铸件表面质量验收规范
铸件表面质量提升验收技术条件

铸件表面质量提升验收技术条件1 范围本文件规定了铸件分类、目测铸件技术要求、检验规则.本标准适用于中国一拖集团有限公司内/外供方采用砂型铸造,金属型铸造方法获得的黑色、有色合金铸件产品。
2 规范性引用文件下列文件对于本文件的应用是必不可少的.凡是注日期的引用文件,仅所注日期的版本适用于本文件。
凡是不注日期的引用文件,其最新版本(包括所有的修改单)适用于本文件.GB/T 6060。
1—1997 表面粗糙度比较样块铸造表面GB/T 15056-1994 铸造表面粗糙度评定方法Q/YT 014.2—2009 图样通用技术要求Q/YT 022。
4—2011 砂型机器造型铸件尺寸公差Q/YT 022。
10—2011 铸铁件机械加工余量Q/YT 303。
1-2011 球墨铸铁件验收技术条件Q/YT 303.2—2011 灰铸铁件验收技术条件Q/YT 303.3—2011 铸造碳钢件验收技术条件Q/YT 303.5-2011 铝合金铸件验收技术条件Q/YT 303。
6-2011 高锰钢履带板验收技术条件Q/YT 303。
7-2011 铜合金铸件验收技术条件Q/YT 303.9-2011 硅锰钢履带板验收技术条件3 铸件分类铸件根据其所处安装位置、工作条件及表面是否加工分三类,其定义和检验项目见表1。
表1 铸件分类4 目测铸件技术要求4.1 一般要求4.1.1 砂型铸造全部外露件和部分外露件表面粗糙度要求Ra25~Ra50。
金属铸造和有色件表面粗糙度要求Ra25,待加工表面允许降低一级。
4.1.2 铸件表面不得有影响零件强度、密封性能及严重影响外观的缺陷。
4.1.3 铸件采购、质量检查和供方可在保证铸件满足铸件验收技术条件的前提下,鼓励三方协商建立铸件外观质量标杆样件(即合格的最低标准实物)库,便于铸件外观质量验收参照标杆样件执行,低于此实物标准时为不合格。
4.2 灰铸铁件及碳钢铸件4.2.1 表面缺陷4.2.1.1 铸件表面不允许有冷隔、裂纹、孔洞贯穿内外表面的缺陷及机械加工不能去除的其它缺陷.4.2.1.2 铸件上的型砂、芯砂、披缝必须清理干净;其中,披缝非加工面不大于 2 mm,加工面不大于 3 mm;4.2.1.3 灰铸铁件表面允许存在的孔洞类缺陷见表 2;表 2 砂型铸造灰铸铁件表面允许存在的孔洞类缺陷4.2.1.4 碳钢铸件表面允许存在的孔洞类缺陷见表 3表 3 碳钢铸件表面允许存在的孔洞类缺陷4.2.1.5 铸件内、外表面应清理干净,不应有浮砂、粘砂、氧化皮。
压铸件品质检验规范

压铸件质检规范1、目的明确压铸件品质验收规范,规范检验动作,使检验、判定规范能达到一致性2、适用范围本规范适用于公司配套的锌合金压铸件的外观检验,包括毛坯、成品)完成铸造后机械加工的产品)。
3、技术要求3.1压铸件质量要求3.1.1压铸件应符合零件图样的规定。
3.1.2表面质量3.1.2.1压铸件表面粗糙度应符合GB/T6060.1的规定。
