铸件表面质量标准
铸钢件表面质量标准

铸钢件表面质量标准
铸钢件是工业生产中常见的零部件,其表面质量直接关系到零部件的使用寿命
和性能。
因此,对铸钢件表面质量的标准化要求非常严格。
本文将对铸钢件表面质量标准进行详细介绍,以便于大家更好地了解和掌握相关知识。
首先,铸钢件表面质量标准包括表面粗糙度、表面缺陷和表面涂装等多个方面。
表面粗糙度是指铸钢件表面的不平整程度,通常通过表面粗糙度仪进行测量。
根据不同的使用要求,铸钢件的表面粗糙度标准也有所不同。
一般来说,表面粗糙度越小,零部件的使用寿命和性能就越好。
其次,表面缺陷是指铸钢件表面的瑕疵和缺陷,包括气孔、夹渣、裂纹等。
这
些表面缺陷会严重影响铸钢件的使用性能,甚至导致零部件的失效。
因此,在生产过程中,必须严格控制铸钢件表面缺陷的产生,确保零部件的表面质量符合标准要求。
此外,表面涂装也是铸钢件表面质量标准中的重要内容。
表面涂装不仅可以美
化零部件的外观,还可以提高零部件的耐腐蚀性能和耐磨性能。
因此,在进行表面涂装时,必须严格按照相关标准进行操作,确保涂装质量符合要求。
总的来说,铸钢件表面质量标准是保证零部件质量的重要保障。
只有严格按照
标准要求进行生产和检测,才能确保铸钢件的表面质量达到标准,从而保证零部件的使用寿命和性能。
希望通过本文的介绍,大家能够更加深入地了解铸钢件表面质量标准的重要性,为生产实践提供参考。
铸件质量标准
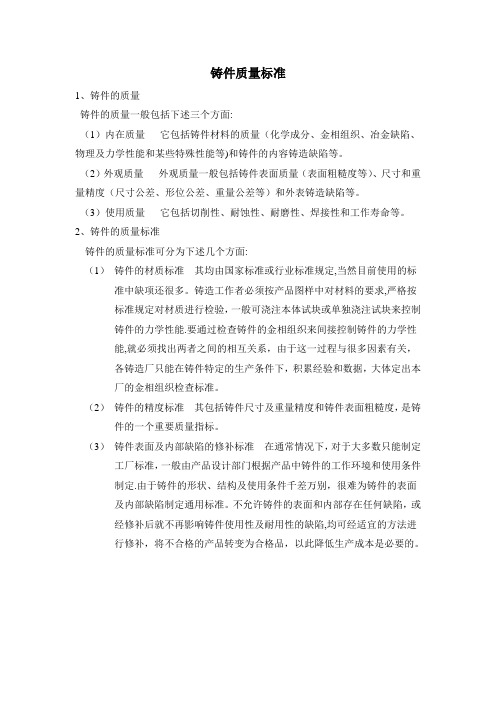
铸件质量标准
1、铸件的质量
铸件的质量一般包括下述三个方面:
(1)内在质量它包括铸件材料的质量(化学成分、金相组织、冶金缺陷、物理及力学性能和某些特殊性能等)和铸件的内容铸造缺陷等。
(2)外观质量外观质量一般包括铸件表面质量(表面粗糙度等)、尺寸和重量精度(尺寸公差、形位公差、重量公差等)和外表铸造缺陷等。
(3)使用质量它包括切削性、耐蚀性、耐磨性、焊接性和工作寿命等。
2、铸件的质量标准
铸件的质量标准可分为下述几个方面:
(1)铸件的材质标准其均由国家标准或行业标准规定,当然目前使用的标准中缺项还很多。
铸造工作者必须按产品图样中对材料的要求,严格按
标准规定对材质进行检验,一般可浇注本体试块或单独浇注试块来控制
铸件的力学性能.要通过检查铸件的金相组织来间接控制铸件的力学性
能,就必须找出两者之间的相互关系,由于这一过程与很多因素有关,
各铸造厂只能在铸件特定的生产条件下,积累经验和数据,大体定出本
厂的金相组织检查标准。
(2)铸件的精度标准其包括铸件尺寸及重量精度和铸件表面粗糙度,是铸件的一个重要质量指标。
