热流道系统的设计
热流道

热流道热流道是由热喷咀,分流板,温控器,加热圈及感温元件组成。
它借助精密的发热元件及温控单元对塑胶材料流经途径进行加热,将熔融的塑胶材料通过精密设计的流道送至模具型腔处。
射出成形之加工就是(塑化)→(流动)→(成形)→(固化结晶化)的工程。
热浇道之原理:热浇道模具是将传统式模具或三板式模具的浇道与流道经常加热,于每一成形时即不需要取出流道和浇道的一种崭新构造。
热流道(hot runner)是在注塑模具中使用的,将融化的塑料注入到模具的空腔中的加热组件集合。
热流道分类:开放式(用于微型半热流道)、针阀式(用于绝热流道)。
开放式结构简单,适用于微型半热流道,不适于绝热流道,绝热流道对材料的局限性较高,而且直接接触到产品表面,易出现拉丝和泄露,表面质量差;微型半热流道不接触产品而是接触到微小流道,所以可以使用开放式热喷嘴,近期在国外的高精密模具中应用较多。
针阀式热流道节省材料,塑件表面美观,同时内部质量紧密、强度高。
现在世界上有两大类针阀式热流道针阀式热流道(根据注射原理):气缸式和弹簧式。
热流道系统如何保养?答:a.如塑料对热敏感度高或具有腐蝕性,在每次停机时,应使用PP将驻留的材料清除。
b.清除所有水气、雾气、油渍等杂物,以防止模具生锈。
c.将模具保存在干燥通风之处。
d.如果模具的保存时间太长,湿气可能侵蚀加热器,使用前务必除湿。
e.如果使用阀针流道系统,需每季做1~2次的保养,以防止碳化腐蚀或因空气不洁而造成活动的不顺畅。
f.为保护热流道系统,须保证进入气缸的空气干净干燥,最好在进气口加装空气过滤器。
g.模具正常生产时如需临时停机(时间30分钟)以上请将热流道温度降低30%温度以防止塑胶料分解后产生碳化或变色。
1.问题:热流道系统要报价和出图时要提供哪些资料?答案:A、产品的重量,厚度和颜色.B、产品的胶料,名称和数量.C、浇口开在产品表面上还是流道上.D、模具图和注塑机的类型.E、温控箱的接线方式.2.问题:热流道系统有什么优缺点?答案:优点:A、节省原料,提高生产效率.B、减少不良问题的产生,产品品质提高.由于注塑压力可直接传达给型腔,可防止因产品缩水和接合线而导致内部应力引起的问题点的改善.C、注塑,保压,冷却和成形时间的缩短,增大成型效率.D、模具寿命延长;由于可以减少注塑压力,可以减少模具内部压力而延长模具寿命.缺点:A、模具前期单价上升一点.B、模具要定期维护和专业人员.C、模具设计要充分检验和加工尺寸要保证.3.问题:汽车模具中的低压注塑产品的热流道系统选择和设计时要注意哪些事项?答案:由于汽车产品要考虑安全性和胶件的力学平衡性,市场上的汽车产品采用热流道系统越来越多,特别是汽车的胶件贴皮或绒布的胶件将会越来越多;这些产品将会采用低压注塑成型才可以,因此这类低压注塑模具选择和设计热流道系统时就要注意以下事项,YUDO的产品对这些事项就很成熟和有实际的设计和生产的经验.A、流道的大小.B、热咀的距离.C、热流道的钢材材质.D、浇口的大小和射胶的先后顺序的设计.分流板加热器功率计算公式:P=MCΔT/60tη0P:分流板加热器的电功率(kW);M:分流板的质量(Kg);C:分流板材料的比热容[Kj/(Kg.℃);t:分流板的加热升温时间;ΔT:分流板注射工作温度与室温之差(℃);η0:分流板的效率系数;6.热损失控制:1、热流道系统的零部件的热传导:Qp=Ap(T1-T2) Qp:分流板的传导热损失(W);λ:绝热零件材料的热导率[W/(m.℃)];S:绝热零件的厚度(m);Ap:绝热零件的接触面积(m2);T1:分流板的注射击队工作温度(℃);T2:注射模具结构件的温度(℃);2、分流板的对流热损失:QK=αk Ak(Ts–Tp) QK:分流板的对流损失(W);αk:给热系数[W/(m.℃)];Ak:分流板的壁表面面积(m2);Ts:分流板壁面的温度(℃);Tp:周边环境空气的温度(℃);8.加热丝和热电偶的更换1、从模具上卸下热半模2、卸下定位环(定位环的另一个作用是固定热咀)3、为了取下热咀头部,如果需要则卸下模具定模固定板4、取下热咀,注意热电偶线和加热丝线不能被挤压5、卸下卡环。