3.1.2.2压铸件表面不允许有裂纹、欠铸、疏松、气泡和任何穿透性缺陷。
3.1.2.3压铸件表面允许有擦伤、凹陷、缺肉和网状毛刺等缺陷。
但缺陷必须符合表1规定。
表1压铸件表面质量要求缺陷名称缺陷范围数值备注擦伤深度(mm)≤0.10面积不超过总面积的百分数5凹陷凹入深度(mm)≤0.30缺肉深度(mm)≤0.50长度不大于(mm)2所在面上不允许超过的数量2离压铸件边缘距离(mm)≥4间距(mm)≥10网状毛刺高度(mm)≤0.23.1.2.4压铸件的浇口、飞边、溢流口、隔皮、顶杆痕迹等应清理干净。
但允许留有痕迹。
3.1.2.5若图样无特别规定,有关压铸工艺部分的设置,如顶杆位置、分型线的位置、浇口和溢流口位置等由生产厂自行规定。
3.1.2.6压铸件需要特殊加工的表面,如抛光、喷丸、镀铬、涂覆、阳极氧化、化学氧化等须在图样上注明。
3.1.3压铸件机加工平面加工后的表面质量3.1.3.1不允许有影响使用的局部铸态表皮存在。
3.1.3.2不允许有超过表2规定的孔穴存在。
表2压铸件机加工平面允许的孔穴项目最大直径(mm)最大深度(mm)最多个数/cm2边缘间最小距离(mm)孔穴0.50.2243.1.4压铸件机械加工螺纹的表面质量3.1.4.1压铸件机械加工螺纹的头两扣不允许有任何缺陷,其余部分螺纹不允许有表3所规定的孔穴缺陷。
表3机械加工螺纹规定的孔穴缺陷范围螺距(mm)平均直径(mm)≤螺纹工作长度内个数≤深度(mm)≤两孔的边距(mm)≥≤0.751122>0.75 1.54 1.553.1.4.2压铸件不铸底孔加工后的螺纹表面质量见表4的规定。
铸造材料技术要求和验收规范
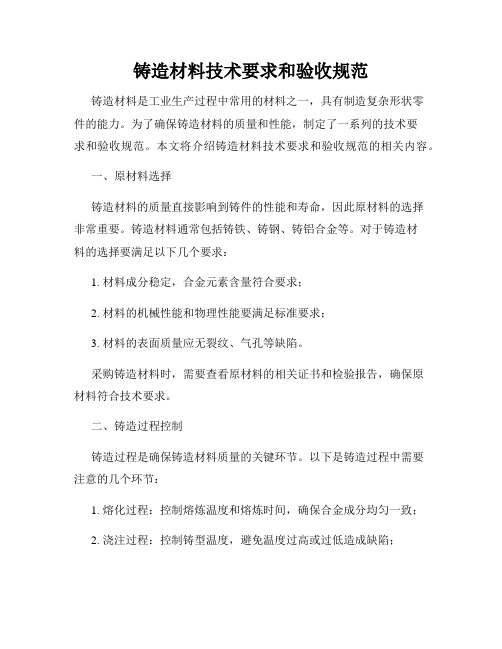
铸造材料技术要求和验收规范铸造材料是工业生产过程中常用的材料之一,具有制造复杂形状零件的能力。
为了确保铸造材料的质量和性能,制定了一系列的技术要求和验收规范。
本文将介绍铸造材料技术要求和验收规范的相关内容。
一、原材料选择铸造材料的质量直接影响到铸件的性能和寿命,因此原材料的选择非常重要。
铸造材料通常包括铸铁、铸钢、铸铝合金等。
对于铸造材料的选择要满足以下几个要求:1. 材料成分稳定,合金元素含量符合要求;2. 材料的机械性能和物理性能要满足标准要求;3. 材料的表面质量应无裂纹、气孔等缺陷。
采购铸造材料时,需要查看原材料的相关证书和检验报告,确保原材料符合技术要求。
二、铸造过程控制铸造过程是确保铸造材料质量的关键环节。
以下是铸造过程中需要注意的几个环节:1. 熔化过程:控制熔炼温度和熔炼时间,确保合金成分均匀一致;2. 浇注过程:控制铸型温度,避免温度过高或过低造成缺陷;3. 热处理过程:根据不同的铸造材料,进行适当的热处理,提高材料的性能;4. 温度控制:铸造材料的温度对最终产品的性能影响很大,需要控制好铸造温度。
三、铸造材料的质量检验铸造材料的质量检验是保证产品质量的重要环节。
