注塑模具设计综述.doc
模具注塑总结报告范文(3篇)

第1篇一、前言随着我国制造业的快速发展,模具注塑技术在汽车、电子、家电、医疗等领域得到了广泛应用。
作为一名模具注塑行业的从业者,我在此对模具注塑技术进行总结,旨在为同行提供参考和借鉴。
二、模具注塑技术概述1. 模具注塑技术定义模具注塑技术是一种将塑料原料在高温、高压下注入模具腔内,冷却固化后得到所需形状和尺寸的塑料制品的加工方法。
该技术具有生产效率高、精度高、成本低、适用范围广等优点。
2. 模具注塑技术分类根据模具材料、注塑工艺、塑料制品类型等因素,模具注塑技术可分为以下几类:(1)按模具材料分类:金属模具、塑料模具、复合材料模具等。
(2)按注塑工艺分类:热塑性塑料注塑、热固性塑料注塑、反应性塑料注塑等。
(3)按塑料制品类型分类:日用品、汽车零部件、电子产品、医疗器械等。
三、模具注塑技术要点1. 模具设计(1)结构设计:确保模具结构合理、强度高、易于维修和更换。
(2)尺寸精度:保证模具尺寸精度,提高塑料制品的尺寸精度。
(3)冷却系统:合理设计冷却系统,保证塑料制品的冷却速度和质量。
(4)排气系统:设计合理的排气系统,防止塑料制品出现气泡、缩痕等缺陷。
2. 注塑工艺(1)塑料原料选择:根据塑料制品的性能和用途选择合适的塑料原料。
(2)温度控制:合理控制注塑机的温度,保证塑料制品的质量。
(3)压力控制:根据塑料制品的尺寸和形状,调整注塑机的压力,保证塑料制品的密度和强度。
(4)速度控制:根据塑料制品的性能和用途,调整注塑机的速度,保证塑料制品的质量。
3. 模具制造(1)模具材料选择:根据模具的使用寿命、精度和成本等因素,选择合适的模具材料。
(2)模具加工:采用先进的加工设备和技术,保证模具的精度和表面质量。
(3)模具装配:确保模具各部件装配准确,提高模具的使用寿命。
四、模具注塑技术发展趋势1. 模具设计智能化随着计算机技术的不断发展,模具设计正向智能化、数字化方向发展。
利用CAD/CAM/CAE等软件,可以快速、准确地完成模具设计。
塑料盒注塑模设计概述(doc 36页)
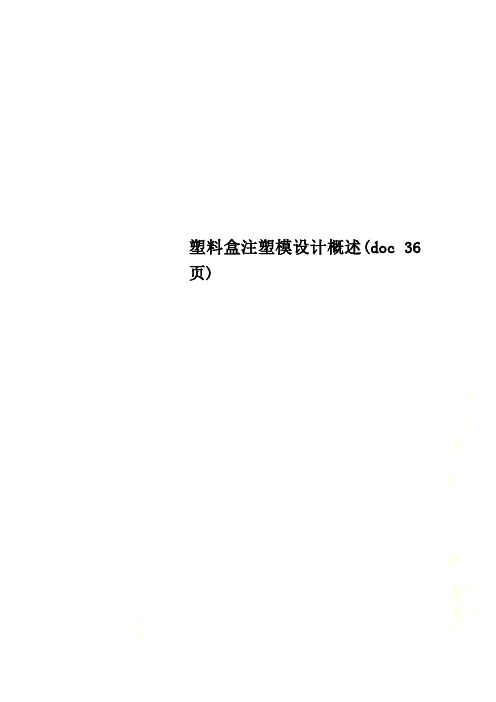
塑料盒注塑模设计概述(doc 36页)塑料盒注塑模设计摘要本课题主要是设计给定的塑料盒子的注塑模,通过对塑件进行工艺的分析和比较,最终设计出一副能生产出符合要求的制件的注塑模。
结合塑件的结构特点,纵观整个模具结构,对模具的浇注系统、排气系统、推出及复位机构等进行了详细的设计和说明,对注塑机进行了慎重选择和认真校核,并对侧型芯的推出及复位机构进行了重点设计说明。
盒子结构简单,精度一般,但是盒子有内缘使模具的结构变得复杂,零件相应增多。
为缩短模具制造周期,在设计过程中选用了大量标准件,个别标准件需经再加工,这在装配要求中有详细说明。
关键词:塑料盒子,模具,侧型芯,注射机目录前言 (1)第1章塑料注射模具的设计步骤和结构组成 (4)1.1 塑料注射模具的设计步骤及内容 (4)1.1.1 任务书 (4)1.1.2 资料收集分析 (4)1.1.3 选择成型设备 (5)1.1.4 确定模具类型的主要结构方案 (5)1.1.5 绘制模具图 (5)1.2塑料注射模具的结构组成和作用 (6)第2章盒子塑料件 (8)2.1 塑料件的结构和特点 (8)2.2 塑料件的材料 (8)2.2.1 塑料简介 (8)2.2.2 塑料的成型工艺特点 (9)2.2.3 工程塑料(ABS)的特性及注射工艺性 (10)2.2.4材料ABS的注射成型过程及工艺参数 (12)2.3盒子塑料件的参数 (13)第3章注射机的选用 (14)3.1 选用注射机的方法和原则 (14)3.2 注射机的种类和应用范围 (14)3.3注射机的选用 (15)3.3.1 注射机的初步选定: (15)3.3.2 注射机的参数校核 (16)第4章塑料注射模具设计 (18)4.1 型腔数目和分型面的选择 (18)4.2 型芯和型腔 (18)4.2.1 型芯和型腔的结构 (18)4.2.2型芯和型腔的成型部分尺寸 (19)4.2.3 侧抽芯的设计 (21)4.3浇注系统 (22)4.3.1浇注系统的作用与组成 (22)4.3.2浇注系统的设计 (22)4.4推出机构 (23)4.4.1 推出机构的作用和种类 (23)4.4.2制件推出机构的设计 (24)4.4.3侧型芯推出机构的设计 (25)4.5导向机构 (26)4.5.1导向机构的作用和组成 (26)4.5.2导柱、导套的选用 (26)4.6冷却和排气系统 (27)4.6.1 冷却系统 (27)4 .6.2排气系统 (27)4.7 模架的设计 (28)4.8注射模的设计结果参数 (31)4.9模具的装配过程与工作过程 (31)4.9.1模具的装配 (31)4.9.2模具工作过程 (31)结论 (33)谢辞 (34)参考文献 (35)前言当今社会是一个高速发达,极速变化的社会,一切都以“快”为原则。
可视化注塑模具设计【文献综述】

毕业设计开题报告机械设计制造及自动化可视化注塑模具设计一、前言1.1工程背景人类社会的进步与材料的使用密切相关。
其中塑料是20世纪才发展起来的一类新型材料,是高分子材料中最大的一类,由于塑料具有品种多、性能各具特色、适应性广等优点,而且生产塑料所消耗的能量低,因此塑料工业的发展保持着旺盛的势头。
目前,注塑成型技术己经广泛的应用到了塑料制品的生产中[1],其中占很大比例的塑料制品是采用此项技术制成的。
虽然注塑成型技术已经是一项比较成熟的技术,但是随着注塑制品在家电、汽车等高科技领域的应用,对制品的质量、性能及产品更新换代提出了更高的要求。
但是高质量高精度高灵敏度的严格要求成为阻止塑料制品快速进入这些高尖领域的限制和束缚,如何提高注塑制品质量和性能成为该领域的重要研究课题。
注塑成型过程是一个高度非线性、时变性的多参数作用过程。
由于此过程具有多个参数相互作用并随时间变化的特性,所以每个参数对最后制件质量的优劣都具有不同程度的影响。
为了减少最终制件的质量缺陷、提高生产质量,需要对整个成型周期中工艺参数的值进行检测控制,使对最终制件质量影响较大的工艺参数值能保持在最佳的工艺窗口内,从而确保最终制件质量达到最优[2]。
高分子材料的成型方法主要有挤出成型、注塑成型、吹塑成型、压延成型、压制成型等,其中,注塑成型因可以生产和制造形状较为复杂的制品、易于与计算机技术结合、易于实现自动化生产等优点,在高分子材料的成型加工中占有极其重要的位置[3]。
注塑成型可以一次成型结构复杂的制品,应用很广[4],但由于材料、成型工艺、模具设计、制品设计及设备等各方面的影响,注塑制品常会出现各种表观缺陷,如:填充不足、凹陷与缩痕、变色与暗纹、熔接痕、银丝与剥层、乱流纹与喷射痕、无光泽与光泽不均匀、翘曲变形、表面划伤与龟裂等[5]。
1.2可视化技术概述可视化技术,是指对于高分子材料的实际成型过程,由固体到熔融态、混炼和分散举动、熔体冷却成型等全过程都可直接观察的一项研究方法。
注塑模具设计总结
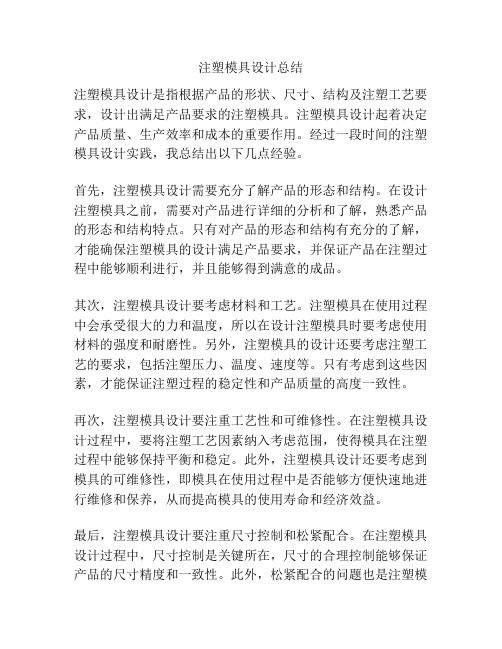
注塑模具设计总结注塑模具设计是指根据产品的形状、尺寸、结构及注塑工艺要求,设计出满足产品要求的注塑模具。
注塑模具设计起着决定产品质量、生产效率和成本的重要作用。
经过一段时间的注塑模具设计实践,我总结出以下几点经验。
首先,注塑模具设计需要充分了解产品的形态和结构。
在设计注塑模具之前,需要对产品进行详细的分析和了解,熟悉产品的形态和结构特点。
只有对产品的形态和结构有充分的了解,才能确保注塑模具的设计满足产品要求,并保证产品在注塑过程中能够顺利进行,并且能够得到满意的成品。
其次,注塑模具设计要考虑材料和工艺。
注塑模具在使用过程中会承受很大的力和温度,所以在设计注塑模具时要考虑使用材料的强度和耐磨性。
另外,注塑模具的设计还要考虑注塑工艺的要求,包括注塑压力、温度、速度等。
只有考虑到这些因素,才能保证注塑过程的稳定性和产品质量的高度一致性。
再次,注塑模具设计要注重工艺性和可维修性。
