MSA测量系统分析控制程序
测量系统分析(MSA)控制程序

(5)如果操作者在不同的班次,可以使用一个替换的方法。让操作者A测量10个零件,并将读数记录在第一行。然后,让操作者A按照不同的顺序重新测量,并把结果记录在第2行和第3行。操作者B和C也同样做。
(9) 将4,9和14行的平均值(指XaXbXc)中最大和最小值填入第18行中适当的空格处。并确定它们的差值,将差值填入第18行标有XDIEF处的空格内(表1)。
(10) 将每个零件每次测量值相加并除以总的测量次数(试验次数乘以操作者数)。将结果填入第16行零件均值Xp的栏中(表1);
(11) 用最大的零件平均值减去最小的零件平均值,将结果填入第16行标有Rp的空格内。Rp是零件平均值的极差(表1);
(7)将行(第1、2、3、6、7、8、11、12、和13行)中的值相加。把每行得到和除以零件数并将结果填入表1中最右边标有“平均值”的列内。
(8) 将第4、9和14行的平均值(排在最后一列)相加除以试验次数,结果填入第4行的Xa格内。对第6、7和8;第11、12和13行重复这个过程,将结果分别填入第9和第14行的Xb,Xc格内(表1)
6.3表3量具研究表(典型极差法)
6.4表4计数型测量系统分析法(小样法)。
4.3.2收集数据后的计算
量具的重复性和再现性的计算如附表1和2所示。表1是数据表格,记录了所有研究结果。表2是报告表格,记录了所有识别信息和按规定公式进行的所有计算。
收集数据后的计算程序如下:
(1)从第1、2、3行中的最大值减去它们中的最小值,把结果记入第5行。在第6、7和第8行,11、12、13行重复第一步骤,并将结果记录在第10行和15行(表1)。
测量系统分析(MSA)控制程序

测量系统分析(MSA)控制程序页次第 3 页共 6 页5.1.2 测量系统分析时机当出现以下情况时,应进行测量系统分析:5.1.2.1新生产之产品PV有不同时;5.1.2.2新仪器,EV有不同时;5.1.2.3 新操作人员,AV有不同时;5.1.2.4易损耗之仪器必须注意其分析频率。
5.1.3 计量型量具的分辨力应用10:1原则检查侧量仪器是否具有足够的分辨力。
所谓10:1原则是指仪器的可视分辨力至少应为被侧特性公差和过程变差两者之间较小者的十分之一。
5.2 可用于GRR分析的方法5.2.1 极差法:简单快捷,能提供整体大概慨况。
5.2.2 均值极差法:将测量系统变差分“重复性”和“再现性”,而不是它们的交互作用.(控制图略)。
5.2.3 方差法(ANOVE):详细将变差细分到4个部分“零件”“人员”“设备”“零件与人员的交互作用”。
计算要求高复杂.“均值极差法”和“方差法”常用Excel表格和MiniTab分析。
5.3 计量型GR&R的制作过程5.3.1 随机挑选10个覆盖全制程服从正态分布的样品(计数型选样尽可能在允收和拒收边缘,且数量相当)。
5.3.2 确定需要的量测设备并保证此设备校验合格且精度满足公差,及操作者3人或2人(培训合格能够胜任测量过程) 。
5.3.3 主导者将样品编号,并不能告知执行者样品的顺序。
