第六章 凸轮机构的运动设计
机械原理:第6章 凸轮机构
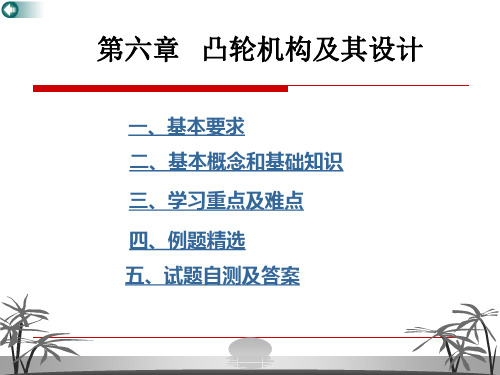
的压力角α ? 3.求出r0 、s 和α之间的关系式?
本题目主要考察对基圆、压力角及位移等 基本概念的理解和压力角的计算方法。 解
(1)图示位置的r0 、s 和α如图。
(2)r0 、s 与α之间的关系式为:
tan
v e
lOP e 1
r02 e2 s s r02 e2
例3 图示为摆动滚子从动件盘形凸轮机构,凸轮为偏心圆盘, 且以角速度ω逆时针方向回转。
试在图上标出: 1. 凸轮基圆;
2. 升程运动角和回程运动角;
3. 图示位置时从动件的初始位置角
0和角位移 ;
4. 图示位置从动件的压力角α;
5. 从动件的最大角位移max 。
r0min
( d s)2 e2 tan[ ]
直动滚子从动件盘 形凸轮机构
凸轮基圆半径
r0
m in
s
d2s
d 2
式中
([ dx )2 ( dy )2 ]3/ 2
d
dx
d
.
d2 y
d 2
d
dy
d
.
d2x
d 2
条件 min
直动平底从动件盘 形凸轮机构
滚子半径的设计
考虑运动失真: rr 0.8min 考虑强度要求: rr (0.1 ~ 0.5)r0
以凸轮转动中心为圆心,以凸轮理论轮廓曲线上的 最小半径为半径所画的圆。半径用r0表示。 从动件从距凸轮转动中心的最近点向最远点的运动过程。 从动件从距凸轮转动中心的最远点向最近点的运动过程。 从动件的最大运动距离。常用 h 表示行程。
基本名词术语
(5)推程角 从动件从距凸轮转动中心的最近点运动到最远点时, 凸轮所转过的角度。用Φ表示。
第六章 凸轮机构
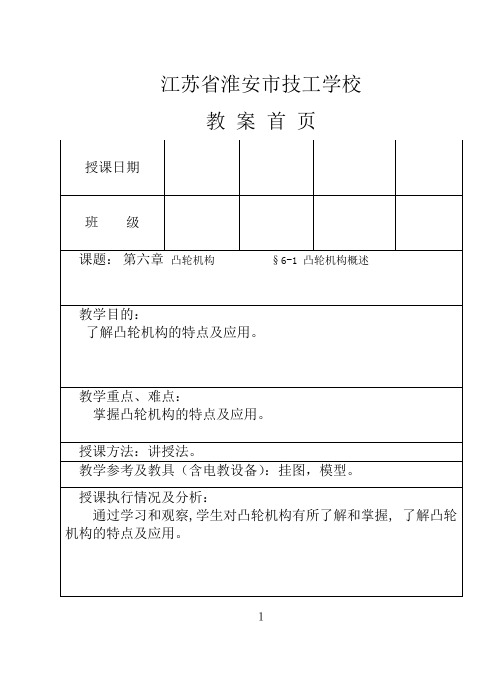
升程——从动件从最低位置升到最高位置的过程。
推程角φ1——推动从动件实现推程时的凸轮转角。
远休止角φ2——当凸轮继续回转时,从动件在最高位置停止不动,与此对应的凸轮转角,又称远停角。
回程——从动件从最高位置下降到最低位置的过程。
回程角φ3——回程时所对应的凸轮转角。
学生回答
板书
挂图
板书
挂图
教学环节
教 学 内 容
教学方法
巩固小结:
布置作业:
合考虑作出决定。
1.等速运动规律
从动件上升(或下降)的速度为一常数的运动规律——等速运动规律。
等速运动规律的凸轮,其轮廓工作曲线上各点的半径与凸轮转角成线性关系,因此工作轮廓曲线设计简单,加工时工件与刀具间相对运动容易实现。
等运动规律凸轮的缺点是:当从动件处于推程的开始位置时凸轮开始回转的一瞬间,从动件由静止状态突然以速度υ1上升运动,当从动件上升到最高位置时速度由υ2骤变为零,两者均使加速度达到无穷大而引起刚性冲击,对构件产生很大的破坏力。
2.凸轮机构的类型。
P107 1、2、5、8、9。
板书
挂图
作图
江苏省淮安市技工学校
教案首页
授课日期
班级
课题:
§6-2凸轮机构的工作原理
教学目的:
1.掌握凸轮机构从动件的运动规律;2.了解凸轮轮廓曲线的画法。
教学重点、难点:
掌握凸轮机构从动件的运动规律
授课方法:讲授法。
教学参考及教具(含电教设备):挂图,模型。
凸轮是具有曲线可曲面轮廓肯且作为高副元素的构件,凸轮轮廓按输出运动学特性和动力学特性的要求设计。
含有凸轮的机构称为凸轮机构。凸轮机构分为平面凸轮机构和空间凸轮机构两大类。所有构件间的相对运动均为平面运动的凸轮机构称为平面凸轮机构。各构件间的相对运动包含空间运动的凸轮机构称为空间凸轮机构。
第6章 凸轮机构及其设计习题
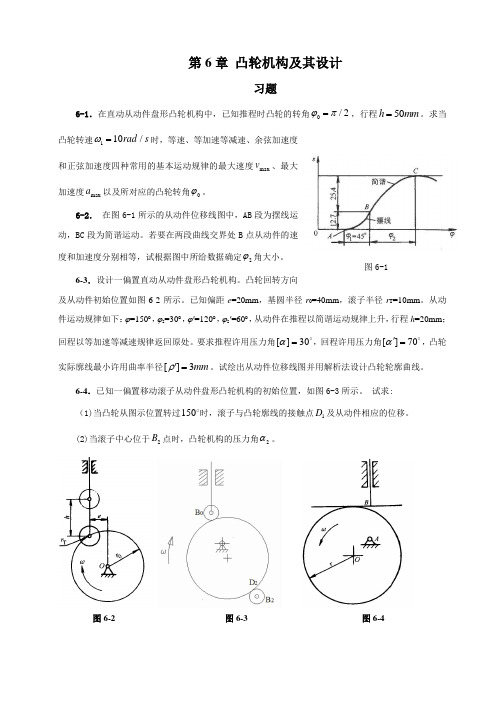
第6章 凸轮机构及其设计习题6-1.在直动从动件盘形凸轮机构中,已知推程时凸轮的转角0/2ϕπ=,行程50h mm =。
求当凸轮转速110/rad s ω=时,等速、等加速等减速、余弦加速度和正弦加速度四种常用的基本运动规律的最大速度max v 、最大加速度max a 以及所对应的凸轮转角0ϕ。
6-2. 在图6-1所示的从动件位移线图中,AB 段为摆线运动,BC 段为简谐运动。
若要在两段曲线交界处B 点从动件的速度和加速度分别相等,试根据图中所给数据确定2ϕ角大小。
6-3.设计一偏置直动从动件盘形凸轮机构。
凸轮回转方向及从动件初始位置如图6-2所示。
已知偏距e =20mm ,基圆半径r 0=40mm ,滚子半径r T =10mm 。
从动件运动规律如下:ϕ=150︒,ϕs =30︒,ϕ'=120︒,ϕs '=60︒,从动件在推程以简谐运动规律上升,行程h =20mm ;回程以等加速等减速规律返回原处。
