钛合金切削技术
钛合金的应用及其切削加工技术的国内外发展现状

钛合金的应用及其切削加工技术的国内外发展现状钛合金的性能及其应用钛及钛合金由于具有比强度高、抗腐蚀性好、耐高温等一系列突出的优点,能够进行各种方式的零件成形、焊接和机械加工。
50年代初期,在一些军用飞机上开始使用工业纯钛制造后机身的隔热板、机层罩、减速板等受力不大的结构件。
60年代,钛合金在飞机结构上的应用,进一步扩大到襟冀滑轧、承力隔框、中冀盒形梁、起落架梁等主要受力结构件中。
到70年代,钛合金在飞机结构上的应用,又从战斗机扩大到军用型轰炸机和运输机,而且在民用飞机上也开始大量采用钛合金结构。
进入80年代后,民用飞机用钛逐步增加,并已超过军用飞机用钛。
对于高速战斗机。
由于高速和高机动性,要求飞机结构尽可能轻,同时还要有耐高温的能力,实践证明,钛合金是最适宜的材料。
从美国各时期主力战机所使用的材料重量比例可以看出,军用机上复合材料和钛合金的比例正在不断加大,两铝合金的比率呈下降趋势钛合金和复合材料的应用水平已是衡量飞机先进性的重要标志之一。
美国王牌战机F一22所使用的钛合金的重量比例达到了41%。
钛合金作为飞机机体材料使用的优势主要有以下几点:1)轻量化,2)节约空间,3)耐热性,4)耐蚀性,5)能与碳纤维强化复合材料(CFRP 材料)互相相容。
钛合金的类型钛是同素异构体,熔点为1720。
C,在低于882。
C时呈密排六方晶格结构,称为a钛;在882℃以上星体心立方晶格结构,称为β钛。
利用钛的上述两种结构的不同特点,添加Al、sn、zr、V、Mo、Mn、Fc、Cr、Cu、Si等合金元素可得到不同类型的钛合金,其分类如下:(1)a钛合金退火组织以a钛为基体的单相同溶体合金称为a钛合金。
主要合金元素a稳定元素A1、中性元素Sn和zr,可固溶强化。
不论是在一般温度下还是在较高的实际应用温度下均是a相,组织稳定,耐磨性高于纯钛,抗氧化能力强。
在500。
C~600。
C的温度下,仍保持其强度和抗蠕变性能,但不能进行热处理强化,室温强度不高。
钛合金的切削加工要领

钛合金的切削加工(六)作者:郑文虎张玉林詹明荣7.切削钛合金时怎样选择切削液?切削钛合金时,为了降低切削温度,应当向切削区域浇注大量的以冷却作用为主的切削液。
对切削液的要求有导热系数大、比热大、热容量大、汽化热大、汽化速度快、流量大、流速快。
一般说来,水比油的导热系数大3~5倍,比热大1倍,汽化热几乎大10倍左右,故用水溶性切削液较为合适。
车、铣削钛合金时,常采用乳化液,或采用有极压添加剂的水溶性切削液。
极压乳化剂的配方为:石油磺酸钠 10%油酸 3%石油磺酸铅 6%三乙醇胺 3.5 %氯化石蜡 4% 20号机油 70.5%氯化硬脂酸 3%极压添加剂的水溶性切削液的配方为:氯化脂肪酸、聚氯乙烯 0.5%~0.8%磷酸三钠 0.59%三乙醇胺 1%~2%亚硝酸钠 1.2%水其余对于钻孔、扩孔、铰孔、拉削、攻丝等工序,应该采用润滑作用较大的极压可溶性油作切削液,如蓖麻油、油酸、硫化油、氯化油等。
冷却润滑的方法最好采用高压喷雾冷却法、高压内冷却法等,这样才可起到良好的冷却、润滑作用。
切削液流量不少于15~20 L/min。
8.切削钛合金时应注意哪些问题?在切削钛合金的过程中,应注意的事项有:(1)由于钛合金的弹性模量小,工件在加工中的夹紧变形和受力变形大,会降低工件的加工精度;工件安装时夹紧力不宜过大,必要时可增加辅助支承。
