包装车间质量检验流程
生产车间包装检验流程

生产车间包装检验流程
生产车间包装检验流程:
①核对订单:确认产品型号、数量与订单一致,确保包装的产品正确无误。
②清洁工作台:保持工作台干净整洁,避免异物污染产品。
③检查包装材料:确认包装盒、说明书、标签等材料齐全且无破损、脏污。
④产品外观检查:目视检查产品表面是否有划痕、凹陷、色差等问题。
⑤功能测试:随机抽样进行功能测试,确保产品质量符合标准。
⑥包装操作:按照规定的方法和顺序将产品放入包装盒内,添加填充物固定。
⑦标签粘贴:准确粘贴产品标签,包括产品信息、批次号、生产日期等。
⑧密封包装:使用胶带或其他密封方式确保包装盒封闭严密。
⑨二次检验:对已包装的产品进行再次检查,确认无漏装、错装、标签错误等情况。
⑩打包加固:对于外包装,使用打包带或胶带加固,确保运输过程中的安全。
⑪批量抽检:对整批包装完成的产品进行随机抽检,验证包装质量和产品一致性。
⑫记录归档:记录检验结果,包括检验日期、检验人、产品批次和检验结论,以便追溯。
⑬异常处理:对检验中发现的问题产品进行标记隔离,分析原因,采取纠正措施。
⑭入库准备:将检验合格的包装产品搬运至指定区域,等待入库或发货。
包装车间操作流程

包装车间操作流程一、概述包装车间是一个重要的环节,它负责对产品进行包装,确保产品的安全运输和销售。
本文将详细描述包装车间的操作流程,包括准备工作、包装流程和质量控制。
二、准备工作1. 确认包装需求:根据产品的特性和客户的要求,确定适合的包装材料和包装方式。
2. 准备包装材料:根据包装需求,准备所需的包装盒、袋、纸张、胶带等材料,并确保其质量符合标准。
3. 检查设备:检查包装设备的运行状况,确保其正常工作。
包括包装机、封箱机、打码机等。
三、包装流程1. 接收产品:从生产线接收产品,确保产品数量和质量与生产计划一致。
2. 检查产品:对产品进行外观检查和质量检测,确保产品符合质量标准。
3. 包装准备:根据产品的特性和包装需求,选择合适的包装材料,并将其准备好。
4. 包装操作:将产品放入包装盒或袋中,根据需要添加填充物,使用胶带或封箱机进行封装。
5. 标记和打码:在包装上标记产品的相关信息,如批次号、生产日期、条形码等。
使用打码机进行打码操作。
6. 包装检查:对包装后的产品进行检查,确保包装完整、无破损,并符合质量要求。
7. 包装装箱:将包装好的产品放入适当的运输箱中,并按照规定的方式进行堆放和固定。
8. 清理和整理:及时清理包装车间,保持工作区域整洁有序。
四、质量控制1. 抽样检验:定期进行抽样检验,检查包装质量是否符合标准要求。
2. 检测设备:确保包装设备的准确性和可靠性,定期进行设备的校准和维护。
3. 培训和培训记录:对包装操作人员进行培训,确保其掌握正确的操作流程和质量控制要求。
同时记录培训内容和培训人员信息。
4. 不良品处理:对发现的不良品进行处理,包括返工、报废等,确保不良品不进入市场。
5. 持续改进:定期评估包装流程和质量控制措施的有效性,并根据评估结果进行改进,提高包装质量和效率。
五、总结包装车间操作流程是确保产品质量和安全的重要环节。
通过准备工作、包装流程和质量控制,可以保证产品包装的完整性和一致性,提高客户满意度。
包装车间工作流程图

包装车间工作流程图标题:包装车间工作流程图引言概述:包装车间是生产线上的一个重要环节,它负责对产品进行包装,确保产品的安全和整洁。