5.3.4 由资深员工确定测量方式及方法或判定标准。
5.3.5 3个或2个操作者轮流测量3/2次.(第1位执行一遍换第2位.....如此循环3/2次) 。
5.3.6 将测量好的数据对应产品编号登记在计量型GR&R运算表中(可以利用客户指定表格或Minitab),以便分析计量型的值(如:图1图2)。
3个人检测员量测三次10PCS需量测的检具图1测量系统分析(MSA)控制程序页次第 4 页共 6 页5.4 计量型GR&R判定标准(具体范围可以依据客户要求)(如:图3)GRR≤10% 量测系统稳定10%<GRR≤20% 量测系统可接受20%<GRR≤30% 量测系统可接受,可不接受。
测量系统分析MSA程序(含表格)
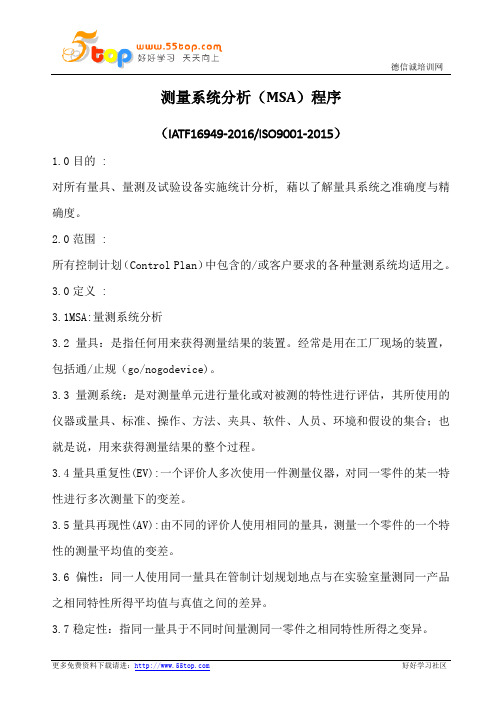
测量系统分析(MSA)程序(IATF16949-2016/ISO9001-2015)1.0目的 :对所有量具、量测及试验设备实施统计分析, 藉以了解量具系统之准确度与精确度。
2.0范围 :所有控制计划(Control Plan)中包含的/或客户要求的各种量测系统均适用之。
3.0定义 :3.1MSA:量测系统分析3.2量具:是指任何用来获得测量结果的装置。
经常是用在工厂现场的装置,包括通/止规(go/nogodevice)。
3.3量测系统:是对测量单元进行量化或对被测的特性进行评估,其所使用的仪器或量具、标准、操作、方法、夹具、软件、人员、环境和假设的集合;也就是说,用来获得测量结果的整个过程。
3.4量具重复性(EV):一个评价人多次使用一件测量仪器,对同一零件的某一特性进行多次测量下的变差。
3.5量具再现性(AV):由不同的评价人使用相同的量具,测量一个零件的一个特性的测量平均值的变差。
3.6偏性:同一人使用同一量具在管制计划规划地点与在实验室量测同一产品之相同特性所得平均值与真值之间的差异。
3.7稳定性:指同一量具于不同时间量测同一零件之相同特性所得之变异。
3.8线性:指量具在预期内之偏性表现。
4.0权责:4.1量测系统测试的排定、数据分析、仪器操作人员的选择:品保部4.2测试执行:各相关单位4.3MSA操作人员的培训:品保部5.0执行方法5.1QA工程师人员依公司PCP文件建立《xx年MSA实施计划表》或客户要求,并依据计划表之排程进行对仪器做量测系统分析。
5.2取样方法:5.2.1计量型取样:从代表整个工作范围的过程中随机抽取10件样品,但所抽取的10件样品其数值必须涵盖该产品的公差带。
5.2.2计数型取样:取50PCS样品,其中包含临近值,不良品与合格品。
5.2.3.需要2或3个测量者随机抽取对每个产品各测量取一定数量样品.5.3计数型:5.3.1被评价的零件的选定随机抽取50个零件,把零件编号,由研究小组给出该50个零件的标准,必须含合格,不合格,模糊品,条件允许的情况下最好各占1/3。
测量系统分析(MSA)管理程序

测量系统分析(MSA)管理程序该计划包括测量系统的分析方法、分析人员、产品抽样编号、测量设备校准过程以及措施效果验证等内容,以确保测量系统的准确性和可信度。
