,形成细小毛刺,造成表面粗糙度增大。
4、振动:在切削加工时,由于工艺系统产生周期性振动,使已加工表面出现条痕或波纹痕迹,使表面粗糙度值明显增大。
凡影响残留面积、积屑瘤、鳞刺、振动的因素都影响加工表面粗糙度。
1、切削用量:进给量对残留面积的影响最大。
进给量减小,残留面积减小。
切削塑性金属时,当切削速度很低或很高时,表面粗糙度值较小。
这是因为低速时积屑瘤不易产生;切削速度较高时,塑性变形减小,可消除鳞刺的产生。
在切削脆性材料时,切削速度的影响较小,因为材料变形小,故表面粗糙度值也减小。
2、刀具几何参数:刀具的刀尖圆弧半径、主偏角和副偏角对残留面积和振动有较大的影响。
一般当刀尖圆弧半径增大,主偏角和副偏角减小时,表面粗糙度值小,但如果机床刚度低,刀尖圆弧半径过大或主偏角过小,会由于切削力增大而产生振动,使表面粗糙度值增大。
3、刀具材料:刀具材料不同,刃口圆弧半径的大小和保持锋利的时间是不同的。
高速钢刀具能刃磨得很锋利,但保持的时间较短,所以在低速切削时表面粗糙度值较小。
硬质合金刀具刃磨后刃口圆弧半径较大,在高速度下切削表面粗糙度值较小。
4、工件材料:加工塑性材料时,工件材料的塑性越低,硬度越高,则出现积屑瘤、鳞刺、冷硬的现象减少,表面粗糙度值越小。
因此高碳钢、中碳钢、调质钢加工后表面粗糙度值比低碳钢小,加工铸铁时,由于切屑呈崩碎型,故在同样加工条件下,切削铸铁的表面形状误差与表面粗糙度之间在数值和测量上尽管没有直接联系,但在一定的加工条件下两者也存在着一定的比例关系,据实验研究,在一般精度时,表面粗糙度占形状公差的1/5~1/4。
简述降低表面粗糙度的措施
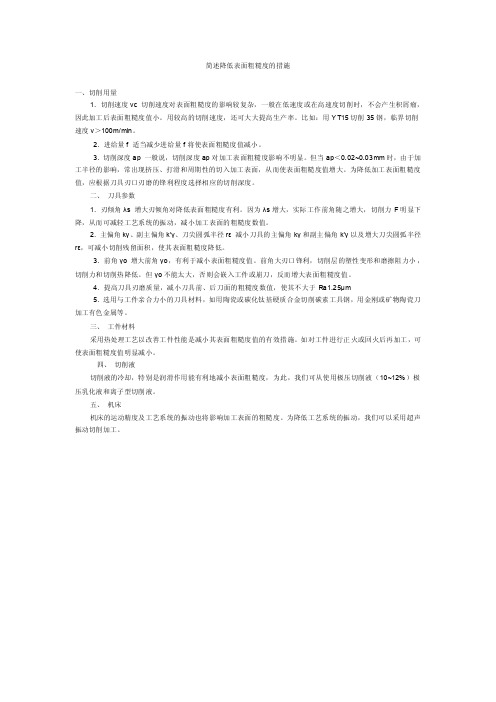
简述降低表面粗糙度的措施一、切削用量1.切削速度vc 切削速度对表面粗糙度的影响较复杂,一般在低速度或在高速度切削时,不会产生积屑瘤,因此加工后表面粗糙度值小。
用较高的切削速度,还可大大提高生产率。
比如:用Y T15切削35钢,临界切削速度v>100m/min。
2.进给量f 适当减少进给量f将使表面粗糙度值减小。
3.切削深度ap 一般说,切削深度ap对加工表面粗糙度影响不明显。
但当ap<0.02~0.03mm时,由于加工半径的影响,常出现挤压、打滑和周期性的切入加工表面,从而使表面粗糙度值增大。
为降低加工表面粗糙度值,应根据刀具刃口刃磨的锋利程度选择相应的切削深度。
二、刀具参数1.刃倾角λs 增大刃倾角对降低表面粗糙度有利。
因为λs增大,实际工作前角随之增大,切削力F明显下降,从而可减轻工艺系统的振动,减小加工表面的粗糙度数值。
2.主偏角kγ、副主偏角k’γ、刀尖圆弧半径rε 减小刀具的主偏角kγ和副主偏角k’γ以及增大刀尖圆弧半径rε,可减小切削残留面积,使其表面粗糙度降低。
3.前角γo 增大前角γo,有利于减小表面粗糙度值。
前角大刃口锋利,切削层的塑性变形和磨擦阻力小,切削力和切削热降低。
但γo不能太大,否则会嵌入工件或崩刀,反而增大表面粗糙度值。
