铸件质量检测方法有哪些
铸件的五种测量方法

铸件的五种测量方法对于铸件的内部缺陷,常用无损检测方法是射线检测和超声检测。
其中射线检测效果最好,它能够得到反映内部缺陷种类、形状、大小和分布情况的直观图像,但对于大厚度的大型铸件,超声检测是很有效的,可以比较精确地测出内部缺陷的位置、当量大小和分布情况。
1、射线检测射线检测,一般用X射线或γ射线作为射线源,因此需要产生射线的设备和其他附属设施,当工件置于射线场照射时,射线的辐射强度就会受到铸件内部缺陷的影响。
穿过铸件射出的辐射强度随着缺陷大小、性质的不同而有局部的变化,形成缺陷的射线图像,通过射线胶片予以显像记录,或者通过荧光屏予以实时检测观察,或者通过辐射计数仪检测。
其中通过射线胶片显像记录的方法是最常用的方法,也就是通常所说的射线照相检测,射线照相所反映出来的缺陷图像是直观的,缺陷形状、大小、数量、平面位置和分布范围都能呈现出来,只是缺陷深度一般不能反映出来,需要采取特殊措施和计算才能确定。
现在出现应用射线计算机层析照相方法,由于设备比较昂贵,使用成本高,目前还无法普及,但这种新技术代表了高清晰度射线检测技术未来发展的方向。
此外,使用近似点源的微焦点X射线系统实际上也可消除较大焦点设备产生的模糊边缘,使图像轮廓清晰。
使用数字图像系统可提高图像的信噪比,进一步提高图像清晰度。
2、超声检测超声检测也可用于检查内部缺陷,它是利用具有高频声能的声束在铸件内部的传播中,碰到内部表面或缺陷时产生反射而发现缺陷。
反射声能的大小是内表面或缺陷的指向性和性质以及这种反射体的声阻抗的函数,因此可以应用各种缺陷或内表面反射的声能来检测缺陷的存在位置、壁厚或者表面下缺陷的深度。
超声检测作为一种应用比较广泛的无损检测手段,其主要优势表现在:检测灵敏度高,可以探测细小的裂纹;具有大的穿透能力,可以探测厚截面铸件。
其主要局限性在于:对于轮廓尺寸复杂和指向性不好的断开性缺陷的反射波形解释困难;对于不合意的内部结构,例如晶粒大小、组织结构、多孔性、夹杂含量或细小的分散析出物等,同样妨碍波形解释;另外,检测时需要参考标准试块。
铸件的检验项目...
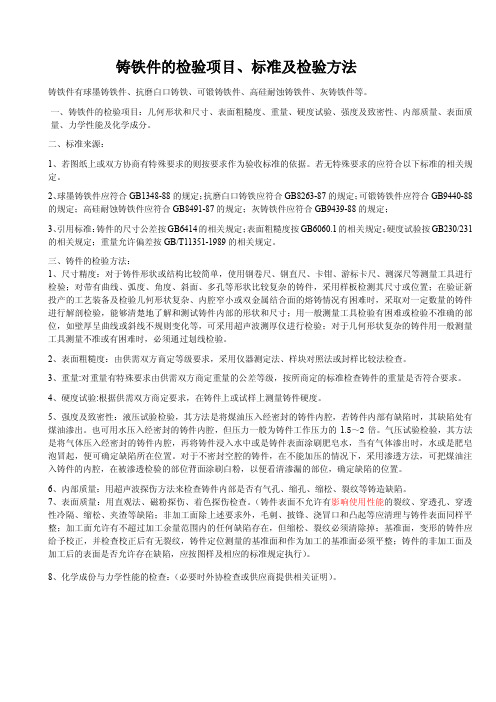
铸铁件的检验项目、标准及检验方法铸铁件有球墨铸铁件、抗磨白口铸铁、可锻铸铁件、高硅耐蚀铸铁件、灰铸铁件等。
一、铸铁件的检验项目:几何形状和尺寸、表面粗糙度、重量、硬度试验、强度及致密性、内部质量、表面质量、力学性能及化学成分。
二、标准来源:1、若图纸上或双方协商有特殊要求的则按要求作为验收标准的依据。
若无特殊要求的应符合以下标准的相关规定。
2、球墨铸铁件应符合GB1348-88的规定;抗磨白口铸铁应符合GB8263-87的规定;可锻铸铁件应符合GB9440-88的规定;高硅耐蚀铸铁件应符合GB8491-87的规定;灰铸铁件应符合GB9439-88的规定;3、引用标准:铸件的尺寸公差按GB6414的相关规定;表面粗糙度按GB6060.1的相关规定;硬度试验按GB230/231的相关规定;重量允许偏差按GB/T11351-1989的相关规定。
