J009制动系统设计规范
制动系统设计规范
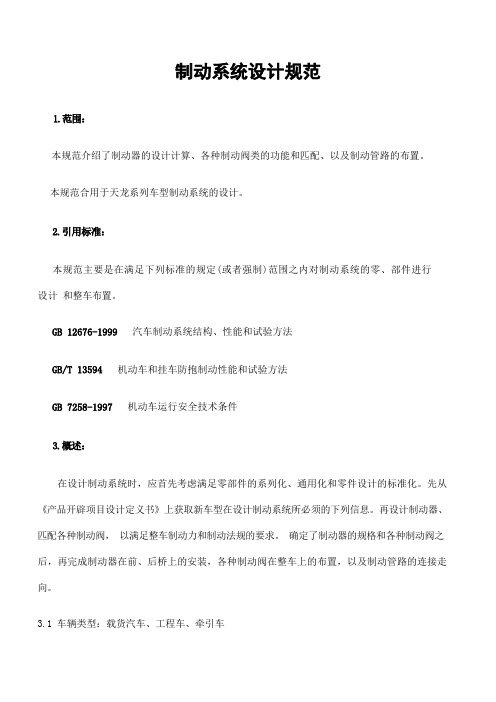
本规范介绍了制动器的设计计算、各种制动阀类的功能和匹配、以及制动管路的布置。
本规范合用于天龙系列车型制动系统的设计。
本规范主要是在满足下列标准的规定(或者强制)范围之内对制动系统的零、部件进行设计和整车布置。
汽车制动系统结构、性能和试验方法机动车和挂车防抱制动性能和试验方法机动车运行安全技术条件在设计制动系统时,应首先考虑满足零部件的系列化、通用化和零件设计的标准化。
先从《产品开辟项目设计定义书》上获取新车型在设计制动系统所必须的下列信息。
再设计制动器、匹配各种制动阀,以满足整车制动力和制动法规的要求。
确定了制动器的规格和各种制动阀之后,再完成制动器在前、后桥上的安装,各种制动阀在整车上的布置,以及制动管路的连接走向。
3.1 车辆类型:载货汽车、工程车、牵引车3.2 驱动形式:4×2、6×4、8×43.3 主要技术及性能参数:长×宽×高、轴距、空/满载整车重心高坐标、轮距、整备质量、额定载质量、总质量、前/后桥承载吨位、 (前/后)桥空载轴荷、 (前/后)桥满载轴荷、最高车速、最大爬坡度等。
3.4 制动系统的配置:双回路气/液压制动、弹簧制动、鼓/盘式制动器、防抱制动系统、手动/自动调整臂、无石棉磨擦衬片、感载阀调节后桥制动力、缓速器、排气制动。
本规范仅对鼓式制动器的各主要元件和设计计算加以阐述,盘式制动器的选型和计算将暂不列入本规范的讨论范围之内。
4.1 鼓式制动器主要元件:4.1.1 制动鼓:由于铸铁耐磨,易于加工,且单位体积的热容量大,所以,重型货车制动鼓的材料多用灰铸铁。
不少轻型货车和轿车的制动鼓为组合式,其圆柱部份用铸铁,腹板则用钢压制件。
制动鼓在工作载荷下将变形,使蹄、鼓间单位压力不均,带来少许踏板行程损失。
制动鼓变形后的不圆柱度过大,容易引起制动时的自锁或者踏板振动。
所以,在制动鼓上增加肋条,以提高刚度和散热性能。
中型以上货车,普通铸造的制动鼓壁厚为 13~18㎜。
TJJW 009-2014 HXD2B电力机车总体技术规范(报批稿)
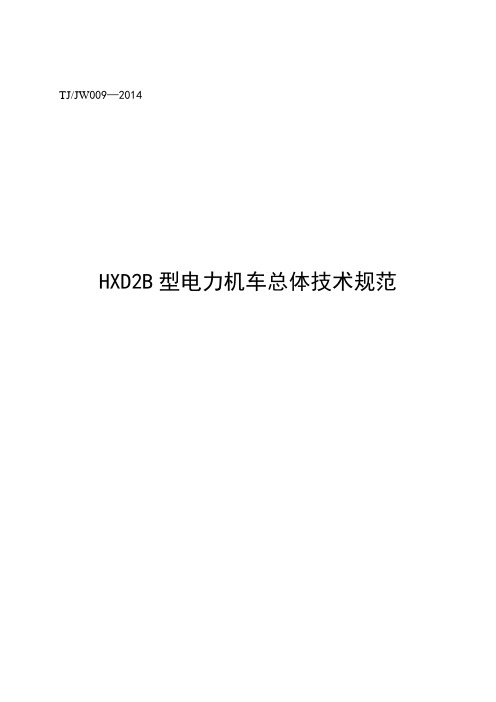
EN 1714:1997焊缝的无损检验—焊接接头的超声波检验(Non-destructive testing of welds-
IEC 60502-2额定电压1 kV(=1.2kV)至30kV( =36kV)挤出绝缘电力电缆及附件第2部分:额定电压1kV( =7.2kV)和30kV( =36kV)电缆(Power cables with extruded insulation and their
accessories for rated voltages from1kV(=7.2kV)up to30kV(=36kV)Part2:Cables with rated voltages from6kV( =7.2kV)up to 30kV( =36kV))
EN 13104铁路应用-轮对和转向-动车车轴设计方法(Railway applications - Wheelsets and bogies - Powered axles - Design method )
EN 13260铁路应用-轮对和转向架-轮对-产品要求(Railway applications - Wheelsets and bogies - Wheelsets - Product requirements)
Ultrasonic testing of welded joints)
EN 10084渗碳钢-交货技术条件 (Case Hardening Steels-Technicaldelivery Conditions)
