化学镀铜配方分析_分析检
化学镀铜

化学镀铜2008-04-03 11:12在化学镀中,化学镀铜是十分重要的镀种。
随着电子工业的发展,特别是电子计算机,电子通讯设备,以及家用电器的高速发展,双面和多层印刷电路板的需求量很大。
而印刷板的孔金属化,从导电性、可焊性、镀层韧性和经济性等综合要求来说,非铜莫属。
另外其它非金属材料(如塑料、陶瓷等),化学镀铜应用亦很广泛。
今后,非金属材料的金属化方面,化学镀铜应用亦很广泛。
今后,非金属材料的金属化方面,化学镀铜的用量约占90%以上。
化学镀铜液从稳定性划分,可分为低稳定性的化学镀铜和高稳定性的化学镀铜;从沉积速度来分,又可分为低速率和高速率的化学镀铜。
前者沉积速率一般为2~4μm/h;后者一般为10μm/h。
高速率化学镀铜一般用于半加成法或全加成法直接镀厚铜。
工艺上已由高温高速发展为低温高速。
近年来又出现了差示镀铜法,即印制板上通孔壁上的化学铜层厚度约为复铜层上化学铜层厚度的3~5倍,既降低了金属铜的消耗,又降低了成本,称之为化学镀铜发展史上的第四个里程碑。
化学镀铜液一般由铜盐、络合剂、还原剂和稳定剂组成。
一、化海陆空镀铜的工艺规范(见表3-1-9)表3-1-9 化学镀铜的工艺规范二、镀液的配制化学镀铜液均应分成A、B两组镀液分别配制,使用前才混合在一起,最后加入稳定剂,调整pH值。
A组包括硫酸铜和甲醛,可用蒸馏水或去离子水先溶解计算量的硫酸铜,然后加入计算量的甲醛。
B组包括络合剂如EDTA钠盐、酒石酸盐;碱性物如氢氧化钠、碳酸钠。
先用纯水溶解碱性物质,然后加入络合剂。
混合时,在搅拌下将A组徐徐加入B组镀液中,开始可能有氢氧化铜沉淀产生,搅拌中会逐渐溶解,此时铜呈络离子状态存在。
将镀液过滤于生产槽中,稀至总体积,调整pH值,最后加入稳定剂,即可使用。
三、化学镀铜的简单原理化学镀铜的历程可概括如下:自催化反应Cu2++2HCHO+4OH-Cu0+2HCOO-+H2↑+2H2O (1)反应(1)中的阴极反应为Cu2++2e→Cu0阳极反应为2HCHO+4OH-→2HCOO-+H2↑+2H2O+2e-除上述主反应外,还会发生如下副反应2Cu2++HCHO+5OH-→Cu2O↓+HCOO-+3H2O (2)Cu2O+H2O→Cu0↓+Cu2++2OH-(3)反应(2)为化学镀铜液中均相氧化还原反应,所产生的Cu2O在碱性液中还会发生反应(3)的岐化反应而形成铜原子。
实验四--光亮电镀铜

实验四光亮电镀铜一、目的及要求1、熟悉电镀小试的装置和仪器设备。
2、掌握光亮镀铜溶液的配制及预镀工艺。
3、进行赫尔槽试验,分析光亮剂影响。
二、仪器、化学试剂直流电源、电炉、控温仪、赫尔槽及试片、电解铜板;硫酸铜、硫酸、镀铜光亮剂、镀镍溶液、镍阳极。
三、实验步骤1、工艺流程试片准备――酸洗――水洗――除油――水洗――浸蚀――预镀镍――(或铜锡合金)――水洗――酸性亮铜――水洗2、溶液配方及工艺条件预镀镍溶液:硫酸镍: 120~140g/L氯化钠: 7~9 g/L硼酸: 0~40 g/L无水硫酸钠: 50~80 g/L十二烷基硫酸钠: 0.01~0.02 g/LpH: 5.0~6.0温度: 30~50℃电流密度: 0.8~1.5A/dm2酸性亮铜溶液:硫酸铜: 200~220 g/L硫酸(1.84): 60~70 g/L四氢噻唑硫酮: 5×10-4~3×10-3 g/L盐酸: 0.02~0.08 g/L十二烷基硫酸钠: 0.05~0.2 g/L温度: 10~30℃(室温)电流密度: 1~4 A/dm2搅拌:阴极移动3、用赫尔槽实验观察光亮剂对同层质量影响,记录试验情况。