锌压铸热流道的设计及应用
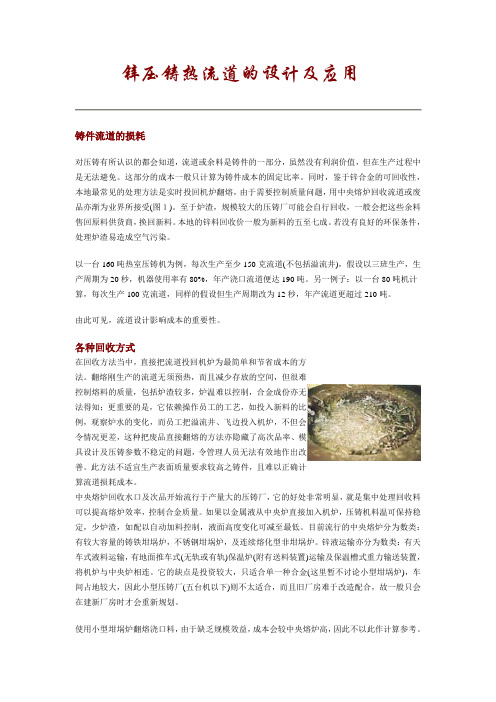
锌压铸热流道的设计及应用铸件流道的损耗对压铸有所认识的都会知道,流道或余料是铸件的一部分,虽然没有利润价值,但在生产过程中是无法避免。
这部分的成本一般只计算为铸件成本的固定比率。
同时,鉴于锌合金的可回收性,本地最常见的处理方法是实时投回机炉翻熔,由于需要控制质量问题,用中央熔炉回收流道或废品亦渐为业界所接受(图1)。
至于炉渣,规模较大的压铸厂可能会自行回收,一般会把这些余料售回原料供货商,换回新料。
本地的锌料回收价一般为新料的五至七成。
若没有良好的环保条件,处理炉渣易造成空气污染。
以一台160吨热室压铸机为例,每次生产至少150克流道(不包括溢流井),假设以三班生产,生产周期为20秒,机器使用率有80%,年产浇口流道便达190吨。
另一例子:以一台80吨机计算,每次生产100克流道,同样的假设但生产周期改为12秒,年产流道更超过210吨。
由此可见,流道设计影响成本的重要性。
各种回收方式在回收方法当中,直接把流道投回机炉为最简单和节省成本的方法。
翻熔刚生产的流道无须预热,而且减少存放的空间,但很难法得知;更重要的是,它依赖操作员工的工艺,如投入新料的比例,观察炉水的变化,而员工把溢流井、飞边投入机炉,不但会令情况更差,这种把废品直接翻熔的方法亦隐藏了高次品率、模具设计及压铸参数不稳定的问题,令管理人员无法有效地作出改善。
此方法不适宜生产表面质量要求较高之铸件,且难以正确计算流道损耗成本。
中央熔炉回收水口及次品开始流行于产量大的压铸厂,它的好处非常明显,就是集中处理回收料可以提高熔炉效率,控制合金质量。
如果以金属液从中央炉直接加入机炉,压铸机料温可保持稳定,少炉渣,如配以自动加料控制,液面高度变化可减至最低。
目前流行的中央熔炉分为数类:有较大容量的铸铁坩埚炉,不锈钢坩埚炉,及连续熔化型非坩埚炉。
锌液运输亦分为数类:有天车式液料运输,有地面推车式(无轨或有轨)保温炉(附有送料装置)运输及保温槽式重力输送装置,将机炉与中央炉相连。
热流道系统的设计
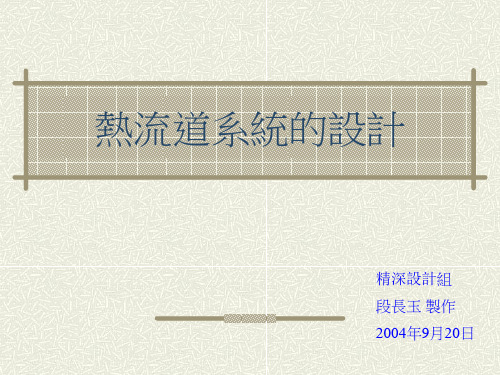
五. 模具設計方面的重點 .
1. 熱流道系統設計的步驟:
a. 根據產品重量選擇適當的熱嘴系列 (Nozzle Product Line),
b. 根據膠料與產品要求選擇最佳的入水方式 (Gating Method),
c. 確定合理的入水孔尺寸(Gate Size), d. 根據模具結構選擇合適的熱嘴長度
(Nozzle Length), e. 選擇熱流道板結構(一字型,X型,H型,Y型等), f. 確定需要哪些配置零件(如法欄,電箱,熱電藕等), g. 設計連同模板在內的熱流道系統尺寸(Hot Half).
2. 熱嘴型號的選擇: 依據產品的重量, 膠料特 性(結晶或非結晶), 有冇加填充劑或換色要 求等, 因為著色劑(COLORANT)會影響粘度 流動性, 具體使用時請遵照資料的選擇依 據來設計, 基本上每家公司都有自己的標 准資料供我們設計參考.
3.可以實現每模多腔的生產, 解決普通流道中 流程長,充模困難問題, 像本公司設計並製 造的2957-01, 2326-01, 每模32個,若采用普通 流道是很難做到的, 每模多腔關鍵技術是流 道的均勻分布問題.