(3)铸件表面及内部缺陷的修补标准在通常情况下,对于大多数只能制定工厂标准,一般由产品设计部门根据产品中铸件的工作环境和使用条件
制定.由于铸件的形状、结构及使用条件千差万别,很难为铸件的表面
及内部缺陷制定通用标准。
不允许铸件的表面和内部存在任何缺陷,或
经修补后就不再影响铸件使用性及耐用性的缺陷,均可经适宜的方法进
行修补,将不合格的产品转变为合格品,以此降低生产成本是必要的。
铸件质量分等标准

本公司铸件质量分为A、B、C、D四个等级、回用品及废品共6种.一、 A等品1、机械性能、金相组织、硬度、尺寸均在合格范围内.2、表面平整光洁,轮廓清晰,形状准确,R规则,光洁度达到Ra100μm左右.3、尺寸公差符合CT10—12级(大件12级,中小件10—11级),关键尺寸图纸有要求的除外。
4、错位值:中小件在1~1。
5mm左右,大件≤2。
5mm,经修正后,无明显高低不平现象.5、表面无明显的砂孔、气孔缺陷。
涂料光洁平整,无漏涂、挂流与堆积现象。
冷铁基本平整,毛胚面高低不平小于2—3mm,加工面在2、4、6mm以内(按小、中、大件区分)。
6、由于浇冒口形状大小的改变,造成剥肉缺陷,其深度大件小于3mm,中小件小于1~2mm.7、分型面披缝:10T以上大件≤3。
5mm,中件≤2.5mm,小件≤1.5mm。
坭芯间隙:大件≤4。
5mm,中小件≤2~3.5mm.8、图号、编号、炉号等标识排列准确,外观清晰完整,无明显凹凸不平。
9、铸件不需电焊。
二、 B等级1、机械性能、金相组织、硬度、尺寸均在合格范围内。
2、表面基本平整光洁,轮廓清晰,形状基本正确,加工面有少量缺陷,其深度小于加工余量1/3,R基本规范,粗糙度在3、Ra150μm以内。
4、尺寸公差:大件按CT13级,中件CT12级,小件CT11级范围内。
5、错位值:大件≤3mm,中件≤2mm,小件≤1。
5mm,图上有明确要求,影响整体肉厚和无法修正的除外。
6、涂料基本光滑平整,无漏涂,无挂流及堆积,允许略有隐阴可见的痕迹。
7、披缝厚度,外模,坭芯,大件(10T以上)≤4.5mm,中件3。
5mm,小件≤2。
5mm.(但需不影响高度尺寸)8、冷铁不平度:大件≤4。
5 mm,中间≤3 mm,小件≤2 mm。
9、表面有不影响使用的少量气孔、砂孔缺陷,其深度≤壁厚的1/6。
加工面有缺陷,修磨后其加工余量:大件≥5 mm,中件≥4 mm,小件≥3 mm。
10、图号、编号、炉号等标识排列准确,外观清晰,简单返修即可符合要求.11、非加工面有缺陷,但电焊或其它修补仍不影响其表面质量的。
检验铝铸件质量9大标准及处理方案-