本文将详细介绍包装车间的工作流程图,包括四个部分:物料准备、包装操作、质量检验和成品入库。
一、物料准备:1.1 物料收集:包装车间根据生产计划,收集所需的包装材料和工具,如纸箱、胶带、泡沫垫等。
1.2 物料检查:对收集到的物料进行检查,确保其质量和数量符合要求,如纸箱是否完好,泡沫垫是否齐全等。
1.3 物料存储:将检查合格的物料按照规定的存储方式进行分类、标识和存放,以便后续使用。
二、包装操作:2.1 包装准备:根据产品的特点和包装要求,选择适当的包装材料和包装方式,如纸箱包装、气泡膜包装等。
2.2 包装操作:将产品放入包装材料中,并按照规定的包装方式进行包装,如折叠纸箱、包裹气泡膜等。
2.3 包装标识:在包装好的产品上标识相关信息,如产品型号、数量、生产日期等,以便后续追溯和管理。
三、质量检验:3.1 外观检查:对包装好的产品进行外观检查,确保产品没有损坏、污染等问题。
3.2 尺寸检测:对包装好的产品进行尺寸测量,确保产品的尺寸符合要求。
3.3 包装完整性检查:对包装材料进行检查,确保包装完好,没有破损或松动的情况。
四、成品入库:4.1 入库登记:将经过包装和质量检验的产品进行入库登记,记录产品的相关信息,如入库时间、数量等。
4.2 包装材料处理:对包装材料进行处理,如回收利用或进行分类处理,以减少资源浪费。
4.3 成品存储:将入库的产品按照规定的存储方式进行分类、标识和存放,以便后续发货或销售。
综上所述,包装车间的工作流程图包括物料准备、包装操作、质量检验和成品入库四个部分。
通过严格的操作流程和质量控制,包装车间能够确保产品的安全、整洁和质量符合要求,为后续的发货和销售提供有力支持。
包装车间产品质量控制流程
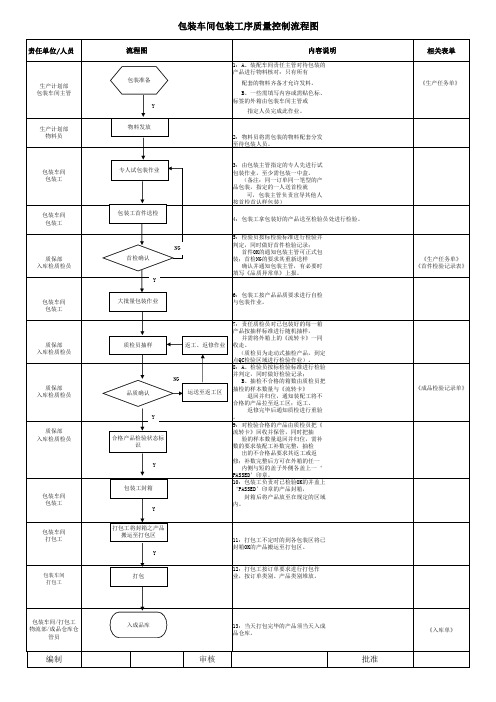
5:检验员按标检验标准进行检验并判定,同时做好首件检验记录; NG 质保部 入库检质检员 首检确认 首件OK的通知包装主管可正式包装;首检NG的要求其重新送样 确认并通知包装主管,有必要时填写《品质异常单》上报。 Y 6:包装工按产品品质要求进行自检与包装作业。 《生产任务单》 《首件检验记录表》
包装车间 包装工
物料发放 2:物料员将需包装的物料配套分发至待包装人员。
包装车间 包装工
专人试包装作业
3:由包装主管指定的专人先进行试包装作业,至少需包装一中盒。 (备注:同一订单同一笔型的产品包装,指定的一人送首检就 可,包装主管负责宣导其他人按首检首认样包装)
包装车间 包装工
包装工首件送检
4:包装工拿包装好的产品送至检验员处进行检验。
Y 内侧与短的盖子外侧各盖上一‘PASSED’印章。 包装工封箱 包装车间 包装工 Y 打包工将封箱之产品 搬运至打包区 11:打包工不定时的到各包装区将已封箱OK的产品搬运至打包区。 Y 12:打包工按订单要求进行打包作业,按订单类别、产品类别堆放。 10:包装工负责对已检验OK的并盖上‘PASSED’印章的产品封箱, 封箱后将产品放至在规定的区域内。
大批量包装作业
7:责任质检员对已包装好的每一箱产品按抽样标准进行随机抽样, 质保部 入库检质检员 质检员抽样 返工、返修作业 并需将外箱上的《流转卡》一同收走。 (质检员为走动式抽检产品,到定点QC检验区域进行检验作业)。 8:A、检验员按标检验标准进行检验并判定,同时做好检验记录; NG 质保部 入库检质检员 B、抽检不合格的箱数由质检员把抽检的样本数量与《流转卡》