制动系统设计规范

制动系统设计规范制动系统是车辆安全性能的重要组成部分,其设计规范的制定对于保证车辆行驶安全具有重要意义。
以下是关于制动系统设计规范的一些考虑因素。
1.制动力量:制动系统必须能够提供足够的制动力量,以便在各种条件下可靠地将车辆停下来。
制动力量应根据车辆的质量、设计速度、使用环境等因素进行评估,并确保能够适应各种道路状况和紧急制动情况。
2.制动系统的灵敏度:制动系统的设计应考虑车辆行驶时的灵敏度。
制动踏板应有适当的行程和力度,以确保驾驶员能够精确地控制制动力的大小,并根据需要适时调整。
3.制动系统的稳定性:制动系统在使用过程中应保持稳定性。
制动力的分配应均匀,以防止车辆在制动时出现不稳定或抱死现象。
此外,制动系统的热稳定性也是一个重要考虑因素,以确保长时间高强度制动时不会出现制动衰减或失效。
4.制动信号传递的可靠性:制动系统的信号传递应能够准确可靠地反映制动操作的实际情况,以保证驾驶员和其他车辆能够及时、准确地对制动操作做出反应。
传感器和传输装置的设计应具有高可靠性,能够承受恶劣的环境条件,如高温、湿度、振动等。
5.制动系统的耐用性:制动系统的设计应具备耐用性,以适应长时间、高频率的使用。
制动片和制动盘的材料选择应具有较高的磨擦耐久性和热稳定性,以延长制动系统的使用寿命,并减少维修和更换的频率。
6.制动系统的自动化和智能化:随着科技的发展,制动系统也向着自动化和智能化的方向发展。
制动系统设计应考虑集成各种智能传感器和控制单元,以提高制动系统的响应速度和精确性,使得制动操作更加方便和安全。
7.制动系统的安全性:制动系统是车辆安全性的关键因素之一,其设计应确保系统在任何情况下都能保持完全可靠和安全。
例如,制动系统应具备防止制动衰减或失效的措施,如制动助力器、制动液液位警告装置等。
总之,制动系统设计规范的制定是为了确保车辆行驶的安全性能。
以上所列的因素只是设计规范的一部分,实际的设计规范还需要涵盖更多方面,以满足不同车型和使用环境的需求,并不断适应科技的发展。
编制说明-商用车制动系统技术要求及试验方法

编制说明-商用车制动系统技术要求及试验方法一、引言商用车制动系统是一项至关重要的安全装备,其性能要求和试验方法的制定,对于保障商用车行驶安全、提高制动系统可靠性和稳定性具有重要意义。
本文将对商用车制动系统技术要求及试验方法进行详细说明。
二、技术要求1.制动力输出商用车制动系统应能提供足够的制动力输出,以确保在各种路况下能够及时有效地停车。
制动力输出应根据车辆的载荷和速度进行调整。
2.制动系统的稳定性商用车制动系统在不同工况下应具有稳定的性能。
制动系统的响应时间应短,制动力输出应平稳,制动褪力和传递系数应稳定。
3.制动距离商用车制动系统的制动距离应符合国家和地区的相关法规要求。
制动距离应足够短,以减少事故风险。
4.制动系统的可靠性商用车制动系统应具有高可靠性,能够在各种工况下正常工作。
制动系统的使用寿命应符合相关标准要求,零部件的耐久性应得到保证。
5.制動系統的回控性商用车制动系统在制动过程中应具有良好的回控性能,司机在操纵过程中应感到灵敏和准确,能够及时调整制动力的大小。
三、试验方法1.手动制动力测试使用相应的测力传感器和测试仪器,对商用车制动系统的手动制动力进行测试。
根据车辆的负载和速度,通过手动制动踏板测量并记录制动力的变化。
2.制动稳定性试验在特定路况下,对商用车制动系统的稳定性进行试验。
根据车辆的负载和速度,进行多次制动,记录制动褪力和传递系数的变化,并评估制动系统的稳定性。
3.制动距离测试在规定的路况下,测试商用车制动系统的制动距离。
根据车辆的起始速度和制动力,记录制动距离,并根据相关法规要求进行评估。
