织物色差的识别及预防
涤棉混纺织物色差产生的原因及防止
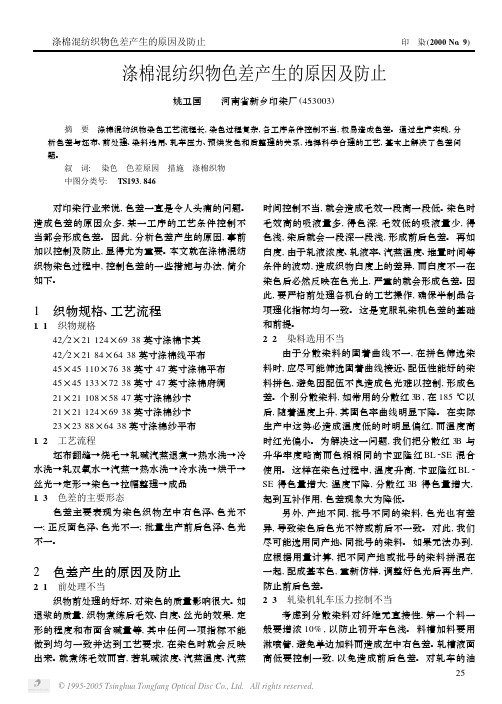
涤棉混纺织物色差产生的原因及防止姚卫国 河南省新乡印染厂(453003)摘 要 涤棉混纺织物染色工艺流程长,染色过程复杂,各工序条件控制不当,极易造成色差。
通过生产实践,分析色差与坯布、前处理、染料选用、轧车压力、预烘发色和后整理的关系,选择科学合理的工艺,基本上解决了色差问题。
叙 词: 染色 色差原因 措施 涤棉织物中图分类号: TS1931846 对印染行业来说,色差一直是令人头痛的问题。
造成色差的原因众多,某一工序的工艺条件控制不当都会形成色差。
因此,分析色差产生的原因,事前加以控制及防止,显得尤为重要。
本文就在涤棉混纺织物染色过程中,控制色差的一些措施与办法,简介如下。
1 织物规格、工艺流程1.1 织物规格42 2×21124×6938英寸涤棉卡其42 2×2184×6438英寸涤棉线平布45×45110×7638英寸47英寸涤棉平布45×45133×7238英寸47英寸涤棉府绸21×21108×5847英寸涤棉纱卡21×21124×6938英寸涤棉纱卡23×2388×6438英寸涤棉纱平布1.2 工艺流程坯布翻缝→烧毛→轧碱汽蒸退煮→热水洗→冷水洗→轧双氧水→汽蒸→热水洗→冷水洗→烘干→丝光→定形→染色→拉幅整理→成品1.3 色差的主要形态色差主要表现为染色织物左中右色泽、色光不一;正反面色泽、色光不一;批量生产前后色泽、色光不一。
2 色差产生的原因及防止2.1 前处理不当织物前处理的好坏,对染色的质量影响很大。
如退浆的质量,织物煮练后毛效、白度、丝光的效果,定形的程度和布面含碱量等,其中任何一项指标不能做到均匀一致并达到工艺要求,在染色时就会反映出来。
就煮练毛效而言,若轧碱浓度、汽蒸温度、汽蒸时间控制不当,就会造成毛效一段高一段低。
染色时毛效高的吸液量多,得色深;毛效低的吸液量少,得色浅,染后就会一段深一段浅,形成前后色差。
纺织品色差检测标准

纺织品色差检测标准纺织品色差是指在同一种光源下,不同批次、不同部位或不同面料的颜色差异。
色差是由于纺织品在生产、加工、储存和使用过程中所受到的各种因素的影响,如原料的不均匀性、染色工艺的不稳定性、机器设备的不精确性等。
色差会影响纺织品的外观质量,降低产品的档次和附加值,因此对纺织品色差进行检测和控制具有重要意义。
一、色差的分类。
根据色差的来源和性质,可以将色差分为原色差和混合色差。
原色差是指由于纺织品面料的原料或者染色工艺引起的颜色差异,如纤维的不均匀性、染色工艺的不稳定性等。
混合色差是指在纺织品生产和使用过程中,由于光照、污染、磨损等外部因素引起的颜色差异。
根据色差的大小,可以将色差分为可接受色差和不可接受色差。
可接受色差是指在一定条件下,人眼无法明显感觉到的色差,而不可接受色差是指人眼可以明显感觉到的色差。
二、色差的检测方法。
目前,常见的纺织品色差检测方法包括目视比对法、仪器检测法和计算机色差分析法。
目视比对法是指通过人眼直接观察和比对纺织品的颜色差异,这种方法简单直观,但受到人眼主观因素的影响,不够准确。
仪器检测法是指利用色差仪、光泽度仪等专业仪器进行色差检测,这种方法准确性高,但设备成本较高。