品质确认
运送至返工区 退回并归位,通知装配工将不合格的产品拉至返工区;返工、 Y 返修完毕后通知质检进行重验。 9:对检验合格的产品由质检员把《流转卡》回收并保管,同时把抽
包装车间质量检验流程
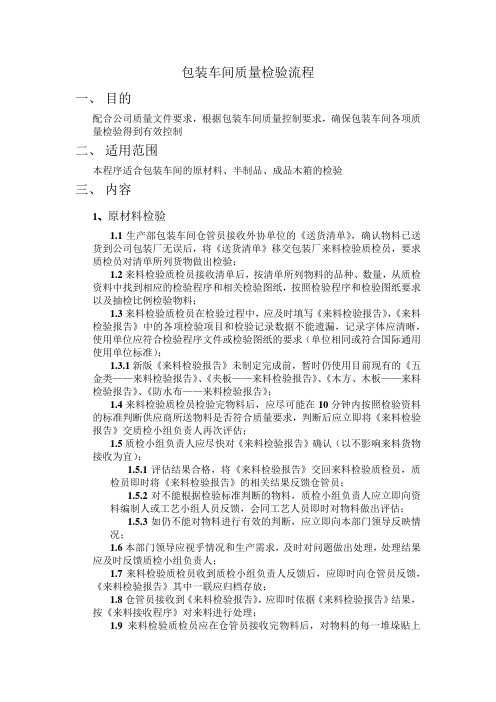
包装车间质量检验流程一、目的配合公司质量文件要求,根据包装车间质量控制要求,确保包装车间各项质量检验得到有效控制二、适用范围本程序适合包装车间的原材料、半制品、成品木箱的检验三、内容1、原材料检验1.1生产部包装车间仓管员接收外协单位的《送货清单》,确认物料已送货到公司包装厂无误后,将《送货清单》移交包装厂来料检验质检员,要求质检员对清单所列货物做出检验;1.2来料检验质检员接收清单后,按清单所列物料的品种、数量,从质检资料中找到相应的检验程序和相关检验图纸,按照检验程序和检验图纸要求以及抽检比例检验物料;1.3来料检验质检员在检验过程中,应及时填写《来料检验报告》,《来料检验报告》中的各项检验项目和检验记录数据不能遗漏,记录字体应清晰,使用单位应符合检验程序文件或检验图纸的要求(单位相同或符合国际通用使用单位标准);1.3.1新版《来料检验报告》未制定完成前,暂时仍使用目前现有的《五金类——来料检验报告》、《夹板——来料检验报告》、《木方、木板——来料检验报告》、《防水布——来料检验报告》;1.4来料检验质检员检验完物料后,应尽可能在10分钟内按照检验资料的标准判断供应商所送物料是否符合质量要求,判断后应立即将《来料检验报告》交质检小组负责人再次评估;1.5质检小组负责人应尽快对《来料检验报告》确认(以不影响来料货物接收为宜);1.5.1评估结果合格,将《来料检验报告》交回来料检验质检员,质检员即时将《来料检验报告》的相关结果反馈仓管员;1.5.2对不能根据检验标准判断的物料,质检小组负责人应立即向资料编制人或工艺小组人员反馈,会同工艺人员即时对物料做出评估;1.5.3如仍不能对物料进行有效的判断,应立即向本部门领导反映情况;1.6本部门领导应视乎情况和生产需求,及时对问题做出处理,处理结果应及时反馈质检小组负责人;1.7来料检验质检员收到质检小组负责人反馈后,应即时向仓管员反馈,《来料检验报告》其中一联应归档存放;1.8仓管员接收到《来料检验报告》,应即时依据《来料检验报告》结果,按《来料接收程序》对来料进行处理;1.9来料检验质检员应在仓管员接收完物料后,对物料的每一堆垛贴上“合格”、“让步接收”标识;1.10具体操作流程可参见附表《原材料检验流程图》;2、生产过程检验2.1生产班组人员对本工序已完工产品应按车间生产图纸或工艺要求进行自检,自检分为首检和批检,首检指操作者最先加工的一定数量的产品进行检查,批检指操作者完成一定数量的加工产品并形成一个批次后的检查,自检合格后的产品方可流到下一生产工序;2.1.1不合格产品应即时在本岗位进行反修,对不合格产品应按《车间工序不合格产品处理程序》进行处理;2.1.2对于工序中要求需质检人员检验确认的产品,生产班组人员应填写《半制品质检报检单》,交生产车间质检员进行检验;2.2车间质检员对生产工序人员提交的《半制品质检报检单》应及时进行检验(以不影响生产为宜);2.2.1检验时应按照产