以下是一些常见的铸造材料的质量检验方法:1. 成分分析:通过化学分析仪器来检测铸造材料的合金成分,以确保其符合标准要求;2. 金相检验:利用金相显微镜观察铸造材料的显微组织,评估其组织性能;3. 机械性能测试:通过拉伸试验、冲击试验等方法来测试铸造材料的力学性能;4. 铸件表面检查:观察铸件表面是否存在缺陷、夹杂物等;根据不同的铸造材料,可以选择相应的检验方法来确保铸造材料质量。
四、验收规范为了确保铸造材料的质量,制定了一系列的验收规范。
以下是一些常见的验收规范要求:1. 材料的外观质量:表面应无裂纹、气孔、夹杂物等缺陷;2. 成分符合要求:合金成分应符合设计要求,不得低于或高于标准限制;3. 机械性能:铸造材料的抗拉强度、屈服强度、伸长率等力学性能应符合标准;4. 金相组织:铸造材料的金相组织应均匀细致,不得存在夹杂物和非金属夹杂。
铸件质量检验标准

—
—
—
—
—
—
—
—
0.64
0.72
0.80
0.9
1.0
1.1
1.2
1.4
1.6
1.8
2.0
2.2
2.6
2.8
3.2
3.6
4.0
4.6
5
6
7
7
8
9
10
11
13
1600
2500
4000
6300
2500
4000
6300
10000
—
—
—
—
—
—
—
—
—
—
—
—
—
—
—
0.24
0.26
0.28
0.32
0.36
0.40
0.46
0.50
0.56
0.64
0.70
0.78
0.9
1.0
1.1
1.3
1.4
1.6
1.8
2.0
2.2
2.6
2.8
CF3M
ASTM
A351
0.03 1.5 1.5 17~21 0.04 0.04 9~13 2~3
CF8M
ASTM
A351
0.08 1.5 1.5 18~21 0.04 0.04 9~12 2~3
CG3M
ASTM
A351
0.03 1.0 2.0 18~20 0.035 0.03 11~15 3~4
铸件验收标准

1)、清理干净后最大直径不大于 3mm,深度在铸件壁上不大于壁厚的 1/3,在安装边上不大于其厚度的 1/4,且不得超过 1.5mm 的单个孔洞和清理干净后最大直径不大于 1.5mm,深度不大于壁厚的 1/3,且不
注:铸件在机械加工前后发现的小缺陷,经有关部门同意,补焊后可不进行热处理。 24、补焊处需经表面检查和根据工艺需要进行 X 光透视,透视不得小于补焊面积的两倍。焊区内允许的标准
与 X 光透视标准相同。 注:铸件表面上小的明孔洞,补焊后可不透视,(扩修后<1.5cm2 明孔洞)。 25、翘曲的铸件允许矫正,矫正后应检查有无裂纹,必要时需重复进行热处理。
≥80 ≥100 ≥50 ≥90 ≥70 ≥80 ≥70 90-115 ≥70 85~115 ≥80 ≥70 ≥80 ≥50 80-100
注: 1)硬度值除设计部门规定按表 2 检验外,仅作验收依据。
2)当测得的机械性能数值遇界限值时,按本标准规定的有效位数进行修约,修约按 GB1780 的规定,强
二:技术要求和检验