(2)如果使用含氯的切削液,切削过程中在高温下将分解释放出氢气,被钛吸收引起氢脆;也可能引起钛合金高温应力腐蚀开裂。
(3)切削液中的氯化物使用时还可能分解或挥发有毒气体,使用时宜采取安全防护措施,否则不应使用;切削后应及时用不含氯的清洗剂彻底清洗零件,清除含氯残留物。
(4)禁止使用铅或锌基合金制作的工、夹具与钛合金接触,铜、锡、镉及其合金也同样禁止使用。
(5)与钛合金接触的所有工、夹具或其他装置都必须洁净;经清洗过的钛合金零件,要防止油脂或指印污染,否则以后可能造成盐(氯化钠)的应力腐蚀。
钛合金薄壁零件切削工艺

钛合金薄壁零件切削工艺通过薄壁工件的分析主要是如何选择加工方案、定位基准、刀具材料、切削要素及工装,防止变形,提高加工效率,可以通过以下方法有效的减少变形,保证加工精度。
(l)合理选择刀具材料,提高刀具寿命实践证明加工钛合金材料时必须选用耐磨性高、抗弯强度高、导热性好,抗枯粘结、抗氧化、抗振性的硬质合金刀片,加工时可选择不含或少含Tic的硬质合金刀具,选用YG(K)类硬质合金加工钛合金材料。
(2)选择合理的角度提高刀具的强度钛合金材料工件粗加工时由于加工余量较大:加大刀具的主偏角,增加刀具的强度,使工件加工时径向力变小,避免振动,适当加大前角,减小切削刃单位长度上的负荷。
散热快、提高刀具的使用寿命。
在精加工时余量较小,切削变形和切削抗力小,因此刀具磨损较小,又因选取较小的走刀量,主要是提高工件表面加工质量、消除变形、保证加工精度为主,因此刀具可选择较大的前角和后角,增大偏角使刀具切削锋利:提高了工件加工表面质量(3)采用合理的切削用量避免机床振动减少变形根据薄壁工件粗、半精、精加工工序的加工余量的划分,制定合理的切削用量,达到消除工件切削过程中刀具引起的振动,避开了工件与机床的共振,避免了切削时的振动引起的变形。
(4)添加合理的切削液及有效地浇注方式加工时添加极压乳化液或极压切削油冷却,及时带走刀具上的切屑,刀杆采用中空,切削液喷管通过刀杆直接加入到刀具的切削区,带走切屑,降低了切削区的温度,避免了积屑瘤的产生,提高了工件加工质量。
(5)精加工前增加定位基准精加工工序钛合金薄壁工件在经过:粗加工一半精加工,此时工件的加工应力逐渐得到释放,为了保证工件精加工定位的可靠性,安排一道精车基准工序,其目的消除定位基准的形状误差,并且提高定位基准的精度作为工艺公差,达到保证零件精加工尺寸精度要求,提高工件加工尺寸的可靠性、稳定性,消除工件椭圆度的目的。
(6)采用端面压紧及螺纹拉紧工装消除径向夹紧变形钛合金薄壁工件定位夹紧时,在径向夹紧的作用下产生弹性变形,当工件加工完毕,此时弹性变形释放,造成工件变形,因此工件夹紧力选择轴向方向夹紧,采用螺母压困端面压紧或心轴定位螺纹拉紧形式,消除径向夹紧力,传导切削力的振动,消除变形。
《钛合金TC4高速切削加工性试验研究》
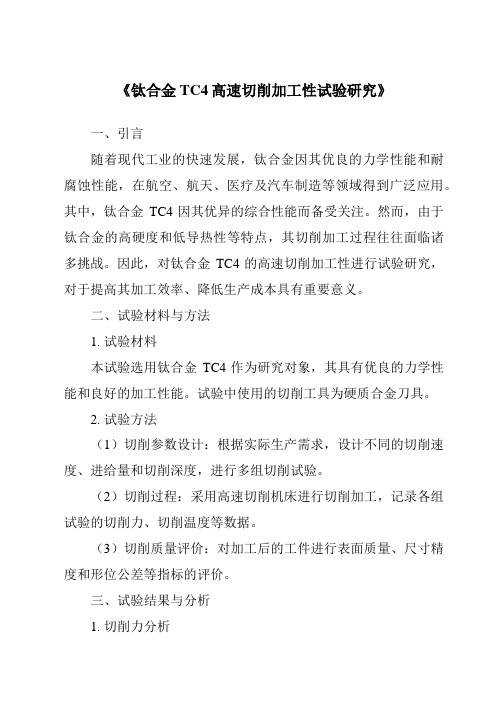
《钛合金TC4高速切削加工性试验研究》一、引言随着现代工业的快速发展,钛合金因其优良的力学性能和耐腐蚀性能,在航空、航天、医疗及汽车制造等领域得到广泛应用。
其中,钛合金TC4因其优异的综合性能而备受关注。
然而,由于钛合金的高硬度和低导热性等特点,其切削加工过程往往面临诸多挑战。
因此,对钛合金TC4的高速切削加工性进行试验研究,对于提高其加工效率、降低生产成本具有重要意义。