五、思考问题及要求1、酸性亮铜电镀前为什么要进行预镀?预镀工艺有哪几种?2、溶液pH对铜层质量有什么影响?4、以论文形式写出光亮剂对镀层质量影响为内容的实验报告。
附录用有机玻璃板自制赫尔槽赫尔槽结构简单,制造和使用方便。
目前国内外已广泛应用于电镀实验和工厂生产的质量管理,特别是应用于光亮电镀添加剂的控制,成为电镀工作者不可缺少的工具,267ml赫尔槽尺寸如图。
材料:有机玻璃;槽深:65;厚:3-5一、目的要求掌握有机玻璃黏结技术,自制267ml赫尔槽二、药品与材料:有机玻璃板3~5mm厚钢锯、细纱布180~270#、脱脂棉。
100ml棕色试剂瓶1个三氯化烷、乙醇三、有机玻璃黏结剂配制:配方:三氯甲烷95ml乙醇1~2 ml有机玻璃碎块或碎屑5克。
酸性光亮镀铜工艺及配方

酸性光亮镀铜工艺及配方一、酸性镀铜光亮剂特点:1、快速出光,特好的填平度,即使低电流密度区也可得到极高的填平度。
2、广泛的电流密度范围均可得到镜面亮度。
3、工作温度范围宽,18—< xmlnamespace prefix ="st1" ns ="urn:schemas-microsoft-com:office:smarttags" />40℃都可得到镜面亮度。
4、镀层内应力低,延展性好,电阻率低,可应用于各种不同的基体材料电镀。
铁件、锌合金件、塑胶件等同样适用。
5、光亮剂对杂质容忍度高,性能稳定,易于控制。
一般在使用一段长时间(约800-1000安培小时/升)后,才需用活性碳粉处理。
6、沉积速度快。
在4.5安培/平方分米的电流密度下,每分钟可镀1微米的铜层,电镀时间因而缩短。
(酸性镀铜溶液是一种强酸性的简单盐电镀溶液,镀液中没有使用络合剂。
)二、电镀工艺条件:原料范围标准硫酸铜200-240g/L220 g/L硫酸55-75g/L65 g/L氯离子15-70mg/L20-40mg/LBFJ-210Mμ5-12ml/L8 ml/LBFJ-210A0.5-1.0ml/L0.6 ml/LBFJ-210B0.5-1.0ml/L0.6 ml/L温度18-40℃24-28℃阴极电流密度0.5-10A/dm2阳极电流密度 1.5-8A/dm2搅拌空气搅拌空气搅拌三、镀液的配制:1、先在镀槽中(待用缸或备用缸)加入1/2体积蒸馏水或去离子水,加热至40-50°。
(所用水的氯离子含量应低于70mg/L(ppm))。
2、加入计算量的硫酸铜,搅拌至完全溶解。
3、加入活性炭2g/L,搅拌1小时后静止8小时用过滤泵,把溶液滤入清洁的电镀槽内。
加去离子水至规定体积。
4、在不断搅拌下慢慢加入计算量的化学纯硫酸,(注意:此时会产生大量热能,故需强力搅拌,慢慢添加,以使温度不超过60℃。
化学镀铜工艺
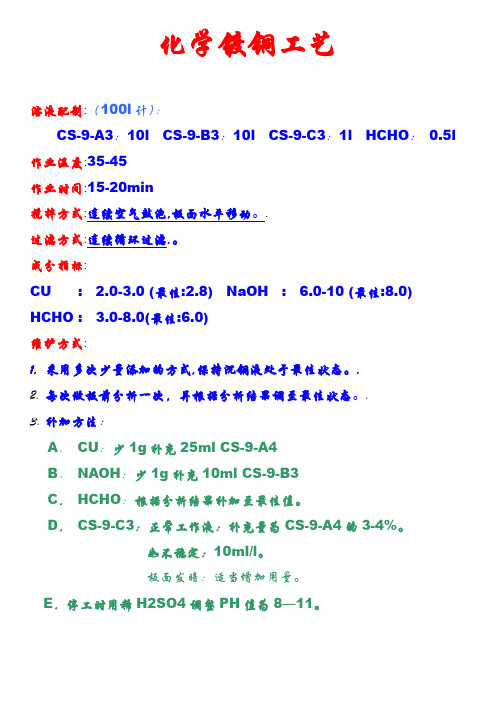
化学镀铜工艺
溶液配制:(100l计):
CS-9-A3:10l CS-9-B3:10l CS-9-C3:1l HCHO:0.5l 作业温度:35-45
作业时间:15-20min
搅拌方式:连续空气鼓泡,板面水平移动。
.
