石油钻杆接头耐磨带焊丝对比分析
石油钻杆磨损原因及应对措施

石油钻杆磨损原因及应对措施摘要::分析了石油钻杆工作原理,耐磨带性能影响因素性能特点与影响因素。
分析材料特性是影响耐磨带性能的核心因素,耐磨带特性的改变取决于堆焊材料成分、组织性能的变化以及配套堆焊工艺的严格实施。
关键词:钻杆磨损;耐磨带;性能分析1、耐磨带工作原理钻杆接头耐磨带实质上是一个沿接头圆周方向,具有一定宽度和一定厚度的隔离带。
通过这个隔离带,使钻杆接头外壁和套管壁或井壁隔离,避免钻杆接头与套管壁或井壁直接接触,以保护钻杆接头和套管免遭强烈磨损。
耐磨带的工况条件比较复杂,性能要求比较苛刻,应当具有良好的综合抗磨性能。
所谓综合抗磨性能,是指具有较高耐磨性的同时还必须具有适度的减磨性。
最佳的耐磨性与减磨性之间存在一定的匹配关系,上述技术指标之间以及与摩擦系数之间的函数关系的量化确立,可能对于耐磨带焊接材料性能的重大突破具有重要参考价值。
2、耐磨带性能影响因素接头耐磨带性能影响因素较多,总体上有三大因素:2.1载荷力的影响在钻井过程中,凡是增大钻杆接头与套管内壁(或井壁)接触力的因素,都会加剧磨损发生。
如在“狗腿”度大的井段,接头与套管内壁接触压力相对增大,此时无论是耐磨带还是套管内壁(或井壁),其磨损现象就会加剧。
2.2摩擦系数的影响在钻井过程中,凡是增大接头与套管内壁摩擦系数的因素,都会加剧磨损发生。
如润滑剂品种或加入量不合适、转盘转速增大以及温度过高或过低时,其磨损现象也会加剧。
2.3耐磨带与套管(或井壁)材料特性的影响根据摩擦学中的“吸附膜”理论,对于钻杆钢与岩石形成的摩擦副,两者之间很难形成吸附膜,摩擦系数主要取决于摩擦副材料的表面特性,而摩擦副其表面特性是稳定的,摩擦系数受载荷的影响较小。
对于钻杆与套管钢形成的摩擦副,两者之间比较容易形成吸附膜,当施加正压力时,随吸附膜逐渐被破坏,摩擦副表面特性对摩擦系数形成的贡献越来越大,摩擦系数受载荷的影响较大。
凡是增大摩擦系数的材料特性,都会加剧磨损发生。
钻杆接头喷焊层耐磨带脱落原因及预防措施

41
焊接 生产应用
Production Theme
失碳形成硬脆 W 2 C 相 , 抗疲劳性能下降 , 在磨损过 程 中 , 首先破碎、 剥落, 并使邻近的碳化物由于缺口应 力 集中, 跟着脆断和剥落 , 所以使耐磨性下降。 2. 2 预防措施 钻杆接头耐磨层脱落原因主要在于合金块与基体 金属间存在气孔和裂纹等缺陷。只有通过工艺控制来 减少和避免这种缺陷 , 才能够获得结合度较高、 抗剥落 性能较好的耐磨层。喷焊修复时, 应注意以下几点 : 2. 2. 1 工件预热并保持喷焊粉末干燥 水、 油污及铁 锈等氧化 物存在 , 易形成 气孔和 夹 杂。喷焊前对基体去除水、 油污及铁锈等氧化物, 进行 400 预热并保温。喷焊粉体不进行干燥处理也是气 孔的一个主要来源。喷焊时 , 水分随粉体到达喷焊层 , 重熔时分解为氢气和氧气, 在重熔不完全的情况下 作 为气孔留在喷焊层中。此外 , 合金粉质量差 , 如熔点过 高、 粘度大、 脱氧能力不足等也是气孔产生的主要原因。 2. 2. 2 保证基体表面合适的粗糙度 钻杆接头基体表面具有适度的凹凸不平可以提高 喷焊层与基体金属之间的结合力, 但并不是越粗糙 结
收稿日期 : 2007 - 10- 22
[ 2~ 4]
43