二、试验材料与方法1. 试验材料本试验选用钛合金TC4作为研究对象,其具有优良的力学性能和良好的加工性能。
试验中使用的切削工具为硬质合金刀具。
2. 试验方法(1)切削参数设计:根据实际生产需求,设计不同的切削速度、进给量和切削深度,进行多组切削试验。
(2)切削过程:采用高速切削机床进行切削加工,记录各组试验的切削力、切削温度等数据。
(3)切削质量评价:对加工后的工件进行表面质量、尺寸精度和形位公差等指标的评价。
三、试验结果与分析1. 切削力分析试验结果表明,随着切削速度的增加,切削力呈现先减小后增大的趋势。
在一定的切削速度范围内,切削力的减小有利于降低切削过程中的热量产生,从而降低切削温度。
然而,过高的切削速度可能导致切削力的增大,增加切削过程中的振动和工件表面损伤。
2. 切削温度分析切削温度是评价高速切削加工性能的重要指标。
试验发现,切削温度随着切削速度的增加而升高。
在一定的进给量和切削深度下,合理的选择切削速度对于控制切削温度、提高工件表面质量具有重要意义。
3. 表面质量与尺寸精度通过对加工后的工件进行表面质量、尺寸精度和形位公差等指标的评价,发现合理的切削参数组合能够获得较好的工件表面质量和尺寸精度。
同时,采用合理的刀具和切削液能够进一步降低工件表面粗糙度,提高形位公差。
四、结论通过对钛合金TC4的高速切削加工性试验研究,得出以下结论:1. 合理的切削参数组合能够降低切削力、切削温度和工件表面粗糙度,提高工件表面质量和尺寸精度。
钛合金零件切削用量与刀具参数的选择-中华工具网
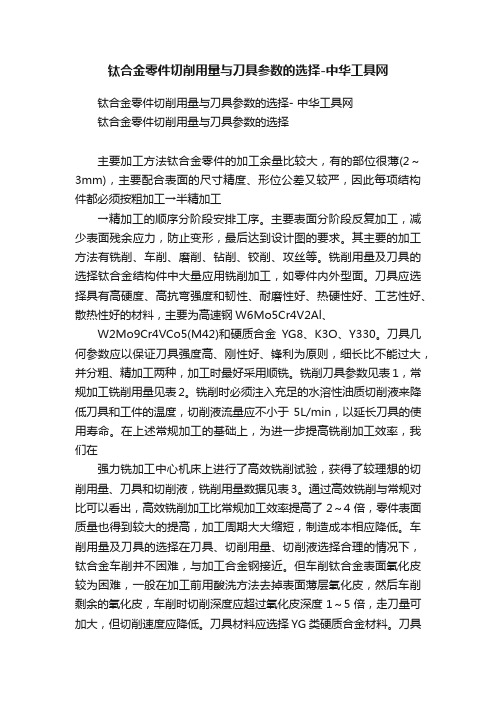
钛合金零件切削用量与刀具参数的选择-中华工具网钛合金零件切削用量与刀具参数的选择- 中华工具网钛合金零件切削用量与刀具参数的选择主要加工方法钛合金零件的加工余量比较大,有的部位很薄(2~3mm),主要配合表面的尺寸精度、形位公差又较严,因此每项结构件都必须按粗加工→半精加工→精加工的顺序分阶段安排工序。
主要表面分阶段反复加工,减少表面残余应力,防止变形,最后达到设计图的要求。
其主要的加工方法有铣削、车削、磨削、钻削、铰削、攻丝等。
铣削用量及刀具的选择钛合金结构件中大量应用铣削加工,如零件内外型面。
刀具应选择具有高硬度、高抗弯强度和韧性、耐磨性好、热硬性好、工艺性好、散热性好的材料,主要为高速钢W6Mo5Cr4V2Al、W2Mo9Cr4VCo5(M42)和硬质合金YG8、K3O、Y330。
刀具几何参数应以保证刀具强度高、刚性好、锋利为原则,细长比不能过大,并分粗、精加工两种,加工时最好采用顺铣。
铣削刀具参数见表1,常规加工铣削用量见表2。
铣削时必须注入充足的水溶性油质切削液来降低刀具和工件的温度,切削液流量应不小于5L/min,以延长刀具的使用寿命。
在上述常规加工的基础上,为进一步提高铣削加工效率,我们在强力铣加工中心机床上进行了高效铣削试验,获得了较理想的切削用量、刀具和切削液,铣削用量数据见表3。
通过高效铣削与常规对比可以看出,高效铣削加工比常规加工效率提高了2~4倍,零件表面质量也得到较大的提高,加工周期大大缩短,制造成本相应降低。
车削用量及刀具的选择在刀具、切削用量、切削液选择合理的情况下,钛合金车削并不困难,与加工合金钢接近。