4.提高刀具刃磨质量,减小刀具前、后刀面的粗糙度数值,使其不大于Ra1.25μm5.选用与工件亲合力小的刀具材料,如用陶瓷或碳化钛基硬质合金切削碳素工具钢,用金刚或矿物陶瓷刀加工有色金属等。
三、工件材料采用热处理工艺以改善工件性能是减小其表面粗糙度值的有效措施。
如对工件进行正火或回火后再加工,可使表面粗糙度值明显减小。
四、切削液切削液的冷却,特别是润滑作用能有利地减小表面粗糙度,为此,我们可从使用极压切削液(10~12%)极压乳化液和离子型切削液。
五、机床机床的运动精度及工艺系统的振动也将影响加工表面的粗糙度。
为降低工艺系统的振动,我们可以采用超声振动切削加工。
2.2 切削对表面加工的影响(了解)
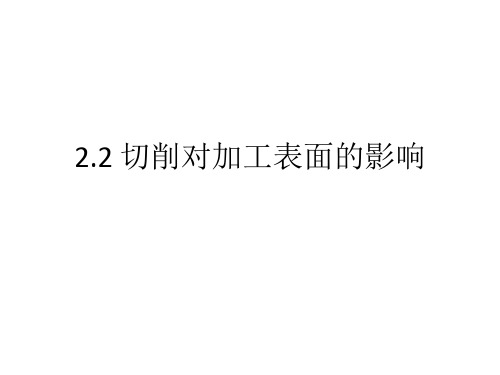
在切削过程中,由于切削力的作用,工件已
加工表面产生了很大的塑性变形且温度升 高。 而晶格扭曲,晶粒长大、破碎,阻碍了表 层金属的进一步变形,使材料强化,硬度提高; 同时较高的切削温度又将引起金属的相变。
可见,工件已加工表面的硬度变化就是这种 强化和相变作用的综合结果。
当塑性变形引起的强化起主导作用时,已 加工表面就硬化;当较高的切削温度引起的 相变起主导作用时,则根据相变的具体情况 而定,如在磨削淬火钢时,若发生退火,则表层 硬度降低,但在充分冷却的条件下,却可能引 起二次淬火而使表层硬度提高。
余面积、积屑瘤、振动波纹、切削力、切 削热等。 要做到这些,可以从刀具材料、刀
具角度、切削用量、工件材料、切削液等 多方面着手,尽可能地減軽以上因素对工件 已加工表面质量的不良影响 。
2.积屑瘤
在采用中等切削速度而又能形成连续性切 屑的情况下,加工一般钢料或其他塑性材料 时,切屑沿刀具前面滑出时,其底层受到很大 的摩擦力 。 当摩擦阻力超过切屑内部分子 间的结合力时, 一部分金属停滞下来,使刀具 切削刃附近的前面上粘附上一块很硬的金 属 。 这块很硬的金属称为积屑瘤 。
在切削处于相对稳定的状态时,积屑 瘤 可 以代替刀刃进行切削,粗加工时对刀刃有保 护作用 。 但积屑瘤轮廓很不规则,切削时会 将工件表面划出深浅、宽窄不一的沟纹;脱
生松动,影响传动副的工作性能。
还有一些其他原因,如鱗刺、刀具的边界 磨损、排屑不 畅而划伤工件已加工表面等, 均会使表面粗糙度值增大。
二、 表层材质变化
1.加工硬化 加工硬化是指在切削过程中,工件已加
工表面受刀刃和后面的挤压和摩擦而产生 塑性变形, 使表层组织发生变化,硬度显著提 高的现象。 其硬化层深度可以达到 0·02 -0. 30 mm,表层硬度约为原工件材料的1. 2-2倍。
影响机械加工表面粗糙度的几个因素及措施

职教类影响机械加工表面粗糙度的几个因素及措施摘要:表面粗糙度是零件表面所具有的微小峰谷的不平程度,它是评价零件的一项重要指标。
一般说来,它的波距和波高都比较小,是一种微观的几何形状误差。
对机械加工表面,表面粗糙度是由切削时的刀痕,刀具和加工表面之间的摩擦,切削时的塑性变形,以及工艺系统中的高频振动等原因所造成的。