品的生产工艺要求或生产图纸进行检验,检验过程中应及时填写《半制品质检报检单》,《半制品质检报检单》中的各项检验项目和检验记录数据不能遗漏,记录字体应清晰,使用单位应符合检验程序文件或检验图纸的要求(单位相同或符合国际通用使用单位标准);2.2.2车间质检员应有足够的能力判断半制品是否符合质量要求,并能独立处理车间半制品质检工作,无需报质检小组负责人决定;2.2.3检验后应对已检验物料贴上“合格”、“不合格”、“让步接收”标识,《半制品质检报检单》应归档存放;2.3生产过程检验中如发现重大不合格或连续两批次不合格,车间质检员应及时发出《纠正和预防措施控制要求通知》,要求相关责任班组整改,具体参见《纠正措施控制程序》;2.4具体操作流程可参见《生产过程检验流程图》3、部件成品检验3.1生产班组人员对已完工部件成品应按车间生产图纸和工艺要求进行自检(此自检定义为批检);3.1.1不合格产品应即时在本岗位进行反修,对不合格产品应按《车间工序不合格产品处理程序》进行处理;3.2自检合格部件成品应填写《部件成品质检报检单》,填写完毕后交车间质检员进行检验;3.3车间质检员对生产工序人员提交的《部件成品质检报检单》应及时进行检验(以不影响生产为宜);3.3.1检验时应按照产品的生产工艺要求或生产图纸进行检验,检验过程中应及时填写《部件成品质检报检单》,《部件成品质检报检单》中的各项检验项目和检验记录数据不能遗漏,记录字体应清晰,使用单位应符合检验程序文件或检验图纸的要求(单位相同或符合国际通用使用单位标准);3.3.2车间质检员应有足够的能力判断半制品是否符合质量要求,并能独立处理车间半制品质检工作,无需报质检小组负责人决定;3.3.3检验后应对已检验物料贴上“合格”、“不合格”、“让步接收”标识,《部件成品质检报检单》应归档存放;3.4部件成品检验中如发现重大不合格或连续两批次不合格,车间质检员应及时发出《纠正和预防措施控制要求通知》,要求相关责任部门整改,具体参见《纠正措施控制程序》;3.5具体操作流程可参见《部件成品检验流程图》;4、拼装木箱成品检验4.1拼装人员(包括客户厂的我司人员)对已完工木箱成品应按生产图纸和工艺要求进行自检(此自检定义为每一个木箱成品);4.1.1不合格产品应即时在本岗位进行反修;不能反修成品应即时通知当班主管;当班主管应即时对木箱成品做出是否更换决定,并通知我司包装厂负责人增加生产计划;4.2自检合格部件成品如在我司包装厂拼装,即按本程序中程序第4部份执行,如拼装在客户厂,则应按客户厂的质检程序执行;4.3对于在客户厂拼装的木箱成品,生产车间质检小组外协质检员应定时及不定时对木箱成品进行抽检,抽检的检验单按《部件成品质检报检单》书写;4.4成品木箱检验的《部件成品质检报检单》应归类存档;4.5成品木箱检验中如发现重大不合格或连续两批次不合格,质检小组外协质检员应及时发出《纠正和预防措施控制要求通知》,要求相关责任部门整改,具体参见《纠正措施控制程序》;4.6包装厂应及时跟踪客户厂对于我司拼装木箱的质量检验情况;及时跟进客户厂提出的质量问题处理,并对问题归类存档;4.7对客户厂提出的质量问题,执行本程序的5.5规定;4.8具体操作流程可参见《木箱成品检验流程图》;5、质检抽样方法5.1质检抽样方法采用美国军用标准MIL-STD-105E方法抽样,一般检查水平Ⅱ级标准抽取样品,具体标准参见附表《批次性抽样样本代字表》、《批次性减量检验单次抽样计划表》、《批次性正常检验单次主抽样计划表》;5.2比较质量AQL值(以AQL值评定批次检验的结果:合格/不合格):致命缺陷(Critical) 