过滤方式:连续循环过滤.。
成分指标:
CU : 2.0-3.0 (最佳:2.8) NaOH : 6.0-10 (最佳:8.0) HCHO : 3.0-8.0(最佳:6.0)
维护方式:
1.采用多次少量添加的方式,保持沉铜液处于最佳状态。
.
2.每次做板前分析一次,并根据分析结果调至最佳状态。
.
3.补加方法:
A.CU:少1g补充25ml CS-9-A4
B.NAOH:少1g补充10ml CS-9-B3
C.HCHO:根据分析结果补加至最佳值。
D.CS-9-C3:正常工作液:补充量为CS-9-A4的3-4%。
如不稳定:10ml/l。
板面发暗:适当增加用量。
E.停工时用稀H2SO4调整PH值为8—11。
化学镀铜溶液成分分析一.。
镀锡铁基体的化学镀铜

广 东 化
工
5 5
第3 8卷 总第 2 5 1 期
www.d h m.o l g c e c n
镀 锡铁基体 的化学镀铜
杨 余芳 ,邓斌 ,文朝 晖
( .湘南学院 化学与生命科学系 ,湖南 郴州 43 0 ;2 1 20 0 .湘南学院 图书馆 ,湖南 郴州 4 30 ) 2 00
【 要】 { 商 为了提高铁的耐蚀性 ,在镀锡铁基体上进行了化学镀铜的研究。系统地研究了柠檬酸一 酒石酸二元配位体化学镀铜体系中各因素对 镀速的影响。结果表明,柠檬酸一 酒石酸二元配位体系的镀速大于柠檬酸单配位体系的镀速。随着 C S H0、柠檬酸、酒石酸、次磷酸钠浓 uO 5 2 度的 增大 ,以及 随 着 p H和 温度 的升 高 ,镀 速均 先 升高 后 降低 。化 学 镀铜 液 的最佳 组 成为 :C S 4 H2 2gL u O 0 1 / ,柠 檬酸 4 / 5 0gL,酒石 酸 4 gL, 0/ 次磷 酸钠 2 / 0gL,抗 氧化 剂 1gL,硼 酸 1 / ,表面 活性 剂 01 L / 0gL . 。最 佳温 度 为 5  ̄6 ℃、p 为 t 5 . 。在最佳 条件 下 ,铜 的镀 速为 5 0 H . ~1 6 2 7 5 6 ̄nh . t/,获 得 的镀层 表 面光 亮平 滑 ,结 晶致密 ,耐蚀 性 良好 。铜 锡镀 层之 间、锡 镀层 与铁 基体 之 间 的结合 力优 良。 0 r [ 关键词】 铜;锡;化学镀 ;铁基体 ;镀速 [ 中图分 类 号]Q13 T 5 [ 献标 识码 ] 文 A [ 章编 号]0716(0 1 30 5.3 文 10 .8 52 1) .0 50 0
Unv ri , h n h u4 3 0 , hn ) ies y C e z o 2 0 0 C ia t
电镀铜 化学实验报告
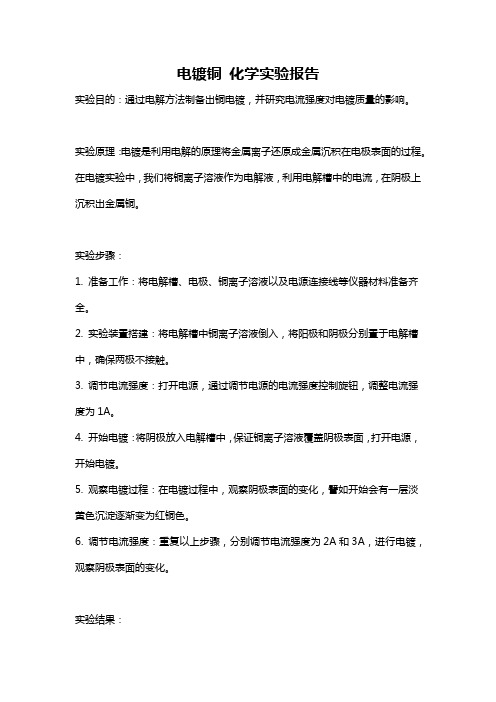
电镀铜化学实验报告实验目的:通过电解方法制备出铜电镀,并研究电流强度对电镀质量的影响。
实验原理:电镀是利用电解的原理将金属离子还原成金属沉积在电极表面的过程。
在电镀实验中,我们将铜离子溶液作为电解液,利用电解槽中的电流,在阴极上沉积出金属铜。