但车削钛合金表面氧化皮较为困难,一般在加工前用酸洗方法去掉表面薄层氧化皮,然后车削剩余的氧化皮,车削时切削深度应超过氧化皮深度1~5倍,走刀量可加大,但切削速度应降低。
刀具材料应选择YG类硬质合金材料。
刀具几何参数选择:前角g0=4°~8°,后角a0=12°~18°,主偏角Ø45°~75°,刃倾角l=0°,刀尖圆弧半径r=0.5~1.5mm。
钛合金加工工艺
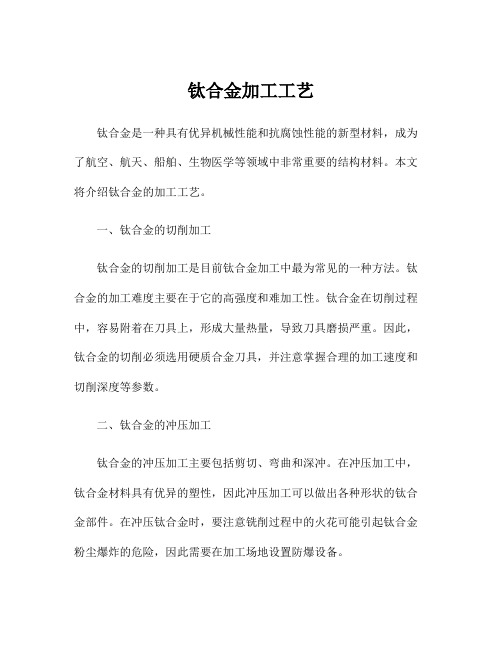
钛合金加工工艺
钛合金是一种具有优异机械性能和抗腐蚀性能的新型材料,成为了航空、航天、船舶、生物医学等领域中非常重要的结构材料。
本文将介绍钛合金的加工工艺。
一、钛合金的切削加工
钛合金的切削加工是目前钛合金加工中最为常见的一种方法。
钛合金的加工难度主要在于它的高强度和难加工性。
钛合金在切削过程中,容易附着在刀具上,形成大量热量,导致刀具磨损严重。
因此,钛合金的切削必须选用硬质合金刀具,并注意掌握合理的加工速度和切削深度等参数。
二、钛合金的冲压加工
钛合金的冲压加工主要包括剪切、弯曲和深冲。
在冲压加工中,钛合金材料具有优异的塑性,因此冲压加工可以做出各种形状的钛合金部件。
在冲压钛合金时,要注意铣削过程中的火花可能引起钛合金粉尘爆炸的危险,因此需要在加工场地设置防爆设备。
三、钛合金的拉伸加工
钛合金的拉伸加工是指利用钛合金材料的塑性形变,来使得钛合金材料变为带有特定形状的工件。
拉伸加工时,必须选择适宜的冷加工方法,如冷挤压、镦锻、卷曲等。
此外,拉伸加工还需要配合热处理,以保证钛合金的性能优良。
四、钛合金的焊接加工
钛合金的焊接加工是比较困难的工艺。
常用的钛合金焊接方法包括手工气焊、手工电弧焊、氩弧焊、电子束焊、激光焊等。
应用不同的焊接方法可以获得不同的焊接质量。
在焊接加工过程中,应注意预加热以及所有焊接接头的准备和清洁。
综上所述,钛合金的加工工艺是比较复杂的。
在加工过程中需要注意掌握加工参数以及选择适合的加工工具。
同时,还需要设置防爆设备以及进行预加热和热处理等措施,以保证钛合金材料的加工质量和性能。
钛合金切削加工特点
钛合金切削加工特点
钛合金是一种高强度、高耐腐蚀性的金属材料,广泛应用于航空、航天、医疗等领域。
然而,由于其高硬度、高热导率和难以切削的特性,钛合金的加工一直是一个难题。
钛合金切削加工需要特殊的工艺和设备,下面我们来了解一下钛合金切削加工的特点。
1. 高硬度
钛合金的硬度比一般的金属材料高,因此需要使用高硬度的刀具进行
切削。
同时,由于钛合金的硬度高,切削时会产生较大的切削力,需
要使用高强度的夹具来固定工件。
2. 高热导率
钛合金的热导率比一般的金属材料高,因此在切削时会产生较大的热量。
如果不及时处理,会导致刀具磨损加剧、工件变形等问题。
因此,在钛合金切削加工中需要采用冷却液来降低切削温度,减少热量的积累。
3. 难以切削
钛合金的切削性能差,容易产生切削热、切削力等问题,导致刀具磨损严重,切削效率低下。
因此,在钛合金切削加工中需要采用高速切削、高效切削等先进的切削技术,以提高切削效率和质量。
4. 高耐腐蚀性
钛合金具有高耐腐蚀性,因此在切削加工中需要采用特殊的切削液,以避免切削液对钛合金的腐蚀。
同时,在切削后需要对工件进行清洗和防腐处理,以保证工件的质量和使用寿命。
总之,钛合金切削加工需要特殊的工艺和设备,需要采用先进的切削技术和切削液,以提高切削效率和质量。
同时,需要注意刀具的选择和夹具的固定,以保证工件的精度和质量。
