夹紧力计算 (2)
夹紧力计算

夹紧力的计算Mz=328.715Nm 转台径向转矩n=4 刹车片个数Mh=Mz/n 每个刹车片承受的摩擦力矩d=0.3 刹车位置到转台中心距离Fh=2*Mh/d 单个刹车片的摩擦力f=0.18 摩擦系数F=Fh/2/f 油压提供的法向力ds=0.030 油压作用面的直径s=pi*ds^2/4 油压作用面积P=F/s 油压求得P =2.1529e+006=2.1529MP4.1.2 百度夹紧力计算及夹紧气缸的设计1、夹紧力的计算工件材料为AS9U3,大平面加工余量为1.5mm,采用硬质合金端铣刀加工,切削力查参考文献〔1〕可根据如下公式计算:•式中:Fz ---铣削力(N)af---每齿进给量(mm/r) aw---铣削宽度(mm) KFZ---铣削力修正系数d0---铣刀外径(mm) ap---铣削深度(mm) z---•铣刀齿数确定各参数值:(1).铣刀外径d0=315mm;(2).铣刀齿数Z=16;(3).每齿进给量af是铣刀每转一个刀齿时铣刀对工件的进量:af=Vf/(z·n)=360/(16×720)=0.031mm/r(4).铣削深度ap对于端铣刀是指平行于铣刀轴线测量的被铣削层尺寸:ap=1.5mm(5). 铣削宽度aw对于端铣刀是指垂直于铣刀轴线测量的被切削层尺寸:aw=240mm(6). 修正系数KFZ取1.6;由表查得: cF=7750 xF=1.0 yF=0.75uF=1.1qF=1.3FFz=276.5N=28Kg(7). 理论所需夹紧力计算确定安全系数:总的安全系数k=k1·k2·k3·k4k1---- 一般安全系数;k1取1.7;k2----加工状态系数;由于是精加工,所以k2取1;k3----刀具钝化系数;k3取1.4;k4----断续切削系数;k4取1.2;∴k=1.7×1×1.4×1.2≈3W=k·p=3×28kg=84kg 2. 气缸的选择Q=W/(i·η1·n)=84/(0.8×0.8×3)=44kg 由气缸传动的计算公式:Q=P·(πD2/4)·η式中: P--压缩空气压力=6atm=6kg/cm2η--气缸摩擦系数,取0.8i—压板与工件的摩擦系数,取0.8n—夹紧气缸个数,本夹具为3D--气缸直径(cm)444463.140.8QDpD=34.2cm通过以上理论计算,可以选择直径为50mm的气缸。
机床夹具在设计过程中夹紧力的计算
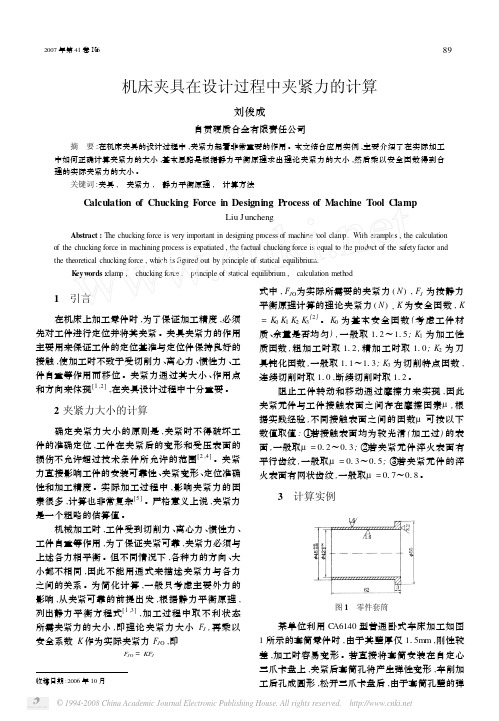
收稿日期:2006年10月机床夹具在设计过程中夹紧力的计算刘俊成自贡硬质合金有限责任公司摘 要:在机床夹具的设计过程中,夹紧力起着非常重要的作用。
本文结合应用实例,主要介绍了在实际加工中如何正确计算夹紧力的大小,基本思路是根据静力平衡原理求出理论夹紧力的大小,然后乘以安全因数得到合理的实际夹紧力的大小。