实验步骤:1. 准备工作:将电解槽、电极、铜离子溶液以及电源连接线等仪器材料准备齐全。
2. 实验装置搭建:将电解槽中铜离子溶液倒入,将阳极和阴极分别置于电解槽中,确保两极不接触。
3. 调节电流强度:打开电源,通过调节电源的电流强度控制旋钮,调整电流强度为1A。
4. 开始电镀:将阴极放入电解槽中,保证铜离子溶液覆盖阴极表面,打开电源,开始电镀。
5. 观察电镀过程:在电镀过程中,观察阴极表面的变化,譬如开始会有一层淡黄色沉淀逐渐变为红铜色。
6. 调节电流强度:重复以上步骤,分别调节电流强度为2A和3A,进行电镀,观察阴极表面的变化。
实验结果:在1A电流强度下电镀,电镀时间为30分钟,阴极表面形成了一层均匀的红铜沉淀。
电镀质量较好。
在2A电流强度下电镀,电镀时间为30分钟,阴极表面形成了一层红铜沉淀,但表面不均匀,有一些凸起和凹陷。
在3A电流强度下电镀,电镀时间为30分钟,阴极表面形成了一层厚厚的红铜沉淀,但表面非常不均匀,有较多的凹陷和坑洞。
实验分析:通过上述实验结果可以看出,电流强度对电镀质量有影响。
在1A电流强度下,电镀质量较好,铜沉淀均匀。
随着电流强度的增加,电镀质量变差,表面变得不均匀,出现凸起和凹陷。
这是因为较低的电流强度有利于离子的均匀分布和沉积,而较高的电流强度则促进了不均匀的沉积。
此外,较高的电流强度会导致阴极温度升高,使电镀质量更加不稳定。
结论:通过本次实验,我们成功制备了铜电镀,并发现电流强度对电镀质量有明显的影响。
较低的电流强度有利于获得均匀的电镀层,而较高的电流强度会使电镀质量变差。
因此,在实际应用中,需要根据所需电镀质量的要求来选择适当的电流强度。
化学镀铜配方组成,化学镀铜成分分析及生产技术工艺
化学镀铜配方组成,生产工艺及技术应用1 背景化学镀(Chemiealplating)又称自催化镀;(Autoeatalytieplating),是指在没有外加电流的条件下,利用溶液中的还原剂将金属离子沉积在具有催化活性的基体表面。
从本质上讲,它发生的是一种自催化的氧化还原反应,又可译为不通电电镀或无电解电镀。
是在基体表面上化学沉积形成金属或合金镀层的一种表面处理技术。
化学镀铜第一次工业应用开始于19世纪50年代中叶,此后化学镀铜技术被大量用于电子和涂装行业,其中印刷电路板的工业生产一度成为规模最大的应用领域。
化学镀铜技术继而被用于金属化工艺,在半导体电子行业等高技术领域扮演着越来越重要的角色,特别是近年来,超大规模集成电路由铝金属化发展为铜金属化工艺以来,化学镀铜技术更加受到关注。
禾川化学引进国外尖端配方解析技术,经过多年的技术积累,成功开发出新型化学镀铜配方技术;该化学镀铜镀层厚度均匀,无明显边缘效应,特别是对复杂形状的基体,在尖角或凹凸部位没有额外的沉积或沉积不足,在深孔、盲孔件、腔体件的内表面也能得到和外表面同样厚度的镀层,因而对尺寸精度要求高的零件进行化学镀铜特别有利;该镀层晶粒细、致密、空隙少,呈光亮或半光亮,比电镀层更加耐腐蚀;该镀铜技术无需电解设备及附件,工艺操作人员也无需带电操作,均可在所需部位镀出合乎要求的镀层。