表面粗糙度是检验零件质量的主要依据,它的选择直接关系到生产成本、产品的质量、使用寿命。
关键词:机械加工表面粗糙度提高措施随着工业技术的飞速发展,机器的使用要求越来越高,一些重要零件在高压力、高速、高温等高要求条件下工作,表面层的任何缺陷,不仅直接影响零件的工作性能,而且还可能引起应力集中、应力腐蚀等现象,将进一步加速零件的失效,这一切都与加工表面质量有很大关系。
因而表面质量问题越来越受到各方面的重视。
一、机械加工表面粗糙度对零件使用性能的影响表面粗糙度对零件的配合精度,疲劳强度、抗腐蚀性,摩擦磨损等使用性能都有很大的影响。
1、表面质量对零件配合精度的影响(1)对间隙配合的影响由于零件表面的凹凸不平,两接触表面总有一些凸峰相接触。
表面粗糙度过大,则零件相对运动过程中,接触表面会很快磨损,从而使间隙增大,引起配合性质改变,影响配合的稳定性。
特别是在零件尺寸和公差小的情况下,此影响更为明显。
(2)对过盈配合的影响粗糙表面在装配压入过程中,会将相接触的峰顶挤平,减少实际有效过盈量,降低了配合的连接强度。
2、表面质量对疲劳强度的影响零件表面越粗糙,则表面上的凹痕就越深明,产生的应力集中现象就越严重。
当零件受到交变载荷的作用时,疲劳强度会降低,零件疲劳损坏的可能性增大。
3、表面质量对零件抗腐蚀性的影响零件表面越粗糙,则积聚在零件表面的腐蚀气体或液体也越多,且通过表面的微观凹谷向零件表层渗透,形成表面锈蚀。
4、表面质量对零件摩擦磨损的影响两接触表面作相对运动时,表面越粗糙,摩擦系数越大,摩擦阻力越大,因摩擦消耗的能量也越大,并且还影响零件相对运动的灵活性。
浅谈加工表面粗糙度和物理力学性能的影响因素研究
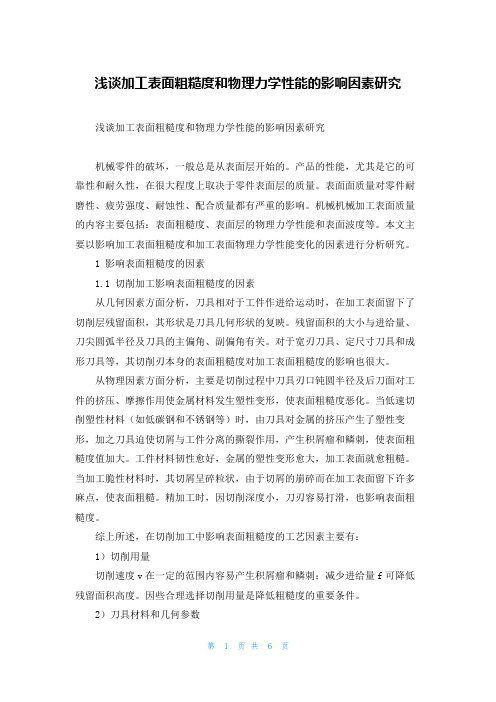
浅谈加工表面粗糙度和物理力学性能的影响因素研究浅谈加工表面粗糙度和物理力学性能的影响因素研究机械零件的破坏,一般总是从表面层开始的。
产品的性能,尤其是它的可靠性和耐久性,在很大程度上取决于零件表面层的质量。
表面面质量对零件耐磨性、疲劳强度、耐蚀性、配合质量都有严重的影响。
机械机械加工表面质量的内容主要包括:表面粗糙度、表面层的物理力学性能和表面波度等。
本文主要以影响加工表面粗糙度和加工表面物理力学性能变化的因素进行分析研究。
1 影响表面粗糙度的因素1.1 切削加工影响表面粗糙度的因素从几何因素方面分析,刀具相对于工件作进给运动时,在加工表面留下了切削层残留面积,其形状是刀具几何形状的复映。
残留面积的大小与进给量、刀尖圆弧半径及刀具的主偏角、副偏角有关。
对于宽刃刀具、定尺寸刀具和成形刀具等,其切削刃本身的表面粗糙度对加工表面粗糙度的影响也很大。
从物理因素方面分析,主要是切削过程中刀具刃口钝圆半径及后刀面对工件的挤压、摩擦作用使金属材料发生塑性变形,使表面粗糙度恶化。
当低速切削塑性材料(如低碳钢和不锈钢等)时,由刀具对金属的挤压产生了塑性变形,加之刀具迫使切屑与工件分离的撕裂作用,产生积屑瘤和鳞刺,使表面粗糙度值加大。