钛合金的切削加工
钛合金以其比强度高、机械性能及抗蚀性良好而成为飞机及发动机理想的制造材料,但由于其切削加工性差,长期以来在很大程度上制约了它的应用。
随着加工工艺技术的发展,近年来,钛合金已广泛应用于飞机发动机的压气机段、发动机罩、排气装置等零件的制造以及飞机的大梁隔框等结构框架件的制造。
我公司某新型航空发动机的钛合金零件约占零件总数的11%。
本文是在该新机试制过程中积累的对钛合金材料切削特性以及在不同加工方法下表现出的具体特点的认识及所应采取工艺措施的经验总结。
1 钛合金的切削加工性及普遍原则钛合金按金属组织分为a相、b相、a+b相,分别以TA,TB,TC表示其牌号和类型。
我公司某新型发动机所用材料为TA,TC两种。
一般铸、锻件采用TA系列,棒料用TC系列。
特点及切削加工性钛合金相对一般合金钢具有以下优点:比强变高:钛合金密度只有4.5g/cm3,比铁小得多,而其强度与普通碳钢相近。
机械性能好:钛合金熔点为1660℃,比铁高,具有较高的热强度,可在550℃以下工作,同时在低温下通常显示出较好的韧性。
抗蚀性好:在550℃以下钛合金表面易形成致密的氧化膜,故不容易被进一步氧化,对大气、海水、蒸汽以及一些酸、碱、盐介质均有较高的抗蚀能力。
另一方面,钛合金的切削加工性比较差。
主要原因为:导热性差,致使切削温度很高,降低了刀具耐用度。
600℃以上温度时,表面形成氧化硬层,对刀具有强烈的磨损作用。
塑性低、硬度高,使剪切角增大,切屑与前刀面接触长度很小,前刀面上应力很大,刀刃易发生破损。
弹性模量低,弹性变形大,接近后刀面处工件表面回弹量大,所以已加工表面与后刀面的接触面积大,磨损严重。
钛合金切削过程中的这些特点使其加工变得十分困难,导致加工效率低,刀具消耗大。
切削加工的普遍原则根据钛合金的性质和切削过程中的特点,加工时应考虑以下几个方面:尽可能使用硬质合金刀具,如钨钴类硬质合金与钛合金化学亲和力小、导热性好、强度也较高。
低速下断续切削时可选用耐冲击的超细晶粒硬质合金,成形和复杂刀具可用高温性能好的高速钢。
钛合金的切削加工工艺研究
钛合金的切削加工工艺研究摘要:钛合金具有密度小、强度高、耐高温等优良特性,在航空航天以及其他方面得到广泛的应用,但由于其加工难度大、切削效率低、刀具寿命短而影响了它的应用。
本文通过对钛合金材料的特性及切削性能的分析,通过生产中的实例,对其车削和铣削工艺方法进行了工艺研究,同时对不同批次的材料加工的零件,出现色差的问题进行了分析。
关键词:钛合金实例色差分析1、引言钛合金是一种典型的难加工材料,其加工特性主要表现在以下几个方面:(1)钛合金强度高,硬度大,所以要求加工设备功率大,刀具应有较高的强度和硬度。
(2)切屑与前刀面接触面积小,刀尖应力大。
(3)钛合金摩擦因素大,导热系数低。
刀具与切屑的接触长度短,切削热积聚于切削刃附近的小面积内而不易散发。
这些因素使得钛合金的切削温度很高,造成刀具磨损加快,并影响加工质量。
(4)由于钛合金弹性模量低,切削加工时工件回弹大,容易造成刀具后刀面磨损的加剧和工件变形。
(5)钛合金高温时化学活性很高,容易与空气中的氢氧等气体杂质发生化学反应,生成硬化层,进一步加剧了刀具的磨损。
(6)钛合金切削加工中,工件材料极易与刀具表面黏结,加上很高的切削温度,所以刀具容易产生扩散磨损和黏结磨损。