4.制动系统可靠性试验通过长时间的模拟使用和特定条件下的试验,评估商用车制动系统的可靠性。
记录系统的工作时间、故障次数和零部件的使用寿命,评估制动系统的可靠性。
5.制动回控性试验在特定条件下,对商用车制动系统的回控性能进行试验。
通过模拟常见的操纵动作,记录司机操纵制动系统的反应时间和准确度,并评估制动系统的回控性能。
13制动系统设计规范

13制动系统设计规范制动系统是一款车辆非常重要的安全系统,直接影响到车辆的制动性能和行车安全。
对于制动系统的设计规范,下面将从设备选型、布置设计、控制系统设计、保养与维护等方面进行详细阐述。
一、设备选型1.制动器选型:根据车辆的类型、质量和运行速度等因素选择适合的制动器,确保其能够承受对应的制动力,并具有稳定的制动性能。
2.主缸和助力器选型:根据车辆的质量和制动需求选择合适的主缸和助力器,确保能够提供足够的制动力,并具有快速响应和稳定性好的特点。
3.制动片/鼓选型:选择耐磨、散热性好、摩擦稳定的制动片/鼓,并根据车辆使用情况进行适当调整。
二、布置设计1.制动管路设计:设计合理的制动管路,确保制动力能够传递到各个轮子,并且管路布置尽量简洁,减少制动力的损失。
2.制动助力器布置:助力器应设置在主缸和制动器之间,布置合理,保证管路短连接,提高制动效果。
三、控制系统设计1.制动系统电气设计:根据车辆的特点,选择合适的电气元件和线路布置,确保电气系统的可靠性和稳定性。
2.制动踏板设计:踏板应符合人体工程学原理,力度适中,操作感受良好,能准确感知制动力大小和变化。
3.制动系统控制策略设计:根据车辆的特点和需求,制定合理的制动控制策略,确保制动力分配均匀、稳定。
四、保养与维护1.定期检查制动系统的工作状况,包括制动片/鼓磨损情况、制动液油位和油质、制动踏板行程、制动管路漏气等。
2.定期更换制动片/鼓和制动液,确保制动系统的正常工作和稳定性。
3.检查和保养助力器,确保其功能正常,能够提供足够的助力。
以上是对13制动系统设计规范的详细阐述,设计和保养制动系统时必须要考虑到车辆的特点和使用情况,确保其能够提供稳定、可靠的制动性能,保障行车安全。
同时,制动系统的设计和维护也需要参考相关的法律法规,以确保制动系统符合强制性标准,且能满足用户需求。
汽车制动系统安全要求
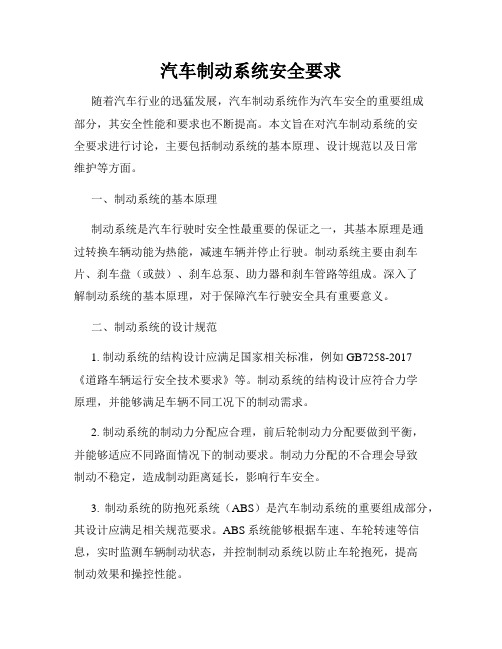
汽车制动系统安全要求随着汽车行业的迅猛发展,汽车制动系统作为汽车安全的重要组成部分,其安全性能和要求也不断提高。
本文旨在对汽车制动系统的安全要求进行讨论,主要包括制动系统的基本原理、设计规范以及日常维护等方面。
一、制动系统的基本原理制动系统是汽车行驶时安全性最重要的保证之一,其基本原理是通过转换车辆动能为热能,减速车辆并停止行驶。
制动系统主要由刹车片、刹车盘(或鼓)、刹车总泵、助力器和刹车管路等组成。
深入了解制动系统的基本原理,对于保障汽车行驶安全具有重要意义。
二、制动系统的设计规范1. 制动系统的结构设计应满足国家相关标准,例如GB7258-2017《道路车辆运行安全技术要求》等。
制动系统的结构设计应符合力学原理,并能够满足车辆不同工况下的制动需求。
2. 制动系统的制动力分配应合理,前后轮制动力分配要做到平衡,并能够适应不同路面情况下的制动要求。
制动力分配的不合理会导致制动不稳定,造成制动距离延长,影响行车安全。
3. 制动系统的防抱死系统(ABS)是汽车制动系统的重要组成部分,其设计应满足相关规范要求。
ABS系统能够根据车速、车轮转速等信息,实时监测车辆制动状态,并控制制动系统以防止车轮抱死,提高制动效果和操控性能。
4. 制动系统的设计应考虑车辆负载情况,以及车辆在爬坡、紧急制动等特殊工况下的制动需求。