在注塑模具设计过程中,要将注塑工艺因素纳入考虑范围,使得模具在注塑过程中能够保持平衡和稳定。
此外,注塑模具设计还要考虑到模具的可维修性,即模具在使用过程中是否能够方便快速地进行维修和保养,从而提高模具的使用寿命和经济效益。
最后,注塑模具设计要注重尺寸控制和松紧配合。
在注塑模具设计过程中,尺寸控制是关键所在,尺寸的合理控制能够保证产品的尺寸精度和一致性。
此外,松紧配合的问题也是注塑模具设计中需要注意的重要问题,合理的松紧配合能够防止模具在使用过程中的松动和变形。
总之,注塑模具设计是一个复杂的工程,需要综合考虑产品的形态、材料、工艺等因素。
只有全面考虑这些因素,才能设计出满足产品要求的注塑模具,保证产品质量和生产效率。
在注塑模具设计过程中,还需要不断总结经验,不断提高设计水平,以适应不断变化的市场需求和技术发展。
注塑模具-文献综述格式模板

说明1.根据学校《毕业设计(论文)工作暂行规定》,学生必须撰写毕业设计(论文)文献综述。
文献综述作为毕业设计(论文)答辩委员会对学生答辩资格审查的依据材料之一。
2.文献综述应在指导教师指导下,由学生在毕业设计(论文)工作前期内完成,由指导教师签署意见并经所在专业教研室审查。
3.文献综述各项内容要实事求是,文字表达要明确、严谨,语言通顺,外来语要同时用原文和中文表达。
第一次出现缩写词,须注出全称。
4.学生撰写文献综述,阅读的主要参考文献应在10篇以上(土建类专业文献篇数可酌减),其中外文资料应占一定比例。
本学科的基础和专业课教材一般不应列为参考资料。
5.文献综述的撰写格式按毕业设计(论文)撰写规范的要求,字数在2000字左右。
文献综述应与开题报告同时提交。
毕业设计(论文)文献综述第2章主题部分(居中小二黑体)(段前1行,段后0.5行) (说明:主题是综述主要内容的叙述部分。
一般要叙述所选研究题目的国内外研究现状;本研究至目前的主要他人研究成果;比较各种学术观点,阐明本研究的发展趋势;目前存在的问题。
对当前工作的现状,今后的发展趋势应作重点、详尽而具体地叙述。
)(格式参照第1章)下面为表、图的排版要求:表2-1 HDPE的主要性能指标(五号宋体)(表内字小五号宋体)密度/(g/cm3) 0.941~0.965 屈服强度/MPa 22~30 体积质量/( cm3/ g) 1.03~1.06 拉伸强度/MPa 27吸水率24h/(%) <0.01 拉伸弹性模量/GPa 0.84~0.95玻璃化温度/℃-120~-125 抗弯强度/MPa 27~40熔点/℃105~137 弯曲弹性模量/GPa 1.1~1.4 计算收缩率/(%) 1.5~3.0 抗压强度/MPa 22比热容/(J/(kg·K) 2310 抗剪强度/MPa —注:表要求绘制,不允许剪贴图2-1 原始铝合金磨痕形貌(五号宋体)毕业设计(论文)文献综述。
灯罩注塑模设计-文献综述

毕业设计(论文)文献综述(包括国内外现状、研究方向、进展情况、存在问题、参考依据等)注塑模设计1. 国内外研究现状注塑模具是生产各种工业产品的重要工艺装备,随着塑胶模具设计工业的迅速发展以及塑胶制品在航空、航太、电子、机械、船舶和汽车等工业部门的推广应用,产品对模具的要求越来越高,传统的塑胶模具设计方法已无法适应产品更新换代和提高质量的要求。
电脑辅助工程(CAE)技术已成为塑胶产品开发、模具设计及产品加工中这些薄弱环节的最有效的途经。
美国上市公司 Moldflow 公司是专业从事注塑成型CAE 软体和谘询公司,自 1976 年发行了世界上第一套流动分析软体以来,一直主导塑胶成型CAE软体市场。
近几年,在汽车、家电、电子通讯、化工和日用品等领域得到了广泛应用。
利用 CAE 技术可以在模具加工前,在电脑上对整个注塑成型过程进行类比分析,准确预测熔体的填充、保压、冷却情况,以及制品中的应力分布、分子和纤维取向分布、制品的收缩和翘曲变形等情况,以便设计者能尽早发现问题,及时修改制件和模具设计,而不是等到试模以後再返修模具。