2、生产中管类零件切削加工工艺分析2.1 管类零件的加工工艺图1是某管类零件的结构图,该零件的材料选用的是TA2 M的钛合金钢管。
材料规格是φ63×3.5×130,每根坯料可做一件。
在加工过程中,根据该零件的要求,用车削和铣削的方法即可完成。
其加工的工艺规程如图2所示。
零件最后成型属于薄壁零件,在进行加工时,为了保证零件的几何尺寸满足使用要求,加工时不变形。
所以,车削和铣削时都要用芯棒装夹。
而铣削时是第二次装夹,为了减小铣削后的接刀痕,在进行芯棒装夹时,其间隙应尽量的小。
铣削完成后,用锉刀和砂皮将接刀痕打掉。
2.2 刀具材料的选择加工钛合金的刀具材料应具备如下性能:高温状态下的化学稳定性;足够的强度和韧性;良好的热传导性。
钛合金切削加工研究现状及发展趋势
I ndustry development行业发展钛合金切削加工研究现状及发展趋势杨 涛摘要:钛合金广泛应用于各个领域,提高其切削性能和降低加工成本,开发出性能更好的新型钛合金是目前钛合金加工的主要研究方向。
钛合金的三种基体组织分别为α合金、(α+β)合金和β合金,我国分别以TA、TC和TB表示,其中TC4钛合金最受青睐。
国内外学者对钛合金进行了大量研究工作,特别是对TC4钛合金进行了深入研究。
关键词:钛合金;切削加工;现状;发展趋势钛合金具有低密度、高韧性和强抗腐蚀性等优点,常被用于制造航空发动机关键零部件,如叶轮和叶片。
优异的物理特性提升了钛合金的服役性能,但同时也增加了加工难度,如刀具寿命短、加工表面质量不可控等问题,使得钛合金成为典型的难加工材料。
钛合金切削过程中产生锯齿形切屑,不仅导致切削力的周期性波动,而且影响加工零件的表面质量。
此外,由热塑性变形引起的表面残余应力对零件的疲劳寿命和服役性能也有显著影响。
因此,准确预测切屑形态和表面残余应力对刀具设计和工艺优化具有重要指导意义。
1 钛合金切削仿真技术研究现状通过建立高速切削三维有限元模型,对切屑的形成过程进行了仿真研究。
研究发现最大应力值出现在第Ⅰ变形区,最大切削温度出现在第Ⅱ变形区。
模型只考虑了模型底部的完全约束,并未考虑夹紧和夹具的定位对加工变形的影响。
另外,建立了变刚度三维仿真模型和热力耦合三维动态铣削模型,误差控制在0.0681mm和0.0255mm内,但为了减小计算量,两种模型均为简化模型。
还建立了高速铣削TC4钛合金的三维全热—力耦合有限元模型,对铣削温度进行了模拟分析结果表明,铣削热只影响被加工表面层的温度,刀具温度随铣削速度和径向切削深度的增加而升高且影响小于切削速度。
在基于TC4钛合金三维铣削有限元仿真模型的基础上,研究发现,切削参数对铣削力的影响程度为轴向切削深度>刀具速度>进给速度。
另外,通过建立斜切模型,对最小切削厚度进行了仿真计算,降低了由于切削厚度设置误差导致的最终仿真误差。
- 1、下载文档前请自行甄别文档内容的完整性,平台不提供额外的编辑、内容补充、找答案等附加服务。
- 2、"仅部分预览"的文档,不可在线预览部分如存在完整性等问题,可反馈申请退款(可完整预览的文档不适用该条件!)。
- 3、如文档侵犯您的权益,请联系客服反馈,我们会尽快为您处理(人工客服工作时间:9:00-18:30)。
37
C刀 具
utting Tools
( 4 )刃倾角 λ s
由于毛坯有硬皮和表层组织