由于钻井技术的不断进步和勘探开发的需要 , 深 井、 超深井、 大斜度井以及水平井大量出现 , 钻柱的摩 擦扭矩和摩擦阻力都显著增大 , 这些 恶劣的工况条件 要求工件表面必须具备较高的耐磨粒磨损性能。钻杆 在使用过程中接头首先磨损, 使钻杆接头强度降低, 从 而导致钻杆先期报废 , 而解决这一问 题的有效手段是 采用接头表面硬化处理达到保护钻杆接头的作用。实 践表明, 表面涂层技术不但能够对失效工件进行修复, 节省材料和能源 , 而且还能大幅度地 提高工件表面的 使用性能 , 是一种简便、 有效的技术手段 。与激光 [ 3~ 5] 熔敷、 等离子喷焊相比 , 氧乙炔火焰喷焊技术具有 成本低、 工艺成熟、 便于操作等优点。但如果火焰喷焊 工艺不当 , 喷焊层会经常出现大量密集的气孔 , 甚至在 合金块边缘产生裂纹。对某公司钻杆耐磨带在钻井过 程中块状脱落的原因进行了分析, 并提出预防措施, 从而 有利于提高耐磨带喷焊层质量, 延长钻杆的使用寿命。 1 耐磨层材料及喷焊工艺 据了解, 工厂喷焊时先在钻杆接 头上喷焊一层镍 基自熔合金粉末 , 之后将 W C 合金块 排放好用氧乙炔 焰重熔镍基粉末, 使 W C 合金块与钻杆基体结合 , 最后 用氧乙炔焰在合金块之间喷焊 N i+ WC 合金粉末。对 耐磨带喷焊层金属取样 , 进行了 X 射线能谱分析 , 结果 见表 1 和表 2 。从表 1 中可以看出 : 喷焊层的合金粉末 是镍基合金粉末, 其中还含有大量的钨 ( W ) 元素。这 种合金粉末是在高硬度镍基自熔合金中加入碳化钨颗 粒而形成的含 碳化钨弥 散型自熔 合金。 由于超 硬度 ( 70HRC 以上 ) 碳化钨颗粒弥散分布在高硬度 ( 50 HRC 以上 ) 自熔合金基体中 , 大大提高了合金的耐磨性、 红
石油钻杆耐磨带磨损原因及耐磨解决方法

石油钻杆耐磨带磨损原因及耐磨解决方法在钻井过程中,钻柱在井眼中与套管内壁发生接触产生摩擦,使得扭矩和摩擦增加,而钻杆接头对套管的磨损影响最大,因为钻杆接头的直径比钻杆本体大20%~30%,很容易与套管内壁接触并磨损套管。
当接触力足够大时,润滑膜的润滑作用完全消失,钻杆接头与套管内壁直接接触产生了干摩擦。
在摩擦过程中,钻杆接头的磨损非常严重,偶然的碰撞就可能使钻杆接头产生断裂;同时,钻杆接头的磨损也使得套管壁厚减薄,抗挤能力随之降低。
若对此估计不足,有可能因此导致钻井事故或油气井的早期报废,给油田造成巨大的损失。
有研究结果表明,钻柱不居中使钻杆接头在钻井施工中与套管内壁相互摩擦是造成套管磨损的主要原因,而钻柱不居中又是钻探过程中不可避免的。
因此,可见如何降低钻杆与套管之间的摩擦接触或摩擦系数是防磨的关键与核心。
钻杆接头耐磨带是以凸起的形式熔合在钻杆接头表面,用以代替钻杆接头来和套管摩擦的材料,对钻杆接头起到了保护作用。
由于耐磨带的硬度低于钻杆本身,因此,对套管起到了一定的保护作用。
而耐磨带在磨损掉一部分之后,可以进行重复堆焊使用。
钻杆耐磨带主要是采用耐磨带焊丝通过CO2气体保护焊的方式堆焊到钻杆接头部位的一种高合金耐磨材料。
目前,国产耐磨带焊丝以北京固本KB150最具代表性。
KB150是北京固本公司第三代产品,是一种高级无裂纹、套管友好耐磨带,继承了KB100和KB300的优点,耐磨带能力介于KB100和KB300之间,摩擦因数低,减摩能力高于KB300和KB100,其焊接简单且焊接过程产生很少的火花和烟尘,且保持一定的韧性可承受在大位移井、深井和水平井的严苛钻井条件下产生的大转矩和高温;能在多种外界环境下补焊,而不会产生裂纹和脱落,同时抗硫化氢腐蚀。
钻杆接头耐磨带材料研究进展
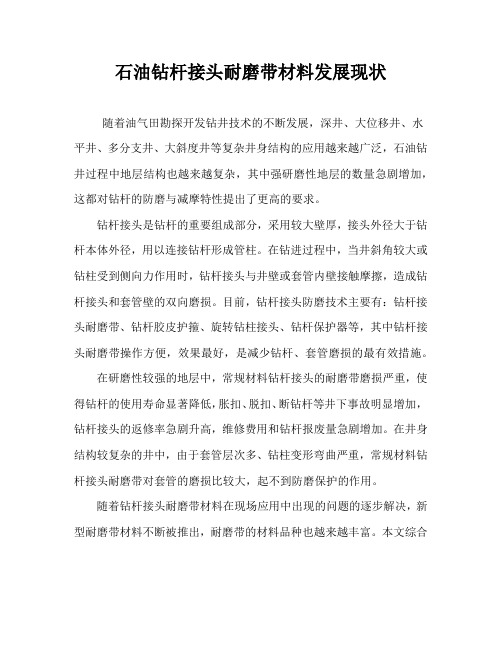