三、铸件的检验方法:1、尺寸精度:对于铸件形状或结构比较简单,使用钢卷尺、钢直尺、卡钳、游标卡尺、测深尺等测量工具进行检验;对带有曲线、弧度、角度、斜面、多孔等形状比较复杂的铸件,采用样板检测其尺寸或位置;在验证新投产的工艺装备及检验几何形状复杂、内腔窄小或双金属结合面的熔铸情况有困难时,采取对一定数量的铸件进行解剖检验,能够清楚地了解和测试铸件内部的形状和尺寸;用一般测量工具检验有困难或检验不准确的部位,如壁厚呈曲线或斜线不规则变化等,可采用超声波测厚仪进行检验;对于几何形状复杂的铸件用一般测量工具测量不准或有困难时,必须通过划线检验。
2、表面粗糙度:由供需双方商定等级要求,采用仪器测定法、样块对照法或封样比较法检查。
3、重量:对重量有特殊要求由供需双方商定重量的公差等级,按所商定的标准检查铸件的重量是否符合要求。
4、硬度试验:根据供需双方商定要求,在铸件上或试样上测量铸件硬度。
5、强度及致密性:液压试验检验,其方法是将煤油压入经密封的铸件内腔,若铸件内部有缺陷时,其缺陷处有煤油渗出。
铸件有损和无损检测方法
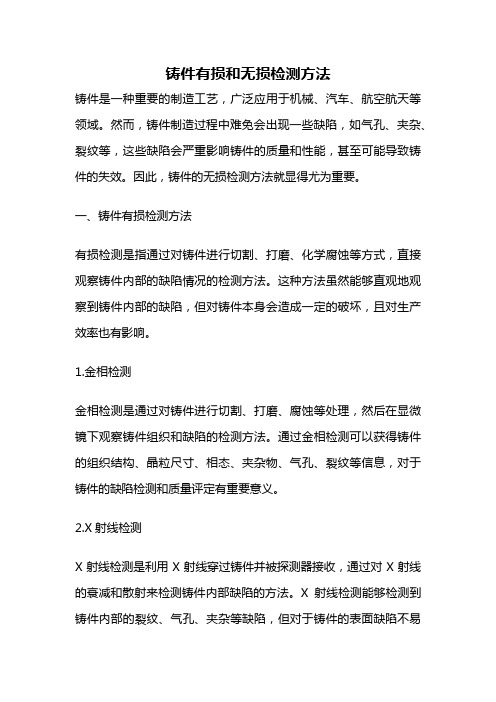
铸件有损和无损检测方法铸件是一种重要的制造工艺,广泛应用于机械、汽车、航空航天等领域。
然而,铸件制造过程中难免会出现一些缺陷,如气孔、夹杂、裂纹等,这些缺陷会严重影响铸件的质量和性能,甚至可能导致铸件的失效。
因此,铸件的无损检测方法就显得尤为重要。
一、铸件有损检测方法有损检测是指通过对铸件进行切割、打磨、化学腐蚀等方式,直接观察铸件内部的缺陷情况的检测方法。
这种方法虽然能够直观地观察到铸件内部的缺陷,但对铸件本身会造成一定的破坏,且对生产效率也有影响。
1.金相检测金相检测是通过对铸件进行切割、打磨、腐蚀等处理,然后在显微镜下观察铸件组织和缺陷的检测方法。
通过金相检测可以获得铸件的组织结构、晶粒尺寸、相态、夹杂物、气孔、裂纹等信息,对于铸件的缺陷检测和质量评定有重要意义。
2.X射线检测X射线检测是利用X射线穿过铸件并被探测器接收,通过对X射线的衰减和散射来检测铸件内部缺陷的方法。
X射线检测能够检测到铸件内部的裂纹、气孔、夹杂等缺陷,但对于铸件的表面缺陷不易检测。
3.超声波检测超声波检测是利用超声波在铸件内部传播并被探测器接收,通过分析超声波的传播时间和衰减程度来检测铸件内部缺陷的方法。
超声波检测可以检测到铸件内部的裂纹、气孔、夹杂等缺陷,并且对于铸件的表面缺陷也有一定的检测能力。
二、铸件无损检测方法无损检测是指不对铸件进行任何破坏的情况下,通过一些物理、化学或其他手段,检测铸件内部缺陷的方法。
无损检测方法不仅能够提高生产效率,减少铸件的损耗,还能够保持铸件的完整性,降低生产成本。
1.磁粉检测磁粉检测是利用铸件表面涂上磁粉,然后通过磁场磁化铸件,观察磁粉的分布情况来检测铸件表面和内部的裂纹、气孔等缺陷的方法。
磁粉检测能够检测到铸件表面和内部的裂纹、气孔等缺陷,但对于夹杂等缺陷的检测能力有限。
2.涡流检测涡流检测是利用涡流原理,在铸件表面或内部引入高频交流电磁场,通过涡流感应电流的变化来检测铸件的缺陷的方法。
铸件质量检验标准

—
—
—
—
—
—
—
—
0.64
0.72
0.80
0.9
1.0
1.1
1.2
1.4
1.6
1.8
2.0
2.2
2.6
2.8
3.2
3.6
4.0
4.6
5
6
7
7
8
9
10
11
13
1600
2500
4000
6300
2500
4000
6300
10000
—
—
—
—
—
—
—
—
—
—
—
—
—
—
—
0.24
0.26
0.28
0.32
0.36
0.40
0.46
0.50
0.56