检验铝铸件质量9大标准及处理方案-
1. 外观质量:检查铝铸件表面是否有气孔、夹渣、表面粗糙等缺陷,应采取去毛刺、打磨等方式处理。
2. 尺寸精度:检查铝铸件的尺寸是否符合要求,如存在尺寸偏差,可以通过机械加工或重新调整模具来处理。
3. 材质成分:通过化学成分分析检查铝铸件的材质成分是否符合标准要求,如有偏差,可以重新选择合适的材料。
4. 机械性能:通过拉伸、硬度等机械性能测试检查铝铸件的强度、硬度等机械性能是否达到要求,如不符合,可以进行热处理或调整合金配方。
5. 内部缺陷:采用X射线或超声波探伤等方法检查铝铸件的内部是否存在气孔、裂纹等缺陷,可采取疏松处理、补焊等方式。
6. 表面处理:对铝铸件进行表面处理,如喷漆、阳极氧化、电镀等,以提高铝铸件的耐腐蚀性和美观度。
7. 焊接质量:如果铝铸件需要进行焊接,需要检查焊接工艺和焊接质量,如焊接缺陷,可进行补焊或重新焊接。
8. 寿命、耐久性:通过模拟使用条件或实际使用过程中的试验,检查铝铸件的寿命和耐久性,如不符合要求,可采取增加材料厚度、改进结构等方式进行改进。
9. 环境适应性:根据铝铸件的应用环境,检查其对温度、湿度、腐蚀等环境因素的适应性,如不适应,可进行材质改进或表面处理等方式来提高适应性。
铸铁件质量标准(YBJQ101.1.88)
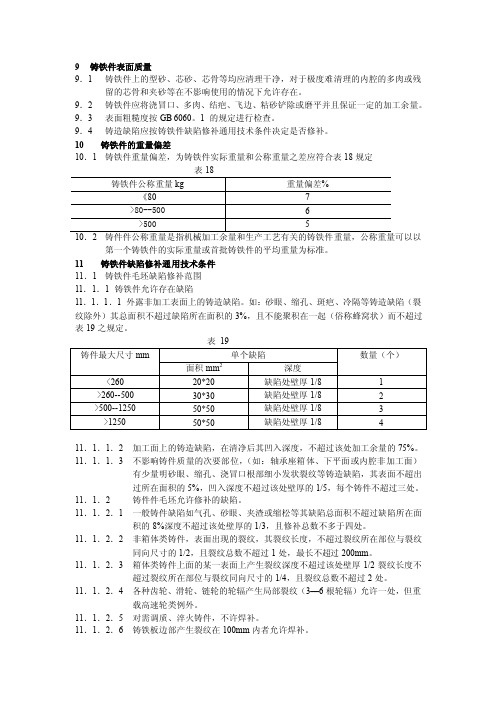
9铸铁件表面质量9.1铸铁件上的型砂、芯砂、芯骨等均应清理干净,对于极度难清理的内腔的多肉或残留的芯骨和夹砂等在不影响使用的情况下允许存在。
9.2铸铁件应将浇冒口、多肉、结疤、飞边、粘砂铲除或磨平并且保证一定的加工余量。
9.3表面粗糙度按GB 6060。
1 的规定进行检查。
9.4铸造缺陷应按铸铁件缺陷修补通用技术条件决定是否修补。
10铸铁件的重量偏差10.1铸铁件重量偏差,为铸铁件实际重量和公称重量之差应符合表18规定第一个铸铁件的实际重量或首批铸铁件的平均重量为标准。
11铸铁件缺陷修补通用技术条件11.1铸铁件毛坯缺陷修补范围11.1.1 铸铁件允许存在缺陷11.1.1.1 外露非加工表面上的铸造缺陷。
如:砂眼、缩孔、斑疤、冷隔等铸造缺陷(裂纹除外)其总面积不超过缺陷所在面积的3%,且不能聚积在一起(俗称蜂窝状)而不超过表19之规定。
表1911.1.1.2加工面上的铸造缺陷,在清净后其凹入深度,不超过该处加工余量的75%。
11.1.1.3不影响铸件质量的次要部位,(如:轴承座箱体、下平面或内腔非加工面)有少量明砂眼、缩孔、浇冒口根部细小发状裂纹等铸造缺陷,其表面不超出过所在面积的5%,凹入深度不超过该处壁厚的1/5,每个铸件不超过三处。