石油钻杆接头耐磨带材料发展现状随着油气田勘探开发钻井技术的不断发展,深井、大位移井、水平井、多分支井、大斜度井等复杂井身结构的应用越来越广泛,石油钻井过程中地层结构也越来越复杂,其中强研磨性地层的数量急剧增加,这都对钻杆的防磨与减摩特性提出了更高的要求。
钻杆接头是钻杆的重要组成部分,采用较大壁厚,接头外径大于钻杆本体外径,用以连接钻杆形成管柱。
在钻进过程中,当井斜角较大或钻柱受到侧向力作用时,钻杆接头与井壁或套管内壁接触摩擦,造成钻杆接头和套管壁的双向磨损。
目前,钻杆接头防磨技术主要有:钻杆接头耐磨带、钻杆胶皮护箍、旋转钻柱接头、钻杆保护器等,其中钻杆接头耐磨带操作方便,效果最好,是减少钻杆、套管磨损的最有效措施。
在研磨性较强的地层中,常规材料钻杆接头的耐磨带磨损严重,使得钻杆的使用寿命显著降低,胀扣、脱扣、断钻杆等井下事故明显增加,钻杆接头的返修率急剧升高,维修费用和钻杆报废量急剧增加。
在井身结构较复杂的井中,由于套管层次多、钻柱变形弯曲严重,常规材料钻杆接头耐磨带对套管的磨损比较大,起不到防磨保护的作用。
随着钻杆接头耐磨带材料在现场应用中出现的问题的逐步解决,新型耐磨带材料不断被推出,耐磨带的材料品种也越来越丰富。
本文综合评述钻杆接头耐磨带材料的发展及其应用,为推动钻杆接头耐磨带技术的进一步完善具有重要意义。
1 钻杆接头耐磨带对材料性能的要求耐磨带是在钻杆接头、钻铤或加重钻杆上固定一层硬化层。
该硬化层将钻杆接头与套管或井壁隔离,具有一定的硬度,可保护钻杆接头。
摩擦因数低于钻杆接头,可减少对套管的磨损。
耐磨带通常采用惰性气体保护焊工艺固定在钻杆母接头末端。
钻杆接头耐磨带早在20世纪30年代就已出现,早期主要用来保护钻杆和其他工具免受磨粒磨损,延长使用寿命。
但是随着大位移井、水平井、高温高压井等复杂井的增加,钻杆接头耐磨带对套管磨损严重,套管失效事故增加,每年给油田造成上百万美元的维修、侧钻甚至全井报废成本。
钻杆接头耐磨带的使用性能及其堆焊材料

度磨 损 , 用 堆焊 方 式 ( 其 他方 法 ) 耐 磨 材料 沿 采 或 将
钻 杆接 头 圆周方 向堆 焊 ( 或熔 敷) 宽约 3 ~ 0mm、 0 5 厚 2 3m 的环形 带 。 - m 此环 形带 即称之为 钻杆接 头耐磨
带 技术 问世 以来 , 着 现场应 用 中 出现 问题 的逐 步 随
力 相 对增 大 , 时 无 论 是 耐 磨 带 还 是套 管 内壁 f 此 或 井壁)其磨损 现象 会加 剧 。 ) , ( 摩擦 系数 的影 响 。 钻 2 在 井过 程 中 , 是增 大 接头 与套 管 内壁 摩擦 系数 的因 凡 素 , 润滑 剂 品种 或加 入 量不 合适 、 盘 转速增 大 , 若 转 以及 温 度过 高 或 过低 时 , 其磨 损 现 象 也会 加 剧 。3 f1 钻杆接头 耐磨带 与套管( 或井 壁) 材料特 性 。 据摩擦 根 学 中的 “ 附膜 ” 论【, 于 钻杆 钢 与岩 石形 成 的 吸 理 l对 】 摩 擦 副 , 者 之 间很 难 形 成 吸 附膜 , 擦 系数 主要 两 摩
取 决于摩 擦 副材 料 的表 面 特性 , 而摩 擦 副其 表 面特
性是 稳定 的 , 摩擦 系数受 载荷 的影 响较小 。 对于钻 杆 与套 管 钢形 成 的摩 擦副 , 者之 间 比较 容易 形成 吸 两
附膜 , 当施加 正压 力பைடு நூலகம்时 , 随着 吸 附膜 逐渐 被破 坏 , 摩