0.64
0.70
0.78
0.9
1.0
1.1
1.3
1.4
1.6
1.8
2.0
2.2
2.6
2.8
CF3M
ASTM
A351
0.03 1.5 1.5 17~21 0.04 0.04 9~13 2~3
CF8M
ASTM
A351
0.08 1.5 1.5 18~21 0.04 0.04 9~12 2~3
CG3M
ASTM
A351
0.03 1.0 2.0 18~20 0.035 0.03 11~15 3~4
精确检测铸造件的方法

精确检测铸造件的方法铸造件是工业生产中常见的零部件,其质量对产品的性能和安全至关重要。
为了确保铸造件的质量,需要使用精确的检测方法来进行评估和验证。
下面将介绍一些常用的精确检测铸造件的方法。
1. 尺寸检测:尺寸是铸造件的重要参数之一。
通过使用精密仪器,如千分尺、游标卡尺等,可以测量铸造件的长度、宽度、高度和直径等尺寸参数。
这些数据可以与设计图纸进行对比,以确认铸造件的尺寸是否符合要求。
2. 表面检测:铸造件的表面质量对其功能和外观至关重要。
通过使用表面粗糙度仪、显微镜等工具,可以评估铸造件的表面平整度、光洁度和纹理等指标。
此外,也可以使用漏磁检测仪等设备来检测铸造件表面是否存在裂纹、夹杂物等缺陷。
3. 成分检测:铸造件的材料成分对其性能起着决定性作用。
通过使用化学分析仪器,如光谱仪、质谱仪等,可以检测铸造件中各元素的含量。
这样可以确保材料成分符合要求,以保证铸造件具有所需的物理和化学性能。
4. 组织检测:铸造件的组织结构对其力学性能具有重要影响。
通过使用金相显微镜、电子显微镜等设备,可以观察铸造件的组织形貌,评估晶粒大小、相分布、夹杂物和气孔等缺陷情况。
这些数据可以用来判断铸造件的强度、韧性和耐磨性等性能。
5. 力学性能测试:铸造件需要具备一定的力学性能,如强度、硬度、延展性等。
通过使用万能材料试验机、洛氏硬度计等设备,可以对铸造件进行拉伸、压缩、弯曲等力学性能测试。
这样可以确保铸造件在应力情况下能够承受所需的载荷和变形。
通过以上的精确检测方法,可以全面评估铸造件的质量和性能。
这些检测结果对于铸造件的优化设计、生产工艺的改进以及产品的质量控制具有重要的参考价值。
同时,准确的检测可以帮助避免因铸造件质量问题而引发的设备故障、安全事故等不可预料的风险。
普通铸件探伤方法

普通铸件探伤是一种检测铸件内部缺陷的技术,以确保铸件的质量和可靠性。
以下是几种常见的普通铸件探伤方法:1. 超声波探伤:超声波探伤是检测铸件内部缺陷的一种常用方法。
它利用超声波在铸件中的传播特性,通过检测反射波、折射波等来确定内部缺陷的位置、大小和性质。
超声波探伤具有检测速度快、成本低、操作简单等优点,但可能对某些特殊铸件(如含铅、锡等易吸收声能的铸件)的检测效果不佳。
2. 磁粉探伤:磁粉探伤是另一种常见的铸件探伤方法。
它利用铁磁性材料在磁场中被磁化的特性,将磁粉吸附在表面或内部缺陷处,形成可见的磁痕,从而判断缺陷的存在、位置和形状。
磁粉探伤具有操作简单、成本低等优点,但可能对某些非铁磁性或非磁性铸件无法检测。
3. X射线探伤:X射线探伤也是常见的铸件探伤方法之一。
它利用X射线穿透铸件的能力,通过检测射线的强度和分布来反映内部缺陷的性质、位置和大小。
X射线探伤具有检测范围广、灵敏度高、操作简便等优点,但可能对某些特殊铸件(如含有高熔点合金或高原子序数材料的铸件)存在检测困难。