这不仅是对传统塑胶模具的设计方法一次突破,而且对减少甚至避免模具返修报废、提高制品质量和降低成本等,都有着重大的技术经济意义。
塑胶模具设计不但要采用 CAD 技术,而且还要采用 CAE 技术。
这是发展的必然趋势。
注塑成型分两个阶段,即开发/设计阶段(包括产品设计、模具设计和模具制造)和生产阶段(包括购买材料、试模和成型)。
传统的注塑方法是在正式生产前,由于设计人员凭经验与直觉设计模具,模具装配完毕後,通常需要几次试模,发现问题後,不仅需要重新设置工艺参数,甚至还需要修改塑料模具设计制品和塑胶模具的设计,这势必增加生产成本,延长产品开发周期。
2.研究方向基于注塑模具制造的特点,对注塑模具制造业提出了相应的要求。
当前模具制造的研究方向主要表现为以下五个方面:2.1从一般的机加工方法,发展至采用光机电相结合的数控电火花成形、数控电火花线切割以及各种特殊加工相结合,例如电铸成形、粉末冶金成形、精密铸造成形、激光加工等。
注塑成型模具设计
注塑成型模具设计注塑成型模具设计是一项非常关键的技术工作,对于提高注塑成型产品的质量和生产效率具有重要意义。
本文将从模具设计的基本原理、设计过程、常见问题和解决方法等几个方面进行详细介绍,以帮助读者更好地理解注塑成型模具设计。
注塑成型模具设计的基本原理是根据产品的形状、尺寸和材料等要求,设计出具有一定刚度和精度的模具,以保证产品的质量和精度。
模具设计的主要目标是尽量减小产品的成本,提高生产效率和模具的使用寿命,同时保证产品的质量。
1.产品分析:根据客户提供的产品要求,对产品的形状、尺寸、功能、材料等进行分析,确定好模具设计的基本要求。
2.模具结构设计:根据产品的形状和尺寸等要求,确定好模具的结构,包括型腔、型芯、定位、顶针、导柱等。
3.模具零件设计:根据模具结构设计的结果,设计出各个零件的尺寸和形状等细节,并确定好材料和加工工艺等要求。
4.模具装配设计:根据模具零件的尺寸和形状,进行模具的装配设计,包括模腔、模芯的装配,以及各个零件的定位、固定等。
5.模具试制和调整:根据模具设计的结果,进行模具的试制和调整,包括模具的制造、装配和调试,以及对产品的抽样检测和调整。
在注塑成型模具设计的过程中,常见的问题和解决方法有以下几个方面:1.塑料材料选择问题:根据产品的要求,选择合适的塑料材料,考虑材料的流动性、收缩率、强度等因素。
2.注塑工艺参数设置问题:根据塑料材料的特性和产品的要求,确定好注塑工艺参数,包括注射压力、注射速度、保压时间等。
3.模具加工工艺问题:根据模具设计的结果,选择合适的加工工艺,包括铣削、电火花、线切割等工艺,以保证零件的质量和精度。
4.模具结构设计问题:根据产品的要求,设计合理的模具结构,包括型腔、型芯、定位、顶针、导柱等,以提高模具的使用寿命和生产效率。
5.模具通道设计问题:针对注塑成型中塑料流动性的要求,设计合适的模具通道,以保证产品的成型质量和产能。
总之,注塑成型模具设计是一项复杂的工作,需要综合考虑产品的形状、尺寸和材料等要求,设计出具有合理结构和良好性能的模具,以提高注塑成型产品的质量和生产效率。
高达玩具造型及其注塑模具设计文献综述
浙江理工大学本科毕业设计(论文)文献综述报告班级姓名课题名称XXXG-01D高达模型足部造型及其注塑模具设计文献综述(内容包括国内外本课题及相关研究现状、分析及参考文献目录,字数不少于2000字)目录1国内外塑料行业发展现状浅析2国内外塑料模具行业发展现状3现代模具设计与制造的发展现状及趋势4 CAD软件在注塑模具行业应用5高达玩具模型简介参考文献(报告全文附后)指导教师审批意见签名:年月日注塑模具设计文献综述1 国内外塑料行业发展现状浅析塑料是以高分子聚合物为主要成分,并在加工为制品的某阶段可流动成型的材料。
塑料具有特殊的物理力学性能和化学稳定性能,以及优良的成型加工性能[1]。
塑料工业是新兴的工业,塑料作为一种新的工程材料,发展势头极其迅猛,跻身于金属、纤维材料和硅酸盐三大材料之列,已经广泛用于工业和日常生活。
因此,塑料的加工和成型工艺越来越得到重视,新技术、新工艺不断涌现。