克 服 , 型 耐磨 带 专 用 堆焊 材 料 不 断 被 推 出 , 磨 新 耐 带 的材料 品 种 已经发 生 了质 的变 化 , 耐磨 带 的使 用
带 。 机理上讲 , 从 钻杆接 头耐磨 带 的作 用是利用 自身 及 其 耐 磨性 , 钻 杆 外 壁 和套 管 内壁 隔 离 , 钻 杆 将 使 不 与套 管壁 或井 壁直 接 接触 , 以保 护 钻杆 接 头 和套 管 免遭 强烈 的磨损 。 然而 , 际情况 并 不简单 , 实 耐磨 带 的出现 , 将钻 杆接 头与套管 内壁 的接触摩 擦 , 换 转 为耐 磨带 与套 管 内壁 的接触 摩擦 。 它们 之 间的摩 擦 磨损 , 不仅 取 决于 两个 接 触体 材料 的特性 及其 匹 配 关系 , 同时还受 到钻井过 程中诸 多因素影响。 近年来 , 在多 种可供 选 用 的套管 防磨技 术 之 中 , 操作 方 便 和 效果最好 者首推 接头耐磨 带 。 研究表 明 , 头耐磨带 接 性 能 ( 与 套管 材 料 的 匹配 性 能) 含 的优化 与改 善 , 是 防止套管 强烈磨损 的关键技 术措施 。 事实上 , 自耐磨
加重钻杆耐磨带焊接实例

加重钻杆耐磨带焊接实例(北京固本科技有限公司)随着石油钻探开采的发展,各类加重钻杆在石油钻探开采中的需求越来越大,用户对产品使用性能的要求也越来越高。
如何采取合理的焊接工艺方法,以实现低成本高效率且又能满足产品技术要求的耐磨带焊接研究成为需要解决的课题之一。
某石油公司研发的材料牌号为AISI4145H钢的114.3mm(4.5in)加重钻杆有4段工作面需要增加耐磨带,4段焊缝分别为币φ158.8mmx101mm、φ127mmx76mm、φ127mmx76mm、φ158.8mmx101mm,焊缝需堆焊3mm厚,加重钻杆内孔为币φ71.41mm,钻杆内螺纹接头与钻杆吊卡扣合处制成18°锥形台肩,焊前经过285~341HBW调质处理。
按石油天然气行业颁布的标准SY/5T146-1997规定:堆焊后,耐磨环外表面应平整过渡,基体不得有裂纹和焊层剥落等缺陷,表面硬度不低于50HRC,为使钻杆焊接后性能满足技术要求,需对原材料的焊接工艺、焊接质量进行分析和试验,以便制定合理可行的焊接工艺。
一、焊接性分析钻杆的材料牌号为AISI4145H,其化学成分符合表1的规定。
表1 AISI4145H的化学成分(质量分数)(%)按照国际焊接学会所推荐的碳当量计算公式,可计算出碳当量Ceq为0.725%~1%。
据大量试验得知:当碳当量Ceq大于等于0.60%时,属于高淬透性的钢,冷裂纹倾向较为严重,焊接性较差,这是因为材料中的含碳量较高,加人的合金元素也较多,在500℃以下的温度区间过冷奥氏体具有更大的稳定性所致其含碳量越高,淬硬倾向越大,冷裂纹倾向也越大,而且由于M点较低,在低温下形成的马氏体一般难以产生“自回火”效应,并且马氏体中的含碳量较高,有很大的过饱和度,点阵的畸变就更严重,因而硬度和脆性就更大,对冷裂纹的敏感性也就更大另外,由于原材料的含碳量及合金元素的含量都较高,因此液一固相区间较大,偏析也更严重,这就促使其具有较大的热裂纹倾向。
石油钻杆耐磨带
石油钻杆耐磨带石油钻杆耐磨带摘要:在钻井过程中,套管经常被磨穿,造成严重损失,因此对钻杆接头耐磨带提出了更高要求。
新型钻杆接头D100耐磨带与钢质钻杆接头相比,套管磨损减少86%;与碳化钨耐磨带的接头相比,套管磨损降低76%;在大斜度井中,由于摩擦系数减小,大大降低了钻具旋转阻力,扭矩增大30%,节省材料消耗10%。