工件材料韧性愈好,金属的塑性变形愈大,加工表面就愈粗糙。
当加工脆性材料时,其切屑呈碎粒状,由于切屑的崩碎而在加工表面留下许多麻点,使表面粗糙。
精加工时,因切削深度小,刀刃容易打滑,也影响表面粗糙度。
综上所述,在切削加工中影响表面粗糙度的工艺因素主要有:1)切削用量切削速度v在一定的范围内容易产生积屑瘤和鳞刺;减少进给量f可降低残留面积高度。
因些合理选择切削用量是降低粗糙度的重要条件。
2)刀具材料和几何参数实践表明,在切削条件相同时,用硬质合金刀具加工的工作表面粗糙度比用高速钢刀具加工的低。
用金钢石车刀加工因不易形成积屑瘤,故可获得粗糙度很低的表面。
刀类圆弧半径rE、主偏角KC和副偏角kcC均影响残留面积的大小。
刀具及切削参数对加工表面粗糙度的影响
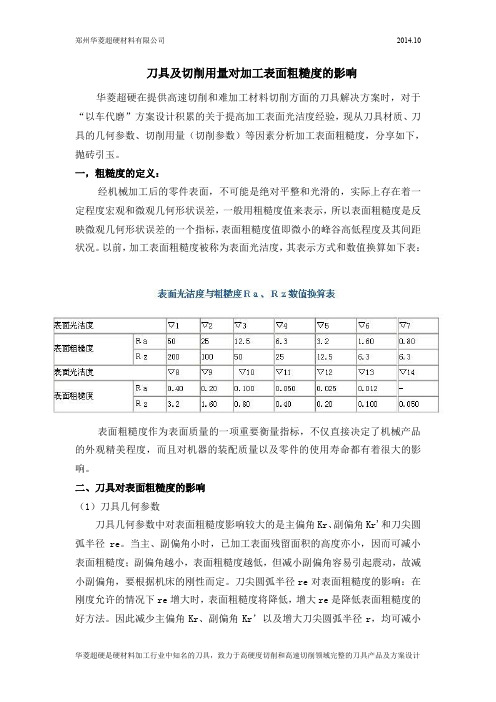
刀具及切削用量对加工表面粗糙度的影响华菱超硬在提供高速切削和难加工材料切削方面的刀具解决方案时,对于“以车代磨”方案设计积累的关于提高加工表面光洁度经验,现从刀具材质、刀具的几何参数、切削用量(切削参数)等因素分析加工表面粗糙度,分享如下,抛砖引玉。
一,粗糙度的定义:经机械加工后的零件表面,不可能是绝对平整和光滑的,实际上存在着一定程度宏观和微观几何形状误差,一般用粗糙度值来表示,所以表面粗糙度是反映微观几何形状误差的一个指标,表面粗糙度值即微小的峰谷高低程度及其间距状况。
以前,加工表面粗糙度被称为表面光洁度,其表示方式和数值换算如下表:表面粗糙度作为表面质量的一项重要衡量指标,不仅直接决定了机械产品的外观精美程度,而且对机器的装配质量以及零件的使用寿命都有着很大的影响。
二、刀具对表面粗糙度的影响(1)刀具几何参数刀具几何参数中对表面粗糙度影响较大的是主偏角Kr、副偏角Kr'和刀尖圆弧半径re。
当主、副偏角小时,已加工表面残留面积的高度亦小,因而可减小表面粗糙度;副偏角越小,表面粗糙度越低,但减小副偏角容易引起震动,故减小副偏角,要根据机床的刚性而定。
刀尖圆弧半径re对表面粗糙度的影响:在刚度允许的情况下re增大时,表面粗糙度将降低,增大re是降低表面粗糙度的好方法。
因此减少主偏角Kr、副偏角Kr’以及增大刀尖圆弧半径r,均可减小残留面积的高度,从而降低表面租糙度。
以解决难加工材料切削和高速切削问题知名的华菱超硬刀具,“对于刀尖圆弧角的选择建议依据加工工件的刚性和粗糙度要求选择,如果刚性好,尽量选择大的圆弧角,不但可提高加工效率,亦可提高加工表面光洁度;但镗孔时或者切削细长轴或薄壁零件时因为系统刚性差,常选用较小的刀尖圆弧半径”,其刀具工程师做刀具选型方案时如是说。
具体的刀尖圆弧角与粗糙度值参见后文(走刀量、刀尖圆弧角、加工表面粗糙度三者的关系)。
(2)刀具材料当刀具材料与被加工材料金属分子亲和力大时,被加工材料容易与刀具粘结而生成积屑瘤和鳞刺,因此凡是粘结严重的,摩擦严重的,表面粗糙度就大,反之就小。