5.2 确定分析方法: 确定适合本公司的分析方法,例如重复性和再现性分析、稳定性分析、线性分析和小样法分析等。
5.3 确定测量者: 确定具有测量能力的人员进行测量分析,以确保测量结果的准确性和可信度。
5.4 测量设备校准过程: 对测量设备进行校准,以确保其测量准确性和可靠性。
5.5 措施效果验证: 对采取的措施进行效果验证,以确保其有效性并纠正任何不足之处。
6、控制流程:本程序的控制流程如下图所示,包括MSA计划、测量系统分析、纠正和预防措施等环节,以确保测量系统处于受控状态,保证测量结果的准确性和可信度。
每年12月,需要编制下一年度的MSA计划,对控制计划中涉及的测量系统进行至少一次分析,且分析间隔不大于12个月。
此外,在以下情况下也需要制定MSA计划:初装的测量设备在安装、调试、验收合格后;测量装置维修或搬迁;操作人员变动;每天使用频率高于7小时;产品出现大批不合格;过程能力Cpk<1.33;GRR在10-30%之间;以及顾客的要求。
在实施计划时,需要确定分析方法。
对于计量型量具,应该使用量具重复性和再现性(GRR)研究分析方法;对于需要监控过程参数的量具,应使用稳定性分析方法;对于计数型量具,应使用小样法。
在需要时,也可以对测量系统进行偏倚、线性分析。
确定测量者时,应从日常操作人员中选择,并规定测量人数m及测量次数t。
对于计量型量具,GRR时m=2-3,t=2-3;稳定性时m=1,t=5(定期);线性时m=1,t≥10.对于计数型量具,m=2,t=2.确定样件时,应从同一批产品的不同班次中选取。
对于计量型量具,GRR时n=10;稳定性时n=1;线性时n≥5(样件的被测量值需包含量具的测量范围);对于计数型量具,n=20(必须包含不合格品)。
测量系统分析MSA控制程序
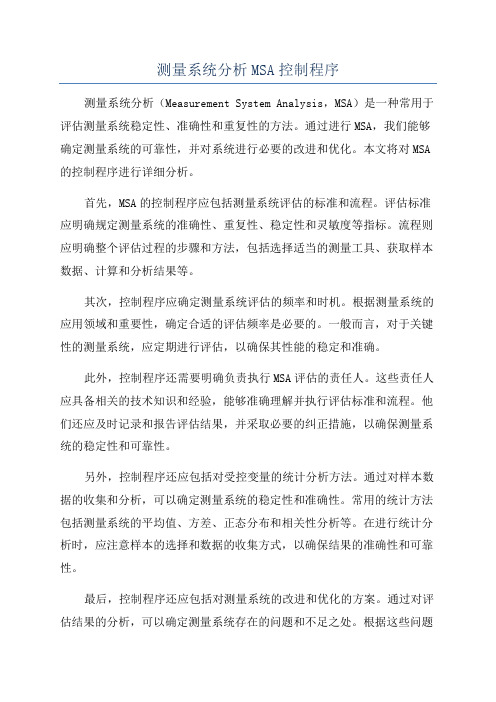
测量系统分析MSA控制程序测量系统分析(Measurement System Analysis,MSA)是一种常用于评估测量系统稳定性、准确性和重复性的方法。
通过进行MSA,我们能够确定测量系统的可靠性,并对系统进行必要的改进和优化。
本文将对MSA 的控制程序进行详细分析。
首先,MSA的控制程序应包括测量系统评估的标准和流程。
评估标准应明确规定测量系统的准确性、重复性、稳定性和灵敏度等指标。
流程则应明确整个评估过程的步骤和方法,包括选择适当的测量工具、获取样本数据、计算和分析结果等。
其次,控制程序应确定测量系统评估的频率和时机。
根据测量系统的应用领域和重要性,确定合适的评估频率是必要的。
一般而言,对于关键性的测量系统,应定期进行评估,以确保其性能的稳定和准确。
此外,控制程序还需要明确负责执行MSA评估的责任人。
这些责任人应具备相关的技术知识和经验,能够准确理解并执行评估标准和流程。
他们还应及时记录和报告评估结果,并采取必要的纠正措施,以确保测量系统的稳定性和可靠性。
另外,控制程序还应包括对受控变量的统计分析方法。
通过对样本数据的收集和分析,可以确定测量系统的稳定性和准确性。