针对不同类型的车辆,制动系统的设计应有所差异,以确保系统能够适应不同工况下的制动需求。
5. 制动系统的材料选择和加工工艺应符合相关标准和规范,以确保制动系统的可靠性和耐久性。
刹车盘、刹车片等制动部件的材料应具有良好的热导性和耐磨性,以满足长期制动以及剧烈制动情况下的要求。
三、制动系统的日常维护1. 定期检查制动系统的工作状态,包括制动片磨损情况、刹车盘变形情况、刹车液是否正常等。
发现异常情况及时更换或修复,以确保制动系统的正常工作。
2. 定期检查制动系统的液压管路是否有渗漏、老化等问题,及时更换损坏的管路,以防止制动失效。
车辆制动方案设计规范
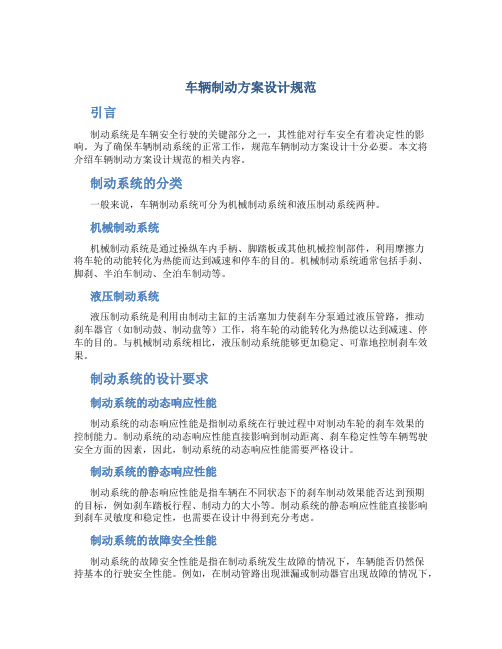
车辆制动方案设计规范引言制动系统是车辆安全行驶的关键部分之一,其性能对行车安全有着决定性的影响。
为了确保车辆制动系统的正常工作,规范车辆制动方案设计十分必要。
本文将介绍车辆制动方案设计规范的相关内容。
制动系统的分类一般来说,车辆制动系统可分为机械制动系统和液压制动系统两种。
机械制动系统机械制动系统是通过操纵车内手柄、脚踏板或其他机械控制部件,利用摩擦力将车轮的动能转化为热能而达到减速和停车的目的。
机械制动系统通常包括手刹、脚刹、半泊车制动、全泊车制动等。
液压制动系统液压制动系统是利用由制动主缸的主活塞加力使刹车分泵通过液压管路,推动刹车器官(如制动鼓、制动盘等)工作,将车轮的动能转化为热能以达到减速、停车的目的。
与机械制动系统相比,液压制动系统能够更加稳定、可靠地控制刹车效果。
制动系统的设计要求制动系统的动态响应性能制动系统的动态响应性能是指制动系统在行驶过程中对制动车轮的刹车效果的控制能力。
制动系统的动态响应性能直接影响到制动距离、刹车稳定性等车辆驾驶安全方面的因素,因此,制动系统的动态响应性能需要严格设计。
制动系统的静态响应性能制动系统的静态响应性能是指车辆在不同状态下的刹车制动效果能否达到预期的目标,例如刹车踏板行程、制动力的大小等。
制动系统的静态响应性能直接影响到刹车灵敏度和稳定性,也需要在设计中得到充分考虑。
制动系统的故障安全性能制动系统的故障安全性能是指在制动系统发生故障的情况下,车辆能否仍然保持基本的行驶安全性能。
例如,在制动管路出现泄漏或制动器官出现故障的情况下,车辆仍然能够安全行驶。
因此,在制动系统的设计中需要考虑故障安全性能,制定相应的应急措施和预防措施。
制动系统的舒适性能制动系统的舒适性能是指车辆在制动时驾驶员和乘客的舒适感受,例如制动的平稳性、噪声和震动的减小等方面。
舒适性能的设计直接影响到驾驶员和乘客的使用体验,也对车辆整体的质量感受和品牌形象有着一定的影响。
制动系统的维护制动系统的正常维护对车辆的安全性至关重要。
制动系统设计概论
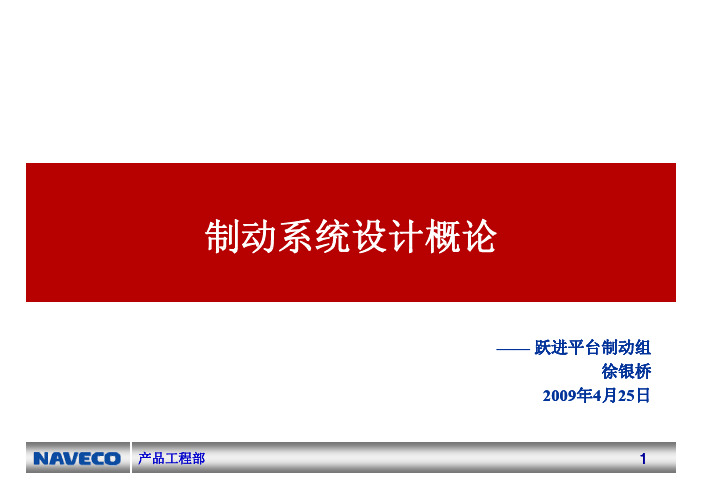
制动系统设计概论——跃进平台制动组徐银桥2009年4月25日制动系统制动系统的分类功能制动系统的分类(功能)1.行车制动系¾双回路机构22. 应急制动系¾不需要每车必备¾轮边驻车制动可兼做应急制动3. 驻车制动系¾中央鼓式或轮边制动4. 辅助制动系¾排气辅助制动、缓速器制动系统应满足如下要求制动系统应满足如下要求(一)1. 应满足有关标准和法规的规定¾“GB12676-1999”汽车制动系统结构、性能和试验方法--新车、路试检测¾“GB7258-2004”机动车运行安全技术条件--年检、台试检测2. 具有足够的制动效能:行车制动效能和驻车制动效能¾制动距离¾制动减速度¾最大坡度3. 制动效能的稳定性好制动系的性能指标¾制动效能的热衰退¾制动效能的水衰退制动系统应满足如下要求制动系统应满足如下要求(二)4. 