目前,塑料成型种类包括注射成型、压铸成型、吸塑成型、吹塑成型、发泡成型、挤压成型等,其中注射成型是最常用的方法,几乎所有的塑料都可以注射成型[2]。
塑料制品行业是中国轻工业中近几年发展速度较快的行业之一,增长速度一直保持在10%以上。
据中国轻工业信息中心统计,2004 年中国塑料制品全部国有和年产品销售收入达到500 万元的非国有独立核算工业企业9473家[3]。
2 国内外塑料模具行业发展现状2、1我国模具发展基本情况我国模具生产最为集中的地区在珠三角和长三角地区,约占全国模具总产值的三分之二以上,模具发展有力地支持着这两个地区工业的快速发展。
从1999年至2009年产值从250亿元增长到979.45亿元,年均增长率在14.8%;进口从9.8274亿美元增至19.64亿美元;出口从1.328亿美元增至18.43亿美元;进口:出口从6.6:1跌至1.06:1。
表明了我国模具工业总产值呈逐年递增趋势,模具进口金额的增幅有逐年下降的趋势,出口比例逐年加大,同时反映我国模具任是供不应求的状态,仍为世界上模具年进口量较大的国家[4]。
注塑模具文献综述
毕业设计(论文)文献综述注塑模具的现状与发展趋势综述1 塑料制品发展概况塑料制品是采用塑料为主要原料加工而成的生活用品、工业用品的统称。
塑料的出现给人类带来了极大地便利,由于其有成本低廉、抗腐蚀能力强、可塑眭强、还可用于制备燃料油和燃料气,降低原油消耗等无可替代的优点,自发明之日起就广受欢迎,随着加工工艺的进步和技术的突破,塑料制品渗透进我们生活的方方面面,成为最重要的必需品[ 1 ]。
根据中国塑料加工工业协会统计数据,我国塑料制品行业塑料用量从2006 年的2802 万吨快速增长到2012 年的5782 万吨。
2013 年1 月~12 月,我国塑料制品行业累计完成产量6188 万吨。
在“十二五”期间,我国塑料产业要推进产业结构优化升级,努力提高产业技术水平,使塑料制品总产量的年增长率为13-15%。
2015年,预计塑料制品总产量可达到8000万吨。
塑料模具工业近20年来发展十分迅速,早在7年前塑料的年产量按体积计算已经超过钢铁和有色金属年产量的总和,塑料制品在汽车、机电、仪表、航天航空等国家支柱产业及与人民日常生活相关的各个领域中得到了广泛的应用。
近年来,人们对各种设备和用品轻量化及美观和手感的要求越来越高,这就为塑料制品提供了更为广阔的市场。
塑料制品要发展,塑料模具是塑料零部件及其制品行业的重要支撑装备,那么必然要求塑料模具随之发展。
绝大部分塑料制品的成型都依赖于塑料模具,因此塑料制品行业的快速发展对塑料模具行业形成了旺盛的市场需求。
尤其是近年来,我国汽车、家电等主机行业快速发展,产能持续增加,同时随着技术进步,塑料零部件使用比例持续上升,直接推动了我国塑料模具行业的快速发展。
塑料制品成形的方法虽然很多,其主要方法是注射、挤出、压制、压铸和气压成型等,但最主要的方法是注塑成形,世界塑料模具市场中塑料成形模具产量中约半数以上是注塑模具,而其中注射模约占成型总数的60%以上。
由于塑料产品应用前景可观,更新换代较快,也就要求注塑模也应跟上时代发展的步伐。
高达玩具造型及其注塑模具设计文献综述
高达玩具造型及其注塑模具设计文献综述高达玩具是指以日本动画片《高达》为主题的模型玩具。
自从1979年首次推出以来,高达玩具一直深受全球年轻人的喜爱。
高达玩具的独特之处在于其精细的造型和注塑模具设计,这使得它成为收集家和模型爱好者的心头好。
本文综述了高达玩具造型及其注塑模具设计方面的文献,以帮助读者了解该领域的最新研究动态。
第一部分:高达玩具造型文献综述在高达玩具的造型设计方面,许多研究都集中在如何还原原型中的细节和比例。
例如,研究人员通过使用三维建模技术和数控加工设备,能够忠实地还原高达机器人的细节和比例。
这些研究为高达玩具的制造提供了技术支持,使得玩具的造型更加精细和真实。
此外,还有许多研究集中在高达玩具的关节设计方面。
高达玩具的关节设计直接影响到玩具的可动性和稳定性。