要求推程许用压力角[]30α= ,回程许用压力角[]70α'= ,凸轮实际廓线最小许用曲率半径[]3mm ρ'=。
试绘出从动件位移线图并用解析法设计凸轮轮廓曲线。
6-4.已知一偏置移动滚子从动件盘形凸轮机构的初始位置,如图6-3所示。
试求:(1)当凸轮从图示位置转过150时,滚子与凸轮廓线的接触点1D 及从动件相应的位移。
(2)当滚子中心位于2B 点时,凸轮机构的压力角2α。
图6-2 图6-3 图6-4图6-16-5.如图6-4所示的直动平底从动件盘形凸轮机构,已知凸轮为30r mm =的偏心圆盘,20AO mm =,试求:(1)基圆半径和升程;(2)推程运动角、回程运动角、远休止角和近休止角;(3)凸轮机构的最大压力角和最小压力角;(4)从动件推杆的位移s 、速度v 和加速度a 的方程式;(5)若凸轮以110/rad s ω=匀速回转,当AO 成水平位置时推杆的速度。
《凸轮机构设》课件

凸轮机构的分类
凸轮机构可分为直线型凸轮、圆弧型凸轮和椭圆型凸轮,每种凸轮形式适用 于不同的运动转换需求。
直线型凸轮的设计
直线型凸轮的设计需要考虑凸轮的轨迹形状以及与其他零件的配合,以达到 所需的运动转换效果。
圆弧型凸轮的设计
圆弧型凸轮的设计需要考虑凸轮的半径和角度,以及与其他零件的配合,以实现所需的运动转换目标。
椭圆型凸轮的设计
椭圆型凸轮的设计需要考虑凸轮的椭圆形状参数,以及与其他零件的配合,实现旋转到直线或曲线的运动转换。
快速设计凸轮的方法
快速设计凸轮的方法包括使用计算机辅助设计软件、凸轮设计图谱和经验设 计法。
凸轮机构设在机械制造中的应用
机床制造
凸轮机构在机床的进给和工作台移动系统中得到 广泛应用。
凸轮机构设在机械改进中的应 用
凸轮机构设在机械改进中的应用可以提高机械设备的性能、效率和可靠性, 推动工业制造的发展进步。
凸轮机构设的未来发展趋势
凸轮机构设的未来发展趋势包括智能化、小型化、高效化和功能多样化等方向。
《凸轮机构设》PPT课件
本课件将深入探讨凸轮机构设计。包括凸轮机构的工作原理、分类、设计方 法以及在机械制造中的应用。欢迎加入本次精彩的凸轮之旅!
什么是凸轮机构设
凸轮机构设是一种机械传动机构,通过凸轮的运动将直线运动转变为曲线运动,广泛应用于机械制造领域。
凸轮机构的工作原理
凸轮机构依靠凸轮的几何形状,通过与其他零件的配合,将旋转运动转变为 直线运动或曲线运动。
凸轮机构设与高效机械制造的关系
凸轮机构设作为高效机械制造的基础之一,对机械制造的效率、稳定性和精度等方面起到关键作用。
凸轮机构设在节能机械制造中 的应用
凸轮机构设在节能机械制造中的应用可以降低能量消耗,提高机械系统的效 率和环保性能。
凸轮机构及其设计详解

第二节 凸轮机构的传力特性 G
传力特性分析目的 确定构件之间相互的作用力,为 解决磨损及强度尺寸设计提供可靠的 数据。
压力角—不计摩擦时,凸轮对
从动件作用力方向线nn与从动件上 力作用点的速度方向之间所夹的锐 角。
FR2 2
d
vl
F2R1
n
tb
B
t
1 F
n
传力特性分析
Fx 0 F sin( 1) (FR1 FR2 )cos2 0
确定凸轮的基圆半径rb。 步骤
● 确定凸轮转动轴心的位置
● 确定从动件的正确偏置方位以及偏距e
● 将[]代入前式
rb
d
s d tan[ ]
e
s
2
e2
● 确定ss(),求出dsd,代入上式求出一系列rb值,选
取其中的最大值作为凸轮的基圆半径
工程上常常借助于诺模图(Nomogram)来确定凸轮的 最小基圆半径。借助于诺模图既可以近似确定凸轮的最大 压力角,也可以根据所选择的基圆半径来校核最大压力 角。
一、工作循环图与凸轮工作转角的确定 凸轮的工作转角应当根据机器中各个执行机构动作之间 的配合关系,由工作循环图(Working cycle diagram)来确 定。
电阻坯件 电阻送料机构凸轮
电阻帽 送帽压帽机构凸轮
送帽压帽机构凸轮
夹紧机构凸轮
工艺过程
电阻自动压帽机传动系统图
电阻体上料
电阻体夹紧
送帽
合。
,t
⑸ 3–4–5次多项式运动规律(Law of polynomial motion)
推程
s
h10
3
15
4
6
5
第6章 凸轮机构(OK)

3. 图示为一偏置直动滚子从动件盘形凸轮机构,凸轮为偏心圆盘, 其直径D=42mm,滚子半径 rT=5 mm,偏距 e=6 mm 试求:
(1)画出基圆,并计算基圆半径; (2)画出凸轮的理论廓线;
(3)确定从动件的行程 h;
(4)确定从动件的推程运动角及回程 运动角;
(5)说明该机构在运动中有无失真现 象,为什么?