*** 化学成份 ***
1、每一炉次的合金,必须对以下成份进行光谱分析。合金的化学成份分析结果应符合表 1 的规定。同时,
在铸件上标识炉号及炉次号进行追溯。
注:当测得的化学成分数值遇界限值时,按本标准规定的有效位数进行修约,修约规则按 GB1780r 规定。
表 1 化学成份 %
合金 代号
铸件检验标准[1]
![铸件检验标准[1]](https://img.taocdn.com/s3/m/9335f22359fb770bf78a6529647d27284b7337d3.png)
铝合金铸造件检验技术条件(试行)1 内容及适用范围本标准根据GB/T 1173-1995及GB/T 9438-1999的相关内容,规定了铝合金铸件的分类和铸件的外观质量、内在质量以及铸件修补等内容的技术要求与检验规则等。
本标准适用于我公司采用金属型铸造所生产的制动器上、下泵体等铸件(不含压力铸造)。
根据工作条件、用途以及在使用过程中如果损坏,所能造成的危害程度,将铸件分类如下:2 技术要求2.1 化学成分2.1.1合金的化学成分根据GB/T 1173-1995的规定,应符合表2-1及表2-2的规定。
2.1.2当使用杂质总和来表示杂质含量时,如无特殊规定,其中每一种未列出的元素含量不大于0.02%。
2.2 状态2.2.1铸件按表2-3的规定,呈铸态或热处理状态供应。
注:在保证合金机械性能前提下,可以不加铍(Be)。
2.3 机械性能2.3.1 每批铸件应按其类别检验机械性能。
2.3.2 合金及其铸件的机械性能应符合表2-3的规定。
2.4外观质量2.4.1铸件在进行表面粗糙度、表面缺陷、尺寸等外观质量检验之前,飞边、溢流口、隔皮等应清理干净、平整,但不可在非加工表面上留有明显的凿痕,且宽度不得超过2mm。
2.4.2铸件的表面粗糙度Ra为6.3μm以上。
2.4.3非加工表面的浇冒口,应清理到与铸件表面齐平;待加工表面的浇冒口残留量应不大于3mm。
2.4.4清除飞翅、夹砂等多肉类缺陷,铸件的内外表面由于型芯及顶杆的磨损所产生的飞边、毛刺应清除干净。
2.4.5根据顾客图样或技术文件的要求,铸件表面可进行喷砂处理。
2.4.6铸件上作为基准用的部位应平整,不允许存在任何凸起痕迹,装饰面上不允许有推杆痕迹(图样上注明)。
2.4.7非加工表面上,由于模具组合镶并或受分型面影响而形成的铸件表面高低不平差值不得超过0.3mm。
2.4. 8非加工表面上,不允许有超过表2-4(Ⅰ)级规定的花纹、麻面和有色斑点。
2.4.9铸件尺寸应符合图样的要求。
01-铸件外观质量检验标准
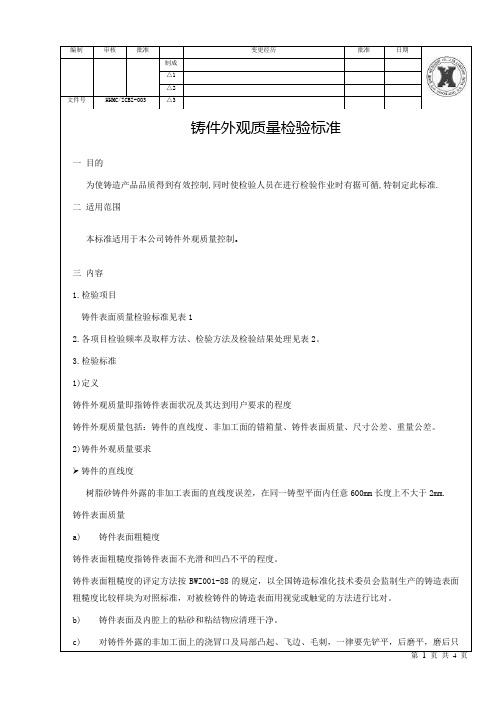
编制审核批准变更经历批准日期
制成
△1
△2
文件号HHMC/ZCBZ-003 △3
铸件外观质量检验标准
一目的
为使铸造产品品质得到有效控制,同时使检验人员在进行检验作业时有据可循,特制定此标准.
二适用范围
本标准适用于本公司铸件外观质量控制.