因此,研究人员尝试设计出更加复杂和可靠的关节系统,以提高高达玩具的可玩性和耐用性。
这些研究不仅改善了高达玩具的购买者体验,还为玩具制造商提供了设计参考。
此外,还有一些研究关注高达玩具的材质选择和表面处理。
高达玩具通常由塑料制成,所以研究人员试图选择合适的材料,以实现玩具的强度和耐用性要求。
同时,一些研究还探索了不同种类的表面处理技术,以增加玩具的质感和附加值。
这些研究为高达玩具的材料和工艺选择提供了指导。
在高达玩具的注塑模具设计方面,有许多研究集中在生产效率和质量控制方面的问题。
注塑模具的设计直接影响到高达玩具的生产效率和质量。
因此,研究人员尝试设计出更加高效和精确的注塑模具,以提高玩具的生产效率和质量。
此外,一些研究还探索了使用快速成型技术在高达玩具注塑模具设计中的应用。
快速成型技术使得设计人员能够快速制造出模型和样品,以验证设计方案的可行性。
这些研究为高达玩具的注塑模具设计提供了一个更加灵活和高效的方法。
此外,还有一些研究关注注塑模具的优化和仿真技术。
优化和仿真技术可以帮助设计人员预测注塑过程中的问题,如热应力、变形等,并提供改进方案。
- 1、下载文档前请自行甄别文档内容的完整性,平台不提供额外的编辑、内容补充、找答案等附加服务。
- 2、"仅部分预览"的文档,不可在线预览部分如存在完整性等问题,可反馈申请退款(可完整预览的文档不适用该条件!)。
- 3、如文档侵犯您的权益,请联系客服反馈,我们会尽快为您处理(人工客服工作时间:9:00-18:30)。
第 1 章注塑模具设计综述随着塑料制品日益广泛的应用,在注塑成型过程中起着重要作用的模具越来越受到重视。
除了塑料制品的表面质量、成型精度完全由模具决定之外,塑料制品的内在质量、成型效率也受模具的控制,所以如何高质量,简明、快捷和规范化地设计注塑模具,成为发挥注塑成型工艺优越性、扩大注塑制品应用的首要问题。
在本章中将介绍注塑模具的组成、类型和设计程序等方面的内容。
1.1注塑模具的结构组成注塑模具由动模和定模两部分组成,动模安装在注塑成型机的移动模板上,定模安装在注塑机的固定模板上。
在注塑成型时动模和定模闭合构成浇注系统和型腔。
开模时动模与定模分离以便取出塑料制品。
图 1-1 所示为典型的单分型面注塑模具结构,根据模具中各个部件所起的作用,一般可将注塑模具分为以下几个基本组成部分。
1—定位圈; 2—主流道衬套;3—定模座板; 4—定模板; 5—动模板; 6—动模板; 7—动模底座; 8—推出固定板;9—推板; 10—拉料杆; 11—推杆; 12—导柱; 13—型芯(凸模); 14—凹模; 15—冷却水通道图 1-1成型部件:成型部件由型芯和凹模组成。
型芯形成制品的内表面形状,凹模形成制品的外表面形状。
合模后型芯和凹模便构成了模具的型腔,该模具型腔由件 13 和件 14 组成。
按工艺和制造要求,有时型芯或凹模由若干拼块组成,有时做成整2Pro/ENGINEER 中文野火版 2.0 教程——塑料模具设计体,仅在易损坏、难加工的部件采用镶件。
浇注系统:浇注系统又称为流道系统,它是将塑料熔体由注塑机喷嘴引向型腔的一组进料通道,通常由主流道、分流道、浇口和冷料穴组成。
浇注系统的设计十分重要,它直接关系到塑件的成型质量和生产效率。
导向部件:为了确保动模与定模合模时能准确对接,在模具中必须设置导向部件。
在注塑模中通常采用四组导柱与导套来组成导向部件,有时还需在动模和定模上分别设置互相吻合的内、外锥面来辅助定位(第 6.3 节中会详细讲解)。
为了避免在制品推出过程中推板发生歪斜现象,一般在模具的推出机构中还设有使推板保持水平运动的导向部件,如导柱和导套。
推出机构:在开模过程中,需要有推出机构将塑件及其在流道内的凝料推出或拉出。
如图1-1 所示,推出机构由推杆11 和推出固定板8、推板 9 及主流道的拉料杆 10 组成。
推出固定板和推板夹持住推杆。
在推板中一般还固定有复位杆,复位杆在动模和定模合模时使推出机构复位。
调温系统:为了满足注塑工艺对模具温度的要求,需要有调温系统对模具的温度进行调节。