0严重缺陷(Major)……………………………… 1.5轻微缺陷(M inor)……………………………… 4.0 致命缺陷:对产品功能、安全产生严重影响或如存在质量问题可能对人体安全产生隐患的检查项目;严重缺陷:对产品功能、安全、外观产生较严重影响的检查项目;轻微缺陷:对产品功能、外观只产生轻微影响的检查项目;。
包装车间工作流程图

包装车间工作流程图一、引言包装车间是一个重要的生产环节,它负责对产品进行包装和标识,确保产品的安全和质量。
本文将详细描述包装车间的工作流程,包括原材料准备、包装操作、质量检验和成品出库等环节。
二、工作流程图```——> 质量检验——> 成品出库|原材料准备——> 包装操作——||——> 废品处理```三、工作流程详细描述1. 原材料准备- 包装车间根据生产计划,提前准备好所需的包装材料和标识物。
- 原材料包括纸箱、塑料袋、泡沫板等,标识物包括产品标签、说明书等。
- 原材料准备工作由仓库人员负责,确保原材料的充足和质量。
2. 包装操作- 操作员根据产品的特点和要求,选择合适的包装材料和包装方式。
- 将产品放入包装材料中,使用封箱机或者手动封箱,确保包装坚固。
- 在包装上粘贴产品标签和说明书,以便消费者了解产品信息。
- 包装操作需要操作员具备一定的包装技巧和经验,确保包装质量和效率。
3. 质量检验- 包装完成后,质量检验员对包装进行检查,确保包装质量符合标准要求。
- 检查包装是否完整、坚固,标签和说明书是否清晰可读。
- 如果发现包装存在问题,质量检验员将及时通知相关人员进行修复或者更换。
4. 废品处理- 如果包装浮现质量问题无法修复,将被归类为废品。
- 废品需要被正确处理,可以进行回收利用或者进行环保处理。
- 废品处理需要符合相关的环保法规和公司规定,确保环境保护和资源利用。
5. 成品出库- 经过质量检验合格的产品,将被安排出库。
- 出库操作需要仓库人员根据定单要求,进行准确的发货和记录。
- 出库时需要对产品进行包装完整性和数量的再次检查,确保发货的准确性。
四、总结包装车间的工作流程图详细描述了原材料准备、包装操作、质量检验和成品出库等环节。
这些环节相互衔接,确保产品的包装质量和安全性。
通过严格的质量检验和废品处理,提高了产品的质量和公司的形象。
同时,准确的成品出库操作,确保了产品能够按时送达客户手中。
包装车间操作流程
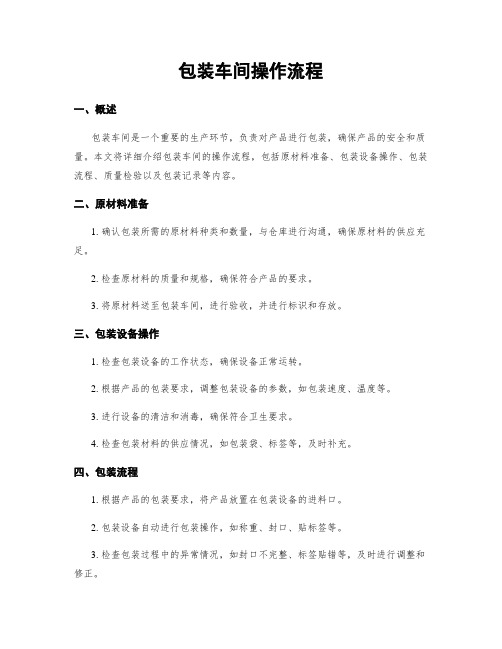
包装车间操作流程一、概述包装车间是一个重要的生产环节,负责对产品进行包装,确保产品的安全和质量。
本文将详细介绍包装车间的操作流程,包括原材料准备、包装设备操作、包装流程、质量检验以及包装记录等内容。
二、原材料准备1. 确认包装所需的原材料种类和数量,与仓库进行沟通,确保原材料的供应充足。
2. 检查原材料的质量和规格,确保符合产品的要求。
3. 将原材料送至包装车间,进行验收,并进行标识和存放。
三、包装设备操作1. 检查包装设备的工作状态,确保设备正常运转。
2. 根据产品的包装要求,调整包装设备的参数,如包装速度、温度等。
3. 进行设备的清洁和消毒,确保符合卫生要求。