关键词:夹具, 夹紧力, 静力平衡原理, 计算方法C alculation of Chucking Force in Designing Process of Machine Tool ClampLiu JunchengAbstract:The chucking force is very important in designing process of machine tool clamp.With examples,the calculation of the chucking force in machining process is expatiated,the factual chucking force is equal to the product of the safety factor and the theoretical chucking force,which is figured out by principle of statical equilibrium.K eyw ords:clamp, chucking force, principle of statical equilibrium, calculation method 1 引言在机床上加工零件时,为了保证加工精度,必须先对工件进行定位并将其夹紧。
夹具夹紧力的作用主要用来保证工件的定位基准与定位件保持良好的接触,使加工时不致于受切削力、离心力、惯性力、工件自重等作用而移位。
夹紧力通过其大小、作用点和方向来体现[1,2],在夹具设计过程中十分重要。
夹紧力计算

盛年不重来,一日难再晨。
及时宜自勉,岁月不待人。
4.1.2 夹紧力计算及夹紧气缸的设计1、夹紧力的计算工件材料为AS9U3,大平面加工余量为1.5mm ,采用硬质合金端铣刀加工,切削力查参考文献〔1〕可根据如下公式计算: •式中:Fz ---铣削力(N)a f ---每齿进给量(mm/r) a w ---铣削宽度(mm) K FZ ---铣削力修正系数 d 0---铣刀外径(mm) a p ---铣削深度(mm) z ---•铣刀齿数 确定各参数值:(1).铣刀外径d 0=315mm ; (2).铣刀齿数Z =16;(3).每齿进给量af 是铣刀每转一个刀齿时铣刀对工件的进量:a f =V f /(z ·n)=360/(16×720)=0.031mm/r(4).铣削深度a p 对于端铣刀是指平行于铣刀轴线测量的被铣削层尺寸:a p =1.5mm(5). 铣削宽度a w 对于端铣刀是指垂直于铣刀轴线测量的被切削层尺寸:a w =240mm(6). 修正系数K FZ 取1.6;由表查得: c F =7750 x F =1.0 y F =0.75u F =1.1 w F =0.2 q F =1.3FZw q 0V wy fX PX FZ K nd Za a a c 25.0F fFFfFF⋅⋅⋅⋅⋅⋅⨯=⋅1.00.751.11.30.277501.50.031240160.25 1.6315720ZF ⨯⨯⨯⨯=⨯⨯⨯Fz=276.5N=28Kg(7). 理论所需夹紧力计算 确定安全系数:总的安全系数k =k1·k2·k3·k4k 1---- 一般安全系数; k 1取1.7;k 2----加工状态系数; 由于是精加工,所以k 2取1; k 3----刀具钝化系数; k 3取1.4; k 4----断续切削系数; k 4取1.2; ∴ k =1.7×1×1.4×1.2≈3 W =k ·p =3×28kg =84kg 2. 气缸的选择Q=W/(i ·η1·n )=84/(0.8×0.8×3)=44kg 由气缸传动的计算公式: Q=P·(πD2/4)·η式中: P--压缩空气压力=6atm =6kg/cm2 η--气缸摩擦系数,取0.8i —压板与工件的摩擦系数,取0.8n —夹紧气缸个数,本夹具为3 D--气缸直径(cm)D ==D=34.2cm通过以上理论计算,可以选择直径为50mm 的气缸。