4. 数字式超声波探伤仪:随着科技的发展,数字式超声波探伤仪逐渐取代了传统的手动示波器检测。
数字式超声波探伤仪可以通过计算机屏幕实时显示检测结果,操作简单、检测效率高。
同时,数字式超声波探伤仪还可以进行数据分析、存储和传输,提高了检测的准确性和可靠性。
在进行铸件探伤时,需要注意选择合适的探伤方法,并根据铸件的材质、结构和使用环境等因素进行综合考虑。
此外,探伤过程中还需要注意安全问题,遵守相关安全规定,确保操作人员的安全。
总之,铸件探伤是保证铸件质量的重要环节,需要严格遵守相关规定和标准,确保铸件的安全性和可靠性。
铸件的表面和内部质量检测方法
铸件的表面和内部质量检测方法(图)铸件的检测主要包括尺寸检查、外观和表面的目视检查、化学成分分析和力学性能试验,对于要求比较重要或铸造工艺上容易产生问题的铸件,还需要进行无损检测工作,可用于球墨铸铁件质量检测的无损检测技术包括液体渗透检测、磁粉检测、涡流检测、射线检测、超声检测及振动检测等。
1 铸件表面及近表面缺陷的检测1.1液体渗透检测液体渗透检测用来检查铸件表面上的各种开口缺陷,如表面裂纹、表面针孔等肉眼难以发现的缺陷。
常用的渗透检测是着色检测,它是将具有高渗透能力的有色(一般为红色)液体(渗透剂)浸湿或喷洒在铸件表面上,渗透剂渗入到开口缺陷里面,快速擦去表面渗透液层,再将易干的显示剂(也叫显像剂)喷洒到铸件表面上,待将残留在开口缺陷中的渗透剂吸出来后,显示剂就被染色,从而可以反映出缺陷的形状、大小和分布情况。
需要指出的是,渗透检测的精确度随被检材料表面粗糙度增加而降低,即表面越光检测效果越好,磨床磨光的表面检测精确度最高,甚至可以检测出晶间裂纹。
除着色检测外,荧光渗透检测也是常用的液体渗透检测方法,它需要配置紫外光灯进行照射观察,检测灵敏度比着色检测高。
1.2涡流检测涡流检测适用于检查表面以下一般不大于6~7mm深的缺陷。
涡流检测分放置式线圈法和穿过式线圈法2种。
:当试件被放在通有交变电流的线圈附近时,进入试件的交变磁场可在试件中感生出方向与激励磁场相垂直的、呈涡流状流动的电流(涡流),涡流会产生一与激励磁场方向相反的磁场,使线圈中的原磁场有部分减少,从而引起线圈阻抗的变化。
如果铸件表面存在缺陷,则涡流的电特征会发生畸变,从而检测出缺陷的存在, 涡流检测的主要缺点是不能直观显示探测出的缺陷大小和形状,一般只能确定出缺陷所在表面位置和深度,另外它对工件表面上小的开口缺陷的检出灵敏度不如渗透检测。
1.3磁粉检测磁粉检测适合于检测表面缺陷及表面以下数毫米深的缺陷,它需要直流(或交流)磁化设备和磁粉(或磁悬浮液)才能进行检测操作。
铸件探伤检测标准
铸件探伤检测标准
一、视觉检验
1.检验人员应具备专业知识和技能,并经过培训和认证。
2.检验环境应满足光照、温度、湿度等要求,以确保检验结果的准确性。
3.视觉检验应包括铸件表面质量、结构、尺寸等方面的检查。
4.对于关键部位和易出现缺陷的部位,应进行重点检查。
5.发现缺陷后,应及时记录并报告,以便采取相应的措施进行处理。
二、超声波探伤
1.超声波探伤应使用合适的探头和仪器,并按照标准操作规程进行。
2.对于铸件中的气孔、裂纹、夹杂物等缺陷,应采用脉冲反射法进行检测。
3.根据铸件材质、厚度、缺陷类型等因素,确定探伤灵敏度和判废标准。
4.对于大型铸件,应进行分区检测,并记录检测结果。
5.发现缺陷后,应及时记录并报告,以便采取相应的措施进行处理。