4. 检查包装材料的供应情况,如包装袋、标签等,及时补充。
四、包装流程1. 根据产品的包装要求,将产品放置在包装设备的进料口。
2. 包装设备自动进行包装操作,如称重、封口、贴标签等。
3. 检查包装过程中的异常情况,如封口不完整、标签贴错等,及时进行调整和修正。
4. 定期对包装设备进行维护和保养,确保设备的正常运转。
五、质量检验1. 从包装流程中抽取样品,进行质量检验。
2. 根据产品的质量标准,对样品进行外观、尺寸、分量等方面的检测。
3. 记录检验结果,并进行统计和分析,及时发现并解决质量问题。
六、包装记录1. 在包装过程中,记录关键环节的数据,如包装开始时间、结束时间、包装员工等。
2. 记录包装设备的运行情况,如设备故障、维修情况等。
3. 记录质量检验的结果和相关数据,如合格率、不合格品数量等。
4. 对包装记录进行归档和保存,以备日后查阅和追溯。
七、安全注意事项1. 包装车间的工作人员必须穿戴符合要求的工作服和防护用具。
2. 在操作包装设备时,注意安全操作规程,避免发生事故。
3. 定期进行安全培训,提高员工的安全意识和应急处理能力。
4. 对包装车间进行定期的安全检查,及时消除安全隐患。
八、总结包装车间操作流程是确保产品包装质量的重要环节。
包装过程检验管理流程

名称
包装过程检验管理流程
编码
受控状态
执行核心部门
包装课
控制部门
品质部
行为实施环节
包装车间
IPQC巡检员
包装车间课长
品质部
工程部
管理
行为
YES
不合格品返工
填写首检记录
填写巡检记录
发现问题反馈
外部
问题
发现
问题
反馈
相关说明
关键控制点:
1包装检验员在收到生产车间所送的首检通知单后,在5分钟到达现场,依据<检验标准><订单要求>对其检验;A.材料错误立即停止生产;B.包装异常现场指导立即改善才可生产;
2A.品管员按抽检频率进行巡检,15分钟巡回一次,30分钟记录一次。100%检验。B.有异常时,标识、隔离、写异常报告、追踪处理结果、归档。[包装全检]
3检验员填写纠正预防措施表,并指定分发责任部门,在异常发生后,40分钟内完成分发此表。
4生产车间课长分析发生原因、现场处理、预防措施,并呈报相关部门,当日处理完毕将处理信息反馈给品质部。检验员将纠正结果与改善效果上报品质部。
5品质检验员进行终检判定合格情况,并记录;不合格登记报废情况记录;合格后盖章确认入成品库;
表格:[质量信息反馈单]、[检验记录]、[异常反馈处理汇总]编制人员审核人员Fra bibliotek批准人员
编制日期
审核日期
批准日期
- 1、下载文档前请自行甄别文档内容的完整性,平台不提供额外的编辑、内容补充、找答案等附加服务。
- 2、"仅部分预览"的文档,不可在线预览部分如存在完整性等问题,可反馈申请退款(可完整预览的文档不适用该条件!)。
- 3、如文档侵犯您的权益,请联系客服反馈,我们会尽快为您处理(人工客服工作时间:9:00-18:30)。
包装车间质量检验流程集团标准化小组:[VVOPPT-JOPP28-JPPTL98-LOPPNN]
包装车间质量检验流程
一、目的
配合公司质量文件要求,根据包装车间质量控制要求,确保包装车间各项质量检验得到有效控制
二、适用范围
本程序适合包装车间的原材料、半制品、成品木箱的检验
三、内容
1、原材料检验