m6螺栓夹紧力
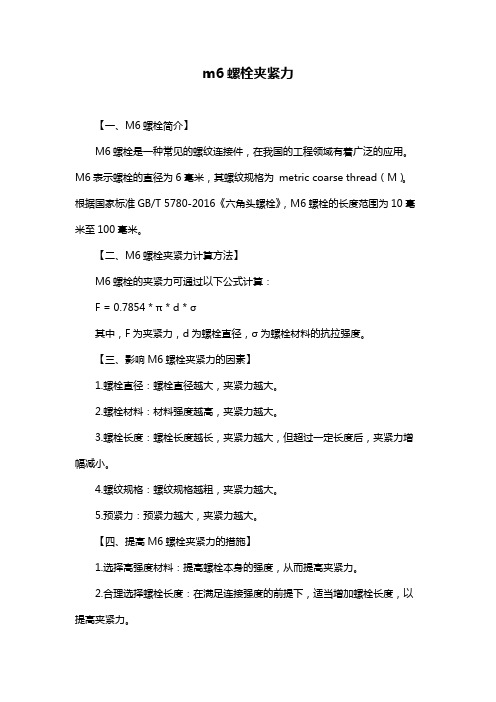
m6螺栓夹紧力
【一、M6螺栓简介】
M6螺栓是一种常见的螺纹连接件,在我国的工程领域有着广泛的应用。
M6表示螺栓的直径为6毫米,其螺纹规格为metric coarse thread(M)。
根据国家标准GB/T 5780-2016《六角头螺栓》,M6螺栓的长度范围为10毫米至100毫米。
【二、M6螺栓夹紧力计算方法】
M6螺栓的夹紧力可通过以下公式计算:
F = 0.7854 * π * d * σ
其中,F为夹紧力,d为螺栓直径,σ为螺栓材料的抗拉强度。
【三、影响M6螺栓夹紧力的因素】
1.螺栓直径:螺栓直径越大,夹紧力越大。
2.螺栓材料:材料强度越高,夹紧力越大。
3.螺栓长度:螺栓长度越长,夹紧力越大,但超过一定长度后,夹紧力增幅减小。
4.螺纹规格:螺纹规格越粗,夹紧力越大。
5.预紧力:预紧力越大,夹紧力越大。
【四、提高M6螺栓夹紧力的措施】
1.选择高强度材料:提高螺栓本身的强度,从而提高夹紧力。
2.合理选择螺栓长度:在满足连接强度的前提下,适当增加螺栓长度,以提高夹紧力。
3.增加预紧力:适当加大预紧力,使螺栓夹紧力得到提高。
4.优化螺栓结构:如采用螺纹加密、加大螺栓头部等措施,以提高夹紧力。
【五、总结】
M6螺栓作为一种常见的螺纹连接件,在工程领域具有重要应用价值。
了解M6螺栓的夹紧力计算方法及影响因素,有助于我们更好地选择和使用M6螺栓,提高连接件的稳定性和安全性。
恩格尔注塑机 夹紧力和吨位的换算

恩格尔注塑机夹紧力和吨位的换算1. 简介恩格尔注塑机是一种常用于塑料制品生产的设备,其夹紧力和吨位是衡量其性能的重要指标。
本文将详细介绍恩格尔注塑机夹紧力和吨位的含义、计算方法以及它们在注塑机操作中的应用。
2. 恩格尔注塑机夹紧力的含义和计算方法2.1 含义恩格尔注塑机的夹紧力指的是注塑机在进行注塑过程中对模具施加的闭合力量。
它决定了模具在注塑过程中是否能够保持稳定,避免产生漏料、渗漏等问题。
2.2 计算方法恩格尔注塑机夹紧力的计算方法如下:夹紧力(kN)= 投影面积 * 注射压力其中,投影面积可以通过模具尺寸计算得到,而注射压力则取决于所需制品的材料特性和成型要求。
3. 恩格尔注塑机吨位的含义和换算关系3.1 含义恩格尔注塑机的吨位是衡量其生产能力的指标,它表示注塑机能够施加的最大闭合力量。
吨位越大,注塑机的生产能力越强。
3.2 换算关系恩格尔注塑机的吨位与夹紧力之间存在一定的换算关系。
一般来说,1吨(t)等于约9.8千牛(kN),即:1 t = 9.8 kN可以通过以下公式将恩格尔注塑机的吨位转换为夹紧力:夹紧力(kN)= 吨位(t) * 9.84. 恩格尔注塑机夹紧力和吨位在操作中的应用4.1 夹紧力的应用恩格尔注塑机的夹紧力直接影响着模具的稳定性和制品质量。
在操作中,需要根据所需制品和模具尺寸选择合适的夹紧力。