11.1.2铸件件毛坯允许修补的缺陷。
11.1.2.1一般铸件缺陷如气孔、砂眼、夹渣或缩松等其缺陷总面积不超过缺陷所在面积的8%深度不超过该处壁厚的1/3,且修补总数不多于四处。
11.1.2.2非箱体类铸件,表面出现的裂纹,其裂纹长度,不超过裂纹所在部位与裂纹同向尺寸的1/2,且裂纹总数不超过1处,最长不超过200mm。
11.1.2.3箱体类铸件上面的某一表面上产生裂纹深度不超过该处壁厚1/2裂纹长度不超过裂纹所在部位与裂纹同向尺寸的1/4,且裂纹总数不超过2处。
11.1.2.4各种齿轮、滑轮、链轮的轮辐产生局部裂纹(3—6根轮辐)允许一处,但重载高速轮类例外。
铸件质量检验标准

西安重装铜川煤矿机械有限公司铸件质量检验标准为了提高铸件的质量,要求铸造分厂、相关科室不断的完善铸造工艺,解决各项铸造质量问题,控制铸造缺陷,使之降到最低。
积极的参与市场调查,不断的掌握用户对铸件质量的要求及信息反馈,持续完善改进铸造工艺,保证出厂铸件的质量,增强我公司铸件在市场的竞争力,特制定本检验标准。
铸件质量检验的依据:铸件图样、铸造工艺文件、相关标准和铸件交货验收技术条件。
铸件质量包括铸件外观质量和铸件内在质量。
铸件外观质量:铸件尺寸公差、铸件表面粗糙度、铸件重量公差、浇冒口残余量、铸件焊补质量和铸件表面缺陷。
铸件内在质量:铸件力学性能、化学成分、金相组织和内部缺陷。
1、铸件化学成分的检验分析(炉前检验分析或成品铸件终端检验分析)应符合图样要求的牌号的化学成分。
2、铸件力学性能的检验应符合相关标准及交货验收技术条件所要求的各种性能。
3、铸件外形几何形状、尺寸、尺寸公差及加工余量的检验(符合GB/T6414-1999)⑴简单铸件外形几何形状、尺寸、尺寸公差及加工余量的检验应按铸件图样、技术要求、铸造工艺文件、国家相关标准及合同规定进行全部尺寸的检验。
⑵形状复杂铸件外形几何形状、尺寸、尺寸公差、形位公差及加工余量应按铸件图样、技术要求、铸造工艺文件、国家相关标准及合同规定采用划线检验、三坐标测量仪检验及超声波测量(厚度)等检测方法进行检验。
4、铸件表面粗糙度的检验⑴不加工铸件的表面必须清理干净,不得有铸造缺陷、锈蚀、油污、砂粒及其它粘附物。
⑵加工铸件的表面必须清理干净,不得有铸造缺陷、锈蚀、油污、砂粒及其它粘附物,且不能提高生产成本。
5、铸件公称重量的检验⑴铸件的公称重量:供需双方共同认定的合格铸件中随机抽取不少于10件铸件,以实称重量的平均值作为公称重量。
⑵铸件在称重量前应清理干净,浇道和冒口残余量应达到技术条件规定的要求,有缺陷的铸件应在修补合格后称重量。