三、射线探伤
1.射线探伤应使用合适的射线源和设备,并按照标准操作规程进行。
2.对于铸件中的气孔、裂纹、夹杂物等缺陷,应采用X射线或伽马射线进行检测。
3.根据铸件材质、厚度、缺陷类型等因素,确定曝光时间和成像质量。
4.对于大型铸件,应进行分区检测,并记录检测结果。
5.发现缺陷后,应及时记录并报告,以便采取相应的措施进行处理。
四、磁粉探伤
1.磁粉探伤应使用合适的磁粉和设备,并按照标准操作规程进行。
2.对于铸件中的裂纹、夹杂物等缺陷,应采用磁粉探伤进行检测。
3.根据铸件材质、缺陷类型等因素,确定磁粉粒度和磁场强度。
4.对于大型铸件,应进行分区检测,并记录检测结果。
5.发现缺陷后,应及时记录并报告,以便采取相应的措施进行处理。
铸件质量检验标准
铸件质量检验标准一、目的:为了确保外协毛坯铸件、采购毛坯铸件、标准铸件、成品铸件质量符合工艺、技术要求,为了满足产品特性,结合相关文件特制定本标准。
二、适用范围:本标准适用于我公司产品外协、采购、生产、装配过程中,全部铸件质量检验标准。
三、检验标准:3.1 铸件结构要符合设计要求或加工工艺要求。
无特殊要求时按铸件通用标准执行。
通用标准等级分为:交货验收技术条件标准;铸件质量分等通则(合格品、一等品、优等品)材质、检验方法;工艺和材料规格等一般性规则。
3.2 铸件成品检验。
铸件成品检验包括:铸件的内部质量检验和外观质量检验。
铸件内部质量检验包括:化学成分、机械性能等。
铸件外观质量检验包括:表面质量、粗糙度、铸件尺寸、重量等。
3.2.1 铸件内部质量检验①化学成分:表1②机械性能表23.2.2 铸件外观质量检验①表面质量检验。
机械加工生产一线人员在工艺过程中对铸造毛坯的检验主要是对其外观铸造缺陷(如有无砂眼、砂孔、疏松、浇不足、铸造裂纹等)的检验;以及毛坯加工余量是否满足加工要求的检验。
表3 铸件外观质量检验项目(GB6060.1-1997)②粗糙度检验。
表4 铸件表面粗糙度(Ra值μm)(GB6060.1-1997)③铸件尺寸检验。
主要一种是采用划线法检查毛坯的加工余量是否足够。
另一种方法是:用毛坯的参考基准面(也称工艺基准面)作为毛坯的检验基准面的相对测量法(需要测量相对基准面的尺寸及进行简单换算)。
表5 铸件尺寸公差数值(mm)(GBT 6414-1997)1)在等级CT1~CT15中对壁厚采用粗一级公差。
2)对于不超过16mm的尺寸,不采用CT13~CT16的一般公差,对于这些尺寸应标注个别公差。
3)等级CT16仅适用于一般公差规定为CT15的壁厚。
表6 单件、小批量生产的铸件公差等级(GBT 6414-1997)注:1)表中所列出的公差等级是小批量的或单件生产的砂型铸件通常能够达到的公差等级。
铸件检验标准
铸件检验标准1.铸件质量检测仪:用于检测合金性能、组织、表面状态等铸件质量的仪器。
2.铸件公称重量检验:根据铸件图计算或根据供需双方认定合格的标准样品铸件的称重结果订出的铸件重量。
包括铸件机械加工余量及其他工艺余量。
3.铸件重量公差检验:用占铸件公称重量的百分比表示的铸件实际重量与公称重量之差的最大允许值。
与铸件尺寸公差对应的分为16个等级,以MT1-MT16表示。
4.铸件重量偏:铸件重量与公称重量之间的正偏差或负偏差。
5.铸件尺寸公差:铸件各部分尺寸允许的极限偏差。
6.铸件尺寸稳定性:铸件在使用和存放过程中保持原来尺寸不变的性能。