车床工件表面粗糙度的形成原因及解决措施
车床工件表面粗糙度的形成原因及解决措施表面粗糙度是机械加工中衡量加工质量的重要因素,表面粗糙度对零件和机器有着重要的意义。
但由于工件材料、切削加工方式、表面硬化等原因,造成了表面粗糙度值提高。
本文详细分析了车床工件表面粗糙度的形成原因,并提出相应的解决措施。
标签:车床工件:表面:粗糙度:原因:解决措施1.引言在实际的机械加工中,工件表面会存在许多高低不平的微小峰谷,这是因为切屑分离时塑性变形、工艺系统的振动以及刀具与已加工表面问的摩擦等因素的影响。
这些零件被加工表面上的微观几何形状误差称为表面粗糙度。
表面粗糙度对零件的耐磨性、耐腐蚀性、疲劳强度和配合性质都有很大影响。
本文详细分析了车床工件表面粗糙度的形成原因,并提出相应的解决措施,具有一定的实际意义。
2.影响工件表面粗糙度的原因2.1工件材料性能。
塑性金属材料在加工的过程中,刀具挤压金属材料,使其产生塑性变形,切屑和工件分离是由于刀具外力的挤压,表面出现撕裂现象,这严重影响表面粗糙度。
伴随着工件材料韧性的提高,在切屑过程中材料的塑性变形也就越大,加工表面粗糙度也就越差。
脆性材料在加工时,所切削形成的铁屑为颗粒状,在切屑崩碎的过程中,加工表面容易产生细小的坑点,提高表面粗糙度值。
2.2刀具切削加工。
在普通刀具在切屑过程中,切削表面势必会产生残留面积,残留面积的高度则是影响加工表面粗糙度的主要因素。
在整个加工过程中,刀具的进给量、主偏角、副偏角、圆弧半径则是造成切削残留面积的主要因素。
砂轮磨削加工过程中,砂轮上硬质颗粒断裂后形成微刃,其分布情况和外形对表面粗糙度有着直接的影响。
因为磨削加工表面是大量微刃在金属表面切削出细小的切削痕迹构成的,所形成的切削痕迹越细小、越密集则表面粗糙度就越好,相反切削痕迹粗大、分布疏散,则表面粗糙度越差。
2.3表面冷作硬化。
在普通刀具切削或砂轮磨削过程中,表面层金属由于刀具外在切削力和材料本身的塑性,使其晶格产生剪切、滑移、拉长、扭曲、破碎,宏观的表现特点则是材料表面层变硬,屈服点提高,延生率降低。
影响加工表面粗糙度的工艺因素及其改善措施
3. 采用适当的冷却方法,如切削液,以降低切削温度和减少热量对刀具的影响。
4. 定期检查和更换刀具,以确保刀具处于良好状态,从而保证加工表面质量。
工件材料对表面粗糙度的影响
04
硬度过低的工件材料在加工过程中容易产生塑性变形,使得工件表面粗糙度增加。
刀具磨损对表面粗糙度的影响
03
总结词
随着刀具磨损的增加,切削力通常会增大。这主要是因为刀具磨损导致切削刃变钝,切削刃与工件之间的摩擦增大,切削力也随之增大。
详细描述
在切削过程中,刀具的切削刃会逐渐磨损,导致切削刃变钝。钝的切削刃与工件表面的摩擦增大,使得切削力增加。这不仅会影响切削过程的稳定性,还可能导致切削热增加,进一步加剧刀具磨损。
影响加工表面粗糙度的工艺因素及其改善措施
汇报人:
2024-01-04