⑶图样有要求公称重量的铸件,应按铸件图样、技术文件及合同规定进行称重检验。
铸件检验标准
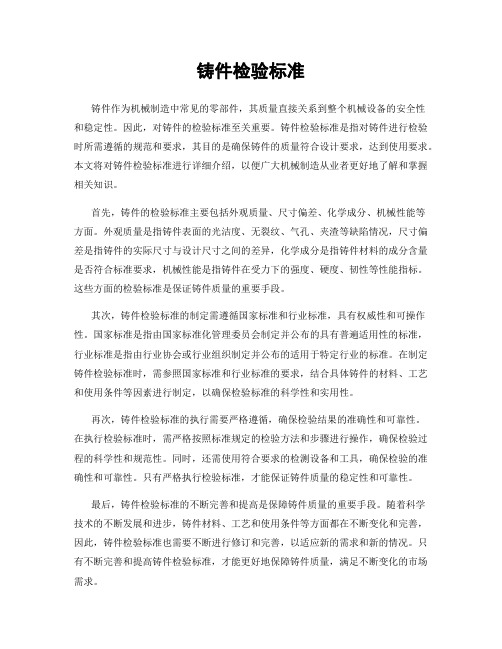
铸件检验标准铸件作为机械制造中常见的零部件,其质量直接关系到整个机械设备的安全性和稳定性。
因此,对铸件的检验标准至关重要。
铸件检验标准是指对铸件进行检验时所需遵循的规范和要求,其目的是确保铸件的质量符合设计要求,达到使用要求。
本文将对铸件检验标准进行详细介绍,以便广大机械制造从业者更好地了解和掌握相关知识。
首先,铸件的检验标准主要包括外观质量、尺寸偏差、化学成分、机械性能等方面。
外观质量是指铸件表面的光洁度、无裂纹、气孔、夹渣等缺陷情况,尺寸偏差是指铸件的实际尺寸与设计尺寸之间的差异,化学成分是指铸件材料的成分含量是否符合标准要求,机械性能是指铸件在受力下的强度、硬度、韧性等性能指标。
这些方面的检验标准是保证铸件质量的重要手段。
其次,铸件检验标准的制定需遵循国家标准和行业标准,具有权威性和可操作性。
国家标准是指由国家标准化管理委员会制定并公布的具有普遍适用性的标准,行业标准是指由行业协会或行业组织制定并公布的适用于特定行业的标准。
在制定铸件检验标准时,需参照国家标准和行业标准的要求,结合具体铸件的材料、工艺和使用条件等因素进行制定,以确保检验标准的科学性和实用性。
再次,铸件检验标准的执行需要严格遵循,确保检验结果的准确性和可靠性。
在执行检验标准时,需严格按照标准规定的检验方法和步骤进行操作,确保检验过程的科学性和规范性。
同时,还需使用符合要求的检测设备和工具,确保检验的准确性和可靠性。
只有严格执行检验标准,才能保证铸件质量的稳定性和可靠性。
最后,铸件检验标准的不断完善和提高是保障铸件质量的重要手段。
随着科学技术的不断发展和进步,铸件材料、工艺和使用条件等方面都在不断变化和完善,因此,铸件检验标准也需要不断进行修订和完善,以适应新的需求和新的情况。
只有不断完善和提高铸件检验标准,才能更好地保障铸件质量,满足不断变化的市场需求。
综上所述,铸件检验标准是保证铸件质量的重要保障,其制定、执行和不断完善都具有重要意义。
01-铸件外观质量检验标准
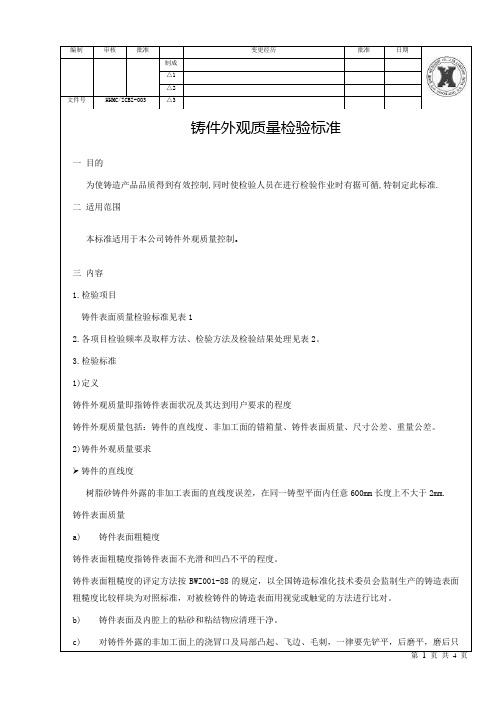
编制审核批准变更经历批准日期
制成
△1
△2
文件号HHMC/ZCBZ-003 △3
铸件外观质量检验标准
一目的
为使铸造产品品质得到有效控制,同时使检验人员在进行检验作业时有据可循,特制定此标准.
二适用范围
本标准适用于本公司铸件外观质量控制.