1.1生产部包装车间仓管员接收外协单位的《送货清单》,确认物料已送货到公司包装厂
无误后,将《送货清单》移交包装厂来料检验质检员,要求质检员对清单所列货物做出检验;
1.2来料检验质检员接收清单后,按清单所列物料的品种、数量,从质检资料中找到相应
的检验程序和相关检验图纸,按照检验程序和检验图纸要求以及抽检比例检验物料;
1.3来料检验质检员在检验过程中,应及时填写《来料检验报告》,《来料检验报告》中
的各项检验项目和检验记录数据不能遗漏,记录字体应清晰,使用单位应符合检验程序文件或检验图纸的要求(单位相同或符合国际通用使用单位标准);
1.3.1新版《来料检验报告》未制定完成前,暂时仍使用目前现有的《五金类——来料检
验报告》、《夹板——来料检验报告》、《木方、木板——来料检验报告》、《防水布——来料检验报告》;
1.4来料检验质检员检验完物料后,应尽可能在10分钟内按照检验资料的标准判断供应商
所送物料是否符合质量要求,判断后应立即将《来料检验报告》交质检小组负责人再次评估;
1.5质检小组负责人应尽快对《来料检验报告》确认(以不影响来料货物接收为宜);
1.5.1评估结果合格,将《来料检验报告》交回来料检验质检员,质检员即时将《来
料检验报告》的相关结果反馈仓管员;
1.5.2对不能根据检验标准判断的物料,质检小组负责人应立即向资料编制人或工艺
小组人员反馈,会同工艺人员即时对物料做出评估;
1.5.3如仍不能对物料进行有效的判断,应立即向本部门领导反映情况;
1.6本部门领导应视乎情况和生产需求,及时对问题做出处理,处理结果应及时反馈质检
小组负责人;
1.7来料检验质检员收到质检小组负责人反馈后,应即时向仓管员反馈,《来料检验报
告》其中一联应归档存放;
1.8仓管员接收到《来料检验报告》,应即时依据《来料检验报告》结果,按《来料接收
程序》对来料进行处理;
1.9来料检验质检员应在仓管员接收完物料后,对物料的每一堆垛贴上“合格”、“让步
接收”标识;
1.10具体操作流程可参见附表《原材料检验流程图》;
2、生产过程检验
2.1生产班组人员对本工序已完工产品应按车间生产图纸或工艺要求进行自检,自检分为首检和批检,首检指操作者最先加工的一定数量的产品进行检查,批检指操作者完成一定数量的加工产品并形成一个批次后的检查,自检合格后的产品方可流到下一生产工序;
2.1.1不合格产品应即时在本岗位进行反修,对不合格产品应按《车间工序不合格产品处理程序》进行处理;
2.1.2对于工序中要求需质检人员检验确认的产品,生产班组人员应填写《半制品质检报检单》,交生产车间质检员进行检验;
2.2车间质检员对生产工序人员提交的《半制品质检报检单》应及时进行检验(以不影响生产为宜);
2.2.1检验时应按照产品的生产工艺要求或生产图纸进行检验,检验过程中应及时填写《半制品质检报检单》,《半制品质检报检单》中的各项检验项目和检验记录数据不能遗漏,记录字体应清晰,使用单位应符合检验程序文件或检验图纸的要求(单位相同或符合国际通用使用单位标准);
2.2.2车间质检员应有足够的能力判断半制品是否符合质量要求,并能独立处理车间半制品质检工作,无需报质检小组负责人决定;
2.2.3检验后应对已检验物料贴上“合格”、“不合格”、“让步接收”标识,《半制品质检报检单》应归档存放;
2.3生产过程检验中如发现重大不合格或连续两批次不合格,车间质检员应及时发出《纠正和预防措施控制要求通知》,要求相关责任班组整改,具体参见《纠正措施控制程序》;