(1)图示位置的r0 、s 和α如图。 (2)r0 、s 与α之间的关系式为:
v tan lOP e r0 e s
2 2
1
e
s r02 e 2
例3 图示为摆动滚子从动件盘形凸轮机构,凸轮为偏心圆盘, 且以角速度ω逆时针方向回转。
试在图上标出:
1. 凸轮基圆; 2. 升程运动角和回程运动角; 3. 图示位置时从动件的初始位置 角0和角位移 ; 4. 图示位置从动件的压力角α; 5. 从动件的最大角位移max 。
解
压力角
摆 角
最大Байду номын сангаас角
(1)、(2)见上图。
(3)当α>[α]时,推动摆杆运动的有效分力减小,机械效率降低,
甚至发生自锁。可通过增大基圆 半径的方法减小压力角。
平底长度的设计
平底的长度:
l 2OPmax
ds l 2( ) max l d
式中:
l 5 ~ 7
mm
偏距的设计
偏距e 的计算公式
emax
vmax
式中
tan ds e d r e s
2 0 2
v e s0 s ( s0 s )
从动件的最大跃度jmax应尽量小
凸轮机构的反转法原理
第6章 凸轮机构 (教案)
第6章 凸轮机构1.教学目标(1)了解凸轮机构的分类及应用;(2)了解推杆常用运动规律的选择原则;(3)掌握在确定凸轮机构的基本尺寸时应考虑的主要问题;(4)能根据选定的凸轮类型和推杆运动规律设计凸轮的轮廓曲线。
2.教学重点和难点(1)推杆常用运动规律特点及选择原则;(2)盘形凸轮机构凸轮轮廓曲线的设计;(3)凸轮基圆半径与压力角及自锁的关系。
难点:“反转法原理”与压力角的概念。
3.讲授方法多媒体课件4.讲授时数8学时6.1 凸轮机构的应用及分类6.1.1凸轮机构的应用凸轮机构是由凸轮、从动件、机架以及附属装置组成的一种高副机构。
其中凸轮是一个具有曲线轮廓的构件,通常作连续的等速转动、摆动或移动。
从动件在凸轮轮廓的控制下,按预定的运动规律作往复移动或摆动。
在各种机器中,为了实现各种复杂的运动要求,广泛地使用着凸轮机构。
下面我们先看两个凸轮使用的实例。
图6.1所示为内燃机的配气凸轮机构,凸轮1作等速回转,其轮廓将迫使推杆2作往复摆动,从而使气门3开启和关闭(关闭时借助于弹簧4的作用来实现的),以控制可燃物质进入气缸或废气的排出。
图6.2所示为自动机床中用来控制刀具进给运动的凸轮机构。
刀具的一个进给运动循环包括:1)刀具以较快的速度接近工件;2)刀具等速前进来切削工件;3)完成切削动作后,刀具快速退回;4)刀具复位后停留一段时间等待更换工件等动作。
然后重复上述运动循环。
这样一个复杂的运动规律是由一个作等速回转运动的圆柱凸轮通过摆动从动件来控制实现的。
其运动规律完全取决于凸轮凹槽曲线形状。
由上述例子可以看出,从动件的运动规律是由凸轮轮廓曲线决定的,只要凸轮轮廓设计得当,就可以使从动件实现任意给定的运动规律。
同时,凸轮机构的从动件是在凸轮控制下,按预定的运动规律运动的。
这种机构具有结构简单、运动可靠等优点。
但是,由于是高副机构接触应力较大,易于磨损,因此,多用于小载荷的控制或调节机构中。
6.1.2 凸轮机构的分类根据凸轮及从动件的形状和运动形式的不同,凸轮机构的分类方法有以下四种:1.按凸轮的形状分类(1)盘形凸轮:如图6.1所示,这种凸轮是一个具有变化向径的盘形构件,当他绕固定轴转动时,可推动从动件在垂直于凸轮轴的平面内运动。
凸轮机构的设计计算和运动分析
% ******** 偏置移动从动件盘形凸轮设计绘图和运动分析******** disp ' ######## 已知条件########'disp ' 凸轮作逆时针方向转动,从动件偏置在凸轮轴心的右边'disp ' 从动件在推程作等加速/等减速运动,在回程作余弦加速度运动' % 基圆半径;滚子半径;从动件偏距;从动件升程rb=40;rt=10;e=15;h=50;% 推程运动角;远休止角;回程运动角;推程许用压力角;凸轮转速ft=100;fs=60;fh=90;alpha_p=35;n=200;% 角度和弧度转换系数;机构尺度hd=pi/180;du=180/pi;se=sqrt(rb^2-e^2);w=n*pi/30; omega=w*du; % 凸轮角速度(°/s)fprintf(' 基圆半径rb = %3.4f mm \n',rb)fprintf(' 滚子半径rt = %3.4f mm \n',rt)fprintf(' 推杆偏距 e = %3.4f mm \n',e)fprintf(' 推程升程h = %3.4f mm \n',h)fprintf(' 推程运动角ft = %3.4f 度\n',ft)fprintf(' 远休止角fs = %3.4f 度\n',fs)fprintf(' 回程运动角fh = %3.4f 度\n',fh)fprintf(' 推程许用压力角alpha_p = %3.4f 度\n',alpha_p) fprintf(' 凸轮转速n = %3.4f r/min \n',n) fprintf(' 凸轮角速度(弧度) w = %3.4f rad/s \n',w)fprintf(' 凸轮角速度(度) omega = %3.4f 度/s \n',omega) disp ' 'disp ' @@@@@@ 计算过程和输出结果@@@@@@' disp ' '% (1)---校核凸轮机构的压力角和轮廓曲率半径'disp ' *** 计算凸轮理论轮廓的压力角和曲率半径***'disp ' 1 推程(等加速/等减速运动)'for f=1:ftif f<=ft/2s(f)=2*h*f^2/ft^2;s=s(f); % 等加速-位移方程ds(f)=4*h*f*hd/(ft*hd)^2;ds=ds(f);d2s(f)=4*h/(ft*hd)^2;d2s=d2s(f);vt(f)=4*h*omega*f/ft^2; % 