7.铸件机械加工余量:为保证铸件加工面尺寸和零件精度,在铸件工艺设计时预先增加而在机械加工时切去的金属层厚度。
8.铸造表面粗糙度:铸造表面上由微小间距和峰谷组成的微观几何特征。
铸造工段铸件质量检验标准根据目前的生产情况,在初期对我单位的铸件检验制定了以下检验标准,随着以后生产和技术的进一步完善对此标准将逐步细化:1. *铸件外表面应平整,1000mm范围内的平整度(或变形量)不大于3mm(特殊要求例外),表面不允许存在高度长度大于3mm和直径大于3mm的铁瘤、脉纹;*不允许存在深度和直径大于3mm的孔洞类缺陷(砂眼、气孔、渣孔、缩孔、缩松等),如果此类缺陷存在面积大于150x150mm而失去修复价值视为废品,可以修复的必须经过焊补并打磨光洁后重新检验;*外型尺寸如有图纸要求公差的应严格按照图纸执行,未注公差的自由尺寸的偏差不能大于该尺寸的光洁度最低一级国家铸件标准规定;*铸件表面不能存在各种严重的裂纹缺陷,如果非加工表面存在长度不大于20mm的轻微裂纹,在请示技术部门后允许采用热焊补的办法进行修复;*铸件表面的粘砂必须清理干净,各种飞刺存在的面积不允许超过200x200mm,否则必须返工;2. *铸件水口冒口经过切割后不得留有高度大于2mm的根部,水口冒口根部的缩松、缩孔必须经过焊补,否则视为废品;*对比较重要的加工面,如果从外表发现各种皮下缺陷应及时反映到工段并对此铸件跟踪,一旦发现加工后存在大量气孔、渣孔、缩松等缺陷应立即将同类产品封存不得出厂并督促工段技术人员改进工艺;3. *每一批次铸件的材质要求单据在质监部门都应有存底,当炉次化验结果和要求对比后可以评判化学成分是否合乎要求;4. *对于用户在加工后发现的各种内在质量缺陷应及时核对并确定生产日期,作为考核数据重新对检验报告进行更改并及时建议工段技术人员改进工艺;5. *检验后发现问题比较严重的铸件只有在厂家提出强行发货要求,经过总经理及其授权人的书面同意后可以作为紧急放行件出厂。
- 1、下载文档前请自行甄别文档内容的完整性,平台不提供额外的编辑、内容补充、找答案等附加服务。
- 2、"仅部分预览"的文档,不可在线预览部分如存在完整性等问题,可反馈申请退款(可完整预览的文档不适用该条件!)。
- 3、如文档侵犯您的权益,请联系客服反馈,我们会尽快为您处理(人工客服工作时间:9:00-18:30)。
铸件质量检测方法有哪些
铸造网讯:铸件的检测主要包括尺寸检查、外观和表面的目视检查、化学成分分析和力学性能试验,对于要求比较重要或铸造工艺上容易产生问题的铸件,还需要进行无损检测工作,可用于球墨铸铁件质量检测的无损检测技术包括液体渗透检测、磁粉检测、涡流检测、射线检测、超声检测及振动检测等。
1 铸件表面及近表面缺陷的检测
1.1 液体渗透检测
液体渗透检测用来检查铸件表面上的各种开口缺陷,如表面裂纹、表面针孔等肉眼难以发现的缺陷。
常用的渗透检测是着色检测,它是将具有高渗透能力的有色(一般为红色)液体(渗透剂)浸湿或喷洒在铸件表面上,渗透剂渗入到开口缺陷里面,快速擦去表面渗透液层,再将易干的显示剂(也叫显像剂)喷洒到铸件表面上,待将残留在开口缺陷中的渗透剂吸出来后,显示剂就被染色,从而可以反映出缺陷的形状、大小和分布情况。
需要指出的是,渗透检测的精确度随被检材料表面粗糙度增加而降低,即表面越光检测效果越好,磨床磨光的表面检测精确度最高,甚至可以检测出晶间裂纹。