4. 可降低注射壓力, 提高制品質量, 尤其是大 制品, 通常的做法是采用直入式大水口或三 板模形式的多點細水口入水, 但大水口由于 澆口四周附近殘余應力和變形會很大程度 地影響制品的物理性能. 而三板模的多點細 水口成型雖然改善大水口成型的問題, 但因 為它在每一成型周期中都要將很重的型腔 板和水口板來回推動, 產生噪音很大, 而且 容易使模具發生故障, 若采用熱流道系統則 綜合解決以上問題, 也不存在水口料回收問 題, 還大大提高制品外觀質量和物理性能.
叠层模具热流道系统及同步开合模机构设计

叠层模具热流道系统及同步开合模机构设计李萍【摘要】目前在包装、家电及汽车模具领域,叠层模具的应用比较多.叠层模具可以实现立体成型、可以提升近一倍的注射生产效率,因其以上特点叠层模具在塑件结构相对简单、塑件需求数量大的模具开发领域应用空间非常大.【期刊名称】《模具制造》【年(卷),期】2013(013)004【总页数】3页(P48-50)【关键词】叠层模具;同步开模机构;热流道【作者】李萍【作者单位】东江模具(深圳)有限公司,广东深圳518000【正文语种】中文【中图分类】TQ320.661 引言叠层模具是在实践中不断进步的模具制造和注射生产的前沿技术,简单讲叠层模是类似将模具叠放在一起安装在一台注塑机上进行生产,等于两副模具同时工作,区别于常规模具的结构要点在于注射系统(热流道系统)、双向顶出系统、同步开合模机构、导向限位机构等。
2 模具基本结构本文以已投入生产的一副内置式同步开合模机构的两层叠模具为例,分析该模具与普通单层模具的区别,以及结构设计时应注意的事项。
2.1 塑件特点及浇注系统方案塑件基本信息如表1所示。
表1 塑件基本信息mm模具尺寸:X=950;Y=1,000;Z=1,178.2定板厚:153;动板厚:170模腔数:1×2塑件尺寸:直径591.5×62塑件类型:家电塑件平均壁厚:1.5胶料:PP缩水率:1.016此塑件属于家电塑件的通用结构件,产量要求大,以往采用多副相同模具实现高产量要求。
此塑件结构简单,塑件直径虽然达ϕ591.5mm,但塑件高度只有62mm,且塑件为环状结构。
根据该塑件特点及量产要求分析,模具比较适宜设计开发成叠层模具。
如成功开发叠层模具,则此塑件需要的模具数量会降低一半以上,在注塑机吨位不变、注射成型周期基本不变的情况下,叠层模具注射成型产能将提升80%,塑件注射成本也会明显降低。
这副叠层模具浇注系统设计阶段径充分论证,方案确定为4点针阀式热流道近胶,两层设计共8个进胶点,CAE分析结果如图1所示,塑件填充时间为1.89s。
热流道模具浇口等的设计

•主流道杯尺 寸
C、井坑式喷嘴的改进:防主流杯中熔体凝固过量,使浇口堵
塞
•开模分离型
•延伸喷嘴加热 型
•便于清理型
•2.2、多型腔绝热流道模具
特点:主流道和分流道为粗大的圆形截面,分流道直径φ16~30mm;停机
后流道会完全凝固,下次开机前应清除凝料。
•衬套加热,
可用于长周期
件
有瞬时关闭浇口功能,防止型腔充满后高 压熔体溢出产生结构飞边;
防止浇口的流涎和拉丝;
在塑件上仅留下柱销周边痕迹;
可用于结构泡沫或波状模塑等特殊注射加 工
•3)开式喷嘴
特点
开式喷嘴会在塑件表面或 冷流道上留下一个短的浇口 凝料;
浇口尺寸相对较大,通常 为φ1~4mm,有较好的保压 压力并减小内应力;
•浇口温度高,适于注射温 度300℃以下的结晶型料
•加工ABS、热塑 性弹性体和添加 金属或珠光颜料 的塑料可消除熔 接痕,适于快结 晶型和高温塑料
D、多顶针喷 嘴
多顶针喷嘴优点 ▪与多个喷嘴相比,缩小了注射点间的空间;解决 微小制品或需多点注射高精度制品的成型问题; ▪取消或简化了流道板; ▪降低了每个注射点的价格。
PS、PC、ABS(偶尔)会出现浇口垂滴现 象;采用顶针式浇口可减少垂滴的缺陷。
•浇口温度过高 时,流涎拉丝
B、机械闭合浇 口
优点
充填型腔容易,特别对高黏度或剪切敏感 的塑料;
有维持较长保压时间的功能,使热流道系 统可用于厚壁塑件;
浇口闭合排除了浇口区域的热平衡影响, 可准确控制保压状态,提高参数控制精度;
A、顶针式喷嘴结 构
•不适合PS、PE、 PP的小尺寸塑件
•鱼雷棒和顶针不能安装加热 器,不适用于快速结晶塑料
Incoe 热流道系统介绍

Incoe 热流道系统介绍尽管热流道在注塑行业有多年应用历史,但仍有一些设计者、工模制造者、生产者对热流道技术仍存在疑问。