该镀铜技术广泛应用于电子、汽车、航空等行业。
2化学镀铜常见组成典型的镀液成分主要由无机盐和有机添加剂组成。
无机盐包括CuCl2、CuSO4、氯离子,采用的主要有机添加剂包括促进剂(或称为光亮剂);抑制剂(表面活性剂,润湿剂,阻化剂)。
2.1铜盐铜盐是化学镀铜的主盐,提供镀铜所需要的铜离子,可以使用CuSO4、CuC12、Cu(NO3)2、Cu(OH)2、(CH3COO)2Cu、酒石酸铜等二价铜盐;目前最常采用的铜盐为硫酸铜,化学镀铜溶液中铜盐的含量越高,镀速越快;但是当其含量继续增加达到某一定值后,镀速变化不再明显。
电镀铜和化学镀铜的性能分析和影响因素
电镀铜的性能分析及影响因素(作者)摘要:关键词:英文摘要:0 绪论●电镀和化学镀概述在国民经济的各个生产和科学发展领域里,如机械、无线电、仪表、交通、航空及船舶工业中,在日用品的生产和医疗器械等设备的制造中,金属镀层都有极为广泛而应用。
世界各国由于钢铁所造成的损失数据是相当惊人的,几乎每年钢铁产量的,三分之一由于腐蚀而报废,当然电镀层不可能完全解决这个问题,但是良好的金属镀层还是能在这方面做出较大贡献的。
电镀和化学镀则是获得金属防护层的有效方法。
化学镀方法所得到的金属镀层,结晶细致紧密,结合力良好,它不但具有良好的防腐性能,而且满足工业某些特殊用途。
●化学镀与电镀的优缺点化学镀与电镀比较具有以下优点:(1)镀层厚度比较均匀,化学镀液的分散力接近百分之百,无明显的边缘效应,几乎是基材形状的复制因此特适合形状复杂工件、腔体件、深孔件、盲孔件、管件内壁等表面施镀。
电镀法因受力线分布不均匀的限制是很难做到的。
(2)通过敏化、活化等前处理化学镀可以在非金属(非导体)如塑料、玻璃、陶瓷及半导体材料表面上进行,而电镀发只能在导体表面上进行。
因此,化学镀工艺是非金属表面金属化的常用方法。
也是非导体材料电镀前作导电底层的方法。
(3)工艺设备简单,不需要电源、输电系统及辅助电极,操作时只需要把工件正确的悬挂在镀液中即可。
(4)化学镀是靠基体材料的自催化活性才能起镀,其结合力一般优于电镀。
镀层有光亮或半光亮的外观。
晶粒细、致密、孔隙率低。
某些化学镀层还具有特殊的物理性能。
电镀也具有其不能为化学镀代替的优点:(1)可以沉积的金属及合金品种远多于化学镀。
(2)价格比化学镀低得多。
(3)工艺成熟,镀液简单、易于控制。
化学镀铜的应用领域及进展铜具有良好的导电、导热性能,质软而韧,有良好的压延性和抛光性能。
为了提高表面镀层和基体金属的结合力,铜镀层常用作防护、装饰性镀层的底层,对局部渗碳工件,常用镀铜来保护不需要渗碳的部位。
1)印刷线路板通孔金属化处理目前化学镀铜在工业上最重要的应用是印刷线路板(PrintedCircuit Board,简称PCB)的通孔金属化过程,使各层印刷导线的绝缘孔壁内沉积上一层铜,从而使两面的电路导通,成为一个整体。
化学镀铜工艺