若夹紧力过小,则可能导致模具不稳定、产生漏料等问题;而夹紧力过大,则可能对模具造成损坏。
4.2 吨位的应用恩格尔注塑机的吨位决定了其生产能力,对于不同规格和要求的制品,需要选择合适的吨位来保证生产效率和质量。
一般来说,制品越大、复杂,所需的吨位就越大。
在操作中,操作人员需要根据制品要求、模具尺寸和注射压力等因素,选择恩格尔注塑机的合适吨位。
还应注意避免超过注塑机的最大吨位限制,以免对设备造成损坏或安全隐患。
5. 总结本文介绍了恩格尔注塑机夹紧力和吨位的含义、计算方法以及它们在操作中的应用。
夹紧力计算

上海德珂斯机械自动化技术有限公司Tuenkers Machinery & Automation Technology Co., Ltd, Shanghai夹紧器夹紧力计算上海德珂斯机械自动化技术有限公司Tuenkers Machinery & Automation Technology Co., Ltd, Shanghai1.压块垂直夹紧时,此时夹紧力处于垂直方向, 其受力分析如下:夹紧力Fs 压块M缸径 5bar气压夹紧力矩L40夹紧力Fs50120Nm 160Nm63380Nm80600NmFs =有效夹紧力 L=夹紧点与转动轴中心距离当压块垂直夹紧时,夹紧力方向与力矩切线方向相同,此时产生的夹紧力最大,计算公式如下: Fs= M ÷ L举例: 当L=200mm时,缸径63mm. 夹紧力Fs=380Nm ÷0.2m=1900N上海德珂斯机械自动化技术有限公司Tuenkers Machinery & Automation Technology Co., Ltd, Shanghai2.压块水平夹紧时,此时夹紧力处于水平状方 向,其受力分析如下:夹紧力Fs压块M L2L1 Fs α FFs =有效夹紧力 L1=夹紧点与转动轴中心距离 F=切向力缸径 5bar气压夹紧力矩M40120Nm50160Nm63380Nm80600Nm当压块水平夹紧时,其有效夹紧力会相对减小,计算公式如下: Cos α =L2 ÷ L1 F= M ÷ L1 Fs= F × Cos α举例: 当L1=200mm,L2=100mm时,缸径63mm。
F=380Nm÷0.2=1900N Fs=F × Cos α=1900N×(100÷200)=950N上海德珂斯机械自动化技术有限公司Tuenkers Machinery & Automation Technology Co., Ltd, Shanghai谢谢!上海德珂斯机械自动化技术有限公司Tuenkers Machinery & Automation Technology Co., Ltd, Shanghai。
夹爪夹紧力计算
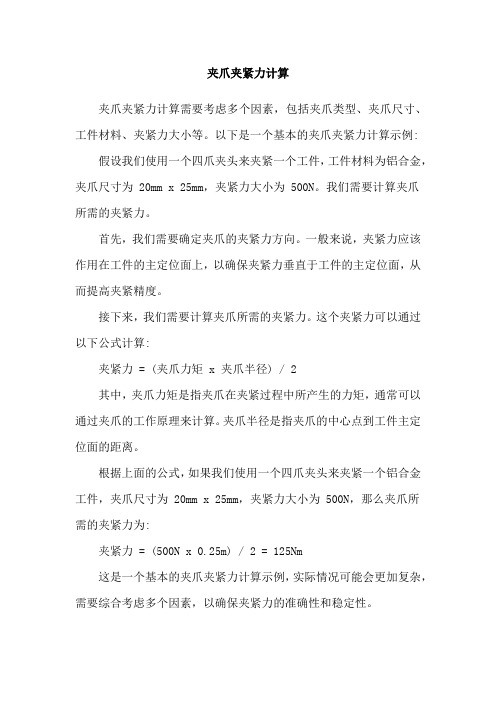
夹爪夹紧力计算
夹爪夹紧力计算需要考虑多个因素,包括夹爪类型、夹爪尺寸、工件材料、夹紧力大小等。
以下是一个基本的夹爪夹紧力计算示例: 假设我们使用一个四爪夹头来夹紧一个工件,工件材料为铝合金,夹爪尺寸为 20mm x 25mm,夹紧力大小为 500N。
我们需要计算夹爪
所需的夹紧力。
首先,我们需要确定夹爪的夹紧力方向。
一般来说,夹紧力应该作用在工件的主定位面上,以确保夹紧力垂直于工件的主定位面,从而提高夹紧精度。