他们常问诸如:热流道专业术语,不同热流道的差别,用热流道可望带来的利益及局限等等。
最近随着塑胶.劳动力成本的提高,促使生产者重新评价其多年所用注塑方法.生产程序。
为求得更高利润,一些公司开始考虑试用热流道系统。
我们为对热流道注塑的优点,对产品及与之相关的专业术语有一定认识是很重要的。
Incoe是全球最大热流道系统生产供应商之一。
我们拥有更丰富的经验和比别厂家更多的标准热流道系统产品,因此,我们是适合于回答有关热流道系统问题权威。
看完此册之后,也许你会有一些我们选册没有包含的问题,不要犹豫,请与我们联系。
1.与传统注塑模相比,热流道系统带来的利益。
2.传统---与直接浇口热流道模口区别。
3.模具成本的分析比较。
4.绝热流道与热流道模具的差别。
5.热流道板模与插发热管板模具比较之差异。
6.Bushigs与Probes差别。
7.热流道系统的改进。
8.从何处得到设计有关热流道系统的信息与帮助。
9.是否所有热流道系统都适合有填充材料?热流道系统对填充材料方面的应用情况。
10.热流道系统对剪切敏感工程塑胶材料的应用情况。
11.温度控制的重要性。
12.热流道系统有用哪些类型的温度控器。
13.哪种类型的温度控器最好。
14.在热流道系统中热量传递.辐射(能)会影响型腔及别的系统的功能吗?15.热流道系统转色的难度易程度。
16.热流道模需流动平衡吗?17.浇口(入水)尺寸之重要性。
18.为什么一些工厂用热流道没问题,而有些工厂用后却麻烦不断。
19.为什么越来越多的生产商采用热流道注塑生产?一.利益利润●优势很多,效益显著.(1)产品质量的改善,生产周期缩短。
(2)节省塑料、不需水口、减少塑胶消耗。
(3)节省劳动力,常常生产自动化,一个操作者可以控制多台机械。
(4)后续加工减少,热流道系统模具无水口,无水口枝需要修剪,产品可直接用手包装或组装,劳动力明显节省。
注塑模热流道技术及系统软件设计
对外加热系统来说 , 流道由外部的加热器加热并保持在加工温度。 两种系统 各自有特点 ,由于外加热系统 的优点 日益明显 ,在设计热 流道软件中更倾向于外加热式。 2)选择热流道平衡方式。实际上热流道的 目的就 是向各 个浇 口输 送相应的塑料熔体。从流变学观点来看 ,热流道的平衡应该是尽可能 自 然平衡 ,即从 注射喷嘴到成型制品间的流道应有同样的直径 , 且长度 并 也应该相等。通常对多模模腔采用机械式平衡分流板设计热流道 ,也就 是从注塑机喷嘴到模腔前的每一个浇 口都有相同长度 的流道长度和流道 直径。
L 孛 _ 参看 凳
应用 方 法 论
l 2 3
影响注塑制品的质量和生产效率。分析热流道温度场 ,可以对发生的应 力 、应变和翘曲变形进行预测 ,其结果对热流道结构设计和注塑工艺参 数有重要的指导意义 ,可以提高一次试模成功率。 因此 ,需要采用一 种适当的知识表达方式 用来 描述热流道设计知 识 ,用来支持热流道的结构设计。同时 ,利用热流道熔体的温度场数学 模 型,在计算机辅助下分析热流道 内部的温度状态 ,并根据分析结果进 步指导热流道的结构设计。 在研究 了以上注塑模及其热流道相关技术后 ,本文设计 了一套热流 道 系统 集成 设 计 方法 ,在 P /平 台上进 行 二 次开 发 ,通过 建 立 热 流道 设 mE 计数学模型与相应的设计知识库 ,根据设计需求 ,系统 自 动获得零件结 构基本参数值 。用户只要通过简单的参数选择和定义即可完成产品的初 步设计 ,并可 以浏览设计的结果。当设计需求变化后,系统重新生成相 应的参数,并驱动三维C D A 系统 ,产生新的设计结果 。同时 ,还对加热 系统进行设计 ,对整个系统设计结果进行温控模拟和分析 ,并实现反馈 修改。热流道系统集成设计结构框图如图l 所示。
模具热流道结构原理
模具热流道结构原理热流道技术是现代模具加工技术的一项重要成果,其原理是通过在模具中设置加热通道和热流道,使塑料熔融前进通道的各部分温度基本相同,以保证模具所注射的每一个塑料制件都能够具有相同的品质和尺寸,从而满足工业制造对于高精度的需求。
本文将介绍热流道结构原理的具体内容。
第一部分:热流道结构的分类根据所有元器件的放置位置和熔塑物的流动情况,可以将热流道结构分为三种类型:点式、线式和面式。
点式热流道的主要特点是在模具中设置单个的加热节点,它们通过塑料内部传递热能以实现加热的目的。
这种结构不仅适用于各种大小尺寸的模具,而且具有精度高和低成本的优点,是热流道系统中使用最广泛的一种类型。