削区域浇注大量的以冷却作用为主的切削液。对切 削液的要求有导热系数大、比热大、热容量大、汽 化热大、汽化速度快、流量大、流速快。一般说 来,水比油的导热系数大 3 ~ 5 倍,比热大 1 倍,汽 化热几乎大 10 倍左右,故用水溶性切削液较为合 适。车、铣削钛合金时,常采用乳化液,或采用有 极压添加剂的水溶性切削液。 对于钻孔、扩孔、铰孔、拉削、攻螺纹等工 序,应该采用润滑作用较大的极压可溶性油作切削 液,如蓖麻油、油酸、硫化油、氯化油等。冷却润 滑的方法最好采用高压喷雾冷却法、高压内冷却法 等,这样才可起到良好的冷却、润滑作用。切削液 流量不少于15~20L/min。
4. 钛合金切削的切削用量选择
切削钛合金时,切削温度高、刀具寿命低,切 削用量中切削速度对切削温度的影响最大,因此应 力求使所选择的切削速度下产生的切削温度接近最 佳范围。高速钢刀具切削钛合金时的最佳切削温度 约为480~540℃,硬质合金刀具约为650~750℃。 切削钛合金一般采用较低的切削速度、较大的切削 深度和进给量。 (1)切削速度vc 切削速度对刀具寿命影响最 大,最好能使刀具在相对磨损最小的最佳切削速度 下工作。切削不同牌号的钛合金,由于强度差别较 大,切削速度应适当调整。切削深度对切削速度也 有一定影响,应根据不同的切削深度来确定切削速 度的大小。 ( 2 )进给量 f 进给量对刀具的寿命影响较 小,在保证加工表面粗糙度的条件下,可选较大的 进给量,一般取 f =0.1 ~ 0.3mm/r 。进给量太小,使 刀具在硬化层内切削,会增加刀具磨损,同时极薄 的切屑在很高的切削温度下容易自燃,因此不允许 f <0.05mm/r。 ( 3 )切削深度α p 切削深度对刀具寿命的影响 最小,一般选用较大的切削深度,这样不仅可以避 免刀尖在硬化层内切削,减小刀具磨损,还可增加 刀刃工作长度,有利于散热,一般取αp=1~5mm。
金刀具材料有YG8、YG3、YG6X、YG6A、813、 643、YS2T和YD15等。涂层刀片和YT类硬质合金 会与钛合金产生剧烈的亲和作用,加剧刀具的粘结 磨损,不宜用来切削钛合金;对于复杂、多刃刀 具,可选用高钒高速钢(如 W12C r4V4M o )、高 钴高速钢(如 W2M o9C r4V C o8 )或铝高速钢(如 W6M o5C r4V2A l 、 M10M o4C r4V3A l )等刀具材 料,适于制作切削钛合金的钻头、铰刀、立铣刀、 拉刀、丝锥等刀具。采用金刚石和立方氮化硼作 刀具切削钛合金,可取得显著效果。如用天然金 刚石刀具在切削液冷却的条件下,切削速度可达 200m/m i n ;若不用切削液,在同等磨损量时,允 许的切削速度仅为100m/min。
1. 钛合金切削特点
钛合金的硬度大于350HBW时切削加工特别困 难,小于300HBW时则容易出现粘刀现象,也难于 切削。 此外,毛坯经过冲压、锻造、热轧等方法加工 后,形成硬而脆的不均匀外皮,极易造成崩刃现 象,使得切除硬皮成为钛合金加工中最困难的工 序。另外,由于钛合金对刀具材料的化学亲和性 强,在切削温度高和单位面积上切削力大的条件 下,刀具很容易产生粘结磨损。车削钛合金时,有 时前刀面的磨损甚至比后刀面更为严重;进给量 f <0.1m m/r时,磨损主要发生在后刀面上;当 f >0.2mm/r时,前刀面将出现磨损;用硬质合金刀 具精车和半精车时,后刀面的磨损以VB max<0.4mm 较合适。
ቤተ መጻሕፍቲ ባይዱ冷加工
2. 钛合金切削的刀具选择