制动时的汽车操纵稳定性好¾制动跑偏制动系的性能指标¾前轮抱死--失去操纵性¾后轮抱死--甩尾,失去方向稳定性5. 制动踏板和手柄的位置和行程符合人-机工程学要求¾操纵方便、轻便¾踏板行程要合适¾制动效能高6. 制动时不应产生振动和噪音制动系统的设计分两大块:制动系统的设计分两大块确定整车所需最小制动力一、确定整车所需最小制动力Â例:4.5T 车辆计算:满载-标准满载-前轴最满载-后轴最空载超载制动减速度总制动力前轮附着力后轮附着力整车输入参数:例车辆计算前后轮附着力:大大重量Kg 4500 4500 4500 2420 5850 前轴轴荷Kg 1650 2100 1200 1400 2280 满载-标准0.7g 5418 2972 2445满载后轴轴荷Kg 2850 2400 3300 1020 3570 重心高度860860860720860满载-前轴最大0.7g 5418 35141904满载-mm 860 860 860 720 860 重心到前轴距离mm 2095 1764 2426 1394 2019重心到后轴后轴最大0.7g 5418 2431 2987超载0.7g 7043 4027 3016 距离mm 1213 1544 882 1914 1289轴矩mm 3308 3308 3308 3308 3308 轮胎滚动半空载0.7g29142129784径mm351351351351351二、制动器类型(一)制动类型从蹄领蹄领从蹄--NJ131系列S凸轮式--气制动制动类型二、制动器类型(二)领蹄领蹄双领蹄国际版前制动器双向自增力式国际版后制动器双领蹄--国际版前制动器双向自增力式--国际版后制动器制动类型二、制动器类型(三)z 优点:¾热稳定性好:易散热;¾水稳定性好:易将沾上的水去除;¾制动稳定性好:制动器效能因素低,摩擦块系数的变化引起的制动力矩变化小;左右盘式制动器的摩擦块与制动盘工作时的接触面差异很小,引起的左右制动力矩变化小;¾间隙自动调整装置易实现;实现¾摩擦块磨损报警装置易实现;z 缺点:盘式制动器浮动钳缺点¾难防尘污和锈蚀;¾装于后轮兼作驻车制动器时,驻车制动盘式制动器-浮动钳驱动机构较复杂;三、选择合适的制动器选择合适的制动z需要考虑的因素:¾制动器效能因素;¾制动器的热衰退性和速度衰退性;制动器的热衰退性和速度衰退性z经验:¾尽量选用效能因素低的制动器;¾选择制动器制动力矩的时候,以台架试验数据为参考,最好以60km/h条件下得到的制动力矩为参考;Â摩擦材料系数:0.4±0.06摩擦材料系数04006四确定前后制动力分系数整车制动力匹配设计四、确定前后制动力分配系数Â例:4.5T 车辆制动力分配曲线图设计要点:设计要点避免后轮先于前轮抱死液压制动系统和气压制动系统比较液压制动系统气压制动系统驱动机构真空助力--伺服制动气压--动力制动真空泵压缩机发动机动力源0.8 bar8 bar 脚踏板装置操纵装置控制装置制动器的执行机构轮边分泵制动气室,S凸轮分泵直径受空间限制制动气室直径大间隙自调装置集成在轮边分泵内,无级式集成在调整臂内,阶跃式系统工作压力120 bar 8 bar驻车制动机械式--人力制动机械式--储能弹簧中央鼓式或轮边制动轮边制动中重型载货汽车适用车辆7T以下轻型载货汽车中、重型载货汽车液压制动动机构的设计液压制动驱动机构的设计Â例:4.5T 车辆计算:制动器制动力矩前(4050Nm/120bar )后(3000Nm/120bar )系统最高压力(120bar )后主缸缸径行程 制动器轮边分泵前(¢30)后(¢25.4)(吸油量)主缸缸径、行程(¢30 、20+15)真空助力器规格(9′+10 ′ )真空泵真空度Â匹配依据:制动踏板的(0.8bar )自由行程、总行程要合适,制动效能高.液压制动驱动机构(真空助力--伺服制动)真空助力器前制动器轮边分泵后制动器轮边分泵真空筒真空泵感载阀真空供能管路双回路制动管路气压制动驱动机构(气压--动力制动)供能管路制动管路驻车管路辅助用气管路再见!。