关键词:石油钻杆耐磨带敷焊工艺随着钻井技术的不断进步,深井、超深井、丛式井、大斜度井、水平井大量出现,钻柱的摩扭、摩阻显著增大,套管经常磨穿,造成严重的损失。
为减少钻柱的摩扭与摩阻以有效保护套管,钻井工作者采取了多种方法,如在钻杆上加橡胶护箍、采用无耐磨带钻杆、使用非旋转钻杆保护器等。
实践表明,在大位移井中橡胶护箍使用寿命很短,而非旋转钻杆保护器需要在每个单根套管保护段加1个,使用不方便而且价格昂贵,有时还可能造成井下复杂事故。
由于对套管造成磨损的主要是钻杆接头,因此对钻杆接头耐磨带性能的要求越来越高,已不仅局限于保护钻杆接头,更重要的是耐磨带在保护钻杆接头的同时,更有效地保护套管,减少套管磨损。
一、钻杆接头耐磨带现状我国大多数油田使用的钻杆接头耐磨带是采用等离子喷焊工艺加工的,喷焊后,耐磨带硬度约为55HRC。
采用等离子喷焊工艺加工的碳化钨耐磨带在使用过程中与套管的摩擦力较大,无论对套管还是钻杆接头磨损都比较快。
在北海挪威区块的GullfaKsA42号井中使用硬质合金耐磨带的钻杆在井深460m和680m处套管的磨损值达29%。
硬质合金耐磨带与套管的摩擦系数和钢差不多,在CWEAR模型中,钢接头在油基钻井液中摩擦系数为1—5,对光滑的碳化钨耐磨层其摩擦系数为5—25。
计算机模拟表明,碳化钨硬质合金耐磨层的摩擦系数为38,与测井结果相符。
碳化钨耐磨带的钻杆在大位移井中使用对套管的磨损也很大,因此在国际钻井工程招标中和国内较深井都被禁止使用。
目前国外钻杆的耐磨带材料已不使用合金粉末而是采用硬度相当、耐磨性更好的合金焊丝。
石油钻杆耐磨带焊接工艺流程及检验标准
石油钻杆耐磨带焊接工艺流程及检验标准耐磨带焊接过程直接影响耐磨带最终成品的外观和质量,并进一步影响石油钻杆的使用风险和寿命。
研究表明,常见的耐磨带焊接缺陷例如耐磨带表面裂纹、飞溅、气孔等均与是否制定和采用了正确的焊接工艺和焊接标准有高度关联。
作为国产耐磨带焊接材料的领军单位,北京固本科技有限公司公开了该公司为客户提供的耐磨带焊接工艺流程及标准规范。
一、焊接设备的选型焊接设备是整个耐磨带焊接的关键所在,一般来说,焊接设备由3大部分组成,分别是:焊机、钻杆旋转装置、焊枪控制装置。
其中,焊机的选择需要注意以下两个事项。
(1)根据钻具耐磨带和堆焊的特殊性,在设备选择上选用电压为22V~28V、电流为240A~320A的自动气体保护直流焊机。
(2)选用速度可调、送丝结构平稳的焊机,压丝轮紧度可调,要适中。
送丝速度应在6~12m/min范围内。
钻杆旋转装置需要注意以下事项:在夹紧钻具接头装置选择上,选用转速可调,能在焊枪下面正、反旋转钻具接头的装置。
焊枪控制装置需要注意。
(1)夹紧焊枪并可以带动焊枪自由摆动,摆动幅度为15~40mm。
(2)焊枪在上、下、左、右范围内均可大幅度移动。
二、耐磨带焊丝的选型不同型号的耐磨带焊丝具有不同的合金成分,焊接后的表面硬度、焊缝裂纹也有所差异。
根据钻杆的应用场合和设计要求,可自行选择合适的耐磨带焊丝型号。
所有耐磨带焊丝应遵循和符合以下要求:(1)直径为1.2或1.6mm,直径误差不得超过3%;(2)焊丝使用SPCC钢带轧制工艺制成,表面应光滑平整,没有毛刺;(3)焊缝表面没有裂纹。
某些型号耐磨带焊丝允许焊缝表面裂纹存在,但裂纹不得渗透到钻杆基体;(4)随焊丝产品附带材质保证书,无磁型耐磨带焊丝附带磁导率检查报告。
三、焊前准备严格地进行焊前准备工作,可以更好地确保耐磨带焊接工作正常进行,获得最佳的焊接效果。
具体地,焊前准备工作分为下列3点:(1)检查钻杆接头表面,保证表面干净,没有任何杂质,如飞尘、污物、油脂和油漆等。