切削用量对表面粗糙度的影响刀具几何参数对表面粗糙度的影响刀具磨损对表面粗糙度的影响工件材料对表面粗糙度的影响切削液对表面粗糙度的影响改善加工表面粗糙度的措施
目录
切削用量对表面粗糙度的影响
01
01
02
在切削塑性材料时,适当降低切削速度可以有效减小表面粗糙度值。在切削脆性材料时,切削速度对表面粗糙度的影响较小。
切削速度越高,切削力越大,切削温度越高,从而使得工件材料软化,容易产生塑性变形,导致表面粗糙度值增大。
进给量增大,切削厚度增加,切削力也相应增大,切削过程中工件材料的塑性变形增大,导致表面粗糙度值增大。
适当减小进给量,可以减小表面粗糙度值。但进给量过小会导致切削力过小,反而使得表面粗糙度值增大。因此,需要根据工件材料、刀具材料和加工要求等因素选择合适的进给量。
切削参数变化对加工表面质量的影响—
从图可以看出,残留应力在切削速度方向和进给方向呈现 出不同的变化规律。在切削速度方向随着切削速度增大, 残留应力由残留压应力逐渐变为残留拉应力;在进给方向, 改变切削速度时,残留应力一直是残留压应力。 改变切削速度时,相应地改变了已加工表面所承受的塑性 变形、切削温度的大小与分布情况,因而影响己加工表面 的残留应力。提高切削速度时,切削温度引起的热应力所 占比重增大,因而切削速度方向的残留压应力减小而残留 拉应力增大。
由残留压应力逐渐变为残留拉应力;在进给方向, 改变切削速度时,残留应力仍然是残留压应力。 2. 当进给量增大时,进给方向的残留压应力逐渐减 小。 3. 切削深度变化时,当切削深度为某一数值时,进 给方向的残留压应力有一极大值。
切削用量选择的基本原则:
1.根据工件加工余量和粗、精加工要求,选定背 吃刀量。 2.根据加工工艺系统允许的切削力,其中包括机 床进给系统、工件刚度及精加工时表面粗糙度要求, 确定进给量。 3.根据刀具耐用度,确定切削速度。
2.3切削参数变化对 加工表面质量的影响
表面质量
已加工表面质量:是指零件在加工后其表面
的状态。 包括: 1、零件表面层的微观几何结构,即表面形貌。 2、表层金属材料性质发生变化的情况。
表面质量包括:表面形貌和表面层材质变化
•表面粗糙度 •表面波度
•残余应力 •加工硬化 •表层金相组织变化
切削参数的影响
► 切削参数包括:
1、切削速度v。2、进给量ƒ。3、切削深度ap。ຫໍສະໝຸດ 1、切削速度对表面质量的影响
在不使用切削液的条件下,切削速度增大到一定值后,表面 粗糙度随着切削速度增大而降低。
在实际生产中,切削液的使用很好的改善了加工表面质量。 切削速度增大一定值时,其变化对表面粗糙度的影响不明显。 较大的切削速度下,都可以得到镜面。
表面粗糙度及其影响因素
表面粗糙度及其影响因素一、切削加工中影响表面粗糙度的因素影响表面粗糙度的因素主要有几何因素和物理因素。
1.几何因素:式中 f ——进给量。
Kr ——主偏角。
Kr’——副偏角考虑刀尖圆弧角:式中 f ——进给量。
r ——刀尖圆弧半径。
如图11-8、9所示,用刀尖圆弧半径r=0的车刀纵车外圆时,每完成一单位进给量f后,留在已加工表面上的残留面积,它的高度Rmax即为理论粗糙度的轮廓最大高度Ry。