- 1、下载文档前请自行甄别文档内容的完整性,平台不提供额外的编辑、内容补充、找答案等附加服务。
- 2、"仅部分预览"的文档,不可在线预览部分如存在完整性等问题,可反馈申请退款(可完整预览的文档不适用该条件!)。
- 3、如文档侵犯您的权益,请联系客服反馈,我们会尽快为您处理(人工客服工作时间:9:00-18:30)。
Q/XRF-J009-2015xxxx制动系统设计规范xxx公司发布Q/XRFXXX公司2015-03-15 发布2015-03-15实施目录一概述................................................... 2...1.1 制动系统基本介绍 (2)1.2 制动系统的结构简图 (2)二法规要求............................................... 3...2.1 GB12676-1999 法规要求 (3)2.2 GB 7258-2012 法规要求 (4)三制动动力学 (4)3.1 稳定状态下的加速和制动 (4)3.2 制动系统设计与匹配的总布置设计硬点或输入参数 (5)3.3 、理想的前、后制动器制动力分配曲线 (6)3.3.1 基本理论 (6)四计算算例与分析改进方法................................. 7..4.1 前、后轮制动器制动力矩的确定 (8)4.1.1 制动器的制动力矩计算 (8)4.1.2 确定车型的制动器制动力矩 (11)4.2 比例阀的设计 (12)4.2.1 举例基本参数 (13)4.2.2 GMZ1 的校核 (13)4.2.3 GZM2 的校核 (14)4.2.4 设计优化曲线 (15)4.3 总泵的校核 (17)4.3.1 基本参数 (17)4.3.2 基本理论 (18)4.3.3 校核结果 (18)概述制动系是汽车的一个重要的组成部分。
它直接影响汽车的行驶安全性。
为了保证汽车有良好的制动效能,本规范指导汽车的制动性能及制动系结构的设计。
1.1制动系统基本介绍微型电动货车的行车制动系统采用液压制动系统。
前、后制动器分别为盘式制动器和鼓式制动器,前制动盘为空心通风盘,制动踏板为吊挂式踏板,带真空助力器,制动管路为双回路对角线(X型)布置,采用ABS以防止车辆在紧急制动情况下发生车轮抱死。
驻车制动系统为机械式手动后轮鼓式制动,采用远距离棘轮拉索操纵机构。
1.2 制动系统的结构简图图1 制动系统的结构简1.真空助力器带制动主缸总成2.制动踏板3.车轮4.轮速传感器5.制动管路6.制动轮缸7.ABS控制器法规要求2.1 GB12676-1999 法规要求发动机脱开的0型试验性能要求。
丰辆类型M,N:N:N:试脸车剧动如遽虞小―山806U典]6D60—___ ____ •_湖动範离耳—小发动机接合的型试验性能要求节豔类熨Mi M s M a N,试瞪车制动初建囉U三凹瓢TZ.但啞km/hJ&C-100120j<X>SCf) 1 3 ij "m Z P 103.f死分雄也的平均械速虜MFDI^mZs s3. 0^.0见乂控制力用5«(|7CI帘衲类型动初連度QpkimZli 濮載制动軍离Sgra 1MFDD问間空戟剖动距縄m秃分览州的〜平为减速廛MFDDUlf*.Ml sc rt, lix-" 1 -“卄器■着 1. 15M.60 1. 51- 3 M,AO.,.- 100T'-1*5"21齧•备1- 5Wi .TO4坊严型•上L2 S0 1151. 5 b i50n ”丄IM /Of+前*帀1*3—罟V氣】40,inc ( z”i冲.崗1-31:,15 t +1151 31 车辆类别丸分岌出的平均减谨度仃民| 二M | 最大控制力,N5002.2 GB 7258-2012 法规要求GB 7258-2012法规要求:汽车、无轨电车和四轮农用运输车的行车制动,必须采用双管路或多管路,当部分管路失效时,剩余制动效能仍能保持原规定值的 30%以上。