接下来,我们需要计算夹爪所需的夹紧力。
这个夹紧力可以通过以下公式计算:
夹紧力 = (夹爪力矩 x 夹爪半径) / 2
其中,夹爪力矩是指夹爪在夹紧过程中所产生的力矩,通常可以通过夹爪的工作原理来计算。
夹爪半径是指夹爪的中心点到工件主定位面的距离。
根据上面的公式,如果我们使用一个四爪夹头来夹紧一个铝合金工件,夹爪尺寸为 20mm x 25mm,夹紧力大小为 500N,那么夹爪所
需的夹紧力为:
夹紧力 = (500N x 0.25m) / 2 = 125Nm
这是一个基本的夹爪夹紧力计算示例,实际情况可能会更加复杂,需要综合考虑多个因素,以确保夹紧力的准确性和稳定性。
夹紧力计算
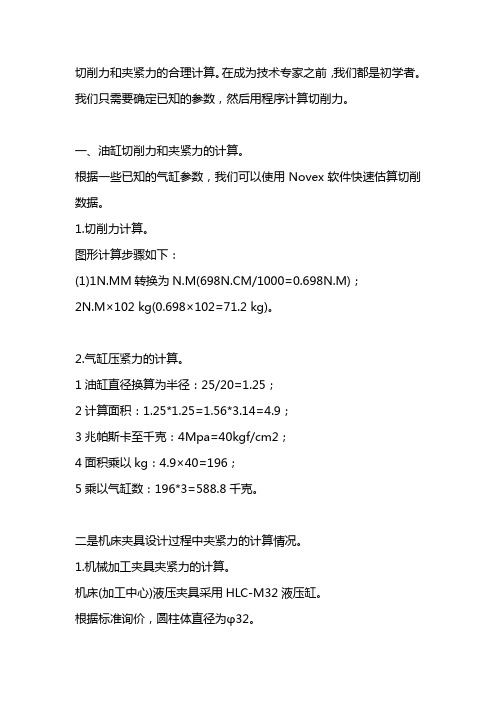
切削力和夹紧力的合理计算。
在成为技术专家之前,我们都是初学者。
我们只需要确定已知的参数,然后用程序计算切削力。
一、油缸切削力和夹紧力的计算。
根据一些已知的气缸参数,我们可以使用Novex软件快速估算切削数据。
1.切削力计算。
图形计算步骤如下:(1)1N.MM转换为N.M(698N.CM/1000=0.698N.M);2N.M×102 kg(0.698×102=71.2 kg)。
2.气缸压紧力的计算。
1油缸直径换算为半径:25/20=1.25;2计算面积:1.25*1.25=1.56*3.14=4.9;3兆帕斯卡至千克:4Mpa=40kgf/cm2;4面积乘以kg:4.9×40=196;5乘以气缸数:196*3=588.8千克。
二是机床夹具设计过程中夹紧力的计算情况。
1.机械加工夹具夹紧力的计算。
机床(加工中心)液压夹具采用HLC-M32液压缸。
根据标准询价,圆柱体直径为φ32。
该夹具共使用6个液压缸。
夹紧力的计算方法如图6所示。
2,f=ps=pπ(d/2)2=4823.04n.。
根据力矩平衡(杠杆)原理,该夹具的动力臂为L1,阻力臂为L2。
公式为:功率臂长度×功率=电阻臂长度×电阻。
计算三个电阻f1、f2和f3以及夹具的夹紧力(图7)。
铣削切削力的计算。
使用下面的软件,这个过程的基本参数,如转速和进给速率。
经计算,进给力FF约为12052N,径向力FP约为12873N,主切削力Fe约为36522N。
以上计算的机床夹紧力f为53053N。
夹紧力×摩擦系数(支撑块和铝合金为0.45)=23874n>ff>fp。
当摩擦力大于进给切削力和径向切削力时,确保定位销不受力。
工件重力质量=9.8×质量=196N,小重力不影响结果,合理选择液压缸压力。
结论。
过去,油缸和钢瓶的尺寸大多由设计者的经验决定。
利用软件计算结果进行合理选型,减少了因选错造成的浪费。
- 1、下载文档前请自行甄别文档内容的完整性,平台不提供额外的编辑、内容补充、找答案等附加服务。
- 2、"仅部分预览"的文档,不可在线预览部分如存在完整性等问题,可反馈申请退款(可完整预览的文档不适用该条件!)。
- 3、如文档侵犯您的权益,请联系客服反馈,我们会尽快为您处理(人工客服工作时间:9:00-18:30)。