化学镀铜主要是用于非金属表面形成导电层,因此在印制板电镀和塑料电镀 中都有广泛应用。铜与镍相比,标准电极电位比较正(0.34v),因此比较容易从 镀液中还原析出,但是也正因为此,镀液的稳定性也差一些,容易自分解而失效。
(1)工艺配方
硫酸铜 碳酸钠 酒石酸钾钠 硫脲 氢氧化钠 pH 值 三乙醇胺 温度
要想获得延展性好又有较快沉积速度的化学镀铜,建议使用如下工艺:
硫酸铜 氰化镍钾
7~15g/L l5mg
LEDTA 温度 甲醛 析出速度 用氢氧化钠调整 pH 值
45g/L 60℃ l5ml/L 8~10μ m/h l2.5
如果不用 EDTA,也可以用酒石酸钾钠 75g/L。另外,现在已经有商业的 专用络合剂出售,这种商业操作在印制线路板行业很普遍。所用的是 EDTA 的衍 生物,其稳定性和沉积速度都比自己配制要好一些。一般随着温度的上升,其延 展性也要好一些。在同一温度下,沉积速度慢时所获得的镀层延展性要好一些, 同时抗拉强度也增强。为了防止铜粉的产生,可以采用连续过滤的方式来当做空 气搅拌。下表是根据资料整理的稳定性较好的一些化学镀铜液的配方。
⑤使用前再加入还原剂甲醛。
在使用中采用空气搅拌,可提高镀液的稳定性,并可将副反应生成的一价铜 氧化为二价铜,以防止因歧化反应生出铜粉而导致自分解。
在镀液用过后,存放时要将 pH 调低至 7~8,并且过滤掉固体杂质,更换一 个新的容器保存,才可防止自分解失效。
用于非金属电镀的化学镀铜工艺如下:
硫酸铜 37%甲醛 酒石酸钾钠 硫脲 氢氧化钠 温度 碳酸钠 搅拌
(2)配制与维护
7g/L 10g/L 75g/L 0.01g/L 20g/L 12 l0mL/L 40~50℃
化学镀铜原理
化学镀铜原理文档编制序号:[KKIDT-LLE0828-LLETD298-POI08]化学镀铜原理发布日期:2012-01-06 浏览次数:6我们先看一个典型的化学镀铜液的配方:硫酸铜5g/L甲醛1OmL/L酒石酸钾钠25g/L稳定剂0.1mg/L氢氧化钠7g/L这个配方中硫酸铜是主盐,是提供我们需要镀出来的金属的主要原料。
酒石酸钾钠称为络合剂,是保持铜离子稳定和使反应速度受到控制的重要成分。
氢氧化钠能维持镀液的pH值并使甲醛充分发挥还原作用。
而甲醛则是使二价铜离子还原为金属铜的还原剂,是化学镀铜的重要成分。
稳定剂则是为了防止当镀液被催化而发生铜的还原后,能对还原的速度进行适当控制,防止镀液自己剧烈分解而导致镀液失效。
化学镀铜当以甲醛为还原剂时,是在碱性条件下进行的,铜离子则需要有络合剂与之形成络离子,以增加其稳定性。
常用的络合剂有酒石酸盐、EDTA、多元醇、胺类化合物、乳酸、柠檬酸盐等。
我们可以用如下通式表示铜络离子:Cu2+·络合物,则化学镀铜还原反应的表达式如下:Cu2+·络合物+2HCH0+40H一一Cu+2HC00一+H2+2H20+络合物这个反应需要催化剂催化才能发生,因此适合于经活化处理的非金属表面,但是在反应开始后,当有金属铜在表面开始沉积出来,铜层就作为进一步反应的催化剂而起催化作用,使化学镀铜得以继续进行。