计算机色差分析法是指利用计算机软件对纺织品的色差进行分析和比对,这种方法准确性高,且可以消除人眼主观因素的影响,是目前较为先进的检测方法。
三、色差的标准。
为了规范纺织品色差的检测和评定,国际上制定了一系列的色差标准,如ISO105-J01,2010《纺织品色牢度试验,J01灰度标准样品》、ISO105-A02,1993《纺织品色牢度试验,A02灰度标准样品》等。
这些标准主要包括了颜色标准样品的制备、色差的计算方法、色差的评定标准等内容,为纺织品色差的检测和评定提供了具体的指导。
四、色差的控制。
要控制纺织品的色差,首先需要从原料和染色工艺上进行控制。
在选用原料时,应尽量选择颜色均匀的纤维,避免出现原色差。
纱线色差产生的原因及预防措施

纱线色差产生的原因及预防措施纱线色差是评定纱线品质的重要指标,也是棉纺企业在生产过程中把关产品质量的重点之一,色差又叫黄白纱,可以分为本色色差和染色色差。
本色色差就是产品在着色前显现的色差。
染色色差就是产品只有在着色后才能显现的色差。
一般来讲,纯化纤纱由于化纤原料颜色单一,故化纤纱线色差较小:涤棉、粘棉纱等化纤与棉混纺纱线色差也较小,而棉型纱线极易产生色差。
色差仅对同一批号的纱线而言,不同批号的纱线没有可比性。
色差仅凭肉眼就能看出来,不明显的需借助荧光灯来观察。
色差纱线对印染布和色织布等色布影响很大,会产生上色不匀、染色条花、染色色差等有损织物外观质量问题。
因此,控制纱线色差是纺纱生产中的一个重点。
纱线色差产生的原因本色色差:本色色差产生的原因是多方面的,如配棉工艺不合理,清棉工序混棉不均匀,各工序没有保证先纺先用,锭速级差引起的长片段和条干引起的短片段的捻度差异等,都是造成本色色差的主要因素。
染色色差:由于产品中掺有异性纤维或原棉成熟度差异过大,致使纤维着色能力不同而产生染色色差。
纱线产生色差的根本原因是原棉颜色的差异和在加工过程中对原料没有进行很好地利用、搭配,以及没有采取必要的把关和预防措施。
控制和预防纱线色差的措施(1)加强棉花检验和逐包检验工作。
取样一定要全面,要确实有代表性,各项指标试验要准确,真突地反映原棉实际质量情况;对正常使用中的棉花进行逐包检验工作,发现个别品级、色泽等质量指标有差异的棉包,要合理使用。
(2)配棉时要保持原棉色泽上有主体。
使一种颜色原棉占70%以上,并且有一定量库存保持相对稳定。
配棉还要满足相似原则。
所谓相似原则,就是某批原棉色泽和主体色泽差距大时,它的各项物理性能指标必须和主体性能相似。
反之,如果原棉性能指标和主体性能差距大时,原棉的色泽就必须和主体色泽相似。
同时,在色泽转变时,要稳定的进行调整,每批调整幅度不大于5%,调整周期可根据细纱车间生产能力确定。
(3)色差的程度随棉纤维成熟情况而变化,成熟度差异越大的纤维,其色差越大,而成熟度接近的棉花,其色差较小。
【涤棉】涤棉混纺织物色差成因及解决方法