4.1.2 夹紧力计算及夹紧气缸的设计1、夹紧力的计算工件材料为AS9U3,大平面加工余量为1.5mm ,采用硬质合金端铣刀加工,切削力查参考文献〔1〕可根据如下公式计算: •式中:Fz ---铣削力(N)a f ---每齿进给量(mm/r) a w ---铣削宽度(mm) K FZ ---铣削力修正系数 d 0---铣刀外径(mm) a p ---铣削深度(mm) z ---•铣刀齿数 确定各参数值:(1).铣刀外径d 0=315mm ; (2).铣刀齿数Z =16;(3).每齿进给量af 是铣刀每转一个刀齿时铣刀对工件的进量:a f =V f /(z ·n)=360/(16×720)=0.031mm/r(4).铣削深度a p 对于端铣刀是指平行于铣刀轴线测量的被铣削层尺寸:a p =1.5mm(5). 铣削宽度a w 对于端铣刀是指垂直于铣刀轴线测量的被切削层尺寸:a w =240mm(6). 修正系数K FZ 取1.6;由表查得: c F =7750 x F =1.0 y F =0.75u F =1.1 w F =0.2 q F =1.3FZw q 0V wy fX PX FZ K nd Za a a c 25.0F fFFfFF⋅⋅⋅⋅⋅⋅⨯=⋅1.00.75 1.11.30.277501.50.031240160.25 1.6315720ZF ⨯⨯⨯⨯=⨯⨯⨯Fz=276.5N=28Kg(7). 理论所需夹紧力计算 确定安全系数:总的安全系数k =k1·k2·k3·k4k 1---- 一般安全系数; k 1取1.7;k 2----加工状态系数; 由于是精加工,所以k 2取1; k 3----刀具钝化系数; k 3取1.4; k 4----断续切削系数; k 4取1.2; ∴ k =1.7×1×1.4×1.2≈3 W =k ·p =3×28kg =84kg 2. 气缸的选择Q=W/(i ·η1·n )=84/(0.8×0.8×3)=44kg 由气缸传动的计算公式: Q=P·(πD2/4)·η式中: P--压缩空气压力=6atm =6kg/cm2η--气缸摩擦系数,取0.8i —压板与工件的摩擦系数,取0.8n —夹紧气缸个数,本夹具为3D--气缸直径(cm)D ==D=34.2cm通过以上理论计算,可以选择直径为50mm 的气缸。
但是,考虑到由于铣削过程中每个刀齿的不连续切削,作用于每个刀齿的切削力大小及方向随时都在变化,致使在铣削过程中产生较大的振动,因此,夹具需有足够的夹紧力。
此外还考虑到工厂所供压缩空气压力不稳定,零件加工余量发生变化,零件材料缺陷,以及其它不可预见性因素的影响,为安全可靠起见,选择直径为63mm 的气缸。
4.2 铣侧面工装定位精度计算定位误差是由基准位移误差和基准不重和误差组成的。
下面对工序尺寸31.85±0.075的定位误差进行分析计算。
4.2.1 基准直线位移误差△x 1定位孔尺寸为φ6.0450.0220+,园柱定位销尺寸为φ6.0450.0130.028--,因工件定位后处于垂直状态,由于自重定位孔与定位销总是单方向接触,所以基准直线位移误差为:△x 1=04.2.2 基准角位移误差△x 2由图可知2-Φ6.0450.0220+孔中心距L 414.6mm定位时因零件自身重量,使得两定位孔移动方向相同。