2.4具体操作流程可参见《生产过程检验流程图》
3、部件成品检验
3.1生产班组人员对已完工部件成品应按车间生产图纸和工艺要求进行自检(此自检定义为批检);
3.1.1不合格产品应即时在本岗位进行反修,对不合格产品应按《车间工序不合格产品处理程序》进行处理;
3.2自检合格部件成品应填写《部件成品质检报检单》,填写完毕后交车间质检员进行检验;
3.3车间质检员对生产工序人员提交的《部件成品质检报检单》应及时进行检验(以不影响生产为宜);
3.3.1检验时应按照产品的生产工艺要求或生产图纸进行检验,检验过程中应及时填写《部件成品质检报检单》,《部件成品质检报检单》中的各项检验项目和检验记录数据不能遗漏,记录字体应清晰,使用单位应符合检验程序文件或检验图纸的要求(单位相同或符合国际通用使用单位标准);
3.3.2车间质检员应有足够的能力判断半制品是否符合质量要求,并能独立处理车间半制品质检工作,无需报质检小组负责人决定;
3.3.3检验后应对已检验物料贴上“合格”、“不合格”、“让步接收”标识,《部件成品质检报检单》应归档存放;
3.4部件成品检验中如发现重大不合格或连续两批次不合格,车间质检员应及时发出《纠正和预防措施控制要求通知》,要求相关责任部门整改,具体参见《纠正措施控制程序》;
3.5具体操作流程可参见《部件成品检验流程图》;
4、拼装木箱成品检验
4.1拼装人员(包括客户厂的我司人员)对已完工木箱成品应按生产图纸和工艺要求进行自检(此自检定义为每一个木箱成品);
4.1.1不合格产品应即时在本岗位进行反修;不能反修成品应即时通知当班主管;当班主管应即时对木箱成品做出是否更换决定,并通知我司包装厂负责人增加生产计划;
4.2自检合格部件成品如在我司包装厂拼装,即按本程序中程序第4部份执行,如拼装在客户厂,则应按客户厂的质检程序执行;
4.3对于在客户厂拼装的木箱成品,生产车间质检小组外协质检员应定时及不定时对木箱成品进行抽检,抽检的检验单按《部件成品质检报检单》书写;
4.4成品木箱检验的《部件成品质检报检单》应归类存档;
4.5成品木箱检验中如发现重大不合格或连续两批次不合格,质检小组外协质检员应及时发出《纠正和预防措施控制要求通知》,要求相关责任部门整改,具体参见《纠正措施控制程序》;
4.6包装厂应及时跟踪客户厂对于我司拼装木箱的质量检验情况;及时跟进客户厂提出的质量问题处理,并对问题归类存档;
4.7对客户厂提出的质量问题,执行本程序的
5.5规定;
4.8具体操作流程可参见《木箱成品检验流程图》;
5、质检抽样方法
5.1质检抽样方法采用美国军用标准MIL-STD-105E方法抽样,一般检查水平Ⅱ级标准抽取样品,具体标准参见附表《批次性抽样样本代字表》、《批次性减量检验单次抽样计划表》、《批次性正常检验单次主抽样计划表》;
5.2比较质量AQL值(以AQL值评定批次检验的结果:合格/不合格):
致命缺陷(Critical) 0
严重缺陷(Major)……………………………… 1.5
轻微缺陷(Minor)……………………………… 4.0致命缺陷:对产品功能、安全产生严重影响或如存在质量问题可能对人体安全产生隐患的检查项目;
严重缺陷:对产品功能、安全、外观产生较严重影响的检查项目;
轻微缺陷:对产品功能、外观只产生轻微影响的检查项目;。