常用的统计方法包括测量系统的平均值、方差、正态分布和相关性分析等。
在进行统计分析时,应注意样本的选择和数据的收集方式,以确保结果的准确性和可靠性。
最后,控制程序还应包括对测量系统的改进和优化的方案。
通过对评估结果的分析,可以确定测量系统存在的问题和不足之处。
根据这些问题和不足,可以采取相应的改进措施,比如调整测量仪器的校准和维护计划、优化测量工艺等。
改进和优化方案应具体、可行,并能够有效地提升测量系统的性能。
综上所述,测量系统分析(MSA)的控制程序应包括评估标准和流程、评估的频率和时机、执行MSA评估的责任人、对受控变量的统计分析方法以及改进和优化的方案。
通过严格执行这些控制程序,可以确保测量系统的稳定性、准确性和可靠性,从而提高产品和过程的质量。
TS16949程序文件:MSA控制程序完整版
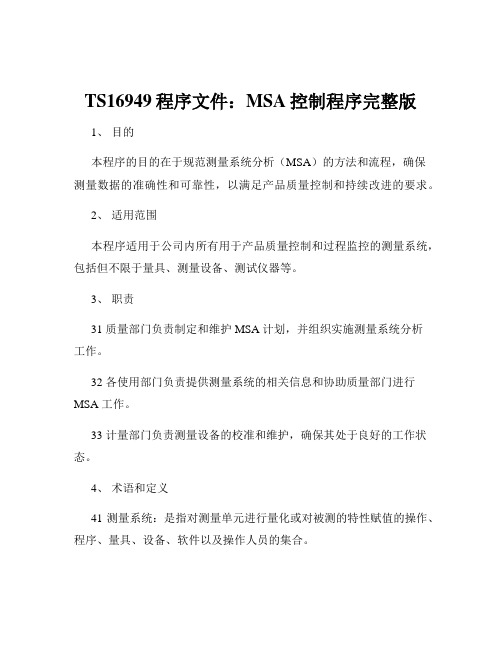
TS16949程序文件:MSA控制程序完整版1、目的本程序的目的在于规范测量系统分析(MSA)的方法和流程,确保测量数据的准确性和可靠性,以满足产品质量控制和持续改进的要求。
2、适用范围本程序适用于公司内所有用于产品质量控制和过程监控的测量系统,包括但不限于量具、测量设备、测试仪器等。
3、职责31 质量部门负责制定和维护 MSA 计划,并组织实施测量系统分析工作。
32 各使用部门负责提供测量系统的相关信息和协助质量部门进行MSA 工作。
33 计量部门负责测量设备的校准和维护,确保其处于良好的工作状态。
4、术语和定义41 测量系统:是指对测量单元进行量化或对被测的特性赋值的操作、程序、量具、设备、软件以及操作人员的集合。
42 重复性:是指由同一个评价人,采用同一种测量仪器,多次测量同一零件的同一特性时获得的测量值变差。
43 再现性:是指由不同的评价人,采用相同的测量仪器,测量同一零件的同一特性时测量平均值的变差。
44 稳定性:是指测量系统在某持续时间内测量同一基准或零件的单一特性时获得的测量值总变差。
45 线性:是指在量具预期的工作范围内,偏倚值的差值。
5、测量系统分析的时机51 新购入的测量设备在投入使用前。
52 测量设备经过维修、校准后。
53 产品的测量特性发生变更时。
54 顾客有特殊要求时。
6、测量系统分析的准备工作61 确定需要进行分析的测量系统和测量特性。
62 选择适当的测量方法和样本数量。
63 准备所需的测量设备和样本零件,并确保其处于良好的状态。
7、测量系统分析的方法71 计量型测量系统分析重复性和再现性分析(GR&R)稳定性分析线性分析72 计数型测量系统分析小样法大样法8、重复性和再现性分析(GR&R)81 选取 10 个代表过程变异的样本零件。
82 选择 3 名测量人员,每名测量人员对每个零件测量 3 次。
83 将测量数据记录在数据表格中。
84 计算重复性和再现性的变差。
MSA测量系统分析控制程序
MSA测量系统分析控制程序文件编号:版本号:AO发布日期:2023-03-11审批:编制:1.目的对测量系统变差进行分析评估,以确定测量系统是否满足规定要求,确保测量系统满足测量要求,确保产品质量。