与点式热流道类似,线式热流道的结构是通过在模具中设置多个线性的加热通道,更加适合于大型模具。
线式结构能够将热能更加准确地传递至需要加热的部分,避免发生温度分布不均匀的现象。
线式结构需要更多的热元器件、更复杂的控制系统和维护,并且可能会在熔塑物中留下接缝痕迹。
通过在模具中设置一个平面式的加热板,这种结构可以实现塑料从同一个平面上准确流动,并且不会产生接缝或热点。
由于它的制造难度和成本较高,目前应用不是非常广泛。
热流道的工作原理是由控制器中的电子温控模块控制。
在注塑机的加压下,熔塑物被压入模具中。
加热通道中的热器会将热量传输到熔塑物中,使其保持一定的温度。
这样,热力流动能够准确快速地移动到需要热加工的模具内部各个位置,以实现高精度注塑的目的。
热流道系统的控制属于高科技,该系统可以调节模具内的温度控制。
在该过程中,重要的技术参数包括熔塑物的注入速度、时间和热力流动的流动速度。
通过具体的温度检测和控制触发信号,控制器可以及时地响应热能流动的需求,从而更好地控制热流道的温度分布和保持出色的注塑效果。
1. 塑料熔点的特性:不同种类塑料的熔点温度不同,这需要在热流道设计时充分考虑塑料的种类和熔点。
2. 注塑过程的温度和压力:注塑过程的温度和压力必须能够精确地控制,以确保热能能够精确地流动到所需的位置,并达到高精度注塑的目的。
模具设计热流道教程
热流道教程一、热流道的过去现在和未来二、热流道的原理及概念三、热流道的优点四、热流道组成五、热流道的应用六、热流道安装本资料由贝斯特MoldBest热流道公司协助制作一、热流道的历史、现在、未来作为一项先进的注塑加工技术—热流道技术;在欧美国家的普及使用可以追溯到上个世纪的中期甚至更早;早在1940年12月;就取得了热流道技术的专利权..由于热流道具有许多优点;因此;在国外发展比较快;许多塑胶模具厂所生产的模具50%以上采用了热流道技术;部分模具厂甚至达到80%以上;而在中国;这一技术在近几年才真正得推广和应用..随着模具行业的不断发展;热流道在塑胶模具中运用的比例也逐步提高..但总体不足10%;这个差距相当巨大..近年来;热流道技术在中国的逐渐推广;这很大程度上是由于我国模具向欧美公司的出口量快速发展带来的..在欧美国家;注塑生产已经依赖于热流道技术..可以这样说;没有使用热流道技术的模具现在已经很难出口;这也造成了很多模具厂家对于热流道技术意识上的转变..由于很多外国进口的热流道系统价格比较贵;国内很大一部分厂家接受不了;所以就出现了一些国产热流道系统元件..这对于热流道技术在中国的推广有很大的好处..虽然热流道技术已经开始推广;但有的公司使用率达20%以上;一般采用简单的尖咀、通咀..少数公司采用具有世界先进水平的高难度针阀式热咀;但总体上热流道的采用率达不到10%;与国外的50~80%相差太远..返回二、热流道的原理冷流道是指模具入口与产品浇口之间的部分..塑料在流道内靠注塑压力和其本身的热量保持流动状态;流道作为成型物料的一部分;但并不属于产品..所以在我们设计模具的时候既要考虑填充效果;又要考虑怎样通过缩短、缩小流道来节省材料;理想情况是这样;但实际应用中则很难达到两全其美..热流道又称无流道是指在每次注射完毕后流道中的塑料不凝固;塑胶产品脱模时就不必将流道中的水口脱出..由于流道中的塑料没有凝固;所以在下一次注射的时候流道仍然畅通..简要言之;热流道就是注塑机喷咀的延伸..返回三、热流道的优点为什么会有这种热流道技术出现呢热流道技术又能够带给我们哪些好处呢熟悉注塑工艺的朋友都知道;常规注塑成型经常会有以下不利因素的出现:A.充模困难B.薄壁大制件的变形C.浇道原材料的浪费D.多模腔模具的注塑件质量不一等热流道技术的出现;则给这些问题提供了比较完善的解决方案;一般来讲;采用热流道有以下的好处:1.流道内压力损耗小;塑料流动性好;温度均匀;则产品的内应力;变形就会减小;产品表面质量和力学性能就会大大提高;常见的缩水、填充不足、熔接痕、颜色不均、飞边、翘曲现象也可以减少;2.消除全部或大部分流道废料;物料的有效利用率高;不必回用旧料;3.缩短了成型周期;开模行程;提高了生产效率;4.热流道均为自动切断浇口;可以提高自动化程度;5.降低注塑压力;有利于保护模具;延长使用寿命;6.多模腔模具可保证填充均匀;质量一致;热流道的缺陷每一项技术都会有自身的缺点存在;热流道技术也不例外1.模具造价成本高;2.模具结构相比较复杂;要求严格控制温度;3.需要专业人士进行维护..