三制动动力学3.1 稳定状态下的加速和制动加速力和制动力通过轮胎和地表的接触面从车辆传送到路面。
惯性力作用于车 辆的重心,引起颠簸。
在这个过程中当刹车时,前后轮的负载各自增加或减少;而 当加速时,情况正好相反。
制动和加速的过程只能通过纵向的加速度 a x 加以区分。
下面,我们先来分析一辆双轴汽车的制动过程。
最终产生结果的前后轮负载F ZV 和F Zh ,在制动过程中,图2随着静止平衡和制 动减速的条件而变为:F ZV 二 mg I -l v l - ma * h l(3.1a ) F zh =mgl v I ma x h I(3.1b )设作用于前后轴的摩擦系数分别为f v 和f h ,那么制动力为:F xv 二 F zV f V(3.2a )Fxh = F zh fh(3.2b )图2双轴汽车的刹车过程2 rr>g4l-lj/h-6 kN Jii = 15ODk5 I =2700 mml^iiaSOffrr.-rnq-i^/h它们的总和便是作用于车辆上的减速力。
F XV FXh - ma对于制动过程,f v和f h是负的。
如果要求两轴上的抓力相等,这种相等使f v = f h= a x/g,理想的制动力分配是:F xv =ma x[g(l - l v) -a x h]/(gl)(3.4)F xh =ma x[gl v a x h]/(gl)(3.5)这是一个抛物线F xh(F xv)和参数a x的参数表现。
在图1的右半部分,显示了一辆普通载人汽车的理想制动力分配。
实践中,向两边分配制动力通常被选用来防止过早的过度制动,或是由刹车片摩擦偏差而引起的后轮所死,因为后轮锁死后将几乎无法抓地,车辆将会失去控制。
防抱死刹车系统这个问题。
当然,每一个负载状态都有它各自的理想制动力分配。
如果所有负载状态都必须由一个固定的分配去应对,那么最重要的条件往往就是空载时的情况。
虽然固定的分配在更多负载时无法实现最优化的制动力分配,b线显示了当后轴的制动力未超过理想值直到最大减速度为0.8g时的制动力分配情况。
弯曲的分配曲线可通过如下方法应用。
对于双轴货车,轮子在制动中的负载只取决于减速度,而不取决于设定的制动力分配。
3.2制动系统设计与匹配的总布置设计硬点或输入参数新车型总体设计时能够基本估算如下基本设计参数,这些参数作为制动系统的匹配和优化设计的输入参数。
(3.3)3.3、理想的前、后制动器制动力分配曲线3.3.1基本理论(1)地面对前、后车轮的法向反作用力在分析前、后轮制动器制动力分配比例以前,首先了解地面作用于前、后车轮 的法向反作用力。
由图2,对后轮接地点取力矩得duF 心”忖式中:Fz1——地面对前轮的法向反作用力;G——汽车重力;b-------- 汽车质心至后轴中心线的距离; m――汽车质量; hg――汽车质心高度;dudt――汽车减速度。
对前轮接地点取力矩,得du F z2L 二Ga -m h gdt g式中hFz1J一 1LFz2L图2地面对前、后车轮的法向反作用力F z2地面对后轮的法向反作用力;a----- 汽车质心至前轴中心线的距离则可求得地面法向反作用力为-g dt 丿h g du " ag dt 丿在任何附着系数的路面上,前、后车轮同时抱死的条件是:前、后轮制动器制 动力之和等于附着力;并且前、后轮制动器制动力分别等于各自的附着力,即:F^ = - Fzi F .2 = ;:F z29消去变量,得1「G 丄 4hgL Gb F厂古;严方印一(可2F “四计算算例与分析改进方法由上述结果可以分别得出车型 A 和车型B 的前、后车轮同时抱死时前、后制动 器制动力的关系曲线一一理想的前、后轮制动器制动力分配曲线,简称 I 曲线。