2.范围本程序适用于本公司所要求的或顾客要求的所有测量设备的测量系统分析。
3.定义3.1MSA:指MeaSUrementSystemsAna1ySiS(测量系统分析)的英文简称。
3.2测量系统:指用来对被测特性赋值的操作、程序、量具、设备、软件以及操作人员的集合;用来获得测量结果的整个过程。
3.3偏倚(准确度):指测量结果的观测平均值与基准值的差值。
一个基准值可通过采用更高级别的测量设备(如:计量实验室或全尺寸检验设备)进行多次测量,取其平均值来确定。
3.4重复性:指由一个评价人,采用一种测量仪器,多次测量同一零件的同一特性时获得的测量值变差。
3.5再现性:指由不同的评价人,采用相同的测量仪器,测量同一零件的同一特性时测量平均值的变差。
3.6稳定性:指测量系统在某持续时间内测量同一基准或零件的单一性时获得的测量值总变差。
3.7线性:指在量具预期的工作范围内,偏倚值的差值。
3.8盲测:指测量系统分析人员将评价的5—10个零件予以编号,然后要求评价人A用测量仪器将这些已编号的5—10个零件第一次进行依此测量(注意:每个零件的编号不能让评价人知道和看到),同时测量系统分析人员将评价人A第一次所测量的数据和结果记录于相关测量系统分析表中,当评价人A第一次将5—10个零件均测量完后,由测量系统分析人员将评价人A已测量完的5-10个零件重新混合然后要求评价人A用第一次测量过的测量仪器对这些已编号的5-10个零件第二次进行依此测量,同时测量系统分析人员将评价人A第二次所测量的数据和结果记录于相关测量系统分析表中,第三次盲测以此类推。
3.9AN0VA:方差分析法3.10计量型数据:定量的数据,可用测量值来分析。
3.11计数型数据:可以用来记录和分析的定性数据。
IATF-I6949MSA测量系统分析控制程序
们的差值,将差值填入第18行标有XDiff处的空格内.
6。4。8将每个样品每次测量值相加并除以总的测量次数(测试次数乘检测人数)将结果填入第16行零件平均值的栏中.
6。4。9从最大的样品平均值减去最小的样品平均值将结果填入第16行标有RP的空格内(Rp是样品平均值的极差)。
1。0目的
更好地了解变差的来源,确保使用场合的测量系统具备适宜的分辨和测量能力,使本公司测量系统评定的方法以及运作步骤和说明有所遵循。
2。0范围
本公司内凡校正合格或出现在产品控制计划中的测量系统。
3。0定义
3。1量具:任何用来获得结果的装置,包括用测量合格/不合格的装置。
3。2分辨力:测量系统检出并如实指示被测特征中极小变化的能力。
6。3。3准备所需的测量量具(此量具须已经过校正为OK)
6。3。4让检测人A以随机的顺序测量10个零件,并让另一观测人将结果记录在第1行,让检测人B和C测量这10个零件并互相不看对方的数据然后将结果分别填入第6、 11行.使用不同的随机测量顺序重复上述操作过程。把数据填入第2、7、12行,在适当的列记录数据.如:第一个测量的零件是7号,则将结果记录在标有第7号的列内,如果需要测试3次重复上述操作时分别记录在第3、8、13行.