∴ tg △θ=(x 2max -x 1max )/(2L)式中:△θ ----两定位孔同向移动时,定位基准的转角x 2max ----定位孔与菱形销之间的最大配合间隙 x 1max ----定位孔与圆柱销之间的最大配合间隙 L ----两定位孔中心距菱形销尺寸为φ60.0130.028--,定位孔尺寸为φ6.0450.022+ ∴x 2max =0.022+0.028+0.045=0.95mm x 1max =0.022+0.028=0.05mmtg △θ=(x 2max -x 1max )/(2L)=(0.95-0.05)/(2X414.6) =0.54×10-4△θ=0.003°加工面(长240)两端角位移误差△x 2'为:240×sin △θ=0.013mm4.2.3 基准不重合误差△B由工序简图可知,定位基准是由底平面B 和2-φ6.0450.0220+孔组成。
而工序尺寸31.83±0.4的工序基准为φ6.0450.0220+孔。
所以基准不重合误差△B =0mm 。
定位误差△D=△x 1+△x 2+△B =0+0.013+0=0.013mm由于0.013mm<<±0.075mm ,故能很好地满足加工精度求。
4.3 铣侧面工装设计4.3.1 铣削力的计算工件材料为铸造铝合金。
侧平面加工余量为1mm 。
•采用硬质合金端铣刀加工。
切削力可根据如下公式计算:式中:Fz ---铣削力(N)a f ---每齿进给量(mm/r) a w ---铣削宽度(mm) K FZ ---铣削力修正系数 d 0---铣刀外径(mm) a p ---铣削深度(mm) z---•铣刀齿数 确定各参数值:1、铣刀外径d 0=125mm ;2、铣刀齿数Z =8;3、每齿进给量af 是铣刀每转一个刀齿时铣刀对工件的进量:a f =v f /(z ·n)=638/(8×1120)=0.071mm/r4. 铣削深度a p 对于端铣刀是指平行于铣刀轴线测量的被铣 削层尺寸:a p =1mm5. 铣削宽度a w 对于端铣刀是指垂直于铣刀轴线测量的被切削层尺寸:FZw q 0V wy fX PX FZ K nd Za a a c 25.0F fFFfFF⋅⋅⋅⋅⋅⋅⨯=⋅a w =70mm6. 修正系数K FZ 取1.6;由表查得: c F =7750 x F =1.0 y F =0.75u F =1.1 w F =0.2 q F =1.31.00.75 1.11.30.277501.0.0717080.25 1.61251120ZF ⨯⨯⨯⨯=⨯⨯⨯=168N=17Kg •4.3.2 铣削夹具底板强度校核 1、夹具底板受力分析底板材料采用45钢,其屈服极限σs =245N/mm2,安全系数ns =1.5•。
故其许用应力[σ]=σs / n s =245/1.5=163N/mm2许用剪切应力[τ]=0.6[σ]=0.6×163N/mm 2=98N/mm 2底板受力情况如下图所示:图4.3 底板受力图(1)支承反力计算如下:根据公式可知:R B=P=168N(2)弯矩计算如下:已知:P:168N L:420mmM B=-PL=-168×0.42=-70.56N.m(3)底板转角计算如下:已知:P:168N L:420mm E:200GPa I:364583mm4θA=-168×4202/(2×200×364583) =0.00108°2、由上图可知:(1)夹具底所承受的最大弯矩:Qmax=168NMmax=168×0.42=70.56N.m(2)对截面尺寸进行校核弯曲正应力:Wz=bh2/6=280×252/6=1.75×105mm3σmax=Mmax/Wz=70.56×103/(1.75×105)=40.32×10-2 N/mm2因为:σmax=40.32×10-2 N/mm2<[σ]=163N/mm2另:底板受力转角仅为0.00108°,故可忽略,不予考虑。