返回四、热流道系统的组成热流道系统由四部分组成:热咀、分流板、加热原件和温控器1.热咀:将从分流板进入的塑料再送进各个模腔;充分降低注射压力..由于客户不同的需求及针对不同塑料的不同特性;热咀的规格型号有多种选择;也可以根据客户的要求定制加工..从加热方式上可分为:内加热热咀和外加热热咀;从结构上分常用的有:尖咀、通咀和针阀咀针阀式热咀技术上较先进;优点有:1.在制品上不留下进浇口残痕;进浇口处痕迹平滑;2.能使用较大直径的浇口;可使型腔填充加快;并进一步降低注射压力;减小产品变形;3.可防止开模时出现拉丝现象及流涎现象;4.当注塑机螺杆后退时;可有效地防止从模腔中反吸物料;5.能实行定时注射以减少制品熔接痕..2.分流板:连接注塑机喷嘴与热咀;将塑料恒温的从主射咀送到各个单独的热咀..在熔体传送过程中;熔体的压力减小;并不允许材料降解..常用热流道板的形式有:一字型;H型;Y型;X字型、米字型;从加热方式上分外加热热流道板和内加热热流道板两大类3.加热原件:加热元件是热流道系统的重要组成部分;其加热精度和使用寿命对于注塑工艺的控制和热流道系统的工作稳定影响非常大..一般有加热棒、加热圈、加热管等4.温控器:温控器就是对热流道系统的各个位置进行温度控制的仪器;由底端向高端分别有通断位式;积分微分比例控制式和新型智能化温控器等种类..返回五、热流道的应用热流道应用非常广阔;从日常用品到家用电器到医疗产品、汽车配件等工业产品..各种不同塑料原料都已可顺利使用热流道加工;以常用PP聚丙烯;PE聚乙稀到PC聚碳酸到玻璃纤维强尼龙和聚砜工程材料..产品大小应用可用于小到0.1克大到15公斤..特别是多型腔模具;注塑产品薄壁化和加工工艺严格的工程塑料也要求必须使用热流道系统加工..返回六、热流道安装返回返回首页。
基于公理化和知识单元的热流道概念设计研究
基于公理化和知识单元的热流道概念设计研究摘要本文从知识单元的基本概念出发,将公理化设计与知识单元有机结合在一起,以注塑模热流道系统设计为载体,提出了基于公理化设计和知识单元的概念产品信息建模方法,并建立相应的模型。
关键词公理化;知识单元;热流道;概念设计中图分类号tk1 文献标识码a 文章编号 1674-6708(2011)38-0076-020 引言在传统的cad系统中,普遍采用的特征建模技术为参数化,设计人员构思好自己的设计,通过cad系统完成二维和三维图纸,这种模式的产品设计效果较高,但这主要面向的是产品设计的详细设计阶段,怎么样将参数化设计拓展到概念设计方面一直没有强有力的支持。
概念设计是新产品开发过程的早期关键活动之一,是新产品开发的关键因素。
概念设计包含了从产品需求分析到进行详细设计之前的设计过程,包括功能设计、原理设计、布局设计和初步的结构设计;概念设计不仅与需求分析、详细设计紧密相连,其内部的各个环节也相互依赖,互为驱动,因而概念设计是一个相当复杂的产品创新设计过程[1]。
要使cad系统能支持概念设计过程,需要实现从概念设计到结构设计间的信息传递,要对概念设计产品信息建模。
在概念设计阶段产品信息是模糊和不确定的,这使得以精确尺寸为特征的传统cad 建模技术无能为力,因此,要支持计算机辅助概念设计,就必须要建立面向概念设计的产品信息建模技术。
本文在研究前人的成果基础上,以注塑模热流道系统设计为载体,提出了基于公理化设计和知识单元的概念产品信息建模方法,并建立相应的数学模型,使得计算机能更好的支持概念信息。
1 知识单元知识单元(knowledge unit,ku)是描述某一对象或事物的知识子集,反映对象或事物的内容与结构特征、问题描述、推理规则及方法等。
知识单元表达概念信息,是产品设计知识系统的基本元素,知识单元在结构层面属于不可细分的知识,可有效地对产品信息单元结构化。
知识单元的表达可以用下面的公式:ku = {n,m,h,x}1)其中n为知识单元的标识属性,id号是的标识符号。
- 1、下载文档前请自行甄别文档内容的完整性,平台不提供额外的编辑、内容补充、找答案等附加服务。
- 2、"仅部分预览"的文档,不可在线预览部分如存在完整性等问题,可反馈申请退款(可完整预览的文档不适用该条件!)。
- 3、如文档侵犯您的权益,请联系客服反馈,我们会尽快为您处理(人工客服工作时间:9:00-18:30)。
B:溫度差---等於熱嘴內的料溫減模溫(℉/℃), 英制尺 寸使 用華氏溫度℉, 公制尺寸使用攝氏溫度℃;
C: 熱膨脹系數: 0.00000736inch/℉ & .0000136mm/℃.