7.0相关文件
《监视和测量装置控制程序》
《测量系统分析》手册
8.0表单记录
《量具重复性和再现性数据表》
《量具重复性和再现性报告》
《重复性极差控制图》
《MSA计数型数据小样分析法》
分发栏
■ 1。 品管部 ■2。 生产工程部 ■3. 人事行政部 ■4.市场部 ■ 5.资财部
MSA控制程序
5.3.5样品的选择对正确的分析至关重要,它完全取决于MSA研究的设计、测量系统的目的以及能否获得代表生产过程的样品。由于每个零件将被测量若干次,必须对每个零件编号以便识别。
5.3.6仪器的分辨力应允许至少直接读取特性公差的十分之一。
3.7精密度:指多次重复测定同一个量时,各量值之间彼此相符合的程度,它表征测量过程中随机误差的大小,用标准差来表示特性中微小变化的能力。
3.8分辨力:是指测量系统检出并如实指示测量特性中微小变化的能力,也称分辨率或可读性。
3.9线性(Linearity):是指在量具预期的工作范围内偏倚值的差值。它表明多个独立的偏倚误差在量具工作量程内的关系。
3.13稳定性(Stability):是指测量系统在某持续时间(即不时间),测定同一基准或零件的单一特性时,获得的测量值总变差,即随时间变化的偏倚值。(如图)
四、职责
4.1品保部长:督导测量系统分析(MSA)之实施;
4.2 品质工程组:依据MSA分析计划实施MSA,对测量系统能力进行评估分析。
五、工作程序
5.5.1.1从制造过程中选取一样本,建立相对于可追溯标准的基准值,如果该样本不可获得,选择一个落在产品测量中程数的样本,在实验室或全尺寸检验设备上对此样本进行精密测量10次,并计算此10次平均值,作为“基准值”,填入“偏倚(Bias)分析表”。
5.3测量系统分析(MSA)的准备
5.3.1实施测量系统分析之前应先进行充分的策划和准备。
5.3.2先计划将要使用的方法。
5.3.3评价人的数量、样品数量及重复读数次数应预先确定。选择中应考虑如下因素:
A.尺寸的关键性----关键尺寸需要更多的零件和(或)试验。
MSA测量系统分析控制程序
一、目的:为了确定一个测量系统(对每个零件能重复读数的)是否持续具有恰当的统计特性,了解变差的来源,以提供适当的测量过程,并获得好的测量质量;二、范围:适用于公司产品控制计划(CP)中所涉及到的所有测量系统;三、定义:3.1 测量系统:用来对被测特性赋值的操作、程序、仪器、设备、软件及操作人员的集合,用来获得测量结果的整个过程;3.2 重复性(Repeatability):是指用同一仪器、同一作业者、多次测量同一零件的同一特性时,所得的测量值变差;3.3 再现性(Reproducibility):是指不同作业者以相同仪器测量同一零件的同一特性时,所得的测量值变差;3.4 %R&R:重复性和再现性变差占总过程变差的百分率;3.5 %EV:重复性或设备变差占总过程变差的百分率;3.6 %AV再现性或评价人变差的百分率四、职责:4.1 品质部检验员负责测量系统(MSA)检测数据收集;4.2 品质部工程师负责测量系统(MSA)数据的分析;4.3 品质部经理负责测量系统(MSA)数据的确认;4.4 各部门负责MSA测量系统分析相关工作的支持;五、工作内容:5.1 测量系统分析时机:5.1.1 首次使用时;5.1.2 试生产时;5.1.3 测量系统发生变更时;5.1.4 仪器校正后;5.1.5 客户要求时;注:控制计划(CP)中所涉及到的测量系统都应进行分析;5.2 计量型测量系统的重复性与再现性分析:5.2.1 从过程中选取代表其整个工作范围的产品10个,由责任人员对测量的产品进行编号,选择3名测量者,并采用盲测;5.2.2 