这与化学镀镍的自催化原理是一样的。
当化学镀铜反应开始以后,还有一些副反应也会发生:2HCHO+OH一→CH30H+HCOO-这个反应也叫“坎尼扎罗反应”,它也是在碱性条件下进行的,将消耗掉一些甲醛。
2Cu2++HCHO+50H→Cu20+HC00一+3H2这是不完全还原反应,所产生的氧化亚铜会进一步反应:Cu20+2HCHO+20H一→2Cu+H2+H20+2HC00—Cu20+H20→2Cu++20H一也就是说,一部分还原成金属铜外,还有一部分还原成为一价铜离子。
- 1、下载文档前请自行甄别文档内容的完整性,平台不提供额外的编辑、内容补充、找答案等附加服务。
- 2、"仅部分预览"的文档,不可在线预览部分如存在完整性等问题,可反馈申请退款(可完整预览的文档不适用该条件!)。
- 3、如文档侵犯您的权益,请联系客服反馈,我们会尽快为您处理(人工客服工作时间:9:00-18:30)。
三.化学镀铜参考配方
3.1化学镀铜参考配方一
成分
质量份
成分说明
硫酸铜
25~30
酒石酸钾钠
140~150
氢氧化钠
40~50
甲醛
18~20
乙二胺四醋酸
0.5~1.5
三乙醇胺
0~1
碳酸钠
8~10
二乙基二硫代氨基甲酸钠
0~1
去离子水
加至1L
以上参考配方数据都经过技术修改,仅供参考
化学镀铜配方分析|分析检
背景
化学镀铜常见组成
常见配方
一.背景
化学镀(Chemiealplating)又称自催化镀(Autoeatalytieplating),是指在没有外加电流的条件下,利用溶液中的还原剂将金属离子沉积在具有催化活性的基体表面。从本质上讲,它发生的是一种自催化的氧化还原反应,又可译为不通电电镀或无电解电镀。是在基体表面上化学沉积形成金属或合金镀层的一种表面处理技术.
加入乙醇酸、乙酸、氨基乙酸、草酸、丁二酸、苹果酸、丙二酸、柠檬酸等,可加速乙醛酸的氧化反应。
2.1.4促进剂
促进剂,通常是含有硫或其它官能团的有机物,包括硫脲及其衍生物。促进剂的作用这类添加剂的主要作用是提高阴极电流密度和使镀层晶粒细化;同时促进剂还可以优先吸附在活性较高、生长速率快的晶面上,使得金属的吸附原பைடு நூலகம்进入这些活性位置有困难,使这些晶面的生长速率下降,从而得到排列整齐的晶体,使镀层均匀。目前,通常使用SPS(聚二硫二丙烷磺酸钠)和MPSA(3-巯基丙烷磺酸钠)。
禾川化学专业从事化学镀铜添加剂配方分析、成分分析、配方检测、成分检测;禾川化学是镀铜企业产品技术革新的风向标;禾川化学成功开发出新型化学镀铜配方技术;该化学镀铜镀层厚度均匀,无明显边缘效应,特别是对复杂形状的基体,在尖角或凹凸部位没有额外的沉积或沉积不足,在深孔、盲孔件、腔体件的内表面也能得到和外表面同样厚度的镀层,因而对尺寸精度要求高的零件进行化学镀铜特别有利;该镀层晶粒细、致密、空隙少,呈光亮或半光亮,比电镀层更加耐腐蚀;该镀铜技术无需电解设备及附件,工艺操作人员也无需带电操作,均可在所需部位镀出合乎要求的镀层。该镀铜技术广泛应用于电子、汽车、航空等行业.