钻具耐磨带敷焊质量可靠性及技术应用
钻具耐磨带敷焊质量可靠性及技术应用论文关键词:耐磨带钻具铁基合金粉焊丝。
论文摘要:在深井超深井勘探过程中,由于径向力、涡动、横向振动等因素的存在,随着钻井时间的增长,钻柱作用于套管内壁的侧向力增大,导致套管和钻具接头磨损的问题越来越严重。
造成钻具耐磨带失效的主要原因有地层研磨性、钻杆的井下工况、耐磨材料选择与敷焊工艺的影响。
选择合理的耐磨材料与敷焊工艺对解决钻具耐磨带失效问题非常重要。
Keyword :Wearproof girdle 、 Drilling rig 、Unalterable foundation compound metal powder 、Welding wire 。
Abstract :Be living in the deep well ultradeep well prospecting process ,Since radial direction force 、Eddy is stird 、Elements such as horizontal vibration and so on being ,In the wake of well drilling time the increase ,The auger post writings is used the casing inside wall crossrange strenuously to broaden ,It is more and more grave to cause casing and drilling rig to join the wornout problem 。
Create the main reason of wearproof brining failure of drilling rig to possess layer abrasivity 、The drill pipe operational mode under the shaft 、Wearproof stuff selection together with effect applying solderer'sskill 。
石油钻杆接头耐磨带焊接研究
石油钻杆接头耐磨带焊接研究内螺纹接头外圆的一段长度内,再堆焊一层耐磨带使之呈“凸起”状态。
通常,建议在内螺纹接头的外圆上堆焊76mm宽、3mm厚的耐磨带。
于是耐磨带自己形成一个接触面,而不是使钻杆内螺纹接头的全部长度管或裸眼井的内壁表面相接触。
这样就减少了套管和钻杆接头双方的磨损。
例如φ168mm钻杆内螺纹接头外圆上堆焊“口起”状态耐磨带示意1所示。
图1 “凸”状态的耐磨带用这种方法堆焊的耐磨带可以吸收载荷的冲击。
一旦发生了最恶劣的情况,比如说耐磨带被破坏了,那就需要剔除损坏的耐磨带,然后重把整个钻杆从意外的灾难中抢救恢复出来,以便今后继续使用。
钻杆和套管的接触力主要分布在较小的耐磨带区域,而耐磨带的摩擦系数比钻小,当耐磨带与套管的内表面接触吋,由于摩擦系数的减小,同时也降低了钻具在延伸区作业或大角度钻井时产生的较大扭矩和拉力。
这样,拉力的减小又可以减少燃料的消耗。
(2)“平坦”焊接状态的耐磨带只有当钻杆接头的最大外径被限制,以免与套管内径相干涉时,才建议使普通平坦耐磨带的类型。
所谓平焊指耐磨带高度与接头本体直径钻杆接头本体的外径与耐磨带同时都在受到摩擦。
钻杆和套管的接触力或多或少地沿整个钻杆接头的长度方向分布,降低了耐磨带的支撑,同了钻杆接头本体与套管的接触,增大了钻杆接头和套管的磨损。