等加速-速度方程elses(f)=h-2*h*(ft-f)^2/ft^2;s=s(f); % 等减速-位移方程ds(f)=4*h*(ft-f)*hd/(ft*hd)^2;ds=ds(f);d2s(f)=-4*h/(ft*hd)^2;d2s=d2s(f);vt(f)=4*h*omega*(ft-f)/ft^2; % 等减速-速度方程endalpha_t(f)=atan(abs(ds-e)/(se+s)); % 推程压力角(弧度)alpha_td(f)=alpha_t(f)*du; % 推程压力角(度)pt1=((se+s)^2+(ds-e)^2)^1.5;pt2=abs((se+s)*(d2s-se-s)-(ds-e)*(2*ds-e));rho_t(f)=pt1/pt2; % 推程曲率半径st(f)=s;endalpha_tm=max(alpha_td);fprintf(' 推程最大压力角alpha_tm = %3.4f 度\n',alpha_tm)for f=1:ftif alpha_td(f)==alpha_tm;ftm=f;break;endendfprintf (' 对应的位置角ftm = %3.4f 度\n',ftm)if alpha_tm>alpha_pfprintf(' * 凸轮推程压力角超过许用值,需要增大基圆!\n')endrho_tn = min(rho_t);fprintf (' 最小曲率半径rho_tn = %3.4f mm\n',rho_tn)for f=1:ftif rho_t(f)==rho_tn;ftn=f;break;endendfprintf(' 对应的位置角ftn = %3.4f 度\n',ftn)if rho_tn<rt+5fprintf(' * 凸轮推程轮廓曲率半径小于许用值,需要增大基圆或减小滚子!\n') enddisp ' 2 回程(余弦加速度运动-简谐运动)'d1=ft+fs;d2=ft+fs+fh; % 回程运动角范围for f=d1:d2k=f-d1;s(f)=0.5*h*(1+cos(pi*k/fh));s=s(f); % 简谐运动-位移方程ds(f)=-0.5*pi*h*sin(pi*k/fh)/(fh*hd);ds=ds(f);d2s(f)=-0.5*pi^2*h*cos(pi*k/fh)/(fh*hd)^2;d2s=d2s(f);alpha_h(f)=atan(abs(ds+e)/(se+s)); % 回程压力角(弧度)alpha_hd(f)=alpha_h(f)*du; % 回程压力角(度)ph1=((se+s)^2+(ds-e)^2)^1.5;ph2=abs((se+s)*(d2s-se-s)-(ds-e)*(2*ds-e));rho_h(f)=ph1/ph2; % 回程曲率半径sh(f)=s;vh(f)=-0.5*pi*h*omega*sin(pi*f/fh)/fh; % 简谐运动-速度方程ah(f)=-0.5*pi^2*h*omega^2*cos(pi*f/fh)/fh^2; % 简谐运动-加速度方程endalpha_hm = max(alpha_hd(d1:d2));fprintf(' 回程最大压力角alpha_hm = %3.4f 度\n',alpha_hm)for f=d1:d2if alpha_hd(f)==alpha_hm;fhm=f;break;endendfprintf(' 对应的位置角fhm = %3.4f 度\n',fhm)rho_hn=min(rho_h(d1:d2));fprintf(' 最小曲率半径rho_hn = %3.4f mm\n',rho_hn)for f=d1:d2if rho_h(f)==rho_hn;fhn=f;break;endendfprintf(' 对应的位置角fhn = %3.4f 度\n',fhn)if rho_hn<rt+5fprintf(' * 凸轮回程轮廓曲率半径小于许用值,需要增大基圆或减小滚子!\n') enddisp ' '% (2)---计算凸轮机构的从动件运动参数'disp ' *** 计算凸轮机构从动件的运动参数***'disp ' 1 推程(等加速/等减速运动)'disp ' 凸轮转角位移s(mm) 速度v(mm/s)'for f=10:10:ftydcs_t=[f st(f) vt(f)];disp(ydcs_t)endat_1=4*h*omega^2/ft^2;at_2=-4*h*omega^2/ft^2;fprintf(' 等加速上升的加速度at_1 = %3.4f (mm/s^2) \n',at_1)fprintf(' 等减速上升的加速度at_2 = %3.4f (mm/s^2) \n',at_2)disp ' 2 回程(余弦加速度运动-简谐运动)'disp ' 凸轮转角位移s(mm) 速度v(mm/s) 加速度a(mm/s^2)'for f=d1:10:d2ydcs_h=[f sh(f) vh(f) ah(f)];disp(ydcs_h)end% (3)---绘制凸轮机构的从动件运动线图figure(1);subplot(3,2,1) % 推程位移线图f=1:ft;plot(f,st);xlabel ('凸轮转角\it \phi / \rm( °)')ylabel ('\it s / \rm(mm)')title('从动件推程位移线图');subplot(3,2,2) % 回程位移线图f=d1:d2;plot(f,sh(d1:d2));xlabel ('凸轮转角\it \phi / \rm( °)')ylabel ('\it s / \rm(mm)')title('从动件回程位移线图');subplot(3,2,3) % 推程速度线图f=1:ft;plot(f,vt);xlabel ('凸轮转角\it \phi / \rm( °)')ylabel ('\it v / \rm(mm/s)')title('从动件推程速度线图');subplot(3,2,4) % 回程速度线图f=d1:d2;plot(f,-vh(d1:d2));xlabel ('凸轮转角\it \phi / \rm( °)')ylabel ('\it v / \rm(mm/s)')title('从动件回程速度线图');subplot(3,2,5) % 推程加速度线图line([0,ft/2],[at_1,at_1]);line([ft/2,ft/2],[at_1,at_2]); % 等加速等减速之间的突变垂线line([ft/2,ft],[at_2,at_2]);xlabel ('凸轮转角\it \phi / \rm( °)')ylabel ('\it a / \rm(mm/s^2)')title('从动件推程加速度线图');subplot(3,2,6) % 回程加速度线图f=d1:d2;plot(f,-ah(d1:d2));xlabel ('凸轮转角\it \phi / \rm( °)')ylabel ('\it a / \rm(mm/s^2)')title('从动件回程加速度线图');disp ' '% (4)---计算凸轮理论廓线与实际廓线的直角坐标和向径'disp ' ****** 凸轮理论轮廓与实际轮廓的直角坐标******'nd=360;for f=1:ndif f<=ft/2 % 等加速运动s(f)=2*h*f^2/ft^2;s=s(f);ds(f)=4*h*f*hd/(ft*hd)^2;ds=ds(f);elseif f>ft/2 & f<=ft % 等减速运动s(f)=h-2*h*(ft-f)^2/ft^2;s=s(f);ds(f)=4*h*(ft-f)*hd/(ft*hd)^2;ds=ds(f);elseif f>ft & f<=d1 % 远休止角s=h;ds=0;elseif f>d1 & f<=d2 % 简谐运动k=f-d1;s(f)=0.5*h*(1+cos(pi*k/fh));s=s(f);ds(f)=-0.5*pi*h*sin(pi*k/fh)/(fh*hd);ds=ds(f);elseif f>d2 & f<=nds=0;ds=0;endxx(f)=(se+s)*sin(f*hd)+e*cos(f*hd);x=xx(f); % 理论轮廓横坐标yy(f)=(se+s)*cos(f*hd)-e*sin(f*hd);y=yy(f); % 理论轮廓纵坐标dx(f)=(ds-e)*sin(f*hd)+(se+s)*cos(f*hd);dx=dx(f);dy(f)=(ds-e)*cos(f*hd)-(se+s)*sin(f*hd);dy=dy(f);xp(f)=x+rt*dy/sqrt(dx^2+dy^2);xxp=xp(f); % 实际轮廓横坐标yp(f)=y-rt*dx/sqrt(dx^2+dy^2);yyp=yp(f); % 实际轮廓纵坐标r(f)=sqrt(x^2+y^2); % 理论轮廓向径rp(f)=sqrt(xxp^2+yyp^2); % 实际轮廓向径enddisp ' 1 推程(等加速/等减速运动)'disp ' 凸轮转角理论x 理论y 实际x 实际y'for f=10:10:ftnu=[f xx(f) yy(f) xp(f) yp(f)];disp(nu)enddisp ' 2 回程(余弦加速度运动)'disp ' 凸轮转角理论x 理论y 实际x 实际y'for f=d1:10:d2nu=[f xx(f) yy(f) xp(f) yp(f)];disp(nu)enddisp '*** 凸轮理论轮廓与实际轮廓的向径***'disp ' 1 推程(等加速/等减速运动)'disp ' 凸轮转角理论r 实际r'for f=10:10:ftnu=[f r(f) rp(f)];disp(nu)enddisp ' 'disp ' 2 回程(余弦加速度运动)'for f=d1:10:d2nu=[f r(f) rp(f)];disp(nu)end% (5)---绘制凸轮的理论轮廓和实际轮廓figure(2);plot(xx,yy,'r-.') % 理论轮廓(红色,点划线)axis ([-(rb+h-10) (rb+h+10) -(rb+h+10) (rb+rt+10)]) % 横轴和纵轴的下限和上限axis equal % 横轴和纵轴的尺度比例相同text(rb+h+3,0,'X') % 标注横轴text(0,rb+rt+3,'Y') % 标注纵轴text(-5,5,'O') % 标注直角坐标系原点title('偏置移动从动件盘形凸轮轮廓') % 标注图形标题hold on; % 保持图形plot([-(rb+h) (rb+h)],[0 0],'k') % 横轴(黑色)plot([0 0],[-(rb+h) (rb+rt)],'k') % 纵轴(黑色)plot([e e],[0 (rb+rt)],'k--') % 初始偏置位置(黑色,虚线)ct=linspace(0,2*pi); % 画圆的极角变化范围plot(rb*cos(ct),rb*sin(ct),'g') % 基圆(绿色)plot(e*cos(ct),e*sin(ct),'c--') % 偏距圆(青色,虚线)plot(e + rt*cos(ct),se + rt*sin(ct),'m') % 滚子圆(品红色)plot(xp,yp,'b') % 实际轮廓(蓝色)******** 偏置移动从动件盘形凸轮设计绘图和运动分析********######## 已知条件########凸轮作逆时针方向转动,从动件偏置在凸轮轴心的右边从动件在推程作等加速/等减速运动,在回程作余弦加速度运动基圆半径rb = 40.0000 mm滚子半径rt = 10.0000 mm推杆偏距 e = 15.0000 mm推程升程h = 50.0000 mm推程运动角ft = 100.0000 度远休止角fs = 60.0000 度回程运动角fh = 90.0000 度推程许用压力角alpha_p = 35.0000 度凸轮转速n = 200.0000 r/min凸轮角速度(弧度) w = 20.9440 rad/s凸轮角速度(度) omega = 1200.0000 度/s@@@@@@ 计算过程和输出结果@@@@@@*** 计算凸轮理论轮廓的压力角和曲率半径***1 推程(等加速/等减速运动)推程最大压力角alpha_tm = 34.2666 度对应的位置角ftm = 50.0000 度最小曲率半径rho_tn = 35.2303 mm对应的位置角ftn = 51.0000 度2 回程(余弦加速度运动-简谐运动)回程最大压力角alpha_hm = 30.9248 度对应的位置角fhm = 213.0000 度最小曲率半径rho_hn = 30.3591 mm对应的位置角fhn = 250.0000 度*** 计算凸轮机构从动件的运动参数***1 推程(等加速/等减速运动)凸轮转角位移s(mm) 速度v(mm/s)10 1 24020 4 48030 9 72040 16 96050 25 120060 34 96070 41 72080 46 48090 49 240100 50 0等加速上升的加速度at_1 = 28800.0000 (mm/s^2)等减速上升的加速度at_2 = -28800.0000 (mm/s^2)2 回程(余弦加速度运动-简谐运动)凸轮转角位移s(mm) 速度v(mm/s) 加速度a(mm/s^2) 160 50 673 -33602170 48 358 -41220180 44 0 -43865190 37 -358 -41220200 29 -673 -33602210 21 -907 -21932220 12.5 -1031.3 -7617.1230 5.8 -1031.3 7617.1240 2 -907 21932250 0 -673 33602****** 凸轮理论轮廓与实际轮廓的直角坐标******1 推程(等加速/等减速运动)凸轮转角理论x 理论y 实际x 实际y 10.0000 21.3848 34.8977 18.7440 25.2527 20.0000 28.1459 33.4732 26.5660 23.5988 30.0000 36.0309 32.4073 34.7788 22.4860 40.0000 45.6105 31.0206 43.9004 21.1679 50.0000 57.1986 28.4142 54.4870 18.7889 60.0000 69.0579 22.5501 63.1030 14.5165 70.0000 78.5024 12.6099 70.2060 7.0270 80.0000 84.4235 -0.3453 74.7846 -3.008390.0000 86.0810 -15.0000 76.0894 -14.5890 100.0000 83.1533 -29.8936 73.7429 -26.51052 回程(余弦加速度运动)凸轮转角理论x 理论y 实际x 实际y 160.0000 15.6881 -86.9597 13.9127 -77.1185 170.0000 0.0875 -86.8780 1.9206 -77.0474 180.0000 -15.0000 -81.2321 -9.9808 -72.5829 190.0000 -27.7230 -70.8432 -20.2897 -64.1539 200.0000 -36.8131 -57.2861 -27.8219 -52.9092 210.0000 -41.8603 -42.5041 -32.0770 -40.4336 220.0000 -43.3607 -28.3394 -33.3609 -28.2733 230.0000 -42.5280 -16.1041 -32.6176 -17.4398 240.0000 -40.9188 -6.3040 -31.0634 -7.9985 250.0000 -39.9750 1.4129 -29.9813 1.0597*** 凸轮理论轮廓与实际轮廓的向径***1 推程(等加速/等减速运动)凸轮转角理论r 实际r10.0000 40.9287 31.449020.0000 43.7338 35.533930.0000 48.4609 41.414840.0000 55.1597 48.737350.0000 63.8674 57.635560.0000 72.6465 64.751270.0000 79.5088 70.556880.0000 84.4242 74.845190.0000 87.3781 77.4754100.0000 88.3634 78.36342 回程(余弦加速度运动)160.0000 88.3634 78.3634170.0000 86.8780 77.0714180.0000 82.6054 73.2660190.0000 76.0745 67.2859200.0000 68.0948 59.7783210.0000 59.6564 51.6121220.0000 51.8003 43.7302230.0000 45.4750 36.9872240.0000 41.4015 32.0766250.0000 40.0000 30.0000。
机械原理凸轮机构含其设计
第六讲凸轮机构及其设计(一)凸机构的用和分一、凸机构1.成:凸,推杆,机架。
2.点:只要合适地出凸的廓曲,就可以使推杆获取各种期的运律,而且机构凑。