【纯干货】涤棉混纺织物色差成因及解决方法涤棉混纺织物热熔染色色差表现形式、产生原因及克服办法1.两边色差1)染液浸轧:两边带液量不一致;2)预烘和焙烘:烘干程度不均匀或不充分;2.边中色差及左中右色差1)轧辊轴心发生变形,产生轧余率不一致;2)在预烘或热熔时布幅中间和两边温度和风量不一致;a)在一般空车情况下,中间温度高于两边温度(焙烘箱)(热熔);b)散热时,两边易干,而中间慢,造成中间温度稍低(预烘);3)染料性能不同:由于温度中高边低,产生固色条件差异;低温型会发生中浅边深,高温型分散染料却相反;克服办法:第一,改善织物干燥的均匀性;第二,采用均匀轧车;第三,改善轧液的均匀性;第四,染色时要合理选用染料;3.正反面色差1)轧辊软硬度差异太大;2)预烘时正反面温度和风量不一致;3)热风预烘拔风效果差,湿度过度;4)克服办法:第一,合理选择软辊的硬度;第一,正反面烘燥力求均匀;第二,热风部分采用横导辊穿布方式;第三,预烘室拔风要充分,防止湿度过高;第四,在染料溶液中适当加入防泳移剂4.左右对角色差(实质上是局部性的正反面色差)1)预烘时左右热量不匀,辐射强度不一;2)喷风量左右不匀;3)金属导辊左右两头散热不一4)克服办法:从设备上找根源;5.前后色差1)坯布方面:纤维的种类、质量、配棉的变动;2)练漂前处理方面A.前处理采用设备不同,工艺条件不容易掌握一致,半制品染色后色泽有区别;B.退浆效果如有差别,也会形成色泽深浅;C.热定型速度和风速;D.丝光后的pH值:最显著的产生原因;3)染色方面A.进焙烘箱之前织物干潮不一致;B.热熔温度是染色过程中影响色差最显著的因素;C.车速、染液、显色液、还原液浓度掌握不一致,造成前后搭色不一;D.产地、批号不同的染料,色光有差异;4)后整理方面:树脂或高温焙烘可引起某些染料色光变化。
6.克服办法:第一,防止坯布因素,掌握纤维原料和上浆成分的变化情况;第二,练漂前处理机台要“三定”(定工艺、定机台、定人员);第三,要经常检查定型机、热风机运转情况;第四,染整加工的半制品,其退浆、丝光后织物上的pH值须“三查”;第五,染色用染料要按产地、批号分开堆放,控制好色光;第六,染料上车要研磨认真;第七,预烘后进入焙烘箱前布身要干;第八,在染色过程中,要严格控制工艺条件和操作规程;第九,染色机上装自控温装置;第十,出布处建贴样制度;第十一,染色后,成品检验按次序进行,分色成包;。
边中色差成因及预防论文等二篇

梭织物印染条花疵布成因及预防关键字:梭织物条花疵布成因措施梭织物所产生的各类条花染疵类别繁多,有织物去浆未净条花、煮练不透雨丝条花、烧毛条花、丝光去碱不匀条花、染色泳移条花和织造疏密不匀条花、灯芯绒割绒条花等,这是印染工作者经常遇到的质量问题。
随着目前纺织品国际竞争愈趋激烈,品质的要求也愈趋严格,各类条花染疵的存在影响织物外观,给企业带来的后遗症是不言而喻的。
染整过程为此返工改染甚至“全军覆没” 的事例不胜枚举,鉴于此,有必要对部分梭织物上呈现出来的各类条花染疵作出分析,提出纠正和预防措施。
1.各类条花疵布成因分析及预防办法1.1去浆未净条花1.1.1表现的形式中深色府绸薄织物纬向宽距为1.0 cm左右的经向条花。
1.1.2成因分析该类织物由于经纱纱支较细,织造时为减少断纱现象,一般给予该类织物经纱施加了大量的混合浆料(其成份复杂,有淀粉、PVA、石蜡、防腐剂等组成),这些高浓度混合浆料的存在增加了印染前处理的难度,若印染前处理过程中未将织物上浆料去净就转入后道生产,染色时就会不可避免地产生条花染疵(深色尤甚)。
1.1.3纠正、预防前处理工艺设计要着重考虑如何去除织物上浆料。