用这种方法堆焊的任何一种耐磨带,包括KB150,都不能产生最大的耐磨效果对于平坦焊接类型的耐磨带的应用,需要在整个接头的耐磨带区域加工凹槽,然后填充磨带,使之与钻杆接头的外径齐平。
耐磨带区域一18°的吊卡台肩。
例如φ168mm钻杆内螺纹接头外圆上堆焊“平坦”状态耐磨带示意图见图2所示。
图2 “平坦”状态的耐磨带三、钻杆接头表而耐磨带堆焊工艺措施根据钻杆接头化学成分表1和国际焊接学会碳当量公式,求得钻杆接头碳当量Ceq约为0.8%。
表1 AISI4137H钢的化学成分(质量分数,%)对于钻杆接头,分别等离子弧堆焊铁基合金粉末、80%Ar+20%CO2气体保护焊KB150焊丝和98%Ar+2%O2气体保护焊ER70S-2焊丝外加碳化按甘油法,测定的扩散[H]含量约为0.2ml/100g。
- 1、下载文档前请自行甄别文档内容的完整性,平台不提供额外的编辑、内容补充、找答案等附加服务。
- 2、"仅部分预览"的文档,不可在线预览部分如存在完整性等问题,可反馈申请退款(可完整预览的文档不适用该条件!)。
- 3、如文档侵犯您的权益,请联系客服反馈,我们会尽快为您处理(人工客服工作时间:9:00-18:30)。
石油钻杆接头耐磨带焊丝对比分析
石油钻杆接头耐磨带以其一定的耐磨性和减磨性,保护钻杆接头和套管免遭强烈的磨损,钻井工程中获得了广泛的应用。
钻杆耐磨带主要是采用耐磨带焊丝通过二氧化碳气体保护焊的方式堆焊到钻杆接头部位的一种高合金耐磨材料。
目前国内所使用的耐磨带焊丝大部分依赖进口,其中美国某公司的100XT型产品使用最为广泛、最具代表性。
北京固本科技发展有限公司根据钻杆现场施焊特点,结合钻杆耐磨带的磨损情况,研制了一种替代进口耐磨带焊丝的国产钻杆耐磨带焊丝KB100,在提高钻杆接头的耐磨性能的基础上,为油田钻井服务和钻杆生产企业降低生产成本,增加企业效益作出了积极作用。
本文从耐磨带焊丝堆焊层的化学成分、金相硬度、磨粒磨损等多个方面对国产KB150和进口100XT钻杆耐磨带焊丝的性能作了分析与对比。
一、钻杆接头耐磨带焊丝
1、美国安科100XT耐磨带焊丝
100XT耐磨带焊丝是一款金属芯焊丝。
该耐磨带100%无裂纹,并且具有硬、坚韧、高耐磨、套管友好等特性。
100XT耐磨带焊丝是美国安科技术公司自主研制,美国安科位于美国德克萨斯州的休斯顿市,属于美国TRITEN集团,是进行井下钻具保护和防磨研究的一个机构。
2、北京固本KB150耐磨带焊丝
KB150耐磨带焊丝为铁基药芯焊丝,是一种高级无裂纹、套管友好耐磨带。
55以上的洛氏硬度,确保了钻杆接头和套管之间的理想
摩擦和均衡保护。
KB150耐磨带焊丝由北京固本科技有限公司自主研制,公司有近10年的钻杆耐磨带焊丝研制、开发、生产、销售和服务经验。
北京固本是国内唯一一家专业研发耐磨堆焊金属材料的高新技术企业,公司是国家级大学科技园企业,并获政府相关部门专项资助。
二、金相硬度对比
在单层焊的情况下,不同位置上分别测试7个点的硬度,100XT 耐磨带焊丝平均硬度值为55.7HRC,KB150耐磨带焊丝平均硬度值为
61.3HRC。
三、磨粒磨损对比
通过这2种型号耐磨带焊丝磨损量测试结果可知,KB150耐磨带焊丝磨损量明显小于100XT。
在相同载荷下,北京固本KB150耐磨带焊丝堆焊后的耐磨带与美国安科100XT型相比,相对耐磨性提高1.75倍。
四、两种耐磨带实际使用结果
实际应用表明,北京固本KB150耐磨带焊丝堆焊层的耐磨性能明显优于美国安科100XT。