缺点:凸廓与推杆之点、接触,易磨,所以凸机构多用在力不大的合。
二、凸机构的分1.按凸的形状分:形凸柱凸2.按推杆的形状分尖推杆:构,能与复的凸廓保持接触,任意期运。
易遭磨,只适用于作用力不大和速度低的合子推杆:摩擦力小,承力大,可用于大的力。
不能够与凹槽的凸廓保持接触。
平底推杆:不考摩擦,凸推杆的作用力与从件平底垂直,受力平;易形成油膜,滑好;效率高。
不能够与凹槽的凸廓保持接触。
3.按从件的运形式分(1)往来直运:直推杆,又有心和独爱式两种。
( 2)往来运:推杆,也有心和独爱式两种。
4.依照凸与推杆接触方法不同样分:(1)力封的凸机构:通其他外力(如重力,性力)使推杆始与凸保持接触,( 2)几何形状封的凸机构:利用凸或推杆的特别几何构使凸与推杆始保持接触。
①等凸机构②等径凸机构③共凸(二)推杆的运动规律一、基本名:以凸的回心O 心,以凸的最小半径r0半径所作的称凸的基,r 0称基半径。
推程:当凸以角速度,推杆被推到距凸中心最的地址的程称推程。
推杆上升的最大距离称推杆的行程,相的凸角称推程运角。
回程:推杆由最位置回到初步地址的程称回程,的凸角称回程运角。
休止:推杆于静止不的段。
推杆在最静止不,的凸角称休止角;推杆在近来静止不,的凸角称近休止角二、推杆常用的运律1.性冲:推杆在运开始和止,速度突,加速度在理大将出瞬的无大,致使推杆生特别大的性力,所以使凸碰到极大冲,种冲叫性冲。
2.柔性冲:加速度有突,所以推杆的性力也将有突,不一突有限,所以引起有限冲,叫柔性冲。
3.掌握等速运律和等加速等减速运律的推程的速度、位移、加速度的方程:推杆运律——推杆在推程或回程,其位移s、速度 v 和加速度 a 随t 化的律。
3.1 多式运律:一般表示:s = C0+ C1δ+ C2δ2+⋯ + C nδn( 1)一次多式运律(等速运律)δδν推程:s=hδ/ δ0v = hω/δ0δa =0δ/ωh+∞δ-∞图7-7回程: s=h(1- δ / δˊ )v=- hδ ˊ0ω/图示为其推程运动线图。
凸轮机构的设计
(3)、许用压力角 为了提高机构的效率、改善其受力情况,通常 规 定 一 许 用 压 力 角 [α] , 使 。 推 程 : 直 动 推 杆 取 [α] = 300 ; 摆 动 推 杆 [α] = 400 ~ 500 ; 回程:通常不会引起自锁问题,但为了使推杆不至产生过大的加速 度从而引起不良后果,通常取 [α]= 700~800。 (4)、压力角校核 αmax一般出现在 1)从动件的起点位置 2)从动件最大速度位置 3)凸轮轮廓向径变化最大部分 滚子从动件按理论轮廓校核 平底从动件一般α=0,不需校核 若αmax > [α]: 增大基圆半径 偏置从动件
4、偏置直动尖顶从动件盘形凸轮机构 已知条件:已知凸轮的基圆半径为r0,凸轮转动方向。凸轮转 动中心与从动件摆动中心的距离,摆动从动件的长度,已知 从动件的运动规律,试设计。(从动件的位移是角位移 )
A0
ψ0 B1 B’1 φ o ω
1
-ω
ψ1 B2 ψ2
A1
B0
B’2
2
A2
φ
三、凸轮机构基本尺寸的确定
图所示为工程上常用的诺模 图,图中上半圆的标尺代表 凸轮转角δ0,下半圆的标尺 为最大压力角α max,直径 的标尺代表从动件规律的 h/rb的值(h为从动件的行程, rb为基圆半径)。下面举例 说明该图的使用方法。
2、凸轮压力角的校核
(1)、凸轮机构的压力角定义 凸轮机构从动件作用力的方向线与从动 件上力作用点的速度方向之间所夹的锐角, 用α表示。 (2)、压力角与作用力以及机构尺寸的关系 将凸轮对从动件的作用力F分解为F1和F2 。F2为有效分力,F1为有害分力,当压力角 α越大,有害分力F1越大,如果压力角增大 ,有害分力所引起的摩擦阻力也将增大,摩 擦功耗增大,效率降低。
- 1、下载文档前请自行甄别文档内容的完整性,平台不提供额外的编辑、内容补充、找答案等附加服务。
- 2、"仅部分预览"的文档,不可在线预览部分如存在完整性等问题,可反馈申请退款(可完整预览的文档不适用该条件!)。
- 3、如文档侵犯您的权益,请联系客服反馈,我们会尽快为您处理(人工客服工作时间:9:00-18:30)。
vmax
amax
从动件动量 mvmax 从动件惯性力 ma
max
对于重载凸轮机构,应选择 对于高速凸轮机构,宜选择
vmax 值较小的运动规律; amax值较小的运动规律。
组合运动规律
采用组合运动规律的目的:
避免有些运动规律引起的冲击,改善推杆其运动 特性。
构造组合运动规律的原则:
对于中、低速运动的凸轮机构,要求从动件的位
动画链接 实际应用 动画链接 实际应用
6.2
凸轮机构从动件运动规律的设计
基本术语
基圆 r0 :以凸轮轴心
s
A
为圆心,以其最小轮廓向 径为半径所作的圆,称为 凸轮的基圆半径。 凸轮转角δ :以导路 为参考轴进行测量
B C
r0
从动件位移S :从最低
位置开始测量
e
凸轮的基圆
D
偏距:从动件导路中心
相对轴心偏置的距离
该位置为最低位置
从动件的运动设计的方法
由于凸轮一般以转速ω 作匀速转动,所以凸轮的 转角δ 与转动时间t成线性关系(δ =ω t)。因此, 通常将从动件的运动规律表示成凸轮转角δ 的函数。 三个线图之间的几何关系为:
s s( ) ds ds d ' v s ( ) dt d dt dv dv d a 2 s '' ( ) dt d dt
从动件常用运动规律的比较和选用
一般以机构中的冲击情况、从动件的最大速度和最 大加速度三个方面对各种运动规律特性进行比较。
运动规律 五次多项式 等速 等加速等减速 余弦加速度 正弦加速度 冲击特性 无 刚性 柔性 柔性 无
amax vmax 2 2 (h / 0 ) (h / 0) 适用场合
讨论:B1点与B点的关系?