由测量者对此选定的产品依次测量2~3次,并由责任人员将测量数据记录在 《GAGE R & R 分析报告》中,注意不要让测量者知道上次测量结果;5.2.3 责任人员将 《量具重复性及再现性数据表》中有关数值计算出R, Xdiff及 RP 值并填写在《量具重复性及再现性报告》中;5.2.4 测量仪器重复性和再现性接受标准(以%EV,%AV,%R&R的数值来判定):5.2.4.1 %R&R值<10%时,测量系统可接受.5.2.4.2 10%≦%R&R值≦30%时──选择性接受,在以下三种情况下可接受:a.量具本身很重要.b.量具很贵重.c.量具维修难,费用高.5.2.4.3 %R&R值>30%时,测量系统不能接受,应采取相应措施.5.2.4.4 当重复性>再现性时,可能是如下情况:a. 测量仪器需进行维护保养.b. 测量仪器要更新或重新设计来提高精密度.c. 夹紧和检测点需要改进.d. 存在过大的零件内变差.5.2.4.5 当再现性>重复性时,可能是如下情况:a. 对测量者需要进行更好的培训如何使用仪器和读数.b. 量具刻度盘上的刻度不清楚.c. 需要某种夹具帮助测量者提高使用量具的一致性.5.3 计数型量具的分析(风险分析法):5.3.1 计数型量具就是把各个零件与某些指定限值相比较,如果满足限值则接受该零件,否则拒收.5.3.2 分析方法:5.3.2.1 选取50个样品,20个样品中应包括一些稍许低于或高于规范限值(限度样品);5.3.2.2 由三位评价人以一种能防止评价人偏倚的方式三次测量所有零件;5.3.2.3 分别计算出各评价人的有效性、漏发警报比率、误发警报比率;5.3.3结果:六、相关文件/表单:A:相关文件a:APQP产品质量先期策划控制程序 EN-02B:相关记录a:测量系统GR&R分析 FM-QA-020评价人不可接受的条件需要改进< 80%> 5%> 10%评价人可接受的条件可能需要改进≧ 80%≦ 5%≦10%评价人可接受的条件≧ 90%≦ 2%≦ 5%判断 测量系统有效性漏发警报比率误发警报比率。
- 1、下载文档前请自行甄别文档内容的完整性,平台不提供额外的编辑、内容补充、找答案等附加服务。
- 2、"仅部分预览"的文档,不可在线预览部分如存在完整性等问题,可反馈申请退款(可完整预览的文档不适用该条件!)。
- 3、如文档侵犯您的权益,请联系客服反馈,我们会尽快为您处理(人工客服工作时间:9:00-18:30)。
广州日信电气有限公司《MSA测量系统分析控制程序》
质量管理体系
QMS
质量管理体系
质量管理体系
QMS
制作王小国
质量管理体系
QMS
发布日期 2020-03-27 版本号 A/0 修订日期 修订人
页码
5/10 制作
王小国
审核
批准
公式中,
取决于是子组大小(m)和在控制图中子组数量(g)。
e )确定对偏倚的统计 t 值 σ b = σ r /√mg t =偏倚/σ b
f )如果 0 落在偏倚值附近的 1-a 置信区间内,则偏倚在这 a 水平内可接受。
这里 d2 , 和 v 可以在MSA 手册附录C 中查到,
在标准 t 表中查到。
所使用的 a 水准取决于敏感度水准,敏感度水准对评价/控制一过程是必要的,并且与产品/ 过程的损失函数(敏感度曲线)有关。
如果 a 值置信度水准不是使用 预设值 0.05(95%置信度),则应该得到顾客的同意。
g) 如果偏倚在统计上不等于 0,检查是否存在以下原因: 1)基准件或参考值有误,检查确定标准件的程序
2)仪器磨损。
这问题会在稳定性分析中呈现出来,建议进行维护或重新修正计划 3)仪器产生错误的尺寸 4)仪器所测量特性有误