三内容
1.检验项目
铸件表面质量检验标准见表1
2.各项目检验频率及取样方法、检验方法及检验结果处理见表2。
3.检验标准
1)定义
铸件外观质量即指铸件表面状况及其达到用户要求的程度
铸件外观质量包括:铸件的直线度、非加工面的错箱量、铸件表面质量、尺寸公差、重量公差。
2)铸件外观质量要求
➢铸件的直线度
树脂砂铸件外露的非加工表面的直线度误差,在同一铸型平面内任意600mm长度上不大于2mm. 铸件表面质量
a)铸件表面粗糙度
铸件表面粗糙度指铸件表面不光滑和凹凸不平的程度。
铸件表面粗糙度的评定方法按BWZ001-88的规定,以全国铸造标准化技术委员会监制生产的铸造表面粗糙度比较样块为对照标准,对被检铸件的铸造表面用视觉或触觉的方法进行比对。
b)铸件表面及内腔上的粘砂和粘结物应清理干净。
c)对铸件外露的非加工面上的浇冒口及局部凸起、飞边、毛刺,一律要先铲平,后磨平,磨后只。
铸件表面质量验收标准

铸铁件验收项目及标准铸件的表面质量主要包括铸件的表面缺陷、尺寸精度、形状偏差、表面粗糙度、表面清理质量等;1、铸件表面缺陷的检验1.1表面缺陷检验的一般要求1.1.1铸件非加工表面上的浇冒口必须清理得与铸件表面同样平整,加工面上的浇冒口残留量应符合技术要求,若无要求,则按表8执行;1.1.2在铸件上不允许有裂纹、通孔、穿透性的冷隔和穿透性的缩松、夹渣等机械加工不能去除的缺陷;1.1.3铸件非加工表面的毛刺、披缝、型砂、砂芯等应清理干净;1.1.4铸件一般待加工表面,允许有不超过加工余量范围内的任何缺陷存在;重要加工面允许有不超过加工余量2/3的缺陷存在,但裂纹缺陷应予清除;加工后的表面允许存在直径*长度*深度小于等于2*2*2的非连片孔洞的铸造缺陷;1.1.5作为加工基准面(孔)和测量基准的铸件表面,平整度小于等于2.0 毫米、粗糙度Ra50以内;1.1.6铸件表面气孔、砂眼、夹渣面积不大,但比较分散或者有连片麻点的表面不予接收;1.1.7除技术要求特别注明的铸件外,对于表面有气孔、缩孔、砂眼等缺陷的铸钢件允许补焊,但铸铁件未经允许不得焊补(铸铁件实行一案一判的原则)但补焊面积不允许超过铸件面积的10%,焊接质量应符合JB/T 5000.7-2007标准要求,补焊后必须退火、机械性能达到图纸要求,且不得有渗漏及影响外观的缺陷;1.2铸件外观质量等级表1 铸件外观质量等级1、一般零部件采用B级精度,在检查过程中,如有一个或多个项目超出B级精度要求的零部件均判定为不合格;2、影响到零部件安全、性能的部位,外观质量采用A级精度,如果有一个或多个项目超出规定级精度要求的零部件均判定为不合格;2、铸件尺寸的检验2.1铸件毛坯尺寸公差铸件尺寸公差应按毛坯图或技术条件规定的尺寸公差等级执行,当技术文件未规定尺寸公差时,则应以GB6414-1999为依据,并按照表2选定公差值(粗线框内为推荐使用公差等级);表2铸件尺寸公差(单位:mm)2.2铸件分型面处最大错型值应不得超过表2所示公差值,当需进一步限制错型量时,应从表3中选取;表 3 错型值(GB6414-1999)2.3铸件加工余量应符合表4的规定,有特殊要求的表面应在技术要求中单独标注加工余量;表4加工余量(单位:mm)3、表面粗糙度检测表面粗糙度总体检测原则依据图纸要求,当图纸无要求是执行国标GB/T15056-1994;3.1一般情况下,表面粗糙度要求Ra50,铸件难以清理的部位,局部允许 Ra100,待加工表面允许降低1级;3.2.