A1 = A + T.E.
其中: A1: 工作尺寸, 熱咀升溫膨脹后的新長度. A: 室溫下之熱咀長度.
六. 流道板的接線
1. 若使用熱流道板, 需在模圖中以 圖表的形式列出各熱咀及其探熱 針(TC)的接線編號, 且與型腔編號 對應(圖示); 我們公司定義從熱嘴 開始編號, 然後是熱流道板, 最後 是熱流道板的主進料口(NOZZLE), 2.工場依照接線示意圖製作熱流道接 線銘牌, 並安裝在模具操作者一側, 工場在接駁電線時必須按照圖紙 設計資料套上相應編號的膠圈, 以 便在生產中調節控制不同模腔的 熱嘴溫度.
e. 選擇熱流道板結構(一字型,X型,H型,Y型等),
f. 確定需要哪些配置零件(如法欄,電箱,熱電藕等), g. 設計連同模板在內的熱流道系統尺寸(Hot Half).
2. 熱嘴型號的選擇: 依據產品的重量, 膠料特 性(結晶或非結晶), 有冇加填充劑或換色要 求等, 因為著色劑(COLORANT)會影響粘度 流動性, 具體使用時請遵照資料的選擇依 據來設計, 基本上每家公司都有自己的標 准資料供我們設計參考.
2.2 閥式噴嘴在每一周期完成後會自動關閉, 避免發生流涎. 在設計時提供給針閥動 力的氣路或油路通常是並聯的(圖示).
3. 熱流道板: “一”字形,H﹑Y﹑X﹑星形等.
4. 熱流道系統的型式:
4.1 普通熱流道, 有單嘴和熱流 道板+單嘴或多嘴等形式; 單嘴直入產品, 單嘴+二次 流道; 熱流道板+單嘴可以 實現單腔偏心注射而模具 不需偏心.
6. 電源線與TC線的線槽尺寸最少3/8”x 5/8”,視 乎電線數量及需要之空間而定,熱流道板內 的電線必須用高溫線套保護及蓋板蓋住, 防止 移動或裝磡模時被壓壞而漏電。蓋板為1/8” 厚鋁片。 所有的線槽應設計在同一件模板上, 且出線位在模具上方TOP, 應偏離中心大約 1.250”, 防止吊模時擠壞電線. 這樣放置不壓 線, 生產成型時也不會因為凍水滴落影響.
三.為什麼要使用熱流道 .
1. 節省原材料和勞動力: 同一般普通流道 模相比, 熱流道模具無需打水口, 減輕工 人勞動強度.
2. 成型周期縮短, 自動化程度提高. 就成型原 理來講,熱流道系統是不會縮短周期的, 那是 因為不會產生水口或者不必要水口,從而更 好利用啤機的注射克重, 縮短充模時間. 故 此, 盡管三板模可以利用機械手來完成取水 口料這一動作,以實現自動化生產,但還是多 了一步動作,影響著成型生產周期.對于大批 量生產作業, 這一點就更加突出了, 而采用 熱流道則可以解決一問題.
硬
殼
度 長
.0" +1
平基
7.有時候熱咀只是為了減短流程而設計, 真正的入水還是普通流道,這在設計時要 注意,當熱咀延伸部位有流道時,要留出 此段延伸尺寸, 有些熱嘴標準長度是不 可再加工的,若流道為梯形,且均在後模 就無此問題.
8.有浮動的模板或穿過頂針板的情形, 需要加司保護熱咀及電線;
七. 熱流道的不足之處
1.模具制作成本高,一次性投入較大,;
2.熱流道的技術含量大, 模具的維護保養費用較 高, 甚至會因為這一方面問題而影響著日後的生 產. 因此, 對於試制品和小批量作業不宜選擇熱 流道系統; 3.不適合於厚壁制品, 原則上, 熱流道要求短時間 內快速固化成型, 假如制品在模內冷卻時間過長, 流道內的膠料會發生變質甚至降解, 而澆口處則 容易固化, 若澆口處(附近)溫度提高,又會產生澆 口的流涎現象, 造成拉絲以致影響制成品外觀, 所以對于一些成型周期長的制品不太適宜 (如三 通, 四通管接頭);
3.接線插座與電箱: 我們設計主要參考 DME和HARTING 兩種牌號 .
Harting connector
4. TC線有正負極之分, 接線時要小心. DME, Mold-Master, Incoe, Husky是按照美國標準協 會(ASA)規定的顏色編碼: White „+‟ / Red„-‟ 而Hasco, Manner則是依歐洲標準區分正負 極: White „-‟ / Black„+‟ 有些TC在電線上 印有‘+‟ „-‟字樣便於駁線.
4.2 絕熱流道, 是靠塑料自身冷凝絕熱隔 熱, 適于熱穩定性較高的塑料如PE, PP 料. 小型制品不用炮仗加熱, 大制品因 成型周期較長需要加熱. 4.3 絕熱流道要設計面收螺絲﹑水口刮 板﹑ 水口拉板… …
二. 常用熱流道的標準版號.