5)仪器没有经过适当的校准,对校准程序进行评审 6)评价者使用仪器的方法不正确,对测量指导书进行评审. 7)仪器纠正的指令错误
如果测量系统偏倚不等于零.若有可能,应该采用硬件修正法、软件修正法或同时使用这两种方法来对量具进行重新校准以达到 0 偏倚,如果偏倚不能调整到 0,通过变更程序(如:对每个读值根据偏倚进行修正)还可以继续使用该测量系统。
由于存在评价人误差这一高度风险, 因此这种方法只能在取得顾客同意后方能使用。
h) 分析结果应该完整填写于《计量型器具测量系统分析报告》。
5.5线性的分析过程
a)由于存在过程变差,选择 g ≥ 5 个零件,使这测量值涵盖量具的整个工作量程。
b)对每个零件进行全尺寸检验测量,以确定其参考值,并确涵盖了这量具的工作量程。
广州日信电气有限公司
管理文件
*
2d *
2d
c)让经常使用该量具的操作者测量每个零件
m≥ 10 次。
随机地选择零件,从而减少评价人对测量中偏倚的“记忆”。
d)计算零件每次测量的偏倚,以及每个零件的偏倚均值。
e)在线性图上画出相对于参考值的每个偏倚和偏倚平均值
用下面等式计算和画出最适合的线和该线的置信度区间。
对于最适合的线,用公式:y i = ax i + b
x i = 基准值
y i = 偏倚平均值
这里 x i 是基准值,y i 是偏倚均值,并且
b= y — ax = 截距
对于给定的 x 0 ,a 水平置信度区间为:
f)画出“偏倚=0”线,并对图进行评审,以观察是否存在特殊原因,以及线性是否可接受.(见
例图 11)
如果“偏倚=0”的整个直线都位于置信度区间以内,则称该测量系统的线性是可接受的。
g)如果图示法分析表示该测量系统线性可接受,则下面的假设就成立:
H 0 :a=0 斜率=0
如果下式成立,则不能被否定
广州日信电气有限公司
GUANGZHOU RUSAN ELECTRIC CO.,LTD CHINA
管理文件
文件名称MSA测量系统分析控制程序文件编号Q/RX-
质量管理体系
QMS 发布日期2020-03-27 版本号A/0 修订日期修订人页码7/10
制作王小国审核批准
h) 分析结果应该完整填写于《计量型器具测量系统分析报告》。
5.6稳定性分析过程
a)取一样件并建立其可追溯到相关标准的参考值。
如果该样品无法取得,选择一个落在产品测量中间的生产零件,指定其为基准样件以进行稳定性分析。
追踪测量系统稳定时,不要求该已知的参考值。
这也许会希望拥有位于预期测量结果的下限、上限和中间位置的基准件。
推荐对每种基准件单独的进行测量和画控制图。
b)以一定的周期基础(天、周)测量基准件 3~5 次,抽样数量和频率应该取决于对测量系统的认识。
可能考虑的因素包括重新校准或维修的频率如何、测量系统的频率,以及操作条件的重要性等。
应在不同的
时间下取得多次读值,以代表测量系统的实际使用情况,
这将考虑了在一天之中因为热机、周遭或其它因素可能发生的变化。
c)将数据按时间顺序画在 X&R 或 X&S 控制图上
d)建立控制限,使用控制图分析法来评价是否有不受控或不稳定情况。
除了正常控制图分析法外,没有用于稳定性分析特别数值分析或指数
应该注意,由于使用、材料和搬运的原因可能造成生产基准零件过度磨损。
这将要求对该生产零件进行
某些改变,如电镀,以延长基准零件的寿命。
如果测量过程是稳定的,数据可以用于确定测量系统的偏倚。
e)分析结果应该完整填写于《计量型器具测量系统分析报告》。
5.7重复性和再现性分析过程
5.7.1MSA的前期准备
a)选择评价人
评价人一般选择加工零件的操作工人或检验员,并由评价人对产品进行测量,选择的人数一般为
质量管理体系
QMS
质量管理体系
QMS
制作王小国。