图11- 8 图11- 9图11- 10 加工后表面实际轮廓和理论轮廓切削加工后表面粗糙度的实际轮廓形状,一般都与纯几何因素所形成的理论轮廓有较大的差别,如图11-10。
这是由于切削加工中有塑性变形发生的缘故。
生产中,若使用的机床精度高和材料的切削加工性好,选用合理的刀具几何形状、切削用量和在刀具刃磨质量高、工艺系统刚性足够情况下,加工后表面实际粗糙度接近理论粗糙度,这样减小表面粗糙度数值、提高加工表面质量的措施,主要是减小残留面积的高度Ry。
2.物理因素多数情况下是在已加工表面的残留面积上叠加着一些不规则的金属生成物、粘附物或刻痕。
形成它们的原因有积屑瘤、鳞刺、振动、摩擦、切削刃不平整、切屑划伤等。
3.积屑瘤的影响积屑瘤的生成、长大和脱落将严重影响工件表面粗糙度。
同时,由于部分积屑瘤碎屑嵌在工件表面上,在工件表面上形成硬质点。
见图11-11。
图11- 11 图11- 12鳞刺的影响鳞刺的出现,使已加工表面更为粗糙不平。
鳞刺的形成分为:抹拭阶段:前一鳞刺已经形成,新鳞刺还未出现;而切屑沿着前刀面流出,切屑以刚切离的新鲜表面抹拭刀——屑摩擦面,将摩擦面上有润滑作用的吸附膜逐渐拭净,以致摩擦系数逐渐增大,并使刀具和切屑实际接触面积增大,为这两相摩擦材料的冷焊创造条件,如图11-12(a)。
导裂阶段:由于在第一阶段里,切屑将前刀面上的摩擦面抹拭干净,而前刀面与切屑之间又有巨大的压力作用着,于是切屑与刀具就发生冷焊现象,切屑便停留在前刀面上,暂时不再沿前刀面流出。
- 1、下载文档前请自行甄别文档内容的完整性,平台不提供额外的编辑、内容补充、找答案等附加服务。
- 2、"仅部分预览"的文档,不可在线预览部分如存在完整性等问题,可反馈申请退款(可完整预览的文档不适用该条件!)。
- 3、如文档侵犯您的权益,请联系客服反馈,我们会尽快为您处理(人工客服工作时间:9:00-18:30)。
实验二 不同切削用量对加工表面粗糙度的影响
2.实验目的
(1)了解工件切削加工中加工表面粗糙度的标志、形成过程及影响因素; (2)掌握采用类比法来确定工件加工表面粗糙度的方法; 3.实验装置及实验材料
(1)卧式车床 (C6132型号) 1台; (2)硬质合金车刀
(前角γ0=10°、主偏角κr =45°、副偏角κr ‘=15°、后角α0=10°、刃倾角λs =4°、刀尖圆弧半径r e =0.5mm ) 1把;
(前角γ0=10°、主偏角κr =45°、副偏角κr ‘=5°、后角α0=10°、刃倾角λs =4°、刀尖圆弧半径r e =0.5mm ) 1把;
(前角γ0=5°、主偏角κr =45°、副偏角κr ‘=15°、后角α0=10°、刃倾角λs =4°、刀尖圆弧半径r e =0.5mm ) 1把; (3)试棒(45钢 , Ф40mm, L=150mm ) 若干; (4)表面粗糙度样板 1套; (5)油石 1块; (6)切削液 若干 4. 实验原理
(1)表面粗糙度Ra 及其影响因素