我們公司正在使用的標準主要有: MoldMaster, Husky, Incoe, DME, Manner, Yudo, Fast-Heat, Hasco ...... 在設計時具體選用 什麼牌號大多由客人指定(Perlos早先使 用Manner, 現在改用Mold-Master熱流道系 統配HARTING接線盒) ,有時候甚至整個 熱流道系統都由客人提供(Emhart使用 Mold-Master Hot Half).
3.可以實現每模多腔的生產, 解決普通流道中 流程長,充模困難問題, 像本公司設計並製 造的2957-01, 2326-01, 每模32個,若采用普通 流道是很難做到的, 每模多腔關鍵技術是流 道的均勻分布問題.
4. 可降低注射壓力, 提高制品質量, 尤其是大 制品, 通常的做法是采用直入式大水口或三 板模形式的多點細水口入水, 但大水口由于 澆口四周附近殘余應力和變形會很大程度 地影響制品的物理性能. 而三板模的多點細 水口成型雖然改善大水口成型的問題, 但因 為它在每一成型周期中都要將很重的型腔 板和水口板來回推動, 產生噪音很大, 而且 容易使模具發生故障, 若采用熱流道系統則 綜合解決以上問題, 也不存在水口料回收問 題, 還大大提高制品外觀質量和物理性能.
4. 并非所有的膠料都適合使用熱流道系統
4.1 要求塑料有較寬的熔融溫度範圍, 低溫時流動性 好, 高溫時具有較好的熱穩定性. 這樣可以較容 易地控制溫度, 防止澆口冷卻固化. 膠料要有較 高的熱變形溫度, 這樣可以在較高模溫下取出成 品, 縮短成型生產周期. 如大缸可樂瓶(PET料), 4.2 壓力敏感, 不加壓力不流動, 但施加壓力時即可 流動. 4.3 比熱小, 導熱性好, 以便在模具中很快冷卻. 市面上最能滿足以上特性的有PE(花料) ﹑PP百折膠﹑PET, 當然, ABS﹑PS也大致滿足以上特性要求, 而PVC則不具備這 些特性.
End
圖 三
圖 四
此嘴要考慮熱膨脹後不 能與對面模件鋼料面接 觸. 可以留空0.3~0.5mm
5. 容易控制整個裝置的溫度, 熱流道系統零件 與模板的接觸面積要按標準設計, 減少熱傳 遞, 熱流道板及熱嘴的附近都要設計冷卻水 道, “A”板底板應加運水控制溫度否則融熔 的膠料所提供的熱量很快會使模溫升高. 模 具在有熱流道系統的一側要設計隔熱板;
熱流道系統(HOT HALF)可以獨立組裝, 利于模 具的維護﹑保養.
五. 模具設計方面的重點 .
1. 熱流道系統設計的步驟:
a. 根據產品重量選擇適當的熱嘴系列 (Nozzle Product Line),
b. 根據膠料與產品要求選擇最佳的入水方式 (Gating Method),
c. 確定合理的入水孔尺寸(Gate Size), d. 根據模具結構選擇合適的熱嘴長度 (Nozzle Length),
四. 對熱流道裝置的性能要求.
流道板與熱嘴各組合部分不發生樹脂在系統 內滯留或泄漏, 不發生澆口阻塞, 即使萬一發 生問題也能容易地清除; 容易獲得澆口帄衡, 多腔或單腔多點入水都應 考慮這一問題, 否則無法控制制品的質量;
對於開放式噴嘴能有效地(TC)控制澆口溫度, 不會出現澆口流涎拉絲現象, 精密產品建議採 用閥式噴嘴來保證;
3. 熱嘴孔直徑以及熱嘴的中心距需參考資料 數據, 在模具圖中熱嘴處應該至少有垂直 兩個方向的切圖, 反映熱嘴實際長度尺寸 狀況, 同時也可確認熱嘴與膠位距離是否 合理.
4. 准确地估算熱流道系統的熱膨脹(如圖三,圖 四),計算公式如下:
T.E. = A x B x C = 預熱膨脹補償.
熱流道系統的設計
精深設計組 段長玉 製作
2004年9月20日
一.熱流道模的概念.
1. 借助於加熱裝置使澆 注系統中的塑料不會 2. 熱嘴的型式包括開式噴嘴 凝固, 也不會隨 製品 和針閥式噴嘴 : 脫模, 所以又稱無流 道模.
2.1開式噴嘴又分為有或無魚雷型分流梭兩種, 每一 成型周期完畢, 模具打開後會產生流涎, 熔融的 膠料會流入模腔, 使得再一次注射時在成品表 面形成疵點.一般可在啤機方面解決此問題.一 個成型周期完畢,注射機螺桿會有小小後縮, 使 得澆口處有負壓﹑倒流. 當然,此種負壓﹑倒流 只是為防止流涎發生的,不可能太大, 以防有空 氣進入熱咀. 關于分流梭的問題,DME的形式如 圖, 該種形式效果不如INCOE的好, 因為會有充 模線產生,分流孔太低造成.今後除非客人指定, 一般不用DME此種咀.