切削加工钛合金应从降低切削温度和减少粘结 两方面出发,选用红硬性好、抗弯强度高、导热 性能好、与钛合金亲和性差的刀具材料, Y G 类硬 质合金比较合适。由于高速钢的耐热性差,因此 应尽量采用硬质合金制作的刀具。常用的硬质合
2013年 第3期
6. 钛合金的铣削加工
钛合金在惰性气体介质中低速铣削时,切屑 变形系数大于 1.0 ;但在大气中,铣削速度 v c =30 m/min时,切屑变形系数小于1.0,这是因为钛合金 在高温铣削时,对大气中氧和氮的亲和性很大,在 800 ℃高温条件下,钛合金的切屑便激烈地从周围 大气中吸收这些气体,产生相变并使缩短的切屑重 新伸长。钛合金铣削时温度很高,冲击力大,应选 用能很好地承受交变载荷和热冲击的铣刀刀齿材 料。通常选用 Y G 类硬质合金,也可用钴、铝超硬 高速钢。 铣削钛合金时,宜采用不对称顺铣法,这样刀 齿前面远离刀尖部分首先接触工件,刀齿切离时的 切屑很薄,不易粘结在切削刃上。而逆铣时正相 反,容易粘屑,当刀齿再次切入时切屑被碰断,造
栏目主持 蒋亚宝
C刀 具
utting Tools
钛合金的切削技术
北京环鼎科技有限责任公司 (102200) 饶立强
我们公司使用的钛合金材料是Ti-TC4钛合金, 属于α + β双相钛合金。它具有良好的综合性能, 组织稳定性好,有良好的韧性、塑性和高温变形性 能。能较好地进行热压力加工,能进行淬火、时效 使合金强化,热处理后的强度约比退火状态提高 50% ~ 100% 。高温强度高,可在 400 ~ 500 ℃的温 度下长期工作。特别适用于本公司生产的部分石油 测井仪器,各个方面均能满足井下仪器的苛刻环境 要求。
不均匀,粗车时切削刃容易崩损,为了增加切削刃 的强度和锋利程度,应加大切屑的滑动速度,一般 ~-5° ,精车时λs=0° 。 取 λ s= - 3 ° (5)刀尖圆弧半径rε 切削钛合金时,刀尖是 最薄弱的部分,容易崩掉和磨损,需磨出刀尖圆 弧,一般rε=0.5~1.5mm。 车 削 时 采 用 负 倒 棱 ( b γ= 0 . 0 3 ~ 0 . 0 5 m m , ~0° ),断(卷)屑槽的槽底圆弧半径 γ o1= - 10 ° Rn=6~8mm。 另外,刀具刃磨质量对提高其寿命也十分重 要。硬质合金刀具宜用金刚石砂轮刃磨,切削时 刃口必须锋利,前后刀面的表面粗糙度值R a应小于 0.4μ m,刃口部分不允许有微小的缺口。刀具刃磨 后进行研磨,其寿命可提高30%。
3. 钛合金切削的刀具几何参数选择
(1)前角γ o 钛合金切屑与前刀面的接触长度
短,前角较小时既可增加刀、屑的接触面积,使切 削热和切削力不至于过分集中在切削刃附近,改善 散热条件,又能加强切削刃,减小崩损的可能性。 ~15° 。 一般取γo=5° (2)后角α o 钛合金已加工表面弹性恢复 大、冷硬现象严重,采用大后角可减小对后刀面造 成的摩擦、粘附、粘结、撕裂等现象,以减小后刀 面的磨损。各种切削钛合金刀具的后角基本上都大 于等于15° 。 ( 3 )主偏角 κ r和副偏角 κ ´ r 切削钛合金时切 削温度高、弹性变形倾向大,在工艺系统刚性允许 的条件下,应尽量减小主偏角,以增加切削部分的 散热面积和减小切削刃单位长度上的负荷,一般采 ,粗加工时取κ r=45° 。减小副偏角可以加 用κ r=30° 强刀尖,有利于散热和降低加工表面粗糙度值,一 ~15° 。 般取κ´r =10°