三内容
1.检验项目
铸件表面质量检验标准见表1
2.各项目检验频率及取样方法、检验方法及检验结果处理见表2。
3.检验标准
1)定义
铸件外观质量即指铸件表面状况及其达到用户要求的程度
铸件外观质量包括:铸件的直线度、非加工面的错箱量、铸件表面质量、尺寸公差、重量公差。
2)铸件外观质量要求
➢铸件的直线度
树脂砂铸件外露的非加工表面的直线度误差,在同一铸型平面内任意600mm长度上不大于2mm. 铸件表面质量
a)铸件表面粗糙度
铸件表面粗糙度指铸件表面不光滑和凹凸不平的程度。
铸件表面粗糙度的评定方法按BWZ001-88的规定,以全国铸造标准化技术委员会监制生产的铸造表面粗糙度比较样块为对照标准,对被检铸件的铸造表面用视觉或触觉的方法进行比对。
b)铸件表面及内腔上的粘砂和粘结物应清理干净。
c)对铸件外露的非加工面上的浇冒口及局部凸起、飞边、毛刺,一律要先铲平,后磨平,磨后只。
- 1、下载文档前请自行甄别文档内容的完整性,平台不提供额外的编辑、内容补充、找答案等附加服务。
- 2、"仅部分预览"的文档,不可在线预览部分如存在完整性等问题,可反馈申请退款(可完整预览的文档不适用该条件!)。
- 3、如文档侵犯您的权益,请联系客服反馈,我们会尽快为您处理(人工客服工作时间:9:00-18:30)。
粗糙
表面有密集的刺状物,用手摸象有锉样感觉。
11-01
型砂过粗,涂料太稀,或漏刷。
粘砂表面粘有一层型砂。 Nhomakorabea11-02
涂料过稀或漏刷,局部过热。
结疤
铸件表面出现粗糙的猪皮状状突起物。
11-03
铸型紧实度不够,涂料刷的匀。
轮廓
错箱
铸件分型面处出现台阶。
12-01
合箱定位不准。
浇不足
型腔未完全充满,棱角呈圆形。常在浇铸温度低的情况下出现。通常浇不足会伴随着皱褶和冷隔出现。
浇铸时炉渣掉入浇口被卷入型腔所造成。
不连续
皮下气孔
在铸件表面存在小的密集的圆形孔洞,孔内表面光滑。常在抛丸、打磨或加工后出现。
04-01
皮下气孔由于金属液中卷入的气体析出或铸型在浇铸时产生气体侵入铸件而产生。
渣气孔
在铸件表面存在密集的孔洞,孔内有氧化物或渣粒存在。常出现在铸件浇铸位置的最高处,或上平面。
07-01
工艺需要;金属液温度低没有完全熔合。
内冷铁
在铸件表面有金属嵌入物痕迹。
07-02
工艺需要;金属液温度低没有完全溶合。
热切割表面
气割痕
氧气切割浇口、冒口或铸件多肉后在铸件表面留下的割痕。
08-01
工艺产物。
气爆痕
用碳弧气爆切除铸件多肉后在铸件表面留下的切痕。
08-02
加工痕迹
磨痕
砂轮打磨后的痕迹。
12-02
浇铸温度低,浇铸系统设计不合理。
碰伤
棱角缺失。
12-03
在运输或清理的过程中将铸件棱角碰伤。
注:a.不连续:铸件上存在的局部缺陷是铸件表面断开,称作不连续。
b.线性不连续:长度大于或等于3倍的宽度的缺陷称作线性不连续。
3.可接受标准
铸件外观验收标准,见表2。
表2铸件外观接收标准
项目
分级
描述
对流
在铸件表面出现线纹,像裂纹一样,通常处于铸件浇铸位置的垂直方向。
05-03
金属液从不同方向充型对接在一起,在液流对接处夹有氧化皮或化合物。浇铸温度低时易出现。
线性不连续
冷裂纹
裂纹比较平滑,少锯齿,无氧化。
06-01
由于不恰当的敲击、碰撞或内应力在接近室温时造成开裂,一般是穿晶裂纹,断裂面无氧化。
铸件表面质量检验标准
1.适用范围
本标准适用于XXX所生产的除小铸模以外的所有产品的外观检验。当用户对表面质量有要求时,执行用户的标准。当用户没有要求时按该标准执行。在和用户签订订单时应该将标准提供该用户进行确认。
2.术语和定义
术语和定义,见表1。
表1术语和定义
项目
名称
外观描述
图片
产生原因
面纹
脉纹
窄的,线状突起物。
01-04
当浇铸温度低时,由于铁水出现紊流和对流产生。
多肉
披缝
在铸件表面延分型面和心头部分有凸起的翅状金属物。