对于热塑性塑料用注塑模,主要是设计冷却系统使模具冷却。
模具冷却的常用办法是在模具内开设冷却通道,利用循环流动的冷却水带走模具的热量;模具的加热除可用冷却水通道引入热水或蒸汽外,还可在模具内部和周围安装电加热元件。
排气槽:排气槽用以将成型过程中的气体充分排除。
常用的方法是在分型面处开设排气沟槽。
由于分型面之间存在有微小的间隔,对于较小的塑件,因排气量不大,可直接利用分型面排气,不必开设排气沟槽,一些模具的推杆或型芯与模具的配合间隙均可起排气作用,有时可不必另外开设排气沟槽。
侧抽芯机构:有些带有侧凹或侧孔的塑件,在被推出以前必须先进行侧向分型,抽出侧向型芯后方能顺利脱模,此时需要在模具中设置侧抽芯机构。
1.2注塑模具分类及简介单分型面注塑模具又称为两板式模具,它是注塑模具中最简单、最常用的一类。
占全部注塑模具的七成,如图1-1 所示。
双分型面注塑模具以两个不同的分型面分别取出流道凝料和塑料件,与两板式的单分型面注塑模具相比,双分型面注塑模具在动模板与定模板之间增加了一块可以移动的中间板(又名浇口板),故称为三板式模具,如图1-2 所示。
带有活动镶件的注塑模具。
对于外形结构复杂的塑件,由于无法通过简单的分型从模具内取出塑料件,这时可在模具中设置活动镶件和活动的侧向型芯及板块(哈夫块),如图 1-3 所示。
带侧向分型抽芯的注塑模具。
当塑件上有侧孔或侧凹时,在模具内可设置出由斜销或斜滑块等组成的侧向分型抽芯机构,它能使侧型芯做横向移动,如图1-4所示。
第 1 章注塑模具设计综述31—定距拉板; 2—弹簧; 3—限位销; 4—导柱; 5—推件板; 6—动模板; 7—动模垫板; 8—模底座; 9—推板;10—推出固定板;11—推杆; 12—导柱; 13—中间板; 14—定模板; 15—主流道衬套图 1-21—定模板; 2—导柱; 3—活动镶件; 4—型芯; 5—动模板; 6—动模垫板;7—模底座; 8—弹簧; 9—推杆; 10—推出固定板;11—推板图 1-3自动卸螺纹的注塑模具。
当要求能自动脱卸内螺纹或外螺纹的塑件时,可在模具中设置转动的螺纹型芯或型环,这样便可利用机构的旋转运动或往复运动,将螺纹制品脱出,或者用专门的驱动和传动机构,带动螺纹型芯或型环转动,将螺纹制件脱出,如图 1-5 所示。
4Pro/ENGINEER 中文野火版 2.0 教程——塑料模具设计1—楔紧块; 2—斜销; 3—斜滑块; 4—型芯; 5—固定板; 6—动模垫板; 7—垫块; 8—动模座板; 9—推板;10—推出固定板;11—推杆; 12—拉料杆; 13—导柱; 14—动模板; 15—主流道衬套;16—定模板; 17—定位圈图1-41—螺纹型芯; 2—模座; 3—动模垫板;4—定距螺钉; 5—动模板; 6—衬套; 7—定模板图1-5推出机构设在定模的注塑模具。
由于制件的特殊要求或形状限制,制件必须要留在定模内,这时就应在定模一侧设置推出机构,以便将制品从定模内脱出。
定模第 1 章注塑模具设计综述5一侧的推出机构一般由动模通过拉板或链条来驱动,如图1-6 所示。
1—模底座; 2—动模垫板; 3—成型镶片; 4—螺钉; 5—动模; 6—螺钉; 7—推件板;8—拉板; 9—定模板; 10—定模座板; 11—型芯; 12—导柱图 1-6无流道凝料的注塑模具(简称为无流道注塑模具)。
通过采用对流道加热或绝热的办法来保持从注塑机喷嘴到浇口处之间的塑料保持熔融状态。
这样在每次注塑成型后流道内均没有塑料凝料,这不仅提高了生产率,节约了塑料,而且还保证了注塑压力在流道中的传递,有利于改善制件的质量。
此外,无流道凝料注塑模具还易实现自动化操作,如图1-7 所示。
1—动模座板; 2—垫块; 3—推板; 4—推出固定板;5—推杆; 6—动模垫板;7—导套; 8—动模板; 9—型芯; 10—导柱; 11—定模板; 12—凹模; 13—支架; 14—喷嘴;15—热流道板; 16—加热器孔道;17—定模座板; 18—绝热层; 19—主流道衬套;20—定位圈; 21—注塑机喷嘴图 1-76Pro/ENGINEER 中文野火版 2.0 教程——塑料模具设计1.3注塑模具设计的一般步骤1.确定型腔的数目确定型腔数目的方法的根据有锁模力、最大注塑量、制件的精度要求、经济性等,在设计时应根据实际情况决定采用哪一种方法。