矢量旋转方程(绕坐标原点) e xB1 B1点 OB1 y r 2 e 2 s ( ), B1 0 B点
xB OB yB
xB cos y sin B
求解:凸轮轮廓曲线上点的坐标值或作出凸轮的轮廓曲线
y
B1
B0
-δ
(1)取定xoy坐标,x或y轴在O1O2 线上,且使初始位置在第一象限; L
0
ro
B
O2
x
O1
位
微 分
移
度 积
分
速
加速度
以凸轮轮廓最小向径r0为半径、凸轮轴心为圆心 所作的圆称为基圆,r0称为基圆半径 推程 行程或升程(h) 推程运动角Ф 0 远休止状态 远休止角Ф s 回程 回程运动角Ф 0’ 动画演示 近休止状态 近休止角Ф s’
从动件的推程,A → B; B →C; 概念:从动件的远休止过程, 从动件的回程,C → D; 凸轮机构完成 近休止状态,D → A 。 s
6.1 凸轮机构的组成及其应用
凸轮机构的组成:
凸轮机构主要由凸轮、从 动件和机架组成。
从动件2
机架3
凸轮---是一个具有
曲线轮廓的构件,一般 作主动件,且为匀速运动
1 A1
从动件-----作往复直
线运动或摆动
凸轮机构的原理
动画演示
实例:专用车床的凸轮控制机构
该机构是加工水表零件的专用自动车床上的凸轮控制
δ
等加速等减速运动规律 amax=(h2/δ02)×4.00 a
0.5 0.125 0.875
正弦加速度运动规律 amax=(h2/δ02)×6.28
δ0 =1 修正梯形组合运动规律
组合等加速等减速 运动规律和正弦加 速度运动规律
2.改进型等速运动规律——消除刚性冲击
s
δ1 v
δ0
δ2
δ
δ a δ
一个运动循环
B
C
行程 h s
A
近休止角
D
2
S
A
B C
r0
0
S
0
e
15:51:53
推程运动角
远休止角
回程运动角
D
多项式运动规律探讨
从动件推程的运动规律 为多项式运动规律,其 位移的一般表达式为:
S C0 C1 C2 2 ..... Cn n
待定系数C0,C1,…,Cn可利用从动件在某些位置的位 移、速度和加速度等边界条件来确定。
6.3凸轮轮廓曲线的设计`
如果已经根据工作要求和结构条件选定 了凸轮机构的型式、基本尺寸,推杆的运 动规律和凸轮的转向,就可进行凸轮轮廓 曲线的设计了 凸轮轮廓曲线设计的方法有作图法和解 析法
6.3.1凸轮廓线设计方法的基本原理
无论是采用作图法还是解 析法设计凸轮轮廓曲线,所 依据的基本原理都是反转法 原理 在设计凸轮廓线时,可假 设凸轮静止不动,而使推杆 相对于凸轮作反转运动;同 时又在其导轨内作预期运动, 作出推杆在这种复合运动中 的一系列位置,则其尖顶的 轨迹就是所要求的凸轮廓线。 这就是凸轮廓线设计方法的
B1
-δ
r0 O
B0
(2)写出点B1的坐标;
B
xB1, yB1
x
T
e, (s0 s)
T
e
s0 r e 2
2 0
注意:δ逆时针为正。
(3)写出平面旋转矩阵
R ;
sin cos
-
cos( ) sin( ) cos R sin( ) cos( ) sin
动画演示 偏置直动
动画演示 偏置直动
对于直动滚子推杆盘形凸轮机构,在设计凸轮廓线时,可首先将滚子中 心视为尖顶推杆的尖顶,按前述方法定出滚子中心在推杆复合运动中的轨 迹(称为凸轮的理论廓线),然后以理论廓线上一系列点为圆心,以滚子半 径rr为半径作一系列的圆,再作此圆族的包络线,即为凸轮的工作廓线(又 称实际廓线)。值得注意,凸轮的基圆半径系指理论廓线的最小半径
在起点、中点和终点时,因加速度有突变而引起推杆惯 性力的突变,且突变为有限值,在凸轮机构中由此会引 起柔性冲击。
余 弦 加 速 度 运 动 规 律
推程:
s h [1 cos( )] 2 0
回程:
h s [1 cos( )] 2 0'
正 推程: 弦 1 2 s h [( ) sin( )] 加 0 2 0 速 度 回程: 运 1 2 动 s h[1 ( ) sin( )] 规 0' 2 0' 律
对于直动平底推杆盘形凸 轮机构,在设计这种凸轮廓 线时,可将推杆导路中心线 与推杆平底的交点视为尖顶 推杆的尖顶,按前述作图步 骤确定出交点在推杆复合运 动中依次占据的各位置。然 后再过这些点作一系列代表 推杆平底的直线,此直线族 的包络线,即为凸轮的工作 廓线
动画演示
6.4 凸轮的轮廓曲线设计
等 加 速 等 减 速 运 动 规 律
推程:
2h 2 s (等加速段0 2) 2 0 0 2h s h 2 ( 0 ) 2 (等减速段 2 ) 0 0 0
回程:
2h 2 s h (等加速段0 2) 0' 0' 2h 2 s 2 ( 0' )(等减速段 2 ) 0' 0' 0 '
凸轮轮廓曲线的设计的主要内容是建立凸轮轮 廓曲线的参数方程。 基本术语回顾:
基圆 r0 :以凸轮最小半径所
作的圆,称为凸轮的基圆半径。
凸轮转角δ :以导路为参
考轴进行测量。
置开始测量。
s
A
从动件位移S :从最低位
r0
B C
e
D
凸轮轮廓曲线的参数方程:得到凸轮轮廓的参数方程 关键是确定凸轮轮廓上的任意点B的坐标 x B、 与凸轮 yB 转角δ 之间的关系。 讨论: δ与B点之间的关系?
原理演示
反转法原理
6.3.2用作图法设计凸轮廓线
在设计凸轮的轮廓时,需先取适当 的比例尺μ 1,根据已知的基圆半径 r0和偏距e 作出基圆和偏距圆,然 后才能运用上述反转法进行作图。 其作图方法及步骤: 1.确定推杆在反转运动中占据的各 个位置; 2.计算推杆在反转运动中的预期位 移; 3.确定推杆在复合运动中依次占据 的位置; 4.将推杆尖点各位置点连成一光滑 曲线,即为凸轮轮廓曲线
a [60( h 2
(2) 凸轮机构设计关键: ① 确定从动件的位移、速度和加速度三者之一 与凸轮转角之间的函数关系; ② 确定相应的边界条件。
其它几种常用的从动件的运动规律
等 速 运 动 规 律
h 推程:s 0 回程:s h(1 ) 0'
在起始和终止点速度有突变,使瞬时加速度趋于无 穷大,从而产生无穷大惯性力,引起刚性冲击。
得五次多项式运动规律的表达式为:
3 4 5 S h[10( ) 15( ) 6( ) ] 0 0 0 h v [30( ) 2 60( ) 3 30( ) 4 ] 0 0 0 0 2 3 ) 180 ( ) 120 ( ) ] 2 0 0 0 0 讨论:(1) 六个边界条件: δ =0 时,S=0,v=0,a=0, δ =δ0时,S=h,v=0,a=0
将矢量沿与凸轮转动方向相反的方向转动
一个对应凸轮的转角,得到新矢量,并利用 平面矢量旋转矩阵得到新矢量的表达式,此 式便为凸轮的廓线方程。
例1:尖顶移动从动件盘型凸轮机构
已知:的转向,ro, e,s=s(δ ) 求解:凸轮轮廓曲线上点的坐标值或作出凸轮的轮廓曲线
- y (1)取定xoy坐标,x或y轴平 行于导路线,且使初始位置在 一象限;