下面着重介绍享斯迈O、D、New高温裂解法。
(1)工艺流程:翻缝→高温裂解去浆煮练→烧毛→氧漂。
(2)高温裂解去浆煮练工艺条件:NaOH 56 g/ L;H2O21.3 g/L;O、D、New 8 g/L;H-982精练剂2 g/ L;工作液温度45℃;轧余率80%;履带箱堆置汽蒸50 min,温度100~102℃。
(3)效果:O、D、New高温裂解剂,其耐碱达300 g/L,是集润湿、乳化、分散、螯合、稳定为一体的复合化合物。
经该工艺处理的各类弹力府绸能有效消除条花染疵的产生。
另外,碱氧冷堆、短蒸复氧漂工艺;液下碱煮练、氧漂工艺;清棉师100 T前处理工艺亦可同样克服该类条花染疵的产生。
1.2 纬弹织物易出现的条花1.2.1表现形式纬弹类直贡、纱卡织物纬向宽距为0.5 cm左右的经向无规则条花。
纱线色差的产生和预防措施

纱线色差的产生和预防措施现代纺织品制造技术的发展为纱线色差的发生提供了更多的机会。
纱线色差是指纱线色调和所需(订单)色调之间的偏差,它可能会破坏最终产品的外观,影响客户的满意度,甚至严重影响纺织品企业的声誉。
因此,研究纱线色差的产生原因,以及采取的相应的预防措施,以确保色彩质量,显得格外重要。
一般来说,纱线色差的产生是由于原料、染色工艺和织造工艺等多种因素引起的。
其中较为重要的原因是原料质量和染色过程中缺乏精确的操作技术。
首先,原料的质量要求会影响纱线色差的发生,如果原料质量低劣,在染色过程中会造成大量残余,这样会影响最终色彩的一致性,从而导致纱线色差的发生。
此外,原料的颜色和光泽也会影响染色的成功程度,如果原料本身的色彩过淡,那么在染色后的色彩效果就会比预期的差。
除原料质量外,纱线色差也可能是由于染色工艺不足而产生的。
现代染色工艺要求对染料的控制,以保证每一批纱线的工艺一致,消除纱线色差的发生。
然而,大多数纺织企业在实际染色过程中都有日常管理的漏洞,以及缺乏操作技术,这些都会导致染色结果的不可预知性。
另外,织造工艺的不当也会导致纱线色差的发生。
机织布由纱线和纬线组成,它们的编织位置会影响布料的外观,而编织不均匀,布料色差也会出现。
此外,机织布也会出现变形,如果这种变形影响布料色调,也会出现色差现象。
上述原因都可能导致纱线色差,但是,可以采取一些措施来预防色差的发生。
首先,在投入生产前,要对原料进行全面检测,严格控制原料的质量。
此外,染色工艺也需要加以完善,包括机器维护、染料和水质的检测,以及精确控制每一步的操作过程,使染色质量达到理想状态。
此外,还需要加强对编织工艺的管理,防止布料变形,以保障机织布的色彩一致性。
以上是纱线色差的产生及其预防措施。
纱线色差的发生将会影响纺织品企业的声誉,因此必须重视,从原料、染色工艺、织造工艺等多方面入手,制定有效的预防措施,以保障纱线色彩的一致性。
仅有一致的控制才能保障纱线色彩的一致性,才能满足市场对纱线色彩的需求。
纺织品常见色牢度问题及预防措施

纺织品常见色牢度问题及预防措施从事纺织印染行业的人士,基本知道牢度问题是所有染色疑问中被问及对多的问题。
染色牢度对染色、印花织物的质量要求很高,染色状态变异的性质或程度可用染色牢度来表示。
它与纱线结构、织物组织、印染方法、染料种类及外界作用力大小有关。