2.选定分型面(又称PL 面)虽然在塑件设计阶段分型面已经考虑或者选定,在模具设计阶段仍应再次核对,从模具结构及成型工艺的角度判断分型面的选择是否最为合理。
3.确定型腔的配置型腔的配置实质上是模具结构总体方案的规划和确定。
因为一旦型腔布置完毕,浇注系统的走向和类型便已确定。
冷却系统和推出机构在配置型腔时也必须给予充分的注意,若冷却管道与推杆孔、螺栓发生冲突,要在型腔布置中进行协调,当型腔、浇注系统、冷却系统、推出机构的初步位置确定后,模板的外形尺寸基本上就已确定,从而可以选择合适的标准模架。
4.确定浇注系统浇注系统中的主流道、分流道、浇口和冷料穴的设计中,浇注系统的平衡及浇口位置和尺寸是浇注系统的设计重点。
另外,需要强调的是浇注系统决定了模具的类型,如采用侧浇口,一般选用单分型面的两板模即可,如采用点浇口,往往就需要选用双分型面的三板式模具,以便脱出流道凝料和塑料制件。
5.确定脱模方式在确定脱模方式时首先要确定制件和流道凝料滞留在模具的哪一侧,必要时要设计强迫滞留的结构(如拉料杆等),然后再决定是采用推杆结构还是推件板结构。
特别要注意确定侧凹塑件的脱模方式,因为当决定采用侧抽芯机构时,模板的尺寸就需要加大,在型腔配置时要留出侧抽芯机构的位置。
6.冷却系统和推出机构的细化冷却系统和推出机构的设计计算详见有关章节。
冷却系统和推出机构的设计同步进行有助于两者的很好协调。
7.确定凹模和型芯的结构和固定方式当采用镶块式凹模或型芯时,应合理地划分镶块并同时考虑到这些镶块的强度、可加第 1 章注塑模具设计综述7工性及安装固定。
8.确定排气方式由于在一般的注塑模中注塑成型时的气体可以通过分型面和推杆处的空隙排出,因此注塑的排气问题往往被忽视。
对于大型和高速成型的注塑模,排气问题必须引起足够的重视。
9.绘制模具的结构草图在以上工作的基础上绘制注塑模完整的结构草图,在总体结构设计时切忌将模具结构搞得过于复杂,应优先考虑采用简单的模具结构形式,因为在注塑成型的实际生产中所出现的故障,大多是由于模具结构复杂化所引起的。
结构草图完成后,若可能,应与工艺、产品设计及模具制造和使用人员共同研讨直至相互认可。
10.校核模具与注塑机有关的尺寸因为每副模具只能安装在与其相适应的注塑机上,因此必须对模具上与注塑机有关的尺寸进行校核,以保证模具在注塑机上正常工作。
11.校核模具有关零件的强度和刚度对成型零件及主要受力的零部件都应进行强度及刚度的校核。
一般而言,注塑模具的刚度问题比强度问题显得更重要一些。
12.绘制模具的装配图装配图应尽量按照国家制图标准绘制,装配图中要清楚地表明各个零件的装配关系,以便工人装配。
当凹模与型芯镶块很多时,为了便于测绘各个镶块零件,还有必要先绘制动模和定模部装图,在部装图的基础上再绘制总装图。
装配图上应包括必要的尺寸,如外形尺寸、定位圈尺寸、安装尺寸、极限尺寸。
在装配图上应将全部零件按顺序编号,并填写明细表和标题栏。
13.绘制模具零件图由模具装配图或部装图拆绘零件图的顺序为先内后外,先复杂后简单,先成型零件后结构零件。
14.复核设计图样应按制品、模具结构、成型设备、图纸质量、配合尺寸、零件的可加工性等项目进行自我校对或他人审核。
表 1-1 的模具设计检查表中列出了一般模具设计必须检查的事项和要点,读者可以参照,在实际设计工作中需要特别注意。
8Pro/ENGINEER中文野火版 2.0 教程——塑料模具设计表 1-1模具设计检查表工部号门产品名设计者客户日期□1.模穴数:()穴。
□2.塑料(),缩水率:()/1000。
□3.是否翻图。
□4.模具的分模面是否与客户要求的內容一致。
□□□5.模座的规格是否正确,规格为(6.模仁钢料为(),模座钢为()。