影响工件加工表面粗糙度的主要因素有:
①切削时刀刃在加工表面上遗留下的刀痕。
这是形成加工表面微观不平的主要原因。
②切削塑性材料时,在一定的切削速度下,由于前刀面与切屑的挤压和磨擦作用而在刀尖处形成积屑瘤对工件加工表面的影响。
③刀具后刀面与加工表面的摩擦与挤压。
④切削脆性材料时,崩碎切屑形成的磨点痕迹。
⑤刀具副偏角κr ’的影响。
⑥加工系统产生振动,造成加工表面形成振纹。
(2)切削量及车刀几何形状对表面粗糙度Ra 的影响分析
①进给量ƒ影响
由图1-10和图1-11可知:加工表面残留面积高度h max 与进给量ƒ、主偏角κr 、副偏角κr ’及刀尖圆弧半径r e 有关。
当r e =0时,h max =
r
r ctg ctg f
'
κκ+ (1.1)
当r e >0时,h max =e
r f 82
(1.2)
图1-10 副偏角κr ’对加工表面残留面积的影响
图1-11 影响加工表面残留面积的因素
由式1.1、式1.2可看出,采用较小的进给量ƒ,加工表面残留面积高度较小,对减小粗糙度R a 值有利。
在实际切削过程中残留面积高度h max 比理论高度要大—些。
这是由于塑性材料在切削时所受到挤压变形、积屑瘤、切削刃的粗细、刀具变形、刀具与工件相对位置的改变以及振动等因素综合造成的。
②切削速度υ的影响
切削塑性材料,当切削速度υ小于5 m /min 或大于100 m /min 时,不易产生积屑瘤,对减小粗糙度Ra 值有利。
当切削速度υ在20--25 m /min ,且切削温度约为300ºC 时,切屑与刀具前刀面摩擦系数最大,此时积屑瘤高度最大,使粗糙度R a 值增加。
③切削深度αp 影响
切削深度αp 比进给量ƒ和切削速度υ对粗糙度R a 值的影响要小。
当αp 减小时,切削力减小,不易产生振动,对减小粗糙度R a 值有利。
④车刀几何形状的影响
a. 由式1、式2可看出,采用较小的主偏角κr或副偏角κr’,或刀尖有小圆弧(r e>0)时,都会减小加工表面残留面积,使粗糙度R a值减小;
b.选用较大的前角γ0,并用油石把前刀面和后刀面打磨得光一些,可减小积屑瘤的形成,也可使粗糙度R a值减小。
5.实验方法与步骤
(1)熟悉实验用车床的结构、操作方法和安全注意事项;
(2)用油石打磨实验用车刀的前刀面和后刀面;
(3)用双顶尖和拨盘将试件装夹在车床上;
(4)按照表1给定实验数据车削试件。
每次切削长度为40 mm,间隔10mm,每个试棒上做3组数据,如图1-12所示,计算出切削速度,记录于表1-2中;
图1-12 切削长度示意图
(5)用粗糙度样板比较且确定各试件上各加工段的表面粗糙度R a值,将R a填入表1-2中。
6、实验数据整理及分析
(1)整理实验数据,填写表1-2;
(2)根据表1中各组测得的的表面粗糙度R a值,分析ƒ、υ、αp、κr‘、γ0、、对粗糙度R a的影响机理。
7.思考题
如何合理的使用切削液?这将对加工表面粗糙度R a有何影响?
表1 -2 实验数据表。