所以:底板所选截面280×25完全满足强度要求。
第三章夹具设计3.1选择工序工艺过程为2.3.2中的方案三,选择工序60粗铣G面的夹具设计,在此工序前顶面B,底面F,左侧面E已经加工完毕,加工要求保证距E面尺寸106.9mm.3.2确定定位方案和定位元件根据零件结构和工序安排,本工序加工时的主要定位基准(限制三个自由度)3.3.1切削力的计算本工序为用硬质合金端铣刀粗铣G面,根据手册[1],铣削切削力的计算公式为:F=490a p.1f z74.0d 0.1-b D90.0z(3.1)注:式中 F —铣削力(N );a p —铣削深度(mm ); f z —每齿进给量(mm/z ); d —铣刀直径(mm );b D —铣削宽度(mm ); z —铣刀的齿数。
其中,a p =2.3mm ,f z =0.28mm/z ,d=160mm ,b D =78mm ,z=8,所以F=490×2.30.1×0.2874.0×1600.1-×7890.0×8=1108N3.3.2夹紧力的计算根据手册[1],夹紧力的计算公式为:F k =21μμ+KF(3.2)K=K 0K 1K 2K 3K 4K 5K 6(3.3)式中 F k —实际所需的夹紧力(N ); F —切削力(N );1μ—夹紧元件与工件间的摩擦因数; 2μ—工件与夹具支承面间的摩擦因数;K —安全系数;K 0~K 6—各种因数的安全系数。
根据[1]表17-10、表17-11,K 0=1.2,K 1=1.2,K 2=1.2,K 3=1.0,K 4=1.0,K 5=1.0, K 6=1.0,则K=1.2×1.2×1.2×1.0×1.0×1.0×1.0=1.7根据[7]表18-1,1μ=0.1,2μ=0.1,则F k =1.01.011087.1+⨯=9418N每个气缸可提供的夹紧力为7000N ,则2F=14000N>9418N ,可满足要求。
3.4定位误差的分析验算夹具的主要功能是用来保证工件加工表面的位置精度,影响位置精度精度的主要因素有三个方面:(1)工件在夹具中的安装误差,它包括定位误差和夹紧误差。
(2)夹具在机床上的对定误差,指夹具相对于刀具或相对于机床成形运动的位置误差。
(3)加工过程中出现的误差,它包括机床的几何精度、运动精度,机床、刀具、工件和夹具组成的工艺系统加工时的受力变形、受热变形,磨损,调整,测量中的误差,以及加工成形原理上的误差等。
第三项一般不易估算,前两项和不大于工件允许的三分之二为合格。
常用符号w D •∆表示。
根据[1]表17-9,B w D •∆=2(H-h )tan ∆g α(3.4).;. 如图3.1:B w D •∆=2×(98-51)×tan0.1º=0.16mm根据手册[1],加工精度等级IT=8,根据《几何量公差与检测》[8]附表3-2,公差为0.54mm ,在允许的范围内。