除着色检测外,荧光渗透检测也是常用的液体渗透检测方法,它需要配置紫外光灯进行照射观察,检测灵敏度比着色检测高。
1.2 涡流检测
涡流检测适用于检查表面以下一般不大于6~7MM深的缺陷。
涡流检测分放置式线圈法和穿过式线圈法2种。
当试件被放在通有交变电流的线圈附近时,进入试件的交变磁场可在试件中感生出方向与激励磁场相垂直的、呈涡流状流动的电流(涡流),涡流会产生一与激励磁场方向相反的磁场,使线圈中的原磁场有部分减少,从而引起线圈阻抗的变化。
如果铸件表面存在缺陷,则涡流的电特征会发生畸变,从而检测出缺陷的存在,涡流检测的主要缺点是不能直观显示探测出的缺陷大小和形状,一般只能确定出缺陷所在表面位置和深度,另外它对工件表面上小的开口缺陷的检出灵敏度不如渗透检测。
1.3 磁粉检测
磁粉检测适合于检测表面缺陷及表面以下数毫米深的缺陷,它需要直流(或交流)磁化设备和磁粉(或磁悬浮液)才能进行检测操作。
磁化设备用来在铸件内外表面产生磁场,磁粉或磁悬浮液用来显示缺陷。
当在铸件一定范围内产生磁场时,磁化区域内的缺陷就会产生漏磁场,当撒上磁粉或悬浮液时,磁粉被吸住,这样就可以显示出缺陷来。
这样显示出的缺陷基本上都是横切磁力线的缺陷,对于平行于磁力线的长条型缺陷则显示不出来,为此,操作时需要不断改变磁化方向,以保证能够检查出未知方向的各个缺陷。
2 铸件内部缺陷的检测
对于内部缺陷,常用的无损检测方法是射线检测和超声检测。
其中射线检测效果最好,它能够得到反映内部缺陷种类、形状、大小和分布情况的直观图像,但对于大厚度的大型铸件,超声检测是很有效的,可以比较精确地测出内部缺陷的位置、当量大小和分布情况。
2.1 射线检测(微焦点XRAY)
射线检测,一般用X射线或γ射线作为射线源,因此需要产生射线的设备和其他附属设施,当工件置于射线场照射时,射线的辐射强度就会受到铸件内部缺陷的影响。
穿过铸件射出的辐射强度随着缺陷大小、性质的不同而有局部的变化,形成缺陷的射线图像,通过射线胶片予以显像记录,或者通过荧光屏予以实时检测观察,或者通过辐射计数仪检测。
其中通过射线胶片显像记录的方法是最常用的方法,也就是通常所说的射线照相检测,射线照相所反映出来的缺陷图像是直观的,缺陷形状、大小、数量、平面位置和分布范围都能呈现出来,只是缺陷深度一般不能反映出来,需要采取特殊措施和计算才能确定。
国际铸业网出现应用射线计算机层析照相方法,由于设备比较昂贵,使用成本高,无法普及,但这种新技术代表了高清晰度射线检测技术未来发展的方向。
此外,使用近似点源的微焦点X射线系统实际上也可消除较大焦点设备产生的模糊边缘,使图像轮廓清晰。
使用数字图像系统可提高图像的信噪比,进一步提高图像清晰度。
2.2 超声检测
超声检测也可用于检查内部缺陷,它是利用具有高频声能的声束在铸件内部的传播中,碰到内部表面或缺陷时产生反射而发现缺陷。
反射声能的大小是内表面或缺陷的指向性和性质以及这种反射体的声阻抗的函数,因此可以应用各种缺陷或内表面反射的声能来检测缺陷的存在位置、壁厚或者表面下缺陷的深度。
超声检测作为一种应用比较广泛的无损检测手段,
其主要优势表现在:检测灵敏度高,可以探测细小的裂纹;具有大的穿透能力,可以探测厚截面铸件。
其主要局限性在于:对于轮廓尺寸复杂和指向性不好的断开性缺陷的反射波形解释困难;对于不合意的内部结构,例如晶粒大小、组织结构、多孔性、夹杂含量或细小的分散析出物等,同样妨碍波形解释;另外,检测时需要参考标准试块。