不同的染色牢度要求,会引起很大的成本差异和质量差异。
一、主要纺织品牢度1、日晒牢度日晒牢度是指有颜色织物受日光作用变色的程度。
其测试方法可采用日光照晒也可采用日光机照晒,将照晒后的试样褪色程度与标准色样进行对比,分为8级,8级最好,1级最差。
日晒牢度差的织物切忌阳光下长时间曝晒,宜于放在通风处阴干。
2、摩擦牢度摩擦牢度是指染色织物经过摩擦后掉色程度,可分为干态摩擦和湿态摩擦。
摩擦牢度以白布沾色程度作为评价原则,共分5级(1~5),数值越大,表示摩擦牢度越好。
摩擦牢度差的织物使用寿命受到限制。
3、洗涤牢度水洗或皂洗牢度是指染色织物经过洗涤液洗涤后色泽变化程度。
通常采用灰色分级样卡作为评定标准,即依靠原样和试样褪色后的色差来进行评判。
洗涤牢度分为5个等级,5级最好,1级最差。
洗涤牢度差的织物宜干洗,如若进行湿洗,则需加倍注意洗涤条件,如洗涤温度不能过高、时间不能过长等。
4、熨烫牢度熨烫牢度是指染色织物在熨烫时出现的变色或褪色程度。
这种变色、褪色程度是以熨斗同时对其它织物的沾色来评定的。
熨烫牢度分为1~5级,5级最好,1级最差。
测试不同织物的熨烫牢度时,应选择好试验用熨斗温度。
5、汗渍牢度汗渍牢度是指染色织物沾浸汗液后的掉色程度。
汗渍牢度由于人工配制的汗液成份不尽相同,因而一般除单独测定外,还与其它色牢度结合起来考核。
汗渍牢度分为1~5级,数值越大越好。
6、升华牢度升华牢度是指染色织物在存放中发生的升华现象的程度。
升华牢度用灰色分级样卡评定织物经干热压烫处理后的变色、褪色和白布沾色程度,共分5级,1级最差,5级最好。
正常织物的染色牢度,一般要求达到3~4级才能符合穿着需要。
布匹色差

布匹色差在线检测技术及应用前言预防和控制染色产品的色差, 并使其保持稳定, 一直是各印染企业和染整工作者所关注的重点。
尤其是随着制衣业工业化和连续化的高速发展, 人们对染色产品的色差提出了更高的标准和要求。
导致染色成品布产生色差的因素多且复杂, 要将色差严格控制在标准范围之内且使其长期保持稳定, 涉及到生产加工过程中的方方面面, 必须对各个要素和影响因素进行综合分析, 制定出相应的预防措施, 严格规范实施手段, 对染色织物的色差加以控制。
染色成品的色差一般分为: 原样色差、前后色差、左中右色差和正反面色差(俗称阴阳面) 四大类。
原样色差是指染色织物与客户来样或标准色卡样, 在色相、色光和色泽深度上存在的差异; 前后色差是指相同工艺先后染出的织物在色相、色光与深度上存在的差异; 左中右色差是指染色织物纬向左中右部分的色相、色光与色泽深度存在的差异; 正反面色差(阴阳面)是指平纹织物两面的色相与色泽深度存在的差异。
以下结合生产实践, 简要分析产生这四类色差的原因, 并提出预防和控制措施。
1 形成色差的主要因素1. 1 前处理随着印染生产加工技术的进步与发展, 前处理的处理能力、处理质量及处理效果对印染加工成品质量的影响越来越突出。
业内专家认为, 70% 左右的产品收稿日期: 2006 - 06- 19 质量应控制在前处理工序中。
在织物印染加工过程中, 前处理后的半成品所存在的疵病一般都具有一定的隐蔽性, 特别是对织物的内在质量指标有影响的疵病, 很难判断查明。