使用面积法作为验收依据面积法常用的比较样块评定铸件表面粗糙度;方法如下:3.2.1铸造表面粗糙度比较样块应符合GB6060.1-1997标准;3.2.2按照国标BWZ001-88评定铸件表面粗糙度的等级;3.2.3铸件的浇道、冒口、修补的残余表面及铸造表面缺陷(如粘砂、结疤等)不列为被检表面;3.2.4以铸造表面粗糙度比较样块为对照标准,对被检铸件的铸造表面用视觉或触觉的方法进行对比;3.2.5用样块对比时,应选用适于铸造合金材料和工艺方法的样块进行对比;3.2.6被检的铸造表面必须清理干净,样块表面和被检表面均不得有锈蚀处;3.2.7用样块对比时,砂型铸造表面被检点数应符合表7的规定;特种铸造表面被检点数应按表8的规定加倍;被检点应平均分布,每点的被检面积不得小于与之对比面的面积;表7 被检铸造表面最低检测数3.2.8当被检铸造表面的粗糙度介于比较样块两级参数值之间者,所确定的被检铸造表面的粗糙度等级为粗的一级;3.2.9对被检铸造表面,以其80%的表面所达到的最粗表面粗糙度等级,为该铸造表面粗糙度等级;3.3铸件表面清理检测3.3.1铸件几何形状必须完整,非加工面上的清理损伤不应大于该处的尺寸偏差,加工面上的损伤不应大于该处加工余量的1/2;3.3.2允许铸件表面有少量的局部低凹或打磨痕迹,在直径不大于8mm,并能保证铸件规定的最小的壁厚;3.3.3为去除铸造缺陷而打磨后的铸件表面粗糙度应与一般铸件表面粗糙度基本一致;3.3.4除特殊情况外,铸件表面允许残留的浇冒口、毛刺,多肉残余量应按表 8的要求进行;表8 浇冒口、毛刺、多肉等允许残留量值3.3.5铸件表面须经过防锈处理,保证在铸件进入面加工时不得有任何的锈蚀;3.3.6铸件表面如有油漆要求的,必须按有关涂装规定执行;4、铸件重量检测对于没有特殊要求的铸件,重量偏差可以不作为验收依据;如果技术条件有要求,供需双方协商后,铸件的重量偏差也应作为验收依据,一般应符合表6的规定;表6铸件重量偏差。
- 1、下载文档前请自行甄别文档内容的完整性,平台不提供额外的编辑、内容补充、找答案等附加服务。
- 2、"仅部分预览"的文档,不可在线预览部分如存在完整性等问题,可反馈申请退款(可完整预览的文档不适用该条件!)。
- 3、如文档侵犯您的权益,请联系客服反馈,我们会尽快为您处理(人工客服工作时间:9:00-18:30)。
222精密机械企业标准
编号:YQB/0004-2016-A
铸件表面质量验收规
发布时间:2016年 7 月 13 日实施时间:2016年 7 月 13 日
222精密机械发布
1、目的
为加强本公司对铸件的质量控制,保证本公司产品的外观质量及加工性能,特制订铸件表面质量验收规;
2、适用围
本规适用于公司所有外来铸铁(钢)件的外观质量验收,包括表面缺陷、尺寸精度、表面粗糙度的验收;
3、引用标准
(1)JB/T 5000.4-2007 重型机械通用技术条件第4部分铸铁件;
(2)JB/T 5000.6-2007 重型机械通用技术条件第6部分铸钢件;
(3)GB6414-1999 铸件尺寸公差与机械加工余量;
(4)GB/T6060.1-1997 表面粗糙度比较样块;
(5)GB/T15056-1994 铸造表面粗糙度评定方法;
(6)Q/XC5101-2001 铸铁件通用技术条件;
(7GB/T11351-1989 铸件重量公差
4、名词解释
(1)全数选别:检验项目100%检测;
5、验收项目及标准
铸件的表面质量主要包括铸件的表面缺陷、尺寸精度、形状偏差、表面粗糙度、表面清理质量等;
5.1铸件表面缺陷的检验
5.1.1表面缺陷检验的一般要求
(1)铸件非加工表面上的浇冒口必须清理得与铸件表面同样平整,加工面上的浇冒口残留量应符合技术要求,若无要求,则按表8执行;
(2)在铸件上不允许有裂纹、通孔、穿透性的冷隔和穿透性的缩松、夹渣等机械加工不能去除的缺陷;
(3)铸件非加工表面的毛刺、披缝、型砂、砂芯等应清理干净;