02-01
由于分型面和芯头间隙形成。
疤瘤
在铸造表面有金属凸起物。
02-02
铸型掉砂或退让引起铸件局部胀大。
芯撑
在放置芯撑处有金属凸起物。
02-03
工艺要求,为了保证芯撑放置和熔合。
浇口余根
切除浇口后留下的凸出铸件表面部分。
9-01
由于打磨方法不对在打磨面上留下打磨得沟槽等。
刀纹
机械加工后的刀痕。
9-02
由于加工过程中出现异常或不正当得操作而在加工表面留下沟槽。
焊补
咬边
焊接区域边沿出现凹陷。
10-01
由于不适合的焊接条件和不恰当的焊接操作造成。
焊渣
焊渣或铁豆粘在焊接区域周围铸件表面。
10-02
焊接时焊缝周围未进行保护。
热裂纹
裂纹比较平滑,少锯齿,有氧化,
06-02
由于铸造固态收缩应力在较高的温度下造成开裂。一般是穿晶裂纹,但断裂表面氧化变色。
缩裂纹
裂纹为锯齿状,宽度比冷裂和热裂宽。
06-03
由于凝固收缩伴随着固态收缩在接近凝固温度下造成开裂,一般是沿着晶界开裂,所以裂纹呈锯齿状,断面严重氧化。
金属镶嵌物
芯撑
在铸件表面有凸起或未融合的金属嵌入物。
II
高出铸件表面≤0.6mm。肉眼可见,手摸有凹凸感。
III
高出铸件表面≤0.9mm。
IV
高出铸件表面≤1.2mm。
非金属夹杂
I
II
III
IV
轮廓
I
II
III
IV
注:a.不连续:铸件上存在的局部缺陷是铸件表面断开,称作不连续。
b.线性不连续:长度大于或等于3倍的宽度的缺陷称作线性不连续。
02-04
割缝离铸件表面太远。切割操作人员操作技术差。
冒口余根
切除冒口后留下的凸出铸件表面部分
02-05
割缝离铸件表面太远。切割操作人员操作技术差。
非金属夹杂
夹砂
在铸件表面可见有铸造型砂嵌入铸件本体,去除后铸件留下凹坑。
03-01
砂型受热膨胀导致表面鼓起并破裂,液态金属进入铸型表层下,凝固后形成。
夹渣
01-01
由于砂型或砂芯在浇铸时受热膨胀剪裂形成。
鼠尾
长的,铸件表面出现窄的线状的凹槽或台阶。
01-02
鼠尾是由于砂型或砂芯在浇铸时膨胀而形成小的皱纹(皱褶)引起的。
冷铁印痕
有不同于砂型形成的表面的规则的印迹,周围有凸起的线纹。
01-03
由于安放外冷铁而在铸件表面形成的痕迹。
皱纹
铸件表面上出现的长的平滑的沟纹。
04-02
由于金属液中的渣滓在凝固时析出气体而产生。
缩孔
去除浇口、冒口后在浇口或冒口根部出现孔洞。
04-03
浇冒口补缩不足,金属凝固时没有足够的液态金属补充,导致留下孔洞。
缩松
去除浇口、冒口后在浇口或冒口根部出现蜂窝状的缩孔。
04-04
浇冒口补缩不足,金属凝固时没有足够的液态金属补充,导致留下孔洞。
样板
应用
面纹
I
高出或低于铸件表面≤0.3mm。肉眼可见,手感平滑。
II
高出或低于铸件表面≤0.6mm。肉眼可见,手摸有凹凸感。
III
高出或低于铸件表面≤0.9mm。在200mmX200mm范围内有一条。
IV
高出或低于铸件表面≤1.2mm。在100mmX100mm范围内有一条。
多肉
I
高出铸件表面≤0.3mm。肉眼可见,手感平滑。
冷隔
重叠
在铸件上出现线纹,像裂纹一样,通常处于铸件浇铸位置的水平方向。
05-01
金属液重叠充型时在层间有氧化膜或化合物存在。当浇铸温度低时,重叠在金属充型不平稳和断流的情况下容易出现。
折叠
在铸件表面出现方向不定线纹,像裂纹一样。
05-02
金属液紊流形成的皱纹折叠在一起,将氧化皮或化合物夹进基体,通常出现在远离浇口部位。在浇铸温度低时易出现。
在铸件表面可见有高熔点炉渣嵌入铸件本体,去除后铸件留下凹坑。
03-02
渣滓从浇口掉入型腔中被金属液包裹后凝固所造成。
熔渣
金属液中低熔点的氧化物凝固后被去除,在铸件表面留下凹坑或孔洞。
03-03
熔炼过程中熔渣没有除干净导致浇入铸型中。
落砂
在铸件表面可见有铸造型砂包铸件本体内,去除后铸件留下孔洞。
03-04