前处理中造成织物成品色差的影响因素主要有退浆除杂不匀、不净; 前后、左中右毛效不一致; 白度批差大; 丝光不匀透; 水洗效果差; 半成品布面碱性过大等。
1. 2半成品退浆除杂不匀、不净织物经过煮练、漂白工序后, 色素已被除去, 仅从织物布面很难发现其退浆及除杂不匀、不净的质量问题。
用这种半成品生产漂白和浅色品种, 容易产生泛黄、变色、色相不稳定(色萎、色暗)、艳度较差等问题; 此外还会影响织物的丝光和染色效果, 造成织物表面丝光和染色白芯等疵病。
- 1、下载文档前请自行甄别文档内容的完整性,平台不提供额外的编辑、内容补充、找答案等附加服务。
- 2、"仅部分预览"的文档,不可在线预览部分如存在完整性等问题,可反馈申请退款(可完整预览的文档不适用该条件!)。
- 3、如文档侵犯您的权益,请联系客服反馈,我们会尽快为您处理(人工客服工作时间:9:00-18:30)。
织物色差的识别及预防
广州庄杰化工有限公司
1.疵病特征:染色制品所得色泽深浅不一,色光有差别。
(1)同批色差:同批产品中.一个色号的产品箱与箱之间、件与件之间、包与包之间、匹与匹之间有色差。
(2)同匹色差:同匹产品中的左中有有色差或前后有色差或正反面有色差。
色差是染整厂常见疵病和多发性疵病之一,严重影响染色成品的质量。
2.产生原因
各类织物的纤维组成不同,染色时采用的染料种类及工艺设备不同、加上染色加工中有不同的要求和特点,产生疵病的原因及表现就不一样,干洗和污渍处理方法也不一样。
色差在外观表现上多种多样,但究其原因,主要有以下几种。
(1)染料在织物上先期分布不均匀:染料在固着之前,如果在织物各部位上分布不匀,固色后必然形成色差。
造成这种现象的主要原因为:
①织物因素:由于纤维性能不同或前处理退、煮、漂、丝不够匀透,使染前半制品渗透性不匀而引起对染料吸收程度的差异。
②吸液因素;由于机械结构上的原因或操作不当,使织物各部位的带液率不一致,因而造成色差。
轧辊压力不匀、加入染化料不匀等都会使织物吸收染料不匀。
②预烘因素:在浸轧染液后预烘时,由于烘燥的速率和程度不一致,引起染料发生不同程度的泳移,使染料在织物上分布不匀。
(2)染料在织物上固着程度不同:尽管染料在织物上先期分布是均匀的,但在固着过程中.如条件控制不当(如温度、时间、染化料浓度等),使织物上某些部位的染料没有得到充分固色,在后处理皂洗时即被去除.从而产生色差。
例如,分散染料热溶温度两边或前后不一致、还原染料部分还原或氧化不充分、活性染料汽蒸条件不良等都会造成织物的前后或左右有色差。
(3)染料色光发生变异:这种差异不是由于织物上染料分布不均匀造成的.而是由于某些原因引起织物上的部分染料的色光发生变化,一般有以下几种原因:
①染前因素:半制品的白度不匀或pH值有较大差异,在染色后往往造成色光差异。
②染色因素:例如分散染料热溶温度过高,使某些染料的色光变得萎暗;还原染料的过度还原,也会使色光有差异。
②染后因素:在后整理过程中.如树脂整理、高温拉幅以及织物上PH值的不同等,都会引起染料色光有不同程度的变化。
④皂洗:如皂洗不充分,会使发色不充足.色光不准。
我公司生产的低温皂洗剂ZJ-RH18在活性染料染棉皂洗后处理中效果突出,低温皂洗工艺,用量在0.1~0.5g/L,不仅节能减排,降低生产成本,提高生产效益,洗后织物色光纯正,无色差烦恼!。