下图为举例车型空载和满载时候的I 曲线 一2( N )F z2⑵前、 后制动器制动力分配曲线图3 I曲线4.1前、后轮制动器制动力矩的确定4.1.1制动器的制动力矩计算制动器通常分为盘式制动器和鼓式制动器。
下面就两种制动器分别进行制动力矩的计算。
举例:已知制动总泵的参数如下:盘式制动器的制动力矩计算(a)基本参数计算依据假定衬块的摩擦表面全部与制动盘接触,且各处单位压力分布均匀,则制动器的制动力矩为:M』2fF0R式中f——摩擦系数;F o——单侧制动块对制动盘的压紧力;R――作用半径(c)计算结果下面为盘式制动器的制动力矩与摩擦系数之间的关系曲线M" (Nm图4盘式制动器的制动力矩-摩擦系数的关系曲线由上图可以看出,当摩擦系数在0.35〜0.42之间时,盘式制动器所能提供的摩擦力矩在1205Nm r 1447Nm 之间。
当f = 0.38时,鼓式制动器提供的摩擦力矩为1309Nm (2)鼓式制动器的制动力矩计算 (a)基本参数 计算依据 在摩擦衬片表面取一横向微元面积,由鼓作用在微元面积上的法向力为:dF1 = dF1 fR 二P max bfR 2 sin : d :- 对于紧蹄: M jitlF^l fh R1 cl/cos (51) + f-sin ((51)) - f ・Rl对于松蹄: M jit2F^l fh R1cl/cos (51) - f-sin ((51)) + f ・Rl 其中 (51atan Cg (2・Gl ) - COS (3TQ :2)(才0 - sin (才疣2) + sin(2*al ) (cos(fll)- cos(fl£2)) R1二]- COS (2-a2))J + 0/3 - sin (2T C^2) + sin (2T CYl))2(c)计算结果 下图为鼓式制动器所能提供的制动力矩一一摩擦系数曲线。
( Nm640620 -600 -580 -560 -540 -520 -500 -480 -460 -440 --------------- >------------ 1------------- 1 ------------ 1 ------------ J--------------- J ------------ 1 ------------ 1 -------------0.34 0.35 0.36 0.37 0.38 01.39 0.4 0.41 0.42 0.43图5鼓式制动器所能提供的制动力矩-摩擦系数曲线由上图可以看出,摩擦系数在0.35〜0.42之间时,制动力矩在524Nm r 706.53Nm 之间。
当f = 0.38时,鼓式制动器提供的摩擦力矩为598.316Nm(3)确定同步附着系数通过上述关于制动器的制动力矩的计算,可以得到前、后制动器之间的制动力分配的比例::p _M耳+M辿通过这个曲线与I曲线的交点处的附着系数为同步附着系数4.1.2确定车型的制动器制动力矩(1)基本原理选定同步附着系数© 0,举例如确定为0.7 并用下列计算前、后轮制动力矩的比值。
然后,根据汽车满载在柏油、混凝土路面上紧急制动到前轮抱死,计算出前轮制动器的最大制动力矩My 1max在根据前、后轮制动力矩的比值计算出后轮制动器的最大制动力矩My 2max (2)基本参数(3)计算结果4.2比例阀的设计由于,对于具有固定比值的前、后制动器制动力的制动系特性,其实际制动力分配曲线与理想的制动力分配曲线相差很大,附着效率低。