(4)铸件一般待加工表面,允许有不超过加工余量围的任何缺陷存在;重要加工面允许有不超过加工余量2/3的缺陷存在,但裂纹缺陷应予清除;加工后的表面允许存在直径*长度*深度小于等于2*2*2的非连片孔洞的铸造缺陷;
(5)作为加工基准面(孔)和测量基准的铸件表面,平整度小于等于2.0毫米、粗糙度Ra50以;
(6)铸件表面气孔、砂眼、夹渣面积不大,但比较分散或者有连片麻点的表面不予接收;
(7) 除技术要求特别注明的铸件外,对于表面有气孔、缩孔、砂眼等缺陷的铸钢件允许补焊,但铸铁件未经允许不得焊补(铸铁件实行一案一判的原则)但补焊面积不允许超过铸件面积的10%,焊接质量应符合JB/T 5000.7-2007标准要求,补焊后必须退火、机械性能达到图纸要求,且不得有渗漏及影响外观的缺陷;
5.1.2铸件外观质量等级
表1 铸件外观质量等级
5.2 铸件尺寸的检验
5.2.1铸件毛坯尺寸公差
铸件尺寸公差应按毛坯图或技术条件规定的尺寸公差等级执行,当技术文件未规定尺寸公差时,则应以GB6414-1999为依据,并按照表2选定公差值(粗线框为推荐使用公差等级);
表2铸件尺寸公差(单位:mm)
5.2.2铸件分型面处最大错型值应不得超过表2所示公差值,当需进一步限制错型量时,应从表3中选取;
表3 错型值(GB6414-1999)
5.2.3铸件加工余量应符合表4的规定,有特殊要求的表面应在技术要求中单独标注加工余量;
表4 加工余量(单位:mm)
5.3表面粗糙度检测
表面粗糙度总体检测原则依据图纸要求,当图纸无要执行国标
GB/T15056-1994;
5.3.1一般情况下,表面粗糙度要求 Ra50,铸件难以清理的部位,局部允许 Ra100,待加工表面允许降低1级;
5.3.2.使用面积法作为验收依据
面积法常用的比较样块评定铸件表面粗糙度;方法如下:
(1)铸造表面粗糙度比较样块应符合GB6060.1-1997标准;
(2)按照国标BWZ001-88评定铸件表面粗糙度的等级;
(3)铸件的浇道、冒口、修补的残余表面及铸造表面缺陷(如粘砂、结疤等)不列为被检表面;
(4)以铸造表面粗糙度比较样块为对照标准,对被检铸件的铸造表面用视觉或触觉的方法进行对比;
(5)用样块对比时,应选用适于铸造合金材料和工艺方法的样块进行对比;
(6)被检的铸造表面必须清理干净,样块表面和被检表面均不得有锈蚀处;
(7)用样块对比时,砂型铸造表面被检点数应符合表7的规定;特种铸造表面被检点数应按表8的规定加倍;被检点应平均分布,每点的被检面积不得小于与之对比面的面积;
表7 被检铸造表面最低检测数
(8)当被检铸造表面的粗糙度介于比较样块两级参数值之间者,所确定的被检铸造表面的粗糙度等级为粗的一级;
(9)对被检铸造表面,以其80%的表面所达到的最粗表面粗糙度等级,为该铸造表面粗糙度等级;
5.3.3铸件表面清理检测
5.3.1铸件几何形状必须完整,非加工面上的清理损伤不应大于该处的尺寸偏差,加工面上的损伤不应大于该处加工余量的1/2;
5.3.2允许铸件表面有少量的局部低凹或打磨痕迹,在直径不大于 8mm,并能保证铸件规定的最小的壁厚;
5.3.3为去除铸造缺陷而打磨后的铸件表面粗糙度应与一般铸件表面粗糙度基本一致;
5.3.4除特殊情况外,铸件表面允许残留的浇冒口、毛刺,多肉残余量应按表8的要求进行;
表8 浇冒口、毛刺、多肉等允许残留量值
5.3.5铸件表面须经过防锈处理,保证在铸件进入面加工时不得有任何的锈蚀;
5.3.6铸件表面如有油漆要求的,必须按有关涂装规定执行;
5.4铸件重量检测
5.4.1对于没有特殊要求的铸件,重量偏差可以不作为验收依据;如果技术条件有要求,供需双方协商后,铸件的重量偏差也应作为验收依据,一般应符合表6的规定;
表6 铸件重量偏差
6.铸件外观图片参考
——本规由222品质部提出
编制:雪刚审核:雪刚批准:。