2.1.2络合剂
络合剂是化学镀液中的关键成分,络合剂一方面可使铜离子的极化增大,使所得的镀层结晶细致光亮,另一方面可使镀液稳定,防止铜离子在碱性条件下生成Cu(OH)2沉淀。常用的配位剂有酒石酸钾钠、柠檬酸钠、乙二胺四乙酸二钠、三乙醇胺、氨二乙酸等;酒石酸是最早使用的络合剂,特别适合于室温和低沉积速率时使用,也较易进行污水处理,但沉积速率低、镀液稳定性低且镀层韧性差限制了它的应用范围;乙二胺四乙酸(EDTA),作为络合剂,是因为该体系的镀铜液稳定性高、镀速快、镀层质量好;以三乙醇胺(TEA)作络合剂的化学镀铜,以一定比例配成的工作液有很高的镀速和稳定性,但是当三乙醇胺、三异丙醇胺用量超过一定值时,镀速会急剧减小,虽然EDTA的用量对镀速的影响不大,但其速率要比三乙醇胺小很多.
2.1.5抑制剂
抑制剂,其特征是在阴极表面上形成一层连续膜以阻止铜的沉积。抑制剂能够吸附在镀件的表面阻化或减少光亮剂和整平剂的扩散传递,而加大在刻槽口的吸附,达到整平效果。目前,最为常用的是PEG和PEG与氯离子的协同作用,氯离子的存在可以加强其吸附和阻化作用。PEG分子量越大,吸附能力越强,阻化作用越强,但是溶解性越差,扩散系数越小。
二.化学镀铜
2.1化学镀铜常见组成
典型的镀液成分主要由无机盐和有机添加剂组成。无机盐包括CuCl2、CuSO4、氯离子,采用的主要有机添加剂包括促进剂(或称为光亮剂);抑制剂(表面活性剂,润湿剂,阻化剂)。
2.1.1铜盐
铜盐是化学镀铜的主盐,提供镀铜所需要的铜离子,可以使用CuSO4、CuC12、Cu(NO3)2、Cu(OH)2、(CH3COO)2Cu、酒石酸铜等二价铜盐;目前最常采用的铜盐为硫酸铜,化学镀铜溶液中铜盐的含量越高,镀速越快;但是当其含量继续增加达到某一定值后,镀速变化不再明显。铜盐浓度对于镀层性能的影响较小,然而铜盐中的杂质可能对镀层性质造成很大的影响,因此化学镀铜溶液中铜盐的纯度要求较高.
化学镀铜第一次工业应用开始于19世纪50年代中叶,此后化学镀铜技术被大量用于电子和涂装行业,其中印刷电路板的工业生产一度成为规模最大的应用领域。化学镀铜技术继而被用于金属化工艺,在半导体电子行业等高技术领域扮演着越来越重要的角色,特别是近年来,超大规模集成电路由铝金属化发展为铜金属化工艺以来,化学镀铜技术更加受到关注.
2.1.3还原剂
镀铜溶液中还原剂的作用是使铜配离子还原为金属铜,常见的还原剂有甲醛(HCHO)、乙二醛、乙醛酸、次磷酸盐、四丁基硼氢化铵二甲氨基硼烷、联氨、硼氢化钠、阱(N2H4)、氨基硼烷及其衍生物等。出于生产成本和操作工艺的考虑,目前工业上仍普遍使用甲醛作为化学镀铜溶液的还原剂。该溶液得到的铜膜电阻率低,沉积速率高,具有很好的应用价值。